Introduction
Internal flows in pipe networks appear in various parts of today’s industrialized society. From the supply of potable water [1,2] to the transportation of chemicals and other industrial fluids [3,4], engineers have designed and built countless miles of piping systems [5]. In the design process of pipe networks, engineers must ensure that the design criteria (e.g., flow rates in the pipes and heads on the nodes) are satisfied with a minimum cost in terms of material, installation, etc. This optimum design of pipe networks can be addressed by optimization techniques.In fact, such an approach has been employed for designing water distribution systems since 1970’s [6]. In what concerns the optimization methods, stochastic methods such as Genetic Algorithmsare widely adopted rather than classical deterministic ones. This stems from the difficulty of deterministic methods in working with commercial diameters which are not continuous functions [6]. The primary requirement or objective in a pipe network design is the cost associated with the chosen commercial diameters. According to [7], this cost is responsible for approximately 70% of the total cost of the network [8].
The methods for solving the flow equations in pipe networks required in the optimization process are not trivial in their majority and not unique because nonlinear equations are always present in the model of hydraulic systems. Generally, two methods, namely, Hardy Cross [3,4,9] and Newton-Raphson are widely employed [2]; besides, they can be classified as indirect or direct.The indirect Hardy Cross methodrequires a set of interior loops and its application to large pipe networks is quite cumbersome. On the other hand, the application of theNewton-Raphsonis straightforward since onlynodal equations are required. Finally, a proper manipulation of the nonlinear equations gives rise to a finite element based method in which element matrices concerning the pipes are assembled to yield the final system of nonlinear equations. Differently from the Newton-Raphson method, in the finite element based method the time required for preparing input data is much reduced [10,11].
In the hydraulic model, it is important to define a correlationthat accounts for the frictional energy loss.The Hazen-Williams (HW) and Colebrook are the mostcommon correlations. The former is widely used in articlesbased on optimization procedures [1,2,6,12,13,14,15] due to its easy computational implementation, while the latter is more general but requires a solution of a nonlinear equation and, therefore, not widely employed in such a context.Moreover, due to the great randomness of GA, a wide range of Reynolds numbers is likely to be explored, leading to a non-recommendation of strict use of the HW correlation.Bearing in mind this fact, the present workpresents a comparison between the HW and Colebrook correlations when applied tothe optimization of pipe networks by the GA, discussing the importance of selecting appropriate correlations in order to yield meaningful results generated by the GA.Furthermore, the developed GA based program is characterized by the implementation of a mixed crossover operator, mutation per variable and a dynamic penalty strategy. The first incorporates the characteristics of both the convex and simulated binary crossovers, the second allows to keepthe information part of the individual, while the third aims at gradually increasing the penalty factor of infeasible individuals during the generations and, therefore, avoiding a premature convergence of the algorithm.
To execute this research work will be necessary sensitivity tests involve the parameters, population size, generation number, crossover and mutation probabilities, elitism, extrapolation size in crossover, polarization probability, penalty factor. After to define the best parameters, the optimizations will be performed with both correlations, HW and Colebrook, and the optimal solution obtained by HW correlation will be simulated with Colebrook correlation.
Finally, the analysis of the results leads to the conclusion that due to the large variation of the Reynolds number during the optimization process, the correlation of Colebrook, despite the increase in cost in the network, is more appropriate than HW, since, this is accurate only for a small range of the Reynolds number.
Methods and Materials
To evaluation of the problem has been proposed, this section will present the approaches used along with their respective mathematical modeling. First,Hydraulic model,the equations of conservation of energy and mass will be presented, addressing mainly the method for calculating the head losses and the Newton-Raphson method, such method is chosen, mainly, due to linearity of the energy equations. Second, will bepresentedthe optimization model and the method that will be used for resolution, in this case the genetic algorithm. Finally, the two source pipe network will be introduced with the respective data required to solve the problem.
