INTRODUCCIÓN
En el desarrollo industrial y económico de cualquier país, la fundición desempeña un papel fundamental por su importancia en la producción de equipos y piezas de repuesto. Si se aspira a alcanzar o mantener un notable desarrollo industrial y económico no se puede prescindir de ella; esta es la razón por la que busca mejorar su eficiencia, rentabilidad económica y competitividad, a través de la aplicación de métodos y herramientas modernas como los softwares de simulación y las técnicas de Computer Assistance Design (CAD) (Chauhan, Anuvadiya y Chauhan 2017; Shankar-Kamble y Kadam 2016; Kyu-Jin, Yoon-Seo y Gil-Kang 2017 y Cheng-Yang et al. 2018) dirigidos a mejorar la eficiencia y el rendimiento a través de la optimización de todos los parámetros del proceso de fundición, incluyendo la aplicación de medios auxiliares.
La fundición es el método de producción de piezas de forma compleja más utilizado, obteniéndose un amplio grupo de piezas en cuanto a variedad de forma y peso. Además, es la forma más común de reciclar la chatarra de diferentes metales.
Ortiz-Prado, Ruiz-Cervantes y Ortiz-Valera (2018) señalan que, por sus características, la industria de la fundición de acero representa una importante fuente de emisión de contaminantes a la atmósfera, a lo que se suma su elevado consumo de energía. Esta situación ha incentivado la búsqueda y aplicación de soluciones que permitan cumplir con las regulaciones y normativas medioambientales implementadas a nivel internacional. Según Wlodawer (1966) y Breton (1965) el máximo aprovechamiento del acero fundido constituye un factor fundamental para aumentar la eficiencia metálica, la productividad y la rentabilidad económica del proceso de fundición de piezas de acero. De este modo también se logra reducir su incidencia medioambiental negativa.
Dada la repercusión que este aspecto tiene para el ahorro de energía eléctrica, materias primas y combustible, ha sido siempre un reto para los fundidores disminuir la cantidad de acero necesario en el molde para obtener la pieza sana (Breton 1965; Wlodawer 1966). Con este fin se utilizan medios auxiliares en diferentes partes de los moldes para dirigir la solidificación, tanto en la cavidad de la pieza como en la cavidad de las mazarotas o alimentadores, siendo los materiales más utilizados los exotérmicos e isotérmicos o termoaislantes en forma de mangas o casquillos.
Según Wlodawer (1966), Ruddle (1979) y Miller (1977) los casquillos o mangas se emplean para prolongar el tiempo de solidificación de las mazarotas, contribuyendo así a dirigir la solidificación hacia estas, permitiendo reducir su tamaño. Al-Shafe y Azadur-Rahman (2015) plantean que las mangas o casquillos para mazarotas son una herramienta bien establecida en todo el mundo para minimizar los costos asociados a la fundición y se estima que en el año 2013 alrededor del 80 % de todas las piezas fundidas de acero en el mundo fueron producidas utilizando estos materiales. Además, señalan que solamente la industria de la fundición de acero de Estados Unidos gasta treinta y ocho millones de dólares por año en mangas para mazarotas.
Schäfer y demás colaboradores (2017) abordan una mazarota para piezas de hierro nodular, compuesta por una manga exotérmica cubierta por otra termoaislante, que combina los efectos de uno y otro material optimizando la eficiencia metálica obtenida con respecto a las mangas puramente exotérmicas.
En las condiciones de Cuba, el costo de los casquillos o camisas exotérmicas y termoaislantes para fundición resulta elevado debido, fundamentalmente, a la imposibilidad de acceder a créditos comerciales, a los elevados gastos de transporte y a la dificultad de obtener contratos para un suministro estable de estos productos. Esto ha provocado la no aplicación de estos materiales en la industria de la fundición cubana.
