INTRODUCCIÓN
La ampliación tecnológica de la Refinería de Cienfuegos, Cuba, traerá consigo un incremento en los niveles de H2S en los productos y corrientes gaseosas procedentes de las unidades de endulzamiento de gas y, por consiguiente, un incumplimiento de la norma de emisiones gaseosas aprobada para el proyecto (IFC, 2007).
Para mitigar este efecto se prevé la puesta en operación de una unidad recuperadora de azufre (SRU) que se alimentará del gas ácido procedente de la unidad despojadora de aguas ácidas (SWS), unidad de Endulzamiento de Gases Ácidos (GSU) y de la Unidad Regeneradora de Amina existente (ARU), (Lobelles y col., 2016).
Sin embargo, para lograr que la corriente de gas ácido proveniente de la regeneradora de amina existente, se pueda integrar a la alimentación de la unidad SRU, se hace necesario aumentar la presión de operación de la torre regeneradora. Este proceso puede ocasionar problemas operacionales, degradación o pérdidas del inventario de amina, entre otros inconvenientes.
El endulzamiento de gases de una refinería es el proceso utilizado para la remoción de los gases de H2S y el CO2 del gas contaminado (ácido) proveniente de unidades de proceso, con el fin de producir un gas combustible con las especificaciones requeridas para su uso, teniendo en cuenta, que estos compuestos son gases que ocasionan problemas en el procesamiento del gas, así como, también problemas de corrosión, olores perniciosos, emisiones de compuestos causantes de lluvia ácida, entre otros (Boyun et al., 2007).
En dicho proceso se produce la absorción del gas ácido en una solución acuosa de amina. La corriente de gas a endulzar y la corriente de amina se ponen en contacto en una torre absorbedora. En esta torre los componentes ácidos del gas reaccionan con la amina y forman un complejo que es soluble en la fase líquida (Haghtalab, 2010). Para que la reacción se lleve a cabo se deben cumplir las siguientes condiciones: presión elevada y temperatura baja (Behroozsarand y Zamaniyan, 2011). Por el tope de esta torre se obtiene una corriente de gas dulce, y por el fondo se obtiene una corriente de amina rica. A fines de minimizar costos de operación y de mitigar la contaminación al medio ambiente se regenera la corriente de solvente. Para ello, se alimenta la corriente de amina rica a una torre regeneradora donde se lleva cabo la desorción de los componentes ácidos. Las condiciones de esta torre regeneradora son opuestas a las condiciones de la torre absorbedora. La corriente de amina pobre se enfría y presuriza para realimentarla a la torre absorbedora (Wankat, 2008).
Los procesos de remoción de gases ácidos utilizados en las refinerías son realizados con objetivos operacionales, para la obtención de hidrógeno y por razones medioambientales (remoción azufre). La quema de H2S conlleva a la aparición de SO2 que junto al NOx provocan las lluvias ácidas que son producidas por la exposición de los compuestos anteriormente citados con la humedad atmosférica mediante la cual se forma ácido sulfúrico diluido. Este compuesto también causa excesiva corrosión en los metales y estructuras industriales (Abedini y col., 2010).
En general los procesos con aminas son los más usados por su buena capacidad de remoción, bajo costo y flexibilidad en el diseño y operación. Las alcanol-aminas más usadas son: Monoetanolamina (MEA), Dietanolamina (DEA), Trietanolamina (TEA), Diglicolamina (DGA), Diisopropanolamina (DIPA) y Metildietanolamina (MDEA), (Erdmann et al., 2012).
Los procesos con aminas son aplicables cuando los gases ácidos tienen baja presión parcial y se requieren bajas concentraciones del gas ácido en el gas de salida (gas residual). La fórmula química de este compuesto es (CH3) N(CH2-CH2-OH)2
La MDEA es una amina terciaria que reacciona lentamente con el CO2, por lo cual, para removerlo requiere de un mayor número de etapas de equilibrio en la absorción. Su mejor aplicación en la absorción, es la remoción selectiva del H2S, cuando en los gases ácidos están presentes H2S y CO2, esto convierte a la MDEA, en un compuesto selectivo de alta efectividad, para remover al sulfuro de hidrógeno (Brito, 2015).
