Introducción
Las tecnologías de Generación Distribuida (GD) en el mundo, se diversifican para hacer resiliente la expansión del sistema eléctrico y en consecuencia optimizar los recursos humanos, materiales, financieros y el impacto medioambiental. Su uso ofrece beneficios por la reducción de costos en pérdidas de transmisión y distribución en el orden del 5 al 10 % de energía generada (Muñoz-Vizhñay et al. (2018).
En América Latina, el empleo de la generación distribuida con grupos electrógenos, incrementa la capacidad generadora por su bajo costo de inversión y de operación en comparación con las grandes centrales termoeléctricas, lo que permite llevar el servicio eléctrico donde las inversiones en infraestructuras obstaculizan el mejoramiento de la calidad de vida de la población.
En Cuba, la generación distribuida, surge como forma eficiente de producción de electricidad durante la crisis energética en el país. Su implementación, optimiza las pérdidas, así como, la afectación del servicio a consecuencia de los fenómenos meteorológicos en la región durante la denominada temporada ciclónica.
En la actualidad, la matriz energética nacional se sustenta en un 95% a partir de generar electricidad con combustibles fósiles (Figueredo, 2022b). La contribución al sistema de generación por tipo se desglosa en: eólica con un 0,1%, solar 0,2%, hidráulica con un 0,5%, diésel con un 3,3%, biomasa con un 3,7%, gas acompañante con un 14,1%, fuel con un 33,1% y crudo con un 45% (Contreras et al., 2021).
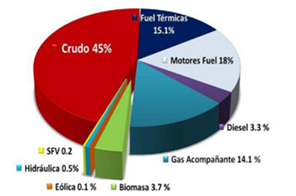
Fig. 1 - Porciento de contribución de cada tipo de energía a la matriz energética cubana.
Tal como se muestra en la Figura 1, en Cuba existe una gran dependencia de los combustibles fósiles, en los que juega un papel importante los grupos electrógenos con motores reciprocantes de combustión interna a fuel oil, impactando en la matriz energética en un 18 %.
Aun cuando el gobierno cubano, se encuentra inmerso en varios procesos inversionistas para transformar la matriz energética con la introducción de nuevas formas de generación renovables según plan de desarrollo hasta el 2030, donde se espera alcanzar el 37% de generación con esta tecnología (Figueredo, 2022b), este proceso tomará tiempo para su materialización, por lo que la preservación de las condiciones tecnológicas actuales es fundamental para el desarrollo del país.
En la actualidad, de los más de 6 000 MW de capacidad instalada en la generación eléctrica en Cuba, el 21,7% se respalda con motores a fuel oil, distribuidos en 35 centrales de generación, involucrando a 507 grupos electrógenos. Su función fundamental es potenciar la generación base del Sistema Eléctrico Nacional (SEN) y crear la reserva necesaria para la operación, realizar intervenciones en las termoeléctricas y reducir la generación con diésel (Figueredo, 2022a).
Materiales y métodos
En el desarrollo de la investigación presentada, se consulta el estado del arte en materia de diagnóstico a las máquinas eléctricas rotatorias, prestando atención a la evolución, desarrollo y perfeccionamiento de cada uno de los métodos existentes. Todo ello se hace posible mediante el uso de métodos científicos que facilitan mostrar los resultados fundamentales del objeto de estudio.
Entre los métodos de nivel teórico se utilizan el histórico -lógico y el análisis-síntesis.
Histórico-lógico. Para conocer los métodos más comunes desarrollados para detectar fallos de los generadores por causas de asimetrías electromagnéticas, desde su surgimiento, evolución y el desarrollo de los patrones de comportamiento, así como las metodologías de diagnóstico.
Análisis-síntesis. Para analizar los componentes de los generadores de modo multidisciplinario y comprender su estructura. En la síntesis deben integrarse, de manera armónica, las partes previamente analizadas, a fin de revelar sus relaciones y características generales.
