Introducción
En los últimos 60 años, ha existido un incremento sostenido en cuanto a instalaciones industriales y de servicios que procesan, producen, transportan o almacenan volúmenes relativamente elevados de sustancias y compuestos químicos muy peligrosos. Estos, debido a su elevada reactividad química, inflamabilidad o toxicidad, conducen a riesgos que representan los peligros de posibles accidentes mayores en dichas instalaciones. Se entiende por “accidente mayor” cualquier suceso tal como: escape de gases, derrame de líquidos tóxicos y/o inflamables, incendio o explosión, que sea consecuencia del desarrollo incontrolado (por fallas o averías) de una actividad o proceso industrial que suponga una situación de riesgo grave, inmediata o diferida para las personas, el medio ambiente y/o los bienes en el interior o exterior de la instalación, en el que estén implicadas una o más sustancias peligrosas. (Brand, King, Dones, 1996; Storch, 1998; Perry, Green, 2008; Crowl, Louvar, 2002; Camejo, Alfonso, 2011; Alfonso, Camejo, 2018).
Las consecuencias de estos accidentes suelen ser: pérdidas de vidas o daños a la salud humana, impactos ambientales negativos, perjuicios económicos, efectos psicológicos en la población, comprometimiento de la imagen de la industria y del gobierno.
Los efectos peligrosos de los accidentes mayores capaces de producir afectaciones (daños) de diferentes grados en las personas, los bienes o al medio ambiente, se expresan mediante las siguientes variables físicas: concentración tóxica (C) en la atmósfera, suelos y aguas; por el escape de gases o derrame de líquidos tóxicos; calor directo o radiación térmica (qr) procedente de los incendios de diferentes tipos; sobrepresión máxima (ΔP) de la onda explosiva; impulso mecánico de proyectiles (I) por las explosiones confinadas y no confinadas (Storch, 1998; Crowl, Louvar, 2002; Perry, Green, 2008).
Referido a un accidente, el riesgo se define como la contingencia de sus consecuencias o daños. La expresión del riesgo (R) más generalizada, se basa en el producto de la probabilidad de ocurrencia de accidentes considerados (P A , absoluta o referida a un período de tiempo determinado: FP accidentes/año o año-1), por las consecuencias esperadas (C) en términos de afectaciones económicas, a la salud o a la vida humana y/o al medio ambiente (Storch, 1998; Crowl, Louvar, 2002; Muhlbauer, K. 2004; Perry, Green, 2008):
En los casos en que la exposición al peligro (de los elementos o sujetos expuestos) no sea permanente, se incluye en la expresión anterior (1) la variable Probabilidad de exposición (P E ). De esta forma la variable el riesgo se expresa como:
La estimación de la distancia y el área, medidas desde el origen de un accidente hasta un punto o zona dada, en el que los efectos peligrosos (C, qr, ΔP, I) alcanzan determinado valor, constituyen una parte importante de los estudios de riesgo. Esto permite estimar la magnitud de las consecuencias de los accidentes identificados como posibles en una instalación (derrames, escapes, incendios, explosiones), y se realizan mediante el uso de los programas de computación desarrollados (Storch, 1998; Alfonso, Barrutia, 2012; Lugo, 2018; Rodríguez, Camejo, Alfonso, 2018).
Se han elaborado una gran diversidad de técnicas o métodos para el análisis de riesgos con carácter reactivo, prescriptivo o predictivo. Todos ejecutan un escrutinio (más o menos conducido, estructurado y/o secuencial) sobre lo que podría fallar del proceso y equipos incluidos en la planta objeto de consideración. Según el grado de cuantificación del riesgo, las técnicas o métodos pueden agruparse o clasificarse en cualitativos, semicuantitativos o cuantitativos (Storch, 1998; Troncoso, Vilaragut, 2010; Casas, Camejo, Rizo, 2012).
Los objetivos generales de estos estudios son (Storch, 1998; Crowl, Louvar, 2002; Camejo, Alfonso, 2016):
Identificar los peligros de accidentes (identificación de los riesgos en su origen) presentes en una instalación, planta o proceso (escapes o derrames inflamables o tóxicos, incendios o explosiones)
Definir si existe la posibilidad de accidentes mayores a partir de la estimación de la distancia y área que pudieran alcanzar los efectos peligrosos de los accidentes identificados, elementos vulnerables y daños probables (evaluación de consecuencias).
Analizar las causas de los accidentes identificados.
Evaluar el riesgo que representa cada accidente identificado, o sea, probabilidad de ocurrencia por la magnitud de las consecuencias estimadas.
Discernir la aceptabilidad o no, de instalaciones y operaciones propias de la planta que se estudia, así como de su ubicación y distribución en planta.
Definir las medidas técnicas, técnico-organizativas y humanas, activas y pasivas, de protección (de prevención o mitigación), para evitar la ocurrencia y/o mitigar las consecuencias de los accidentes identificados.
Cumplir con los requisitos legales que se vinculan con los objetivos.
En Cuba, la realización y actualización de estudios de riesgos, basadas en la evaluación de la seguridad en instalaciones con peligro de accidente mayor, están reguladas por el Decreto Ley 309/2013. “De la Seguridad Química” y su reglamento, contenido en la Resolución 148/2013. “Reglamento sobre la gestión de los riesgos a la seguridad de procesos en instalaciones industriales con peligro mayor” del Ministerio de Ciencia, Tecnología y Medio Ambiente, así como por la Directiva No. 1 “del Presidente del Consejo de Defensa Nacional para la Reducción de Riesgos de Desastres”. En ninguna de estas regulaciones se precisan los métodos de estudios a utilizar.
