Introducción
En la formación del Producto Interno Bruto de cualquier país, la transportación de carga por carretera es una fuente apreciable de generación de riquezas. En la Unión Europea, por ejemplo, soporta el trabajo directo de casi diez millones de personas y supone cerca del 5 % de ese indicador. Un problema de las flotas de transporte terrestre es no disponer de la capacidad logística suficiente para sostener en el tiempo, la creciente demanda exigida por los esquemas productivos. Entre las múltiples causas de esta situación, se destaca la escasa utilización de herramientas de evaluación integrales.
Como tendencia, en el mundo se opta por el reemplazo de las flotas antes de que éstas lleguen al deterioro técnico. En el caso de la entidad objeto de estudio, imposibilitada de hacerlo, no dispone de métodos o procedimientos que faciliten la evaluación integral de los sistemas de gestión del mantenimiento y permitan implementar acciones de mejoras de manera oportuna. Ante el detrimento de los indicadores técnicos, económicos y operacionales, existe poca claridad en las acciones para evitar y revertir la situación.
El escenario actual caracterizado por los limitados recursos, los escasos repuestos e insumos, impone como estrategia de reparación el reacondicionamiento de las partes y piezas defectuosas, en lugar de la sustitución por nuevas. Por otra parte, la renovación no se realiza bajo criterios de recurso consumido (kilómetros recorridos), sino que se trabaja hasta el estado límite o de fallo.
Un programa de gestión del mantenimiento basado en la confiabilidad, es un sistema de monitoreo estadístico que ofrece reportes relacionados con el estado técnico de un determinado tipo de medios productivos (en el caso de análisis, de los medios de transporte). Teniendo en consideración que los operadores de flotas de vehículos realizan sus funciones adecuándose a las características específicas del medio de transporte, las variables de medición y control de cada tipo de flota serán, por lo tanto, específicas.
En [1] se propone un sistema que vincula diferentes estrategias de mantenimiento. Se fundamenta en la determinación de la probabilidad de ocurrencia de fallos empleando herramientas de análisis, listas de chequeo y programación de tareas, sin embargo, no muestra cómo llegar a ellas y se sostiene en escasas variables.
Por su parte, [2] resalta algunos problemas presentes en los programas de confiabilidad para el mantenimiento en pequeñas flotas. Se enfoca solamente en el procesamiento estadístico, pero no define indicadores relacionados con el estado técnico. Para [3], la propuesta se sostiene en modelos para predecir la confiabilidad del mantenimiento de sistemas técnicos complejos, basados en las cadenas de Markov y las redes bayesianas, la propuesta se evalúa mediante simulaciones, en un escenario teórico, distante de una aplicación práctica.
En un estudio realizado por Ballester-Bauset et al.[5] propone para las flotas de transporte, incrementar el mantenimiento predictivo y la disminución del mantenimiento correctivo con propuestas que en la actualidad se consideran elementales en el mantenimiento preventivo. Por su parte, Arnaiz [6] propone un modelo para evaluar la función mantenimiento empleando herramientas que ayuden a mejorar la efectividad de los costos, enfocado en su estimación. Mientras que Seyr-Muskulus [7], consideran una revisión del estado del arte de los tipos de modelos de mantenimiento para aerogeneradores, teniendo en cuenta una amplia variedad de variables con influencia en otras esferas, en las que incluye también operacionales. Tiene una alta dosis didáctica, aunque no llega a mostrar modelo teórico o práctico alguno.
Díaz [8] propone un procedimiento para diseñar una encuesta para analizar, estimar, el estado de gestión del manteamiento en plantas de producción de bioproductos con la limitación de no incluir propuestas de mejora con los resultados obtenidos. Viveros [9] en su investigación, propone un modelo de gestión del mantenimiento al que le aporta el ingrediente de mejora continua, introduciendo dos nuevos procesos, emplea varios métodos o herramientas modernas, definiendo el costo global como indicador clave para la toma de decisiones, aunque queda pendiente su aplicación práctica.
Para autores como Muganyi y Mbohwa [10], los modelos de gestión del mantenimiento se enfocan desde una perspectiva gerencial, donde los sistemas de medición de variables están en función del mantenimiento y deben utilizarse en la toma de decisiones de manera sistemática, para aprovechar el alto valor que poseen. Los autores no esclarecen el alcance de las variables, ni cómo calcularlas. Una de las variables utilizadas para evaluar la función mantenimiento es la fiabilidad, que está relacionada con la frecuencia de ocurrencia de los fallos. Esta resulta insuficiente y parcializada, pues no evalúa el costo ni el impacto de los fallos.