Hydraulic Model
Let
where
where
The friction factorsfor the turbulent flow can be determined by the Colebrook equation [16] defined as, equation (3)
where
In order to simplify the calculation of the hydraulic resistances, Hazen-Williams [17] proposed an alternative expression that is not directly dependent on the friction factor, i.e. equation (4)
where the valuesof
Under the assumptions of the same head lossand water at 20ºC, equations and can be manipulated in order to yield the following equivalent friction factors for the HW [5], equation (5)
Figure 1 shows the difference between equations and considering different values for the diameters(such a range of diameters will be employed in the results section). Analyzing the figure, one can conclude thatthe calculation of the head losses using the HW is only accurate for a limited range of Reynolds numbers; even though, it is quite common to find several published articles that adopt the HW.

Fig. 1 Friction factor comparison between the Colebrook equation with
In addition to the energy equation, the mass conservation must be employed in each node. For incompressible and steady flow, uniform velocity and non-deformable control volume, one obtains equation (6)
where
Finally, let
where
Optimization Model
Let
where
where
To perform the optimization, a computational implementation based on real-coding Genetic Algorithmhas been employed. Theadopted crossover operator is based on a combination of simulated binary and convex crossovers;in the latter, individuals can be extrapolated following this equation
Finally, it is necessary to couple the hydraulic and optimization models asillustrated inthe below flowchart, figure 2. The first step is to generate a random initial population with the diameters of the pipe networkas variables. With the diameter vector, the hydraulic simulation is performedto calculate the flow rates inthe pipes and loads in the nodes. Then, the fitness function is evaluated,and the constraints
Two Source Problem
The pipe network analyzed inthis workis called Two-Source, and it is consisted of 34 pipes, 26 nodes and two water reservoirswith elevations(altitutes) of 95 and 100 m asdepicted in figure 3. The HW coeficient
Table 1 Nodal and Pipe Data for the Two-Source Network
|
|
|
|
|
|
|
|||||
---|---|---|---|---|---|---|---|---|---|---|---|
1 | 100 | 14 | 10.6 | 82 | 1 | 300 | 14 | 500 | 27 | 900 | |
2 | 95 | 15 | 10.5 | 85 | 2 | 820 | 15 | 1,960 | 28 | 650 | |
3 | 18.4 | 85 | 16 | 9.0 | 82 | 3 | 940 | 16 | 900 | 29 | 1,540 |
4 | 4.5 | 85 | 17 | 6.8 | 82 | 4 | 730 | 17 | 850 | 30 | 730 |
5 | 6.5 | 85 | 18 | 3.4 | 85 | 5 | 1,620 | 18 | 650 | 31 | 1,170 |
6 | 4.2 | 85 | 19 | 4.6 | 82 | 6 | 600 | 19 | 760 | 32 | 1,650 |
7 | 3.1 | 82 | 20 | 10.6 | 82 | 7 | 800 | 20 | 110 | 33 | 1,320 |
8 | 6.2 | 82 | 21 | 12.6 | 82 | 8 | 1,400 | 21 | 660 | 34 | 3,250 |
9 | 8.5 | 85 | 22 | 5.4 | 80 | 9 | 1,175 | 22 | 1,170 | ||
10 | 11.5 | 85 | 23 | 2.0 | 82 | 10 | 750 | 23 | 980 | ||
11 | 8.2 | 85 | 24 | 4.5 | 80 | 11 | 210 | 24 | 670 | ||
12 | 13.6 | 85 | 25 | 3.5 | 80 | 12 | 700 | 25 | 1,080 | ||
13 | 14.8 | 82 | 26 | 2.2 | 80 | 13 | 310 | 26 | 750 |
Results and Discussion
In the stochastic optimization, a sensitivity analysis of the parameters must be performed because of the randomness of the variables. The parameters involved in the GA are the population size (Pop), number of generations (
The following value ranges for the parameters were tested in the developed GA program:
Finally, a statistical analysisis also performed, considering 11 independent runs of the GA and based on four sets of parameters as shown in table 3. These sets are classified as follows: (I) standard set of parameters, (II) set of parameters that resulted in the lowest found fitness function using the HW correlation, (III) set of parameters that presented a lower meanin the sensitivity analysis and with the use of the HW correlation, and (IV) same parameters adopted in (III) but with the Colebrook correlation.The minimum cost of the network, mean (both in thousands) and standard deviation (STD) are also presented in this table, whereas the optimum commercial diametersfor these four sets are displayed in table 4.