Importancia de los métodos de estudios para el análisis de riesgos
Los estudios para el análisis y evaluación de riesgos de procesos con peligro de accidente mayor, constituyen una valiosa herramienta científico-técnica, aplicables tanto en las etapas de diseño y proyecto, como en las de construcción, explotación y mantenimiento. Los resultados obtenidos aportan información imprescindible en relación con las medidas de protección (preventivas y de mitigación) requeridas para garantizar la seguridad de los procesos. Por ello dichos estudios constituyen el punto de partida para establecer un sistema de gestión de seguridad industrial o valorar los ya establecidos, lo que determina la necesidad de aplicar el o los métodos más adecuados para su realización en cada caso.
Este trabajo tiene como objetivo, describir las características y principales limitaciones de los métodos predictivos más utilizados en los estudios para el análisis y evaluación de riesgo de procesos con sustancias peligrosas, o sea con peligro de accidente mayor, facilitando así la selección del método a utilizar para el estudio en una instalación determinada.
Metodología experimental y descripción de los métodos de estudio. Resultados que se obtienen
Para la realización de los estudios se requiere disponer de información amplia y de calidad sobre el proceso objeto de análisis: descripción del proceso, diagramas de flujo y parámetros de operación; diagramas de tuberías e instrumentos (P&ID siglas en inglés) actualizados, instrucciones de operación; balance de materiales y energía; descripción de los sistemas de control básico del proceso, alarmas, enclavamientos y sus diagramas lógicos; hojas de seguridad de los productos que se incluyen en el proceso; información sobre el diseño, dimensiones y materiales utilizados en la construcción de los equipos, manual de construcción e inspección, diagrama y planos de su distribución en planta, clasificación de las áreas a efectos de la protección eléctrica; descripción de los sistemas auxiliares (aire, vapor, electricidad, etc.)
El conocimiento del proceso, así como la comprensión de las secuencias accidentales que pudieran ocurrir por parte del equipo multidisciplinario que debe constituirse para la realización de los estudios, es determinante para garantizar su racionalidad y objetividad; donde al menos uno de los integrantes del grupo debe estar bien familiarizado con el o los métodos de estudio a utilizar.
Métodos cualitativos de análisis de riesgos
Estos métodos, frecuentemente son preliminares y sirven de soporte estructural para los estudios semicuantitativos o cuantitativos.
Método: Análisis ¿Qué pasa si…? (QPS)
Objetivo
Detectar y analizar de forma cualitativa las desviaciones del proceso y sus variables, respecto de su comportamiento normal previsto, dando lugar a sucesos indeseables (Storch, 1998; Troncoso, Vilaragut, 2010).
Descripción
Preguntas QPS: ¿qué pasa si...? (Ejemplos)
¿Se detienen (cada uno de ellos) los equipos impulsores (bombas, compresores, eyectores, etc.) y agitadores?
¿Fallan (cada uno de ellos) los sistemas de instrumentación y control?
¿Fallan (cada una de ellas) las actuaciones previstas para los operadores humanos?
Procedimiento
Se elige un enfoque o alcance para cada parte del estudio (seguridad del propio proceso, seguridad de las personas, seguridad eléctrica, defensa contra incendios, etc.), o se decide llevar el estudio de manera global con la referencia a la secuencia del proceso.
Comenzando por el principio del proceso, avanzando a lo largo de las etapas del mismo hasta el final, se plantean y anotan todas las preguntas QPS que se les ocurra a los participantes. No contestarlas durante esta etapa.
Respuestas a las preguntas QPS por todo el equipo. Algunas requerirán estudio aparte o la participación de especialistas (control, materiales, mantenimiento).
Consideración para cada pregunta QPS, de qué medidas existen y cuáles caben tomar para prevenir el riesgo, anulándolo o disminuyéndolo, en su origen.
Efectuar todo lo anterior para cada una de las partes decididas en 1.
Limitaciones
Análisis de Modos de Fallos y sus Efectos (AMFE)
Objetivo
Establecer los fallos posibles en todos y cada uno de los elementos, equipos (de proceso y de control) en una planta, en los modos de detección de los fallos, sus causas y consecuencias y definir, medidas de protección para los fallos que sean más significativos (Storch, 1998; Bestratén, Orriol, Mata, 2004; Troncoso, Vilaragut, 2010).
Este método se aplica también para identificar las desviaciones que pueden afectar la calidad de los productos o servicios (Scarpatti, 2014).
Descripción
Fallos: establecidos por situaciones contrarias a las normales. Se muestran ejemplos de desviaciones que pueden ocurrir como fallos (Tabla 1).
2. Los resultados se recogen en una tabla de la siguiente forma (Tabla 2):
Procedimiento
Identificar y listar todos los elementos de equipo (de proceso y de control) dentro de una sección del proceso en la planta.
Definir el funcionamiento de cada elemento del equipo.
Definir los modos de fallo como se indicó en la descripción.
Definir las afectaciones (consecuencias) de los fallos definidos en 3.
Establecer si los fallos definidos en 3 y las consecuencias definidas en 4 afectan a otros elementos de equipo aparte del que se esté considerando. En caso afirmativo, debe trasladarse la parte del análisis correspondiente al elemento receptor de la influencia para determinar consecuencias sobre el mismo.
Discernir y recomendar medidas preventivas viables que eviten los fallos definidos en 3, que sean significativos a efectos de seguridad.
Repetir de 1 a 7 para todas las secciones del proceso.
Limitaciones
Pueden pasarse por alto alguno fallos y consecuencias.
Sólo considera fallos por disyuntivas operacionales entre extremos.
No considera combinaciones de fallos coincidentes o en secuencia.
Análisis funcional de operabilidad (AFO/HAZOP, siglas en español e inglés)
Objetivo
Detectar riesgos, sus orígenes y consecuencias, para establecer las medidas remediales mediante análisis cualitativo pero sistemático y escrupuloso, considerando la esencia del proceso que son las desviaciones de sus variables y condiciones operacionales (Storch, 1998; Freedman, 2003; Flores, 2003; Troncoso, Vilaragut, 2010).
