Introducción
La simulación numérica ayuda a optimizar los parámetros del proceso durante las primeras etapas de un nuevo diseño, evitando las costosas reparaciones que podrían producirse posteriormente [1]. En [2, 3, 4] desarrollaron una simulación de un proceso de soldadura de una soldadura a tope de planchas de acero hipoeutectoide basados en el método de los elementos finitos, obteniendo resultados similares a la experimentación que realizaron.
Zhang y Shirzadi [5], Yu et al, [6] y Memon et al, [7], emplearon la simulación para estudiar termomecánicamente una unión soldada realizada por el método de fricción agitación tradicional. Memon et al. [7] comparan esta variante con otra sumergida mostrando la existencia de mayores índices de deformación y menor viscosidad en la unión sumergida. Kulawik et al, [8] investigaron la relación entre la tecnología de soldadura por arco de tungsteno con gas (Gas Tungsten Arc Welding, GTAW) y los parámetros de las condiciones de contorno para la simulación del proceso de tratamiento térmico de elementos de acero de medio carbono.
Un modelo termo-mecánico-metalúrgico de una soldadura híbrida para predecir el tamaño de la zona de fusión y la formación de fases fue empleado por Urbanczyk y Adamiec [9] , Du et al, [10] y Han et al, [11]. Los autores emplearon diferentes métodos de soldadura lo que muestra la amplitud de opciones de esta técnica. Chen et al. [12] utilizaron la simulación de procesos de soldadura para estudiar una unión soldada en T por el proceso metal inert gas (MIG) empleando muestras más grandes a las indicadas por las normas para ensayos de tracción. Concluyeron que los parámetros de soldadura tienen una influencia más significativa en las respuestas estructurales que la dimensión de la placa.
Alhafadhi y Krallics [13] y Hu et al, [14] mostraron un procedimiento para predecir los estados de esfuerzos residuales en soldaduras multipasadas. Llegaron a la conclusión de que la simulación 3D puede utilizarse para estimar los esfuerzos residuales en diferentes regiones de la soldadura y ayudar a ahorrar tiempo. Peric et al, [15] realizaron una simulación numérica y en una estructura soldada con parche circular de acero para investigar las distribuciones del campo de temperatura y esfuerzos residuales causadas por la aplicación de la tecnología de soldadura de soldadura de alta densidad de corriente.
Alhafadhi y Krallics [16] estudiaron los efectos de la transformación de fase en estado sólido sobre las tensiones residuales durante la soldadura de aceros de bajo y alto carbono demostrando que los esfuerzos residuales en el acero de bajo carbono no son afectados por el cambio de volumen causado por la transformación austenita - martensita, mientras que los esfuerzos en el acero con alto contenido de sí. Mientras que Zhang et al, [17] estudiaron la evolución y distribución de los esfuerzos residuales térmicos en una soldadura de pasada simple de un acero al carbono. Determinaron que la austenita subenfriada y la deformación debido a la transformación austenítica, fueron cruciales para predecir los esfuerzos residuales de soldadura.
El presente trabajo tiene como objetivo modelar los esfuerzos residuales, la distorsión y los ciclos térmicos de una soldadura por arco de tungsteno con gas (GTAW) de un acero de bajo carbono, empleando el método de los elementos finitos teniendo en cuenta las transformaciones microestructurales.
Métodos y Materiales
Se declaran los materiales de aporte y base empleados. Las propiedades termo - dependientes y el comportamiento microestructural se determinados a través de un software de modelación a partir de la composición química, límite elástico (LE) y resistencia a la tracción (RT) a temperatura ambiente de cada uno de los materiales involucrados.
Se empleó una placa de 200 x 100 x 4 mm (largo x ancho x espesor) de un acero ASTM A - 210 Gr. A1 (B) con preparación de borde en V, ángulo de 60º. Como material de aporte se empleó un alambre ER 70s6 (A). La composición LE y RT a temperatura ambiente para ambos materiales, así como los parámetros de soldadura empleados, se muestran en la tabla 1.
