Introducción
En el mundo, es tarea de alta prioridad la construcción de plantas de procesos químicos, que incluyen recipientes a presión (calderas de vapor, autoclaves, digestores, tuberías que transportan hidrocarburos), o elementos para el transporte y almacenamiento de hidrocarburos y sustancias químicas (Solari, 2004). En correspondencia con los altos niveles de multidisciplinaridad y especialización, en el caso de los países en desarrollo, como Cuba, estas tareas de inversión se acometen casi en su totalidad con participación de colaboración extranjera.
El alto grado de complejidad, el costo económico de dichas plantas, el peligro para la salud de los seres humanos y las medidas de protección ambiental, constituyen aspectos indispensables a tener en cuenta al concebir las inversiones (Ministerio de la Inversión Extranjera, 2014 y Solari, 2012). El diseño de estas plantas, con frecuencia solo tiene en cuenta los aspectos de optimización, fabricación, montaje y operación y, en base a ello, las plantas se diseñan para una larga vida de explotación, de 30 a 40 años (Sroka ,2017 y Viswanathan, 1993). Sin embargo, en la práctica no se alcanza esta vida útil antes de reparaciones capitales, ya que, no se consideran en detalle las particularidades climatológicas y geográficas, se realizan adecuaciones durante la fabricación y montaje que no fueron previstas en el diseño original (ejemplo, cambio de materiales por homólogos del mercado), durante la explotación no se cumple a rigor los sistemas de inspección y mantenimiento y, a veces, se operan los equipos fuera de las condiciones nominales de diseño.
Por otra parte, las exigencias, desde el punto de vista ambiental y seguridad, son cada día más rigurosas, haciendo que, aun cuando las instalaciones mantengan capacidad para su desempeño desde el punto de vista técnico, puedan ser sacadas de servicio por regulaciones ambientales o de seguridad (Solari,2012).
La respuesta a las circunstancias planteadas, con vistas a garantizar mayores niveles de vida útil de las instalaciones, se basa en aplicar los criterios de análisis de fallas, a priori durante el diseño, la ejecución del montaje y la explotación (Collins, 1993). De este modo, la aparición de un fenómeno de degradación o, incluso, la presencia de la causa que lo induce es detectada, posibilitando evitar la falla.
Un análisis de las consideraciones metalmecánicas, de los aspectos fundamentales a tener en cuenta en una inversión de planta de procesos químicos, comienza por conocer los procesos de fallas y fenómenos de degradación en los equipos e instalaciones. La ocurrencia de fallas en estas plantas, puede tener diversos orígenes (American Society for Metals [ASM], 2002):
Condiciones de servicio extremadamente severas.
Defectos del material base.
Desviaciones del proyecto original en el proceso de fabricación.
Diseño inadecuado.
Mala selección y manejo de los materiales bases y de soldadura.
Dificultades en el montaje (montaje propiamente dicho, soldadura y tratamiento térmico).
Rediseño inadecuado, por no tener en cuenta la degradación estructural de los materiales de los equipos.
En base a lo planteado, el presente trabajo tiene como objetivo establecer las particularidades, desde el punto de vista metalmecánico, a tener en cuenta en una inversión de la industria de procesos químicos, para garantizar la resistencia, fiabilidad y durabilidad de los componentes y agregados.
Desarrollo
El alargamiento de la vida útil de una planta de procesos químicos está indisolublemente relacionado con la integridad de los componentes y equipos; por tanto, es esencial la prevención de la ocurrencia de fallas. En tal sentido, la presencia de fenómenos de degradación y, relacionado a ello, la selección de materiales y los sistemas de inspección, deben ser considerados desde el diseño y durante la vida útil de la instalación.
2.1. Función del análisis de fallas
Según Collins (1993), la función primaria del análisis de fallas, es definir, determinar y describir los factores responsables generadores de la falla (Fig 1), para poder prever posibles averías al diseñar los componentes de las plantas.
Se debe considerar la selección del material desde el enfoque de la prevención de la falla, o sea, que esté capacitado para enfrentar los fenómenos de degradación que operan en la instalación.
Durante la fabricación pueden ser inducidos defectos que conducen a la falla. En tal sentido, los regímenes de trabajo de las herramientas son esenciales a considerar. Por ejemplo, la elección de una herramienta para el maquinado, o incluso un régimen severo de corte, puede conducir a una rugosidad generadora de fallas por fatiga. En igual sentido, un proceso de conformado puede inducir corrosión bajo tensión.
