1. INTRODUCTION
An invert sugar is the equimolar mixture of glucose and fructose obtained by the hydrolytic activity of invertases (β-D-fructofuranosidase, EC 3.2.1.26). The resulting invert syrup is non-crystallizable and sweeter than sucrose because of the fructose content, finding specific applications in the food industry. Thermotoga maritima β-fructosidase (BfrA) is the most thermoactive and thermostable invertase so far identified and it is less susceptible to substrate inhibition than the S. cerevisiae enzyme. The BfrA has been produced in a Pichia pastoris strain BfrA4X, which secreted BfrA both to the cell periplasm and to the culture medium (Menéndez et al., 2013).
In a previous study, Pichia pastoris BfrA4X was successfully grown in a culture media with refined sugar as carbon source (Martínez et al., 2014). One of the key aspects in the fermentation process is the development of a cost-effective culture medium to obtain maximum product yield. Cane molasses is a relatively inexpensive raw material obtained as by-product of the sugar industry, which contains water (17-25%), sugar (~50%), polysaccharides (~25%), nitrogenous substances, vitamins (thiamine, riboflavin, pyridoxine, folic acid, biotin, and pantothenic acid), and trace elements (Najafpour & Poi Shan, 2003). Cane molasses has already been used for the production of a number of industrially important enzymes (Helm et al., 2023); (Muller et al., 2023); (Torrellas et al., 2023). In the particular case of invertases, several reports have shown the use of molasses (Hapeta et al., 2021); (Lin et al., 2021). The low nitrogen levels in cane molasses (0.4-1.5% nitrogenous substances), and the resultant high C:N ratio, prompted the need for supplementation with an external source of nitrogen, such as yeast extract or yeast hydrolysate. Yeast hydrolysate consisted of crude carbohydrate (23.6%) and crude protein (68.3%) with low contents of crude ash (3.1%) and crude fat (0.3%) (Lee et al., 2009).
For scale-up different criteria can be used. The two major scale-up criteria in continuously stirred bioreactors are constant gassed power input per liquid volume (Pg/V) and constant volumetric O2 mass transfer coefficient (k L a) (Doi et al., 2020), (Pillaca-Pullo et al., 2022) However, Pg/V is only influenced by the stirrer geometry, stirrer speed, aeration, and working volume, while the k L a includes relevant parameters that influence oxygen supply (sparging of gas, bioreactor design, etc ) but is additionally affected by physiochemical properties of the medium (temperature, pH, salt content, etc.) (Rastädter et al., 2023). Since in aerobic cultures, oxygen transfer is the controlling step for the microbial growth, it could be a good indicator of changes in the metabolic state of the culture. The basis of a constant k L a scale-up is to ensure the maintenance of a certain mass transfer capability to supply the oxygen demand of the culture at the high sized fermentors (Muñoz et al., 2019). The value of k L a is experimentally determined in the small bioreactor to determine the agitation and aeration rates to give equal k L a in the larger scale fermentor.
In order to maximize the production of BfrA from the recombinant P. pastoris BfrA4X, the objective of this investigation was to evaluate four combinations of carbon and nitrogen sources for industrial production of BfrA by Pichia pastoris BfrA4X.
2. MATERIAL AND METHODS
2.1 Microorganism
Pichia pastoris GS115 strain BfrA4X, expressing the Thermotoga maritima β-fructosidase, was obtained from the culture collection of the Center for Genetic Engineering and Biotechnology, Havana, Cuba (Menéndez et al., 2013).
2.2 Carbon sources
The sucrose source used was raw cane sugar from the Melanio Hernández sugar-factory (Sancti Spíritus, Cuba). Cane molasses was obtained from Boris Luis Santa Coloma sugar-factory, (Mayabeque, Cuba). The molasses was diluted 2-fold and homogenized in distilled water. After being incubated at room temperature for 24 h, the supernatant was obtained by decantation and it contained 35% (w/w) sucrose, 15% (w/w) inverted sugars, 2.5% (w/w) other carbohydrates, 8% (w/w) ash, 4.6% (w/w) metal ions and 20% (w/w) water. All chemical characterizations of molasses were done in Agricultural research Center, Cuba (NC 715, 2009).
2.3 Nitrogen sources
Two sources of nitrogen were used: yeast extract (Biocen, Cuba) and hydrolyzed Candida utilis obtained through aerobic fermentation from Sugar Enterprise Ciro Redondo, Ciego de Ávila. To differentiate between the two, the Biocen source will be referred to as yeast extract and the C. utilis source as yeast hydrolysate.