Desde hace varios años se ha indicado la aplicación de este método para el análisis de sistemas en los que estudios de riesgos laborales realizados, establecen la posibilidad de ocurrencia de “accidentes muy graves”, o sea, de accidentes mayores (Rodríguez, et al, 2015).
Descripción
Análisis sistemático (estructurado) de las desviaciones plausibles en cada una de las variables y parámetros de procesos y equipos, respecto a los valores y condiciones operacionales que se consideran normales correspondiente con la intención de diseño para el elemento que es objeto de análisis: flujo, composición, nivel, presión, vacío, temperatura, viscosidad, material de construcción, espesor, corrosión-erosión, pérdida de contención, etc. Las desviaciones se plantean mediante el empleo de unas palabras de guía que articulan las preguntas: no (nada de); más de (cantidad); menos de (cantidad); contrario de (invertido); además de (añadido cualitativo); parte de (falto cualitativo); diferente de (otro que).
Establecida la desviación objeto de consideración, se investigan (inductivamente) las causas posibles de la desviación. Se reserva el resultado.
Se investigan (deductivamente) las consecuencias posibles de la desviación con el fin de establecer cuál de las alternativas siguientes es aplicable al caso:
Las consecuencias no entrañan riesgo: descartar la consideración de esta desviación en concreto.
Las consecuencias entrañan riesgos menores o medianos: consideración de esta desviación en la etapa siguiente.
Las consecuencias entrañan riesgos mayores: consideración de esta desviación en la etapa siguiente y envío de aquella (con lo obtenido en estas etapas 1, 2 y 3) para su análisis mediante un método más detallado y/o cuantitativo.
Volviendo (inductivamente) a las causas posibles examinadas en la etapa 2, se trata ahora de determinar las medidas convenientes de protección (activa y pasiva) que eviten o debiliten dichas causas.
Registro escrito de lo que sea significativo y sensato de entre lo obtenido en las etapas 1 a 4.
Procedimiento
El documento o información que actúa como soporte principal para la aplicación del método es el diagrama de flujo de proceso o, preferiblemente el diagrama de tuberías e instrumentos (P&ID). Este último debe dividirse en secciones o nodos para cada equipo o aparato, sus tuberías y servicios o sistemas auxiliares. La sección objeto de estudio se enumera y se declara su cometido o intención de diseño donde se procede para cada componente de la sección (tuberías con sus válvulas y bombas, re recipiente, instrumentos y sistema de control, etc.) como se describió más arriba. Se han desarrollado diferentes programas de computación que facilitan significativamente la aplicación del método.
Limitaciones
La calidad del contenido y del resultado del análisis depende mucho de los conocimientos, experiencia y compenetración del equipo de profesionales analistas.
Consume mucho tiempo y recursos si se hace bien.
Análisis cualitativo mediante árboles de fallos (AAF)
Objetivo
Analizar cualitativamente eventos o sucesos de fallo en sistemas complejos mediante su descomposición inductiva en otros escalonadamente más sencillos, hasta llegar a sucesos básicos (de sencillez máxima) que pueden considerarse como causas iniciadoras (Storch, 1998; Perry, Green, 2008; Calderón, 2016; López, Alonso, Mazaira, Ricardo, 2018; Análisis, 2020).
El método se utiliza también en los análisis de seguridad laboral para determinar las causas de accidentes de trabajo (Rodríguez, et al, 2015).
Descripción
Procedimiento inductivo para establecer el árbol de fallos: desde los sucesos capitales (SC) hasta los sucesos básicos, iniciadores o causales (SB).
Se emplean símbolos lógicos para expresar relaciones e interacciones. A continuación, se definen las más usuales.
Sucesos. Su representación se indica (Figura 1). SC: suceso capital, de cabecera, o complejo (pero normalmente más fácil de intuir; por ejemplo: explosión de un recipiente a presión). SI: suceso intermedio. SB: suceso básico iniciador, causal o sencillo. SND: suceso no desarrollado porque no hay información o porque no se considera necesario. Se procesa como un SB. SN: suceso normal (condiciones operativas normales de diseño) o externo. Se procesa como un SB.
Se utilizan símbolos de transferencia para enviar de unas hojas a otras, partes de los árboles de fallos cuando ello resulta necesario. Suelen añadirse a un suceso intermedio.
Interacciones entre sucesos: puertas lógicas
Puertas «y»: Para que ocurra el suceso inmediatamente superior deben ocurrir (concurrir, concomitar) todos los sucesos conectados por la parte inferior del símbolo. La probabilidad compuesta transmitida por la salida superior del símbolo es igual al producto de las probabilidades individuales que acceden o conectan por la parte inferior del mismo. La probabilidad se «parte» a través de una puerta «y»: el producto de dos factores menores que 1 es aún menor (Figura 2).
Puertas «o»: Para que ocurra el suceso inmediatamente superior basta que ocurra cualquiera (alternativos excluyentes o no) de los sucesos conectados por la parte inferior del símbolo. La probabilidad compuesta transmitida por la salida superior del símbolo es igual a la suma de las probabilidades individuales que acceden o conectan por la parte inferior del mismo. La probabilidad se «transmite» entera a través de una puerta «o» (Figura 2).
3. Se definen, determinan y analizan conjuntos mínimos de fallos (CMF). Se entiende por CMF a agrupaciones de sucesos básicos que, directamente a través sólo de puertas «o» (orden = 1) o también a través de puertas «y» (órdenes superiores), determinan la ocurrencia del suceso capital. Al no producirse uno de los sucesos (fallos) incluidos en un CMF, no se producirá el suceso capital.
Un conjunto mínimo de fallos se caracteriza por su orden n, que es el número de sucesos básicos que lo integra: CMF (I), n = 1; CMF (II), n = 2; CMF (III), n = 3; etc. El orden de los CMF indica el número de sucesos básicos que tienen que producirse para que ocurra el suceso capital.
