INTRODUCCIÓN
Según su origen, los eventos capaces de ocasionar desastres pueden ser: naturales, tecnológicos o sanitarios. Si bien las causas que originan los accidentes naturales (tormentas, huracanes, terremotos, maremotos, etc.) y los tecnológicos son independientes; los accidentes de origen natural pueden provocar el desarrollo de accidentes tecnológicos. Pudiera tratarse de una fuerte tormenta o de un sismo intenso que ocasione daños al equipamiento, así como de alguno de los componentes tecnológicos de una instalación industrial.
Contrario a los eventos naturales, los accidentes de origen tecnológico son evitables. Ocupan un lugar importante entre estos, los denominados accidentes mayores. Estos se definen como cualquier suceso tal como la fuga de gases o derrames de líquidos tóxicos y/o inflamables, incendio o explosión, que sea consecuencia del desarrollo incontrolado de una actividad industrial o de servicios. De ahí a que, los trabajadores, la instalación, el medio ambiente y/o a la comunidad u otras instalaciones, ubicadas en su entorno exterior, se expongan a un alto riesgo inmediato o diferido, creando por tanto una situación de emergencia. De esta forma, los estudios para el análisis y evaluación de riesgos en instalaciones con peligro de accidentes mayores, constituyen una valiosa herramienta científico-técnica, aplicable tanto en las etapas de diseño y proyecto, como en las de construcción y operación de las mismas (Storch, 1998; Camejo, Alfonso, 2016).
El desarrollo tecnológico creciente en las industrias y el comercio, encaminado a satisfacer las necesidades progresivas de la sociedad, ha conducido al incremento de riesgos de accidentes de gran magnitud. Muchos procesos industriales trabajan en condiciones críticas de presión, temperatura, con volúmenes elevados de materiales o sustancias peligrosas debido a su inflamabilidad, toxicidad y/o corrosividad, que a su vez tienen que ser producidas, transportadas y almacenadas. Todos ellos han representado un aumento progresivo de los peligros de accidentes mayores y, por ende, un considerable incremento del número de personas, tanto trabajadores como ciudadanos en general, expuestas a dichos peligros.
Las consecuencias de estos accidentes en el entorno de las instalaciones en que se producen suelen ser: daños a la salud o pérdidas de vidas humanas, impactos ambientales negativos, perjuicios económicos y efectos psicológicos en la población, comprometiendo la imagen de la industria y los gobiernos (Camejo, Alfonso, 2016; Camejo, Domínguez, Marrero, 2008; Camejo, Parad, 2014).
La Central Termoeléctrica “Otto Parellada”, comúnmente conocida como “Tallapiedra”; está destinada a la generación de electricidad a partir de la producción de vapor sobrecalentado. La misma pertenece al Grupo Empresarial Generación Distribuidora de Ciudad Habana (GediCH) de la Unión Nacional Eléctrica (UNE) del Ministerio de Energía y Minas. Está ubicada en el consejo popular Jesús María del municipio La Habana Vieja, exactamente en la calle Alambique entre Diaria y Avenida del Puerto. Sus coordenadas geográficas son: Longitud Oeste 82°21'35.19" y Latitud Norte 23° 7'30.61". Se trata de una zona de densidad poblacional elevada. En la figura 1 se presenta una imagen satelital de la central y su entorno.
El objetivo general de este estudio fue identificar y analizar de forma preliminar los principales riesgos de accidentes mayores presentes en los procesos que integran la operación de la central termoeléctrica “Otto Parellada”.
Para el cumplimiento de este objetivo, se utilizaron una serie de herramientas ingenieriles contenidas en la metodología de estudio para el análisis y evaluación de riesgos de desastres por accidentes mayores en la industria química. Es evidente que, la detección y prevención a tiempo de la posible ocurrencia de incidentes o accidentes, frecuentemente causados, directa o indirectamente, por el fenómeno de la corrosión de cualquier naturaleza, es decir, química o electroquímica, incrementa la durabilidad y la vida útil de todo equipamiento y proceso tecnológico en la industria y contribuye a evitar las pérdidas de vidas humanas debido a la ocurrencia de accidentes (Camejo, Marrero, Betancourt, 2007).
METODOLOGIA
Para la realización del estudio se aplicaron los procedimientos y métodos propios del análisis de la seguridad o análisis de riesgos de procesos, partiendo de su caracterización tecnológica y peligrosidad, como se expone a continuación en forma sintetizada (Camejo, Alfonso, 2016; Camejo, Domínguez, Marrero, 2008).
Descripción resumida del proceso tecnológico de la Central Termoeléctrica “Otto Parellada”
La central termoeléctrica (CTE) “Otto Parellada”, cuenta con un generador de vapor (caldera) checoslovaco marca BRNO, acuotubular de paredes de fuego. Es el encargado de producir vapor con los parámetros necesarios para ser suministrado al turbogenerador (turbina) de que dispone, así como para suplir el consumo requerido para el trabajo de la planta.
La caldera es de circulación natural con un domo para evaporación en dos etapas y se compone de: precalentadores y calentadores de aire, economizadores, condensador de vapor saturado, domo, paredes de agua, cabezales inferiores, horno, 15 quemadores, ocho en la pared frontal y siete en la trasera, sobrecalentadores, sistema de atemperar, válvulas de seguridad en los sobrecalentadores y en el domo, nivostatos, ventiladores de tiro forzado e inducido para el suministro de aire a los quemadores, ventiladores de tiro inducido para la circulación de los gases de combustión desde el horno hasta la chimenea, sistemas de extracciones y drenajes.
El vapor sobrecalentado producido en la caldera que normalmente se encuentra a 90 atm (9,0 MPa) y 545ºC, se inyecta a un turbogenerador marca SKODA con una potencia nominal de 64 MW y una potencia económica de 60 MW. En la figura 2 aparece una representación esquemática de los principales procesos que se desarrollan en la CTE.