Resultado y discusión
El fallo en una máquina eléctrica constituye un proceso inevitable debido a las solicitaciones térmicas, mecánicas, eléctricas y ambientales a las cuales se ven expuestas a lo largo de su vida útil. Sin embargo, con una adecuada estrategia de mantenimiento es posible evitar fallas imprevistas y lograr que la máquina alcance su vida útil. Antes de someter al activo a cualquier régimen de pruebas, es preciso evaluar su historial de operación, debido a que el indicio de cambio inusual en su condición, podría acusar una falla incipiente. Una herramienta de peso en el diagnóstico es la inspección visual, cuando es realizada por el personal calificado (Calo et al., 2019).
Los generadores de polos salientes son comúnmente utilizados en los grupos electrógenos debido a la baja velocidad de giro de su rotor, por ser accionados a través de un motor de combustión interna.
Tal como lo demuestran investigaciones realizadas por el Instituto de Ingenieros Eléctricos y Electrónicos y el Instituto de investigaciones de Energía Eléctrica (IEEE y EPRI por sus siglas en inglés), y que se ilustra en la Figura 2, los fallos de mayor ocurrencia en los generadores sincrónicos de polos salientes son los de excentricidad, al estar directamente ligados a síntomas de daños en los cojinetes (Sadeghi et al., 2017).
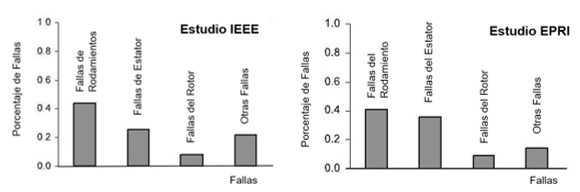
Fig. 2 - Diferentes tipos de fallos en las máquinas eléctricas rotatorias
Por este motivo, minimizar este modo de fallo es un reto vital para garantizar la confiabilidad del activo y la estabilidad de la producción de energía eléctrica.
Los modos de fallos presentes en los generadores eléctricos, pueden ser de origen mecánico o eléctrico. Dentro de los modos de fallos de origen mecánico, se encuentra la excentricidad del conjunto estator-rotor, una de las fallas más críticas que causa daños irreversibles al generador sincrónico, provocando alteraciones en sus parámetros eléctricos y mecánicos que caracterizan la operación (Ehya et al., 2017).
Se plantea que las excentricidades aparecen cuando el entrehierro no es uniforme, teniendo esta un origen multifactorial. Además, el incremento en la excentricidad a niveles fuera de los rangos admitidos, pueden conllevar al rozamiento entre rotor y estator, con daños catastróficos en ambos componentes y en consecuencia la parada imprevista de la máquina, conjuntamente a costosas reparaciones (Castro, 2020).
El mantenimiento y la salud del activo
La ejecución del mantenimiento afecta la continuidad del servicio de un sistema. La realización restringida de mantenimientos puede conducir a un incremento del número de fallos, lo que genera excesivos costos de explotación, y la ejecución en demasía de mantenimientos, puede aumentar la confiabilidad, pero también incrementa el costo de operación y mantenimiento considerablemente. Por lo tanto, se debe llegar a una solución de compromiso entre estos dos costos.
Los mantenimientos comúnmente implementados en la industria son: el correctivo, el preventivo y el predictivo (Tabla 1). El mantenimiento correctivo (MC), también conocido como mantenimiento reactivo, se aplica cuando la máquina sale de servicio por la ocurrencia de una falla o avería y su objetivo es restablecer su funcionamiento lo más rápido posible y en consecuencia evitar la menor afectaciones de la productividad. Estas estrategias son utilizadas por las empresas debido a que no cuentan con los conocimientos, herramientas, personal calificado, presupuestos asignados y tecnologías para la implementación de otros tipos de mantenimientos. Su mayor ventaja es su bajo costo de implementación. La desventaja fundamental del mantenimiento correctivo es no poder anticiparse al diagnóstico de la posible falla en la máquina, por lo que puede aparecer de forma inoportuna (Pérez, 2021).
