INTRODUCCIÓN
El diseño de las transmisiones por engranajes cilíndricos metálicos continúa siendo un tema importante en la ingeniería debido al uso de estos elementos de máquina en las más disimiles aplicaciones. Durante años, los especialistas en esta actividad, han servido de apoyo a los distintos sectores de la industria que utilizan estos componentes, dando lugar a la aparición de normas técnicas, las cuales se han aplicado de manera general logrando aportar uniformidad y seguridad en el diseño de los mismos.
Con el continuo crecimiento de las exigencias técnicas hacia los engranajes debido al aumento de su capacidad de trabajo, han llevado a la necesidad de perfeccionar los métodos de cálculo y en particular, el desarrollo de métodos de selección óptima de sus parámetros. A la vez que existen discrepancias entre los valores de las tensiones de contacto en el flanco del diente calculados por las diferentes normas de diseño de engranajes existentes, a pesar de estar fundamentadas sobre la misma teoría sustentada sobre el modelo de dos cilindros en contacto planteado por Heinrich Hertz en 1882 (Budynas & Nisbett, 2012; Machado, 2000) superponiendo cilindros a los perfiles evolventes de los dientes de los engranajes.
Uno de los métodos más utilizados por los ingenieros para la disminución de las tensiones de contacto y por tanto atenuar las fallas asociadas, es la utilización del factor de corrección. Debido a que las modificaciones del perfil afectan directamente las tensiones en los dientes y, por tanto, a la capacidad de carga y la estabilidad de la transmisión. Las normas disponibles como (DIN, 1964; IS 3756, 2002; ISO 6336-2, 2006) recomiendan la selección de este factor, sin embargo, es sus valores son muy aproximado ya que generalmente se presentan en forma de gráficos o cuadros implícitos. Los autores (Gunay et al., 1996; Karadere y Yilmaz, 2018; Milera et al., 2017), entre otros, hacen uso del método de simulación numérica (elementos finitos) para evaluar el comportamiento tensional de los dientes para varios factores de corrección, y validar la eficacia de este método como vía para la disminución de las tensiones en el flanco del diente. Mientras que otros (Rodríguez y Espinosa, 2000; Rodríguez et al., 2007) mediante análisis geométricos de la transmisión brindan una expresión (ecuación 1) que corresponde al valor de corrección de altura necesarios para obtener el mínimo valor de tensiones de contacto, o lo que es lo mismo, la máxima resistencia a la picadura.
La formulación de dicha expresión parte de una deducción geométrica de la transmisión en la cual x σ Hmin representa el factor de corrección del piñón donde los cilindros teóricos en contacto son iguales (r1=r2, (Fig. 1)), para transmisiones con corrección de altura. La ecuación 1, no tiene en cuenta las restricciones geométricas del dentado comentadas por (Lemos y Delgado, 2007; Merritt, 1975; Rey, 2001; Rodríguez y Espinosa, 2000; Rodríguez et al., 2007), las cuales deben ser chequeadas, según plantean los autores, y reajustar los valores de corrección obtenidos, de ser incumplidas alguna de las restricciones.
Otros trabajos (Caballero et al., 2013; Korta y Mundo, 2017; Marimuthu y Muthuveerappan, 2014; Milojevi´, 2013) se centran en el uso de algoritmos de optimización en los cuales se incluye el factor de corrección como criterio de optimización entre otros parámetros. En estos casos tampoco se tienen en cuenta las restricciones geométricas de la transmisión las cuales pueden ser afectadas por el factor de corrección.
La solución del problema puede ser formulada como un problema de optimización, con restricciones, y resuelto por los métodos de optimización conocidos, donde la determinación de las tensiones de contacto puede ser evaluada por la norma requerida por el diseñador.
El objetivo del presente trabajo es evaluar la influencia del factor de corrección sobre las tensiones de contacto en el perfil del diente, considerando las restricciones geométricas y determinar el factor de corrección para mínimas tensiones de contacto.
