Introducción
Las investigaciones relacionadas con la gestión de mantenimiento comienzan a desarrollarse fundamentalmente en la última etapa de la década de los años 90 del siglo XX, notándose, en las publicaciones seleccionadas para este estudio, un incremento de la necesidad e interés de abordar el diagnóstico a la gestión del mantenimiento, lo que se refleja posteriormente en las investigaciones que se realizan y publican en el presente siglo XXI. De aquí que se han diseñado diferentes herramientas de diagnóstico (Acosta, et al., 2011; Vásquez, 2011; Díaz, et al., 2017) para los diferentes sectores del ámbito empresarial. Estas fueron creadas para ayudar a las organizaciones a mejorar su desempeño, al brindarle con este análisis, el grado de economía, eficiencia y eficacia en la planificación, control y uso de sus recursos.
En las últimas décadas la concepción del mantenimiento a nivel internacional ha cambiado, pasando de una actividad reactiva a adoptar una concepción proactiva y extendiéndose a asegurar la confiabilidad de los activos a través de acciones concretas, vinculadas a nuevas prácticas y referenciada bajo un sistema de gestión a través del cual se define cómo se realizan los procedimientos, de manera tal que puedan ser medidos y auditados de forma más precisa (Díaz. et al., 2017).
La gestión del mantenimiento es la variable que más repercute en el desempeño de la función mantenimiento. Con una administración efectiva de las labores de mantenimiento, en cualquier tipo de empresa, se puede obtener la máxima calidad posible y un control eficiente de los costos y recursos materiales utilizados en los activos, garantizando disponibilidad, confiabilidad y rendimiento operativo de los equipos, con un alto nivel de eficiencia en los costos. La forma actual de gestionar el mantenimiento está estrechamente vinculada al proceso de producción o servicio que se realice por lo que se hace de extrema importancia conocer las particularidades de diferentes herramientas para poder seleccionar la más idónea a cada contexto radicando en este punto la necesidad de esta investigación.
En este trabajo se analizaron las diferentes herramientas aplicadas para el diagnóstico de la gestión del mantenimiento a través de una revisión bibliográfica. Los resultados de la investigación realizada permiten a los investigadores conocer los beneficios e insuficiencias para la selección de herramientas que mejor se contextualicen a su campo de trabajo, permitiendo la toma de decisiones ante los problemas presentados. Y se propone un concepto de mantenimiento relacionado con su función y objetivo.
Materiales y métodos
El desarrollo de esta investigación acerca de las diferentes herramientas (modelos, procedimientos y metodologías) empleadas para el diagnóstico de la gestión del mantenimiento se realiza empleando la Metodología de clasificación propuesta por Lage y Godinho (Luna, et al., 2016) pero contextualizada a este objeto de investigación; se compone de los siguientes pasos:
Desarrollo del marco conceptual.
Revisión del estado del arte y planteamiento del método de clasificación.
Organización y tabulación de la información.
Análisis y conclusiones arribadas.
Para el análisis de conglomerados o análisis clúster se utilizaron todas las variables analizadas en el paso 3 Organización y tabulación de la información. Al ser variables cualitativas se utilizó el método Ward y la distancia raíz cuadrática euclidiana según proponen Chávez, et al. (2010), que utilizan en sus investigaciones variables de este tipo.
Resultados y discusión
A partir de la aplicación de la Metodología de clasificación propuesta por Lage y Godinho se obtuvieron los siguientes resultados.
En la bibliografía investigada se recoge una amplia gama de autores que han conceptualizado el término mantenimiento fundamentado en la época en que se propuso la definición, entre algunos conceptos publicados se pueden citar:
Uno de los primeros conceptos de mantenimiento que ha sido utilizado en las publicaciones realizadas hasta el día de hoy es el que expresa “acciones dirigidas a asegurar que todo elemento físico continúe desempeñando las funciones deseadas" (Moubray, 1999). Otra forma de conceptualizar el mantenimiento es la brindada por García, et al. (2012), “mantenimiento son todas las actividades que deben ser desarrolladas en orden lógico, con el propósito de conservar en condiciones de funcionamiento seguro eficiente y económico, los activos fijos, herramientas y demás propiedades de las diferentes instalaciones de una empresa". En este concepto además de lo ya planteado en el de Moubray se anexan aspectos relacionados con la seguridad, la eficiencia y la economía.
Otros autores como Díaz, et al. (2019), a partir de sus investigaciones lo han planteado como “el conjunto de acciones encaminadas a preservar, corregir o conservar las funciones y condiciones de disponibilidad, seguridad, eficiencia de los activos fijos durante su ciclo de vida". En este concepto se retoma la necesidad de dirigir las acciones al cumplimiento de las funciones de los activos del concepto de Moubray, pero también expresa la necesidad de realizar acciones no solo para garantizar el cumplimiento de las funciones sino también cuando se pierde al menos una de estas. Mantiene los aspectos relacionados con la seguridad, la eficiencia y economía del concepto de García, et al. (2012), incorporándole que estas acciones deben estar presentes durante todo el ciclo de vida de los activos.
Tomando el concepto anterior como soporte de la investigación y usando lo expresado por Díaz, et al. (2019), se deriva que la función de mantenimiento sería: asegurar que todo activo físico continúe desempeñando las funciones deseadas en el contexto de desempeño con el objetivo de asegurar la competitividad de la empresa, garantizando niveles adecuados de la confiabilidad y disponibilidad de los equipos, respectando los requerimientos de calidad, seguridad y medioambientales. Del concepto de mantenimiento anteriormente expuesto se deriva una propuesta de función y objetivo de mantenimiento, que para su cumplimento se hacen necesarias la ejecución de acciones soportadas en estrategias y políticas.
En cuanto a las estrategias de mantenimiento Díaz et al. (2017) la define como “acciones dirigidas a perfeccionar el estado de la gestión de mantenimiento así como la estrategia organizacional que beneficie y haga eficiente las medidas que se tomen, atendiendo a las tendencias actuales del mantenimiento, estas acciones a emprender tendrán como fin dar solución a las necesidades derivadas del análisis del estado de la gestión del mantenimiento, obtenidas por diferentes métodos, ellas determinarán los lineamientos a seguir, los recursos necesarios para dar cumplimientos a las mismas, atendiendo a la proyección económica de los procesos que se analicen" (p. 308). Entre las estrategias seleccionadas se encuentran: el Mantenimiento Productivo Total, TPM, el Mantenimiento Centrado en Confiabilidad, RCM, el Mantenimiento basado en riesgo, RBM, el Mantenimiento basado en restricciones productiva, MBRP y el mantenimiento basado en la Confiabilidad operacional (Ayo-Imoru, 2018; Ziyue, et al., 2020).
