Introducción
El acero resistente al calor Cr25Ni20 (ACI HK 40), es un material importante que se utiliza ampliamente en dispositivos de hornos y tubos industriales de alta temperatura. Esta es una aleación base Fe(Cr(Ni con una matriz austenítica.1-3
La formación de microestructuras de solidificación puede proporcionar información útil sobre el proceso de fundición en aleaciones base Fe(Cr(Ni. La ruta de solidificación y la posterior transformación sólida en las mismas, depende de su composición química [2]. Estudios previos realizados por Fu et al. 4 demostraron que las rutas de solidificación y las transiciones de fase se pueden predecir teóricamente de acuerdo con la composición en la aleación de equivalentes de Cr y Ni. Estos autores argumentaron que el análisis y evaluación de estos materiales pueden realizarse mediante el uso de diagramas de fases.
Kim et al. 5 y Whittaker et al. 6 plantean que la modelación de las transformaciones de fases permite aclarar los detalles de sus formaciones microestructurales de solidificación, especialmente de la última etapa. Inoue y Koseki 7, Calliari et al. 8 y Xianfei et al. 9, consideran que los datos de la modelación son muy importantes para evaluar sus propiedades y defectos en los procesos de fundición y soldadura.
Ding et al. 10 establecen que la ruta de transición de fase de la aleación ACI HK 40 es L → L + γ → L + γ + M7C3 → γ + M7C3 → γ + M7C3 + M23C6 → γ + M23C6. Estos autores concluyeron que en la aleación ACI HK 40, la dendrita γ primaria crece en un ángulo inclinado de aproximadamente 30° con respecto a la dirección del gradiente de temperatura, debido a la simetría cúbica subyacente. Fu et al.11 determinaron que los carburos eutécticos precipitan directamente en el líquido, y este se vuelve más viscoso durante el proceso de enfriamiento.
Sin embargo, Argains-Juarez et al.12 y Goković-Gekić et al. 13, afirman que, en casos reales, la secuencia de solidificación en aceros austeníticos también depende de la velocidad de solidificación, lo que influye en la posible competencia de crecimiento entre las fases sólidas estable y metaestable, a través del subenfriamiento cinético requerido para su crecimiento. Las variaciones en la tasa de solidificación también afectan la cantidad de ferrita, y provocan su aumento o disminución, dependiendo de la secuencia de solidificación para la tasa de solidificación considerada.
Guo et al. 14, reportan que durante el proceso de explotación de un tubo de aleación ACI HK 40 sometidos a altas temperaturas, los carburos primarios M7C3 y NbC se transforman en carburos del tipo M23C6 y fases (, respectivamente, y que una gran cantidad de carburos secundarios del tipo M23C6 precipitaron en el interior de las dendritas. Estos autores demostraron que los cambios de fase en la aleación ACI HK 40 no solo afectan su microestructura durante el proceso de solidificación, sino que estas transformaciones pueden ocurrir también durante el proceso de explotación. De la misma forma Kondrat’ev et al. 15, demostraron que durante la exposición a 1 000 h y 1 150 ºC de una probeta de acero termorresistente ACI HP40 NbTi, los carburos eutécticos primarios se vuelven gruesos y una gran cantidad de carburos secundarios se precipitan en el interior de la dendrita.