4. Se hace análisis cualitativo, semicuantitativo y cuantitativo para determinar la importancia de los sucesos básicos y de los sucesos capitales con el fin de establecer aceptabilidad, medidas correctoras o la necesidad de estudios más profundos.
Procedimiento
Listar los sucesos capitales (SC): como se dijo antes, son los más complejos, por eso se analizan, pero los más fáciles de intuir y de obtener de la experiencia o de un banco de datos. Ejemplos: explosión de un recipiente a presión (depósito, reactor, etc.), explosión e incendio en un horno, fallo de un compresor, etc. Cada SC será la cabecera de un árbol de fallos independiente.
Establecer y listar los sucesos intermedios y básicos mediante el camino inductivo y las preguntas:
Dibujar el árbol de fallos. Utilizando los símbolos vistos antes. A efectos de referencia se marcan las puertas con letras y los sucesos básicos con números. No conviene ahorrar el empleo de actividades intermedias: intercaladas siempre entre puertas.
Se determinan los conjuntos mínimos de fallos (CMF) y su orden n: es normal hacerlo mediante el álgebra de Boole (diagramas de Venn, etc.) o mediante el método matricial del Instituto Americano de Ingeniería Química (AICHE, por sus siglas en inglés) y la utilización de programas de computación.
A continuación, se incluye un ejemplo para ilustrar su análisis aplicando la lógica artesanal para determinar los CMF y su orden (Figura 3):
Recorrer el árbol de arriba abajo pasando sólo por puertas «o». Cada vez que se llega a un SB (SND o SN) éste será un conjunto mínimo de fallo (CMF) orden 1, porque cada uno de ellos es capaz de desencadenar el SC. En el ejemplo se obtienen: CMF (I): (A - B): (1) y (2).
Recorrer el árbol de arriba abajo pasando por puerta «o» y por una sola puerta «y» de dos salidas (C). Cada dos SB que se encuentren (uno por cada rama o salida) en la puerta «y» determinarán el desencadenamiento del SC. Orden: el número de salidas de la última (única en este caso) puerta «y» que se ha pasado (CMF de orden II). En el ejemplo se obtiene: CMF (II): (A - C): (3) (4).
Recorrer el árbol de arriba abajo pasando por puertas «o» y por una sola puerta «y» con tres salidas. Cada tres SB (uno por cada rama o salida) en la puerta «y» determinará un CMF (de orden III) desencadenante del SC.CMF (III): En el ejemplo no existe.
Recorrer el árbol de arriba abajo pasando por puertas «o» y por dos puertas «y». Es de notar que cada cuatro SB (tres de la segunda puerta «y». más uno de la última puerta «o» que confluyan en la puerta D) determinarán un CMF de orden IV desencadenante del SC. En el ejemplo se obtiene: CMF (IV): (A-D-E-F): [(5 + (7) (8) (9)]; [(6 + (7) (8) (9)]
Aplicando la misma lógica se pueden resolver puertas y combinaciones de puertas de distintas características.
5. Análisis del árbol de fallos teniendo en cuenta que:
a) el orden de los CMF indica el número de SB que tienen que ocurrir para que se produzca el SC, por lo que los CMF de menor orden deben ser de mayor riesgo que los de orden superior.
b) si se introducen medidas protectoras en forma de SB en confluencia «y»: aumentan el orden y disminuyen el riesgo.
c) los sucesos básicos que aparecen en varios CMF debe ser objeto de atención preferente porque está aportando su probabilidad de fallo a varias alternativas. Para determinar su importancia relativa, el número de veces que aparece podría ponderarse con el inverso del orden de los CMF en que lo hace.
Se presenta la importancia relativa de los sucesos básicos (SB) del árbol de fallos (Tabla 3) tomado como ejemplo, el representado (Figura 3).
Puede apreciarse que, los sucesos básicos 1 y 2 tienen la mayor importancia relativa. La ocurrencia de cualquiera de ellos conduce directamente al suceso capital, lo que sugiere la necesidad de adoptar medidas que disminuyan la probabilidad de ocurrencia de los mismos
6. Elaboración de recomendaciones: introduciéndolas en el árbol pueden evaluarse los efectos de las mismas. De esta forma se usa el árbol como un medio de simulación.
Limitaciones
Pueden no detectarse fallos (SC o SB) que quedarían sin considerar.
Pueden darse errores en la lógica del árbol: no considerar fallos intermedios, puertas incorrectas, relaciones causa- efecto, etc.
Consume bastante tiempo, lo que se puede disminuir si se dispone de los softwares establecidos para su uso. Se recomienda su utilización para el estudio de sistemas complejos de procesos que incluyen muchos aparatos, instrumentos, equipo para control y alarma, operadores humanos, etc.
Análisis cualitativo mediante arboles de sucesos o eventos (AAS)
Objetivo
Analizar cualitativamente eventos o sucesos de fallo en sistemas complejos, partiendo de sus causas iniciadoras (Storch, 1998; Salomón, Perdomo, 2001; Perry, Green, 2008; Troncoso, Vilaragut, 2010).
Descripción
En gran medida, es el procedimiento inverso al del análisis mediante el árbol de fallos. Esto se debe a que, partiendo de sucesos básicos (de sencillez máxima) que pueden considerarse como causas iniciadoras, se llega por vía deductiva a sucesos complejos que pueden ser accidentes.
Es un método deductivo tanto en la construcción lógica del árbol como en su análisis cuantitativo posterior. La predicción se hace por etapas, analizando las dos (sí/no) o varias alternativas de ocurrencia de cada suceso. El análisis deja establecida la estructura (árbol de sucesos) que representa la relación causa-efecto entre los mismos.
Procedimiento
Identificación de los sucesos básicos iniciadores (SB). Estudiando con detalle los elementos de equipo (de proceso y de control) se contesta a las preguntas ¿Qué puede fallar de este elemento y de cada una de sus partes?