El mantenimiento preventivo planificado (MPP), se fundamenta en la ejecución de rutinas de mantenimientos pre establecidas por espacios de tiempos fijados para las condiciones de operación y donde los ingenieros inspeccionan completamente todos los aspectos de la maquinaria, considerando las experiencias del fabricante y enriquecidas por las acumuladas por los explotadores de la tecnología. El objetivo fundamental es garantizar que los activos cumplan con las funciones para los que fueron diseñados y en consecuencia optimizar la eficiencia de los procesos, prevenir y adelantarse a las fallas de los elementos y componentes, evitando su parada. Como ventaja, se destaca que mejora los indicadores de disponibilidad y confiabilidad de la máquina en comparación con el mantenimiento correctivo. La desventaja principal es que implica un costo inevitable, al sustituir insumos producto a las acciones de desarme y arme de la máquina y no por deterioro de estos (Pérez, 2021; Ehya et al., 2017).
Estos procedimientos anteriormente descritos, no optimizan los costos del mantenimiento, en el MPP, debido a que se corre el riesgo de realizar operaciones innecesarias, con el uso de insumos materiales y tiempos de trabajos obligatorios con gastos inevitables. En el caso del MC, es el más grave, ya que la salida del activo es imprevista, por lo que acarrea los mayores costos de mantenimiento y afectación del servicio. En consecuencia, por razones de seguridad y económicas, existe una necesidad crucial de monitorear el comportamiento de la condición del generador durante su operación y la introducción paulatina de un sistema de mantenimiento más novedoso.
Antes de expandirse el empleo de los sistemas de monitoreo de la condición como herramienta soporte del mantenimiento predictivo, los relés de protección desempeñaron un papel vital en la protección de las máquinas eléctricas rotatorias. La principal diferencia entre estos, radica en la gravedad de la ocurrencia de fallas y el tiempo de alerta para los operadores. Cuando la falla alcanza su estado final en el generador, los relés de protección sacan la máquina de servicio. Mientras que, los sistemas de monitoreo de la condición, evitan daños severos al generador, transfiriendo la alarma al operador en el inicio del progreso de la falla, es por ello, que el uso del sistema de monitoreo de la condición, puede reducir el costo del mantenimiento en un 60% (Ehya et al., 2017).
El mantenimiento predictivo (MP). Se interpreta como un mantenimiento, donde se asocia la relación de parámetros físicos con el desgaste o estado de una máquina. Además, se tiene en cuenta la medición, el seguimiento y el monitoreo de parámetros de operación en las condiciones de instalación. Para el activo en su ambiente de operación, se precisan y se gestionan los valores de todas aquellas variables de diagnóstico que se predefinen de medir y gestionar.
El mantenimiento predictivo también se puede considerar como una técnica para pronosticar el punto futuro de falla, anomalía, rotura o avería de una máquina, de modo que, pueda reemplazarse el elemento o componente de forma planificada, justo antes de que falle. De esta manera se disminuye el tiempo improductivo y se prolonga la vida útil del activo. Se sustenta en pruebas de carácter no destructivo y un seguimiento de las variables de diagnóstico identificadas, para captar signos de advertencia que indiquen anomalías en el funcionamiento. La meta principal de este tipo de mantenimiento, es detectar un fallo en su estado incipiente y consigo evitar el fallo catastrófico de la máquina. Además, ofrece como ventaja adicional: la optimización de los repuestos, eliminando los stocks innecesarios (Pérez, 2021).
Tabla 1 - Comparación entre tipos de mantenimientos
Indicadores | Mantenimiento Correctivo | Mantenimiento Preventivo Planificado | Mantenimiento Predictivo |
---|---|---|---|
Personal y equipamientos | Carencia de personal calificado, herramientas y recursos tecnológicos. | Existencia de personal calificado, herramientas y recursos tecnológicos limitados. | Existencia de personal calificado, herramientas y recursos tecnológicos especiales. |
Costo de operación y mantenimiento | Menos costos de operación. No genera gastos fijos. Se gasta dinero cuando se realiza el mantenimiento. Puede generar costos excesivos por la afectación del servicio de forma imprevista. |
Control de las fallas, que redundan en una reducción en los costos de operación. Se generan gastos según los ciclos de mantenimientos. Se incrementan costos por capacitación del personal. |
Menores costos de operación. Costos elevados por la adquisición de tecnologías. Se incrementan costos por capacitación del personal. |
Nivel de inventarios | Altos niveles de inventarios, para poder corregir las fallas. | Reducción en los niveles de inventarios para asegurar los ciclos de mantenimientos programados. | Bajos niveles de inventarios |
Predicción de la falla | No existe | Baja nivel de predicción de la falla | Alto nivel de predicción de las fallas en su estado incipiente. |
Producción | Es impredecible la producción y poco confiable | Control de la producción, afectación en consecuencia con los ciclos de mantenimientos. | Producción con índices de confiabilidad elevados. |
Fuente: Pérez, (2021)
Diagnóstico de excentricidades en las máquinas eléctricas rotatorias
Los operadores constituyen el primer escalón del sistema de diagnóstico al generador eléctrico, se enfrentan a diferentes modos de fallos, adoptando las decisiones necesarias para mantener la producción de energía eléctrica sin afectar el activo. Dentro de los modos de fallos de origen mecánico, se encuentra la excentricidad, una de las fallas más críticas para el generador sincrónico, provocando alteraciones en sus características de operación, tales como: aumento de los armónicos de tensión y corriente, reducción de la eficiencia, aumento de la temperatura, y del par pulsante, entre otras (Ehya et al., 2017).
