INTRODUCCIÓN
El empleo de ensayos de laboratorio para evaluar la resistencia al desgaste de materiales es una de las técnicas más comunes aplicadas en la caracterización de materiales de ingeniería y depósitos de recargue. Según refiere Cozza, (2006), uno de los primeros ensayos de abrasión fue realizado por Mikhail Lomonosov, miembro de la Academia Científica de Moscú entre los años 1745 y 1765, con el objetivo de estudiar la abrasión en los metales, minerales y vidrios. Desde entonces los ensayos con ese objetivo han seguido evolucionando y desarrollándose variantes para aplicaciones específicas, algunas de ellas normados por instituciones especializadas en la materia, como la Sociedad Americana de Ensayos de Materiales (ASTM, por sus siglas en inglés), y otros que no han sido normados, pero su aplicación se respalda en su factibilidad técnica y la reproducibilidad de las mediciones (Cruz-Crespo et al., 2019) y (Cruz-Crespo et al., 2019).
Cozza (2006), Cozza (2013), Gant y Gee, (2011) y Badisch y Mitterer, (2003) plantean que en las últimas décadas, para el estudio del desgaste abrasivo de aleaciones ferrosas, se ha extendido el uso del método de ensayo microabrasivo con esfera rotativa, inicialmente aplicado en la medición de espesores de revestimientos. Esto se debe a sus probadas ventajas, entre las que se encuentran la rapidez del ensayo, el pequeño tamaño de las zonas de estudio y por tanto de las muestras, así como el uso de equipamientos relativamente baratos. Lo anterior contribuye a disminuir los costos de los trabajos de caracterización sin que decaiga la calidad del estudio, respaldado además por la reproducibilidad de las mediciones (Adachi y Hutchings, 2005). Basado en lo anterior, Stachowiak et al., (2006) lo describen como un ensayo que puede sustituir los normalizados con ese fin.
Dentro del método de ensayo de desgaste microabrasivo se han desarrollado diferentes configuraciones del equipamiento, siendo la nombrada como “ensayo microabrasivo con esfera rotativa libre” la de mayor sencillez constructiva y operativa. Este ensayo está estandarizado para el estudio de recubrimientos cerámicos bajo las normas BS EN 1071-6 (2007) e ISO 26424 (2008), pero la eficacia de su uso en materiales metálicos, tales como las fundiciones blancas aleadas, ha sido demostrada por diversos autores (De Mello y Polycarpou, 2010), (Stachowiak et al., 2006).
Este ensayo consiste en generar desgaste en un cuerpo de prueba debido a la acción de rotación de una esfera sobre su superficie, con la participación de pequeñas partículas abrasivas que se suministran a la zona de ensayo mediante un sistema de alimentación, Figura 1, (Cozza, 2014) y Cozza (2013). Las partículas están en forma de suspensión dentro de un volumen de agua, formando una mezcla abrasiva, de una concentración dada. El resultado del ensayo es un cráter de desgaste, con geometría esférica, en la superficie (Figura 1b). La carga estática que actúa sobre la superficie está determinada por el peso de la bola rotatoria y el ángulo de inclinación de la superficie a ensayar.
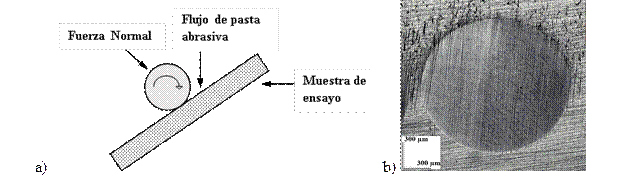
Figura 1 Ensayo de desgaste microabrasivo con esfera rotativa libre. a) Imagen típica de la huella de desgaste, b) principio de funcionamiento
Dada la variedad y complejidad de los mecanismos de desgaste, es común que se realicen estudios de caracterización del depósito de recargue previo a la elaboración del procedimiento de soldadura, con el objetivo de evaluar el desempeño del material de aporte frente a determinadas condiciones de trabajo, así como el efecto del régimen de soldadura y el número de capas del depósito (Oliveira et al., 2014), (Oliveira, 2015), (Ortiz-Méndez et al., 2019). En estos casos ha sido demostrada la efectividad del ensayo microabrasivo, ya que debido al pequeño tamaño de la huella de desgaste la precisión del método no se afecta por los defectos en el acabado superficial típicos en los depósitos de recargue (agrietamiento o porosidad del depósito). A lo anterior se suma la facilidad que brinda para la fijación precisa de la zona de ensayo y con ello la posibilidad de realización de perfiles de desgaste en función de la dilución de la capa de recargue.