Es importante considerar el comportamiento de la aleación durante la fundición, para garantizar un procesamiento eficaz del material (fundición, maquinado y tratamiento térmico) durante las etapas de elaboración de piezas sometidas a altas temperaturas y una microestructura que garantice el conjunto de propiedades y requerimientos durante las operaciones.14,16
La obtención del diagrama de fases permite estudiar la evolución de las fracciones de fases sólidas, durante la solidificación en condiciones de equilibrio, en los rangos de temperatura y composición correspondientes a las zonas de precipitación de las fases obtenidas, en correspondencia con las propiedades mecánicas estimadas.17,18 Además, se puede pronosticar la evolución de la microestructura del acero al someterlo a elevadas temperaturas, prevenir la precipitación de fases secundarias indeseadas como las fases sigma (σ), y predecir la viabilidad de aplicar tratamientos térmicos para inducir la precipitación de dichas fases secundarias, lo que podría incrementar la termoresistencia de la aleación.10,16
La utilización de softwares informáticos especializados permite realizar la modelación y simulación de las transformaciones de fases, con mayor precisión y rapidez que los métodos tradicionales. El Thermo-Calc es un software flexible, aplicable para todo tipo de cálculo termodinámico y de diagramas multifases y multicomponentes arbitrarios, que contiene una base de datos que cubre 83 elementos químicos en estado puro, y 5 043 sustancias y compuestos químicos de las más disímiles naturalezas (metálicos, intermetálicos, sólidos, líquidos, gases y minerales) agrupados en distintos módulos, según sus características específicas.19
El programa utiliza cálculos de diagramas de fases para extrapolar descripciones termodinámicas, y luego aplicarlas a sistemas de “n” componentes, basado sobre la evaluación de datos experimentales de diagramas binarios, ternarios y de orden superior, incorporados a la base de datos. Con la utilización de varios modelos, se minimiza la energía libre de Gibbs de las fases en el sistema generado por el programa, y sobre la base de estos cálculos, se definen las fases y regiones de menor energía libre, donde las ecuaciones de balance, acción y conservación de masa se satisfacen a través de soluciones matemáticas y termodinámicas.20
La técnica de Minimización de Energía Libre de Gibbs para el cálculo de equilibrio de fases, está soportada en 4 modelos: (1) Energía Libre de Gibbs (GES), para el tratamiento de las fases estables calculadas; (2) Cálculo de equilibrio heterogéneo (POLY), para el tratamiento de los cálculos en condiciones de equilibrio heterogéneo; (3) Tabulación (TAB), para el tratamiento de las derivadas de las funciones termodinámicas y sus constantes, y (4) Optimización de parámetros (PARROT), para el tratamiento de las variables termodinámicas evaluadas.
Thermo-Calc verifica cálculos termodinámicos, aplicando funciones termodinámicas de estado siguiendo la primera y segunda leyes de la termodinámica.
En las que G, A, U y H son las energías de Gibbs Helmholtz, interna y la entalpía, respectivamente (kJ · mol-1); S es la entropía del sistema (kJ mol-1 K-1; T la temperatura (K); P es la presión (Pa); V el volumen (m3); ( es el potencial químico (kJ mol-1 y N la cantidad de sustancia (Mole).
Estas funciones de estado simplifican la descripción del estado de equilibrio, con las correspondientes ventajas que reporta el uso de las mismas, dependiendo en cómo se controla el sistema según las cuatro posibilidades siguientes:
Cuando se controla la temperatura, presión y composición, la función más apropiada es la energía de Gibbs (G), debido a que G es mínima (ΔG = 0) durante el equilibrio.
Si se controla la temperatura, el volumen y la composición, la función más apropiada sería la energía de Helmholtz (A) debido a que A es mínima cuando se alcanza el equilibrio.
Si se controla la entropía, el volumen y la composición del sistema, se asegura que la energía interna (U) sea la mínima al alcanzarse el equilibrio.
El control de la entropía, la presión y la composición del sistema conlleva a que la entalpía (H) sea la función más apropiada, por ser H mínima cuando se alcanza el equilibrio.
En este trabajo se realiza la simulación del diagrama de fases de la aleación termorresistente ACI HK 40, modificada con la adición de diferentes contenidos de aluminio y boro, utilizando el software Thermo-Calc
Materiales y métodos
Para la simulación de los diagramas, se utilizó el módulo TCFE4 de TCW.4 (versión 2010a). Inicialmente se estudiaron tres posibles variantes de aleaciones con diferentes contenidos de aluminio y boro (% en masa). Los cálculos se realizaron sobre la base de las composiciones prefijadas en la tabla 1, y las variaciones propuestas en la tabla 2.
