Introducción
Los electrodos con doble revestimiento (dos capas) son conocidos desde hace mucho tiempo, y su aplicación fundamental ha estado dirigida, a incrementar la estabilidad del arco en la soldadura con corriente alterna en electrodos de revestimiento básico. En la actualidad se reportan varios trabajos relacionados con esta temática. En 2011 Marchenko, et al, [1] realizaron un estudio del estado del arte de la temática, donde se constata la importancia y la gran aplicación que tienen los revestimientos de doble capa en la fabricación de electrodos básicos, con el objetivo de mejorar las propiedades operativas y metalúrgicas. Sin embargo, los autores no hacen referencia a las posibilidades de estos revestimientos para introducir elementos de aleación que modifiquen la composición química y por tanto las propiedades mecánicas del metal depositado, aspecto que se desea lograr en este trabajo.
De igual modo, Cruz, et al, [2] evaluaron el comportamiento de los electrodos revestidos E7018, con el objetivo de mejorar su desempeño. En la evaluación se priorizó el contenido de los componentes en el revestimiento periférico aplicado. Como resultado se obtuvo que la composición del revestimiento de mejor desempeño condiciona cambios favorables frente al electrodo sin revestimiento periférico. Este resultado justifica la propuesta de aplicar un revestimiento periférico a un electrodo de soldadura convencional, a partir de utilizar una cinta con revestimiento, en el cual se introducirán los elementos de aleación para mejorar las propiedades del metal depositado.
Mas reciente, en 2021, González, et al, [3] evaluaron la influencia de la posición relativa de la carga de aleación en la estructura del recubrimiento de electrodos de rutilo para recargue, sobre el comportamiento operacional (la estabilidad del arco) del mismo. Demostraron que la posición de la carga de aleación en el revestimiento, ejerce una marcada influencia sobre el comportamiento operativo del electrodo. Cuando la carga de aleación se encuentra situada en la parte interna del revestimiento, o sea en contacto con el núcleo, el electrodo presenta la mejor estabilidad del arco. En este caso la carga de aleación estará en la periferia del revestimiento del electrodo y al interior en contacto con el núcleo solo estará el revestimiento de rutilo, que se caracteriza por excelentes propiedades operativas de soldadura, por tanto no deben ocurrir afectaciones en el funcionamiento estable del electrodo cuando se aplique el revestimiento periférico.
Los electrodos con revestimiento de doble capa son ampliamente utilizados en la industria en muchos países. Empresas de Suiza (Oerlikon), Suecia (ESAB), Japón (Kobe Steel), Austria (Boehler), Alemania (Thyssen Draht, UTP), Países Bajos (Philips), EE. UU. (Lincoln Electric) producen estos electrodos [1]. El objetivo es combinar las buenas propiedades operativas del revestimiento de rutilo con las elevadas propiedades mecánicas que se obtienen con los revestimientos básicos, por ejemplo, los electrodos OK 53.16 y LINCOLN 7016DR.
Los revestimientos periféricos constituyen una alternativa para modificar las propiedades del metal depositado por electrodos convencionales empleados para la soldadura de aceros al carbono. La aplicación de los revestimientos periféricos al electrodo se puede realizar por inmersión o prensado, en ambos casos se requiere de equipamiento especializado y de personal entrenado en la actividad. Por tanto, la utilización de una cinta revestida obtenida de forma independiente al electrodo, constituye una solución alentadora para obtener recargues de soldadura.
En los electrodos de recargue se emplean fundamentalmente revestimientos básicos y en menor medida de rutilo. Sin embargo, los revestimientos de rutilo son de bajo costo, garantizan el funcionamiento estable del arco, con un fácil encendido y reencendido, tanto con corriente alterna o directa, casi no desprenden gases y vapores nocivos durante la soldadura y los cordones presentan escasas salpicaduras, con buena presencia y uniformidad, siendo poco sensibles a la humedad [4]. Por tanto son fácilmente aplicables a las condiciones de cualquier taller. Por estas razones se seleccionó un electrodo AWS E6013 para el trabajo.
A partir de las consideraciones anteriormente señaladas, el presente trabajo tuvo como objetivo evaluar el comportamiento operativo y de fusión de electrodos AWS E6013, bajo un revestimiento periférico aplicado con una cinta revestida con variaciones en la composición, el cual puede ser aplicado para el recargue de piezas expuestas a desgaste adhesivo.