En cuanto a política de mantenimiento se define el término como "orientaciones y objetivos generales de una organización con respecto a mantenimiento determinado y expresada formalmente por la máxima dirección" (Díaz, et al., 2017, p. 310). En la investigación se toma este concepto de política dado que expresa la necesaria importancia que debe brindarle la dirección de una entidad a este proceso.
Del análisis realizado se puede observar una relación entre el concepto de mantenimiento; así como su función y objetivo y como se entrelazan con las estrategias y políticas que se propongan en las organizaciones. En la figura 1 se muestra esta interrelación.
En general se puede decir que la implementación de las estrategias de mantenimiento ayuda a la organización a mantener y asegurar la disponibilidad y funciones de los activos físicos, cumpliendo el ciclo de vida de estos.
En cuanto a la gestión de mantenimiento se concibe como una herramienta para apoyar al personal de ingeniería en el desarrollo, control y dirección de un programa de mantenimiento para los equipos, garantizando su operación segura a máximas prestaciones y a costos efectivos. En Prando (1996), se propone que la gestión del mantenimiento debe basarse en aspectos de control empresarial: disponibilidad, confiabilidad, medio ambiente, costos, calidad, seguridad y otros específicos, con análisis crítico periódico. Al igual que en el anterior concepto da importancia a las variables costo y seguridad, pero añade otros aspectos como son disponibilidad, confiabilidad, calidad y expresa de forma explícita que estas acciones deben tener carácter cíclico.
Otra definición es la propuesta por Toledo (2017), que explica que son las actividades de la gestión que determinan los objetivos del mantenimiento, las estrategias y las responsabilidades. Se realiza por medio de la organización, planificación, supervisión y control del mantenimiento, la mejora de los métodos en la organización, incluyendo los aspectos económicos, la calidad, la seguridad y que tiene que tener como finalidad la mejora continua. En este concepto se expresa la necesidad de basarse no solo en estrategias sino también en políticas; la necesaria ejecución de un ciclo basado en la mejora continua y plantea la necesidad de tener presente elementos como costos, calidad y seguridad. Este concepto demuestra el cumplimiento del ciclo de gestión de una organización planteado en la ISO 9000, en la figura 2 se muestra esta relación.
Para la gestión del mantenimiento con la finalidad de lograr los aspectos económicos, la calidad y la seguridad en un proceso de mejora continua, cada organización debe diseñar sus estrategias, sobre la bases de la búsqueda de las mejores prácticas. Una de estas, es la denominada Mantenimiento Clase Mundial, que son el conjunto de las mejores prácticas operacionales y de mantenimiento, que reúne elementos de distintos enfoques organizacionales con visión de negocio, para crear un todo armónico de alto valor práctico, las cuales aplicadas en forma coherente generan ahorros sustanciales a las empresas (Vásquez, 2011), concepto compartido por los autores de esta investigación.
La orientación de la gestión de mantenimiento hacia clase mundial entre otras metas, exige cambiar de actitud y de cultura en la organización. Requiere que se tenga un alto nivel de prevención y planeación, soportado en un adecuado sistema gerencial de información de mantenimiento [sistema de gestión de mantenimiento asistido por computadora], muy orientado hacia las metas y objetivos fijados previamente y realizando las actividades que haya que hacer en la forma más correcta posible con el mayor grado de profundidad científica. Utiliza el benchmarking como herramienta para alcanzar mejores costos, mejor productividad y máxima competitividad a través del mejoramiento continuo (García, et al., 2012; Sultana & RezaulKarim, 2015).
Llegar a alcanzar estas metas no ocurre de forma espontánea, ocurre a través de un proceso de compromiso con el cambio y solo se logra con la implementación de prácticas más efectivas en el tiempo. Debe partir, en primera instancia, del conocimiento del estado actual de la organización con respecto a esta actividad. El conocimiento de este estado debe realizarse sobre la base de la implementación de un diagnóstico a la actividad. El diagnóstico a la gestión del mantenimiento consiste en el examen y evaluación que se realiza a una entidad para establecer el grado de economía, eficiencia y eficacia en la planificación, control y uso de los recursos y comprobar el cumplimiento de las disposiciones establecidas, con el objetivo de verificar la utilización racional de los recursos y mejorar las actividades y materias examinadas (Acosta, et al., 2011). El autor desarrolla un cuidadoso y detallado análisis con la calificación de cada una de las funciones características de la gestión del mantenimiento, agrupadas según las áreas básicas que constituyen su campo de actividad.
Para ejecutar el diagnóstico a la gestión del mantenimiento de una organización es necesario conocer una serie de aspectos que permitan comprender la manera de pensar, actuar y decidir de sus trabajadores y directivos. Esto es algo extremadamente difícil, pero no imposible si se consideran conscientemente los presupuestos que proporcionarán crear un cierto acercamiento al escenario donde se ejecuta la labor de la organización (Acosta, et al., 2011).
Los presupuestos más importantes son:
Objeto social: origen del centro ya sea de producción o servicios, principales objetivos económicos, sociales, etc.
Características de la organización: estructura organizativa, condiciones de trabajo y de vida, nivel del centro en estructura de mando de su organización superior.
Tecnología y equipamiento: tipo de tecnología, características de su equipamiento, obsolescencia, modernidad y estado técnico.
Como se ha expuesto las herramientas de diagnóstico a la gestión del mantenimiento son un conjunto de métodos creados y usados por autores de diferentes países (Vásquez, 2011; Viveros, et al., 2013; Díaz, et al., 2017) donde se identifican los procedimientos racionales utilizados para alcanzar un conjunto de objetivos en el examen a la gestión del mantenimiento.