Tabla 1 Elementos incluidos en las bases de datos de TCFE4
Elemento | % peso | Elemento | % peso | Elemento | % peso |
---|---|---|---|---|---|
Al | 5,0 | Cu | 1,0 | Nb | 5,0 |
B | 1,0 | Mg | Trazas | Ni | 22,0 |
C | 5,0 | Mn | 20,0 | O | Trazas |
Co | 15,0 | Mo | 10,0 | P | Trazas |
Cr | 30,0 | N | 1,0 | S | Trazas |
Si | 5,0 | Ti | 2,0 | V | 5,0 |
W | 15,0 | Fe | 50,0 mínimo |
Tabla 2 Composición química de las aleaciones propuestas
Elemento (%) | Aleación I (HK-40 + Al) | Aleación II (HK-40 + B) | Aleación III (HK-40 + Al + B) |
C | 0,4-0,45 | 0,4-0,45 | 0,4-0,45 |
Si (máx.) | 1,0 | 1,0 | 1,0 |
Mn (máx.) | 1,0 | 1,0 | 1,0 |
Cr | 24,0 | 24,0 | 24,0 |
Mo (máx.) | 0,5 | 0,5 | 0,5 |
Ni | 22,0 | 22,0 | 22,0 |
Al | 1,5 | --- | 1,0 |
B | --- | 0,5 | 0,5 |
P (máx.) | 0,015 | 0,015 | 0,015 |
S (máx.) | 0,02 | 0,02 | 0,02 |
Fe | Balance (49,4) | Balance(50,4) | Balance(49,4) |
Masa total (kg) | 20 | 20 | 20 |
El análisis se efectuó considerando dos aspectos, la composición de la aleación: acero fundido altamente aleado en cromo, níquel y carbono, en presencia de otros microconstituyentes como silicio, manganeso y aluminio. Estos elementos poseen diferentes temperaturas de solidificación, pero a su vez, pueden reaccionar entre sí para formar otros compuestos intermetálicos, y en segundo lugar, este acero en estado de fundición es una microestructura compuesta fundamentalmente por dendritas.21
Luego de definidas las condiciones de temperatura (máxima: 1 400 °C) y presión (máxima: 100 000 Pa), así como la composición elemental porcentual de las aleaciones, se precisará el diagrama de fase correspondiente a cada aleación.
Para determinar y caracterizar de forma experimental las fases predominantes en las aleaciones para los diferentes estados, el grado de desajuste entre las partículas y la matriz, la morfología y los parámetros de la matriz ( y los precipitados de ('; se realizaron análisis con técnicas de Microscopía Electrónica de Barrido (MEB), utilizando un microscopio electrónico de barrido PHILIPS Xl 40 SFEG.
Resultados y discusión
Las figuras 1, 2 y 3 muestran los resultados de los diagramas de fases simulados para las aleaciones I, II y III. Para la aleación I (figura 1) se reporta la evolución de las fracciones en por ciento en masa de las fases principales: líquido; fase austenítica “(”, y en menor cantidad la fase ferrítica “(" (hasta 5 % a 400 °C), correspondientes a la matriz metálica, fase (' y fases de carburos complejos del tipo M7C3 a elevadas temperaturas, en la región libre de (' y carburos del tipo M23C6 (alrededor de 28 %), que prevalecen hasta bajas temperaturas.
Las temperaturas calculadas correspondientes al líquido, sólido y solubilidad de (' son 1 375 °C, 1 292 °C y 1 021 °C, respectivamente. El gráfico indica, además, los rangos de temperatura adecuados para los tratamientos de solubilización por encima de 1 287 °C, y envejecimiento por debajo de 1 021 °C, y la fracción de (' a las temperaturas de análisis 10-15 %.
Estos rangos de temperatura y composición correspondientes a las zonas de precipitación de las fases reportadas, sugieren la factibilidad de obtener un material con características termodinámicas similares a las de la aleación diseñada en correspondencia con las propiedades mecánicas prefijadas. Además, es posible pronosticar la evolución de la microestructura del acero al someterlo a elevadas temperaturas, prevenir la precipitación de fases secundarias perjudiciales como las fases σ, y predecir la viabilidad de aplicar tratamientos térmicos de envejecimiento para inducir la precipitación de fases (' secundarias, que junto a las fases de carburos M23C6 podrían incrementar las propiedades de termoresistencia de la aleación propuesta en los rangos de temperatura prefijados.
En los diagramas mostrados en las figuras 2 y 3 se aprecia un incremento en la cantidad de fases sigma precipitadas (35 %) hasta temperaturas de 400 °C, la ausencia de fases (', y un descenso en las cantidades de carburos del tipo M23C6 (alrededor de 10 %).