Una ventaja de la MDEA, para la remoción del CO2 es que la solución contaminada o
rica se puede regenerar por efectos de una separación flash.
En tal sentido, es objetivo del presente estudio analizar la influencia de los parámetros operacionales del regenerador de aminas para suministrar H2S a la unidad recuperadora de azufre..
MATERIALES Y MÉTODOS
La unidad de regeneración está diseñada para regenerar 43 860 kg/h de amina rica con un contenido de H2S de 1,56 % molar que permite obtener una corriente de amina pobre de 43 190 kg/h con un contenido máximo de H2S de 0,02 % molar.
Tipo de amina MDEA. Concentración de amina 40 % peso. Caudal de circulación a regeneración 42,1 m3/h. Carga amina rica 0,172 moles H2S/mol amina. Carga amina pobre 0,002 moles H2S/mol amina, reportado por (Vargas y González, 2005; Sohbi et al., 2007) sobre trabajos realizados por diferentes autores. Las características de las corrientes de la unidad de regeneración de amina se muestran en la Tabla 1.
Tabla 1 Características de la amina rica en sulfuro, amina pobre en sulfuro de hidrógeno y del gas ácido
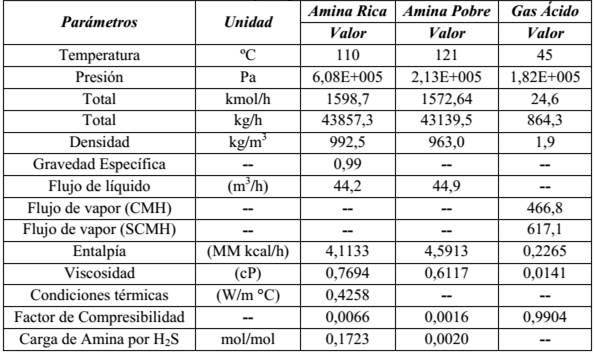
2.1 Metodología para analizar los parámetros operacionales del regenerador de aminas
La unidad regeneradora de amina está compuesta por intercambiadores que aprovechan la energía de la corriente de salida de la torre para calentar la corriente de alimentación a la misma. Teniendo en cuenta las características de este proceso se selecciona el simulador CHEMCAD (Gutiérrez y col., 2011), ya que es uno de los simuladores que contiene el paquete termodinámico de amina, necesario para la simulación de la unidad de regeneración de aminas. Esto permitirá la validación del modelo a estudiar. Para lograr el objetivo antes expuesto se trazaron las siguientes tareas:
Obtener el modelo de simulación.
Validación del modelo a través del ajuste del caso base.
Análisis de sensibilidad del modelo.
2.1.1. Obtención del modelo de simulación:
Para obtener un modelo de simulación se deben seguir los siguientes pasos:
Construcción del diagrama de flujo de información.
Definir el orden de cálculo.
Definir los módulos e implementar el simulador.
A continuación, se hace una descripción de cada uno de ellos.
2.1.2. Construcción del diagrama de flujo de información
La elaboración de un diagrama de flujo de información no es más que un diagrama donde los flujos de masa o energía del proceso son equivalentes a flujos de información (valores numéricos de las variables de las corrientes y parámetros necesarios para definir los módulos), y los equipos del proceso equivalentes a modificaciones de la información que fluye entre ellos (Romero y Vásquez, 2013).
Los diagramas de flujo se transforman en diagramas de flujo de información (DFI) para la simulación del proceso, teniendo en cuenta la cantidad de módulos que representa a una operación o proceso.
2.1.3. Definir el orden de cálculo:
Para el caso en estudio no será necesario aplicar el método de Scenna (1999), teniendo en cuenta que el simulador CHEMCAD no es modular, por lo que no se consideran corrientes de corte.