El combustible es suministrado a la CTE mediante embarcaciones, o mediante el empleo de los camiones cisternas, pudiendo ser descargado a dos de las tres cisternas soterradas existentes, construidas de material cerámico, o directamente a los tanques de almacenamiento y proceso. Las cisternas a las que puede descargarse el combustible desde la embarcación (patana), tienen una capacidad de 600 m3 y 700 m3 respectivamente. La tercera, denominada tanque mezcla, se emplea para recoger los residuos oleosos de las diferentes áreas. De las cisternas, el combustible se bombea hacia los tanques de proceso construidos de acero con capacidad de 1200 m3 cada uno, desde los cuales se suministra a la caldera, como se muestra en la figura 2.
Antes de su entrada a los quemadores de la caldera, el fuel oíl se hace pasar por los calentadores de combustible. Como parte del sistema de protección, las bombas que suministran el combustible a la caldera, no entran en funcionamiento sin la arrancada previa del sistema de aire y gas para evitar la posible acumulación de combustible en el interior del horno o de gases de combustión. Además, se dispone de un sistema de recirculación que permite el reenvío del combustible no consumido en los quemadores, a los tanques.
El consumo de combustible es de 17,8 ton/h y antes de su entrada a los quemadores se le inyecta un aditivo para disminuir la acción corrosiva de los gases. La relación aditivo combustible es de: un litro de aditivo por un m3 de combustible. Los tanques del proceso poseen cubetos de contención de aceros al carbono, cuyo volumen es equivalente al del tanque correspondiente.
El agua de reposición a la caldera proviene de la planta de tratamiento químico de que dispone la CTE. Su tecnología corresponde al método de desmineralización por intercambio iónico antecedida por una etapa de decloración con la utilización del carbón activado. En la misma, se utiliza ácido sulfúrico (H2SO4) para la regeneración de la resina catiónica fuerte e hidróxido de sodio (NaOH) para la regeneración de la resina aniónica fuerte. Ambos son suministrados a la entidad mediante camiones cisternas, aunque el NaOH puede recibirse también en estado sólido para su disolución en la propia planta. El H2SO4 es almacenado en un tanque de 20 toneladas, construido de acero al carbono, con un recubrimiento interior de plomo para su protección contra la corrosión. El tanque es instalado sobre un cubeto de 20 m3, construido de ladrillos recubierto con cemento y láminas de plomo, para contener los posibles derrames provenientes del tanque. Desde el tanque, el H2SO4 se bombea al tanque disolutor y después se hace circular por la torre de intercambio catiónico.
Previo a su introducción a la caldera tanto el agua desmineralizada de reposición como el condensado, son sometidos a un proceso de desgasificación con el objetivo de eliminar los gases incondensables, especialmente los gases corrosivos como son el anhídrido carbónico y el oxígeno. Para eliminar el oxígeno remanente, el que aún a concentraciones muy bajas en el agua, puede provocar serios problemas de corrosión en las condiciones de trabajo de la caldera, se inyecta a la entrada de la misma hidracina, la que reacciona con el oxígeno y lo elimina según la ecuación:
Por último, el tratamiento químico del agua culmina con la inyección de fosfato trisódico (Na3PO4) al interior del domo. Este compuesto, inhibidor de la corrosión, ejerce determinado poder buffer de manera que, a la concentración requerida, se logra un pH del agua en el interior de la caldera comprendido entre 6,5 y 7, haciendo insignificante su acción corrosiva (Domínguez, Castro, Matos, Hing, 2006).
Caracterización de la peligrosidad de las sustancias manipuladas en la CTE
Fuel oíl
Es el combustible más pesado de los que se pueden destilar a presión atmosférica. Posee un aspecto de líquido oscuro viscoso con olor característico. Es estable, pero por encima de 620C sus vapores pueden formar con el aire (oxígeno) mezclas explosivas. Puede reaccionar con violencia frente a materiales oxidantes. Su combustión incrementa las emisiones gaseosas a la atmósfera de humos tóxicos de aldehídos, acetonas, así como gases como CO y CO2. Las propiedades físicas y químicas se pueden encontrar en la literatura especializada y en las fichas técnicas y de seguridad (Perry, Green, 2008).
Ácido sulfúrico (H2SO4 al 98%)
Es un líquido ligeramente viscoso, incoloro, más denso que el agua, corrosivo, e inodoro. Sus vapores son tóxicos por inhalación, resultando la concentración máxima permisible en el puesto de trabajo (CMPT) 3 mg/m3. La concentración Límite Inmediatamente Peligrosa para la Vida y la Salud (IDLH, por sus siglas en inglés) y su concentración letal 50 (CL50%) 15 y 510 mg/m3 respectivamente. Como concentrado, es sofocante e higroscópico. No es inflamable, ni combustible; sin embargo, al presentar una concentración elevada puede causar combustión al estar en contacto con líquidos y sólidos. Es corrosivo y reacciona de forma exotérmica vigorosamente al entrar en contacto con el agua. Puede dar lugar a la ignición (inicio de una explosión) al entrar en contacto con materia orgánica y compuestos tales como carburos, cloratos, nitratos, metales en polvo, sodio, fósforo, acetona, entre otros. De ahí, la posibilidad de ocurrencia de eventos accidentales en caso de una manipulación deficiente. Sus principales propiedades químico-físicas y toxicidad pueden obtenerse en la literatura especializada y en las hojas y fichas de seguridad química (Pauling, 1965).
