INTRODUCCIÓN
En la industria de la refinación de petróleo es frecuente trabajar con crudos de oportunidad, lo que incrementa el riesgo de daños por corrosión en unidades de destilación atmosférica y de vacío, instalaciones necesarias para la separación primaria del crudo en fracciones o cortes.
Los hidrocarburos ya sea en forma líquida o gaseosa no son corrosivos, aunque en zonas de menor temperatura podría ocurrir la corrosión cuando el vapor de agua condensa y se disuelve en ella constituyentes ácidos y otras especies corrosivas presentes en la fracción hidrocarbonada. Tal condición se limita a los cabezales de las columnas de destilación, donde se presenta el agua libre (Kumar, 2017). Los problemas de corrosión pueden aumentar significativamente el costo de operación y mantenimiento en las refinerías.
Los componentes del sistema de tope de la unidad de destilación atmosférica (UDA) como: la columna de destilación, carcasas de intercambiadores, tambores separadores y tuberías, en su mayoría son fabricados de acero al carbono, material que al estar en contacto con una disolución acuosa que contiene ácidos como el clorhídrico (HCl) y sulfhídrico (H2S), se corroe. El mecanismo de corrosión presente es electroquímico e incluye dos reacciones: anódica y catódica, que ocurren simultáneamente (Groysman, 2017).
Existen diferentes métodos para la protección del acero en estas unidades de refinería dentro de los que se encuentran, la aplicación de diversos productos químicos, incluidos inhibidores de la corrosión (IC), cuya función es minimizar la velocidad de corrosión a límites aceptables. Entre las características que poseen tales productos químicos se mencionan: mayor eficiencia en dosis más bajas y cumplir con requisitos prácticos como baja emulsión, ser térmicamente estable, baja tendencia a la formación de espuma, entre otros (Saji y Umoren, 2020). En la investigación, se evaluó un inhibidor comercial constituido por una mezcla líquida de aminas formulada para neutralizar en el agua condensada, gases disueltos como el H2S y HCl, según proveedor del producto. El objetivo de la presente investigación es determinar el desempeño electroquímico actual del inhibidor de corrosión comercial utilizado en el tope de la columna de destilación atmosférica.
MATERIALES Y MÉTODOS
Mediante la técnica de Espectrometría de Emisión por Arco Eléctrico, se determinó la composición química elemental del acero. Se utilizó un espectrómetro multicanal digital modelo Spectrolab No.6536/94.
En el análisis estructural de la aleación por la técnica de metalografía, se empleó un microscopio portátil modelo PSM-10 de la Struers, con una cámara digital acoplada que permitió obtener micrografías con aumento de 400X. Previamente, se prepararon probetas metalográficas mediante operaciones de corte, montaje, desbaste y pulido como establece la norma ASTM E3-11 (2017). Posteriormente, para el revelado de la estructura metalográfica de las probetas, se utilizó la disolución de ataque químico No. 74 (Nital), de acuerdo con la norma ASTM E407-07 (2015).
En los ensayos electroquímicos se empleó un medio electrolítico binario compuesto por hidrocarburo/agua residual del sistema de tope de la UDA, esta última como medio corrosivo. Se estableció que el agua residual representa el 48% de la disolución total del sistema y a la misma se le determinó a temperatura de 24,7 ᵒC y humedad 45%, el contenido de calcio (Ca) (ISO 6058:1984, 2017), magnesio (Mg) (ISO 6059:1984, 2017), sodio (Na) (ISO 9964-1:1993, 2019), hierro (Fe) (ISO 6332:1988, 2017), pH (ISO 10523:2008, 2017) y Sulfuros (S2-), Cloruros (Cl¯) y Conductividad (APHA-AWWA-WEF, 2017).
Resistencia de polarización lineal (LPR por sus siglas en inglés): La técnica de resistencia de polarización lineal se aplicó en correspondencia a la norma ASTM G59-97 (2020). Los ensayos se ejecutaron en circuito abierto bajo condiciones estáticas a temperatura de 32 ᵒC. La celda electroquímica consistió en un balón de vidrio de 500 mL de capacidad, donde se colocó el electrodo de trabajo de acero (ET) de 1 cm2 de área expuesta, el de referencia Ag/AgCl (ER) y el auxiliar de grafito (EA). La superficie del ET se preparó según norma ASTM G1-03e1 (2017).