En base a lo planteado, el presente trabajo tiene como objetivo desarrollar un equipo de ensayo microabrasivo con esfera rotativa libre, destinado a la caracterización de materiales metálicos y depósitos de recargue, empleando soluciones de diseño que permitan su fabricación económica.
MATERIALES Y MÉTODOS
Se empleó el software “Autodesk Inventor Professional 2014” para el diseño de cada una de sus piezas, la elaboración de los planos y la comprobación de resistencias de los elementos más cargados del conjunto, a partir de la modelación de las cargas y desplazamientos. Los materiales empleados fueron acero de construcción GOST 9XBG para la fabricación del eje, acero al carbono AISI 1020 para los tornillos y las guías, y una aleación de aluminio con clasificación ASM 6063 T832 para la estructura base y el porta muestras.
La máquina de ensayo fue construida en el Taller de Antenas Profesionales y otras producciones pertenecientes a la Empres de Antenas, de Villa Clara, Cuba, basado en una estrategia de cooperación Universidad-Empresa. Las piezas fueron elaboradas mediante maquinado (cizallado, torneado, fresado y barrenado), tratamiento térmico (temple y revenido bajo al eje) y el proceso de soldadura con protección gaseosa (argón) y electrodo de tungsteno (GTAW, según sus siglas en inglés), para la fabricación de la estructura de aluminio y los sistemas de posicionamiento de la muestra. Como material de aporte para la soldadura se emplearon varillas de clasificación ER 4043.
La circularidad de las huellas de desgaste obtenidas con este tipo de ensayo tiene un elevado efecto en la calidad de las mediciones de desgaste. La falta de circularidad es evidencia de elevadas vibraciones del equipo y de falta de alineación del eje respecto al plano de ensayo de la muestra de estudio (Oliveira, 2015). Es por esto que se utilizó este criterio como parámetro de ajuste del equipo de ensayo fabricado. Con este fin se empleó muestra constituida de un material de alta dureza (acero GOST X12M templado y revenido).
Para la determinación de las variables de ensayo se partió de experiencias previas en aplicaciones del ensayo microabrasivo con esfera rotativa libre sobre materiales metálicos, tales como en los trabajos de Stachowiak et al., (2006), Camerini, (2011), (De Barros, 2014), entre otros. Sobre esta base se seleccionó la alúmina como material abrasivo en concentración de 15 g/100 ml de agua destilada, una frecuencia de goteo de 1gota/10 s, un tiempo de ensayo de 20 minutos bajo el efecto de la fuerza normal de 0,24 N. Para la visualización y medición del diámetro de la huella se empleó un microscopio portátil (read-out), de bajo aumento con un poder de resolución de 24x, marca MPB-2T, de fabricación soviética. Se midió la huella en el eje horizontal (dx), vertical (dy) y diagonal (d45º), es decir a 45º respecto a x. Se realizaron tres réplicas del ensayo.
RESULTADOS Y DISCUSIÓN
3.1. Diseño del equipo de ensayo microabrasivo con esfera rotativa libre
Como paso previo al diseño de la máquina de ensayo microabrasivo con esfera rotativa libre, basado en las características del ensayo (Suzuki, 2006), (Stachowiak et al., 2006), se establecieron los requisitos específicos que deben ser cumplidos, los cuales se relacionan a continuación:
1. Eje motriz de disposición horizontal, con velocidad de giro en el rango entre 37 y 100 rpm, que garantice la trasmisión eficiente del movimiento giratorio a una esfera.
2. Sistema de desplazamiento del portamuestras que permita establecer y modificar el punto de aplicación de la carga en la superficie de la muestra, es decir, ajustar la zona de estudio según las necesidades de la experimentación.
3. Mecanismo para garantizar la fijación del ángulo de inclinación de la muestra con respecto al plano horizontal.
4. Método que garantice de manera estable la frecuencia de goteo seleccionada para la experimentación.
5. Rigidez del equipo, que minimice las vibraciones para evitar su efecto sobre la circularidad de la huella de desgaste y con ello en la calidad de la medición.