En el montaje, pueden ser creadas las condiciones para fallas futuras. Por ejemplo, un anclaje inapropiado, puede conducir a vibraciones excesivas y a fallas en menores números de ciclos. También, las desalineaciones pueden llevar a la falla temprana de los componentes.
El servicio de las instalaciones y componentes los somete a temperaturas, presiones, contacto con medios agresivos, etc., que provocan mecanismos de daños, que pueden llevar a la falla. Por tanto, el control de parámetros durante la operación es esencial.
Durante todas las etapas, al aplicar el análisis de fallas, si aparecen defectos no admisibles se debe corregir de manera preventiva. En el caso particular de nuevas inversiones, todo está centrado en el diseño, fabricación y montaje. Antes de iniciar el montaje de la planta, debe ser revisada la documentación técnica y el estado de los equipos y agregados. Durante la fabricación de agregados y el montaje de equipos y componentes deben ser realizadas inspecciones, dejando constancia de registros.
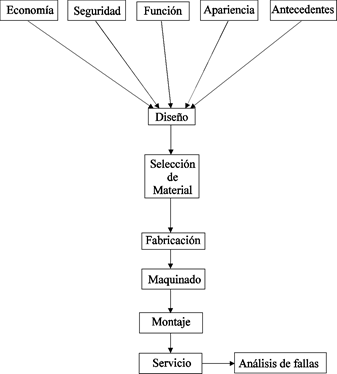
Fig. 1 - Relación del diseño y la fabricación de un componente con el Análisis de fallas (Collins, 1993).
2.2 Fenómenos de degradación en equipos e instalaciones de plantas de procesos químicos
En el análisis para prolongar la vida útil de equipos e instalaciones de planta de procesos químicos, manteniendo la resistencia, fiabilidad y durabilidad en el tiempo, es de vital importancia, conocer cuáles son los fenómenos más importantes que degradan a los materiales, así como a las uniones soldadas; es decir, cuales son los fenómenos que con el tiempo hacen que los materiales y sus uniones soldadas pierdan estabilidad durante su servicio. La degradación consiste en la disminución de algunas propiedades mecánicas fundamentales, lo cual está asociado a una pérdida de la capacidad de trabajo de los equipos, disminuyendo su vida útil.
El conocimiento profundo de los fenómenos de degradación de la estructura, permite realizar el diseño más adecuado de los equipos, teniendo presente las condiciones de trabajo, tales como, la presión, la temperatura, el tipo de carga, el medio ambiente, etc. La detección de los fenómenos de degradación en una fase embrionaria, permite la realización de pequeñas reparaciones con bajo costo para evitar la falla.
Los fenómenos que fundamentalmente degradan a los materiales y uniones soldadas en equipos de plantas de procesos químicos son: Fatiga mecánica, corrosión, cavitación, erosión, fragilización, endurecimiento por precipitación, desgaste, tensiones residuales, grafitización, esferoidización, termofluencia en la etapa primaria y secundaria, grietas inducidas por la termofluencia a partir de su etapa terciaria, fatiga térmica, fatiga termomecánica y choque térmico (Castillo, 2020; Fernández, 2021 y Komai, 1998).
La pérdida de espesor y el agrietamiento, son las consecuencias más frecuentes que provocan los fenómenos de degradación en plantas de procesos químicos. Especial interés merecen la corrosión y la erosión en sus diferentes manifestaciones, así como el agrietamiento inducido por hidrógeno y corrosión bajo tensión (Komai, 1998).
Dada su alta incidencia como fenómeno de degradación en plantas químicas, la corrosión construye el mayor foco de interés. La alta versatilidad de medios que actúan y de materiales de los equipos y componentes, hacen que existan múltiples tipos de corrosión en las instalaciones (Komai, 1998; Solari, 2004 y Viswanathan, 1993):
Corrosión bajo tensión.
Corrosión intercristalina.
Corrosión -Oxidación.
Corrosión-Fatiga.
Corrosión por HCl.
Corrosión por picadura.
Corrosión orgánica.
Corrosión Inorgánica por cloruros.
Corrosión por CO2.
Corrosión cáustica.
Corrosión por H2/H2S.