2.4 Shake-Flask Batch Culture
Cultivation was performed with four different means in 1 L Erlenmeyer flasks containing 0.2 L of medium with the follow composition (g/L) SYE [sucrose, 50; Yeast extract, 5; (NH4)2SO4, 22; K2HPO4, 28.5; MgSO4 7H2O, 7.5 and CaCl2 2H2O, 0.5]; MYE [Molasses, 55; Yeast extract, 5; (NH4)3PO4, 7.8]; SYH [sucrose, 50; Yeast hydrolysate, 5; (NH4)2SO4, 11.3; K2HPO4, 23.4; MgSO4 7H2O, 6.3 and CaCl2 2H2O, 0.1]; MYH [Molasses, 55; Yeast hydrolysate, 5; K2HPO4, 20; MgSO4 7H2O, 4.7]. The pH of all media was adjusted to 5.5. As inoculum, one percent (v/v) of a 24-h-old yeast cells grown in the basal medium described by Martínez et al., (2014) was used. Vitamins and traces were prepared and added as recommended Martínez et al., (2014), and they were only used in sucrose media because molasses provides vitamins and trace elements (Xu et al., 2015).
Flasks were incubated at 28ºC with shaking at 250 rpm for 48 h. Cells were harvested by centrifugation at 5000 rpm for 10 min to determine dry weight and BfrA activity.
2.5 Fed-batch fermentation in 7.5 L and 42 L fermenters
Fed-batch fermentation was performed in a 7.5-L fermenter (INFORS) as described Martínez et al., (2014). The fermenter contained 3 L of SYE or MYH medium and was inoculated with 0.2 L of a shaking batch culture to an initial cell concentration of 3 g/L (wet biomass). The feeding medium [50.0 % (w/v) raw cane sugar or 46.3% (w/v) molasses] was added at a constant flow rate of 7 mL/h/L of initial volume. The P pastoris BfrA4X culture was scaled up from the 7.5-L scale to the 42-L fermenter (INFORS) in the MYH medium. Fermentation conditions were as follows: temperature 28°C; pH 5.5. Inoculation and feeding were performed as in the previous scale. The fermenter was operated at 0.4 MPa and the aeration was 0.42 vvm for both, the batch and fed-batch phases. According to the calculations described on 2.6 the agitation was adjusted from 327 to 589 rpm, for the batch and fed-batch phases, respectively. The culture supernatant and biomass were harvested by centrifugation and used for the determination of BfrA activity.
2.6 Scale-up experiments
The scale-up was based on a constant volumetric mass transfer coefficient (k L a). The k L a in the 7.5-L bioreactor was determined using the dynamic method (Damiani et al., 2014). The mass balance for the dissolved oxygen (DO) in the assumed well mixed liquid phase can be written as the following equation:
The temporal changes of oxygen concentration are influenced by the k L a, maximum solubility of oxygen (C ∗ L ), actual oxygen concentration (C L ), specific oxygen uptake rate ( Q O 2 ), and viable cell concentration (X).
The dynamic method was used to determine both the oxygen uptake rate and k L a at one instant during the fermentation. By plotting CL versus time, the DO behavior was obtained, due to the respiration of the cell culture the first phase is usually a straight line and its slope provides an estimate of the oxygen uptake rate ( 𝑄 𝑂 2 𝑋). Before the DO reached its critical value, the air was reintroduced into the bioreactor and agitation was resumed. The oxygen uptake rate could then be estimated and the value of k L a determined from the rate of change of the DO up to its stationary value. k L a was calculated by rearranging Equation 2.
Therefore, K L a was determined from the slope of C L versus dC L /dt obtained graphically from Equation 2. It is worth noting that the estimation of k L a does not depend on the quality of the estimation of the value of 𝑄 𝑂 2 𝑋, obtained in the first step. Initially, k L a was estimated in the 7.5-L fermenter at three agitation speeds (500, 650 y 900 rpm) and two aeration rates (1 and 2 vvm) at different growth stages. DO concentration was monitored on-line. Since the experimental kLa values are between 20-40% of the values obtained with the correlation shown in Equation 3 (Van’t, 1979), it was selected among the correlations reported in the literature, since this accuracy is considered acceptable (Van’t, 1979).