Penabad-Sanz et al.[11] muestran que, en Cuba, las flotas de transporte, fundamentalmente, utilizan el CDT (Coeficiente de Disponibilidad Técnica) y recomiendan prestarle mayor atención al indicador de disponibilidad técnica, debido a que está asociado al plan de transportación para satisfacer las demandas, algo que puede ser útil para los que renuevan las flotas constantemente.
Parida et al. [12] hace una revisión de la literatura hacia los indicadores y marcos de trabajo que miden el desempeño de la función mantenimiento, resaltan la importancia en los estudios de los parámetros de Fiabilidad, Disponibilidad, Mantenibilidad y Seguridad (RAMS, Reliability, Availability and Maintainability), Análisis del Costo del Ciclo de Vida (LCC, Life Cycle Costing), el Benchmarking y el e-Maintenance, para la toma correcta de decisiones aunque no presenta ningún modelo o ejemplo de aplicación.
Muchiri et al. [13] sostienen que los indicadores de mantenimiento deben vincularse a los indicadores de producción. Los autores proponen el marco conceptual para seleccionar indicadores que evalúan el desempeño de la función mantenimiento, clasificándolos en dos grupos: los que miden el desempeño del equipamiento y los que evalúan el rendimiento y los costos, la limitante estaría en dejar abierta y general la propuesta, sin una definición específica para su implementación.
Penabad-Sanz et al.[14] amplía su aporte al incorporar la disponibilidad límite, vinculada al desempeño económico. Estos métodos necesitan de un sistema de equipos y medios para realizar el diagnóstico y el registro de la información, que permitan determinar indicadores, coeficientes y tendencias. A la vez, resultan complejos de integrar para ser aplicados en la práctica diaria por los especialistas y directivos del transporte.
En la literatura científica, se observan claramente los diferentes métodos y herramientas para evaluar la función mantenimiento en distintos campos, sin embargo, una propuesta práctica, aplicable a una flota de vehículos de transporte de carga no queda definida con la mayor claridad. Esta brecha del conocimiento permite proponer un procedimiento propio.
Tomando en consideración el análisis anterior, este artículo tiene como objetivo evaluar la función mantenimiento en una flota de transporte de carga en un escenario de recursos limitados. El procedimiento considera la información técnica, de operación vigente, el capital humano y los recursos tecnológicos disponibles en la entidad. El análisis bibliográfico, la modelación y el empleo de herramientas de fiabilidad y la estadística, permitieron integrar los indicadores asociados a la fiabilidad, disponibilidad, y costos por mantenimiento, para evaluar el rendimiento por líneas de vehículos.
Métodos y Materiales
Se tomó como unidad investigativa una flota de vehículos para el transporte de carga por carretera que brinda los servicios de transportación de combustibles y sus derivados en volúmenes aproximados de 280 mil metros cúbicos, con un recorrido cercano a los 1,8 millones de kilómetros anuales. Se utilizaron métodos estadísticos, el análisis y síntesis, la modelación teórica, el análisis sistémico del proceso de mantenimiento, así como el empleo de indicadores de la confiabilidad.
Se analizó la información correspondiente al año 2017, referente a la línea Hyundai con un parque de 73 vehículos. La información primaria se obtiene de registros y documentos primarios empleados por los grupos de Control de la Flota de Transporte, Operaciones y Técnicos. En la entidad los procesos fundamentales se encuentran certificados por la Norma Cubana NC-ISO 9001:2015.
La fuente de los datos procede de 3 915 órdenes de trabajo, 10 365 hojas de rutas, 11 mil lecturas de chips de consumo de combustibles. El conjunto de datos analizados, utilizando el Microsoft Excel, permitió procesar y obtener diferentes indicadores, variables y parámetros. Entre estos se encuentran el kilometraje recorrido por cada equipo, las horas trabajadas, los metros cúbicos de combustible transportados, el tiempo en taller por mantenimiento planificado o correctivo, el gasto en materiales, mano de obra, número de fallos (3 171) clasificados por sistemas, subsistemas y componentes, entre otros. La aplicación del procedimiento se evalúa mediante los indicadores RAMS.