En las últimas décadas, se han desarrollado diferentes herramientas para evaluar el estado de la gestión del mantenimiento. Para esta investigación fueron seleccionadas 52 bibliografías publicadas en internet entre los años 1990-2020. De ellas fueron seleccionadas 25 (ver listado de bibliografías en el anexo) donde los autores realizaron su trabajo utilizando las herramientas necesarias para esta investigación, se tuvo en cuenta como criterio de inclusión que fuesen herramientas referenciadas en bases de datos con soporte científico y/o libros, incluyéndose trabajos publicados en tesis doctorales y de maestría, donde se demostró rigor científico en su obtención y validación. Los elementos investigados para cada bibliografía fueron:
Áreas funcionales: determinar si la evaluación se realiza por áreas funcionales o no, y en caso afirmativo cuáles son estas áreas.
Forma de obtener la información: directa (observación in situ o revisión de documentos) o indirecta (a partir de encuestas).
Variables analizadas por los autores: elementos de la gestión del mantenimiento evaluados.
En el estudio, a cada bibliografía analizada se le otorga el valor 1 si contiene el aspecto analizado relacionado con la gestión del mantenimiento y el valor 0 si no lo contiene. En el caso del análisis de los elementos de la gestión del mantenimiento se amplió el rango de valoración entre 0 y 3, sobre la base de la cantidad de ítems que propone cada autor para la evaluación de cada elemento, a continuación se exponen los criterios, tabla 1.
Tabla 1 - Valores y criterios de evaluación.
Valor | Criterio |
---|---|
0 | No analiza el elemento. |
1 | Lo analiza débilmente, propone un (1) ítem para establecer su estado. |
2 | Lo analiza con mayor exactitud proponiendo entre 2 y 3 ítems para establecer su estado. |
3 | Es analizado con suficiente profundidad proponiendo más de 3 ítems para establecer su estado. |
La información recogida de las distintas herramientas fue organizada en tablas. En la tabla 2 se exponen las distintas herramientas, así como se analiza la gestión del mantenimiento en cada entidad a través de la división de áreas funcionales o no y en caso, de existir las áreas funcionales, cuantas y cuáles son analizadas, así como, también la forma de análisis de las mismas. En la tabla 3 se muestran los resultados de las valoraciones dadas por los expertos a cada componente de la gestión del mantenimiento de cada herramienta analizada.
Tabla 2 - Análisis de las herramientas de evaluación de la gestión de mantenimiento.
Referencia de la herramienta | (COVENIN, 1993) | (Prando, 1996) | (Zusammenarbeit, 2000) | (Tavares, 2002) | (Carvajal, et al., 2019) | (Borroto, et al., 2013) | (Krzysztof, 2007) | (Espinosa et al., 2008) | (García, et al., 2012) | (Gutierrez, et al., 2011) | (Vásquez, 2011) | (Acosta, et al., 2011) | |
---|---|---|---|---|---|---|---|---|---|---|---|---|---|
Área funcional | Existencia | 1 | 1 | 0 | 0 | 1 | 1 | 1 | 1 | 0 | 1 | 1 | 1 |
Cantidad | 12 | 10 | 0 | 0 | 8 | 6 | 6 | 12 | 0 | 8 | 10 | 7 | |
Organización | 1 | 1 | 0 | 0 | 1 | 1 | 1 | 1 | 0 | 1 | 1 | 1 | |
Ingeniería | 0 | 1 | 0 | 0 | 0 | 1 | 0 | 1 | 0 | 0 | 1 | 1 | |
Planificación | 1 | 0 | 0 | 0 | 1 | 0 | 1 | 1 | 0 | 1 | 1 | 1 | |
Economía | 0 | 1 | 0 | 0 | 0 | 0 | 1 | 1 | 0 | 0 | 1 | 1 | |
Capital humano | 1 | 1 | 0 | 0 | 1 | 1 | 1 | 1 | 0 | 1 | 0 | 1 | |
Logística | 1 | 1 | 0 | 0 | 1 | 0 | 0 | 1 | 0 | 0 | 1 | 0 | |
Tercerización | 0 | 0 | 0 | 0 | 0 | 1 | 0 | 1 | 0 | 0 | 0 | 1 | |
Servicios de mantenimiento | 0 | 1 | 0 | 0 | 0 | 1 | 0 | 0 | 0 | 0 | 0 | 0 | |
Infraestructura | 0 | 0 | 0 | 0 | 0 | 1 | 0 | 1 | 0 | 1 | 0 | 0 | |
Estrategias de mantenimiento | 1 | 0 | 0 | 0 | 0 | 0 | 1 | 0 | 0 | 1 | 0 | 0 | |
Seguridad | 0 | 0 | 0 | 0 | 0 | 0 | 0 | 0 | 0 | 0 | 1 | 1 | |
Calidad | 0 | 1 | 0 | 0 | 0 | 0 | 0 | 1 | 0 | 0 | 1 | 0 | |
Medio ambiente | 0 | 0 | 0 | 0 | 0 | 0 | 0 | 1 | 0 | 0 | 1 | 0 | |