Sosa cáustica (NaOH al 48%)
Se puede encontrar en forma de líquido viscoso en una disolución al 48% o en estado sólido, el cual es de color blanquecino, inodoro y absorbe humedad del aire (higroscópico). Es corrosivo y estable. Tiende a reaccionar violentamente con hidrocarburos clorados, acetileno, plomo, aluminio, cobre, amoníaco, cianuro, estaño, provocando la formación de hidrogeno inflamable gaseoso. Al entrar en contacto con agua, ácidos y líquidos inflamables y compuestos halogenados orgánicos, especialmente el tricloroetileno, libera una gran cantidad de calor que puede ser suficiente como para encender materiales combustibles causando incendios y explosiones. El contacto con nitrometano y otros nitros similares, causan la formación de sales sensibles a los impactos. Ataca a algunas clases de plásticos, cauchos y revestimientos (Pauling, 1965)
Breve caracterización de los residuales y desechos del proceso y del tratamiento para su neutralización
La quema de combustible es la principal fuente de residuales y contaminación en la central. Durante su funcionamiento normal se emiten diferentes sustancias tóxicas (gases) contaminantes a la atmósfera, en mayor o menor magnitud en dependencia del combustible utilizado y de la tecnología empleada en la generación de la electricidad. Entre las sustancias tóxicas contaminantes se incluyen principalmente: el SO2, los óxidos de nitrógeno (NOx), el material particulado (MP) (cenizas, hollín, polvos), aldehídos, el CO e hidrocarburos (HC) que forman parte de su composición química. Además, las emisiones gaseosas pueden contener elementos menores proporciones presentes en el combustible utilizado. En la atmósfera, las reacciones fotoquímicas pueden dar lugar a nuevos contaminantes (H2SO4, CaSO4, NaSO4 y otros). De esta forma, pudiera producirse una agresividad corrosiva de la atmósfera clasificada como media (C3) llegando a ser elevada (C4) en la zona donde se encuentra la central. Los resultados de estudios de corrosión atmosférica ejecutados en las proximidades de la central, han demostrado la existencia de una atmosfera industrial debido a la elevada deposición de compuestos de azufre o iones sulfato (Castañeda et al, 2006; Corvo et al, 2008). Se trata de una atmósfera no muy perjudicial para el acero al carbono, pero si para las aleaciones de cobre y aluminio. Esto pudiera ser un factor esencial basado en la durabilidad que han mantenido los elementos de acero al carbono expuestos a la atmósfera, desde la instalación de los componentes y equipos tecnológicos, durante el largo proceso de funcionamiento que ha presentado la CTE en el tiempo de explotación. Por otra parte, la quema de combustibles fósiles, libera apreciables cantidades de CO2 que, aunque no es tóxico, juega un papel importante como gas de efecto de invernadero. Para la disminución de la emisión de estos compuestos, la unidad presenta filtros a la salida de los gases por la chimenea.
La central dispone de una canalización que recorre la planta completa al que se vierten los residuales oleosos, los que son depositados en el tanque mezcla. No se dispone de un sistema para el tratamiento adecuado del resto de los residuales y deshechos que se generan en el proceso. Solamente presentan trampas para eliminar los aceites y petróleos que acompañan a las aguas que se expulsan a la bahía de La Habana (aguas ácidas de lavado y limpieza de la caldera, aguas oleosas, etc.). La dirección de la entidad es consciente de las afectaciones que provocan a la bahía constituyendo un impacto ambiental negativo, por lo que tienen proyectado la construcción de una planta de tratamiento de residuales. Hasta la fecha, no han podido disponer del presupuesto para el financiamiento de la planta.
Sistemas, medios y medidas técnicas, técnico-organizativas y humanas, activas y pasivas de protección (prevención y mitigación) existentes.
Según la información obtenida durante la investigación realizada, entre los medios técnicos y medidas técnico-organizativas y humanas establecidas en la central para lograr la seguridad requerida de los procesos y operaciones que se desarrollan en la misma, se encuentran:
La central dispone de una sala de control que es un sistema integrado, para la puesta en marcha y control automático de la operación de los sistemas de suministro de combustible, aire y agua, y de circulación y extracción de los gases de combustión, así como todos los parámetros indicativos del funcionamiento de la caldera y turbina. En general, los principales indicadores o parámetros registrados y controlados son: flujos, presiones, temperaturas y niveles.
En los casos que resulta necesario, existen alarmas que se activan cuando el parámetro controlado alcanza cierto valor y se requiere la intervención del operador para ajustarlo al valor que corresponda a la operación normalmente prevista o detenerla si fuera necesario. También existen dispositivos para la parada por emergencia de la caldera como son los nivostatos.
Todos los equipos o aparatos que trabajan normalmente a presiones por encima de la atmosférica, disponen de válvulas de seguridad. En el caso de la caldera tiene instaladas varias válvulas de seguridad tanto en el domo como en los sobrecalentadores, calibradas con diferentes presiones de consigna o disparo.
Se lleva un control periódico y monitoreo de los equipos que participan en el proceso. Este control se registra en el expediente de cada equipo, donde se reportan aspectos como el tiempo de explotación y los mantenimientos realizados.
La instalación dispone de las normas de explotación elaboradas por la Unión Nacional Eléctrica (UNE) específicas de la central, en las que se describe la función y reglamenta la operación correcta y control de los diferentes sistemas y equipos que los integran, tales como: norma de operación del sistema de regulación (lazos de control) de la unidad, norma general de caldera, norma de combustible, norma del sistema de aire y gases, norma del sistema de vapor de uso de planta, norma de agua de alimentar, sistema de agua de enfriamiento y norma de la planta de tratamiento químico de agua.
Se realizan pruebas de medición de espesores y pruebas de termografías con cámaras termografías para detectar zonas calientes en los sistemas de tuberías, producto principalmente a las deficiencias en el aislamiento.
