Introducción
En la actualidad, es muy difundido el empleo de los techos flotantes internos para la reducción de las pérdidas por evaporación del producto que se almacena y la emisión de componentes ligeros a la atmósfera.Para la fabricación de los elementos estructurales de los techos, son muy utilizadas las aleaciones de aluminio por su durabilidad, ligereza, fácil mantenimiento y buena resistencia a la corrosión.
Tanto el aluminio puro como sus aleaciones presentan una gran resistencia a la corrosión debido a la formación de una capa fina (~ 4 y 5 µm de espesor) y adherente de óxido de aluminio sobre la superficie del metal. Esta capa de óxido constituye una película impermeable que impide la difusión del oxígeno hacia el metal base, haciendo al aluminio y sus aleaciones muy resistentes a la corrosión (Gil F.J y col, 2001). Sin embargo, el proceso de corrosión en el aluminio y sus aleaciones puede ocurrir, esto depende del medio al que se encuentre expuesto, tipo de aleación utilizada y diseño.
El grado de corrosión en el interior de los tanques de almacenamiento, depende de la naturaleza del producto almacenado. La corrosión de los techos de los tanques se debe fundamentalmente a la combinación de los gases sulfurosos, la humedad y el oxígeno presentes en el interior del equipo (Groysman, A., 2014).
El techo flotante (membrana) de un tanque vertical que se utiliza para el almacenamiento de la gasolina producida en una refinería de petróleo, presentó falla en un corto periodo de explotación. Como resultado se originó el escape a la atmósfera de componentes ligeros del producto que se almacena. Determinar la causa de la falla presentada, es el objetivo de este trabajo.
Materiales y Métodos
La técnica de Inspección Visual se aplicó a la membrana del tanque, para determinar las zonas de mayor afectación y la formación de productos de corrosión. Las muestras de la aleación que presentó la falla y de los sólidos depositados se tomaron para ser estudiados.
Mediante la técnica de Espectrometría de Emisión por Arco Eléctrico y con el uso del Espectrómetro Multicanal Digital modelo SPECTROLAB No.6536, se determinó la composición química elemental de la aleación.
El análisis estructural de la aleación se realizó por la técnica de Metalografía. Se empleó el microscopio invertido de luz reflejada modelo AXIOVERT 25 de la firma Zeiss y se tomaron micrografías a diferentes aumentos (300,100 y 50 μm) con la cámara digital a color PANASONIC acoplada al microscopio. Las probetas metalográficas se prepararon previamente a partir de las operaciones de corte, montaje, desbaste y pulido según se establece en la norma ASTM E3-11 (2017). La estructura metalográfica de las probetas se reveló con la solución de ataque químico No. 1 de composición: 1mL de HF y 200 mL de agua destilada, de acuerdo con lo planteado en la norma ASTM E407-07 (2015).
Para la caracterización de los depósitos de corrosión se empleó la técnica de Difractometría de rayos-X. Los difractogramas se registraron por el método de polvos en un equipo Philips, serie PW-1710. Se utilizó la radiación Kα del Fe y filtro de manganeso; los registros angulares se tomaron entre 6 y 80 grados en 2θ. Los difractogramas se obtuvieron según la variante de medición punto a punto; paso angular de 0,050, el tiempo de medición en cada posición de 3 segundos. Para el análisis cualitativo de fases se utilizó el programa PAnalytical “X Pert High Score”.
Resultados y Discusión
Inspección visual de la membrana del tanque.
A partir de la inspección visual de la membrana, se determinó que el daño se presentó en algunas de las planchas de aluminio que la conforman. En el resto de los elementos estructurales no se evidenció deterioro. También se constató la existencia de cantidades considerables de un sólido anaranjado esparcido sobre determinadas zonas de la membrana, del cual se desconoce su procedencia. Debajo de este sólido se evidenció un elevado deterioro de la plancha que ocasionó la pérdida total de la resistencia mecánica de la aleación.
La zona de falla de una de las planchas de aluminio se evaluó visualmente, observándose un ataque profundo en la parte superior de la plancha de aluminio (figura 1a) que se exhibe fundamentalmente a la humedad y al oxígeno. La parte inferior (figura 1b) que está expuesta a los gases sulfurosos que emanan de la gasolina no presentó este grado de ataque. La presencia de productos de corrosión y de sales en ambos lados de la plancha de aluminio se constató en el estudio.
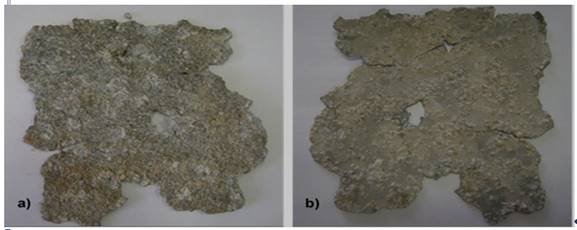
Fig. 1 Muestra de la zona de falla de una de las planchas de aluminio, a) parte superior de la plancha y b) parte inferior de la plancha.