Where: P g represents the gassing power of the impeller motor (W), V is the volume of the broth (m3) and v s is the superficial gas velocity (m/s). Sometimes, additional terms are added to include the effect of the apparent viscosity of the medium. The coefficient values α (0.4), β (0.5) and γ (0.026) have been found to depend on the type of bioreactor, the agitation used, the range of mixing intensity and the nature of the medium (Patel et al., 2004).
Applying the constant volumetric mass transfer coefficient scale-up criteria, the following correlation can be proposed:
Substituting Equation 3 into equality (4) and then substituting the equations corresponding to the variables P g , V and v s for each bioreactor and performing the necessary mathematical operations, we arrive to expression (5). In this study, it was used to determine the impeller speed (N) (Equation 5), the constant gas flow number (NQ) was analyzed to determine the air flow rate (Qa) using the Equation 6 and the geometric correction factor (fc) was determined by Equation 7.
Where N is the number of impellers, n i is the rotational speed (rpm); d i is the impeller diameter (m); H is the height of liquid (m), D is the vessel diameter (m), the sub-indices M and P refer to the model 7.5 and prototype 42-L fermenters, respectively. The calculations were based on the following geometric dimensions. Working volume (L) of M 5 P 30; DM 0.15, DP 0.267; d iM 0.054, d iP 0.089; HM 0.3136, HP 0.5341; NM 2 NP 3; fcM 1.339; fcP 1.414. Both the M and P with Rushton turbine Impellers.
2.7 Enzyme assays and statistical analysis
Enzyme activity in the culture supernatants or biomass samples was conducted as described by Martínez et al., (2014). One unit of BfrA is defined as the amount of enzyme that releases one µmol of fructose or glucose per minute, under the above-mentioned reaction conditions. Significant differences between treatments were determined by fully randomized ANOVA. The Statistical Package for Social Sciences (SPSS) 15.0 was used for the data analysis. Data are presented as the means ± S.D. The significance level used in this study was P<0.05.
3. RESULTS AND DISCUSSION
3.1 Growth of P. pastoris BfrA4X in shake flasks culture with different carbon and nitrogen sources
To study the feasibility of using low-cost substrates for the BfrA production, four media based on the combination of sucrose (raw cane sugar) or molasses and yeast extract or yeast hydrolysate, were evaluated in shake flasks as an alternative to the minimal medium with refined sugar, as proposed previously (Martínez et al., 2014). The compositions of sucrose, molasses, yeast extract and yeast hydrolysate were varied to maintain a similar initial concentration of each macro element in the four culture media.
The substitution of sucrose and yeast extract by molasses and yeast hydrolysate resulted in a similar biomass dry weight (Table 1). However, in the SYH and MYE the enzyme expression in was lower than that of BfrA expressed in SYE and MYH (Table 1). The combination of sugarcane molasses as carbon source and yeast hydrolysate as nitrogen source resulted in the highest BfrA expression and productivity. Sugarcane molasses contains sucrose, glucose and fructose. An additional amount of glucose could be released by the hydrolytic action of periplasmic and extracellular BfrA during cell growth. The BfrA expression is under the GAP promoter, although constitutive, is known to behave more strongly in glucose-grown cells (Cereghino & Cregg, 2000), therefore the continuous availability of glucose could have enhanced the transgene transcription (Pérez et al., 2021). Thus, substituting refined sugar for molasses or raw cane sugar as a carbon source will provide a cost-effective medium for large-scale BfrA production.
Table 1 . Comparison of the production of invertase and biomass in the four evaluated culture media
|
|
||
SYE | 11 ± 2 | 6.5 ± 1.0 | 0.012 |
SYH | 10 ± 3 | 0.8 ± 0.2 | 0.002 |
MYE | 11 ± 1 | 4.2 ± 0.8 | 0.008 |
MYH | 9 ± 2 | 8.3 ± 0.6 | 0.019 |
3.2 BfrA production by fed-batch fermentation in a 7.5-L fermenter
Pichia pastoris strain BfrA4X, which constitutively expresses Thermotoga maritime BfrA was cultured using a fed-batch strategy, using SYE and MYH media. The feed phase was started after the initial carbon source was almost consumed after 20 h of cultivation, as indicated by the spike in the DO. A linear feed flow rate was used as was previously reported (Martínez et al., 2014), it allowed to maintain the total reducing sugars around 2 g/L (data not shown).