Las excentricidades aparecen cuando el entrehierro no es uniforme, teniendo esta un origen multifactorial. Además, el incremento en la excentricidad a niveles fuera de los rangos admitidos, pueden conllevar al rozamiento entre rotor y estator, con daños catastróficos en ambos componentes y la salida imprevista de la máquina, conjuntamente a costosas reparaciones (Castro, 2020).
Tipos de excentricidades
La bibliografía técnica consultada expone tres tipos principales de excentricidades: las estáticas, las dinámicas y las mixtas(Ehya et al., 2017; Pal & Mohanty, 2020; Terron-Santiago et al., 2022), como se ilustra en la Figura 3.
La excentricidad estática es la excentricidad en la que la posición de mínimo entrehierro permanece fija en el espacio. La excentricidad dinámica es la que se produce cuando la posición de mínimo entrehierro es variable en el espacio y la excentricidad mixta es la combinación de las excentricidades estática y dinámica.
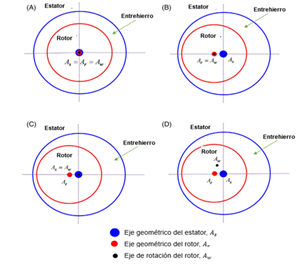
Fig. 3 - Tipos de excentricidades. a) máquina sana, b) excentricidad estática, c) excentricidad dinámica, d) excentricidad mixta.
Métodos más utilizados en el diagnóstico de excentricidades
Existen variados métodos para el diagnóstico de excentricidades en las máquinas eléctricas rotatorias, enfocados fundamentalmente al diagnóstico de los motores de inducción, no siendo así en los generadores sincrónicos (Mostafaei & Faiz, 2021).
Para diagnosticar la excentricidad en la máquina eléctrica rotatoria, los especialistas se han centrado en el espectro de la Transformada Rápida de Fourier (FFT) de la corriente del estator. También, se destacan como otras técnicas: el análisis de la corriente en transitorios, del flujo y las vibraciones, los cuales han probado ser fuentes de información valiosa. Se recomienda para mejor precisión en el diagnóstico, el complementar las diferentes técnicas y métodos entre sí, sin embargo, a diferencia del análisis de vibraciones, los análisis de corrientes y flujo de dispersión son técnicas muy versátiles en aplicaciones hostiles o de difícil acceso en donde la instrumentación para realizar la medida de vibraciones u otro aparato de diagnóstico no sea posible (Castro, 2020).
Aunque la mayoría de las investigaciones relacionadas con el diagnóstico de este modo de fallo tratan sobre su aplicación en los motores de inducción, la literatura científica actualizada aporta gran volumen de información. Como novedad, los métodos de diagnósticos modernos requieren, no solo la diferenciación entre una máquina sana o en falla, sino también, la estimación confiable del nivel de gravedad de la falla, que permita la planificación de las acciones de mantenimiento y del servicio (Gyftakis et al., 2019).