2.1.4. Validación del modelo de simulación
Ajuste al caso base:
Con los resultados obtenidos se realizó un análisis comparativo entre los parámetros de diseño y los resultados obtenidos en la simulación de la torre regeneradora de amina, como criterio de comparación se define el error relativo mediante la Ecuación 1:
Donde: 𝑒 𝑟𝑒𝑙𝑎𝑡𝑖𝑣𝑜 : Error relativo (%); 𝑥 𝑑𝑖𝑠𝑒ñ𝑜: Valores de diseño (ºC; Pa; kmol/h); 𝑥 𝑐𝑎𝑙𝑐𝑢𝑙𝑎𝑑𝑜 : Valores calculados por el simulador (ºC; Pa; kmol/h)
La diferencia entre el resultado de los valores calculados y los de diseño tienen que ser menor 10 %, esto fundamenta la confiabilidad del modelo en las operaciones en planta.
Análisis de sensibilidad:
Para el análisis de sensibilidad del modelo, se realiza un diseño de experimentos donde se definen un nuevo flujo de entrada a la torre regeneradora, la composición de H2S en dicha corriente y como variable dependiente la concentración de H2S en la corriente de salida (gas ácido) de la torre.
2.2. Estudio del caso base
En el estudio de caso se analiza el comportamiento de los parámetros operacionales en las corrientes de salida de la torre regeneradora al variar la presión en el tope de la misma, de la siguiente forma:
Variación de la presión en el tope de la torre regeneradora de 1,74E+005 - 2,94E+005 Pa.
Teniendo en cuenta las condiciones siguientes:
Composición de la MDEA en la amina pobre y el H2S gas ácido en las corrientes de salida, porque no es conveniente que en la amina pobre tenga presencia de sulfuro de hidrógeno y en el gas ácido exista amina.
Temperatura en la corriente de salida de la amina pobre, debe estar entre 125-150 °C, superior a este rango podría ocurrir la degradación de la amina.
RESULTADOS Y DISCUSIÓN
Con la metodología descrita anteriormente se construye el Diagrama de Flujo de Información (DFI) (Figura 1) y se obtiene el modelo de simulación para la evaluación de la Unidad Regeneradora de Amina (Figura 2).
3.1 Validación del modelo de simulación
Con el modelo de simulación representado en la Figura 2, se realizó inicialmente una primera corrida estableciendo la presión de entrada a la torre en 6,08 Pa y un flujo total de entrada de 1598,7 kmol/h; obteniendo una presión de tope de 1,74 Pa con una concentración de H2S en la corriente de gas ácido de 24,5986 kmol/h, así como, de 0,371479 kmol/h en la corriente líquida de amina pobre. Esta primera corrida fue comparada con los valores de diseño de la torre para poder validar la efectividad de dicho modelo de simulación, los resultados se muestran en la Tabla 2.
En la Tabla 2 se muestran los resultados del ajuste del caso base, en el cual se calcula el error relativo que se comete entre los parámetros operacionales de las corrientes de salida de diseño y los simulados por CHEMCAD. Se puede apreciar que los errores al simular, no superan el valor de un 10% comparado con las condiciones de diseño, lo cual demuestra que el modelo representa adecuadamente el sistema.
Tabla 2 Comportamiento de las corrientes de salida
Temperatura (°C) | 45 | 44,12 | 1,9 |
Presión (Pa) | 1,77E+005 | 1,74E+005 | 1,69 |
Flujo total (kmol/h) | 26,1 | 26,1004 | 0,0015 |
Composición H2S (kmol/h) | 24,68 | 24,6 | 0,32 |
Temperatura (°C) | 121 | 121,7 | 0,58 |
Presión (Pa) | 2,06E+005 | 2,12E+005 | 2,91 |
Flujo total (kmol/h) | 1583,6 | 1572,64 | 0,69 |
Composición H2S (kmol/h) | 0,38 | 0,37 | 2,63 |
Con la variación del flujo total de entrada, la composición de sulfuro de hidrógeno en la corriente de gas ácido, se comporta de forma proporcional (Figura 3). Lo que demuestra la validación del modelo de simulación para el caso en estudio. Posteriormente se realizaron siete nuevas corridas variando la presión de tope de la torre regeneradora para evaluar el comportamiento de los demás parámetros operacionales de dicha torre, así como, las variaciones en sus salidas líquidas y gaseosas (Ver Tabla 3).