Aplicación de la disyuntiva (sí /no o fracaso /éxito) al suceso básico capital (cabecera) del árbol.
Deducción del suceso intermedio (SI), sobre cada una de las alternativas de la disyuntiva, cuando haya lugar.
Aplicación del factor condicionante (FC) que puede influir sobre cada alternativa de las disyuntivas establecidas en 2. Ejemplos de FC: alarma, intervención humana o automática derivada de aquélla, alivio mediante dispositivo, sistema de protección contra incendio, parada de emergencia, etc.
Aplicación de la disyuntiva (si /no o fracaso /éxito) a cada suceso intermedio y/o factor condicionante dispuesto en secuencia lógica de ocurrencia.
Representación gráfica de: suceso básico (SB), sucesos intermedios (SI), factores condicionantes (FC) formando el árbol de sucesos. Los SB, SI, FC y las disyuntivas se representan en el orden secuencial de su intervención lógica en el accidente. Este es un aspecto delicado en la elaboración del árbol.
Exploración crítica de todas las disyuntivas definidas para ver si hay más SI y más FC que deban tenerse en cuenta en el análisis. Si aparecen: aplicar 3, 4, 5 y 6 como sea oportuno. Si no aparecen: las disyuntivas últimas determinan las consecuencias finales del análisis.
Establecimiento y análisis de las consecuencias. Una consecuencia puede ser: «sin consecuencia».
Las mejoras que se introduzcan se traducirán en nuevos FC, o en la eliminación de FC anteriores, con los que conviene repetir el análisis para observar la sensibilidad (resultado, sobre las consecuencias) del árbol a las medidas recomendadas. Un ejemplo de árbol de sucesos es representado (Figura 4).
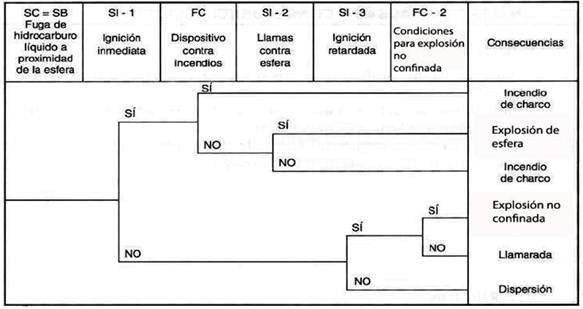
Fig. 4 Árbol de sucesos para el caso de una fuga de hidrocarburo líquido (derrame) en las cercanías de un recipiente esférico conteniendo GLP.
Limitaciones
Puede no detectar fallos (SB, SI, FC) que quedarían sin considerarse.
Puede haber errores en la lógica del árbol.
El método denominado “Análisis de Causas y Consecuencias” que no se trata aquí por razones de espacio, es en buena medida una combinación de las técnicas de árbol de fallos y de árbol de sucesos.
Métodos semicuantitativos para el análisis de riesgos
Los estudios semicuantitativos pretenden mediante la combinación de unos factores globales (penalizadores o bonificadores) de riesgo, establecer directamente el riesgo (R) o la magnitud de las consecuencias (C). A continuación, se exponen los métodos semicuantitativos de William Fine, R. Pickers y de Modos de Fallos, Efectos y Criticidad.
Estimación del riesgo y justificación de medidas correctoras: métodos de William T. Fine y R. Pickers
Han sido utilizados tanto para la realización de estudios de riesgos de accidentes laborales (de trabajo) como para el análisis de riesgos de procesos con peligro de accidente mayor (Alfonso, Betancourt, Camejo, 2008; Troncoso, Vilaragut, 2010; Rodríguez, et al, 2015).
Objetivos
Estimar la magnitud de los riesgos a partir de índices globales de probabilidad y consecuencias.
Definir las medidas correctoras y su justificación desde el punto de vista económico.
Método matemático de William T. Fine
Se basa en la determinación del grado de peligro (GP) o de peligrosidad mediante la expresión:
Donde
P, |
es la probabilidad de que la secuencia del accidente se complete. |
E, |
es la frecuencia con que ocurre la situación de riesgo. |
C, |
representa las consecuencias o resultado más probable si el accidente se produce. |
Los valores de E, C y P se miden en escalas cuantitativas (arbitrarias). Se utilizan valores de referencia y estadísticas históricas. Se presentan los indicadores o criterios propuestos por William T. Fine para la evaluación de cada uno de los factores que determinan el GP (Tabla 4), así como la puntuación para cada indicador. Seguidamente se muestra, la clasificación del GP según su valor (Tabla 5), así como los criterios para la justificación económica de las medidas correctoras propuestas (Tabla 6). (Aplicación, 2011; Camejo, Arcos, 2011).
La justificación de las medidas correctoras (J) se determina mediante la siguiente expresión:
Donde, GC, indica el grado de corrección, o sea, el grado en que será reducido el riesgo o grado de peligrosidad (GP), y FC, indica el factor de costo. Para que la medida correctora propuesta sea aceptada, o sea se justifique económicamente, debe cumplirse que J sea igual o mayor que 10 (J > 10). Se nuestra la puntuación que se asigna a cada indicador según el nivel de disminución del riesgo y el costo de cada medida correctora respectivamente (Tabla 6).
Análisis practico de riesgos de R. Pickers
Se basa en la estimación del grado del riesgo (R) según la expresión (Troncoso, Vilaragut, 2010; Métodos, 2014):
Dónde: P, probabilidad: de que se produzca un accidente en condiciones técnicas y de proceso; E, Frecuencia de exposición: factor temporal que aumenta o disminuye la magnitud del riesgo (frecuencia con que ocurre la situación del riesgo); C, Consecuencia: valoración de daños posibles debido a un accidente determinado.
Se presenta la clasificación de los criterios y el puntaje para la evaluación del grado de riesgo (Tabla 7), así como la magnitud o grado de riesgo y su clasificación (Tabla 8).