Por otra parte, se supervisa que las maniobras de arranque, purgas y paradas de caldera se realicen con la mayor seguridad para las personas, el medio ambiente y la propia instalación. Además, están establecidas otras medidas y regulaciones como son:
Las maniobras para la intervención en componentes del sistema eléctrico, válvulas, bombas, tanques y otros equipos para su mantenimiento o reparación, se ejecuten según la secuencia establecida en los procedimientos, con las medidas de seguridad requeridas y en coordinación con los responsables en la sala de control. Todo ello es supervisado por el especialista que ocupa el cargo denominado ʺInspector de Explotaciónʺ por ser parte de sus funciones como miembro de la Dirección de la CTE.
La vigilancia en cuanto al comportamiento de presiones, temperaturas, niveles de caudales volumétricos, consumo y demás parámetros del proceso, se efectúe de modo continuo, comprobando que se correspondan con los valores de referencia.
Los posibles problemas o disfunciones se identifiquen y en su caso, se tramiten de forma inmediata, para que los responsables actúen según los protocolos establecidos, con el propósito de restituir la condición de funcionamiento estable o asegurar la puesta en servicio de los dispositivos de emergencias.
Considerando el peligro de incendio presente en la instalación, el Comando # 1 del cuerpo de bomberos de La Habana realiza inspecciones periódicas a diferentes áreas, principalmente donde se encuentran instalados los tanques de almacenamiento de combustible. La unidad posee:
Una brigada contra incendio preparada para actuar en situaciones de emergencia.
Medios pasivos de protección como son el cubeto de los tanques de almacenamiento de combustible, así como de muros protectores que contribuyen a disminuir la distancia de la propagación de un posible incendio y/o explosión. Se dispone de las vías de acceso y escape que posibiliten la evacuación del personal en caso de producirse un incendio. Dentro de los medios activos de protección se tienen los extintores y una línea de agua de extinción que recorre todas las áreas de la instalación.
Se garantiza que todos los trabajadores posean la capacitación necesaria y los medios de protección individual, según el trabajo a desempeñar.
Gestión de mantenimiento
A nivel nacional, la UNE tiene establecido un sistema de mantenimiento para estos tipos de instalaciones que comprende:
Mantenimiento general de 5 días (2 o 3 veces al año).
Mantenimiento general de 45 días (1 vez al año).
Mantenimiento capital (cada 5 años).
Sin embargo, en la práctica por diversas razones, no se cumple con estos períodos en el tiempo establecido. En particular, con el mantenimiento general de 45 días y el capital cada 5 años. Por ejemplo, en esta central termoeléctrica, se debió haber realizado un mantenimiento capital en el año 2016, pero no fue hasta el año 2018 que fue llevado a cabo, luego de haberse producido un incendio en los precalentadores de aire por combustión de residuos sólidos acumulados en los mismos. El incendio se produjo, cuando se intentó poner en funcionamiento el generador de vapor, después de haber realizado una limpieza química en el mismo.
Caracterización del medio físico en el entorno de la instalación y su interacción con la misma
Como se ha indicado, la empresa se encuentra ubicada en el municipio Habana Vieja, en la localidad Jesús María, dentro de una comunidad densamente poblada. En los alrededores de la instalación se localizan principalmente viviendas y vías de alta densidad de tráfico automotor y de ferrocarril, como son la avenida del Puerto y la calle Alambique. Se encuentra cerca de la bahía de La Habana como se muestra en la figura 1. En caso de un accidente mayor, el entorno de la planta pudiera ser afectado de manera considerable, produciendo daños tanto humanos como ambientales y económicos.
El proceso de producción de electricidad a partir de la combustión del petróleo o sus derivados, puede provocar afectaciones directas al medio ambiente con la emisión de gases contaminantes y altamente corrosivos en presencia de niveles elevados de humedad relativa. Por otra parte, el ruido indeseable asociado al funcionamiento de los equipos del proceso, puede afectar a las zonas habitacionales aledañas a la instalación. Además, como ya se expuso, se vierten fluidos residuales tóxicos a la bahía sin el tratamiento previo requerido.
Recopilación de información relativa a incidentes y accidentes ocurridos con anterioridad
Aunque no existe en la instalación un registro completo de los incidentes y accidentes mayores ocurridos, a partir del estudio realizado se pudo recopilar cierta información con respecto a los eventos y accidentes ocurridos en la central en los últimos tres años:
Año 2017: Incendio de pequeñas proporciones en los precalentadores de aire por combustión de residuos sólidos acumulados, luego de realizar una limpieza en el generador de vapor.
Año 2018: Durante el proceso de descarga de combustible desde la patana hacia los tanques, se produjo un derrame apreciable del fuel oíl por deficiencias en el bombeo, lo que obligó a la extracción del derrame y la sustitución del suelo.
Año 2019: Derrame de una cantidad apreciable de H2SO4 durante el proceso de descarga desde el camión cisterna debido al empleo de una tubería de material inadecuado (acero al carbono sin recubrimiento interior de plomo).
De manera general, se trata de la ocurrencia de eventos accidentales que deben ser evitados en cualquier industria que opere con sustancias tóxicas y/o inflamables.
Identificación de los peligros de accidentes mayores presentes en el proceso: derrames, escapes, incendio y/o explosión
Para la identificación de los peligros y riesgos de accidentes en la CTE “Otto Parellada”, se utilizó el esquema de flujo del proceso tecnológico representado en la figura 2, así como la amplia información disponible en las normas de operación de los diferentes sistemas que integran dicho proceso. A partir de esta herramienta ingenieril, fueron identificados los peligros de accidente mayor en cada equipo o etapa del proceso. Se trata de los peligros de derrame o escape de líquidos o gases tóxicos y/o inflamables, incendio o explosión, considerando el estado físico, presión y temperatura de operación, propiedades físico-químicas, nivel de toxicidad, formas de contención, y volúmenes de las sustancias involucradas. Esto permite obtener el mapa o matriz de peligros de accidentes mayores de la instalación.