MATERIALES Y MÉTODOS
2.1. Metodología
Las normas y métodos de diseño de las transmisiones por engranajes para atenuar la falla por picadura presentadas por: (Merritt, 1975), (Estrems, 1998), (AGMA, 2004), (ISO 6336-2, 2006), coinciden en que el modelo más aceptado para la determinación de las tensiones de contacto ( 𝜎 𝐻 ) se rige por la formulación de la teoría de Hertz Budynas−Nisbett para dos cilindros en contacto. La aplicación de dichos métodos formula una simplificación en la cual se sustituyen los perfiles evolventes de los dientes en contacto por dos cilindros, donde la suma de sus radios r1 y r2 (Fig. 1) es igual a la longitud de la línea teórica de engranaje T1T2.
En la (Fig. 2) se muestra la distribución de las tensiones de contacto en un diente engranado. Siempre que se garantice un factor de recubrimiento mayor que 1.2 (Ԑ ≥ 1.2), en el inicio y final del contacto la carga en el diente es distribuida entre dos pares engranados, de ahí que la zona de mayor nivel de tensiones sea la zona donde solo existe una pareja de dientes en contacto (zona 1 (Fig. 2)).

Fig. 2 Distribución de tensiones de contacto ( 𝜎 𝐻 ) sobre el flanco del diente, 1) Zona de contacto de un solo par de dientes. 2) Zona de contacto de más de un par de dientes. HPSTC) punto superior de contacto de un solo par de dientes. LPSTC) punto inferior de contacto de un solo par de dientes
Cualquier modificación en la geometría del perfil del diente que disminuya la magnitud de las tensiones de contacto ( 𝜎 𝐻 ) reduce la posibilidad de aparición de la falla en el mismo y disminuye la tendencia a su destrucción. Es común utilizar el factor de corrección como vía para atenuar esta falla. Debido a que una correcta selección de los factores de corrección puede hacer la distribución de tensiones en el flanco del diente simétrica con respecto a su punto mínimo, mediante el desplazamiento de la línea práctica de engranajes (AE) sobre la línea teórica (T1T2) (Rodríguez y Espinosa, 2000; Rodríguez et al., 2007) logrando una mejor distribución de tensiones a lo largo del contacto (Fig. 3).

Fig. 3 Distribución de las tensiones antes (izquierda) y después (derecha) de ser corregida la transmisión
La utilización de un factor de corrección adecuado aumenta la resistencia del flanco del diente logrando una mejor distribución de las tensiones de contacto sobre el mismo. Mientras que la elección de valores incorrectos de dicho factor, trae consigo efectos indeseables en la geometría de la transmisión que lejos de aumentar su resistencia la disminuyen, por lo que los límites del factor de corrección están condicionados fundamentalmente por:
Presencia de socavado (límite inferior): El socavado ocurre en engranajes con número de dientes relativamente pequeños, o engranajes que se corrigen con corrección negativa, su límite está determinado por la siguiente ecuación:
Donde:
Z |
Número de dientes |
h a * |
Factor de altura del diente |
x |
Coeficiente de corrección |
m |
Módulo del engranaje |
α |
Ángulo de presión |
De donde se deduce el primer límite para la corrección despejando el factor de corrección obteniendo el factor límite para el cual no exista socavado:
Presencia de aguzado del diente en su punta. (Límite superior): Un criterio aceptado por las normas y algunos autores es que el espesor del diente en su cabeza (S a ), debe ser superior que 0,20 (DIN, 1964; IS 3756, 2002; ISO, 1982) y hasta 0,30 (Rockwen, 2001) veces el valor del módulo, o sea que:

Factor de recubrimiento: Por observaciones experimentales, las normas (AGMA, 2004) sugieren el diseño de engranajes que tengan como mínimo una relación de contacto ε = 1,2. En casos donde se dan correcciones angulares positivas o correcciones de altura corrigiendo positivamente el piñón y negativamente la corona, la relación de contacto tiende a disminuir, por lo que hay que garantizar que no se pierda el contacto ininterrumpido de los dientes, para esto es importante mantener la siguiente relación:
Donde:
Las correcciones angulares negativas o de altura corrigiendo negativamente el piñón y positivamente la corona tienen muy poca aplicación práctica; no obstante, en estos casos no hay que chequear el coeficiente de recubrimiento, pues el mismo aumenta.
