Introducción
En el diseño de una placa de circuito impreso (Printed Circuit Board, PCB), se deben considerar y cumplir requisitos de diseño térmico [1]. El calor generado por el equipo electrónico hace que la temperatura interna aumente rápidamente y si no se disipa a tiempo, pueden llegar a fallar los dispositivos que lo componen por sobrecalentamiento. Es, por tanto, de vital importancia analizar la conductividad térmica, la transferencia de calor, la radiación y el flujo de calor emitido en los prototipos. En una fuente de alimentación de corriente directa (Direct Current, DC), destinada a un equipo que puede ser utilizado en régimen continuo, el sobrecalentamiento es un problema importante a considerar. Este inconveniente puede agravarse por la tendencia hacia la reducción del tamaño de los equipos electrónicos, lo cual conspira contra la posibilidad de la disipación del calor de los elementos que lo componen. Otra limitante es el material utilizado para la construcción del ensamblaje, usualmente plástico, pues reduce las posibilidades de disipación de calor desde la PCB. Se listan en la literatura variedad de investigaciones [2, 3, 4, 5, 6, 7, 8, 9, 10, 11] que tratan el tema del diseño de las PCB desde diferentes perspectivas tomando en consideración la incidencia de la temperatura en las placas, una temática en que han trabajado los autores de la presente investigación [12, 13, 14, 15].
Entre los aspectos que influyen en la disipación de calor en la PCB según [1, 2] se encuentran: (i) resistencias térmicas, (ii) área / superficie de la lámina de cobre, (iii) espesor de la placa, (iv) número de capas, (v) grosor de los trazos de cobre, (vi) posición de la fuente de calor, (vii) fuentes de calor vecinas, (viii) vías térmicas, (ix) distribución de las conexiones de cobre, (x) espesor de lámina de cobre, (xi) componentes pasivos, entre otras; estos constituyen aspectos esenciales para efectuar un diseño eficiente.
La utilización de una herramienta de diseño electrónico asistido por computadora (Electronic Computer-Aided Design, ECAD) durante el proceso de diseño permite estimar el comportamiento térmico de la PCB y seleccionar la variante adecuada para lograr reducir la emisión de calor en el prototipo antes de su realización práctica. Este proceso comprende la verificación de los esquemas eléctricos, el análisis de la integridad de la señal y la simulación térmica [16, 17]. El propósito fundamental es lograr reducir las densidades de corrientes en las vías conductoras para evitar el calentamiento en las áreas de cobre.
En esta investigación se presenta el análisis de alternativas de diseño de la PCB para una fuente de alimentación con el fin de gestionar las temperaturas disipadas en el circuito y reducir el autocalentamiento y el tamaño de la PCB. El circuito analizado corresponde a una realización típica de fuente de alimentación formada por la combinación de reguladores lineales de voltaje integrados que permiten obtener los voltajes de 3.3V, 1.8V y 1.2V a partir de un voltaje de alimentación de 5V. Para el análisis de los resultados se muestra, a través de varias variantes diseñadas, la incidencia de los aspectos que han de ser considerados en la disipación del calor en la PCB ya sea de manera independiente como combinada. Con el análisis propuesto ha de ser posible obtener un diseño con mayor rendimiento y confiabilidad sustentado en el análisis térmico basado en simulación asistida por computadora del circuito impreso de una fuente de alimentación.
Diseño térmico y métodos de disipación de calor de la pcb.
Las PCB contienen dispositivos electrónicos tanto activos como pasivos, que cumplen funciones específicas y disipan calor durante el funcionamiento. Debido a que, en general, la disminución de la temperatura favorece la extensión de la vida útil de los productos electrónicos, se deben considerar y cumplir requisitos de diseño térmico de la PCB [15, 16, 17, 18]. La gestión térmica en la PCB se centra en dirigir el calor de las áreas calientes a las frías, lo que en última instancia reduce la temperatura y produce una distribución uniforme de la temperatura en toda la placa de circuito impreso. Algunas de las herramientas ECAD existentes contienen herramientas para realización de evaluaciones térmicas de comportamiento de la PCB, entre ellas están Altium Designer, Flotherm y Eagle.