Monitoreo de la densidad del flujo magnético
En un generador sano y con el entrehierro simétrico, la densidad de flujo es uniforme (Figura 4 a). La falla de excentricidad, conduce a un entrehierro asimétrico, trayendo consigo la distorsión en la densidad de flujo magnético (Figura 4 b). El monitoreo del flujo del entrehierro es uno de los métodos invasivos que se ha utilizado para investigar la ocurrencia de fallas de excentricidad en el generador sincrónico. Para ello, se requiere de la existencia de un sensor llamado sonda de flujo o bobina de búsqueda, cuyo funcionamiento está basado en la ley de Faraday (Ehya et al., 2017).
Una forma más económica para monitorear la densidad de flujo magnético del entrehierro, es a través de la tensión terminal de la máquina por su relación directa con la distorsión del patrón de flujo magnético causada por una falla de excentricidad, al no requerir de la introducción de sensores en el estator. También existen otros factores que distorsionan este flujo magnético, como los armónicos debido a la estructura sincrónica del generador, el cortocircuito de barras del estator o el devanado del rotor y la rotura de la barra de amortiguación de los polos del rotor. Esto indica, no ser una variable efectiva para la detección de fallas de excentricidad, debido a que no permite distinguir el tipo y la gravedad de la falla de excentricidad en el generador sincrónico (Ehya et al., 2017).
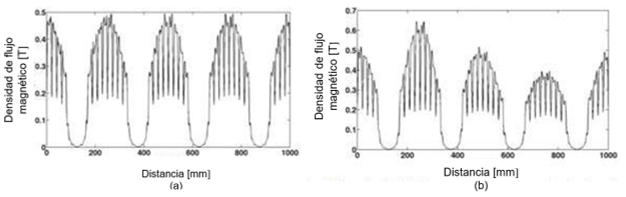
Fig. 4 - Distribución de la densidad del flujo magnético en el entrehierro del generador síncrono de polos salientes a carga nominal, a) sana, b) 30% de excentricidad dinámica.
Monitoreos de las corrientes del estator
En (Ehya et al., 2017), se expone que el 85% de las fallas de excentricidad dinámica en el generador sincrónico de polo saliente, aumentan la magnitud de los armónicos de corrientes del estator. Además, que el incremento en los armónicos 3ero, 17mo y 19no, se han utilizado como índice para la detección de este fallo. Sin embargo, ninguno de los indicadores mencionados se pudo utilizar como herramienta suficiente para su detección, ya que estos armónicos existen inherentemente en señales de la máquina sincrónica debido a su estructura. También, las componentes de armónicos en los sistemas de potencias causados por cargas no lineales son similares a estos armónicos. Por lo tanto, estos índices pueden ser útiles en generadores sincrónicos (GS) aislados.
Monitoreo de la tensión en los terminales del estator
A través de la tensión de fase en el generador sincrónico, se puede detectar un fallo de excentricidad, ya que la misma estimula armónicos de alto orden en esta variable. El armónico de orden 21ero, se ha utilizado como índice para el diagnóstico de fallas de excentricidad. Aunque este indicador tiene una sensibilidad ante falla de excentricidad, puede verse afectada por el ruido. También los armónicos de tensión de fase como 3ero, 5to, 13ero, 17mo y 19no, han sido utilizados como índice para el diagnóstico de excentricidad, sin embargo, la forma del estator y las ranuras del rotor, la saliencia del polo del rotor y la conexión en serie o en paralelo del devanado del estator, tiene un efecto sobre los armónicos mencionados (Ehya et al., 2017).
Monitoreo del flujo de eje y tensión de eje
En una máquina ideal, el flujo que atraviesa la sección transversal de la máquina es idéntico para todos los pares de polos. Ante la ocurrencia de una falla por excentricidad, la longitud del entrehierro se distorsiona, afectando la distribución del flujo magnético en el rotor. Este parámetro se denomina, flujo de eje de la máquina (Figura 5). La tensión de eje varía desde unos mV hasta cientos de mV en correspondencia con la potencia del generador. Si la resistencia de la trayectoria es baja, pasa una corriente alta a través del eje y el cojinete de la máquina a tierra, la cual puede provocar daños graves en la misma.
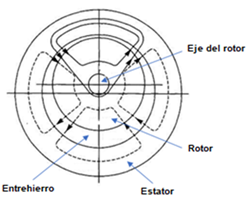
Fig. 5 - Flujo concatenado en el eje con respecto a los flujos giratorios del entrehierro.