Tabla 1 Composición, LE (MPa), RT (MPa) y parámetros de soldadura empleados. Fuente: [24]
Elemento | ASTM A - 210 Gr. A1 | ER 70s6 | Parámetros | Valores | |
---|---|---|---|---|---|
C | 0,27 | 0,025 | Raíz | Relleno | |
Mn | 0,93 | 1,45 | I: Intensidad de corriente (A) | 104 | 103,7 |
P | 0,035 | 0,008 | v: Velocidad de soldeo (cm/min) | 17,6 | 17,8 |
S | 0,035 | 0,011 | U: Voltaje (V) | 11,4 | 12 |
Si | 0,10 | 0,84 | |||
Cr | - - | 0,025 | |||
Mo | - - | 0,002 | |||
V | - - | 0,002 | |||
Ni | - - | 0,013 | |||
Cu | - - | 0,12 | |||
LE | 255 | 470 | |||
RT | 415 | 573 |
Se estudiaron puntos en la base (y = 0), centro (y = 2 mm) y superficie (y = 4 mm) de la placa en su sección media (z = 100 mm) para analizar el comportamiento de los esfuerzos residuales y la distorsión en el espesor de la geometría. Los puntos en la coordenada x están a 0; 1; 1,5; 2,5; 5; 10; 20; 30; 40; 50; 60; 70; 80 y 90 mm desde el centro del cordón de soldadura. Debido a la simetría de la unión respecto a la dirección de avance de la fuente, solo se modeló el proceso una de las dos placas a unir.
Mallado
Se dividió la pieza en cuatro secciones que coinciden con las zonas de soldadura como se muestra en la figura 1. Se utilizó una malla de 1 mm en la dirección de desplazamiento de la fuente de calor en la ZF siendo el más pequeño, mientras que para el MB se empleó una malla de 1,5 mm.
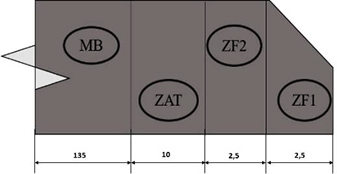
Fig. 1 Seccionamiento para el mallado de las zonas de soldadura. Material Base (MB), Zona Afectada Térmicamente (ZAT) y Zona Fundida (ZF).
Se redujo el tamaño de la malla a 0,5mm para determinar la factibilidad del tamaño de los elementos mediante un análisis de convergencia de la temperatura máxima. Para la malla de 1mm se obtuvo una temperatura máxima de 1936,73 ºC y para la malla de 0,5 mm fue de 1941,53 ºC como se observa en la figura 2. Lo anterior representa un error relativo del 0,24 % seleccionando la malla de 1 mm, resultando en 67452 nodos y 54145 elementos.
Se redujo el tamaño de la malla a 0,5 mm para determinar la factibilidad del tamaño de los elementos mediante un análisis de convergencia de la temperatura máxima. Para la malla de 1mm se obtuvo una temperatura máxima de 1936,73 ºC y para la malla de 0,5 mm fue de 1941,53 ºC como se observa en la figura 2. Lo anterior representa un error relativo del 0,24 % seleccionando la malla de 1 mm, resultando en 67452 nodos y 54145 elementos.
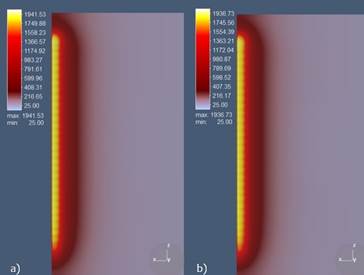
Fig. 2 Convergencia de la malla empelada. a) Elementos de 0,5 mm b) elementos de 1 mm.