En el caso particular de la empresa Planta Mecánica de Santa Clara el hecho de no utilizar materiales auxiliares repercute en una baja eficiencia metálica (< 50 %), debido al gran tamaño que requieren las mazarotas convencionales, que solo puede entregar hasta el 14 % de su volumen, lo que afecta también la calidad final de las piezas. Suárez-Lisca (2017) sitúa la eficiencia metálica de Planta Mecánica entre un 35 % y un 45 % atribuyéndolo, además de lo señalado, a la aplicación de un método de cálculo de mazarotas anticuado y obsoleto.
En Planta Mecánica fue establecido el empleo de la cáscara de arroz como material de cobertura sobre la superficie superior de las mazarotas de arena, después de investigarse los resultados reportados por Gerstman y Bruhr (1955) en su proceso de producción de piezas de acero.
Posteriormente, se ensayó la aplicación de una manga, camisa o casquillo isotérmico confeccionado con cáscara de arroz molida, para retener calor en la pared lateral de la mazarota cilíndrica, en combinación con una capa de cobertura de cáscara de arroz sin moler, llegando a extenderse su aplicación a más del 95 % de la producción de piezas fundidas de acero con un efecto significativamente positivo sobre los principales indicadores de eficiencia del proceso de fundición.
El presente trabajo tiene como objetivo exponer el efecto positivo para el medio ambiente y la economía de la utilización de la cáscara de arroz como material auxiliar en la fundición de piezas de acero.
MATERIALES Y MÉTODOS
Preparación del polvo de cobertura
En la función de polvo de cobertura se utiliza la cáscara generada durante el proceso de descascarado del arroz (Figura 1 A) sin procesos previos de preparación. Para esta aplicación, es tomada de la zona de almacenamiento y lanzada sobre el acero fundido en la cuchara de vertido, además, siguiendo un procedimiento similar es colocada sobre las mazarotas una vez terminado el vertido y llenado de cada molde. La cáscara de arroz al entrar en contacto con el acero fundido no produce emanaciones nocivas para la salud, al ocurrir de inmediato la ignición y eliminación de los gases generados por su pirólisis o combustión, como puede apreciarse en la Figura 1 B.
Al colocarse la cobertura sobre el acero en la cuchara de vertido, se reducen las pérdidas de calor durante el proceso de llenado de los moldes.
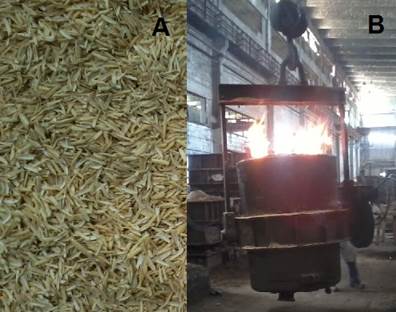
Figura 1 A: Cáscara de arroz utilizada como cobertura, B: Cuchara de vertido con la cobertura de cáscara de arroz en combustión.
Esto permite aumentar el tiempo disponible para realizar el llenado de cada molde con el sobrecalentamiento adecuado del acero, permitiendo ahorrar ladrillos refractarios al facilitar la limpieza posterior de la cuchara sin que queden capas solidificadas de acero adheridas al refractario que lo dañen al tener que retirarlo con lanza de oxígeno o medios mecánicos.
Con este objetivo se utilizaba como polvo de cobertura en la cuchara de vertido un granulado exotérmico importado de Polonia, el cual se sustituyó por cáscara de arroz a partir del año 1966. En esta aplicación la cáscara de arroz proporcionó resultados similares a los obtenidos con el producto importado.
Preparación de los casquillos
Los casquillos se confeccionan de 30 mm de espesor de pared para diámetros de mazarota desde 50 mm hasta 300 mm, con una altura de 150 mm para, con dos o tres de ellos, alcanzar la altura calculada de la mazarota en el molde.
Para su preparación, la cáscara de arroz se tritura, en un molino de martillos, hasta una composición granulométrica donde el 80 % quede retenido en tres tamices (de 0,4; 0,63 y 1 mm de diámetro). Posteriormente se mezcla con agua y silicato de sodio metalúrgico, con una densidad de 1,47 a 1,52 g/cm3 y una relación SiO2: Na2O, conocida también como módulo del silicato, entre 2 y 2,3; la cual define las características tecnológicas más apropiadas de este compuesto y sus potencialidades como aglutinante para las mezclas de moldeo (Cruz-Pérez 2009).