En [19] se proponen métodos para la simulación de la temperatura en la PCB. Demuestra [9] cómo las condiciones de contorno no pueden ignorarse para un diseño térmico adecuado y optimizado de las trazas de las placas de circuito impreso. En [10] se propone y prueba una solución mecánica y térmica utilizando un método para medir las pérdidas por corrientes parásitas en motores implementados en la PCB. En [20] se desarrolla un modelado térmico y la optimización del diseño de vías y terminales de conexión de la PCB mediante simulaciones de dinámica de fluidos computacional y mediciones experimentales. El artículo [3] presenta un diseño termo-mecánico de la PCB utilizando una estructura de refrigeración para lograr una mayor densidad de potencia manteniendo el rendimiento térmico. Por su parte, [21] se centra en el diseño térmico y la optimización del encapsulado tridimensional de componentes magnéticos planares, transformadores e inductores para su aplicación en un convertidor de refuerzo para vehículos eléctricos. En [7] se realiza un análisis más profundo sobre la modelización tridimensional de los diseños de las vías térmicas mediante simulación para determinar la distribución de la temperatura dentro del componente soldado y la PCB. En [22] se investiga sobre los factores del diseño térmico de las PCB para reducir la temperatura de unión de los MOSFET de SiC de montaje superficial en condiciones estacionarias y transitorias de sobrecarga.
Entre las herramientas consideradas para la realización de la simulación térmica de la PCB, Altium Designer [23] se encuentra bien posicionada entre las del tipo profesional, permitiendo un alto grado de complejidad tanto de los esquemas eléctricos como de la PCB, soportando además un elevado número de componentes por diseño. Abarca áreas funcionales principales, incluida la captura esquemática, el diseño de la PCB en 3D, el desarrollo de arreglos de puertas programables en campo, la gestión de liberación/datos y se integra con varios distribuidores de componentes para acceder a los datos del fabricante.
Metodología
El rendimiento práctico de diseño de la PCB depende de una gran cantidad de factores, muchos de los cuales se pueden predecir, en un grado razonable, a través de una gama de herramientas de diseño y análisis. Sin embargo, el desarrollo de un diseño efectivo para la sección de suministro de energía debe estar fundamentado en criterios específicos aplicados a la definición de las áreas de cobre, las rutas conductoras que suministran la energía de corriente directa al circuito, así como a las rutas conductoras de tierra o de retorno común a la fuente de suministro. En esta sección se presentan los pasos para el análisis del suministro de corriente directa y las herramientas a emplear para realizar la simulación térmica de la PCB.
Análisis de corriente directa de la red de la fuente de alimentación
Los diseños digitales modernos que cuentan con circuitos de alta velocidad, múltiples dispositivos, tableros densamente poblados y múltiples rieles de suministro precisan de un análisis detallado del suministro de corriente directa. El análisis de DC de una Red de Suministro de Energía (Power Delivery Network, PDN), o los resultados de su Integridad de Energía de DC (DC Power Integrity, PI-DC,), tienen como objetivo fundamental garantizar que se haya proporcionado el cobre adecuado en la ruta conductora desde las fuentes de voltaje hasta las cargas. Es decir, que los planos, trazos y vías de la placa tengan el tamaño y las características adecuados para cumplir con los requisitos de consumo de energía de los dispositivos de la placa [24].
Análisis con pdn analyzer
El proceso de evaluación del diseño de la red de alimentación en la PCB se realiza en Altium con el PDN Analyzer de forma asequible e intuitiva para los diseñadores de la PCB, independientemente de su nivel de experiencia. PDN Analyzer proporciona información precisa sobre la idoneidad de la distribución de DC de forma sencilla, directa y ágil lo que permite realizar diseños de distribución de energía más eficientes. Los resultados se presentan de manera adecuada para la verificación del diseño final, y además se pueden utilizar en las fases de planificación del proceso de composición de un diseño para delinear un suministro de energía lo más eficiente posible.
La extensión (plugging) PDN Analyzer de Altium se inicia con la configuración del análisis a realizar, que incluye definir la red de alimentación de la fuente, la red de alimentación de la carga y la red de tierra. Se debe especificar cuál es el dispositivo fuente y el dispositivo de carga relativo a un riel de potencia de DC específico de interés. Se establece también el voltaje de la red de la fuente y la corriente máxima. Los valores de la corriente de la red de carga y los niveles de voltajes mínimos relativos a una red de potencia específica también necesitan ser establecidos como parte de la simulación.