Table 3 GA parametersand results
Pop |
|
Cross | Mut | α0 | e | φ | Minimum | Mean | Sth | ||
---|---|---|---|---|---|---|---|---|---|---|---|
I | 1000 | 800 | 95 % | 5 % | 0.3 | 16 | 30 % | 6.5 | 1,261.33 | 1,263.15 | 312,367 |
II | 1000 | 800 | 95 % | 5 % | 0.3 | 24 | 30 % | 6.5 | 1,253.11 | 1,263.15 | 438,346 |
III | 1000 | 800 | 95 % | 5 % | 0.3 | 24 | 10 % | 7.5 | 1,255.13 | 1,263.66 | 520,771 |
IV | 1000 | 800 | 95 % | 5 % | 0.3 | 24 | 10 % | 7.5 | 1,348.82 | 1,368.00 | 1,098,907 |
Table 4 Optimized diameters for the pipes
1 | 2 | 3 | 4 | 5 | 6 | 7 | 8 | 9 | 10 | 11 | 12 | 13 | 14 | 15 | 16 | 17 | |
---|---|---|---|---|---|---|---|---|---|---|---|---|---|---|---|---|---|
I | 900 | 900 | 350 | 300 | 150 | 250 | 800 | 150 | 600 | 600 | 800 | 750 | 500 | 450 | 150 | 500 | 350 |
18 | 19 | 20 | 21 | 22 | 23 | 24 | 25 | 26 | 27 | 28 | 29 | 30 | 31 | 32 | 33 | 34 | |
350 | 450 | 150 | 600 | 150 | 200 | 350 | 600 | 250 | 300 | 300 | 200 | 300 | 150 | 150 | 150 | 150 | |
1 | 2 | 3 | 4 | 5 | 6 | 7 | 8 | 9 | 10 | 11 | 12 | 13 | 14 | 15 | 16 | 17 | |
II | 900 | 900 | 350 | 300 | 150 | 250 | 800 | 150 | 450 | 500 | 800 | 700 | 500 | 500 | 150 | 500 | 350 |
18 | 19 | 20 | 21 | 22 | 23 | 24 | 25 | 26 | 27 | 28 | 29 | 30 | 31 | 32 | 33 | 34 | |
400 | 150 | 150 | 700 | 150 | 450 | 350 | 700 | 250 | 250 | 300 | 200 | 300 | 150 | 150 | 150 | 150 | |
1 | 2 | 3 | 4 | 5 | 6 | 7 | 8 | 9 | 10 | 11 | 12 | 13 | 14 | 15 | 16 | 17 | |
III | 900 | 900 | 350 | 300 | 150 | 250 | 800 | 150 | 450 | 500 | 800 | 700 | 500 | 500 | 150 | 500 | 350 |
18 | 19 | 20 | 21 | 22 | 23 | 24 | 25 | 26 | 27 | 28 | 29 | 30 | 31 | 32 | 33 | 34 | |
400 | 150 | 150 | 700 | 150 | 450 | 350 | 700 | 250 | 250 | 300 | 200 | 300 | 150 | 150 | 150 | 150 | |
1 | 2 | 3 | 4 | 5 | 6 | 7 | 8 | 9 | 10 | 11 | 12 | 13 | 14 | 15 | 16 | 17 | |
IV | 900 | 900 | 400 | 300 | 150 | 250 | 900 | 150 | 450 | 600 | 900 | 750 | 500 | 500 | 150 | 500 | 400 |
18 | 19 | 20 | 21 | 22 | 23 | 24 | 25 | 26 | 27 | 28 | 29 | 30 | 31 | 32 | 33 | 34 | |
400 | 150 | 150 | 700 | 150 | 500 | 400 | 700 | 250 | 300 | 300 | 250 | 300 | 150 | 150 | 150 | 150 |
Concerning the set of parameters (II), a minimum cost of 125,311,060 rupees has been found, which is better than that found by [9], which is 125,501,130 rupees. On the other hand, it is observed that the minimum cost found with the Colebrook correlation, i.e. 134,882,470 rupees, set of parameters (IV), is greater than 125,513,720 rupees. Because of this result, a simulation with the Colebrook correlation considering the optimum network employing the HW correlation has been performed to verify if the constraints were indeed satisfied. The simulation results are presented in table 5 for roughness equal to 0.25 and 0.50 mm. It is worth noting that some head constraints are violated, indicating that the diameters are actually underestimated.