2.2. Modelo de optimización
Para la determinación de los factores de corrección para mínimas tensiones de contacto que cumplan con las restricciones geométricas antes preestablecidas (ecuaciones 2, 3, 4) se puede formular el problema como un problema de optimización mono-objetivo con restricciones de la siguiente forma:
Determinar X 1 tal que:
Minimice 𝜎 𝐻 =𝑓( 𝑥 1 , 𝑥 𝑠 )
Sujeto a:
Xs = X 1 + X 2 ; corrección sumaria, asumida como constante de diseño
Xmin ≤ X1 ≤ Xmáx
Donde:
Xmin y Xmáx garanticen las restricciones geométricas (ecuaciones 2 y 3) del dentado en cada engranaje, a la vez que la transmisión garantice un factor de recubrimiento mayor igual a 1,2 (ecuación 4).
En el modelo planteado se define una función objetivo, las tensiones de contacto ( 𝜎 𝐻 ), que pueden ser evaluadas por cualquiera de las normas de diseño existentes (ISO, AGMA, DIN, GOST, etc.), la cual describe una función con un solo mínimo global 𝜎 𝐻𝑚𝑖𝑛 (Fig. 3). Dicha función objetivo se plantea en función de la corrección del piñón (X1) y la corrección sumaria ( 𝜎 𝐻 =𝑓( 𝑥 1 , 𝑥 𝑠 )), con el objetivo de no afectar la distancia entre centros de la transmisión haciendo el modelo válido tanto para corrección de altura ( 𝑥 𝑠 =0 como para corrección angular ( 𝑥 𝑠 ≠0). El valor del factor de corrección para la corona ( 𝑥 2 ) es determinado en cada caso como 𝑥 2 = 𝑥 𝑠 − 𝑥 1 .
Siendo 𝑥 𝑠 una constante de diseño, para cada par engranado, y el factor de corrección del piñón ( 𝑥 1 ) variable en el rango establecido en el modelo (𝑥 min − 𝑥 máx ) que cumpla con las restricciones de las ecuaciones (2, 3 y 4); la solución del problema planteado puede ser determinada por cualquier método de optimización mono-objetivo con restricciones, los cuales fueron utilizados con este fin, a la vez que se desarrolló e implementó (Donéstevez, 2014) una solución numérica, presentada en la (Fig. 4), basada en el conocido método de bisección, descrito a continuación.
2.3. Método de solución numérica del problema de optimización
En el método de solución desarrollado para este trabajo (Fig. 4) requiere de una precisión para su convergencia, pues el mismo está basado en el método numérico de bisección. La precisión establecida para los algoritmos presentados anteriormente es de cinco valores decimales (10-5), la cual en situaciones prácticas podría estar condicionada por la precisión de la máquina herramienta donde se construirán dichos engranajes, en conjunto con las especificaciones del diseño.
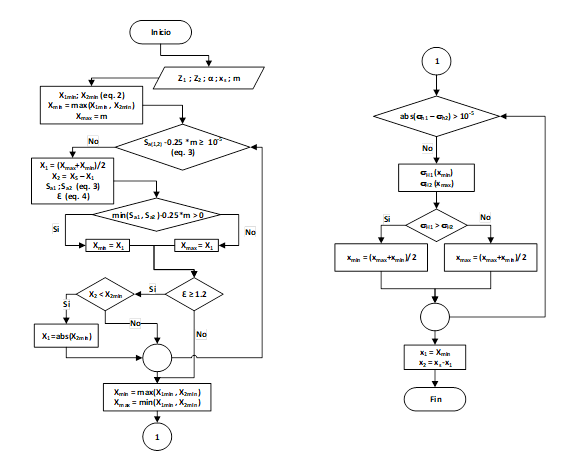
Fig. 4 Diagrama de bloque para la determinación de los factores de corrección máximo para mínimas tensiones de contacto
El algoritmo consta de dos ciclos de convergencia, el primero con el objetivo de buscar los factores de correcciones límites que cumplan con las restricciones geométricas planteadas en las ecuaciones 2-4 que funciona de la siguiente forma:
Determina un factor de corrección que garantice que no hay socavado en ninguno de los engranajes (máx. (X1min, X2min)), obtenidos por la ecuación 2, y es establecido como el factor de corrección mínimo.