Los resultados experimentales demuestran, que la falla de excentricidad, genera tensiones en el eje y su magnitud tiene relación directa con la gravedad de la falla. Aunque los armónicos 5to, 6to y 8vo de la tensión en el eje, se han utilizado como índices de falla de excentricidad, hay muchos factores que conducen a una densidad de flujo magnético desequilibrado en el entrehierro, los que en consecuencia generan tensión en el eje. El flujo magnético del eje existe en una máquina sincrónica sana debido a su estructura geométrica interna, que hace que el núcleo del estator se convierta en asimétrico (Ehya et al., 2017).
Crítica a los métodos presentados
En concordancia con lo analizado y resumido en (Ehya et al., 2017), los métodos propuestos presentan desventajas que afectan su uso para la detección de fallos de excentricidad.
La densidad del flujo magnético es un método invasivo costoso, que requiere de la existencia de la sonda de flujo insertada dentro de la ranura del estator de la máquina, por lo que no es aplicable al generador que esté funcionando.
El armónico de corriente del estator del generador no resulta eficaz para diagnosticar el fallo de excentricidad cuando se encuentra en presencia de cargas no lineales. Aunque variaciones temporales del vector espacial de la corriente del estator, es una medida apropiada para el reconocimiento del tipo de fallo de excentricidad, la severidad de la falla no puede ser estimada por este indicador.
El contenido de armónicos de la tensión de fase en el generador sincrónico, se ve afectado bajo cargas no lineales, así como también en condiciones de carga nominal, debido al aumento de los niveles de ruido.
La tensión y el flujo de eje son métodos invasivos que requieren para su implementación equipamientos sensibles, además, estos métodos no permiten reconocer el tipo de fallo por excentricidad ni su severidad.
Con el propósito de mejorar todas las desventajas mencionadas de los índices propuestos anteriormente, se propone un nuevo enfoque apoyado en el método de minería de datos de series temporales, que se basa en utilizar la tensión de fase del generador sincrónico para cuantificar el grado de fallo de excentricidad a través del radio de giro normalizado (NGR por sus siglas en inglés). La utilización de este índice globalizado, permite diagnosticar este modo de fallo en cualquier tipo de generador sincrónico independiente de su potencia nominal. Además, al presentar este índice, mayor sensibilidad ante fallas de excentricidad estática que dinámica, puede usarse como una herramienta adecuada para reconocer el tipo de excentricidad (Ehya et al., 2017).
Medición del Grado de excentricidad del entrehierro en la GD en Cuba
La excentricidad es un parámetro mecánico, que comúnmente es verificado en los generadores eléctricos de los grupos electrógenos de forma manual durante las rutinas de mantenimiento que se apliquen, según el programa previsto en la matriz de mantenimiento de la entidad explotadora de la tecnología. Esto, de igual modo se realiza en la Generación Distribuida en Cuba.
Para la realización del procedimiento, se requiere poner fuera de servicio al grupo, interrumpiendo el proceso de generación. Este procedimiento tiene como objetivo, verificar el estado de simetría del entrehierro con el paso del tiempo de operación del activo.
Insuficiencias identificadas en el proceso de mantenimiento que afectan la producción de energía eléctrica en los grupos electrógenos Hyundai.
El tipo de mantenimiento aplicado a los grupos electrógeno dentro del sistema de gestión de mantenimiento en la GD en Cuba, es el preventivo planificado, el cual tiene descrita todas las rutinas de mantenimiento, según el programa previsto en la matriz de mantenimiento contenida en el procedimiento general, así como, el detalle de sus operaciones en sus instrucciones de trabajo. En su evaluación se identifican insuficiencias que afectan la producción de energía en estos activos.
Las intervenciones de mantenimiento que contemplan los componentes que influyen en la excentricidad del entrehierro, se verifican espaciadas en el tiempo, en función del ciclo de mantenimiento que se realice y para ello se requiere que el grupo electrógeno, se encuentre fuera de servicio.
El grupo electrógeno (GE), no contiene sensores que muestren alarmas ante situaciones de excentricidad del entrehierro de la máquina, por lo que puede ocurrir un fallo sin ser detectado por el operador.