Métodos y Materiales
Para realizar el trabajo se consideró, el empleo de materias primas nacionales, tales como, la cromita refractaria, el grafito proveniente de desechos de electrodos de hornos de fundición por arco eléctrico y los electrodos E6013, además, para el estudio del revestimiento periférico se tomaron dos espesores de revestimiento en la cinta (0,3 mm y 0,7 mm), para evaluar la influencia en el aporte de carbono y cromo al metal depositado, así como la dureza en el cordón de soldadura.
Características del electrodo AWS E6013
El electrodo E6013 utilizado es de producción nacional en la fábrica de Nuevitas en Camagüey, Cuba. La composición química del metal depositado según norma AWS A5.1-2010 es la siguiente: C 0,11 %; Mn 0,47 %; Si 0,24 %; P 0,015 %; S 0,018 %. El diámetro es de 4 mm y la longitud de 350 mm. El factor de revestimiento es de 1,45.
Características de la cinta para el revestimiento periférico
Las cintas revestidas deben ser flexibles de forma que se puedan enrollar sobre el electrodo y no se produzca el desprendimiento del revestimiento. En esta propiedad inciden variables, tales como, el tipo de material de la cinta, el espesor del revestimiento y el aglutinante empleado en la mezcla. En la fabricación de las cintas se utilizó un tejido de lienzo con 100 % de algodón, de 0,3 mm de espesor, con un ancho de 15 mm y una longitud de 450 mm. La textura del tejido facilita la adherencia del revestimiento, además de ser muy resistente. El algodón está compuesto por celulosa en su totalidad, por tanto durante la combustión del revestimiento por el arco eléctrico se generan gases reductores.
Diseño de la composición del revestimiento de las cintas
El aglutinante ejerce dos funciones básicas, aglutinar los componentes de la mezcla y actuar como pegamento del revestimiento en la cinta. Con este objetivo se seleccionó el acetato de polivinilo (cola blanca) de importación, debido a que posee un buen poder adhesivo con resistencia a la fuerza de tracción y una estructura de alta viscosidad.
Para modificar las propiedades del metal depositado por los electrodos E6013, el revestimiento periférico debe poseer una composición que permita la transferencia de elementos de aleación hacia el baño metálico durante la fusión del electrodo. En este caso se busca incrementar la resistencia al desgaste adhesivo, mediante el incremento de la dureza y la modificación de la microestructura del metal depositado.
A partir del estudio de la bibliografía [5, 6, 7] y para las condiciones de trabajo del depósito de soldadura se decidió utilizar en la composición del revestimiento periférico un componente que aporte Cr y otro que aporte C y así facilitar la obtención de componentes estructurales de alta dureza. Para aportar el C se seleccionó el grafito y para el Cr se partió del mineral, o sea la cromita refractaria, disponible en el yacimiento Victoria I de la provincia de Camagüey [8, 9]. La cromita posee la siguiente composición: Cr2O3 = 31,07 %, Al2O3 = 27,8 %, MgO = 18,49 %, SiO2 = 5,5 %, FeO = 14,77 %, CaO = 0,8 % [10]
Para el trabajo de investigación se seleccionó un diseño de mezcla de red simple. Para el cual se definieron dos variables independientes (X1: cromita, X2: grafito). Se asumió como variables dependientes: el contenido de carbono (Y1), el contenido de cromo (Y2) y la dureza en el metal depositado (Y3). Se asignaron dos niveles a cada variable independiente. Para X1 (Cromita): 60 y 80 %, para X2 (Grafito): 20 y 40 %.
Para la obtención de la matriz experimental se utilizó el software Statgraphics Centurion XV versión 15.2.14, definiendo los experimentos según se muestra en la tabla 1. Se creó un diseño simple reticular el cual permitió estudiar los efectos de dos componentes en cinco corridas.
Tabla 1 Matriz experimental. Fuente: autores
Experimentos | X1 (%) | X2 (%) | Σ X1, X2 |
---|---|---|---|
1 | 65 | 35 | 100 |
2 | 70 | 30 | 100 |
3 | 75 | 25 | 100 |
4 | 60 | 40 | 100 |
5 | 80 | 20 | 100 |
Cada experimento se replicó una vez para un total de 10 puntos experimentales. La codificación de las cintas se muestra en la tabla 2.