El factor de corrección máximo se establece con un valor arbitrario igual al módulo de la transmisión.
El ciclo comienza tomando como punto de parada del ciclo el criterio de la ecuación 3, en busca de la corrección máxima que garantice que no hay afilamiento del diente en ninguno de los engranajes. Los valores máximo y mínimo de corrección van siendo evaluados según las restricciones de la ecuación 3 cambiando su valor utilizando el punto medio entre la corrección máxima y mínima en cada iteración (bisección).
Antes de salir de cada iteración se evalúa el factor de recubrimiento, el cual de ser incumplida esta restricción el ciclo se detiene automáticamente.
El segundo ciclo comienza con las correcciones máximas y mínimas obtenidas previamente, utilizadas como factor de corrección para el piñón (X1) y el factor de corrección de la corona es determinado según la corrección sumaria (X2=Xs-X1); con estos valores se evalúan las tensiones de contacto, por cualquiera de las normas o métodos existentes, para los valores máximo y mínimo del factor de corrección, luego se comparan dichas tensiones para saber hacía cuál de los extremos del factor de corrección se encuentran las tensiones mínimas, y se aproxima su encuentro utilizando nuevamente bisección hasta alcanzar la precisión prescrita al principio.
RESULTADOS Y DISCUSIÓN
La validación del método propuesto se hace partir de la determinación de los factores de corrección obtenidos por el modelo propuesto comparados por los recomendados por el programa de diseño KISSSoft-v2014, evaluadas para las normas (AGMA, 2004; ISO 6336-2, 2006) implementadas por los autores. El análisis se hace a partir de una muestra de 12 pares de engranajes, donde:
Número de dientes piñón (Z1): 17 - 40
Relación de transmisión (u): 1 < u < 4
Módulo del engranaje (m): 1
Factor de altura del diente (ha*): 1
Ángulo de presión: (α) 20°
La (Fig. 5) muestra comparativamente los tiempos de convergencia de los distintos métodos evaluados para los 12 pares engranados, calculados utilizando las tensiones de contacto según la norma (AGMA, 2004). La principal diferencia en el resultado del método numérico presentado y otros algoritmos de optimización conocidos está dada por el tiempo de convergencia de los mismos.
La (Fig. 6) ilustra los resultados obtenidos por cada uno de los algoritmos de optimización con los cuales se determinó el factor de corrección máxima para mínimas tensiones de contacto, dándole solución al objetivo planteado. Los valores del factor de corrección determinados por todos los métodos evaluados arrojan los mismos resultados.
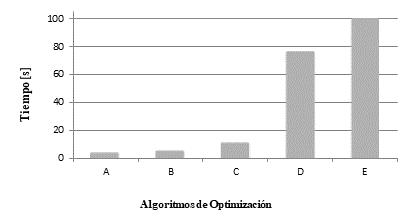
Fig. 5 Comparación del tiempo de convergencia de los diferentes algoritmos de optimización con el método presentado. A) Método presentado. B) Optimización Lineal, C) Optimización no Lineal, D) Algoritmos Genéticos, E) Recocido Simulado
La obtención de valores similares del factor de corrección óptimo para mínimas tensiones de contacto por todos los algoritmos (Fig. 6) garantiza la validez del planteamiento del problema como problema de optimización haciéndolo fiable para la determinación de un valor del factor de corrección que minimiza las tensiones de contacto. Por otra parte, también se valida el algoritmo presentado (Fig. 4), como un algoritmo válido para la solución del problema planteado, lo cual simplifica la implementación de esta solución, siendo más sencilla que cualquiera de los algoritmos clásicos de optimización.