Simulación de la segregación primaria
La segregación química primaria ocurre durante la cristalización de la aleación. Durante este proceso, las dendritas crecen con gradientes de concentración y, por consiguiente, la composición final del medio interdendrítico difiere de la composición de la aleación. Para efectuar el análisis de la ocurrencia de los fenómenos de microsegregación, es preciso estudiar la evolución de las fracciones de fases sólidas durante la solidificación en función de la temperatura, lo que es posible realizar también con el uso del software Thermo-Calc. Los análisis se verificaron bajo condiciones de equilibrio y se utilizó el modelo de la aproximación de Scheil. Durante la solidificación en condiciones de equilibrio, las pequeñas velocidades de enfriamiento favorecen la ocurrencia de los procesos difusivos y las transformaciones ocurren totalmente.
En la figura 4 se muestra la evolución de la fracción sólida durante la solidificación de la aleación I en condiciones de equilibrio, en función de la temperatura, reportada por el software Thermo-Calcy utilizando la aproximación de Scheil. El modelo de Scheil asume una homogeneidad perfecta en la fracción líquida, y la no ocurrencia de difusión en la fracción sólida, lo que realmente no ocurre a las temperaturas en las que se realizó el proceso de simulación y, en consecuencia, debido a que los procesos retrodifusivos reducen la microsegregación, es lógico que los perfiles de concentración durante la solidificación se encuentren en la región comprendida entre los pronosticados, asumiendo el equilibrio y los pronosticados utilizando la aproximación de Scheil.
Como se observa, ambas curvas presentan similitudes en las temperaturas de líquido y sólido, acentuándose la diferencia cuando la temperatura alcanza valores alrededor de los 1 350 °C. Se observa, que para las condiciones extremas analizadas (presencia y ausencia de difusión en la fase sólida), el perfil de concentración se debe tomar entre los valores pronosticados comprendidos entre ambas curvas, lo que conduce a un análisis más engorroso, que puede simplificarse utilizando el modelo de aproximación de Scheil.
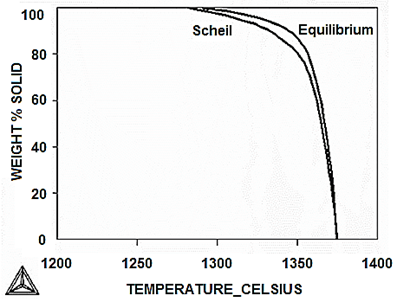
Fig. 4 Evolución de la fracción total de sólido en la aleación I pronosticada para condiciones de equilibrio y la aproximación de Scheil
El cromo y el níquel (figura 5) segregan ligeramente desde el líquido hasta que se ha alcanzado aproximadamente el 40 % de la fracción de sólido. Las cantidades de ambos elementos permanece dentro de un rango del 10 % de la composición nominal hasta que, aproximadamente el 86 % del material ha solidificado, momento en que, además, parte del cromo precipita desde el líquido para formar parte de los carburos complejos del tipo M7C3, lo cual constituye una de las formas de segregación esperadas según el diagrama de equilibrio de la figura 4. En este caso, es de esperar que “M” en M7C3 sea principalmente cromo.
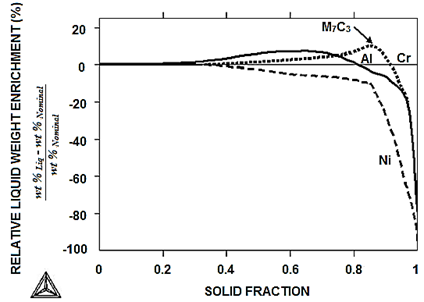
Fig. 5 Evolución de las concentraciones relativas de Cr, Ni y Al en el líquido durante la solidificación de la aleación I
En la figura 6 se muestra la ampliación de la zona correspondiente a la ventana de solidificación del Al y el Ni para la aleación I. Como se puede observar, las partículas (' no precipitan desde el aluminio y el níquel hasta tanto no se haya alcanzado aproximadamente el 99,75 % de sólido.
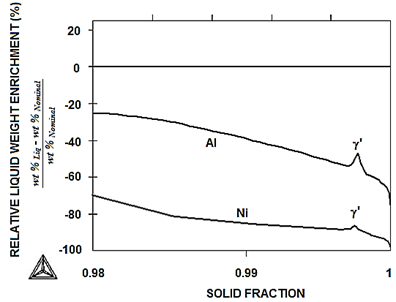
Fig. 6 Ampliación de la zona correspondiente a la ventana de solidificación del Al y el Ni en la aleación I
Durante la evolución de las concentraciones relativas de Fe y C en el líquido durante el progreso de la solidificación para la aleación I (figura 8), el hierro se concentra ligeramente en el sólido hasta que se alcanza un 96 % de la fracción sólida. El carbono no segrega del líquido hasta tanto los carburos no comienzan a precipitar.