La celda electrolítica se conectó a un equipo GILL AC serial No1704 Sequencer, versión 5.1.4 de la firma ACM Instruments, mediante cables recubiertos que trasmiten las señales de los procesos de corrosión y las expresan en valores gráficos y numéricos. El equipo se programó para realizar un barrido de potencial en ± 10 mV en torno al potencial de corrosión (Ecorr), registrando lecturas de corriente. Los datos obtenidos de la velocidad de corrosión (Vcorr) se procesaron estadísticamente (ASTM G16-13, 2019). Antes de cada registro se estableció un período de una hora para estabilizar el potencial de la muestra de acero en contacto con la disolución corrosiva.
Curvas de polarización potenciodinámicas: La técnica se aplicó de acuerdo con la norma ASTM G5-14e1 (2014). Para la obtención de las curvas de polarización potenciodinámicas se realizó un barrido de potencial ± 250 mV respecto al Ecorr, con una velocidad de 28,3 mV/min. Las ramas anódicas y catódicas se obtuvieron para la determinación de manera cualitativa del comportamiento de la velocidad de corrosión.
Ruido electroquímico (RE): En los ensayos de RE se emplearon las normas ISO 17093 (2015) y ASTM G199-09e1 (2020). Los materiales utilizados se correspondieron con 2 especímenes de acero al carbono de áreas similares (1.15 cm2) como ET, insertados en resina y un ER de Ag/AgCl. Los mismos fueron inmersos en una celda electrolítica de 600 ml de capacidad, que se acopló al equipo multipropósito Gill AC de 6 canales secuenciales. La superficie del electrodo de trabajo se preparó de igual manera que el procedimiento descrito en las técnicas anteriores.
La tasa de muestreo fue de 1 punto/segundo y se hicieron 2048 registros en la serie de tiempo. Los resultados se analizaron de modo cualitativo y cuantitativo. Los cuantitativos permitieron obtener el índice de localización (IL), a partir del cociente de la desviación estándar de la corriente, entre la raíz cuadrática media de la corriente. La figura 1 muestra el montaje de los sistemas experimentales.
RESULTADOS Y DISCUSIÓN
Composición química elemental y microestructura del acero
La tabla 1 expone los resultados del análisis de la composición química elemental del acero utilizado en la línea de tope de la columna de destilación atmosférica. El mismo se corresponde con un acero al carbono estructural A106 de bajo contenido en carbono (0,1 a 0,35 % peso) (Kumar, 2017), especificado en la norma ASTM A106/A106M-19a (2019). Estos aceros al carbono son empleados ampliamente en la industria de la refinación del petróleo, en sistemas donde se espera una velocidad de corrosión menor que 0.5 mm/año y temperaturas inferiores a 427°C. No obstante, podrían ser susceptible a daños por corrosión en presencia de H2S y HCl en medio acuoso.
El examen metalográfico reveló que la microestructura del acero (figura 2), consta de una matriz ferrítica- perlítica obtenida mediante tratamiento térmico de normalizado. La ferrita es una fase blanda de baja resistencia con una estructura cristalina cúbica centrada en el cuerpo, en cambio la perlita es una mezcla de ferrita y cementita, en que las dos fases se forman a partir de la austenita en un patrón laminar alterno, su formación requiere un enfriamiento relativamente lento de la región austenita y depende de la composición del acero. La resistencia y la dureza de los aceros de microestructura ferrítica-perlítica, se incrementan con el contenido de perlita y más aún con la reducción del espacio interlaminar de esta.
Parámetros fisicoquímicos del medio corrosivo (MC)
El análisis fisicoquímico del agua residual como MC (tabla 2), reportó un medio ácido con una conductividad de 75 µS/cm. Groysman (2010), refiere que las soluciones acuosas con conductividad eléctrica superior a 10 µS/cm se consideran muy agresivas para los metales, debido a la mayor capacidad del líquido de conducir la corriente eléctrica entre sitios anódicos y catódicos localizados en la superficie metálica, lo que propicia un incremento de la velocidad de corrosión.