Los análisis se desarrollan en un solo riel de potencia a la vez y en ellos se calcula la resistencia de DC en toda la ruta de los objetos de cobre que conecta los pines de tierra, la energía de la fuente y la energía de la carga. La caída de voltaje de DC resultante calculada permite determinar la integridad de la red de alimentación. Los resultados del análisis se muestran gráficamente sobre los objetos de cobre físicos de la red analizada y pueden visualizarse en modo 2D o 3D. Los resultados de la red de tierra, las redes de la alimentación y las capas de la PCB pueden alternarse de forma individual, permitiéndole identificar cualquier sección de la red de distribución de potencia.
Caso de estudio. Fuente de alimentación
La sección de alimentación analizada está compuesta por reguladores de voltaje alimentados por una fuente externa común. La red de distribución de energía está formada por tres reguladores de voltaje de la serie LM1117 con encapsulado SOT-223 conectados en serie y alimentados con una fuente DC de 5V. En la Figura 1 (a) se observa el diagrama esquemático de la fuente con todos los componentes del circuito. A las salidas de los reguladores de voltaje se ha conectado resistores de carga (R1, R2 y R4 de 4.7kΩ en cada caso) con valores que garantizan el consumo de corriente previsto por diseño. La PCB tiene que cumplir con las especificaciones eléctricas, de voltaje y temperatura establecidas por diseño. La Figura 1 (b) indica una posible realización de las interconexiones en la PCB que se corresponden con el circuito del diagrama esquemático.
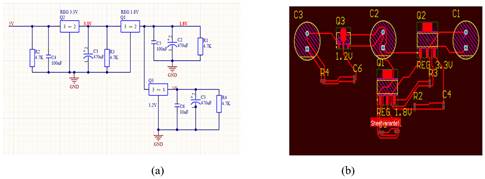
Figura 1 (a) Diagrama esquemático implementado en el diseño de fuente implementado y (b) PCB obtenida para el diseño de fuente.
La extensión PDN Analyzer permite emular la red de distribución de potencia que incluye las rutas conductoras de cobre de alimentación y tierra. La aplicación extrae automáticamente toda la información física y eléctrica (lista de redes, dispositivos y formas de capas, etc.) del diseño de la PCB actualmente activo y obtiene los datos necesarios para realizar la simulación PI-DC.
Simulación térmica
Una vez establecidas las opciones de visualización de voltajes y corrientes en ambas capas de la tarjeta los resultados de la simulación pueden observarse gráficamente en el editor de la PCB de Altium Designer. En la Figura 2 (a) se muestra mediante transiciones de color los valores porcentuales de voltaje a través de las rutas de la red de potencia. El nivel mínimo, 0%, es el azul y el nivel máximo el rojo, 100%. El análisis de corriente se realiza mediante el estudio de la densidad de corriente y se representan las variaciones de esta mediante escalas de colores en las rutas de cobre de la placa. El 100% (rojo) indica la densidad de corriente máxima calculada en el diseño de la ruta de red, y el 0% (azul) es el mínimo (0 A/mm2), Figura 2 (b).
Resultados y discusión
El análisis térmico de la PCB tiene en consideración la resistencia térmica de la PCB. Este parámetro está determinado por las propiedades del material del sustrato y la disposición de los elementos de cobre en su placa e incide en la transferencia de calor entre las regiones de la PCB. En los diseños de la PCB de una sola capa de cobre el calor no se disipa eficientemente por conducción térmica vertical, porque la capa de aire en la superficie inferior tiene una pequeña conductividad térmica, por lo cual la conducción térmica horizontal tiene prioridad. Por otro lado, la resistencia térmica tiende a ser menor cuando la superficie de la placa o lámina de cobre es mayor y cuando existe un mayor número de capas de cobre. La adición de áreas de cobre facilita la transferencia de calor hacia el entorno y, aunque existen numerosos elementos a considerar en un equipo electrónico real, es importante colocar intencionalmente la fuente de calor en el centro del área para asegurar una radiación uniforme a su alrededor. Otro factor a considerar es el uso de vías térmicas en la PCB, pues se reduce la resistencia térmica al aumentar su número. Nótese que cada dispositivo insertado en la PCB experimenta interferencia térmica con sus vecinos, lo que aumenta la temperatura ambiente a su alrededor, cuanto más corta es la distancia entre las fuentes de calor, más fuerte es la influencia que experimentan. Las conexiones de cobre en la PCB a través de las que circula corriente deben tener un ancho y grosor mínimo que está en función de la capacidad de corriente requerida y la tolerancia máxima permisible del aumento de la temperatura.