Tabla 7 Indicadores para la evaluación del grado de riesgo según el método análisis práctico de riesgo R. Pickers.
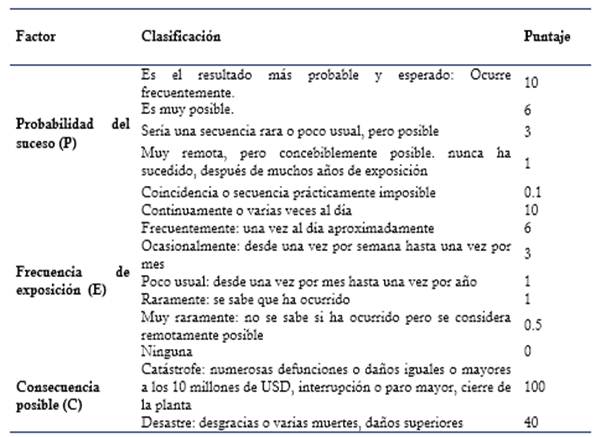
Para determinar si se justifica la acción correctiva propuesta para reducir o eliminar el riesgo generado por un peligro, se mide el costo estimado de las medidas correctivas contra la magnitud del riesgo. Esto se hace mediante la integración de dos factores adicionales en la fórmula de Magnitud del Riesgo:
Dónde:
F J , es el factor de eficiencia de la medida correctora;
Fc, es el factor de corrección de los riesgos
D, es el factor de costo determinado por:
Se presenta el puntaje para el factor de corrección (Tabla 9).
Un factor de corrección menor de 10 es de dudoso valor. La reducción del riesgo es tan pequeña que no se justificaría el gasto de la inversión. Valores entre 10 y 20 indican que la acción está justificada y la experiencia sugiere que un factor mayor que 20 indica que la acción para reducir el riesgo sería de alto valor o altamente justificable.
Análisis de los modos de fallos, efectos y criticidad (AMFEC)
Objetivo
Similar al método cualitativo AMFE, pero con indicación semicuantitativa del grado de criticidad (grado de riesgo) que permite ordenar la importancia de los fallos /efectos, así como las prioridades de medidas correctoras (Storch, 1998;Aguilar, Torres, Magaña, 2010; Troncoso, Vilaragut, 2010).
Descripción
Se parte de la definición de riesgo:
Por otro lado, se tiene que:
Si a la ecuación (8) se aplican logaritmos:
Son estos logaritmos, o mejor sus características, que son los exponentes de 10 correspondientes, los que el método AMFEC toma como índices:
Índice de criticidad = IC = log R (su característica) (11)
Índice de probabilidad = IP = log FP (su característica) (12)
Índice de severidad = IS = log S (su característica) (13)
Con lo que:
La clasificación de fallos mediante sus índices de probabilidad (IP), así como la clasificación de los fallos mediante sus índices de severidad de fallo (IS) es mostrada (Tablas 10 y 11).
Se considera adoptar medidas protectoras al menos para los fallos que resulten con un índice de criticidad:
Métodos cuantitativos para el análisis de riesgos
Son métodos detallados que se inician en el origen de los fallos o averías y que consideran las relaciones causa-efecto de forma estructural, secuencial y cuantitativa, así como las relaciones entre las mismas (confluencia o concurrencia). Los más utilizados son los análisis cuantitativos mediante árboles de fallos, árboles de sucesos y análisis de causas y consecuencias.
Al aplicar cualquiera de estos métodos deben tenerse en cuenta las siguientes recomendaciones generales:
Analizar la calidad de los datos probabilísticos o estadísticos a utilizar y la homogeneidad de su expresión, en particular cuando se obtienen en diferentes bases de datos.
Incluir riesgos originados en errores de diseño, así como en operación y mantenimiento de las plantas.
Comparar los resultados del análisis con los correspondientes a plantas y/o procesos semejantes o iguales: pueden detectarse así errores en el análisis o en los datos.
Analizar la incertidumbre y la sensibilidad del análisis.
A continuación, se expone el método cuantitativo de árbol de fallos muy utilizado en la práctica. Es frecuente el uso de este método para una exploración detallada y profunda de aquellos sistemas (complejos) que hayan demostrado fuentes de riesgo muy alto en los análisis generales realizados en comparación con otros métodos cualitativos o semicuantitativos (Storch, 1998; Perry, Green, 2008; Calderon, 2016; López, Alonso, Ricardo, 2018; Análisis, 2020).
Análisis cuantitativo mediante árboles de fallos (ACAF)
Objetivo
Analizar cuantitativamente los eventos o sucesos de fallo en sistemas complejos estimando deductivamente (desde los sucesos básicos al suceso capital) las probabilidades de acontecimiento.
Descripción
La naturaleza y estructura de los árboles de fallos se han descrito más arriba. Igualmente se han definido los conjuntos mínimos de fallos. A continuación, se aborda el análisis cuantitativo de los árboles:
Búsqueda de datos probabilísticos para los sucesos básicos (SB) en las bases de datos.
Homogeneización de los datos: las fuentes de datos para los análisis cuantitativos de riesgos son variadas en su procedencia, alcance y características, por ello se recomienda realizar un análisis crítico de los datos a la hora de aplicarlos a un proyecto o planta determinados.
Deducción de la probabilidad del suceso capital (SC) del árbol a partir de las probabilidades individuales de los SB y a través de la lógica del árbol:
Análisis de incertidumbre o sensibilidad.
Análisis probabilístico de los conjuntos mínimos de fallos (CMF). Permite discernir la probabilidad de concurrencia de sucesos básicos (SB) que determinan la ocurrencia del suceso capital. Obtenidas las probabilidades para los conjuntos mínimos de fallos, se traducen éstos a los términos accidentales de los SB contenidos y se enjuician su aceptabilidad y/o mejora.