Estimación de la distancia de alcance de los efectos peligrosos (concentración tóxica) de posibles derrames de H2SO4
Para estimar la distancia de alcance (variación con la distancia) de la concentración de la nube tóxica de vapor formada a partir de posibles derrames de H2SO4 en el tanque de almacenamiento, recogidos en el cubeto de contención existente, se utilizó el programa informático ALOHA versión 5.4.1 (Areal Locations of Hazardous Atmospheres). Este programa, desarrollado por The CAMEO Software System, permite simular el desplazamiento (dispersión) de la nube tóxica en la atmósfera, considerando dos niveles (clases) de estabilidad atmosférica: la clase D, con velocidad del viento 5 m/s que se corresponde con el nivel medio de estabilidad atmosférica, que es el más frecuente y la clase F que se corresponde con una atmósfera muy estable con velocidades del viento menor que 2 m/s (Storch, 1998; Camejo, Alfonso, 2016). En la Tabla 1 aparecen las cantidades derramadas de sulfúrico que se consideraron para las simulaciones, las concentraciones para las cuales se determinaron las distancias de alcance, así como el resto de las variables y condiciones introducidas en el programa para la simulación de los diferentes escenarios considerados.
Análisis de los riesgos de accidentes mayores presentes en la instalación
Para el análisis preliminar de los riesgos de accidentes mayores presentes en la instalación, se aplicaron los métodos cualitativos denominados Análisis de Modos de Fallos y sus Efectos (AMFE) y Análisis mediante Árboles de Fallos (AAF):
El método AMFE tiene los siguientes objetivos (Storch, 1998; Camejo, Alfonso, 2016):
Establecer los fallos posibles en todos los elementos y equipos (de proceso y de control) en una planta.
Analizar las consecuencias de los fallos detectados en el objetivo anterior, con el propósito de detectar aquellos que puedan dar origen a la ocurrencia de accidentes.
Establecer medidas de protección para evitar los fallos que sean significativos según el objetivo anterior.
Es un método que va directamente a los fallos importantes procedentes de la experiencia y del funcionamiento de los aparatos, que requiere pocos analistas. No es sistemático, por lo que pueden pasarse por alto, fallos y consecuencias. No considera combinaciones de fallos coincidentes o en secuencia. Aplicable a distintas etapas de proyecto y a la operación de plantas o procesos existentes de complejidad relativamente baja. Se aplicó para el análisis de los riesgos presentes en el sistema de combustible y el de ácido sulfúrico.
El método de Análisis de Árbol de Fallos (AAF) tiene los siguientes objetivos (Storch, 1998; Camejo, Alfonso, 2016):
Análisis cualitativo de los eventos o sucesos de fallo en sistemas complejos.
Descomposición inductiva de sucesos complejos en otros escalonadamente más sencillos hasta llegar a sucesos básicos (de sencillez máxima) que pueden considerarse como causas iniciadoras. La descomposición se hace dejando establecida la estructura (árbol de fallos) que representa las relaciones (causa-efecto) y las interacciones (concomitancias «Y», así como alternativas «O») entre sucesos.
Dejar preparado el marco estructural citado que sirve para realizar análisis cualitativos, semicuantitativos y cuantitativos de las relaciones y de las interacciones citadas.
Permite diferenciar terminológicamente los fallos de los componentes de las instalaciones y de los errores en el comportamiento humano. Se trata de un método deductivo de análisis que parte de la previa selección de un "suceso no deseado o evento que se pretende evitar", sea éste un accidente de gran magnitud (explosión, fuga, derrame, etc.) o se trate de un suceso de menor importancia (fallo de un sistema de cierre, etc.) para averiguar en ambos casos los orígenes de los mismos. Seguidamente, de forma sistemática y lógica, se representan las combinaciones de las situaciones que pueden dar lugar a la producción del "evento a evitar", conformando niveles sucesivos. De tal manera que cada suceso esté generado a partir de sucesos del nivel inferior, siendo el nexo de unión entre niveles, la existencia de "operadores o puertas lógicas". El árbol se desarrolla en sus distintas ramas hasta alcanzar una serie de "sucesos básicos", denominados así debido a que no se precisan de otros sucesos anteriores para ser explicados. También alguna rama puede terminar por alcanzar un "suceso no desarrollado" en otros, sea por falta de información o por la poca utilidad de analizar las causas que lo producen.
ANALISIS DE LOS RESULTADOS
Mapa de peligros de accidentes mayores presentes en la instalación
En la Tabla 2, se presenta el mapa de peligros de accidentes mayores que están presentes en la CTE “Otto Parellada”, a partir de los principales equipos y aparatos que intervienen en las diferentes etapas.
Los peligros más comunes están asociados a los derrames tóxicos de H2SO4 y a los derrames inflamables, incendios y explosiones que se pueden producir en tanques, bombas, válvulas y tuberías que transportan el fuel oíl, lo que podría ocurrir debido, entre otras causas, a la insuficiente inspección y mantenimiento, al empleo de materiales inadecuados, incumplimiento de las normas de explotación, rotura mecánica de los equipos y al deterioro por corrosión electroquímica.
Por otra parte, el generador de vapor es el equipo con mayor peligro, en el que es posible la explosión por sobrepresión del domo debido a fallos del sistema de control y de las válvulas de seguridad instaladas, o por pérdida de espesor de sus paredes o la explosión en el horno por acumulación de combustible sin quemar en su interior, como resultado de errores de operación durante la parada o puesta en marcha, por ejemplo.