Control | 0 | 0 | 0 | 0 | 0 | 0 | 0 | 0 | 0 | 0 | 0 | 0 | |
Gestión de la información | 0 | 1 | 0 | 0 | 1 | 0 | 1 | 1 | 0 | 1 | 1 | 0 | |
Tipos de mantenimiento | 1 | 0 | 0 | 0 | 1 | 0 | 0 | 0 | 0 | 1 | 1 | 0 | |
Obtención de la información | Directa | 1 | 1 | 0 | 1 | 1 | 0 | 1 | 1 | 0 | 1 | 0 | 1 |
Indirecta | 1 | 1 | 1 | 1 | 1 | 0 | 1 | 1 | 1 | 1 | 1 | 1 |
Tabla 3 - Análisis de las herramientas de evaluación de la gestión de mantenimiento. Ver bibliografías en anexo. Continuación
Referencia de la herramienta | (Raña, et al., 2013) | Borroto, et al., 2013) | (Ortiz, et al., 2013) | (Velazquez, 2014) | (Institute, 2014) | (Sondalini, 2015) | (Morla, 2015) | (Herrera et al., 2016) | (Altamirano, 2017) | (Díaz, et al., 2017) | (Díaz, et al., 2019) | (Carvajal, et al., 2019) | (Díaz, et al., 2020) | |
---|---|---|---|---|---|---|---|---|---|---|---|---|---|---|
Área funcional | Existencia | 0 | 1 | 0 | 1 | 1 | 0 | 1 | 1 | 0 | 1 | 1 | 8 | 0 |
Cantidad | 0 | 6 | 0 | 9 | 5 | 0 | 9 | 4 | 0 | 8 | 5 | 1 | 0 | |
Organización | 0 | 1 | 0 | 1 | 1 | 0 | 1 | 1 | 0 | 1 | 1 | 0 | 0 | |
Ingeniería | 0 | 1 | 0 | 0 | 0 | 0 | 0 | 0 | 0 | 1 | 1 | 1 | 0 | |
Planificación | 0 | 1 | 0 | 0 | 1 | 0 | 0 | 0 | 0 | 0 | 1 | 1 | 0 | |
Economía | 0 | 1 | 0 | 0 | 0 | 0 | 0 | 0 | 0 | 1 | 1 | 1 | 0 | |
Capital humano | 0 | 1 | 0 | 1 | 0 | 0 | 1 | 1 | 0 | 1 | 1 | 1 | 0 | |
Logística | 0 | 0 | 0 | 1 | 1 | 0 | 1 | 0 | 0 | 1 | 0 | 0 | 0 | |
Tercerización | 0 | 0 | 0 | 1 | 0 | 0 | 1 | 0 | 0 | 0 | 0 | 1 | 0 | |
Servicios de mantenimiento | 0 | 0 | 0 | 0 | 0 | 0 | 0 | 0 | 0 | 1 | 0 | 0 | 0 | |
Infraestructura | 0 | 0 | 0 | 1 | 0 | 0 | 1 | 0 | 0 | 1 | 0 | 1 | 0 | |
Estrategias de mantenimiento | 0 | 1 | 0 | 0 | 0 | 0 | 0 | 0 | 0 | 1 | 0 | 0 | 0 | |
Seguridad | 0 | 0 | 0 | 1 | 0 | 0 | 1 | 0 | 0 | 0 | 0 | 0 | 0 | |
Calidad | 0 | 0 | 0 | 1 | 0 | 0 | 1 | 0 | 0 | 0 | 0 | 1 | 0 | |
Medio ambiente | 0 | 0 | 0 | 1 | 0 | 0 | 1 | 0 | 0 | 0 | 0 | 0 | 0 | |
Control | 0 | 0 | 0 | 1 | 0 | 0 | 1 | 0 | 0 | 0 | 0 | 1 | 0 | |
Gestión de la información | 0 | 0 | 0 | 0 | 1 | 0 | 0 | 1 | 0 | 0 | 0 | 0 | 0 | |
Tipos de mantenimiento | 0 | 0 | 0 | 0 | 1 | 0 | 0 | 0 | 0 | 0 | 0 | 0 | 0 | |
Obtención de la información | Directa | 0 | 1 | 1 | 1 | 0 | 1 | 0 | 1 | 1 | 1 | 1 | 1 | 1 |
Indirecta | 1 | 1 | 1 | 1 | 1 | 1 | 1 | 1 | 1 | 1 | 0 | 1 | 0 |
Tabla 4 - Valoración del análisis de los elementos de la gestión del mantenimiento para cada herramienta.
Elementos | Herramientas | |||||||||||
---|---|---|---|---|---|---|---|---|---|---|---|---|
(COVENIN, 1993) | (Prando, 1996) | (Zusammenarbeit., 2000) | (Tavares, 2002) | (Carvajal, et al., 2019) | (Borroto, et al., 2013) | (Krzysztof, 2007) | (Espinosa, et al., 2008) | (García, et al., 2012) | (Gutierrez, et al., 2011) | (Vásquez, 2011) | (Acosta, et al., 2011) | |
Sistema de mantenimiento | 0 | 2 | 0 | 0 | 0 | 1 | 0 | 0 | 0 | 0 | 1 | 0 |
Plantilla | 2 | 2 | 2 | 2 | 1 | 1 | 0 | 1 | 2 | 2 | 2 | 3 |
Estructura organizativa | 3 | 2 | 2 | 2 | 2 | 1 | 2 | 2 | 2 | 2 | 3 | 2 |
Políticas y objetivos | 2 | 3 | 2 | 1 | 2 | 0 | 2 | 2 | 0 | 1 | 2 | 3 |
Funciones del personal | 3 | 2 | 1 | 2 | 2 | 1 | 0 | 2 | 2 | 2 | 2 | 3 |
Aplicaciones informáticas | 0 | 2 | 2 | 2 | 3 | 2 | 3 | 1 | 3 | 2 | 3 | 3 |
Gestión de la información | 2 | 3 | 1 | 2 | 2 | 2 | 2 | 1 | 2 | 2 | 2 | 2 |
Gestión de la documentación | 2 | 2 | 1 | 2 | 2 | 2 | 1 | 1 | 2 | 1 | 2 | 2 |
Gestión de órdenes de trabajo | 2 | 3 | 2 | 3 | 3 | 2 | 2 | 2 | 3 | 2 | 3 | 3 |
Gestión logística | 2 | 2 | 2 | 2 | 2 | 0 | 2 | 2 | 2 | 3 | 3 | 2 |
Gestión de almacenes | 2 | 1 | 2 | 3 | 1 | 1 | 1 | 2 | 3 | 3 | 3 | 2 |
Gestión de inventarios | 2 | 2 | 2 | 3 | 1 | 1 | 1 | 2 | 3 | 3 | 2 | 2 |
Capacitación | 2 | 3 | 3 | 3 | 2 | 2 | 2 | 3 | 3 | 2 | 2 | 3 |
Evaluación del desempeño | 2 | 3 | 2 | 2 | 2 | 1 | 0 | 2 | 2 | 1 | 2 | 3 |
Estimulación | 2 | 3 | 2 | 3 | 2 | 2 | 0 | 2 | 2 | 2 | 2 | 2 |