Corrosión por ácido nafténico.
Corrosión por ácido sulfúrico.
Corrosiónpor ácido fluorhídrico.
Corrosión -erosión.
Corrosión bajo aislación.
Corrosión atmosférica.
Corrosión en caliente.
Corrosión galvánica.
Corrosión en rendijas.
Corrosión Biológica.
Estos fenómenos de degradación estructural deterioran el estado físico de equipos y componentes. Estos se pueden reflejar en:
Disminución de la resistencia del material.
Reducción de la sección transversal o del espesor de pared.
Aparición de grietas y otros defectos
Las consecuencias de la acción de los fenómenos de degradación sobre los equipos e instalaciones son:
Reducción en la capacidad de la estructura para soportar cargas.
Probabilidad de fallas inesperadas y catastróficas.
Reducción de la vida remanente de los equipos.
2.2 Selección de materiales
Como ha sido planteado anteriormente, uno de los aspectos más importante a tener en cuenta, en las consideraciones metalmecánicas, al realizar la inversión en una industria de procesos químicos es la selección de materiales. En todos los casos se deben revisar las especificaciones de los aceros con el contratista.
Las particularidades de mercado pueden conducir a la necesidad de empleo de aceros equivalentes. En esos casos, se requiere un análisis profundo para la toma de decisiones.
Como regla, las plantas de procesos químicos utilizan dos familias fundamentales de materiales, para altas temperaturas y para trabajos con sustancias agresivas. Esto obedece a que los procesos se ejecutan a temperaturas y presiones determinadas y en ocasiones frente a determinados medios, con temperaturas y concentraciones diferentes.
La mayoría de los aceros para aplicaciones en planta de procesos químicos, se encuentran dentro de las siguientes categorías: aceros al carbono; aceros al carbono-molibdeno; aceros al cromo-molibdeno de aleación baja e intermedia; aceros inoxidables austeniticos; aceros inoxidables martensítico y aceros inoxidables ferríticos (American Society of Mechanical Engineers [ASME], 2015; Fernández, 2021; InduraSA, 2010; Saquid, 2018 y Viswanathan, 1993).
En la Tabla 1 se lista una gama de aceros inoxidables austeníticos frecuentemente empleados en plantas de procesos químicos, debido a su elevada resistencia a la corrosión en un amplio tipo de ambientes corrosivos, generalmente mayor que la de los aceros Martensíticos o Ferríticos, pero son vulnerables al agrietamiento por corrosión bajo tensión (SCC) en ambientes de cloruro. Estos aceros poseen excelente soldabilidad, mejor que los grados ferríticos y martensíticos; presentan también muy buenas propiedades criogénicas, buena resistencia a alta temperatura y excelente resistencia al impacto aun a temperaturas criogénicas. Algunos aceros completamente austeníticos pueden ser usados a temperaturas tan bajas como -270 °C. En Plantas, equipos químicos y equipos para procesamiento de alimentos, los aceros inoxidables austeniticos ocupan un lugar especial.
En la Tabla 2 se presentan las principales marcas de aceros inoxidables ferríticos que más se emplean en procesos químicos, estos poseen excelente resistencia al “pitting” y a la corrosión por rendija (Crevice) inducida por cloruros. Se les prefiere en general, por su resistencia a la corrosión y bajo costo, más que por sus propiedades mecánicas. Sus aplicaciones típicas son en: Tubos de intercambiadores de calor donde la corrosión bajo tensión sea un problema, por ejemplo, en plantas de procesamiento de petróleo o gas natural; estampado profundo de piezas como, recipientes para industrias químicas y alimenticias, reactores catalíticos y tanques de ácido nítrico. También son muy empleados en componentes que requieren protección contra subidas de temperatura, tales como partes de hornos, boquillas, cámaras de combustión y tanques de agua caliente.
Tabla 1 - Composición química típica de aceros inoxidables austeníticos, en % masa (ASME, 2015; InduraSA, 2010).