Análisis de importancia de los conjuntos mínimos de fallos para establecer los CMF críticos para la instalación evaluada.
Procedimiento
Análisis de proceso, equipo y servicios auxiliares; preparación de las listas de sucesos, construcción del árbol de fallos, determinación de los conjuntos mínimos de fallos y análisis cualitativo del árbol: según se trató más arriba.
Recolección, asignación y homogeneización de datos probabilísticos para los sucesos básicos (SB).
Resolución probabilística del árbol. Comprobar que los resultados, final e intermedios, sean plausibles; si no: repasar los datos y la lógica del árbol.
Análisis de incertidumbre si se considera necesario.
Análisis probabilístico de los CMF. Muy útil para enjuiciamiento y mejoras.
Análisis de importancia de los SB si se considera necesario.
Enjuiciamiento de la probabilidad del suceso capital frente a los criterios de aceptabilidad. Definición, asignación y control probabilístico de mejoras.
Limitaciones
La aplicación del método es cara en tiempo y medios (acceso a bases de datos, programas informáticos para elaboración, etc.).
Existe la posibilidad de no detectar fallos (SB o SC) que quedarían sin considerar.
Pueden no detectarse fallos en modo común o efectos de los mismos.
Para ilustrar de manera simplificada el procedimiento descrito, se presenta (Figura 5) el mismo árbol de fallos visto anteriormente (Figura 4) pero, considerando la probabilidad (supuesta) de ocurrencia de cada suceso básico en términos de frecuencia
CMF (I): (1) y (2); P = 1. 10 -3 + 2. 10 -3 = 3. 10 -3
CMF (II): (3)(4); P = (1. 10 -1 ) (1. 10 -2 ) = 1. 10 -3
CMF (III): No hay
CMF (IV):[(5 + (7) (8) (9)]; [(6 + (7) (8) (9)]
Probabilidad del SI entre las puertas D y E: (5 + 6): P = (1,5. 10 -2 + 1. 10 -2 ) = 2,5x10 -2
Probabilidad del SI entre las puertas D y F: (7) (8) (9):
P = (1. 10 -1 ) (1. 10 -1 ) (1. 10 -1 ) = 1x10 -3
Probabilidad del SI entre las puertas A y D: P = (2,5. 10 -2 ) (1. 10 -3 ) = 2,5x10 -5
La probabilidad de ocurrencia del suceso capital (PSC) será:
P SC = 3. 10 -3 + 1. 10 -3 + 2,5. 10 -5 = 4,025. 10 -3 sucesos/año
La disminución de la probabilidad o frecuencia probabilística del SC, por ejemplo, hasta 1x10-4 sucesos/año, o menor, podría lograrse introduciendo mejoras que constituyan SB en el CMF (II)(A-C), debajo de la puerta C, y/o en el CMF (IV), debajo de la puerta F, o disminuyendo la probabilidad de ocurrencia de los sucesos básicos 1, 2, 5 y 6, o de alguno de ellos, de resultar posible técnicamente, y el grado de reducción de dicha frecuencia que pudiera lograrse lo justifique económicamente.
Método Bow-Tie para el análisis de riesgos
El método Bow-tie toma el nombre por la similitud del diagrama que se elabora para el análisis, con una corbata de lazo/moño o corbatín. Es una manera esquemática de describir y evaluar la ruta de un riesgo, desde las amenazas o causas iniciadoras hasta las consecuencias o impactos finales. Resulta una combinación de dos técnicas diferentes: un árbol de fallos (lado izquierdo) analizando las causas de un accidente o evento tope, por ejemplo, escape tóxico, incendio, explosión, etc. (representado por el nudo de una corbata de lazo) y un árbol de sucesos o eventos (lado derecho) analizando las consecuencias. Sin embargo, el enfoque del Bow-tie está en las barreras existentes entre las causas y el riesgo (medios y medidas de control preventivo) y las barreras existentes entre riesgo y consecuencias (medios y medidas de mitigación), indicadas mediante rectángulos o barras en posición vertical (Figura 6). (Ormelia, 2016; El método, 2017).
El objetivo del análisis Bow-tie es presentar de manera gráfica un escenario de riesgo, mostrando un rango de posibles causas y consecuencias, y las barreras o capas de protección existentes para evitar o interrumpir la secuencia del accidente. Se diferencian las barreras preventivas de las de mitigación, resultando ideal para comprender la dinámica de posibles accidentes mayores, debido a que facilita una conceptualización de los riesgos de una manera muy clara y visual, facilitando la identificación y análisis de las variables involucradas.
Para la elaboración de un diagrama Bow-tie se requieren conocimientos e información sobre los factores que podrían favorecer las causas y magnitud de las consecuencias de un riego. Entre estos factores se encuentran los denominados “factores de escalamiento”. Estos factores se refieren a los fallos que pueden presentar los medios de control instalados y que deben ser considerados en el análisis.
El siguiente paso lógico para gestionar los factores de escalamiento es crear barreras para los mismos, denominadas “barreras del factor de escalamiento”.
El método puede ser utilizado de forma cualitativa o cuantitativa (utilizando frecuencias de ocurrencia de eventos y probabilidad de falla de las distintas barreras o capas de protección). Constituye una herramienta muy efectiva para comunicar los resultados de un análisis de accidentes mayores en una instalación a personal de todo nivel, y que de hecho más importan a los ejecutivos de una empresa.
Matrices de riesgo
Constituyen un método simple de categorización del riesgo a partir del análisis combinado de la probabilidad de ocurrencia del evento indeseado y las consecuencias de sus efectos.