Las mediciones registradas durante la operación del GE, por sí sola no permiten decidir sobre el estado de excentricidad del generador.
La corriente por el neutro, una variable de estado de diagnóstico de la excentricidad
La corriente por el neutro del generador puede ser originada por causas externas y/o internas, dentro de estas últimas se encuentra la excentricidad. Esto trae como consecuencia la aparición de componentes del orden armónico fundamental, de secuencia positiva, negativa y cero que producen efectos no deseados (Díaz et al., 2019): corrientes circulantes entre los neutros de generadores que compartan la misma puesta a tierra, ocasionando potenciales de paso peligrosos; calentamiento de la conexión de puesta a tierra del neutro, además del devanado del estator, debido a la pérdida adicional de energía causada por las componentes de secuencia cero y negativa; el calentamiento adicional debido a la circulación de la corriente capacitiva a través del devanado, contribuye a la reducción de las propiedades fisicoquímicas del aislamiento, reduciendo la rigidez dieléctrica y aumentando las descargas parciales.
Por otro lado, debido a la componente de secuencia negativa, aparecen momentos de frenado, vibraciones y emisión de ruido acústico, aumentan las pérdidas adicionales en los núcleos de hierro y en el cobre del devanado amortiguador, se incrementan los potenciales eléctricos y corrientes entre el eje y tierra, deteriorando las características metalúrgicas del rotor y los puntos de contacto de los cojinetes, se afecta el funcionamiento de dispositivos eléctricos de regulación, tanto de potencia, como de control y puede haber mala operación en dispositivos de protección y medición entre otros.
En el neutro del generador, la forma de onda predominante de la corriente es de tercera armónica, con cierto nivel de frecuencia fundamental y en menor proporción frecuencias impares. Además, debido a las diferencias constructivas de la máquina, estos valores son diferentes aun cuando sean de igual capacidad y el mismo fabricante. Por tanto, con el monitoreo de esta variable, puede diagnosticarse el balance electromagnético de la máquina, ya que la ocurrencia de cambios mecánicos o eléctricos, trae como consecuencia un desbalance electromagnético que se ve reflejado en el contenido armónico de la corriente en el neutro(Martínez et al., 2017).
La componente de tercera armónica de la corriente en el neutro del generador, es dependiente de las condiciones de carga de este, por lo que, en condiciones de carga máxima, alcanza su valor máximo. Debido a ello, este indicador no es efectivo para el diagnóstico de la excentricidad durante la operación del activo. En cambio, la corriente de frecuencia fundamental no se modifica con la carga y se mantiene prácticamente invariable con el tiempo de operación, constituyendo un parámetro que brinda información del estado de excentricidad de la máquina, al verse afectada por los balances eléctrico, magnético y mecánico del generador (Martínez et al., 2017).
En una máquina sana, circula una corriente por el neutro que se encuentra entre el 5 y el 10% de su valor nominal (Salah et al., 2019). El uso de esta variable proporciona beneficios para el diagnóstico de la excentricidad del generador debido a que, no se ve afectada por las variaciones que experimente la carga. Además, si el balance electromagnético y mecánico se conservan, entonces la magnitud de la componente fundamental de la corriente por el neutro, debe mantenerse invariable en el tiempo (Martínez et al., 2017). Por otro lado, constituye un método no invasivo que requiere de menos costos para su implementación, con un apreciable fin práctico.
Conclusiones
La componente fundamental de la corriente por el neutro del generador, brinda información del estado de excentricidad del entrehierro. Además, de no modificarse ante las variaciones de la carga y cuando permanecen invariables las condiciones electromagnéticas en el interior de la máquina.
La aplicación del sistema de mantenimiento preventivo planificado conduce a gastos insostenibles en la actualidad, por lo que una transición a sistemas de mantenimientos más novedosos, es requerida como estrategia para la generación distribuida.
La introducción paulatina de técnicas de diagnóstico basadas en la condición del generador eléctrico apegado a la ciencia y la innovación, conducen al perfeccionamiento del sistema de gestión del mantenimiento de la generación distribuida.
La implementación del mantenimiento predictivo en la generación distribuida optimiza los recursos humanos, materiales, financieros y el impacto medioambiental, así como, eleva la confiabilidad del sistema de generación.