Introducción
El origen de buena parte de los contaminantes atmosféricos es la combustión de carbón, petróleo y gasolina. Muchos de estos contaminantes emitidos a la atmósfera proceden de las calderas industriales, las centrales eléctricas y particularmente las refinerías de petróleo que queman combustibles fósiles. Un 80 % del monóxido de carbono y un 40 % de los óxidos de nitrógeno e hidrocarburos emitidos proceden de la combustión de la gasolina y el gas combustible en los motores de combustión.
Las altas chimeneas de las industrias no reducen la cantidad de contaminantes, simplemente los emiten a mayor altura, reduciendo así su concentración in situ ..1 Asi mismo, en la combustión de combustibles fósiles se producen grandes cantidades de SO2, por la presencia del azufre en dichos combustible.2
Las emisiones mundiales anuales de SO2 se estiman en 200 millones de toneladas, casi la mitad procedente de fuentes industriales. Cuando el SO2 gaseoso se combina con agua líquida, se forma una solución acuosa diluida de ácido sulfúrico (H2SO4), que es el componente principal de la lluvia ácida, junto con el ácido nítrico (HNO3).3
Para enfrentar estas emisiones, los métodos de control de la contaminación atmosférica incluyen la eliminación del producto peligroso antes de su uso, la eliminación del contaminante una vez formado, o la alteración del proceso para que no produzca el contaminante o lo haga en cantidades inapreciables.
Dentro de la refinería de petróleo, las unidades de procesos auxiliares basadas en diferentes tecnologías, se agrupan con el objetivo común de la protección medio ambiental. Específicamente las que se relacionan con el tratamiento de las corrientes sulfurosas trabajan en un circuito cerrado, con varias plantas incluidas y cuyo objetivo final es la recuperación de azufre elemental como producto y que constituye el principal agente contaminante en el proceso.4)
En el mundo, el control de las emisiones a la atmósfera se establece por medio de regulaciones federales y normas en materia ambiental, (5,6 cuyo objetivo es impedir que se emitan grandes cantidades de estos contaminantes al aire. El cumplimiento de dichas regulaciones requiere la inversión en complementos tecnológicos novedosos y procesos auxiliares, en ocasiones muy costosos. Sin embargo, la efectividad de los procesos auxiliares de refinación 7,8 y específicamente los de recuperación de azufre, 9 se están viendo seriamente limitados en los últimos años, principalmente por restricciones ambientales cada vez más estrictas como la norma IFC/2007, del grupo de normas del Banco Mundial. Donde se especifica que el máximo de emisiones permisibles de NOX es 450 mg/Nm3 y de SOX es de 150 mg/Nm3 para las unidades de recuperación de azufre, 500 para el resto de unidades, así como 50 mg/Nm3 para partículas sólidas y 10 mg/Nm3 de H2S. 10
En este sentido, es objetivo del presente trabajo, evaluar un despojador cáustico, para el tratamiento de los gases residuales, como propuesta de mejora tecnológica en la unidad recuperadora de azufre que permita el cumplimiento de los parámetros de calidad de dicho proceso y consigo la reducción de las emisiones gaseosas.
Fundamentación teórica
De acuerdo con, 11 el proceso Claus se utiliza en refinerías para la recuperación de azufre elemental a partir del sulfuro de hidrógeno (H2S) contenido en los gases ácidos, que se producen durante la regeneración de aminas y los gases generados durante el despojamiento de las aguas agrias del craqueo catalítico y otros procesos. El proceso consiste en una oxidación catalítica multi-etapas del sulfuro de hidrógeno. Sin embargo, 12y13 afirman que la conversión completa del H2S en azufre está impedida por limitaciones termodinámicas de las reacciones que tienen lugar en dicho proceso. El mismo implica la quema de una tercera parte de H2S con aire en un horno-reactor para formar dióxido de azufre (SO2) según la ecuación (1), que posteriormente continúa reaccionando con H2S para formar azufre elemental por la ecuación (2)
Aproximadamente el 60-70% del azufre es recuperado en este horno-reactor.
El H2S remanente de dicho horno Claus, se hace reaccionar con SO2 a temperaturas más bajas sobre un catalizador en base de dióxido aluminio o titanio para producir más azufre, por la siguiente ecuación (3):
Como promedio, alrededor del 70 % del H2S y el SO2 reacciona por la ecuación (3).