Gestión de indicadores | 1 | 1 | 3 | 2 | 1 | 2 | 3 | 3 | 3 | 2 | 3 | 3 |
Gestión de costos de mantenimiento | 2 | 2 | 3 | 2 | 1 | 2 | 2 | 3 | 2 | 2 | 3 | 3 |
Presupuesto | 1 | 2 | 2 | 2 | 0 | 2 | 1 | 2 | 2 | 2 | 3 | 3 |
Planificación | 3 | 1 | 3 | 3 | 2 | 2 | 3 | 2 | 2 | 2 | 2 | 3 |
Programación | 3 | 1 | 3 | 3 | 2 | 2 | 3 | 2 | 2 | 2 | 2 | 3 |
Contratación [tercerización] | 1 | 1 | 2 | 3 | 0 | 3 | 3 | 2 | 0 | 2 | 3 | 3 |
Infraestructura | 1 | 2 | 0 | 2 | 1 | 3 | 1 | 3 | 2 | 2 | 2 | 2 |
Útiles y herramientas | 3 | 1 | 2 | 2 | 1 | 2 | 1 | 2 | 3 | 3 | 2 | 2 |
Inspección | 2 | 1 | 1 | 2 | 2 | 2 | 3 | 2 | 2 | 2 | 3 | 3 |
Tecnologías de diagnóstico | 2 | 1 | 1 | 2 | 2 | 2 | 3 | 2 | 2 | 2 | 3 | 3 |
Calidad | 1 | 2 | 2 | 1 | 1 | 0 | 1 | 3 | 1 | 2 | 2 | 3 |
Medio ambiente | 0 | 1 | 1 | 1 | 1 | 0 | 1 | 3 | 0 | 2 | 2 | 3 |
Seguridad | 0 | 3 | 1 | 1 | 1 | 0 | 1 | 3 | 0 | 2 | 2 | 3 |
Tipos de mantenimiento | 3 | 2 | 0 | 2 | 2 | 1 | 2 | 1 | 2 | 3 | 3 | 3 |
Portadores energéticos | 0 | 0 | 0 | 1 | 0 | 0 | 2 | 1 | 0 | 0 | 2 | 2 |
Gestión de lubricación | 0 | 0 | 0 | 2 | 2 | 0 | 0 | 0 | 0 | 1 | 2 | 2 |
Diagnóstico mantenimiento | 0 | 0 | 0 | 2 | 0 | 0 | 0 | 0 | 0 | 1 | 2 | 3 |
Tabla 5 - Valoración del análisis de los elementos de la gestión del mantenimiento para cada herramienta. Continuación
Elementos | Herramientas | ||||||||||||
---|---|---|---|---|---|---|---|---|---|---|---|---|---|
(Raña, et al., 2013) | (Borroto, et al., 2013) | (Ortiz, et al., 2005) | (Velazquez, 2014) | (Institute, 2014) | (Sondalini, 2015) | (Morla, 2015) | (Herrera, et al., 2016) | (Altamirano, 2017) | (Díaz, et al., 2017) | (Carvajal, et al., 2019) | (Díaz, et al., 2019) | (Díaz, et al., 2020) | |
Sistema de mantenimiento | 1 | 0 | 0 | 0 | 2 | 1 | 0 | 0 | 0 | 0 | 2 | 3 | 3 |
Plantilla | 2 | 2 | 2 | 2 | 0 | 1 | 3 | 2 | 1 | 2 | 2 | 3 | 1 |
Estructura organizativa | 2 | 2 | 2 | 2 | 2 | 2 | 0 | 2 | 3 | 1 | 2 | 3 | 1 |
Políticas y objetivos | 0 | 2 | 1 | 2 | 2 | 2 | 1 | 1 | 3 | 0 | 1 | 3 | 0 |
Funciones del personal | 0 | 2 | 2 | 2 | 2 | 2 | 2 | 2 | 3 | 0 | 2 | 3 | 1 |
Aplicaciones informáticas | 2 | 1 | 2 | 3 | 2 | 2 | 2 | 1 | 2 | 3 | 2 | 1 | |
Gestión de la información | 0 | 1 | 2 | 2 | 3 | 2 | 3 | 2 | 1 | 2 | 2 | 3 | 2 |
Gestión de la documentación | 0 | 1 | 2 | 2 | 2 | 1 | 3 | 1 | 1 | 2 | 1 | 3 | 3 |
Gestión de órdenes de trabajo | 0 | 3 | 3 | 3 | 3 | 3 | 2 | 2 | 2 | 3 | 2 | 3 | 3 |
Gestión logística | 0 | 2 | 2 | 3 | 3 | 3 | 2 | 2 | 3 | 0 | 3 | 3 | 2 |
Gestión de almacenes | 0 | 2 | 2 | 3 | 3 | 2 | 2 | 2 | 3 | 2 | 2 | 3 | 2 |
Gestión de inventarios | 0 | 1 | 2 | 3 | 3 | 2 | 3 | 2 | 3 | 2 | 2 | 3 | 2 |
Capacitación | 2 | 1 | 2 | 3 | 3 | 3 | 2 | 2 | 1 | 2 | 2 | 3 | 1 |
Evaluación del desempeño | 0 | 1 | 2 | 2 | 3 | 0 | 1 | 1 | 1 | 0 | 1 | 2 | 0 |
Estimulación | 1 | 1 | 2 | 2 | 3 | 0 | 0 | 1 | 1 | 0 | 1 | 2 | 0 |
Gestión de indicadores | 0 | 3 | 1 | 2 | 1 | 2 | 3 | 1 | 2 | 3 | 3 | 3 | 3 |
Gestión de costos de mantenimiento | 0 | 2 | 3 | 3 | 2 | 2 | 3 | 2 | 2 | 3 | 3 | 3 | 3 |
Presupuesto | 2 | 2 | 2 | 2 | 1 | 2 | 3 | 2 | 2 | 3 | 3 | 2 | 3 |
Planificación | 2 | 3 | 2 | 3 | 3 | 3 | 1 | 2 | 3 | 3 | 3 | 3 | |
Programación | 2 | 3 | 3 | 2 | 2 | 3 | 2 | 1 | 2 | 3 | 3 | 3 | 3 |
Contratación [tercerización] | 2 | 2 | 3 | 3 | 2 | 3 | 3 | 1 | 1 | 2 | 3 | 3 | 2 |
Infraestructura | 0 | 3 | 2 | 3 | 0 | 0 | 3 | 2 | 0 | 3 | 3 | 3 | 0 |
Útiles y herramientas | 0 | 2 | 3 | 2 | 2 | 1 | 3 | 2 | 3 | 3 | 2 | 3 | 3 |
Inspección | 0 | 2 | 2 | 2 | 2 | 2 | 1 | 1 | 2 | 1 | 3 | 3 | 3 |
Tecnologías de diagnóstico | 0 | 2 | 2 | 2 | 2 | 1 | 1 | 1 | 2 | 1 | 3 | 3 | 1 |
Calidad | 2 | 2 | 2 | 3 | 2 | 2 | 3 | 1 | 1 | 2 | 3 | 2 | 2 |
Medio ambiente | 0 | 2 | 2 | 3 | 2 | 2 | 3 | 1 | 1 | 0 | 3 | 2 | 3 |
Seguridad | 1 | 2 | 1 | 3 | 2 | 2 | 3 | 1 | 1 | 0 | 3 | 2 | 3 |
Tipos de mantenimiento | 0 | 2 | 2 | 2 | 2 | 2 | 2 | 2 | 2 | 2 | 2 | 2 | 1 |
Portadores energéticos | 0 | 1 | 1 | 1 | 0 | 2 | 0 | 1 | 1 | 0 | 1 | 2 | 0 |