Procedimiento para la evaluación de la función mantenimiento
a) Evaluación del mantenimiento
El procedimiento propuesto busca satisfacer la necesidad de evaluar y mejorar el funcionamiento del sistema de mantenimiento en el contexto vigente. La evaluación de la función mantenimiento se basa en la información obtenida al procesar los datos relacionados con la transportación y el mantenimiento. Además, la información complementaria del sistema de gestión, control de la flota de vehículos, indicadores económicos y de capital humano, acogidos al Sistema de Gestión de la Calidad, certificados por la norma NC-ISO 9001: 2015. Toda esta compilación de la propuesta empleando el conocimiento del personal de mantenimiento, expertos, del Grupo de Ingeniería, operarios (mantenedores) y la Gerencia; en una interrelación sinérgica; permite identificar las acciones, medidas, tareas, que modifican la manera de hacer actual, figura 1, A
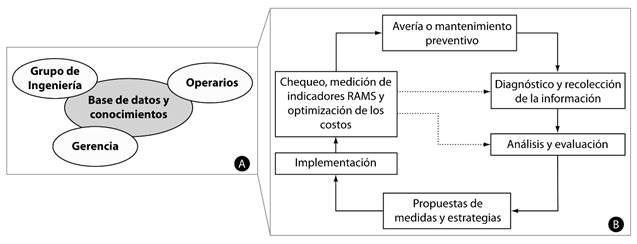
Fig. 1 Variables genéricas de evaluación del mantenimiento (A) y de mejora continua para evaluar el mantenimiento (B).
La evaluación del mantenimiento, de manera sistemática se somete a una mejora continua, que utiliza algunos principios del ciclo de Deming, figura 1, B, que incluye un conjunto de pasos que se describen a continuación:
Avería o mantenimiento preventivo: recoge el ingreso por fallos inesperados o por alguna acción de mantenimiento preventivo.
Diagnóstico: recolección de información: ingresa la información del diagnóstico, defecta, registra la lectura de los parámetros técnicos, calcula las variables, y define los problemas. Se considera, junto a los pasos siguientes, 3 y 4, acciones de "Planificación" propios del Ciclo de Deming.
Análisis y evaluación (de la información): se interpreta y compara con la información técnica del fabricante y los datos históricos. Se emplean herramientas de confiabilidad, Análisis de Modos y Efectos de Fallos (AMEF), Análisis Causa Raíz (ACR), etc. Se ejecuta el benchmarking. Se determinan relaciones causales, elementos críticos y medidas técnicas más efectivas. Se crean grupos de colaboración para desarrollar el trabajo integral que permitan mejoras.
Propuestas de medidas y estrategias: son actualizados los procedimientos y técnicas de mantenimiento.
Implementación: se capacita al personal, se motiva y compromete; se aplican e implementan las acciones de mejoras. Se considera una acción de “Hacer”.
Chequeo, medición de indicadores de Fiabilidad, Disponibilidad, Mantenibilidad y Seguridad (RAMS) y optimización de los costos: se evalúa el comportamiento de los indicadores, así como los costos por tipos de mantenimiento. Se considera una acción de “Verificación”.
Se cierra el Ciclo de Deming, “Actuando”, debido a que los resultados del paso 6 son reevaluados y enviados al paso 2 o 3 según correspondan.
b) Procedimiento para evaluar la función de mantenimiento
En la figura 2 se muestra el algoritmo de trabajo que permite aplicar el procedimiento para evaluar la función de mantenimiento, la entrada al mismo proviene de una acción de mantenimiento preventiva o correctiva. En él se integran los diferentes actores: la gerencia, el grupo de ingeniería y el personal de mantenimiento y operación, quienes realizan la evaluación sistemática; y se apoyan en métodos, indicadores y herramientas. La gerencia estableció un sistema de Mantenimiento Preventivo Planificado (MPP), históricamente aplicado, que se somete a la evaluación y mejora. El grupo de ingeniería procesa la base de datos de registros y con la información logra el monitoreo de los indicadores, la evalúa, analiza el desempeño y emite propuestas, indicaciones, para que el grupo de gerencia avale y el de operarios (mantenedores) implemente, este último grupo también aporta experiencias, conocimientos prácticos en una relación sinérgica.