A lo anterior se suman otros requisitos indispensables, como son: la sencillez del equipamiento, su facilidad de operación, la adecuada resistencia frente a las condiciones de trabajo, lo que garantiza la durabilidad, economía y facilidad de mantenimiento, además del buen aspecto.
En la Figura 2 se muestra un diseño conceptual de la máquina de ensayo microabrasivo con esfera rotativa libre que garantiza estos requisitos de diseño, como una idea de partida para el diseño y dimensionamiento de sus partes. Con este fin se empleó el software “Solidworks2022”.
El sistema motriz tiene como función suministrar el movimiento rotacional del eje a la esfera rotativa o bola. Para esto es necesario calcular la potencia máxima (𝑃𝑚𝑎𝑥) exigida según los requisitos del equipo, lo cual se realiza basado en el procedimiento desarrollado por Suzuki, (2006). Para ello se establece el diámetro de la esfera rotatoria de 27 mm, constituida de acero AISI 52100, a partir de lo cual se obtiene una potencia necesaria en el motor de 0,48 W.
El eje se encarga de la trasmisión del movimiento desde el motor hacia la esfera mediante la interferencia con la bola rotatoria, para lo que se requiere una distancia entre los puntos de contacto entre el eje y la bola de un 70 % del diámetro de la esfera (Figura 3), (Suzuki, 2006). Para su fabricación fue seleccionado un acero para construcción clasificado por la norma GOST 5950 como 3X2B6, con un tratamiento térmico de mejoramiento para aumentar la resistencia al desgate del material en la zona de contacto con la esfera bajo el efecto de la pasta abrasiva.
Se seleccionó un pedestal para el soporte del eje del tipo de pie con rodamiento auto-centrante, compuesto por un rodamiento radial de bolas, el sello y un soporte de acero fundido, con capacidad de carga superior al valor de la reacción en los apoyos del eje (0,40 N).
Con vistas a la fijación de la muestra de ensayo se diseñó un conjunto al que se nombró “base inclinada del portamuestras”, Figura 4, el cual permite, además, la fijación del ángulo de la superficie de ensayo y el posicionamiento en el eje “y”. Para lograr el desplazamiento de la muestra en los ejes “x” y “z”, además de fijar la distancia entre el eje y la muestra, se diseñó la “base horizontal del portamuestras” (Figura 4b).
La “base del equipo” (Figura 4c) es la encargada de sostener y fijar los mecanismos que componen la máquina de ensayo. Con vistas a garantizar la ligereza, buena apariencia y adecuada resistencia a la corrosión ambiental, se seleccionó aluminio de clasificación SAE 6063 T832 para el diseño de estas piezas. Se consideró la fijación de los pedestales a la base mediante atornillado, al igual que la fijación de los ejes para el sistema de desplazamiento del porta-muestras.
A partir del peso de la bola de 0,7 N y del peso máximo que puede alcanzar la muestra, de 1,2 N considerando las dimensiones del portamuestras, agregando además el peso de los diferentes mecanismos sobre la base del equipo, se realizó la modelación de las tensiones y deformaciones con el empleo del software “Autodesk Inventor Professional 2014”.
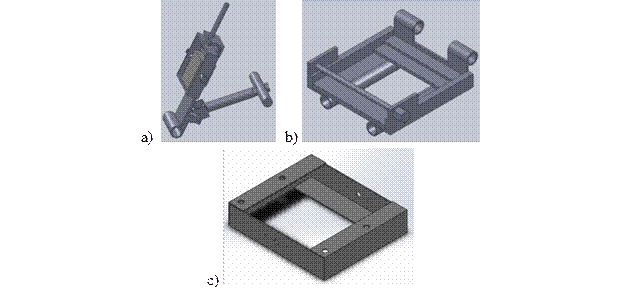
Figura 4 Esquemas de la base inclinada del portamuestra (a), la base horizontal del porta-muestra (b) y la base del equipo (c)
En todos los casos, las tensiones de Von Mises obtenidas en los puntos críticos de las diferentes partes están por debajo de límite elástico del material, lo cual demuestra su rigidez. Igualmente el factor de seguridad superó por lo general el valor de 10 y los desplazamientos máximos resultan despreciables, desde el punto de vista de los requisitos de funcionamiento de esta máquina de ensayo. En la Figura 5 se muestran los resultados de la simulación en la base del equipo que resultó ser la pieza más cargada.