En la zona alejada de la falla, se evidenció un ataque localizado poco profundo en la parte superior de la plancha de aluminio y en el inferior no hubo ataque (figura 2). Este comportamiento indicó que el proceso corrosivo se inició en la parte superior de la membrana debido a la interacción del metal con la humedad y el oxígeno.
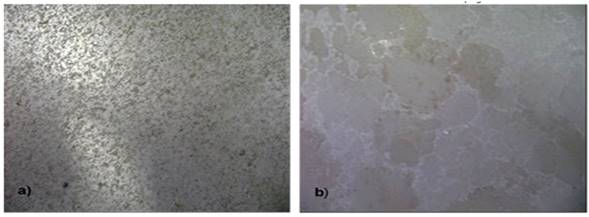
Fig. 2 Muestra de la zona alejada de la falla de la plancha de aluminio estudiada, a) parte superior de la plancha y b) parte inferior de la plancha.
Estudio estructural de la aleación utilizada para la construcción de la membrana del tanque.
El resultado del análisis de la composición química elemental de la lámina de aluminio para la fabricación de la membrana, se expone en la tabla 1. El material corresponde a un aluminio aleado al manganeso de designación 3003.
Tabla 1 Composición química elemental de la aleación

Se reporta el valor promedio de tres mediciones.
La composición química límite que se especifica en la norma ASTM Designación B209M-06 (2006) para la aleación de aluminio 3003, se presenta en la tabla 2. Los resultados del análisis de la composición química del material estudiado, muestran una adecuada correspondencia con lo que especifica la norma.
La aleación de aluminio 3003 pertenece a la serie 3xxx de las aleaciones forjadas de aluminio no tratadas térmicamente. El manganeso es su principal elemento aleante, la adición de 1,25 % de Mn incrementa la resistencia mecánica sin afectar la ductilidad. (ASM Handbook, 1992; ASM International, 2015)
La estructura metalográfica de la aleación (figura 3), se corresponde con su composición química. Una estructura monofásica de solución sólida de Mn en Al, que es típica de esta aleación se observó (Guliáev, 1978 y Kuzmín, 1986). No se detectaron deficiencias estructurales que sensibilicen el material a la corrosión.
Las aleaciones de la serie 3xxx no son susceptibles a las formas más drásticas de corrosión localizada. El principal tipo de corrosión que se apreció fue la corrosión por picaduras. Con un contenido de Cu inferior a 0,05 %, estas aleaciones son casi tan resistentes como el aluminio puro. (Schweitzer, 2010; Schweitzer, 2006)
El estudio metalográfico también permitió constatar el ataque localizado profundo de la superficie de la aleación (figura 4) en la zona de falla.
El mecanismo de corrosión que se observó es el típico de una corrosión galvánica por celdas de concentración. Domínguez, Tomashov y Bahadori (1987, 1971, 2014) plantean que dicho mecanismo, se presenta cuando en una misma estructura metálica se establece una diferencia de potencial entre dos zonas debido a diferencias de concentración del medio oxidante. En el caso particular del estudio, el medio oxidante fue el oxígeno. Las zonas metálicas cubiertas por el sólido anaranjado depositado, tienen una menor concentración de oxígeno (zona anódica) que las zonas sin depósito donde hay mayor concentración de oxígeno (zona catódica), por lo que se forman celdas de aireación diferencial.
Dicho proceso además se favorece por la presencia de la humedad dentro del tanque. El aire normalmente contiene vapor de agua que se condensa sobre la superficie metálica cuando la temperatura cae por debajo del punto de rocío del aire circundante durante las noches (Roberge, 2000). El sólido depositado sobre la superficie de la membrana retiene por más tiempo el agua condensada lo que intensifica el proceso corrosivo.
El ensayo de Difracción de rayos-x permitió obtener los registros difractométricos de polvos (productos de corrosión), que se formaron sobre la plancha de aluminio expuesta al medio corrosivo en el interior del tanque. Los mismos presentan alta complejidad analítica, pues aparecen máximos de difracción superpuestos entre las posibles fases inorgánicas presentes.
En el difractograma que corresponde a la muestra de material tomada de la zona alejada de la falla (figura 5), con menor grado de deterioro, pero con signos visibles del proceso de corrosión, se observan tres máximos de difracción estrechos e intensos del metal base aluminio, característicos de los planos cristalinos de índices de Miller: (111), (200), (220) a distancias interplanares: d= 2,33, 2,02 y 1,429 Ǻ (PDF: 89 - 4037) respectivamente.