La mezcla se prepara en una proporción que permite alcanzar las características adecuadas para el moldeo del macho-casquillo y su curado con CO2. Para el moldeo o confección de los casquillos se utiliza un método similar al seguido por Al-Shafe y Azadur-Rahman (2015) e Idamayanti y otros investigadores (2020), en una caja de machos (Figura 2 A).
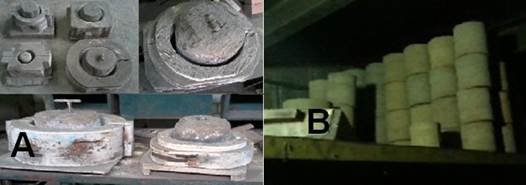
Figura 2 A: Cajas de macho para la confección de casquillos de cáscara de arroz, B: Local donde se almacenan los casquillos.
Finalmente se estufan a una temperatura de 120 °C durante 2 h (Cruz-Pérez 2012). Después del estufado, los casquillos se almacenan en un local con un ambiente de temperatura y humedad controlada para garantizar que estén totalmente secos en el momento de su inserción en los moldes de fundición (Figura 2 B).
En el proceso de moldeo, el macho casquillo se inserta en el lugar de la plantilla donde deberá estar la mazarota en un proceso de moldeo manual, pudiendo también adaptarse su aplicación a un proceso de moldeo mecanizado.
RESULTADOS Y DISCUSIÓN
Disponibilidad y características de la cáscara de arroz
El arroz es un cereal que se cultiva en todos los continentes, el cual durante su procesamiento genera como residuo la cáscara, formando verdaderas montañas en áreas próximas a los molinos. Según Olivier (2011) y Díaz-Pita (2011), la cáscara constituye aproximadamente el 20 % de la masa del grano, generándose anualmente en el mundo más de 100 000 000 t.
De las Pozas-del Río (2012) menciona que en Cuba se producen alrededor de 400 000 t de cáscara de arroz al año en el sector estatal y privado, de las cuales se aprovecha una ínfima parte en la economía nacional y el resto queda como residuo agrícola contaminante.
De acuerdo con Díaz-Pita (2011), la cáscara de arroz contiene materia orgánica, fundamentalmente celulosa, hemicelulosa y lignina, por lo que se considera un problema a solucionar al no ser biodegradable y constituir una carga contaminante para el medio ambiente, pese a esto, de este residuo solo el 5 % se está aprovechando.
También menciona que entre las propiedades físicas de la cáscara de arroz se destacan su densidad específica de 1,42 kg/m3, elevada porosidad y una conductividad térmica (K) de 0,03605 W/mK, lo que la convierte en un material termoaislante eficiente para la fundición. A pesar de esto su aplicación en esta industria no se ha extendido con la misma fuerza que en otras.
Olivier (2011) plantea que la cáscara de arroz no se quema con facilidad, es altamente resistente a la penetración de la humedad y a la descomposición por hongos, no transmite el calor muy fácilmente, no emite gases ni mal olor y no es corrosiva al contacto con el aluminio, el cobre y el acero; presenta de forma natural las propiedades requeridas para los materiales isotérmicos de aplicación industrial, clasificándose como material de clase A o clase I, por tanto, puede ser utilizada para termoaislar paredes, pisos y techos de casas.
Por otro lado, el empleo de la cáscara de arroz tiene las ventajas de ser de fácil manejo y procesamiento y no requerir de almacenes de alta seguridad, siendo posible almacenarla en cualquier espacio del taller de fundición.
Uso de la cáscara de arroz en Planta Mecánica
Además de usar la cáscara de arroz como cobertura en la cuchara de vertido, también se aplica sobre la superficie abierta de las mazarotas. Esto se ejecuta de manera aleatoria, sin tener en cuenta el espesor de cobertura adecuado (50 mm como promedio). A pesar de ello la concentración del rechupe en dicha superficie es notable (Figura 3), lo cual se debe al efecto termoaislante que produce su ceniza, que da como resultado la retención del calor que se perdería por radiación.