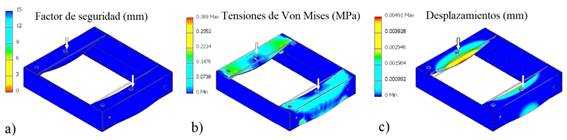
Figura 5 Resultados de la simulación de la base del equipo, a) factor de seguridad, b) tensiones de Von Mises y c) desplazamientos
En la Figura 6 se muestran el equipo luego de ensamblado, así como los diferentes sistemas que garantizan la ubicación y los desplazamientos de la zona de ensayo.
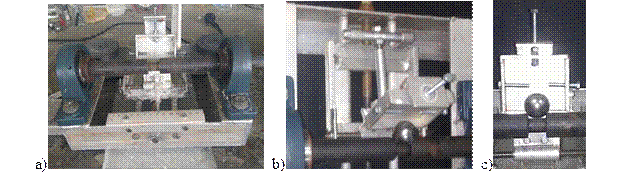
Figura 6 Equipo de ensayo de desgaste microabrasivo (a), detalles de los mecanismos de posicionamiento de la zona de ensayo y fijación de la muestra (b y c)
Para la selección del motor se tuvo en consideración la recomendación de Cozza et al., (2009), al referir la posibilidad de ocurrencia del efecto hidrodinámico a alta velocidad de soldadura, por lo cual fue seleccionado un motor reductor de corriente directa marca “VEB Elektromotorenwerk Hartha/Kreis Döbeln”, de fabricación alemana, que brinda una velocidad de rotación del eje de salida de 70 rpm.
3.2. Ajuste del equipo
En la Figura 7 se muestra una huella representativa, obtenida con el equipo de ensayo microabrasivo desarrollado y con los parámetros seleccionados para su ajuste sobre una muestra de material de alta dureza (acero GOST X12M). En ella se observa una adecuada definición del contorno, que permite realizar la medición de la huella con un microscopio de bajo aumento como el empleado.
El estudio de circularidad de las huellas arrojó los resultados mostrados en la Tabla 1.
Del análisis de las mediciones puede apreciarse que la variación del diámetro está en el orden de las centésimas de mm, con un coeficiente de variación que tiende a cero lo que evidencia la poca variabilidad de las mediciones y avala una alta circularidad de la huella. Esto apunta a la no existencia de vibraciones que afecten el funcionamiento del equipo y demuestra que los parámetros seleccionados son correctos para materiales de alta dureza.
Tabla 1 Resultados de las mediciones de las huellas
Diámetro de la huella (mm) | dx | dy | d45º | dx | dy | d45º | dx | dy | d45º |
1,325 | 1,300 | 1,325 | 1,350 | 1,325 | 1,300 | 1,350 | 1,300 | 1,300 | |
Valor medio del diámetro (mm) | 1,317 | 1,325 | 1,317 | ||||||
Coeficiente de variación (%) | 0,89 | 1,54 | 1,79 |
CONCLUSIONES
1. Dados los requisitos de diseño del equipo de ensayo de desgaste microabrasivo con esfera rotativa libre, este presenta una configuración sencilla. Los esfuerzos mecánicos a que se someten sus partes son relativamente bajos, lo que permite el diseño de la mayoría de sus partes con empleo de materiales de baja resistencia mecánica y ligeros.
2. La sencillez en el diseño del equipo de ensayo microabrasivo con esfera rotativa libre, así como sus pequeñas dimensiones, permite la fabricación de sus partes y mecanismos con el empleo de procesos y máquinas herramientas convencionales, mediante operaciones simples y un mínimo consumo de materias primas.
3. Las huellas obtenidas con el equipo desarrollado sobre un acero GOST X12M tratado térmicamente, con el empleo de alúmina como abrasivo en una concentración de 15 g/100 ml de agua destilada, una frecuencia de goteo de 1gota/10 s, un tiempo de ensayo de 20 min y una fuerza normal de 0,24 N, presentan adecuada circularidad y definición del contorno, lo que indica la no existencia de vibraciones que afecten el funcionamiento del equipo y demuestra que los parámetros seleccionados son correctos para materiales de alta dureza.