Marca | C | Mn | Si | Cr | Ni | P | S | otros |
---|---|---|---|---|---|---|---|---|
201 | 0,15 | 5,5-7,5 | 1,00 | 16,0-8,0 | 3,5-5,5 | 0,06 | 0,03 | 0,25N |
202 | 0,15 | 7,5-10,0 | 1,00 | 17,0-9,0 | 4,0-6,0 | 0,06 | 0,03 | 0,25N |
205 | 0,12-,25 | 14,0-5,5 | 1,00 | 16,5-8,0 | 1,0-1,75 | 0,06 | 0,03 | 0,32-0,40N |
301 | 0,15 | 2,00 | 1,00 | 16,0-8,0 | 6,0-8,0 | 0,045 | 0,03 | |
302 | 0,15 | 2,00 | 1,00 | 17,0-9,0 | 8,0-10,0 | 0,045 | 0,03 | |
302B | 0,15 | 2,00 | 2,0-3,0 | 17,0-9,0 | 8,0-10,0 | 0,045 | 0,03 | |
303 | 0,15 | 2,00 | 1,00 | 17,0-9,0 | 8,0-10,0 | O,20 | 0,15min | 0,6Mo |
303Se | 0,15 | 2,00 | 1,00 | 17,0-9,0 | 8,0-10,0 | O,20 | 0,06 | 0,15min Se |
304 | 0,08 | 2,00 | 1,00 | 18,0-0,0 | 8,0-10,5 | 0,045 | 0,03 | |
304H | 0,04-0,10 | 2,00 | 1,00 | 18,0-0,0 | 8,0-10,5 | 0,045 | 0,03 | |
304L | 0,03 | 2,00 | 1,00 | 18,0-0,0 | 8,0-12,0 | 0,045 | 0,03 | |
304LN | 0,03 | 2,00 | 1,00 | 18,0-0,0 | 8,0-12,0 | 0,045 | 0,03 | 0,10-0,16N |
302Cu | 0,08 | 2,00 | 1,00 | 17,0-9,0 | 8,0-10,0 | 0,045 | 0,03 | 3,0-4,0 Cu |
304N | 0,08 | 2,00 | 1,00 | 18,0-0,0 | 8,0-10,5 | 0,045 | 0,03 | 0,10-0,16N |
305 | 0,12 | 2,00 | 1,00 | 17,0-9,0 | 10,5-3,0 | 0,045 | 0,03 | |
308 | 0,08 | 2,00 | 1,00 | 19,0-1,0 | 10,0-2,0 | 0,045 | 0,03 | |
309 | 0,20 | 2,00 | 1,00 | 22,0-4,0 | 12,0-5,0 | 0,045 | 0,03 | |
309S | 0,08 | 2,00 | 1,00 | 22,0-4,0 | 12,0-5,0 | 0,045 | 0,03 | |
310 | 0,25 | 2,00 | 1,50 | 24,0-6,0 | 19,0-2,0 | 0,045 | 0,03 | |
310S | 0,08 | 2,00 | 1,50 | 24,0-6,0 | 19,0-2,0 | 0,045 | 0,03 | |
314 | 0,25 | 2,00 | 1,50-,00 | 23,0-6,0 | 19,0-2,0 | 0,045 | 0,03 | |
316 | 0,08 | 2,00 | 1,00 | 16,0-8,0 | 10,0-4,0 | 0,045 | 0,03 | 2,0-3,0 Mo |
316F | 0,08 | 2,00 | 1,00 | 16,0-8,0 | 10,0-4,0 | 0,20 | 0,01min | 1,75-2,75Mo |
316H | 0,04- 0,10 | 2,00 | 1,00 | 16,0-8,0 | 10,0-4,0 | 0,045 | 0,03 | 2,0-3,0Mo |
316L | 0,03 | 2,00 | 1,00 | 16,0-8,0 | 10,0-4,0 | 0,045 | 0,03 | 2,0-3,0Mo |
316LN | 0,03 | 2,00 | 1,00 | 16,0-8,0 | 10,0-4,0 | 0,045 | 0,03 | 2,0-3,0Mo; 0,10-0,16N |
316N | 0,08 | 2,00 | 1,00 | 16,0-8,0 | 10,0-4,0 | 0,045 | 0,03 | 2,0-3,0Mo; 0,10-0,16N |
317 | 0,08 | 2,00 | 1,00 | 16,0-8,0 | 11,0-5,0 | 0,045 | 0,03 | 3,0-4,0Mo |