Se calculan los indicadores RAMS; así como también otros indicadores clásicos, tales como: la probabilidad de trabajo con fallo (Q(t)) y sin fallo (P(t)), el flujo de fallos (W(t)) y los costos. Según corresponda, se aplican otros métodos para evaluar la fiabilidad, como son: el ACR, el Análisis de Criticidad, el AMEF y el LCC, para actualizar y comparar (Benchmarking). Esto permite evaluar el desempeño de la función mantenimiento y proponer medidas técnicas-organizativas que favorezcan el proceso. Esta etapa se explica detalladamente en el próximo acápite.
La toma de decisiones sistemática a nivel de gerencia se sustenta en indicadores que justifican, por ejemplo, invertir en capacitación para mejorar las competencias y habilidades del personal de mantenimiento y operarios; o definir qué activos, sistemas y partes requieren ser jerarquizados para la compra, de acuerdo a su criticidad. También, se controla los requerimientos medio ambientales, de riesgos y seguridad. Con ello se logra que el mantenimiento sea un proceso que de manera dinámica incida en la rentabilidad y eficiencia de la entidad.
c) Análisis y procesamiento de la información
La información se procesa por métodos estadísticos y se clasifica, con el objetivo de obtener los indicadores necesarios para evaluar la función de mantenimiento; posteriormente se identifican los sistemas, subsistemas y componentes críticos fundamentales que afectan el parque de vehículos y la causa de los fallos. Finalmente se definen las tareas específicas que favorecen la efectividad del mantenimiento.
Se calculan los indicadores asociados a la operatividad, durabilidad, conservabilidad y mantenibilidad de los equipos industriales según la Norma Cubana NC 92-31:1981. Se utilizan diversos indicadores que describen con mayor integralidad la función de mantenimiento. A nivel teórico, la ecuación 1 y la ecuación 2 predicen la probabilidad de trabajar sin fallos o de que ocurran. Un indicador muy útil e importante para medir la fiabilidad y realizar el análisis causal es el flujo de fallos, representado en la ecuación 3 en un intervalo de tiempo. La ecuación 4 es recomendada para medir la operatividad, fiabilidad, en artículos reparables.
Donde: t, b y k son coeficientes.
Donde:
N |
es el número de artículos que han fallado |
n |
es el número de artículos que se ensayan |
Δt |
es el intervalo de tiempo considerado |
Donde:
TMEF |
es el tiempo medio entre fallos |
NOIT |
es el número de artículos ensayados |
HROP |
son las horas totales en operación |
NTMC |
es el número total de mantenimientos correctivos |
Como alternativa para los equipos de flotas de transporte, es usual utilizar la distancia recorrida por las horas en operaciones. Se obtiene, por tanto, la distancia media recorrida a la que se presenta el fallo, o sea, el Kilómetro Medio Entre Fallos (KMEF). El indicador Tiempo Medio para Reparar (TMPR), como se muestra en la ecuación 5, es uno de los más difundidos para medir la mantenibilidad y obtiene su valor teniendo en cuenta únicamente el tiempo en el mantenimiento correctivo. Depende de las horas totales en mantenimiento correctivo (HTMC) y del Número Total de mantenimientos correctivos (NTMC).
Clasificado como un índice complejo, el CDT, como muestra la ecuación 6, en las flotas de transporte se utiliza con regularidad para evaluar la disponibilidad física. Tiene como inconveniente que considera el tiempo de parada por otras causas que con frecuencia son significativas, por ejemplo, el de espera de piezas o aseguramientos por la logística, pero cuantifica el porciento del medio disponible para ser utilizado. Depende del tiempo calendario total medido (TTM) y del tiempo total en el taller en operaciones de mantenimiento preventivo y correctivo (TTT).
Resultados y Discusión
a) Selección de la línea de vehículos crítica
Para el estudio se seleccionó la línea de transporte Hyundai, que representa el 57,1 % de este tipo de vehículos comerciales. Constituye un mismo tipo de marca de vehículo, con algunas características comunes en cuanto a la función que cumplen, referentes a los tipos de motores y sistemas de frenos instalados, las tecnologías, etc. Tienen una gran importancia económica y social por encargarse de transportar a los clientes, los cilindros de gas licuado del petróleo. Este grupo de medios tiene, además, muy pobres resultados de disponibilidad (56,1 %), el índice de Mantenimiento Correctivo (IMC) es de 82,61 %, la fiabilidad muestra que fallan cada 1 138 km recorridos y, por su parte, el Índice de Relación de Mantenimientos (IRM) es apenas del 33,8 %.
b) Cálculo de los indicadores en la línea de vehículos Hyundai
La figura 3 refleja la inestabilidad de esta línea de vehículos y su alta frecuencia de fallos en largos periodos de tiempo.