Los resultados de la evolución de las concentraciones relativas de Cr, Ni y Al en el líquido durante la solidificación, zona correspondiente a la ventana de solidificación del Al y el Ni y evolución de las concentraciones relativas de Fe y C en el líquido durante el progreso de la solidificación, mostrados en las figuras 5, 6 y 7, se corresponden con los obtenidos previamente en el diagrama de fases mostrado en la figura 1(aleación I) en el sentido de que en esta nueva aleación no se pronostica la formación de fases indeseables a las temperaturas de interés.
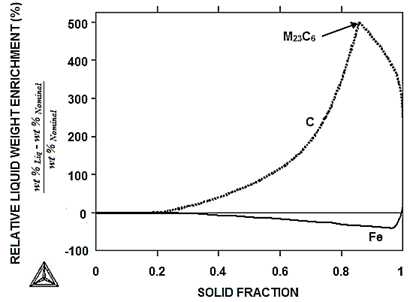
Fig. 7 Evolución de las concentraciones relativas de Fe y C en el líquido durante el progreso de la solidificación para la aleación I
Estos resultados de la simulación de las transformaciones de fases sugieren descartar, a priori, las aleaciones II y III, pues analizando cuidadosamente todos los diagramas obtenidos, en los mismos se puede observar, en mayor masa, fases y estructuras indeseadas (fases σ), tanto a temperatura ambiente como a altas temperaturas, y la ausencia de las fases responsables del endurecimiento por precipitación: carburos M23C6 y partículas ('.
Predicción del desajuste
Los parámetros de las redes ( y (’ se utilizaron para estimar el grado de desajuste cristalográfico entre las matrices ( y (’, según la ecuación (1). En esta ecuación se deduce que esta magnitud es proporcional a la diferencia entre los parámetros de las redes ( y ('. El signo de este parámetro lo determinan los valores absolutos de (( y (('. Cuando (( > ((', el desajuste es positivo, mientras que si el mismo es negativo significa que la fase (' tiene parámetro de la red menor que el de la fase (. Las cantidades relativas de (( y ((' deben ser controladas para lograr los bajos valores requeridos y una morfología uniforme en los precipitados. En la figura 8 se muestra el pronóstico de la evolución del desajuste de las redes (/(’ con la temperatura para las composiciones en equilibrio.
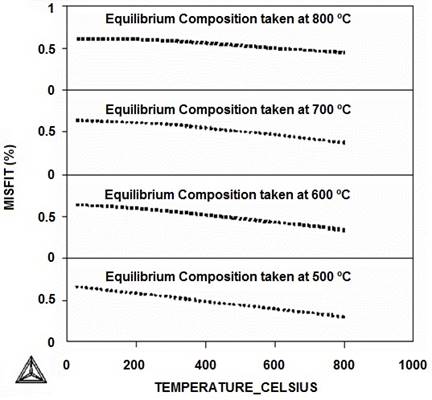
Fig. 8 Pronóstico de la evolución del desajuste de las redes (/(’ de la aleación I con la temperatura
Como se observa, el grado de desajuste pronosticado es pequeño, tanto a temperatura ambiente como a las temperaturas de servicio, y toma valores entre 0,25 y 0,5; lo que está en correspondencia con los resultados deseados. Estos pequeños valores de grado de desajuste resultan beneficiosos para el funcionamiento de la aleación, pues incrementan la resistencia a la termofluencia al estabilizar la interfase (/(', y dificultan el crecimiento de las partículas (' y su aglomeración durante la termofluencia a elevadas temperaturas.