Estimación de la distancia de alcance de diferentes niveles de concentración tóxica por posibles derrames de H2SO4
Como se ha indicado anteriormente, para la estimación de la distancia a la que pueden alcanzarse diferentes concentraciones en la atmósfera de la nube tóxica, formada a partir de un posible derrame de ácido sulfúrico concentrado (H2SO4 al 98%) en el tanque de almacenamiento del mismo, lo que afectaría fundamentalmente la salud de las personas, se empleó el programa ALOHA, para la simulación de diferentes escenarios, considerando el derrame de 1, 5, 10, 15, y 20 ton.
En la Tabla 3, se muestran las distancias en metros (m) que alcanzarían los distintos niveles de concentración tóxica evaluados para las diferentes cantidades de H2SO4 derramadas y clases de estabilidad atmosféricas consideradas.
Las distancias que alcanzan cada una de las concentraciones para una misma clase de estabilidad atmosférica son prácticamente las mismas para las diferentes cantidades de ácido sulfúrico derramadas. Esto es determinado por el hecho de que los derrames se recogen en el cubeto sobre el cual está ubicado el tanque. De esta forma, el área de evaporación del ácido derramado es la misma en todos los casos, lo que evidencia, en este caso, la importancia del cubeto como medio pasivo de mitigación de las consecuencias de un derrame tóxico. No obstante, en todos los casos, las concentraciones tóxicas especialmente las correspondientes al IDLH y la CMPT, alcanzarían el entorno exterior de la instalación produciendo afectaciones de diferentes grados en las personas ubicadas en el mismo de forma permanente o temporal (residentes y transeúntes). El número de personas afectadas aumentaría en la medida que resulte mayor la estabilidad de la atmósfera al momento de producirse el derrame. Al ser menor la velocidad del viento, entre otros factores, la nube tóxica se desplaza a mayores distancias con menor dispersión, como puede apreciarse en la Tabla 3 para estabilidad atmosférica clase F.
En la figura 3 se presenta a modo de ejemplo, la imagen que genera el programa ALOHA representando las distancias (longitudes) y amplitudes, o sea, las áreas que alcanzarían en la dirección del viento las diferentes concentraciones evaluadas para el caso del derrame de una tonelada de H2SO4, estabilidad atmosférica clase D. La zona roja corresponde a la CL50%, la naranja al IDLH y la zona amarilla al CMPT.
Análisis de riesgos por el método de Modo de Fallos y sus Efectos
En las Tablas 4 y 5 se presentan los resultados obtenidos a partir de la aplicación del método de estudio indicado a los sistemas de ácido sulfúrico y fuel oíl respectivamente. Como puede apreciarse, los principales modos de fallos identificados están relacionados con el posible incumplimiento de los estándares y procedimientos de trabajo establecidos, deterioro físico y/o químico por corrosión de los tanques, tuberías y accesorios. Estos modos de fallos pueden incrementarse, en caso de insuficiencias en las inspecciones y revisiones, así como en el mantenimiento, fundamentalmente si no se realizan en los periodos de tiempo y con la calidad requerida.
Análisis de riesgos por el método de Árbol de Fallos
En las figuras 4, 5 y 6 se representan las diferentes secciones del análisis de riesgos de accidentes mayores que están presentes en la CTE “Otto Parellada”, por el método de Árbol de Fallos; a partir de considerar como suceso tope no deseado (evento que se pretende evitar) una posible explosión del generador de vapor, considerando que la misma podría producirse por: explosión del domo, recalentamiento excesivo de los tubos o explosión del hogar o cámara de combustión. El árbol de fallos obtenido está integrado por cinco conjuntos mínimos de fallos (CMF), uno por cada rama del árbol de fallos, que agrupan 19 sucesos básicos. Los CMF obtenidos fueron: dos, de orden III; uno, de orden IV; uno, de orden V; uno, de orden VII; como se indica a continuación (el orden de un CMF indica el número de sucesos básicos que tienen que ocurrir para que se produzca el evento tope):
CMF (VII): (A-B-C-D-E-F): (1+2+3+4+3+5+3)
CMF (IV): (A-B-G-H-I): (6+3+7+3)
CMF (III): (A-J-K): (6+8+9)
CMF (III): (A-J-L-M): (10+13+14), (11+13+14), (12+13+14)
CMF (V): (A-N-O): (15+16+17+18+19)
Un suceso básico que aparece en muchos CMF debe ser objeto de atención por encima de los demás debido a que está aportando a la probabilidad de fallos en muchas alternativas. Para determinar su importancia relativa, debe ponderarse el número de veces con el inverso del orden de los CMF en que aparece. Como se puede apreciar en la Tabla 6, ocupan un primer lugar en importancia los sucesos 13 y 14 o sea, el fallo del sistema de control automático del agua de alimentación y el fallo del nivostatos. El segundo lugar; el suceso 3, insuficiente inspección y mantenimiento y el tercer lugar lo ocupa el suceso 6, insuficiencias en el tratamiento químico del agua.
Resulta de interés señalar el hecho de que para que se produzca la explosión del domo por sobrepresión en el generador, tienen que producirse siete sucesos básicos, seis de ellos asociados al fallo de los sistemas de protección y del sistema de control automático del agua de alimentación. La posible explosión por deterioro pudiera ocurrir, al producirse cuatro sucesos básicos, ninguno de ellos relacionados con los sistemas de protección (nivostatos y válvulas de seguridad), debido a que estos no están concebidos para proteger a los equipos por deterioro. Esto indica, la importancia de garantizar la integridad mecánica del equipamiento mediante la realización de las inspecciones y mantenimientos en correspondencia con las buenas prácticas reconocidas internacionalmente, lo cual hace posible la operación de los equipos y procesos para las condiciones de diseño inicialmente concebidas, garantizando así tanto su eficiencia como seguridad.