El análisis de la red de alimentación implementada se basó en la evaluación de la influencia de los aspectos:
Área / superficie de la lámina de cobre
Grosor de los trazos de cobre
Posición de la fuente de calor
Fuentes de calor vecinas
Vías térmicas
Distribución de las conexiones de cobre.
Otros aspectos que influyen en el comportamiento térmico, como el espesor de la placa, el número de capas y el espesor de lámina de cobre, se mantuvieron invariantes por depender del diseño o de las opciones ofrecidas por el fabricante de la PCB. El estudio de comportamiento se realizó a partir de la implementación de las variantes descritas en la Tabla 1.
Tabla 1 Variantes para el análisis del comportamiento térmico.
Variante | Descripción | Aspectos considerados | |||||
---|---|---|---|---|---|---|---|
1 | 2 | 3 | 4 | 5 | 6 | ||
1 | Fuentes colocadas en cascada; ubicación de las componentes en una sola cara | X | |||||
2 | Fuentes colocadas en paralelo; ubicación de las componentes en una sola cara | X | X | ||||
3 | Fuentes colocadas en paralelo; ubicación de las componentes en ambas caras | X | X | X | |||
4 | Fuentes colocadas en paralelo; engrosamiento de venas e inclusión de vías térmicas | X | X | X | X | X | |
5 | Fuentes colocadas en paralelo; inclusión de área de disipación | X | X | X | X | X | X |
Variante 1. Fuentes colocadas en cascada
La primera versión se basa en una fuente externa de 5V empleada para la alimentación de los reguladores de voltaje, los cuales están conectados en cascada como se muestra en la Figura 1. En el diseño de la PCB todos los componentes fueron ubicados en la capa superior (Top Layer), las venas utilizadas tienen el ancho predeterminado por el software 0.4 mm. A continuación, se muestra en la Figura 3 (a) el comportamiento del voltaje en la capa superior, vista en 3D. Se visualiza que el máximo voltaje es de 5V y el mínimo voltaje es de 1.23V. Se evidencia cómo, a medida que el voltaje pasa a través de los reguladores, este tiende a disminuir (se aleja del color rojo en la escala). Para el análisis de corriente se estableció la escala automática que brinda la simulación: de 0 a 75.9 A/m m 2 . Esta escala será empleada en todas las versiones para observar la evolución de la red a medida que se le hagan transformaciones. La Figura 3 muestra que la mayor densidad de corriente se encuentra en la salida del regulador de voltaje de 3.3V pues al estar conectado en cascada con los demás reguladores tiene que manejar toda la carga.
Variante 2. Fuentes colocadas en paralelo
Debido a que en la variante 1 el regulador Q1 de 3.3 V mostraba un calentamiento ocasionado por el flujo de corriente que tenía que manejar, se decidió utilizar la alimentación en paralelo de los reguladores de voltaje, tal como se muestra en el diagrama en bloques simplificado de la Figura 4 desde el visor de Altium, PDN Analyzer.
En la Figura 5 (a) se muestra el comportamiento del voltaje en la PCB. Los voltajes más pequeños se encuentran a la salida de los reguladores (pines de VOUT), mientras que los más altos están a la entrada de cada regulador; por lo que todos dependerán del suministro de la fuente externa de 5V para su buen funcionamiento. Nótese que Q1 representa al regulador con más voltaje a su salida (3.3V), le sigue Q2 con un voltaje de 1.8V y Q3 con un voltaje 1.2V. La Figura 5 (b) muestra la densidad de corriente en la PCB en la nueva configuración. Se evidencia que la mayor densidad de corriente está presente en el conductor de alimentación de 5V. Se constata que los reguladores muestran una gran mejora con respecto a la versión anterior, lográndose una disminución de 62.3% para la densidad de corriente en Q1 y una disminución del 72.5% para Q2 con respecto a la versión anterior.