El contenido de iones Cl¯ presente en la muestra se relaciona con la existencia de HCl en el MC. El HCl proviene, principalmente, del hidrólisis de sales de calcio (CaCl2) y magnesio (MgCl2), cuyos cationes se encuentran presentes en el medio acuoso (Groysman, 2017; Ahmed, 2020). Experiencias obtenidas en refinerías han demostrado que contenidos de iones Cl¯ superiores a 20 mg/L, tienen el potencial de provocar importantes daños por corrosión e incrustaciones en los sistemas de tope de la UDA (Subramanian, 2020; Groysman & Hiram, 1997).
La concentración de Fe supera al valor de control aceptable en la UDA (0,5 mg/L). Su presencia se podría atribuir a la disolución del acero en el MC ácido (Groysman & Hiram, 1997).
En el sistema de tope de la UDA junto al HCl se presenta el S2-, aportado principalmente por el H2S. Este último es un gas ácido corrosivo que ataca al acero al carbono en áreas donde se origina la condensación del agua, favoreciendo la corrosión por HCl, especialmente, en condiciones de bajo pH. Aunque el H2S tiene un impacto menor sobre la corrosión que el HCl y otros ácidos orgánicos que podrían estar presentes, el mismo podría causar daños relacionados con el hidrógeno, entre los que se mencionan: formación de ampollas, agrietamiento inducido por hidrógeno, agrietamiento por tensión en presencia de sulfuros, etc. (Kumar, 2017).
Resultados de las técnicas electroquímicas LPR y curvas de polarización potenciodinámicas
La tabla 3 muestra los datos obtenidos de la efectividad del inhibidor de corrosión (IC) a varias concentraciones, por la técnica LPR.
La Vcorr del acero no inhibido fue de 1,0404 mm/año, valor que la industria química establece como un comportamiento a la corrosión de moderado a pobre, en el intervalo de 0,5 < Vcorr < 5,0 mm/año (Pedeferri, 2018). Solo a concentraciones superiores de 50 ppm es significativo el efecto del IC, hecho que se manifiesta en un incremento sustancial de la resistencia a la polarización. A partir de 75 ppm se alcanzan eficiencias superiores al 90%, resultado que refleja mayor efectividad en la protección del acero en el MC.
Las curvas de polarización indican las regiones anódica y catódica. En los sitios anódicos, ocurre la disolución y oxidación de los metales. Mientras que en los sitios catódicos los procesos de reducción. La principal reducción catódica en medio ácido es el desprendimiento de átomos de hidrógeno.
En los sitios anódicos, la oxidación podría ocurrir de acuerdo con la ecuación siguiente:
Mientras que, en los sitios catódicos, la principal reducción catódica en medio ácido es la evolución del hidrógeno:
Los átomos de hidrógeno se combinan para la formación de hidrógeno gaseoso, pero parte del hidrógeno en estado atómico se difunde en el material.
El comportamiento de las curvas de polarización expuestas en la figura 3, demuestran que la adición del IC a 50, 75 y 100 ppm, propició un desplazamiento marcado de las ramas anódicas y catódicas, en dirección al decrecimiento de las densidades de corriente (Icorr), y por tanto, a menores Vcorr, lo que se corresponde con los resultados obtenidos por la técnica de LPR.
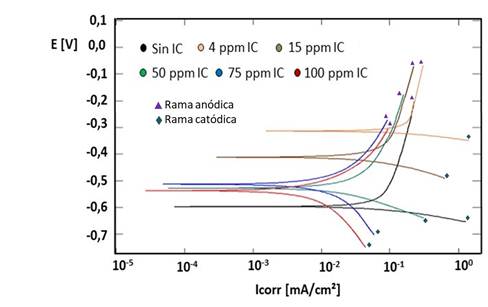
Fig. 3 Curvas de polarización potenciodinámica del acero A106 en el MC a diferentes concentraciones de inhibidor.