La retención del calor se atribuye a las propiedades de la cáscara de arroz como material termoaislante, debido al elevado contenido de sílice amorfa (más de 90 %), la elevada porosidad, baja densidad y área superficial específica de la ceniza resultante de la combustión de la cobertura sobre la mazarota a alta temperatura (Fernández et al. 2017).
La combustión de la cáscara de arroz al colocarla como cobertura sobre el acero a una temperatura sobre los 1 540 °C, en intercambio con el medio, en dos minutos como promedio, favorece su combustión completa mejorando las propiedades termoaislantes de la ceniza y su efectividad como material auxiliar para la fundición de piezas de acero.
La caracterización de muestras de ceniza de cáscara de arroz quemada a 1 350 °C, mediante técnicas de Fluorescencia de Rayos X (XRF por sus siglas en inglés), Energía Dispersiva de Rayos X (EDX por sus siglas en inglés), Difracción de Rayos X (XRD por sus siglas en inglés), entre otras (Fernández et al. 2017), demuestran la influencia de la temperatura de combustión en los contenidos de sílice y carbono, así como en el área superficial específica de dicha ceniza.
A medida que aumenta la temperatura de combustión y la presión parcial de oxígeno en el horno, en la ceniza resultante se eleva el contenido de sílice, disminuyendo el de carbono y el área superficial específica. De las Pozas-del Río (2012) le atribuye gran importancia a la influencia del régimen de combustión de la cáscara de arroz, específicamente a la temperatura y al tiempo, en determinadas propiedades de la ceniza.
En la década de 1990 se introdujeron los casquillos de cáscara de arroz, conjuntamente con la cáscara de arroz como cobertura, en la producción de piezas fundidas de acero de Planta Mecánica, con el objetivo de dirigir la solidificación hacia las mazarotas y, con ello, disminuir el consumo de metal. Su uso se extendió a una amplia gama de piezas, fundamentalmente de las industrias azucarera, del cemento y minera.
La implementación de esta alternativa de material auxiliar de alimentación redundó en un significativo aumento de la eficiencia metálica y de la calidad final de las piezas fundidas. Un estudio reciente dio un resultado similar al obtenido en análisis anteriores realizados en Planta Mecánica, y a los que se logran con materiales exotérmicos y termoaislantes comercializados en el mundo para este servicio.
En la Figura 4 se puede observar en la imagen A la diferencia de tamaño entre la mazarota convencional de la pieza situada a la izquierda y la situada a la derecha, asistida con el casquillo y la cobertura de cáscara de arroz. En este caso con la mazarota asistida con la cáscara de arroz se ahorraron 130 kg de acero con respecto al peso bruto de 500 kg planificado para la fundición de esta pieza.
En la imagen B se puede observar la gran cavidad resultante en la mazarota como resultado del aumento del volumen de acero entregado a la pieza por el efecto termoaislante de la cáscara de arroz en forma de casquillo y cobertura. En este caso se ahorraron 190 kg de acero con respecto al peso bruto planificado de 720 kg y se logró una eficiencia de alimentación del 30 % de la mazarota.
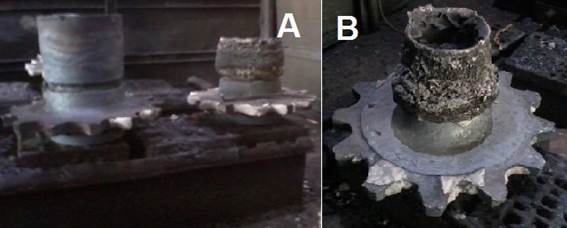
Figura 4 A: Mazarota convencional y mazarota asistida con la cáscara de arroz de una misma pieza (sprocket), B: Gran cavidad de entrega lograda en la mazarota.