La tabla 1 muestra un análisis comparativo de los resultados obtenidos por el método de optimización planteado y los valores del factor de corrección, para atenuar la falla por picadura, recomendados por el programa comercial KISSSoft-v2014 para las normas de diseño (AGMA, 2004; ISO 6336-2, 2006).
La comparación de los resultados obtenidos con uno de los programas comerciales de diseño más reconocidos (KISSSoft-v2014) valida el planteamiento y solución del problema de la obtención del factor de corrección óptimo para menores tensiones de contacto como un problema de optimización con restricciones geométricas. Las mayores diferencias obtenidas, pueden estar dadas por diferencias en la implementación de las normas por los autores. Teniendo en cuenta que el porciento de error nunca supera el 10% se recomienda ésta metodología.
Tabla 1 Comparación de los valores del factor de corrección obtenidos por el método presentado y los recomendados por el programa de diseño KISSSoft-v2014, para diferentes normas
1 | 0,2869 | 1,0798 | 0,2800 | 1,0090 | 2,,48 | 7,02 |
2 | 0,4061 | 0,7589 | 0,4090 | 0,8010 | 0,72 | 5,25 |
3 | 0,3022 | 1,0140 | 0,3050 | 1,0090 | 0,92 | 0,49 |
4 | 0,2639 | 0,7617 | 0,2620 | 0,7920 | 0,72 | 3,82 |
5 | 0,3870 | 0,7982 | 0,3880 | 0,8420 | 0,26 | 5,20 |
6 | 0,4061 | 0,7589 | 0,4090 | 0,8010 | 0,72 | 5,25 |
7 | 0,3259 | 0,9454 | 0,3280 | 0,9930 | 0,63 | 4,80 |
8 | 0,3870 | 0,7982 | 0,3880 | 0,8420 | 0,26 | 5,20 |
9 | 0,3538 | 0,8736 | 0,3500 | 0,9190 | 1,10 | 4,94 |
10 | 0,3696 | 0,8364 | 0,3970 | 0,8440 | 6,89 | 0,90 |
11 | 0,9505 | 0,9983 | 0,9600 | 0,9600 | 0,99 | 3,99 |
12 | 0,3022 | 1,0140 | 0,3050 | 1,0090 | 0,92 | 0,49 |
En las tabla 2 y tabla 3 se presenta una comparación entre el valor del factor de corrección máxima para mínimas tensiones de contacto expresado por la ecuación 1 y el mismo determinado por los métodos del presente trabajo, mediante un análisis de estos resultados se puede determinar que:
En 9 de los 12 casos presentados, el factor de corrección calculado por la ecuación 1 supera el máximo valor geométrico de corrección que se puede dar (casos marcados con *), por lo que de utilizar la ecuación 1, sin chequear las restricciones (ecuaciones 2, 3 y 4) traería defectos en el dentado (afilamiento).
El factor de corrección determinado por el modelo presentado, determina en cada uno de los casos, geométricamente posibles, tensiones menores que los determinados por la ecuación 1, tanto para la norma ISO como AGMA, aunque las diferencias no son muy notables. Lo que hace del punto anterior el principal fundamento para el uso del modelo presentado en este trabajo sobre el ya defendido en la ecuación 1.