Gestión de lubricación | 0 | 0 | 0 | 2 | 0 | 0 | 0 | 0 | 0 | 0 | 0 | 2 | 2 |
Diagnóstico mantenimiento | 0 | 2 | 3 | 2 | 0 | 2 | 2 | 0 | 0 | 0 | 0 | 3 | 0 |
Resultados y discusión
Del análisis de la tabla 2 se puede concluir que 16 herramientas, el 64 %, se publicaron a partir del 2011 por lo que se consideran de actualidad el tema investigado. En la figura 3 se muestra como están diseñadas de forma general estas herramientas en cuanto a las áreas funcionales.
Del análisis de la figura 3 se determinó que el 68 % (17) de las herramientas proponen la evaluación de la gestión del mantenimiento a partir del análisis de áreas funcionales, sin embargo los autores difieren entre cuántas y cuáles son estas áreas. En cuanto a la cantidad, las mismas van desde 4 hasta 12, siendo las áreas más comunes Organización (16) y Capital humano (15), seguidas por otras como Planificación (11); Ingeniería y Economía (ambas con 9); Gestión de la información (8) e Infraestructura (7). Es de señalar que como las áreas difieren entre sí, las mismas se combinan, por ejemplo:
En Acosta, et al. (2011), el área de Planificación evalúa Control.
En Díaz, et al. (2019), el área de Planificación evalúa Tercerización, Control y Diagnóstico a la gestión; en Ingeniería se evalúa Calidad, Medio ambiente, Seguridad y Tipos de mantenimiento, y en Organización se evalúa Logística.
En Prando (1996), el Capital humano se evalúa a partir de 3 áreas funcionales.
Con respecto a la forma de obtener la información se puede concluir que el 76 % (19) de las herramientas emplean simultáneamente métodos directos e indirectos para la toma de la información, en tanto el 24 % (6), recopilan información usando solamente métodos indirectos. Por otro parte, del examen de la tabla 2 se pueden arribar a las siguientes conclusiones:
En el análisis de las diferentes herramientas analizadas se determinan un total de 32 elementos diferentes. Los resultados cuantitativos del estudio de las herramientas en cuanto a los elementos de la gestión del mantenimiento que se consideran se muestran en la figura 4, para este análisis a cada elemento se le otorga el valor 0 si no lo analiza y el valor 1 si lo analiza, sin importar la fortaleza de dicho análisis y cuyos resultados se muestran en la figura 4.
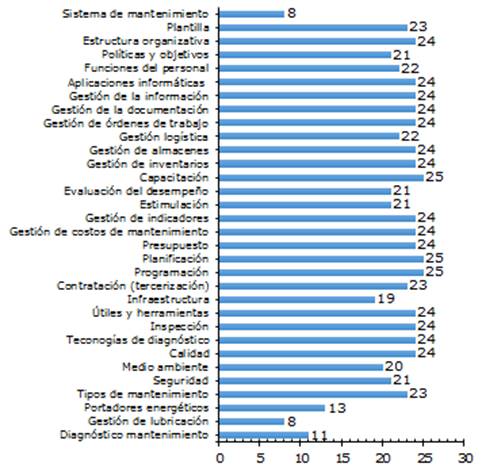
Fig. 4 - Resultados cuantitativos del estudio de las herramientas en cuanto a los elementos de la gestión del mantenimiento.
En la figura 4 se puede observar que más del 85 % (28) de los elementos, son tratados en el 76 % (19) de las herramientas analizadas, siendo los menos tratados sistema de mantenimiento (8), gestión de lubricación (8), diagnóstico de mantenimiento (11) y portadores energéticos (13). Esto demuestra que aun cuando hay diferencias de criterios en cuanto a las áreas funcionales a analizar, si existe acuerdo entre los elementos que deben ser evaluados en la gestión del mantenimiento. Un análisis de cómo están presentes estos elementos dentro de cada herramienta se muestra en la figura 5.
En la figura 5 se puede observar como más del 92 % (23) de las herramientas analizan al menos el 75 % (24) de los elementos determinados. Solo las herramientas planteadas en Raña & Castillo (2013); y Díaz, et al. (2017), no se encuentran dentro de este grupo. Se observa que incluso las metodologías planteadas por Vásquez (2011); y Díaz, et al. (2019), evalúan todos los elementos, mientras que en otras 11 herramientas se evalúan entre 29 y 31 elementos. Esto ratifica que existe encuerdo en este aspecto entre los diferentes autores.
Posteriormente se realiza un análisis sobre la fortaleza con la que se aborda cada uno de estos elementos a partir del promedio de las valoraciones dadas a cada elemento (entre 0 y 3, según criterio planteado con anterioridad) en cada herramienta a partir de la valoración promedio obtenida para cada elemento. Este resultado se muestra en la figura 6.