Simulación térmica
La simulación de procesos de soldadura suele realizarse en dos momentos. El primero corresponde al análisis térmico donde se obtiene la distribución de temperaturas en los componentes soldados. Según Masubuchi [18] la ecuación de conducción de calor que gobierna el análisis térmico en sólidos está dada por la ecuación (1).
Donde ρ es la densidad kg m3, c el calor específico , λx, λy, λz, la conductividad térmica
en las tres direcciones (para materiales isotrópicos este coeficiente es el mismo en las tres direcciones y q el calor generado por unidad de volumen
.
Las pérdidas de calor al medio circundante por convección se consideran con el empleo de la ecuación (2) correspondiente a la ley de Newton [3].
Donde h es el coeficiente de convección , T 0 la temperatura ambiente (K) y T es la temperatura de la superficie (K). Las pérdidas por radiación están guiadas por la ecuación de Stefan - Boltzman, ecuación (3), [3].
Donde e es el coeficiente de emisividad de la superficie del cuerpo y B la constante de Stefan - Boltzmann. Los valores de los coeficientes asociados a las condiciones de contorno térmicas se detallan en la tabla 2.
Tabla 2 Coeficientes empleados en el análisis térmico para las condiciones de frontera. Fuente: autores.
Modelo de la fuente de calor
El flujo de calor volumétrico empleado es descrito mediante el modelo de Goldak [19]. La geometría del modelo se puede apreciar en la figura 3 donde se observan sus diferentes parámetros geométricos. Este modelo combina dos fuentes elipsoidales, donde la mitad delantera está constituida por el cuadrante de una fuente elipsoidal y la mitad trasera por el cuadrante de otra. El modelo de Goldak es el más empleado dentro de la simulación de procesos de soldadura [19].
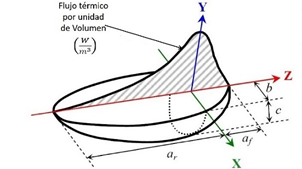
Fig. 3 Distribución gaussiana de doble elipsoide de la fuente de calor, Modelo de Goldak.
La configuración tridimensional del modelo de la fuente de calor empleado para los puntos que se encuentran en la zona delantera y trasera de la fuente viene dada por las ecuaciones 4 y 5 respectivamente [19].
Donde: a, b, c, parámetros dimensionales de la fuente de calor (m), rf y rb son coeficientes adimensionales de proporción de aporte del calor en la parte delantera y trasera respectivamente calculados según la ecuación (7) y (8) [19]. Y que deben cumplir que rf +rf = 2. Q es Aporte térmico efectivo del arco y se define según la ecuación (6) [19, 21, 22, 23].
Donde η = 0,66 es la eficiencia del proceso de acuerdo a lo planteado por Lindgren [21].
Los parámetros geométricos de la fuente de calor que se utilizaron se muestran en la tabla 3.
Tabla 3 Parámetros geométricos de la fuente de calor. Fuente: autores
Parámetros Geométricos | Valores |
---|---|
af | 6,0 mm |
ar | 15,1 mm |
b | 10,0 mm |
d | 2,0 mm |
Parámetro Gaussiano | 1 |
Simulación mecánica
Los campos de temperatura obtenidos en el análisis térmico son empleados como cargas térmicas en el análisis estructural debido a las deformaciones generadas por las dilataciones térmicas. En el caso de análisis no lineales como los que se desarrollan en la simulación de procesos de soldadura, se asume una descomposición de la deformación total () en zonas según se muestran en las ecuaciónes (9) y (10), para el cálculo del esfuerzo.
Donde es la componente elástica,
la deformación plástica,
la deformación debida a la expansión térmica,
la deformación plástica inducida por las transformaciones microestructurales,
la deformación debida a los cambios de volumen asociados a la trasformación,
el esfuerzo objetivo y
el tensor constitutivo elástico.
La deformación térmica se obtiene a través de la relación física de dilatación térmica [19] reflejada en la ecuación (11).