Entre los años 2000 y 2001 se realizó un muestreo, a un amplio grupo de piezas fundidas de diferentes tipos, con el objetivo de obtener datos sobre el ahorro de acero propiciado por la aplicación de esta alternativa. La evaluación de 486 piezas posibilitó determinar que al emplear combinaciones de cobertura y casquillos de cáscara de arroz se produjo como promedio una eficiencia metálica de un 83 %, con un ahorro de 120 t de acero, lo cual corrobora lo ilustrado en la Figura 4.
Para mostrar y comparar los resultados de dicho análisis de forma abreviada, debido a la extensión de la tabla de referencia, la Tabla 1 se confeccionó a partir del promedio del peso bruto y de la eficiencia metálica para cada tipo de tecnología. Además, se consideró el promedio del metal ahorrado por cada tipo y cantidad de piezas de la muestra analizada, de acuerdo con datos previamente reportados (Cruz-Pérez 2009).
Tabla 1 Peso bruto, eficiencia metálica y metal ahorrado promedio
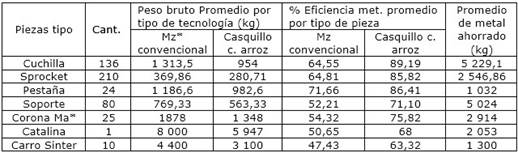
*Mz - Mazarota. Ma*- Masa alimentadora.
Otro efecto favorable que produce el empleo de los casquillos para la economía de la fundición y el medio ambiente es el significativo ahorro de los materiales que se utilizan en el taller de plantillas. Al evitar la utilización de plantillas altas se disminuye de forma apreciable el consumo de madera, clavos, tornillos, cola y pintura.
Además, permite disminuir la cantidad de mezcla de moldeo necesaria. En la Figura 5 pueden apreciarse plantillas de 865 mm y 830 mm de altura para mazarotas convencionales utilizadas en el taller de fundición de Planta Mecánica.
A ello se suma que frecuentemente es necesaria la reparación de dichas plantillas para dichas mazarotas, debido a que se deterioran durante el proceso de moldeo, tal como ilustra la Figura 6.
Las cajas de macho o moldes para la elaboración de los casquillos suelen requerir de mucho menos madera y de los demás materiales necesarios para la confección de las plantillas. Además, pueden durar muchos años en este servicio sin necesidad de reparación. En la Figura 2A se observan cajas de macho, utilizadas en la confección de casquillos de cáscara de arroz de diferentes diámetros, sin un deterioro significativo después de más de diez años de explotación. Las cajas de macho se pueden fabricar de plástico o de metal.
Otro de los aspectos importantes de la aplicación de la cáscara de arroz como material termoaislante en la fundición es que las cenizas generadas, tanto por los casquillos como por la cobertura, no afectan la reutilización de la arena de moldeo al no generarse, durante su combustión, compuestos o subproductos que dificulten la acción de los aglutinantes utilizados y afecten las propiedades de la mezcla de moldeo con la arena recuperada, o que generen defectos en las piezas, como sucede con algunos casquillos exotérmicos, según reportan algunos autores (Aufderheide et al. 2002; Twardowska y Aufderheide 2002).
Ochulur y demás colaboradores (2017) estudian la influencia de la adición de ceniza de cáscara de arroz como aditivo para modificar las propiedades de la mezcla en verde de arena sílice para fudición, en porcentaje del peso de la mezcla. La adición del 1 % de ceniza aumentó inicialmente la resistencia en verde de la mezcla a 97 KN/m2 pero se redujo a 64 KN/m2 cuando aumentó a 6 %. La permeabilidad gaseosa bajó de 110 cm/s a 60 cm/s con el aumento de 1 % a 6 % del peso de la mezcla. El contenido de humedad también se redujo de 4 % a 2,8 % para un aumento de 60 % del peso de la mezcla. La conductividad térmica de la mezcla se redujo un 30 % con el aumento del 6 % del peso de la mezcla, lo que garatiza un buen potencial para fundir piezas de paredes finas.