Esta concentración de fallos (Fig. 4) provoca elevados gastos en las actividades de mantenimiento correctivo, observándose que llega hasta el 55,6 %, superior al mantenimiento preventivo, que evidentemente tiene baja efectividad.
La aplicación conjugada del principio de Pareto (Fig. 5), a partir de la frecuencia de fallos por sistemas y la determinación del flujo de fallos W(t) (Fig. 6), permite definir que la mayor concentración ocurre en los sistemas: motor, eléctrico, ruedas y frenos, casi el 70 %. De esta manera se facilita el análisis para identificar los elementos críticos e influyentes en la baja fiabilidad-disponibilidad alcanzada, sus causas y las medidas más efectivas a adoptar.
El mismo análisis se realiza hacia los sistemas y/o subsistemas, permitiendo definir que en el sistema motor, figura 7, un 61 % de los fallos se ubican en el subsistema de alimentación, y de ellos el 72,7 % se concentra en obstrucciones en los filtros, tuberías o mangueras conductoras.
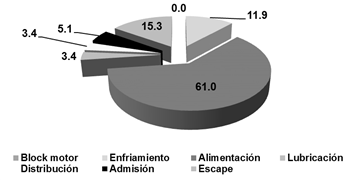
Fig. 7 Por ciento de fallos en componentes del sistema motor en los equipos Hyundai en 2017.
Un análisis similar a la figura 7 aplicado al sistema eléctrico, posibilita identificar el 40 % de las averías en cambios de bombillas o lámparas y un 23,6 % en el cableado. De igual manera, para los dos restantes sistemas más influyentes; en el sistema ruedas el 67,5 % ocurren por ponches o roturas de neumáticos en su banda de rodamiento, deterioro irregular, abrasivo, cortes laterales o grietas en sus pestañas, con un acortamiento considerable de su vida útil. Para el sistema de frenos, se define el 88 % de los fallos en los cilindros de freno, válvulas de accionamiento, bomba, hidroback o servofreno; forros y zapatas de freno, tuberías y mangueras.
c) Cálculo de los indicadores en los componentes críticos de los sistemas analizados
La tabla 1 resume los gastos por materiales y por mano de obra por estas averías, el tiempo en el taller y el TMPR en los componentes críticos. Se observan por una parte los sistemas con una mayor incidencia desde el punto de vista económico por el valor de los componentes o la mano de obra y, por otra parte, se observan los sistemas desde el punto de vista de la inestabilidad diaria, lo que propician la frecuencia de fallos en el proceso de transportación.
Tabla 1 Gastos y tiempo de los fallos de los componentes más críticos de la línea Hyundai. Fuente: autores
Ítem | Sistema | Componentes o partes que fallan | Gastos por averías ($) | % de gastos | Tiempo en taller (h:m:s) | TMPR (h:m:s) |
---|---|---|---|---|---|---|
1 | Alimentación | Tuberías | 357,32 | 1,5 | 18:12:30 | 1:31:02 |
2 | Alimentación | Filtros | 527,11 | 2,2 | 63:10:20 | 4:30:44 |
3 | Eléctrico | Luces | 2 124,89 | 8,9 | 396:05:00 | 18:00:14 |
4 | Eléctrico | Cableado | 532,57 | 2,2 | 133:35:00 | 10:16:32 |
5 | Frenos | Cilindro de freno | 4 474,51 | 18,7 | 693:27:30 | 34:40:23 |
6 | Ruedas | Neumáticos | 5 488,45 | 23,0 | 326:30:00 | 12:05:33 |
Resumen | 13 504,85 | 56,5 | 1 631:00:20 | 15:06:07 |
d) Definición de las acciones técnicas preventivas
El análisis de los indicadores calculados permitió identificar para la línea de vehículos Hyundai, aquellos sistemas, subsistemas, componentes y partes críticas; así como su incidencia, los modos de fallos, sus causas objetivas, subjetivas. Con estos fundamentos se diseñaron un grupo de tareas preventivas, tabla 2, que ayudan a reducirlas o eliminarlas. En todos los casos es efectivo capacitar al personal en las buenas prácticas; así como el manejo de la carta de fallos y soluciones.