Donde α es el coeficiente de dilatación térmica del material, T la temperatura instantánea y T r la temperatura de referencia donde la deformación térmica es nula (corresponde a la temperatura máxima de soldeo en procesos de enfriamiento) [3].
Por su parte la componente elástica del material se determina mediante la ley de Hooke donde el módulo de Young termo - dependiente. La componente plástica se determina estableciendo el dominio elástico que, de manera general, se define en base al criterio de fluencia de Von Mises como muestran las ecuaciones (12) y (13).
Donde σeq es el esfuerzo equivalente de Von Mises, y σx, σy, σz, Txz los esfuerzos normales y tangenciales que definen el estado tensional triaxial de un punto.
Comportamiento microestructural durante la soldadura
Se tuvo en cuenta el efecto de la microestructura en el proceso debido a que los aceros utilizados poseen una microestructura de tipo ferrítica. Para investigar la evolución microestructural del proceso de soldadura fue empleado el modelo Johnson - Mehl - Avrami - Kolmogorov (JMAK) basado en la teoría de recristalización difundida por Melvin Avrami que es ampliamente utilizada como modelo para analizar los procesos de transformación basados en la nucleación y el crecimiento. Describe, además, la cinética de los procesos de cristalización partiendo de una fase sólida cristalina [24]. El modelo es presentado en las ecuaciones (14) y (15), tomada de Fanfoni y Tomellini [24].
Donde X es el volumen de la fracción de la fase resultante, V f es el volumen transformado, V eq (T) es la cantidad de volumen en equilibrio de la fase en función de la temperatura T, f es un factor de forma, N r es la velocidad de nucleación, G r es la velocidad de crecimiento y t es el tiempo.
Para el caso donde ocurra una saturación en el lugar de nucleación entonces la ecuación (14) adopta la forma de la ecuación (15)
Resultados y Discusión
Esfuerzos residuales
Los esfuerzos residuales longitudinales se originan en sentido paralelo al cordón de soldadura [25] mientras que los transversales lo hacen en la dirección perpendicular. En la figura 4a se muestran los esfuerzos residuales longitudinales y en la figura 4b los transversales en la base (y = 0), centro (y = 2 mm) y superficie (y = 4 mm), según la distancia al centro de soldadura en la sección media (z = 100 mm).
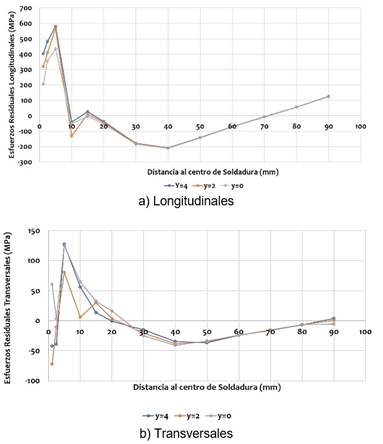
Fig. 4 Comportamiento de los esfuerzos residuales en función de la distancia al centro de soldadura.
En las zonas cercanas a la línea central de soldadura (hasta los 10 mm) se presentan altos valores de esfuerzos residuales longitudinales tractivos debido a la resistencia a la contracción del material cuando inicia la fase de enfriamiento. Luego, disminuyen hasta cero, a medida que aumenta la distancia al centro del cordón de soldadura, tornándose compresivos (15 - 70 mm) en las zonas más alejadas. Pasados los 70 mm comienzan a ser de tracción nuevamente, coincidiendo con lo planteado en la literatura especializada [19, 21] para el comportamiento general de los esfuerzos residuales longitudinales y con los reportados por Sepe et al, [2]. Un comportamiento similar se aprecia en el espesor de la placa.