Prabhushankar y otros investigadores (2018) reportan la variación de las propiedades de la mezcla de moldeo de arena sílice a través de la adición entre un 5 % y 12,5 % del peso de la mezcla de iguales cantidades de ceniza de cáscara de arroz y de tusa de maíz. La resistencia a la compresión en verde, a la cizalladura en verde, el contenido de humedad y la permeabilidad gaseosa disminuyeron con el aumento del contenido en la mezcla de estos aditivos; al tiempo que la resistencia a la compresión y a la cizalladura en seco aumentaron.
Si se compara el peso de la ceniza de cáscara de arroz con el de la arena, vemos que para modificar el comportamiento de las propiedades de la arena o mezcla de moldeo se requieren cantidades abundantes de ceniza de cáscara de arroz. La cantidad de ceniza que resulta de la aplicación de la cáscara de arroz como termoaislante es insuficiente para modificar a un nivel perjudicial las propiedades de la arena de moldeo, como indica la experiencia de su aplicación de más de dos décadas en Planta Mecánica. Por otra parte, dichas cenizas, por ser muy ligeras, resulta fácil eliminarlas de la arena a través de un sistema mecánico por vía seca o por un sistema neumático de recuperación (Cruz-Pérez 2009).
Valoración de los resultados
Los resultados expuestos en la Figura 4 y la Tabla 1 demuestran que el uso de combinaciones de casquillo-polvo de cáscara de arroz en la fundición aumenta la eficiencia metálica a un 83 % como promedio. Ello es el resultado del aumento del tiempo de solidificación de las mazarotas, lo que direcciona la solidificación hacia ellas, garantizando la sanidad interna de las piezas con mazarotas más pequeñas que las convencionales. Con esto se logra un significativo ahorro de acero fundido, energía eléctrica y otros portadores energéticos, así como de materias primas. Además, permite sustituir la importación de casquillos y de polvo de cobertura, constituyendo una solución autóctona y asequible de material auxiliar.
En general, los resultados prácticos obtenidos al emplear la cáscara de arroz como material auxiliar en la fundición de piezas de acero en Planta Mecánica se encuentran justificados por un grupo de resultados experimentales.
Con las combinaciones casquillo-cobertura de cáscara de arroz empleadas en trabajos previos (Cruz-Pérez 2009) obtuvo un módulo promedio de 7,54 cm con respecto al módulo geométrico de una probeta cilíndrica de diámetro 200 mm x 200 mm de altura, que es de 3,33 cm. Ello generó un factor de prolongación del módulo promedio de 2,26, superior a valores de este parámetro publicados por Steger y Wlodawer (1967), Rio Tinto Iron & Titanium Inc. (2000) y Williams, Hardin y Beckermann (2016), respectivamente. Idamayanti y demás colaboradores (2020) reportan un factor de prolongación del módulo para su casquillo de cáscara de arroz de 1,4 como promedio.
En este sentido se reporta que en mazarotas asistidas con materiales exotérmicos e isotérmicos el factor de prolongación del módulo, con respecto a la arena de moldeo, puede estar entre 1,4 y 1,5 (Rio Tinto Iron & Titanium Inc. 2000).
Por otro lado, al emplear materiales altamente exotérmicos para mazarotas pequeñas, el factor de prolongación del módulo puede alcanzar 2,3 veces el módulo de la mazarota convencional. Steger y Wlodawer (1967) señalan, para materiales isotérmicos, un factor de prolongación del módulo entre 1,1 y 1,6. Williams, Hardin y Beckermann (2016) reportan valores de este parámetro, obtenidos de forma experimental y a través de la simulación con el software MAGMAsoft, sin aplicación de cobertura, desde 1,07 hasta 1,28 para un grupo de 13 camisas entre exotérmicas e isotérmicas de fabricantes como: Joymark, Exochem, ASK Chemical, FOSECO, y AMCOR.
Otros parámetros importantes relacionados con los materiales auxiliares utilizados en la fundición de piezas de acero, y que además se emplean para determinar el factor de prolongación del módulo, son los Factores de Alteración Aparente de la Superficie (ASAF por sus siglas en inglés). El valor de estos factores varía entre 0 y 1. Los valores más cercanos a 0 indican la mayor eficiencia del material auxiliar en cuestión. Ruddle (1979) reporta valores de estos factores de 0,65 y 0,7 al emplear materiales de la firma FOSECO.