317L | 0,03 | 2,00 | 1,00 | 16,0-8,0 | 11,0-5,0 | 0,045 | 0,03 | 3,0-4,0Mo |
321 | 0,08 | 2,00 | 1,00 | 17,0-9,0 | 9,0-12,0 | 0,045 | 0,03 | 5x%C minTi |
321H | 0,04-0,10 | 2,00 | 1,00 | 17,0-9,0 | 9,0-12,0 | 0,045 | 0,03 | 5x%C minTi |
330 | 0,08 | 2,00 | 0,75-,50 | 17,0-9,0 | 34,0-7,0 | 0,04 | 0,03 | |
347 | 0,08 | 2,00 | 1,00 | 17,0-9,0 | 9,0-13,0 | 0,045 | 0,03 | 10x%Cmin Nb |
347H | 0,04-0,10 | 2,00 | 1,00 | 17,0-9,0 | 9,0-13,0 | 0,045 | 0,03 | 8x%Cmin-1,0Nb |
348 | 0,08 | 2,00 | 1,00 | 17,0-9,0 | 9,0-13,0 | 0,045 | 0,03 | 0,2Co;10x%C |
348H | 0,04-0,10 | 2,00 | 1,00 | 17,0-9,0 | 9,0-13,0 | 0,045 | 0,03 | |
384 | 0,08 | 2,00 | 1,00 | 15,0-7,0 | 15,0-9,0 | 0,045 | 0,03 |
Tabla 2 - Composición química típica de aceros inoxidables ferriticos, en % masa (ASME, 2015; InduraSA, 2010).
Marca | C | Mn | Si | Cr | Ni | P | S | Otros |
---|---|---|---|---|---|---|---|---|
405 | 0,08 | 1,00 | 1,00 | 11,5-14,5 | 0,04 | 0,3 | 0,10-0,3Al | |
409 | 0,08 | 1,00 | 1,00 | 10,5-1,75 | 0,50 | 0,045 | 0,045 | 6x%Cmin-0,75maxTi |
429 | 0,12 | 1,00 | 1,00 | 14,0-1,75 | 0,04 | 0,03 | ||
430 | 0,12 | 1,00 | 1,00 | 16,0-18,0 | 0,04 | 0,03 | ||
430F | 0,12 | 1,25 | 1,00 | 16,0-18,0 | 0,06 | 0,15min | 0,6 Mo | |
430F Se | 0,12 | 1,25 | 1,00 | 16,0-18,0 | 0,06 | 0,06 | 0,15 min Se | |
434 | 0,12 | 1,00 | 1,00 | 16,0-18,0 | 0,04 | 0,03 | 0,75-1,25 Mo | |
436 | 0,12 | 1,00 | 1,00 | 16,0-18,0 | 0,04 | 0,03 | 0,75-1,25Mo;5x%Cmin-0,70mxNb | |
439 | 0,07 | 1,00 | 1,00 | 17,0-19.0 | 0,50 | 0,04 | 0,03 | |
442 | 0,20 | 1,00 | 1,00 | 18,0-23,0 | 0,04 | 0,03 | 1,75;2,50Mo;0,025N; | |
444 | 0,025 | 1,00 | 1,00 | 17,5-19,5 | 1,00 | 0,04 | 0,03 | 0,25N |
446 | 0,20 | 1,50 | 1,00 | 23,0-27,0 | 0,04 | 0,03 |
En la Tabla 3 se presentan algunos de los aceros inoxidables martensiticos, más utilizados en piezas que están sometidas a corrosión y que requieren cierta resistencia mecánica, tales como, aspas de turbinas (Tipo 403), revestimiento de asientos para válvulas, carcasas de bombas, cuerpos de válvulas y compresores, cuchillería, hojas de afeitar e instrumentos quirúrgicos (Tipos 420 y 431), ejes, husos y pernos.
Tabla 3 Composición química típica de aceros inoxidables martensíticos, en % masa (ASME, 2015; InduraSA, 2010).