El máximo valor de esfuerzo longitudinal tractivo se encontró a los 5 mm del centro de soldadura (580,842 MPa) en la superficie, donde la fuente de calor tiene contacto directo con la placa; mientras que el de compresión se observó sobre los 40 mm ( - 200 MPa). Estas diferencias se justifican en la distribución de la temperatura y en el posterior enfriamiento al que es expuesta la placa, los cuales no ocurren simultáneamente en la superficie y el interior de esta.
Se observan diferencias en el comportamiento de los esfuerzos residuales transversales en el centro del cordón. En la superficie (y = 4) resultaron ser de compresión, mientras que en la base comenzaron siendo de tracción. A los 5 mm los esfuerzos en la superficie alcanzan el mayor valor (127,451 MPa) superando a los esfuerzos en el centro y base de la placa (125.129 MPa y 80,2518 MPa, respectivamente).
Los valores de los esfuerzos residuales transversales resultaron se menores que los obtenidos para los esfuerzos longitudinales en cualquier sección del espesor de la placa en la vecindad de los 10 mm de distancia al centro de soldadura. Luego de los 20 mm ambos tipos de esfuerzos disminuyen a cero para luego transformarse en esfuerzos de compresión. Aun en esta situación las magnitudes de los esfuerzos residuales longitudinales continúan siendo mayores que los transversales.
Distorsión
En la Fig 5 se describe el comportamiento de la distorsión total contra diferentes longitudes respecto al centro de soldadura para (y = 4; y = 2, y = 0) en la sección media de la placa (z = 100).
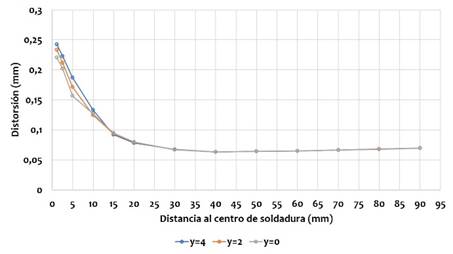
Fig. 5 Comportamiento de distorsión en función de la distancia al centro de soldadura.
Las mayores magnitudes de distorsión se observan en las zonas cercanas al centro de soldadura. Los valores tienden a disminuir con el aumento de la distancia al centro del cordón. Hasta los 5 mm se observan las mayores diferencias en el comportamiento de la distorsión según el espesor de la placa. Esto se debe al efecto de la dilatación y contracción del material durante el proceso de soldadura. Las magnitudes de distorsión en la superficie tienden a ser mayores que para el centro y la base de la placa, además disminuyen en el espesor. A partir de los 5 mm, la distorsión, en los tres puntos del espesor analizados, es similar.
El comportamiento de la distorsión coincide con la relación entre la distorsión y los esfuerzos residuales reportados por la literatura especializada. El comportamiento observado en la distorsión hasta los 5 mm coincide con el aumento de los esfuerzos residuales longitudinales y transversales. A partir de los 20 mm el comportamiento de la distorsión en el espesor parece estar relacionado con la transformación a esfuerzos residuales de compresión, tanto para los transversales como para los longitudinales. La relación entre estos dos fenómenos de soldadura es consistente con lo reportado en la literatura especializada [19].
Las diferencias entre las magnitudes de distorsión en los distintos puntos del espesor analizados coinciden con las observadas en estos puntos para los esfuerzos longitudinales y transversales. Antes de los 20 mm los comportamientos de los fenómenos estudiados no parecen coincidir, sin embargo, cuando la distorsión es similar en los tres puntos del espesor luego de los 20 mm, los esfuerzos en los tres puntos del espesor también parecen coincidir.
Conclusiones
Existe una marcada diferencia entre los esfuerzos residuales longitudinales y los transversales en las zonas cercanas a la línea central de soldadura. Los esfuerzos residuales longitudinales resultaron ser mayores que los esfuerzos residuales transversales. Los esfuerzos residuales disminuyen con el aumento de la distancia hacia la superficie. Similar comportamiento presenta la distorsión total. La magnitud de la distorsión y de los esfuerzos residuales está influenciada por el espesor de la placa.