Otro aspecto significativo es que la capacidad de alimentación, capacidad de entrega de acero o eficiencia de alimentación, alcanzada con mazarotas asistidas por materiales exotérmicos o isotérmicos, es de al menos un 33 % según FOSECO (2003), o más del 80 % según Rio Tinto Iron & Titanium Inc. (2000).
Por otro lado, en un estudio previo, en el que se utilizaron combinaciones casquillo-cobertura de cáscara de arroz (Cruz-Pérez 2009, 2012), se obtuvo un valor promedio de los factores ASAF de 0,44 para dichas combinaciones. Los valores del factor de prolongación del módulo y del ASAF conseguidos en dicho estudio, permitieron alcanzar una eficiencia de alimentación de las mazarotas entre 55 % y 70 % de su volumen.
Este resultado demuestra que con la correcta utilización de la cáscara de arroz es posible obtener valores de estos parámetros en el entorno de los reportados para materiales comercializados para dicho fin. En general, los valores experimentales de estos parámetros corroboran los resultados prácticos que se obtienen en la fundición al utilizar la cáscara de arroz como material auxiliar.
La utilización de la cáscara de arroz como material isotérmico en la fundición de piezas de acero, según trabajos previos (Cruz-Pérez 2009) permite disminuir el tamaño de las mazarotas, y por tanto, ahorrar una cantidad significativa de recursos ya que:
Disminuye el consumo de acero fundido al menos en un 30 % con respecto a las mazarotas convencionales en arena, o sea 300 kg/t.
Disminuye el consumo de energía eléctrica al menos en un 30 % por colada de acero.
Aumenta la productividad en el moldeo y acabado de las piezas.
Disminuye el consumo de madera en la elaboración de plantillas en un 25 %.
Disminuye el gasto de materiales de moldeo en un 20 %.
Disminuye el consumo de gases (oxígeno, acetileno o propano) para el proceso de oxicorte entre 30 % y 40 % por pieza.
Permite con una misma capacidad de hornos de fundición producir un mayor número de piezas o piezas de mayor peso, generando beneficios económicos.
Permite producir piezas con mayor garantía de sanidad y calidad.
De acuerdo con Serrano-Méndez y demás colaboradores (2009), para la implementación y el desarrollo de la producción más limpia en una empresa, por lo general, es necesario modificar el producto y el proceso. Modificar el proceso implica realizar cambios de diseño, selección de nuevos materiales, modificación o cambio de la tecnología instalada y establecer buenas prácticas.
La utilización de la cáscara de arroz en la fundición de Planta Mecánica de la forma anteriormente descrita, en su momento no requirió una inversión de recursos, modificar la tecnología ni el proceso de producción. Para aprovechar mejor su potencial y obtener mayores beneficios solo es necesario cambiar la concepción tecnológica actual (Suárez-Lisca 2017). Por ejemplo, aplicar el módulo térmico como concepción tecnológica más adecuada para la utilización de medios auxiliares de alimentación y, además, mejorar la disciplina tecnológica en cada paso del proceso tecnológico.
CONCLUSIONES
La utilización de la cáscara de arroz en forma de casquillos termoaislantes y como polvo de cobertura en la fundición de piezas de acero, es una eficaz contribución a la disminución de los costos de producción por las razones siguientes:
Debido a que aumenta la eficiencia metálica del proceso de fundición de piezas de acero hasta un 83 % como promedio, incrementa la eficiencia energética y disminuye el consumo de materias primas.
Presenta un positivo impacto medioambiental por ser una forma útil y efectiva para aprovechar la cáscara de arroz como residuo agroindustrial y reducir su carga contaminante, contribuyendo al ahorro de recursos naturales no renovables.
Contribuye de forma efectiva al desarrollo sostenible y al logro de la producción más limpia en la industria de la fundición.