Tabla 2 Codificación de las cintas para la experimentación. Fuente: autores
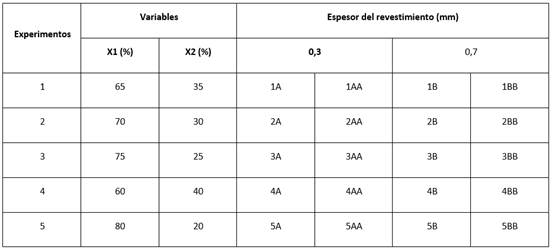
Observación: A: para identificar las cintas con 0,3 mm de espesor de revestimiento. AA es la réplica de la cinta. El número que la antecede indica la composición del revestimiento. B: para identificar las cintas con 0,7 mm de espesor de revestimiento. BB es la réplica de la cinta.
Obtención del revestimiento en la cinta
Los componentes del revestimiento periférico se molieron por separado en un molino de bolas de laboratorio, marca Yantra modelo B07NQMXHQP con capacidad de 2 kg, hasta obtener una fracción de granulometría: en el grafito de +0,1 - 0,04 mm y en la cromita de +0,2 - 0,1 mm. La arena de cromita, antes de la molienda, fue lavada para eliminar suciedades y secada a 120 oC en una estufa.
Los componentes se dosificaron y pesaron en una balanza técnica OKLAUS modelo GAI2200N del año 2018 de procedencia alemana, con una precisión de 0,01 g. Las mezclas secas se homogenizaron en una mezcladora de laboratorio por 30 min. La mezcla para el revestimiento se obtuvo mediante mezclado de forma manual del aglutinante diluido en agua y la masa seca. La aplicación del revestimiento a la cinta se realizó de forma manual por un lado con una espátula, en el dispositivo que se muestra en la figura 1, el cual garantiza un espesor uniforme y el cubrimiento de toda la superficie en el ancho de la cinta.
Las cintas con el recubrimiento fueron colocadas sobre una superficie plana para el secado al aire por 24 h. Posteriormente fueron secadas en una estufa universal de marca Memmert modelo UN30 a una temperatura de 80 oC durante 1 h. Las cintas fueron inspeccionadas y medidas para comprobar el espesor del revestimiento, figura 2. La medición se realizó a intervalos de 100 mm con un Pie de Rey de 0 a 150 mm con 0,05 mm de apreciación de marca Mitutoyo. Con el objetivo de comprobar el aporte del material en el revestimiento las cintas fueron pesadas antes y después de ser revestidas en una balanza técnica de marca Gibertini modelo CEN 2000 del 2019 de procedencia italiana, con una precisión de 0,01 g.
Aplicación del revestimiento periférico al electrodo E6013
La cinta revestida se situó en la superficie del electrodo E6013 siguiendo la siguiente secuencia: primero se aplicó con un pincel una película de silicato de sodio sobre la superficie del electrodo y en la cinta por el lado del revestimiento. Trascurrido 2 min se procedió a pegar la cinta en el electrodo, para lo cual la cinta se fue enrollando en forma de espiral por el lado del revestimiento en la superficie del electrodo. Al mismo tiempo se tiraba de ella para lograr una mejor adherencia. Este proceso fue de forma manual, obteniendo un electrodo con cada cinta, figura 3. Los electrodos con la cinta pegada se dejaron secar al aire por 2 h. Posteriormente se secaron en la estufa universal de marca Memmert modelo UN30, a una temperatura de 60 oC durante 30 min.
Evaluación del desempeño operativo de los electrodos en estudio
Los electrodos se sometieron a pruebas de soldadura con la técnica de avance sin oscilación, empleando el siguiente régimen de soldadura: intensidad de la corriente: 140 ± 5 A, tipo de corriente: directa con polaridad normal (electrodo negativo), velocidad de soldadura: 18 cm/min. La soldadura se realizó por un soldador calificado utilizando como fuente de alimentación un inversor Genesis 1800 RC de 2018 de procedencia italiana. El metal base empleado fue un acero AISI 1010 con las siguientes dimensiones: 100 x 50 x 10 mm. Los cordones se depositaron en una longitud de ≈ 90 mm y se dejaron enfriar al aire.