Variante 3. Posicionamiento de elementos en ambas caras
En esta versión se realizó una modificación a la estructura de la PCB de la variante 2. Se usaron las dos caras de la placa para el montaje de los componentes: la cara inferior para los reguladores de voltaje y la superior para los demás componentes. Esta modificación tuvo como objetivo reducir el calentamiento a una sola cara y mantener la densidad de corriente dentro de límites permisibles en un área determinada. Al ubicar los reguladores en esta posición, el calor generado se disipa hacia arriba. Nótese que cada dispositivo experimenta interferencia térmica, lo que aumenta la temperatura ambiente alrededor de los dispositivos. La Figura 6 (a) muestra la caída de voltaje en la PCB. En el comportamiento de la densidad de corriente, observado en la Figura 6 (b), no se evidencia un gran cambio. Los reguladores de voltaje mantienen una densidad de corriente muy similar a la versión anterior; solo Q3 presentó un aumento de un 4 %. En dicha Figura se puede ver que las venas finas tienden a estar más calientes que las vías conectadas a ellas. Esto puede ser atribuido a las diferencias en la conductividad térmica entre la vena expuesta al aire, y la vía; en efecto, el calor es disipado más rápidamente en la vía que en las venas finas. Este análisis demuestra que el empleo de vías para la comunicación entre ambas caras genera calor y pérdidas de corriente sino se realiza correctamente.
Atendiendo a las consideraciones de [25] se puede pensar en usar vías ciegas o enterradas en lugar de un orificio pasante como alternativas a valorar. Las vías ciegas y enterradas pueden realmente ayudar a reducir la EMI en la PCB. El efecto de la inclusión de vías en este estudio de caso se manifiesta en que los talones en las vías de hueco pasante actúan como líneas de transmisión abiertas y reflejarán cualquier señal transmitida a través de la vía nuevamente al circuito; la solución simple para la fabricación para este problema podría ser quitar el talón. Las vías ciegas y enterradas no tienen talones, por lo que no provocarán tanta reflexión. No obstante, simplemente porque no se pueda ver una vía enterrada, o el final de una vía ciega, no significa que no puedan causar problemas de EMI, la inclusión de cualquier variante de diseño resulta factible a realizar por el desarrollador en el software de diseño. Es importante diseñar teniendo en cuenta la compatibilidad electromagnética, el costo y la durabilidad a largo plazo.
Variante 4. Engrosamiento de las venas e inclusión de vías térmicas
En esta versión se añadieron modificaciones para incidir en la resistencia térmica y lograr una mayor reducción de la temperatura en las áreas de cobre. La primera modificación se realizó a las venas del circuito: estas vienen predeterminadas con un ancho de 0.4 mm y se aumentaron a 0.8 mm para reducir la cantidad de energía perdida por calor. En el diseño se verificó la no existencia de problemas relativos al estrechamiento antes de la conexión a un pad, pues se sabe que esto contribuye al aumento de la resistencia, el nivel de calentamiento y los daños potenciales en la placa. En [26, 27] se encuentran a disposición de los usuarios una calculadora de ancho de pistas que utiliza como datos la corriente que debe circular por la pista, el espesor de cobre de la tarjeta PCB (Trace thickness) y la temperatura máxima que puede tolerar la pista.
La segunda modificación consiste en la adición de vías térmicas. Una vía térmica es un buen conductor de calor que se extiende entre la parte superior e inferior de la placa. El calor se transfiere a la vía mediante una conducción simple y la vía térmica permite que el calor se aleje de los componentes electrónicos críticos. Se realizó un aumento del diámetro a 1.5 mm para evitar que el calor se transfiera a los componentes eléctricos críticos de la placa. La Figura 7 (a) muestra los valores de voltajes en la PCB una vez realizadas las modificaciones. La red de 3.3V a la salida del regulador Q1, conectada con los elementos C1 y R2 es representada en amarillo. La salida del regulador Q2 de 1.8V, conectada a los elementos C2 y R3 está representada en verde y por último la salida del regulador Q3 de 1.2V conectada a los elementos C3, R4 está representada en azul. En la Figura 8 (b) se muestra distribución de la densidad de corriente. En esta variante 4, se evidencia cómo incide en el enfriamiento de las venas la distancia hasta el punto de emisión de calor. A la salida de Q1 la disminución fue de 32.2 %, a la salida de Q2 la disminución fue de 14.2 % y la salida de Q3 la disminución fue de 56.7%.