A partir del análisis de la figura 6 se clasificaron los resultados en 3 grupos:
Grupo 1: elementos con puntuaciones promedios menores o igual a uno 1 (color rojo): está conformado por 4 elementos sistema de mantenimiento (0,52), gestión de lubricación (0,60), portadores energéticos (0,72) y diagnóstico de mantenimiento (0,88), coincidiendo con los elementos menos tratados en las herramientas analizadas.
Grupo 2: elementos con puntuaciones promedios entre 1 y 2 (color verde): compuesto por 12 elementos entre los que se encuentran plantilla (1,76) y objetivos (1,61), entre otros.
Grupo 3: elementos con puntuaciones superiores a 2 (color azul): compuesto por 16 elementos, donde las mayores valoraciones se obtienen en gestión de órdenes de trabajo (2,48), planificación (2,40), programación (2,36), capacitación (2,32) y gestión de costo (2,28).
Los resultados demuestran que de forma general los elementos son tratados en las herramientas con algún nivel de desarrollo, dado que el 87,5 % de los elementos (28) se encuentran en los grupos 2 y 3, incluso todos con puntaciones promedios por encima de 1,4. Un análisis del promedio de las puntuaciones de los elementos para cada herramienta se muestra en la figura 7. Los promedios son calculados sobre la base de los elementos de diagnóstico analizados en cada herramienta, no se tuvieron en cuenta los valores puntuados con cero ya que falsearía el valor en esa herramienta.
Como se muestra en la figura 7 el 44 % (11) de las herramientas obtienen una valoración entre 1 y 2, incluso todas por encima de 1,50, mientras que el 56 % (14) obtienen un resultado superior a 2. Estos resultados implican que de manera general los análisis que se realizan en las diferentes herramientas son profundos, dando criterios claros de como evaluarse los mismos. Este resultado está en concordancia con los análisis realizados en la figura 5.
Como resumen se puede decir que la mayoría de las herramientas (17) proponen el empleo de áreas funcionales para la evaluación de la gestión del mantenimiento, sin embargo no muestran concordancia en cuales serían estas áreas. Contrario a esto si se muestra concordancia entre los elementos que se evalúan dentro de ellas, pero los mismos no se encuentran fundamentados de igual forma en cada herramienta, aunque se detecta como promedio una valoración profunda de los mismos. Para el estudio de estas diferencias y similitudes a continuación se realiza un análisis de agrupamiento o análisis clúster (Salazar, 2013).
Para el análisis de conglomerados o análisis clúster se utilizaron todas las variables estudiadas anteriormente, con excepción de las áreas que aborda cada herramienta. Todas estas variables son cualitativas, a las cuales se les otorgó valores según escala referida con anterioridad y cuyos resultados se muestran en tabla 3 y tabla 4 y 5. Los resultados obtenidos con un nivel similitud de 60 % se muestran en el dendrograma de la figura 8.
Como se observa en la figura 8 se conforman 5 grupos o clúster. A continuación se caracteriza a cada uno de los grupos y se realiza el análisis crítico de algunas de las herramientas componentes de cada grupo.
Como característica general de todos los grupos o clúster es que las variables análisis por área funcional (0 y 1) y método de obtención de la información (0 y 1) no inciden en la formación de los grupos ya que indistintamente dentro de los mismos están presentes ambas valoraciones de las dos variables. Las variables relacionadas con los elementos evaluados para la gestión del mantenimiento son analizadas en los 5 grupos.
Grupo I: conformado por el 52 % (13) de las referencias.
Se caracteriza por no abordar de manera general las variables sistema de mantenimiento, gestión de lubricación y diagnóstico de mantenimiento, (predominan en estos casos valoraciones con 0), mientras que la variable portadores energéticos se valora muy débilmente (mayoritariamente valores entre 0 y 1). Por otra parte las variables plantilla, política y objetivos, aplicaciones informáticas, gestión de la información, gestión de la documentación, evaluación del desempeño, estimulación, gestión de indicadores, presupuesto, inspección, tecnología de diagnóstico, calidad, medio ambiente y seguridad se analizan con una fortaleza media (de forma general se encuentran entre 1 y 2).
Las variables estructura organizativa, funciones del personal, gestión de órdenes de trabajo, gestión logística, gestión de almacenes, gestión de inventarios, capacitación, gestión de costos del mantenimiento, planificación, programación, útiles y herramientas y tipos de mantenimiento son fuertemente analizadas (de forma general se encuentran entre 2 y 3). Las restantes 2 variables obtienen resultados variables (indistintamente valoraciones entre 0 y 3).
En este grupo se puede mencionar la herramienta propuesta por la norma emitida por la Comisión Venezolana de Normas Industriales y que por mucho tiempo fue empleada por PDVSA. La misma tiene como principal característica que la evaluación de los elementos se realiza a partir de una valoración en méritos o deméritos otorgados sobre la base de un patrón pre definido. Como peculiaridades fundamentales dentro del grupo están la no evaluación de la variable aplicaciones informáticas, única en el grupo que no lo realiza y que solo esta herramienta y la propuesta por Gutiérrez & Díaz (2011), analizan fuertemente la variable tipos de mantenimiento.
En el caso de esta última herramienta propuesta por Gutiérrez & Díaz (2011), presenta como característica general que analiza prácticamente todas las variables obteniendo valoraciones medias (2) en la mayoría de las mismas, exceptuando portadores energéticos y gestión de lubricación donde obtiene puntuaciones muy bajas, característica de este grupo.
La herramienta propuesta por Díaz, et al. (2020); surge como una necesidad para evaluar el estado de implementación de la RS 116 / 2017 emitida por el Ministerio de Industria de Cuba con la finalidad de organizar la actividad de mantenimiento en el sector industrial cubano. En la misma se valoran la mayoría de las variables exceptuando infraestructura y diagnóstico a la gestión del mantenimiento. Como aspecto negativo es que es la única herramienta en el grupo que valora la variable capacitación con un valor bajo (1).
Grupo II: conformado por el 12 % (3) de las referencias.
Este grupo se caracteriza al igual que el grupo I por no abordar prácticamente los elementos sistema de mantenimiento, gestión de lubricación y diagnóstico de mantenimiento, pero tampoco aborda de manera general lo relacionados con portadores energéticos, política y objetivos, medio ambiente y seguridad. En el caso de la variable estructura organizativa es evaluada de forma muy débil, a diferencia del grupo I que se aborda fuertemente.