Los gases de cola residuales de este proceso son enviados a un reactor de reducción para reconvertirlos a H2S y recircularlos nuevamente a proceso, con el objetivo de lograr mayor conversión a azufre. Luego son enviados a incinerar antes de emitirlos a la atmósfera. Sin embargo, aún no se cumplen las normas de emisiones. Para lograrlo se propone la inclusión de un despojador húmedo (cáustico) antes de la incineración. Los despojadores cáusticos son dispositivos para el control de la contaminación del aire que recogen las partículas por contacto directo con un líquido (generalmente agua), razón por la cual, también son conocidos como lavadores.
Antes de emitirse a la atmósfera por la chimenea, este gas residual recibe un lavado con una solución de NaOH al 10 % de concentración en un despojador húmedo, donde tiene lugar la siguiente reacción: 14
Métodos utilizados y condiciones experimentales
Para la evaluación del despojador cáustico (torre empacada) es necesario conocer principalmente las características de diseño del mismo y los parámetros de operación del proceso. 15 Así como, definir las corrientes de entrada y sus composiciones. 4 Ver tabla 1. Para ello se consultaron los balances de materiales y energía del proceso de recuperación de azufre.
Tabla 1 Características de diseño del despojador cáustico, parámetros de operación y composición de la corriente gaseosa de entrada al despojador
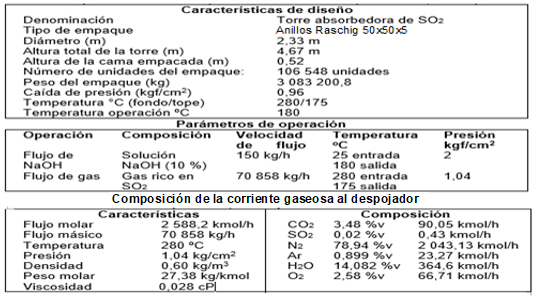
Para la evaluación técnica de la presente investigación se seleccionó el simulador de procesos ProMax® 2.0.7047 16 y el modelo termodinámico Tratamiento Cáustico-SRK que puede aplicarse en simulaciones de torres despojadoras, hidrotratadoras y otros procesos que contengan hidrocarburos, gases ácidos y agua.
• Fase de vapor: SRK Ecuación de estado
• Fase Líquida: Electrolítico Gibbs Excess; • Modelo de entalpía electrolítica: Sí
Elegido el modelo termodinámico del proceso, mediante la opción “Components”, se añaden los componentes presentes en el caso de estudio: SO2, CO2, N2, H2O, O2 y Ar. Se construye el Diagrama de Flujo de Información (DFI), mostrado en la figura 1.
Inicialmente se obtiene el modelo de simulación para el despojador cáustico. Para validar el modelo se simula la operación de la torre absorbedora a las condiciones de diseño y se comparan los resultados obtenidos a través de la simulación en ProMax, estimándose el error que se comete al estudiar el sistema con el modelo simulado.
Como criterio de comparación se toma el error relativo:
Se considera que un error relativo menor que 10 %, permite definir la confiabilidad del modelo para predecir y estudiar la operación de la torre.
A partir del desarrollo del modelo se realizan estudios de sensibilidad de diferentes parámetros del proceso. Para ello, se hace variar uno de los parámetros de entrada manteniendo el resto constante y obtener el comportamiento de los parámetros a analizar.
En la tabla 2 se presentan los estudios para determinar la misma, ellos son: cambiar la fracción de NaOH en la solución cáustica y el flujo de solución de sosa (kg/h), para de esta forma evaluar el comportamiento del gas de salida y fundamentalmente la absorción de SO2 de la corriente entrada.
Metodología para la evaluación económica
Para realizar la estimación de costo de un proyecto hay que tener en cuenta el costo total de inversión, que incluye costo del equipamiento, costo de la ingeniería, costo de materiales, entre otros indicadores que serán calculados por la metodología propuesta.17,18
Para conocer el costo total actual de equipamiento se necesita actualizar los mismos por el Índice de Costo (19) de acuerdo con la siguiente ecuación:
El costo total del equipamiento (CTE) incluye: costo del absorbedor y accesorios (EC), instrumentación (0,10 EC), impuestos de ventas (0,03 EC) y fletes (0,05 EC).