Tabla 2 Modos de fallo y medidas preventivas de mejoras para la línea Hyundai. Fuente: autores
No | Sistema | Componentes | Modo de fallo | Medidas preventivas |
---|---|---|---|---|
1 | Alimentación | Filtro, conexiones y tuberías | Restricciones en el flujo de combustible y caída de su presión |
Incluir en la primera operación de mantenimiento (12 000 km), la succión del combustible del depósito y su limpieza con auxilio del filtro interceptor y la bomba de reciclado externa, así como la limpieza de la parte primaria de la línea de conducción. Comprobar la estanquidad y el desgaste de las conexiones y tuberías. Eliminar las torceduras, las curvas cerradas o estrangulamientos. Revisar las fijaciones y la rigidez de las tuberías. |
2 | Iluminación | Lámparas, focos, bombillas y cables | Carencia o falta de iluminación y alimentación eléctrica |
Utilizar conectores, contactos, cables y bombillas adecuadas para las reparaciones (según catálogo de piezas). Emplear y fijar adecuadamente los conectores, los contactos o terminales para el cableado según la carta tecnológica. |
3 | Frenos | Cilindros de frenos | Pérdida de líquido hidráulico, deterioro de los sellos y las juntas. Ineficiencia del frenado |
Emplear las partes de cilindros originales. Limpiar las conexiones, las tuberías y los cilindros antes del desarme, para evitar la entrada de suciedad o eliminar la que ya tienen. Reparar o cambiar los cilindros de los frenos, presurizar y purgar el sistema. Emplear siempre el líquido hidráulico nuevo y limpio de un envase cerrado, que cumpla con las especificaciones recomendadas. Evitar que absorba la humedad del aire. |
4 | Ruedas | Neumáticos | Ponches y roturas frecuentes, desgaste acelerado |
Chequear la presión de inflado de diseño cada cuatro días calendario. Incluir en la segunda operación de mantenimiento (48 000 km), la rotación posicional de los neumáticos y la comprobación de la convergencia de las ruedas direccionales. Emplear herramientas y materiales adecuados en el arme y desarme de los neumáticos. |
e) Definición de las necesidades de partes y piezas críticas
Desde el punto de vista logístico, tabla 3, se determinaron las necesidades de partes y piezas críticas (cantidades mínimas necesarias).
Tabla 3 Partes y piezas críticas en la línea Hyundai. Fuente: autores
No | Sistema: | Componente, parte, pieza o material: | Código de pieza: | Cantidad y UM |
---|---|---|---|---|
1 | Alimentación | Filtro interceptor o bomba de reciclado de combustible | IN FDW 51125 de 25 micras | 4 u |
Elemento filtro RACOR | 2020TM-OR | 80 u | ||
2 | Iluminación | Bombilla chica del farol de carretera, bombilla de un polo | 18653-05009, 18652-12003, 18652-21008 | 150 u |
Kit de reparación de arnés y cables | 18652-25008 | 3 kit | ||
Kit de reparación de arnés y cables | 3162899 | 10 kit | ||
3 | Frenos | Cilindros de freno | 58350-62003, 58430-62003 y 58450-6200 | 8 u |
Líquido de freno con parámetros técnicos adecuados | ---- | 130 L | ||
4 | Rodaje Pasta universal para montaje de neumáticos Remaxx | 593 0625 | 120 Kg |
En el período del 2018- 2020 en un escenario de recursos limitados, que impiden la renovación de la flota y la adquisición oportuna de partes y piezas, la aplicación del procedimiento ha permitido que se sostengan los indicadores productivos, y se extienda el ciclo de vida del activo, evitando un incremento del deterioro de la disponibilidad y seguridad.
Conclusiones
Se desarrolló un procedimiento para la evaluación de la función de mantenimiento en una flota de transporte de carga por carretera, empleando su base de datos, el conocimiento, las herramientas adecuadas, y mediante una evaluación estratificada de los resultados. El procedimiento permite identificar equipos, sistemas, subsistemas y componentes críticos; además de cuantificar su afectación económica, fundamentar las acciones técnicas y de capacitación más efectivas, que se incorporan al sistema de mantenimiento. Se incluye la demanda de compras urgentes para las partes, piezas e insumos críticos.