Tabla 2 Tensiones de contacto según norma AGMA evaluada para factores de corrección límite, con Xs = 0, según método presentado y la ecuación 1
|
|
|
|
|
|
|
|
---|---|---|---|---|---|---|---|
1 | -0,520 | 1,079 | 1,468* | 1,079 | 1295,4 | 1273,8 | 21,6 |
2 | 0,005 | 0,758 | 1,005* | 0,758 | 2097,8 | 2054,8 | 42,9 |
3 | -0,403 | 1,013 | 1,518* | 1,013 | 1393,9 | 1358,0 | 35,9 |
4 | -0,637 | 1,143 | 0,458 | 0,761 | 1401,3 | 1408,1 | -6,8 |
5 | -0,052 | 0,798 | 1,952* | 0,798 | 1815,4 | 1637,3 | 178,1 |
6 | 0,005 | 0,758 | 1,156* | 0,758 | 2060,5 | 1989,8 | 70,7 |
7 | -0,286 | 0,945 | 0,648 | 0,945 | 1708,1 | 1723,7 | -15,6 |
8 | -0,052 | 0,798 | 1,506* | 0,798 | 1873,6 | 1763,8 | 109,8 |
9 | -0,169 | 0,873 | 1,198* | 0,873 | 1729,6 | 1693,6 | 36,0 |
10 | -0,111 | 0,836 | 1,060* | 0,836 | 1853,7 | 1825,7 | 27,9 |
11 | -1,04711 | 1,34883 | 0,69917 | 0,99831 | 1083,438 | 1086,537 | -3,1 |
12 | -0,403 | 1,013 | 1,127* | 1,013 | 1454,6 | 1447,6 | 6,9 |
+ Representa factor de corrección obtenido por la ecuación 1.
* Casos para los cuales el factor de corrección obtenido por la ecuación 1, está fuera del rango de las restricciones geométricas planteadas por las ecuaciones 2-4.
Tabla 3 Tensiones de contacto según norma ISO evaluada para factores de corrección límite, con Xs = 0, según método presentado y la ecuación 1
|
|
|
|
|
|
|
|
---|---|---|---|---|---|---|---|
1 | -0,520 | 1,079 | 1,468* | 0,286 | 1241,8 | 1308,9 | -67,1 |
2 | 0,005 | 0,758 | 1,005* | 0,406 | 2292,4 | 2309,0 | -16,5 |
3 | -0,403 | 1,013 | 1,518* | 0,302 | 1378,1 | 1431,3 | -53,1 |
4 | -0,637 | 1,143 | 0,458 | 0,263 | 1235,5 | 1241,4 | -5,9 |
5 | -0,052 | 0,798 | 1,9527* | 0,386 | 2006,9 | 2013,4 | -6,4 |
6 | 0,005 | 0,758 | 1,156* | 0,406 | 2267,0 | 2286,8 | -19,7 |
7 | -0,286 | 0,945 | 0,648 | 0,325 | 1665,5 | 1677,1 | -11,6 |
8 | -0,052 | 0,798 | 1,506* | 0,386 | 2048,1 | 2047,2 | 0,8 |
9 | -0,169 | 0,873 | 1,198* | 0,353 | 1803,9 | 1839,1 | -35,2 |
10 | -0,111 | 0,836 | 1,060* | 0,369 | 1955,9 | 1981,8 | -25,9 |
11 | -1,047 | 1,348 | 0,699 | 0,950 | 944,2 | 964,0 | -19,7 |
12 | -0,403 | 1,013 | 1,127* | 0,302 | 1415,3 | 1456,0 | -40,6 |
+ Representa factor de corrección obtenido por la ecuación 1.
*Casos para los cuales el factor de corrección obtenido por la ecuación 1, está fuera del rango de las restricciones geométricas planteadas por las ecuaciones 2-4.
CONCLUSIONES
La obtención de un valor del factor de corrección, puede ser planteada y resuelta como un problema de optimización con restricciones; considerando los límites del factor de corrección, cumpliendo las restricciones geométricas para evitar el socavado y aguzado del dentado, y con un coeficiente de recubrimiento mayor o igual 1,2.
El modelo presentado determina el valor del factor de corrección para mínimas tensiones de contacto, considerando las restricciones geométricas de la transmisión, para determinar las tensiones de contacto.
El método numérico presentado en el trabajo para la solución del modelo obtiene los mismos resultados que los métodos clásicos de optimización, validando su uso en la solución del problema.
Las diferencias del factor de corrección determinado por el modelo presentado, en comparación con los valores recomendados por el programa de diseño de elementos de máquina KISSSoft-v2014, no difieren en más de un 10%, lo cual avala su validez para su uso futuro. Estas diferencias son significativamente mayores en las normas AGMA lo cual sugiere una revisión en la implementación de las mismas por los autores.