Basado en trabajos previos de los autores [11], se utilizó el criterio de expertos para evaluar cualitativamente la operatividad del electrodo. De acuerdo a la metodología, en la tabla 3 se muestran las propiedades estudiadas para el consumible y la evaluación que obtendría en cada caso, según su comportamiento.
Tabla 3 Criterios para definir la operatividad del electrodo. Fuente: [11]
Propiedades | Observación | Evaluación |
---|---|---|
Desprendimiento de la escoria | Se desprende una vez terminada la soldadura | Excelente |
Se desprende fácilmente con golpes ligeros con la piqueta | Buena | |
Se desprende con golpes reiterados con la piqueta | Regular | |
La escoria queda atrapada al reiterar los golpes. | Mala | |
Sanidad del cordón | No se aprecian defectos | Excelente |
Pocos defectos pequeños | Buena | |
Defectos grandes aislados o en colonias | Regular | |
Muchos defectos en todo el cordón. | Mala | |
Aspecto del cordón | El cordón es uniforme en ancho y altura | Excelente |
El ancho es uniforme y la altura presenta irregularidad | Buena | |
El ancho y la altura son irregulares | Regular | |
Cordón muy irregular y discontinuo | Mala | |
Estabilidad del arco | El arco arde estable y funde parejo el revestimiento | Excelente |
El arco es estable pero se producen salpicaduras | Buena | |
El arco arde con dificultad y el electrodo tiende a soldarse | Regular | |
El arco es muy inestable y se apaga a ratos, el electrodo funde mal | Mala |
Determinación de la composición química y la dureza del metal depositado
Para determinar la composición química de los depósitos de soldadura sin dilución se hicieron soldaduras superficiales con cada electrodo sobre chapas de acero AISI 1010 hasta obtener un recargue con un espesor mayor de 16 mm de acuerdo con la norma AWS A5.13:2000. La operación se llevó a cabo depositando cordones rectos sin oscilación, utilizando un inversor Genesis 1800 RC. Se empleó polaridad normal con una intensidad de corriente de 140 ± 5 A. Una vez obtenido el cupón de prueba, se realizó un amolado, pulido y limpieza de las superficies para determinar la composición química por el método de espectrometría de emisión óptica con un espectrómetro de emisión óptica de marca SPECTRO, modelo SpectromaXx de 2017 de procedencia alemana.
Para determinar la dureza del recargue se depositaron cordones de soldadura de ≈ 60 mm de longitud en probetas de acero AISI 1010 de 100 x 50 x 10 mm. Se obtuvieron depósitos de una y dos capas, el ensayo de dureza se realizó siguiendo las indicaciones de la norma ISO 6508 con un durómetro Rockwell modelo 200 HRS-150 de procedencia china de 2018, utilizando la escala C. Las mediciones se realizaron en cada capa siguiendo la siguiente secuencia: soldadura, limpieza de la escoria, enfriamiento al aire y esmerilado de la superficie.
Resultados y Discusión
Influencia del revestimiento periférico en el desempeño operativo del electrodo E6013
La evaluación de las características operativas del electrodo se realizó de forma cualitativa mediante el criterio de expertos de acuerdo a lo indicado en la tabla 3. Uno de los factores fundamentales en la soldadura manual por arco eléctrico es la estabilidad del arco.
Los resultados experimentales, tabla 4, muestran que estos electrodos poseen excelente estabilidad en el arco durante su fusión. Mientras el desprendimiento de la escoria se evaluó de bien en todos los cordones de soldadura. De igual modo, la sanidad del cordón resultó excelente en todas las soldaduras. También, el aspecto del cordón se evaluó de bien en el 100 % de los casos, figura 4. Estos resultados están en correspondencia con el comportamiento operativo de los electrodos con revestimiento de rutilo [4], lo que demuestra que el revestimiento periférico constituido por la cinta no provoca afectaciones operativas en el electrodo E6013. Además, la introducción de grafito en el revestimiento de la cinta contribuye favorablemente en la estabilidad del arco.