Es válido precisar el hecho de que el fallo de los nivostatos del sistema automático de control del nivel de agua en el domo y el insuficiente tratamiento de la misma, así como la insuficiente inspección, aparecen como sucesos intermedios o sucesos básicos. En varias ocasiones, asociados a la posible explosión de la caldera por explosión del domo y por el recalentamiento de los tubos, (explosión física), lo cual evidencia su papel trascendental en la seguridad de la operación.
Para el caso de que ocurra una explosión en la cámara de combustión (explosión química), deben ocurrir al menos cinco sucesos básicos iniciadores, asociados principalmente al sistema de protección del generador de vapor, a errores en la maniobra de arranque y puesta en marcha del mismo. Esto indica el nivel de seguridad con que trabaja el sistema y, por tanto, la baja probabilidad de ocurrencia del mismo.
Medidas generales recomendadas para mejorar la gestión de riesgos en la CTE
El análisis de riesgos de accidentes mayores en los procesos tecnológicos de la CTE, aplicando las herramientas ingenieriles expuestas, hizo posible recomendar una serie de medidas a implementar por parte de la entidad para mejorar la gestión de riesgos y elevar la seguridad de dichos procesos, las cuales se relacionan a continuación:
Cumplir estrictamente con la realización de las inspecciones a los diferentes equipos y componentes del proceso en los periodos o frecuencias establecidas, con el objetivo de controlar la integridad mecánica de los mismos.
Establecer y ejecutar un programa de mantenimiento que considere la criticidad de los equipos, tanto desde el punto de vista de la eficiencia como de la seguridad de los procesos, asegurando así tanto el aumento de los fallos evitados y gestionados, como la disminución de los fallos sorpresivos.
Elaborar el "manual de proceso" o sea, un repositorio o archivo digital que incluya los siguientes documentos actualizados: diagrama de flujos del proceso; diagramas de equipos, tuberías e instrumentos (P&ID); descripción del proceso incluyendo la descripción funcional de cada equipo que lo integra; instrucciones (normas) de operación; descripción de los sistemas de control, alarmas, enclavamiento y sus diagramas lógicos; las fichas de seguridad de los productos que se incluyen en el proceso.
Proceder con la instalación de la planta de tratamiento para los residuales vertidos a la bahía de la Habana, con la finalidad de asegurar que la carga contaminante de los mismos se corresponda con las normas establecidas.
Las medidas recomendadas para mejorar la gestión de los riesgos en cuanto a la ocurrencia de eventos accidentales, son básicamente de carácter técnico-organizativo. Su implementación conduciría a un costo muy bajo, además de la ejecución de un programa adecuado de mantenimiento. Esto contribuiría a elevar de manera significativa, no solo la seguridad, sino también la eficiencia de los procesos que se desarrollan en la instalación, así como a la disminución del nivel de riesgo que representan para los trabajadores y la población ubicada en su entorno exterior.
La instalación de una planta para el tratamiento de residuales supone una inversión que pudiera tener un costo apreciable. No obstante, su instalación y puesta en funcionamiento con la eficiencia y efectividad requerida, se corresponde con las regulaciones establecidas en el país para la conservación del medio ambiente.
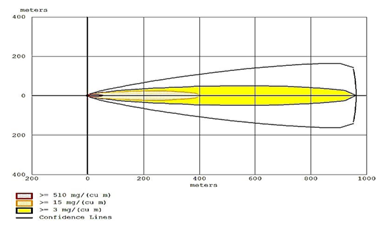
Fig.3. Imagen generada por el programa ALOHA para el derrame de una tonelada ácido sulfúrico, estabilidad atmosférica clase D.
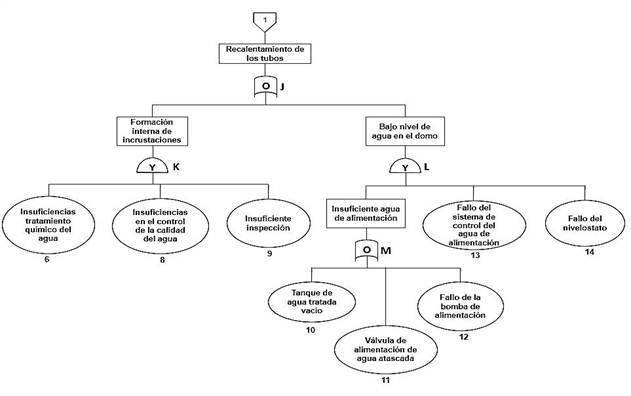
Fig. 5 Sección del árbol de fallos desarrollado para el suceso intermedio: Recalentamiento de los tubos en el generador de vapor.
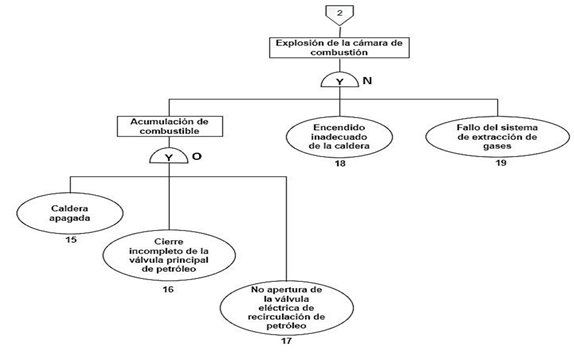
Fig.6. Sección del árbol de fallos desarrollado para el suceso intermedio: Explosión de la cámara de combustión
Tabla 3 Distancias (m), de alcance de las concentraciones tóxicas correspondiente al derrame de 1, 5, 10, 15, y 20 ton de H2SO4.