3.2 Análisis de parámetros operacionales del sistema de regeneración de amina.
La implementación de una unidad regeneradora de amina permite procesar la amina rica proveniente de la sección de hidrofinación de diésel, que tiene un alto contenido de azufre y es regenerada para luego ser utilizada en dicho proceso de hidrofinación. En el caso de estudio se evalúa la variación de los parámetros operacionales de la planta regeneradora de amina, para lograr la materia prima necesaria a la planta recuperadora de azufre, evitando pérdidas y fallos operacionales. En este caso se harán varias corridas del modelo de simulación variando la presión del tope de la torre regeneradora de amina en el rango de 1,74E+005-2,94E+005 Pa.
3.3 Comportamiento de la torre regeneradora de amina.
Con la variación de la presión en el tope de la torre se obtiene el comportamiento del modelo simulado. La Figura 4 muestra que al variar la presión desde 1,74E+005- 2,94E+005 Pa en el tope de la torre no ocurren cambios desmedidos en la composición del H2S en la corriente de gas ácido. Pero trabajando con un rango de 1,91E+005- 2,26E+005 Pa, que es suficiente para poder introducir la corriente de gas ácido en el tambor de materia prima a la planta recuperadora de azufre, la variación de la composición del H2S es tolerable, lo cual define dicha posibilidad.

Figura 4 Comportamiento de la composición del H2S en la corriente de gas ácido al variar la presión en el tope de la torre
La Figura 5 muestra que no existe variación apreciable en la composición de la MDEA en la corriente de amina pobre al variar la presión en el tope de la torre y como consecuencia en el fondo de la misma.

Figura 5 Comportamiento de la composición de la MDEA en la corriente de amina pobre al variar la presión en el tope de la torre y como consecuencia en el fondo
La Figura 6 muestra un comportamiento prácticamente lineal de la temperatura, por lo que es improbable que ocurre una degradación de la amina, pues la temperatura se desplaza desde (121,698 - 121,702) °C.
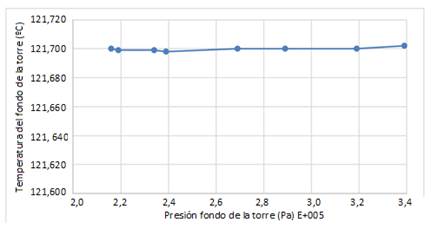
Figura 6 Comportamiento de la temperatura en el fondo de la torre al variar la presión en el tope de la torre y como consecuencia en el fondo.
Por otra parte, en la Tabla 3, se puede apreciar el comportamiento general de las corrientes de salida (líquida y gaseosa) ante los diferentes cambios de presión en la torre regeneradora de amina (ocho corridas), así como, las diferentes variables operacionales del proceso. En ella queda demostrado que no ocurren cambios significativos en la composición del H2S en las corrientes de salida y que en el rango de 1,91E+005- 2,26E+005 Pa de presión de tope los cambios son aceptables, demostrándose entonces, que sí es posible garantizar, con estas condiciones operacionales, una correcta alimentación de H2S a la unidad recuperadora de azufre.
CONCLUSIONES
El modelo de simulación del proceso de regeneración de amina queda validado al obtener en el análisis de las corrientes de diseño y las de simulación un error menor del 3 % de un 10 % permisible para la validación.
Al evaluar el comportamiento de la torre regeneradora de amina con la variación de la presión desde 1,74E+005-2,94E+005 Pa, queda demostrado que, sí se puede lograr la entrada del gas ácido al tambor de alimentación a la planta recuperadora de azufre, pues no afecta significativamente la composición del H2S en la corriente de gas ácido, ni la composición de la MDEA en la corriente de amina pobre.
Luego de tener un comportamiento de la simulación de la torre de amina se puede proponer un rango de presión en la corriente de gas ácido entre 1,91E+005-2,26E+005 Pa, con la cual se obtiene una composición del H2S en dicha corriente entre 24,36 - 23,90 kmol/h y en la corriente de amina pobre una composición de MDEA entre 144,898 - 144,899 kmol/h. La temperatura para estos parámetros descritos no supera el valor de 121,7 °C, lo que elimina la posibilidad de la degradación de la amina y por ende pérdidas.