Tabla 4 Desempeño operativo del electrodo E6013 con revestimiento periférico. Fuente: autores
Electrodos | Desprendimiento de la escoria | Sanidad del cordón | Aspecto del cordón | Estabilidad del arco |
---|---|---|---|---|
ERP-1A | Bien | Excelente | Bien | Excelente |
ERP-1B | Bien | Excelente | Bien | Excelente |
ERP-2A | Bien | Excelente | Bien | Excelente |
ERP-2B | Bien | Excelente | Bien | Excelente |
ERP-3A | Bien | Excelente | Bien | Excelente |
ERP-3B | Bien | Excelente | Bien | Excelente |
ERP-4A | Bien | Excelente | Bien | Excelente |
ERP-4B | Bien | Excelente | Bien | Excelente |
ERP-5A | Bien | Excelente | Bien | Excelente |
ERP-5B | Bien | Excelente | Bien | Excelente |
ERP- Electrodo con revestimiento periférico.
Como rasgo particular de estos electrodos se pudo constatar, que la cinta arde de conjunto con el revestimiento del electrodo produciendo una ligera llama que al interrumpir el arco se extingue.
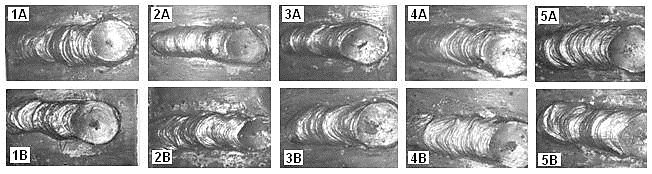
Fig. 4 Cordones de soldadura depositados con los electrodos E6013 con revestimiento periférico tipo cinta revestida.
Influencia de la composición del revestimiento periférico en la composición química del metal depositado
La masa del revestimiento aplicado en cada cinta es la diferencia entre la masa inicial de la cinta y la masa final de esta con el revestimiento aplicado. Para el revestimiento de espesor 0,3 mm la masa promedio fue de 1,96 g, mientras para el revestimiento de 0,7 mm de espesor fue de 3,56 g.
Mediante un análisis de regresión múltiple, se determinó la dependencia de los diferentes elementos de aleación del metal depositado respecto a la composición de la mezcla aditiva del revestimiento, demostrándose que las variables dependientes, derivadas de la composición química: % C, % Cr, tienen una relación estadísticamente significativa con las variables independientes; % cromita, % grafito.
Según la norma AISI/SAE el acero 1010 en su composición química posee 0,08 - 0,13 % de C y 0,3 - 0,6 % de Mn. Mientras el metal depositado por el electrodo E6013 contiene 0,11 % de C, 0,4 % de Mn y 0,22 % de Si de acuerdo a la especificación AWS A5.1. Por tanto, el metal depositado por los electrodos en estudio con revestimiento periférico, tabla 5, difiere considerablemente en cuanto a composición y cuantía de los elementos químicos. El C es superior, variando desde 0,193 a 0,289 % para un espesor de revestimiento de 0,3 mm y de 0,481 a 0,567 % para el espesor de 0,7 mm. Mientras el Cr aparece como elemento de aleación en cuantías desde 0,181 a 0,292 % para un espesor de revestimiento de 0,3 mm y de 0,323 a 0,513 % para el espesor de 0,7 mm.
La composición química del metal depositado está relacionada con la composición del revestimiento periférico, tabla 2, en el cual se introdujo cromita y grafito. Además, el espesor y la masa del revestimiento influyen sobre la cuantía de los elementos, aspecto corroborado en la tabla 5, donde se aprecia que las aleaciones obtenidas con cintas de 0,3 mm de espesor poseen menor cuantía en los elementos componentes en comparación con las obtenidas con cintas de 0,7 mm de espesor.
Según los modelos A y B el grafito tiene una influencia favorable sobre la cantidad de C en el cordón de soldadura, y puede estar en solución sólida con el Fe o formando carburos de Fe o de Cr. Además, ayuda a la transferencia del Cr debido a que el C reduce al Cr2O3 (ecuación 1) y propicia la presencia de este elemento en el cordón de soldadura en solución sólida o formando carburos [9]. En este caso, resulta más probable desde el punto de vista termodinámico la formación del carburo del tipo Cr7C3, a partir de la reducción carbotérmica, al requerir una temperatura más baja para su formación, 1115 oC.