Para determinar el costo total de inversión (CTI) se utiliza la metodología propuesta por Peters, por lo que los costos directos e indirectos, así como, el capital fijo invertido, entre otros, se calcularán utilizando como base la tabla 17 de este libro, según las ecuaciones 9-13:
Para determinar los por cientos que se utilizan en este procedimiento se tiene en cuenta que el cálculo se realiza para un circuito o sistema que está incluido dentro de una unidad de proceso, por lo que muchos de los aspectos para el presente caso de estudio son adaptados a las condiciones reales. Para la estimación del costo total de producción se utilizaron los factores de proporción y las ecuaciones correspondientes de la tabla 27 del Peter. Entonces los valores dinámicos de rentabilidad serán calculados según las ecuaciones 14-17:
Resultados y discusión
Implementación y validación del modelo de simulación en ProMax
La tabla 3 muestra las composiciones de las corrientes de entrada y salida del despojador cáustico, estas últimas obtenidas mediante el simulador. En ella, se comparan las corrientes resultantes con las que ofrecen los balances de materiales por diseño para la torre absorbedora. Se observa como disminuye significativamente el por ciento de contaminantes en el gas debido a la alta selectividad de la NaOH sobre el SO2 (0.12 kmol/h lo que equivale a 116 mg/Nm3), resultado esperado tras el proceso de absorción.
En la tabla puede apreciarse que los errores que se cometen al simular la operación de la torre no superan el valor de un 8 % comparado con las condiciones de diseño, Es bueno señalar que las pérdidas referidas a los arrastres de solvente en el gas, así como las pérdidas de los componentes hidrocarbonados presentes en las corrientes de gas y que no intervienen en el proceso difusivo, no son considerados como pérdidas apreciables, pues el error no supera el 2 %. Se obtuvo una eficiencia de la torre del 85 %, valor adecuado para este tipo de sistema. Teniendo en cuenta estos elementos se considera que el modelo se ajusta a los parámetros de este tipo de proceso.
Resultados del estudio de sensibilidad
Una vez que se comprueba el ajuste del modelo al caso base, se realiza el análisis de sensibilidad al mismo, para comprobar su respuesta ante los cambios que se designaron en los diseños de experimentos expuestos. Como resultado se puede apreciar en la figura 2, que al aumentar el % de NaOH en la solución solvente ocurre una disminución del flujo molar de SO2 en el gas limpio de salida de la torre, manteniendo constante el flujo de gas a la entrada de despojador.
Estos resultados son lógicos debido a que la eficiencia de la planta se mantiene constante y la NaOH es muy selectiva para la remoción de SO2, no obstante, para la elección de la cantidad de solvente, la solución de sosa al 10 % representa la mejor opción pues esta es determinada según la máxima concentración de SO2 a la salida de la columna y por tanto este porciento resulta el mínimo necesario para llevar a cabo la operación de absorción.
En la figura 3, se puede apreciar que, al aumentar el flujo de solvente a la entrada de la torre, manteniendo constante en el flujo de gas a endulzar, la composición de SO2 en el gas del tope comienza a disminuir de forma estable, aunque en menor proporción. Estos resultados son lógicos debido que se alcanza el equilibrio y aunque se continúe aumentando el flujo de solvente no se logrará remover más gas ácido.
En la figura 4, se aprecia que al variar la composición de SO2 en el flujo de gas que se suministra a la torre y mantener constante el flujo de solvente con el cual se endulza, la composición de SO2 en la salida del absorbedor se mantiene prácticamente constante hasta un flujo aproximado de 2,15 kmol/h, pero al añadirse flujos mayores a este, comienza a ascender rápidamente. Estos resultados son lógicos debido a que, para concentraciones del gas por debajo de su valor de diseño, la difusión se dificulta producto del equilibrio en las masas de SO2 en el gas y el solvente. A medida que la composición de SO2 en el gas comienza a aumentar, el equilibrio se altera y para su restablecimiento se difunde el SO2 en el solvente.