Table 5 Nodal head values considering the Colebrook correlation for the optimum HW network. The highlighted values represent a violation of the constraints
Head (m) | H1 | H2 | H3 | H4 | H5 | H6 | H7 | H8 | H9 | H10 | H11 | H12 |
---|---|---|---|---|---|---|---|---|---|---|---|---|
Colebrook 0.25 mm | 98.3 | 95.2 | 85.0 | 82.3 | 82.7 | 87.3 | 91.3 | 88.3 | 86.1 | 84.5 | 80.6 | 93.5 |
H13 | H14 | H15 | H16 | H17 | H18 | H19 | H20 | H21 | H22 | H23 | H24 | |
87.5 | 80.4 | 89.8 | 84.0 | 85.5 | 80.8 | 86.3 | 83.4 | 80.4 | 76.1 | 77.8 | 76.0 | |
H1 | H2 | H3 | H4 | H5 | H6 | H7 | H8 | H9 | H10 | H11 | H12 | |
Colebrook 0.50 mm | 98.1 | 94.5 | 82.7 | 79.7 | 80.5 | 86.0 | 90.0 | 86.6 | 84.0 | 82.2 | 78.3 | 93.2 |
H13 | H14 | H15 | H16 | H17 | H18 | H19 | H20 | H21 | H22 | H23 | H24 | |
85.7 | 78.0 | 89.0 | 81.6 | 83.4 | 78.5 | 84.9 | 81.5 | 77.4 | 72.6 | 75.1 | 73.0 |
This occurs because in the optimization process, the Reynolds number varies from
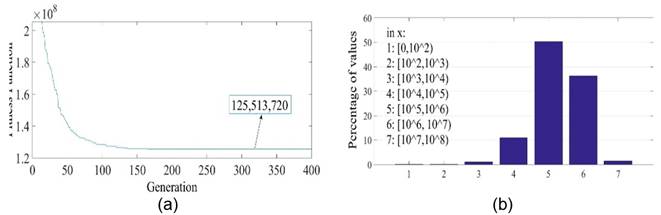
Fig. 4 Results for HW: (a) Convergence of the fitness function (Left), (b) Percentage of Reynolds ranges for all generations (Right)
Thus, in an optimization process via GA, the Colebrook correlation should be used due to its high accuracy in calculating the hydraulic results for all Reynolds numbers. In this sense, the minimum cost of 134,882,470 rupees using the Colebrook correlation is justified by the fact that the some diameters need to be larger in order to guarantee the minimum heads in the nodes, see table 4.
Conclusions
Due to the great variation of the Reynolds number during the optimization process,it has been evident that the HW correlationis not appropriate since its use is accurate only for a small range of Reynolds number. This fact may lead to an optimum or good network configuration that is not the same when the Colebrook correlation, which is valid for all the range of Reynolds number, is employed, generating misleading results. In fact, it has been verified through an example that taking into account the optimumpipe network generated using the HW correlation, some of the heads in the nodes are underestimated when such a network is simulated employing the Colebrook correlation. Thus, it is concluded that when performing the optimization process with the Colebrook correlation, the diameters of the network are enlarged in order to satisfy the constraints, increasing the total cost of the network.