Por otro lado, en el registro difractométrico de dicha muestra, aparece también el óxido de aluminio amorfo (Al 2 O 3 . 3 H 2 O), dada la elevación del fondo del difractograma en intervalo angular entre 10 y 600 (2ϴ), el que propicia a su vez la formación de la película primaria adherente que retarda la velocidad de corrosión que transcurre sobre la superficie del metal base.
En esta muestra, también se identificaron otras fases de interés: mezcla compleja de óxidos de aluminio en sus formas cristalinas: alúmina gel (d= 8,04, 7,80, 7,21 y 4,24 Ǻ; PDF: 31-23); α - Al 2 O 3 (d = 2,55, 3,48 y 2,09 Ǻ; PDF: 89-7717; γ- Al2O3 (d= 4,33, 2,80, 2,39 y 1,98 Ǻ; PDF: 29-63); ϴ- Al 2 O 3 (d=2,45, 2,83 y 2,84 Ǻ; PDF: 79-1559), que constituye la serie de productos cristalinos secundarios del proceso de corrosión del aluminio. (Morcillo, 1996)
Como otro aspecto de interés a considerar, se identificaron en la muestra, cuatro máximos en la zona angular entre 6 y 200 (2ϴ) de muy baja cristalinidad, los cuales se asocian a sulfatos e hidroxisulfatos de aluminio con alto grado de hidratación: zaherita, Al 12 (SO 4 ) 5 (OH) 26 ; PDF: 29-88 y d= 16 Ǻ; 7Al 2 O 3 .3 SO 3 . 33 H 2 O; PDF: 11- 0467 y d = 14,0 Ǻ; además presencia de azufre elemental en sus formas cristalinas ortorrómbica; d= 7,7 y 5,68 Ǻ PDF: 65-1436 y romboédrica d= 3,89 Ǻ; PDF: 65-1436 correspondientemente.
Por último, en esta muestra se detectaron contenidos adicionales de fases atípicas del proceso de corrosión como son el cuarzo y calcita, presentes por procesos de arrastre mecánico, con máximos de difracción: d= 3,34 y 3,03 Ǻ respectivamente.
Por su parte, el difractograma de polvos correspondiente a la muestra de material tomada de la zona de falla (figura 6), donde se observan los signos más importantes de deterioro del metal, denota presencia de un mayor número de fases cristalinas de la misma naturaleza que las que se reportan para la muestra anterior, pero todas en mayor cuantía. Se corroboró la formación de sulfatos e hidroxisulfatos de aluminio con alto grado de hidratación. No obstante, en la muestra destaca el hecho de la menor intensidad y cristalinidad (mayor semiancho) de los tres máximos de difracción del metal base aluminio, de lo que se infiere la notable intensidad del proceso de corrosión que tuvo lugar en la plancha de aluminio objeto de evaluación.
En esta muestra se observaron con mayor intensidad los máximos de difracción del azufre elemental (formas romboédrica y ortorrómbica), la mezcla del óxido de aluminio amorfo (Al 2 O 3 . 3 H 2 O) y sus homólogos cristalinos: α, γ, y ϴ. Además, se identificó una fase de aluminio típica del proceso de corrosión del aluminio; el hidróxido de aluminio, en este caso particular la variedad norstrandita: d = 4,79 y 4,33 Ǻ, la cual no se detectó en la muestra anterior.
Por último, en la muestra se observaron con claridad los sulfatos de aluminio hidratados: aluminita Al2 (SO4) (OH)4. 7 H2O (d = 7,79, 8,97, 6,37 y 5,49 Ǻ, PDF: 70-1103); zaherita (Al 12 (SO 4 ) 5 (OH) 26 (d= 16 Ǻ, PDF: 29-88); 7Al 2 O 3 .3 SO 3 . 33 H 2 O (d = 13,8, 11,6 y 8,7 Ǻ, PDF: 11- 0467); (Al2O3)13 (SO3)6 (H2O)79 (d= 12,5, 11,5 y 9,8 Ǻ; PDF: 74 - 1414), todo lo cual confirma las elevadas concentraciones de especies sulfuradas presentes en la atmósfera en el interior del tanque debido al ponche de la membrana.
Conclusiones
La causa del deterioro de la membrana del tanque fue la corrosión galvánica por celdas de concentración que tuvo lugar, debido a diferencias de concentración del oxígeno entre las zonas que se encontraron cubiertas del sólido anaranjado y las zonas libres del mismo. Este estuvo favorecido por la presencia de la humedad dentro del tanque. Los productos de corrosión encontrados, constataron que hubo interacción del oxígeno y la humedad con la superficie de las planchas de aluminio. Además, hubo reacción de los productos de corrosión formados con los vapores sulfurosos que emanan de la gasolina, una vez que se produjo el ponche de la membrana.