Marca | C | Mn | Si | Cr | Ni | P | S | OTROS |
---|---|---|---|---|---|---|---|---|
403 | 0,15 | 1,00 | 0,50 | 11,5-13,0 | 0,04 | 0,03 | ||
410 | 0,15 | 1,00 | 1,00 | 11,5-13,5 | 0,04 | 0,03 | ||
414 | 0,15 | 1,00 | 1,00 | 11,5-13,5 | 1,25-2,50 | 0,04 | 0,03 | |
416 | 0,15 | 1,25 | 1,00 | 12,0-14,0 | 0,06 | 0,15min | 0,6 Mo | |
416 Se | 0,15 | 1,25 | 1,00 | 12,0-14,0 | 0,06 | 0,06 | 0,15min Se | |
420 | 0,15min | 1,00 | 1,00 | 12,0-14,0 | 0,04 | 0,03 | ||
420F | 0,15min | 1,25 | 1,00 | 12,0-14,0 | 0,06 | 0,15min | 0,6 Mo | |
422 | 0,20-0,25 | 1,00 | 0,75 | 11,5-13,5 | 0,5-1,0 | 0,04 | 0,03 | 0,75-1,25Mo, 0,75-1,25W, 0,15-0,3V |
431 | 0,20 | 1,00 | 1,00 | 15,0-17,0 | 1,25-2,50 | 0,04 | 0,03 | |
440A | 0,60-0,75 | 1,00 | 1,00 | 16,0-18,0 | 0,04 | 0,03 | 0,75 | |
440B | 0,75-0,95 | 1,00 | 1,00 | 16,0-18,0 | 0,04 0,04 | 0,03 | 0,75 | |
440C | 0,95-1,20 | 1,00 | 1,00 | 16,0-18,0 | 0,04 | 0,03 | 0,75 |
La Tabla 4 contiene los aceros más utilizados en refinerías y planta petroquímica en la construcción de equipos y tuberías para el transporte de hidrocarburos y otras sustancias agresivas. A su vez, la Tabla 5 muestra aceros de amplio uso en calderas de vapor.
Tabla 4 - Aceros utilizados en tuberías en refinería y planta petroquímica (Viswanathan, 2004).
MATERIAL | PIPES AND TUBES | PLATES |
---|---|---|
Carbon steel |
A53, A106, A134,A135, A139, A155,A178, A179, A192,A210, A214, A226, A333, A334, A381,A524, A587 |
A283, A285,A299,A433, A443,A455,A515,A516, A537,A573 |
C-1/2Mo |
A161,A209,A250, A335,A369,A426 |
A204, A302,A533 |
1Cr-1/2 Mo |
A213,A335,A369, A426 |
A387 |
1 1/4 Cr-1/2Mo |
A199, A200, A213, A335,A369, A426 |
A387, A389 |
2Cr-1/2Mo |
A199,A200,A213, A335,A369 |
|
2 1/4Cr-1Mo |
A199,A213,A335, A369,A426 |
A387,A542 |
3Cr-1Mo |
A199, A200, A213, A335,A369,A426 |
A387 |
5Cr-1/2Mo |
A199,A200, A213, A335,A369, A426 |
A357 |
7Cr-1/2Mo |
A199, A200,A213, A335,A369, A426 |
|
9Cr-1Mo |
A199, A200,A213 A335,A369, A426 |
|
Ferritic and Austenitic Stainless steels |
A213,A249,A268, A269,A271,A312, A358,A362,A376, A409,A430,A451, A452,A511 |
A167,A176, A240, A412, A457 |
Tabla 5 - Aceros utilizados en las construcción de calderas de vapor (ASME, 2017, Fernández, 2019).
TIPO DE ACERO | ESPECIFICACIÓN | TEMPERATURA MÁXIMA 0C |
---|---|---|
Carbono | SA36, SA178, SA192, SA210, SA106, SA515, SA516 | 454 |
Carbono-0.5Mo | SA209 | 482 |
1.25Cr - 0.5Mo | SA213 T-11, SA335 P-11 | 552 |
2.25Cr - 1Mo | SA213 T-22, SA335 P22 | 579 |
18Cr - 10Ni | SA213 TP304(H), 321(H), 347(H) | 815 |
En el proceso de montaje de la planta es obligatorio realizar, mediante ensayo no destructivos, comprobaciones de la sanidad de la soldadura y si aparece algún defecto, inmediatamente debe ser reparado; por tal motivo, es recomendable constar con una lista de electrodos de aceros inoxidables (Tabla 6), para acometer dicha reparación con éxitos.
Tabla 6 - Recomendaciones de electrodos de Acero Inoxidable de acuerdo al material base. (InduraSA, 2010).