En resumen, los diagramas de las figuras 5, 6 y 7 revelan la no presencia de fases indeseables después de la solidificación de la aleación I. La presencia de pequeñas cantidades de fase ferrítica ( (hasta 5 %) en la aleación I (figura 1) no afecta en modo alguno la estabilidad microestructural de aleación a las temperaturas de trabajo, en el sentido de que esas cantidades no son suficientes para promover fases secundarias indeseables como las fases σ, resultados que coinciden con los de Velázquez.22 La predicción de la no ocurrencia de fenómenos de microsegregación durante la solidificación de la aleación pronosticada utilizando la aproximación de Scheil, es un factor esencial para considerar en la valoración de la calidad de la aleación I pues, conjuntamente con los resultados mostrados en la figura 1, permite pronosticar una estabilidad microestructural de la aleación durante las exposiciones a largo plazo a elevadas temperaturas.
La presencia de fases indeseables como las fases sigma y ferrítica, en cantidades superiores al 5 % indica que se descarten las aleaciones II y III. Estos resultados parciales obtenidos mediante las simulaciones justifican que la aleación I sea tomada como aleación patrón por cumplir a priori, los requisitos de ingeniería establecidos desde el punto de vista metalúrgico (microestructura de la aleación) y mecánico (termoresistencia de la aleación), resultados que serán verificados en el próximo capítulo a través de los correspondientes ensayos.
Análisis microestructural y microanálisis de las aleaciones
El análisis microestructural de las aleaciones I, II y II en estado fundido, mostrado en las figuras 9, 10 y 11, permitió determinar la presencia de una microestructura formada por granos dendríticos típicos de acero inoxidable fundido. En el caso de la aleación I (figura 9), se observan anchas franjas de carburos que bordean los granos austeníticos y de partículas distribuidas uniformemente por toda la matriz. En las aleaciones II y III (figuras 10 y 11) se aprecian franjas de carburos en el límite de los granos austeníticos, fase ferrítica y partículas (' acompañadas de fases sigma dispersas en la vecindad del borde los granos.
En las figuras 12, 13, y 14 se muestran los espectros EDAX correspondientes a las fases ferrítica y sigma de las aleaciones II y III. En estas figuras, la altura de los picos de Fe denota el predominio de este elemento en las fases analizadas, reportándose, además, la presencia del Cr y Ni disueltos en las mismas. Los espectros EDAX correspondientes a cada microanálisis aparece el contenido de cada elemento en fracción másica (Wt %) y por ciento atómico (At %). La presencia de cromo, hierro y níquel en fases sigma pertenecientes a aceros austeníticos fundidos también fue reportada por Velázquez.22
Los resultados de los análisis metalográficos resumidos y de los microanálisis mostrados en las figuras 12-15, tienen plena correspondencia con los pronósticos de los diagramas de fases analizados.
Después de realizar el análisis de los resultados se llegó a las siguientes consideraciones:
Los diagramas de fases obtenidos para las aleaciones evaluadas pronostican a las temperaturas de análisis, la presencia de las fases austenítica “(”, ferrítica “(" con cantidades inferiores al 5 %; gamma prima “('”, carburos complejos del tipo M23C6 para la aleación I. La ausencia de gamma prima “('” y presencia de fases sigma, con un incremento considerable de la fase ferrítica y un descenso en las cantidades de carburos del tipo M23C6, se predicen para las aleaciones II y III.
Se verificó que durante la solidificación de la aleación I las concentraciones relativas de Cr y Ni permanece dentro de un rango del 10 % de la composición nominal hasta que, aproximadamente el 86 % del material ha solidificado, momento en que parte del cromo precipita desde el líquido para formar parte de los carburos complejos del tipo M7C3, lo cual constituye una de las formas de segregación esperadas según el diagrama de equilibrio.
Se demostró, que durante la evolución de las concentraciones relativas de Fe y C en el líquido en el progreso de la solidificación para la aleación I, el hierro se concentra ligeramente en el sólido hasta que se alcanza un 96 % de la fracción sólida. El carbono no se separa del líquido hasta tanto los carburos no comienzan a precipitar.
Conclusiones
La presencia de una estructura austenítica con extensas bandas de carburos distribuidos en el borde de los granos y precipitados intermetálicos dispersos en la matriz de la aleación I y la existencia de una fase ferrítica con fracciones volumétricas superiores al 10 % y fases sigma en las aleaciones II y III, permiten validar el criterio de selección de la aleación I como la idónea para evaluar su comportamiento mecánico, fundamentalmente el conjunto de requisitos metalúrgicos relacionados con la estabilidad microestructural y presencia de las fases deseadas.