Pero si esta concentración continúa aumentando y no se adiciona un volumen mayor de solvente, este se satura y la concentración del gas ácido en el gas dulce aumenta y no se cumple con los requisitos de este tipo de proceso. Analizados los resultados de los experimentos aplicados al modelo se determina que este responde de acuerdo a lo esperado, por tanto, se valida el modelo.
Determinación del estimado de costo
Para la actualización de los costos se utiliza la ecuación 6 y los índices de costo se obtuvieron de 19 tomándose como base de cálculo 1 año de trabajo.
Costo total del equipamiento (CTE)
Para calcular el costo del solvente (tabla 4) se tuvo en cuenta el flujo de líquido, el flujo másico de NaOH necesario para el proceso (𝑚NaOH=138 320,4 𝑘g/𝑎ñ𝑜), así como, el costo del agua utilizada en la solución de sosa y el costo unitario del hidróxido de sodio. El costo unitario del agua es de 1,55 CUC/m3 (4) y el costo unitario de la sosa cáustica es de 0,7956 CUC/kg (20).
Para determinar el costo del equipamiento se utilizó la ecuación 7 y se definieron los equipos mostrados en la tabla 5. Los datos de los costos del equipamiento para el año 2012 se obtuvieron del proveedor (empresa china HQCEC).
Teniendo en cuenta que el diseño realizado garantiza el cumplimiento de la norma IFC/2007, entonces el costo del equipamiento decide finalmente sobre el despojador cáustico. Tomando esto en consideración se selecciona el empaque anillo Raschig de 2 pulgadas de tamaño nominal y de cerámica para ser aplicado en dicho despojador. Para determinar el costo total del equipamiento se utiliza la ecuación 8:
Desarrollo de la evaluación económica
Costo total de inversión (CTI) y Costo total de producción (CTP)
Con el costo total del equipamiento calculado anteriormente se calcula el costo total de inversión. Los resultados obtenidos se muestran en la tabla 6. Para el cálculo del costo de fabricación se utilizaron las ecuaciones 9-12. Primero se determinó la depreciación para 20 años de vida útil y 0 de valor residual:
Para el cálculo de los gastos generales se tuvieron en cuenta solo los gastos administrativos, pues en el caso de estudio no inciden los restantes aspectos:
Cálculo de la ganancia
Con los resultados del costo total de producción y los ingresos por ventas del azufre se determinó la ganancia mediante la ecuación 13:
Costo unitario del azufre = 117 CUC/t. 20
Cálculo del VAN, TIR y PRD
Las variables económicas que se tienen en cuenta para este análisis: ingresos por ventas; costos de producción, gastos generales y costo total de inversión. Se tuvo en consideración que en la industria petrolera se toma un 12 % como tasa de descuento. Con dichas variables y los flujos de caja de la propuesta tecnológica se obtuvieron los indicadores económicos de VAN, TIR y PRD que se muestran en la figura 6, cuyo procesamiento se hizo a través del software Microsoft Excel.
Como se observa en la figura 5 el VAN va incrementando su valor en el futuro, comenzando a ser positivo a partir de 2,5 años aproximadamente (PRD) a una tasa de interés fija. Por tanto, la evaluación económica indica la factibilidad de la implementación de la propuesta de mejora a partir del cálculo de los indicadores de rentabilidad.
Conclusiones
El desarrollo del modelo de simulación y su validación a partir de los parámetros operacionales del proceso permitió establecer los pasos necesarios para lograr el cumplimiento de los estándares de calidad y demostró la viabilidad técnica para la inclusión del despojador cáustico como propuesta de mejora.
La implementación de un despojador cáustico para el tratamiento de los residuales gaseosos de la recuperación de azufre, como propuesta de mejora, complementa el ciclo final de dicho tratamiento lo que permite disminuir las emisiones SO2 hasta 116 mg/Nm3 y por consiguiente dar cumplimiento a las normas de emisiones del Grupo del Banco Mundial, establecidas como requisitos mandatorios para el proceso de recuperación de azufre.
La evaluación económica a partir de los indicadores dinámicos de rentabilidad demostró la factibilidad de la implementación de la propuesta de mejora, conociéndose el VAN de 67 410 929,18 CUC, una tasa interna de retorno de 51 % y PRD de 2,5 años, lo que constituye un aporte para la mejor toma de decisiones respecto a la inversión.