Material base Aisi no | 10 alternativa Electrodo indura | 10 alternativa Clasificación AWS | 20 alternativa Electrodo Indura | 20 alternativa Clasificación AWS |
---|---|---|---|---|
202 | 308 | E308-16 | 308L | E308L-16 |
301 | 308 | E308-16 | 308L | E308L-16 |
302 | 308 | E308-16 | 308L | E308L-16 |
302B | 308 | E308-16 | 309 | E309L-16 |
304 | 308 | E308-16 | 308L | E308L-16 |
304L | 308L | E308-16 | 347 | E347-16 |
305 | 308 | E308-16 | 308L | E308L-16 |
308 | 308 | E308-16 | 308L | E308L-16 |
309 | 309 | E309-16 | 309L | E309L-16 |
309S | 309 | E309-16 | 309L | E309L-16 |
310 | 25-20 | E310-16 | ||
310S | 25-20 | E310-16 | ||
314 | 25-20 | E310-16 | ||
316 | 316 | E316-16 | 316L | E316L-16 |
316L | 316L | E316L-16 | ||
317 | 317 | E317-16 | 309Cb | E309Cb-16 |
321 | 347 | E347-16 | 308L | E308L-16 |
347 | 347 | E347-16 | 308L | E308L-16 |
348 | 347 | E347-16 | ||
403 | 410 | E410-16 | ||
410 | 410 | E410-16 | 430 | E430-16 |
410NiMo | 13(SLASH)4 | E410NiMo-15 | ||
414 | 410 | E410-16 | ||
416 | 410 | E410-16 | ||
416Se | ||||
420 | 410 | E410-16 | ||
431 | 430 | E430-16 | ||
440A | ||||
440B | ||||
440C | ||||
405 | 410 | E410-16 | 405Cb | E404Cb-16 |
430 | 430 | E430-16 | 309 | E309-16 |
430F | ||||
430FSe | ||||
446 | 309 | E309-16 | 310 | E310-16 |
501 | 502 | E502-16 | ||
502 | 502 | E502-16 |
2.4 Sistema de inspección en componentes y equipos de plantas de procesos químicos
En el campo de la inspección en componentes y equipos de plantas de procesos químicos de nueva creación, es importante para los especialistas, disponer de un sistema de inspección, que les permitan decidir, bajo criterios científico, el estado técnico de todos los equipos y componentes, teniendo en consideración las exigencias de seguridad industrial, las implicaciones económicas y el impacto ambiental.
Un sistema de inspección consta de dos etapas básicas:
Nivel I. Recopilación de la información, relacionada con los certificados de los materiales, fundamentalmente de composiciones químicas y propiedades mecánicas, sustentados en normas y procedimientos.
Nivel II. Inspección mediante ensayos no destructivos, antes, durante y después de terminada la inversión (Fig 2).
En el sistema se incluyen, las premisas que se pueden considerarse para establecer la necesidad de la inspección, a qué componentes inspeccionar, las zonas críticas, los daños esperados, los métodos y técnicas para identificarlos, caracterizarlos y evaluarlos, así como las decisiones posibles para determinar las acciones preventivas y/o correctivas, con ayuda de códigos reconocidos por la comunidad internacional.
En el sistema de inspección de la Fig 2, se observa que en la medida que se avanza en la inspección aumenta la complejidad de los ensayos, iniciando con la inspección visual y finalizando con pruebas hidráulicas, cuando se requiera comprobar hermeticidad. Si lo requiere la inspección, son realizados ensayos complementarios de composición química, metalografía y dureza in situ y medición de tensiones. En el momento que es detectado el defecto, debe ser realizada la reparación, si fuera admisible, o la reposición del componente, como se indica (ASME, 2018).
Conclusiones
Desde el punto de vista metalmecánico, en una inversión de la industria de procesos químicos, para garantizar la resistencia, fiabilidad y durabilidad de los componentes y agregados es de vital importancia aplicar los criterios de análisis de fallas durante el diseño, la fabricación y el montaje. Es esencial la consideración de los fenómenos de degradación que operan y la adecuada selección de los materiales. La aplicación de un sistema de inspección antes, durante y después del montaje, basado en la aplicación de ensayos no destructivos y análisis complementarios, garantiza la detección oportuna de defectos y la posible reparación o reposición del componente.
La selección del material adecuado, que toma en cuenta las condiciones de trabajo a que está sometido el componente, constituye un aspecto determinante para enfrentar los fenómenos de degradación y consecuentemente la aparición de fallas.