Variante 5. Inclusión de área de disipación
Después de realizar las modificaciones anteriores se logra que los reguladores operen a temperaturas comprendidas dentro del rango normal de funcionamiento. Para mejorar el comportamiento del circuito se añadió en esta variante un área de disipación para facilitar la extracción del calor generado por los reguladores. La adición de vías térmicas a las áreas de cobre añadidas favorece también la disipación de calor al disminuir la resistencia térmica. Cuanto mayor sea el número de vías, menor será la resistencia térmica. Aunque se pudo observar que el efecto es notable con la adición de una sola vía, los resultados mostrados han sido con la inclusión de 3 vías. La Figura 8 (a) muestra el comportamiento del voltaje una vez creadas las áreas de disipación.
En la Figura 8 (b) se muestra cómo este diseño presenta una reducción de la densidad de corriente. Los reguladores de voltaje presentan en su encapsulado un total de 4 pines, el pin 4 en el caso de los reguladores de 3.3V y 1.8V es la salida y en el 1.2V es el común. Este cuarto pin, para todos los reguladores, es el encargado de disipar el calor por lo que tiene que estar conectado al área de disipación ubicada en las dos caras de la PCB.
Análisis de variantes
En la Figura 9 se muestra el comportamiento de la densidad de corriente en la PCB a medida que se incorporaron modificaciones para lograr un mejor diseño. Para cada variante analizada se indica el valor de máxima densidad de corriente en el punto identificado por el software como más “contribuyente” a la potencia radiada. Nótese que se logra que la densidad de corriente disminuya para todas las salidas entregadas por los reguladores. En la variante 5 se logra una disminución de las densidades de corriente en las salidas de los reguladores de 3.3V, 1.8V y 1,2V de alrededor del 80% en los dos primeros y de 55% en el último, con respecto a la primera variante.
La Figura 10 muestra los datos que se obtienen de la simulación de PDN Analyzer, correspondientes a las vías utilizadas en el diseño final. Se observan los comportamientos de los voltajes en los extremos de las vías en la cara superior (Top Layer) e inferior (Bottom Layer) de la PCB. La columna Net indica la red a la que está conectada la vía, Layer 1 y Layer 2 corresponden a las capas de la PCB que interconecta la vía ubicada en la posición indicada por las coordenadas X y Y. Las columnas Voltage1 y Voltage2 contienen los voltajes en los extremos de cada vía en la capa correspondiente. La corriente que circula por la vía y la densidad de corriente se muestran en las columnas Current y Current Density. Los valores de densidad de corriente (A/m m 2 ) son los más satisfactorios obtenidos y corresponden a la variante 5.
Los análisis para todos los casos presentados fueron realizados en condiciones estáticas de operación de los dispositivos conectados a las fuentes. En el caso de alimentación de dispositivos con condiciones dinámicas de consumo, en que debe satisfacerse un rango de valores, los análisis deben extenderse para cubrir estas situaciones y garantizar la integridad energética del diseño. Es necesario controlar el consumo de la PDN y cerciorarse desde el diseño de que le son suministrados los voltajes especificados dentro de unos límites de tolerancia aceptables (normalmente entre ± 2 y 5%), a través de los terminales de los voltajes de alimentación y de tierra de los distintos elementos presentes en la PCB. Si se garantiza la operación ante corriente continua bajo las condiciones anteriores las demandas de corriente dinámica de los dispositivos serán satisfechas en todo momento y en toda su gama de frecuencias funcionales.
Conclusiones
El uso de herramientas de diseño electrónico automatizado para le estimación del comportamiento térmico del circuito impreso de la fuente de alimentación permite evitar los problemas relacionados con el sobrecalentamiento en el diseño de equipos electrónicos destinados a un régimen continuo de operación. La generación de un mapa término mediante el uso de la extensión PDN Analyzer de la plataforma Altium Designer ayudó a identificar las zonas calientes en las variantes analizadas y a estimar las posibilidades de disipación de energía de los componentes. A partir del análisis de los resultados del caso de estudio de la fuente de alimentación y sus variantes, cuantificados mediante valores de densidades de corriente, se determinó la variante 5 como la más favorable en términos de comportamiento térmico. Se logró que las densidades de corriente en todos los reguladores descendieran con respecto a la variante inicial considerada. El procedimiento seguido reafirma la necesidad de realizar las simulaciones que permitan garantizar, además del comportamiento eléctrico adecuado de los prototipos de las fuentes de alimentación que utilizan reguladores integrados, la estabilidad de su funcionamiento electrónico.