Las matrices se construyen en dos ejes, donde un eje representa el incremento de las consecuencias y el otro el incremento de la probabilidad de ocurrencia. El grado de urgencia o criticidad se establece interceptando ambos ejes. Aunque no es un método que permite cuantificar el riesgo con precisión, en muchos casos es suficiente para establecer prioridades sin ser necesario la realización de un análisis cuantitativo de riesgo (En que, 2015; Cuatro, 2019; Madrid, Serrano, 2019). Se muestra una matriz de riesgo clásica con cuatro niveles de probabilidad de ocurrencia del accidente o sea, que se presente el escenario de riesgo y cuatro niveles de consecuencias (Figura 7). (Camejo, Alonso, 2016; Camejo, Sibila, Hernández, 2019).
Las celdas o cuadrículas rojas indican niveles altos de riesgos que se consideran inaceptables, por lo que requieren actuaciones inmediatas para su disminución hasta niveles aceptables (cuadrículas verdes), en primer lugar, aquellos cuyas consecuencias pudieran resultar catastróficas (Figura 7).
Las cuadrículas amarillas indican niveles medios de riesgos que deben ser disminuidos hasta aceptables, siempre que sea posible técnicamente y el grado de reducción del riesgo que se logre justifique la inversión (Figura 7).
En cuanto a los riesgos aceptables (cuadrículas verdes), se requiere actuar sistemáticamente en función de que los mismos se mantengan en ese nivel, en particular mediante la elaboración y cumplimiento de los programas de inspección y mantenimiento requeridos.
A continuación, se presentan a manera de ejemplo, criterios o indicadores para expresar cualitativa y cuantitativamente la probabilidad de ocurrencia de los escenarios de riesgo y la clasificación cualitativa de las consecuencias.
Probabilidad del escenario de riesgo cualitativa y en términos de frecuencia probabilística (accidentes/año) de ocurrencia de fallos o averías:
Frecuente (Muy alta): 10-2< FRECUENCIA ESTIMADA ≤ 10-1 accidentes/año
Periódica (Alta): 10-3< FRECUENCIA ESTIMADA ≤ 10-2 accidentes/año
Ocasional (Media): 10-4< FRECUENCIA ESTIMADA ≤ 10-3accidentes/año
Remota (Baja): 10-5< FRECUENCIA ESTIMADA ≤ 10-4accidentes/año
Catastrófica: muerte de trabajadores, daños a la instalación con pérdidas iguales o superiores al millón de USD, lesiones, muertes o daños a instalaciones vecinas o ambientales graves, en exterior de la instalación.
Alta: lesiones incapacitantes permanentemente a trabajadores, daños a la instalación con pérdidas financieras iguales o superiores a los 50000 pero menores que un millón de USD. Lesiones leves a personas en el exterior de la instalación, afectaciones ambientales de consideración, pero recuperables a corto o mediano plazo
Moderada: lesiones leves o incapacitantes temporalmente a trabajadores, daños en la instalación con pérdidas iguales o superiores a los 100 000 pero menores que 500 000 USD, afectaciones ambientales no violatorias de las regulaciones establecidas.
Baja: problemas operacionales, incidentes, pérdidas financieras mínimas.
Tienen una amplia utilización de conjunto con otros métodos de estudio (QPS, AMFE, HAZOP, etc.), para facilitar la jerarquización de los riesgos identificados (Zamora, Caballero, Camejo, 2015; Camejo, Sibila, Hernández, 2019).
Frecuentemente se elaboran matrices para la evaluación, por separado, de los riegos económicos, para la salud y para el medio ambiente
Discusión
Dentro de los métodos de estudio más utilizados para el análisis de riesgos de procesos con sustancias peligrosas, a partir de la definición de sus objetivos, descripción, procedimiento y limitaciones, se confirma que: el método cualitativo HAZOP es el más estructurado entre los métodos disponibles actualmente para el análisis y evaluación de riesgos de accidentes con sustancias peligrosas, resultando una herramienta muy poderosa para la identificación de riesgos en procesos con cualquier nivel de complejidad; el método cuantitativo de análisis mediante árboles de fallos ACAF es recomendado para procesos complejos que incluyan muchos aparatos, instrumentos, operadores, equipos para control, etc., especialmente después de aplicado el método HAZOP, u otro método cualitativo o semicuantitativo, para profundizar en el análisis de los riegos de sucesos (accidentes) que, según el mismo, podrían tener consecuencias muy graves o catastróficas, por lo que se requiere precisar las mejoras que podrían introducirse como SB en el árbol de fallos para disminuir la probabilidad de ocurrencia de tales sucesos, utilizando al árbol como un medio de simulación.
Por otra parte, el método Bow-Tie encuentra aplicación cuando se pretende centrar el análisis en las barreras de control, o sea de los medios y mediadas técnicas, técnico-organizativas y humanas de protección (preventivas y de mitigación), para determinar sus suficiencias e insuficiencias, así como las mejoras que deben introducirse para alcanzar los niveles de protección requeridos.
Independientemente del método de estudio que se utilice, la presencia en el equipo que ha de conformarse para la realización de estudios de riesgo, de personas con conocimiento profundo de los procesos objeto de estudio, así como de las secuencias accidentales que pudieran ocurrir, resulta imprescindible para garantizar la objetividad y valor práctico del estudio realizado.
Conclusiones
Este estudio permitió establecer una descripción y caracterización precisa de los métodos de estudios cualitativos, semicuantitativos y cuantitativos, predictivos, más utilizados para el análisis de riesgos de procesos con peligro de accidente mayor; especialidad de suma importancia que debe estar presente tanto en las etapas de diseño y construcción, como en las de explotación, mantenimiento y desactivación de las instalaciones, con el fin de prevenir los riesgos de accidentes mayores y evitar, además de las pérdidas económicas directas e indirectas, las pérdidas valiosas de vidas humanas, así como afectaciones ambientales irreversibles.
De esta forma, se cuenta con un material de consulta que, además de agrupar los métodos, le facilitará tanto a especialistas como a ejecutivos, establecer la selección adecuada del o los métodos a la hora de realizar un estudio para el análisis y evaluación de riesgos de accidentes mayores en una instalación determinada