Otra semejanza con el grupo I es que analiza aplicaciones informáticas, evaluación del desempeño, estimulación, inspección y tecnología de diagnóstico, con una fortaleza media; sin embargo, a diferencia del grupo I se analizan de igual forma otras como funciones del personal, gestión logística, gestión de almacenes y tipos de mantenimiento que en el grupo I se evalúan fuertemente.
Otra similitud con el grupo I es que gestión de órdenes de trabajo, capacitación, gestión de costo, planificación, programación y útiles y herramientas están evaluadas fuertemente, pero en este grupo además de estas 6 variables existen otras evaluadas fuertemente como gestión de la información, gestión de la documentación, gestión de indicadores, presupuesto y calidad que en el grupo I se evalúan con una fortaleza media; mientras que contratación e infraestructura también son evaluadas fuertemente, a diferencia de en el grupo I, donde presentan un comportamiento variable. En el caso de las variables plantilla y gestión de inventarios se presenta un comportamiento variable.
Entre las herramientas en este grupo se puede citar la propuesta por Díaz, et al. (2017), que al igual que la anterior está diseñada para un contexto específico, en este caso, para aplicar en plantas de bioproductos.
Grupo III: conformado por el 12 % (3) de las referencias.
En este grupo, al igual que en los dos primeros, las variables sistema de mantenimiento y gestión de lubricación tampoco se analiza de manera general; mientras que las variables evaluación de despeño y estimulación tampoco se analizan de manera general en este grupo, a diferencia de los anteriores que se evalúan con fortaleza media. Otra diferencia con los grupos anteriores es que la variable gestión de la documentación se analiza de forma muy débil (valoración 1 en todas las herramientas de diagnóstico).
Una característica de este grupo es que la mayoría de las variables (15) para un 60 % del total se analizan con una fortaleza media y solamente 7 variables para un 28 % del total, se analizan fuertemente. En las primeras se encuentran las variables estructura organizativa, política y objetivos, funciones del personal, gestión de la información, gestión de almacenes, gestión de inventarios, gestión de costo del mantenimiento, presupuesto, útiles y herramientas, calidad, medio ambiente, seguridad, tipos de mantenimientos, portadores energéticos y diagnóstico del mantenimiento. Las 7 variables evaluadas fuertemente son gestión de órdenes de trabajo, planificación, programación, gestión logística, gestión de indicadores, contratación, e inspección, las 3 primeras evaluadas fuertemente también en los 2 grupos anteriormente analizados. Las restantes 5 variables obtienen indistintamente valoraciones entre 0 y 3.
En este grupo se puede citar la herramienta propuesta por Borroto, et al. (2013), que presenta como características distintiva que solamente no evalúa 2 elementos, sistema de mantenimiento y gestión de lubricación, aunque evaluando de forma débil un conjunto de estos como aplicaciones informáticas, capacitación, portadores energéticos, evaluación del desempeño y estimulación. En el caso de estos 2 últimos elementos, es la única herramienta en el grupo que realiza el análisis de los mismos.
Grupo IV: conformado por el 20 % (5) de las referencias.
Este grupo se caracteriza por abordar fuertemente la mayoría de los elementos (25), para un 78 %. Estos elementos están relacionados con plantilla, estructura, funciones del personal, aplicaciones informáticas, gestión de la información, gestión de la documentación, gestión de órdenes de trabajo, gestión logística, gestión de almacenes, gestión de inventarios, capacitación, gestión de indicadores, gestión de costos, presupuesto, planificación, programación, contratación, infraestructura, útiles y herramientas, inspección, tecnologías de diagnóstico, calidad, medioambiente, seguridad y tipos de mantenimiento. El resto de los elementos obtienen evaluaciones dispersas entre 0 y 3, pero dentro de este grupo algunos elementos se encuentran evaluados en todas las herramientas, como son política y objetivos, evaluación del desempeño, estimulación y portadores energéticos. De este análisis se puede plantear que este grupo se constituye por las herramientas más robustas.
Entre las herramientas se puede citar la propuesta por Carvajal, et al. (2019), que se basa en la metodología denominada AMORMS (Asset Management, Operational Reliability and Maintenance Survey), que presenta como característica distintiva dentro del grupo que no trata las variables gestión de lubricación y diagnóstico a la gestión del mantenimiento. Otra herramienta es la propuesta por Acosta, et al. (2011), la cual solamente no evalúa la variable sistema de mantenimiento y al resto de las variables son analizadas fuertemente (valoraciones entre 2 y 3).
En este grupo se encuentran las dos herramientas que tratan todas las variables analizadas. La propuesta por Vásquez (2011), que incorpora la variable sistema de mantenimiento pero de forma débil y el resto de las variables las analiza con valoraciones medias altas (entre 2y 3), predominado las primeras y la propuesta por Díaz, et al. (2019), que analiza todas las variables con valoraciones medias y fuertes pero predominando la valoración de alta.
Grupo V: agrupa al 4 % (1) de las referencias.
Este grupo como se observa está constituido por una sola herramienta, la propuesta por (Raña, et al., 2013). En esta herramienta solo se evalúan 12 variables de las 32 investigadas, y las mismas se analizan con evaluaciones medias y bajas (entre 1 y 2), aunque como aspecto positivo se puede señalar que predomina este último valor.
Conclusiones
En la investigación se muestra una revisión de 25 herramientas para el diagnóstico de la gestión del mantenimiento, así como las particularidades de las mismas aportando información a los especialistas para su selección de acuerdo al contexto operacional que se desee implementar.
Se evidencio la división de las entidades en áreas funcionales como forma de obtener una información más exacta y así potenciar la toma de decisiones en las acciones a implementar para solucionar los problemas que se detecten, aunque no existe concordancia en cuáles deben ser, infiriéndose la necesidad de evaluar para cada entidad cuales son las pertinentes.
Se observó que la mejor forma de obtener la información durante el proceso de diagnóstico es vincular herramientas cuantitativas y cualitativas y que las herramientas contenidas en el Grupo IV del análisis de agrupamiento deben ser las primeras en su análisis para una posible selección dado que son las que con mayor rigor evalúan las diferentes variables que denotan la gestión del mantenimiento en una entidad.