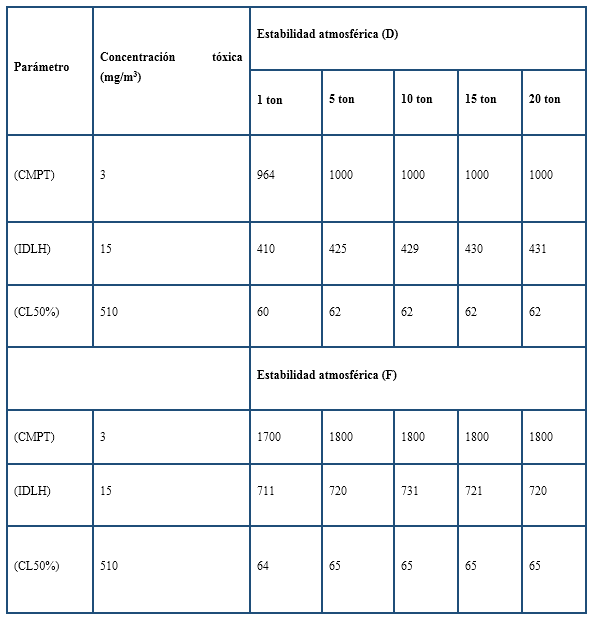
Tabla 5 Resultados del análisis del modo de fallos y sus efectos en el sistema de combustible (Fuel oíl).
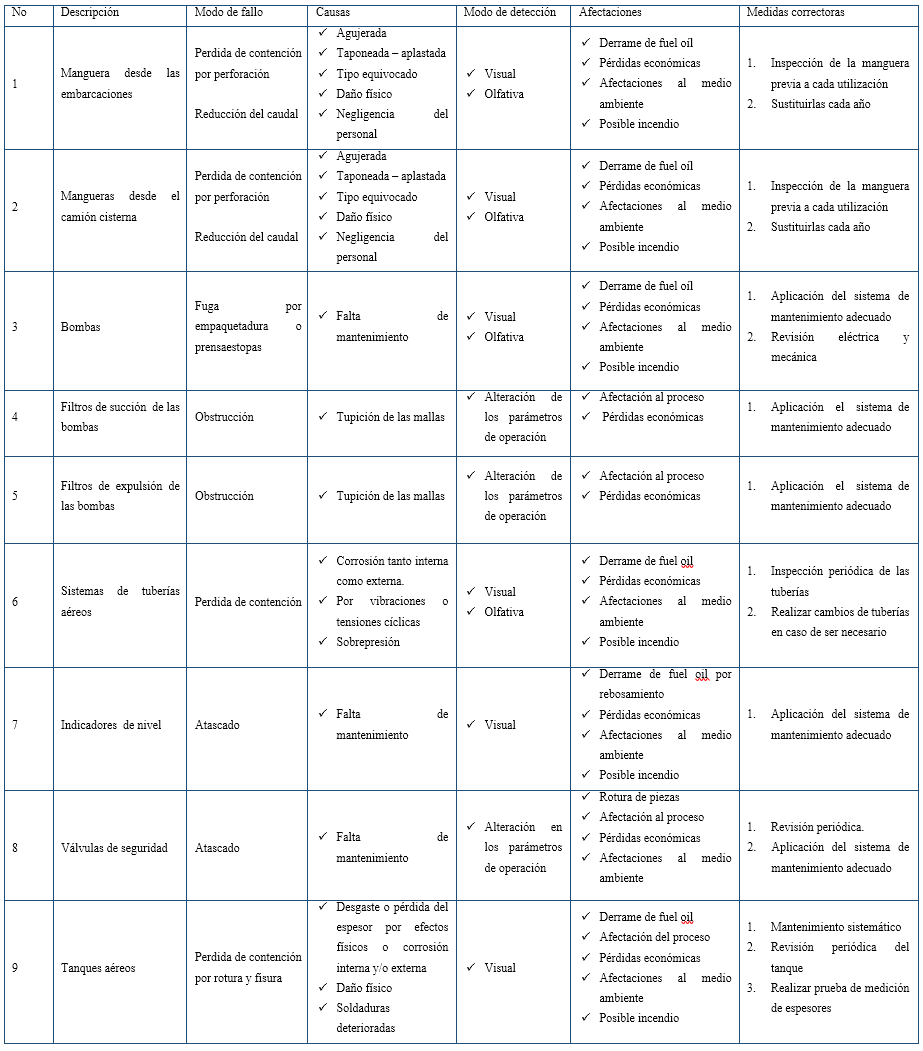
CONCLUSIONES
En la termoeléctrica “Otto Parellada” están presentes los peligros de derrames tóxicos de H2SO4, derrames inflamables de fuel oíl, incendios y explosiones en el sistema de suministro de combustible y en el generador de vapor. Para todos los escenarios considerados para derrames de H2SO4, las concentraciones evaluadas de la nube tóxica formada afectarían tanto al entorno interior como exterior de la instalación. Las principales causas de accidentes mayores identificadas fueron: fallo del sistema de control automático del agua de alimentación; fallo de los sistemas de protección; insuficiente inspección y mantenimiento a equipos e instrumentos, así como insuficiencias en el tratamiento químico del agua. Las medidas recomendadas para mejorar la gestión de seguridad de procesos de la instalación son de tipo técnico-organizativas, relacionadas con la frecuencia y alcance de las inspecciones, mantenimiento y actualización del manual de proceso, así como, proceder con la instalación de una planta de tratamiento de residuales para disminuir la carga contaminante que se vierte actualmente a la bahía. La implementación de las medidas recomendadas contribuiría a elevar la seguridad y eficiencia de los procesos que se desarrollan en la instalación y disminuir los riesgos que los mismos representan para sus trabajadores y la población ubicada en su entorno exterior, correspondiéndose básicamente con las regulaciones establecidas para este tipo de instalación.