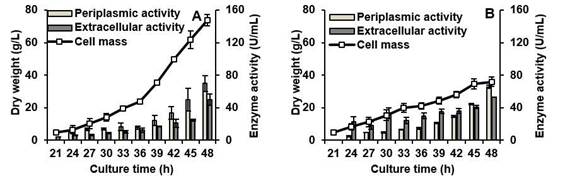
Figure 1 . BfrA production by recombinant Pichia pastoris strain BfrA4Xat 7.5-L fed-batch fermentation with SYE medium (A) and MYH medium (B). Values represent means ± standard deviations of three fermentations
After 48 h of culture significant differences (F=211.894, p≤0.000) were obtained between the dry biomass reached in SYE (74.0 g/L) and MYH (35.8 g/L). The growth difference could be caused by the inhibition of the cell growth because of impurities (ashes, sodium chloride, etc.) present in the molasses added in the diet. DO levels and the concentration of reducing sugars such as glucose are also factors that influence both cell growth and the mechanisms of synthesis and secretion (Ahmad et al., 2014). However, at the end of the cultures, regardless of carbon and nitrogen sources, no significant differences were observed for periplasmic activity (F=1.124, p=0.349) and extracellular activity (F=0.521, p=0.511) (Figure 1). The sum of the invertase activities in the undisturbed biomass and the culture supernatant provides an overall BfrA yield of 120 ± 7 U and 118 ± 1 U per mL of fermentation culture for the SYE and MYH media, respectively. In SYE 41.7% of the invertase was secreted into the culture medium compared to 44.6% that was secreted in the MYH medium. The MYH medium yielded 2-fold lower dry biomass compared with the SYE medium, then 1.25 fold more BfrA as free enzyme could be obtained per liter of fermentation culture in MYH. Therefore, the MYH medium was selected to scale-up the BfrA production.
3.3 Scale-up of BfrA production by fed-batch fermentation in 42-L fermenter
Three replicates of the experiments were conducted to examine the effects of cellular dry weight on k L a for the system with P. pastoris BfrA4X system in the 7.5-L fermenter. Three different cellular dry weights were studied, which were 1.9, 10.6 and 28.0 g/L. The oxygen uptake rate was determined from the depletion in the DO concentration after stopping the air flow, in each condition. The estimated values of k L a in the 7.5-L fermenter at different times, stirrer speed, aeration rate and stage of yeast growth are shown on Table 2.
The scale-up equations 5 and 6 were applied in order to determine the minimum and the maximum values of the operating variables (impeller speeds and air flow rates) to maintain the values of the mass transfer coefficients values (k L a) between 0.6227 and 2.1042 min-1 in the 42-L fermenter when scale-up on a basis of constant k L a from 7.5 L to 42 L bioreactor.
Table 2 . k L a estimation in the 7.5-L fermenter at different conditions
k
|
|||||
---|---|---|---|---|---|
1 | 6 | 500 | 1 | 1.9 ± 0.4 | 0.6227 |
2 | 24 | 650 | 1 | 10.6 ± 0.9 | 1.0133 |
3 | 32 | 900 | 2 | 28.0 ± 1.9 | 2.1042 |
Finally, using the above calculated values, the pilot bioreactor was operated at an agitation rate between 327 and 589 rpm while the air flow rate was maintained at 0.42 vvm. At 42-L was obtained higher cell mass (48.1 ± 3.2 g/L) and showed significant differences (F=26.766, p=0.007) with respect to the lower scale, probably the physiological conditions of the starting inoculum allowed to reach a higher dry weight from the beginning of the culture. As consequence, since the enzyme is constitutively expressed and associated with growth, significant differences were obtained with respect to the periplasmic enzyme activity (F=39.650, p=0.03) and extracellular enzyme activity (F=13.014, p=0.023), corresponding to 100.0 ± 9.8 U/mL and 67.3 ± 6.8 U/mL, respectively (Figure 2). Of the total BfrA activity, 167 U per mL of fermentation culture, 40.1% could be recovered as free invertase in the culture supernatant.
4. CONCLUSIONS
This study demonstrates the feasibility of using molasses and yeast hydrolysate to develop a cost-effective medium for the scale-up of the fermentation process to produce BfrA enzyme from the recombinant P. pastoris BfrA4x.
Once the culture was scaled up based on a constant k L a, the operating conditions were sufficient enough to provide the oxygen requirements of the culture.
A positive effect on the total BfrA yield was observed at pilot scale, compared with the yield value obtained at laboratory scale.