En la condición inicial sin IC, el control de la semirreación anódica ocurre por difusión y en la semireacción catódica por transferencia de carga, estados que se mantienen cuando se adiciona el IC en concentraciones de 4 y 15 ppm. Por otra parte, las dosificaciones inducen el desplazamiento del potencial del acero a valores más electropositivos, con disminución perceptible de la Icorr, al adicionarse 15 ppm del inhibidor, lo que podría sugerir que el IC actúa bloqueando los sitios activos localizados en la superficie metálica, lo que es común en inhibidores del tipo anódico. En cambio, a mayores concentraciones (≥ 50 ppm), se evidencian variaciones importantes en las pendientes de las ramas anódicas y catódicas, que influyen notablemente en la caída significativa de la Icorr. Tal comportamiento, se atribuye a una mayor adsorción de los compuestos orgánicos presentes en el inhibidor, sobre la superficie del electrodo de acero, lo que influye en el retardo del proceso de disolución del acero y de la difusión del hidrógeno, comportamiento característico de los inhibidores tipo mixtos.
Según refiere Zavaleta et al. (2018), si el desplazamiento de Ecorr es más de 85 mV con respecto al potencial del acero en la disolución desinhibida, el comportamiento del inhibidor podría ser de tipo catódico o anódico, en caso contrario del tipo mixto. Del cálculo realizado a partir de la referencia citada, se obtuvieron desplazamientos de potencial (Ecorr Inh.-Ecorr sin Inh.), inferiores a 85 mV, cuando la dosificación del IC se incrementa desde 50 ppm hasta 100 ppm, lo que permitió definir que el inhibidor es del tipo mixto a estas concentraciones.
El registro de corriente vs tiempo (figura 4), presentó para el sistema no inhibido, fluctuaciones rápidas de alta amplitud, representativas de un sistema bajo corrosión generalizada (Casquete, 2016). Además, se muestran puntualmente fluctuaciones marcadas de corriente, comportamiento que se atribuye a posibles eventos localizados, como picaduras, cuya causa es frecuentemente atribuida a la presencia de especies químicas como los iones de cloruros. Los registros de densidad de corriente en el tiempo con adición del inhibidor en concentraciones de 50, 75 y 100 ppm, presentaron niveles de ruido notablemente inferiores al compararse con el medio desinhibido, que se relacionan con formación de la película de inhibidor que actúa como una barrera entre la superficie metálica y el medio acuoso agresivo, lo que limita los procesos corrosivos.
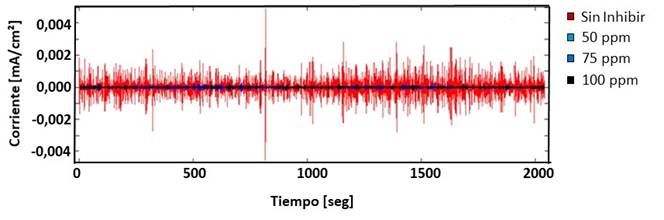
Fig. 4 Registros de densidad de corriente en el tiempo del acero A106 inmerso en el MC sin inhibir y a diferentes concentraciones de IC.
En la tabla 4 se exponen los resultados del cálculo de los índices de localización (IL) en ausencia y presencia de inhibidor, los que se clasificaron por el siguiente criterio (Contreras et al., 2017): 0,1<IL<1,0 localizada, 0,1<IL<0,01 mixta y 0,001<IL<0,01 general.
La corrosión localizada en el acero con presencia del IC, podría atribuirse a la formación de micropicaduras metaestables de corto tiempo de existencia, originadas por defectos puntuales en la película que recubre al acero.
CONCLUSIONES
La velocidad de corrosión del acero A106 expuesto al medio corrosivo ácido desinhibido, manifestó una corrosión de 1,0404 mm/año clasificada como una resistencia a la corrosión entre moderada y pobre. El inhibidor comercial solo mostró un efecto inhibidor significativo en concentraciones por encima de 50 ppm y eficiencias superiores al 90% a partir de 75 ppm. El acero A106 expuesto al medio corrosivo ácido, evidenció un ataque corrosivo del tipo mixto con predominio de corrosión generalizada. En cambio, en presencia de una concentración superior a 50 ppm del inhibidor comercial el tipo de ataque predominante fue el localizado. La técnica de ruido electroquímico reveló que concentraciones de inhibidor superiores a 50 ppm, el ruido disminuye notablemente, cuando se compara con el medio corrosivo desinhibido.