Tabla 5 Composición química del metal depositado sin dilución, en %. Fuente: autores
Probetas | Espesor del revestimiento (mm) | Fe | C | Si | Mn | Cr |
---|---|---|---|---|---|---|
1A | 0,3 | Balance | 0,289 | 0,048 | 0,072 | 0,196 |
2A | 0,3 | Balance | 0,262 | 0,056 | 0,078 | 0,216 |
3A | 0,3 | Balance | 0,236 | 0,053 | 0,065 | 0,252 |
4A | 0,3 | Balance | 0,302 | 0,045 | 0,090 | 0,181 |
5A | 0,3 | Balance | 0,193 | 0,059 | 0,076 | 0,292 |
1B | 0,7 | Balance | 0,528 | 0,111 | 0,167 | 0,384 |
2B | 0,7 | Balance | 0,511 | 0,131 | 0,181 | 0,404 |
3B | 0,7 | Balance | 0,481 | 0,123 | 0,151 | 0,472 |
4B | 0,7 | Balance | 0,567 | 0,106 | 0,210 | 0,323 |
5B | 0,7 | Balance | 0,487 | 0,137 | 0,178 | 0,513 |
De acuerdo con los modelos C y D, la cromita contribuye favorablemente sobre la composición química del cordón de soldadura en cuanto al aporte de Cr. Este resultado es lógico debido a que el componente portador del Cr es el Cr2O3 y con el aumento de su concentración se favorece la obtención de este elemento en el metal depositado. Sin embargo, limita la trasferencia del C al cordón de soldadura debido a que los óxidos FeO; SiO2 y Cr2O3 son reducidos por el C según las reacciones (1; 2; 3), lo cual consume parte del C adicionado a la mezcla.
A pesar de que el grafito puede contribuir a la presencia de Si en el cordón de soldadura, al facilitar el fenómeno de la reducción del SiO2, ecuación (3), el contenido de este óxido en la cromita es bajo, 5,5 %, por tanto el Si que se reduce es consumido en el proceso de desoxidación y no se transfiere al metal depositado.
A partir de los resultados de la composición química mostrados en la tabla 5, se puede hacer un análisis de las particularidades de las aleaciones obtenidas con los electrodos fabricados con diferentes variantes de revestimientos. En el caso del C, los contenidos están en un rango desde 0,193 a 0,567 %, lo que está en correspondencia con los aceros hipoeutectoides. Si además se considera el contenido de Cr, algunas de las aleaciones, 3B y 5B, son semejantes a un acero de baja aleación al Cr según la clasificación AISI/SAE de los aceros de baja aleación, 5045 y el 5046.
En condiciones reales de recargue esta composición química variará en función de la dilución y la cantidad de capas (pasadas) que se depositen. Si el recargue de una pieza de acero AISI 1045 se realiza con una dilución del 35 % en la primera pasada, el contenido de C será de 0,48 % y el de Cr es 0,41 %.
Influencia de la composición del revestimiento periférico en la dureza del metal depositado
De acuerdo al resultado del procesamiento de los datos del diseño de experimento en cuanto a los valores de dureza, obtenidos en depósitos realizados con electrodos con revestimientos periféricos en dos pasadas [12], tabla 6, existe un efecto significativo sobre esta propiedad de las variables independientes, según los modelos E, F, G y H, los cuales se presentan a continuación.
Las dos variables independientes resultan significativas para la magnitud de la dureza con un nivel de confianza del 95 %. Esto se debe a que el grafito aporta C a la aleación y la cromita es fuente de Cr. El Cr aumenta la dureza y la resistencia mecánica y mejora la templabilidad de la aleación [13, 14]. En estado de fusión el Cr es capaz de sustituir los átomos de hierro del acero y formar una solución sólida que aumenta la resistencia mecánica y la dureza del cordón.
Tabla 6 Dureza del metal depositado por electrodos con revestimiento periférico, HRC. Fuente: autores
Probetas | Espesor del revestimiento (mm) | Pasadas | Puntos de medición | Promedio | ||||
---|---|---|---|---|---|---|---|---|
1 | 2 | 3 | 4 | 5 | ||||
1A | 0,3 | 1 | 15 | 13 | 14 | 14 | 15 | 14,2 |
2 | 16 | 15 | 17 | 16 | 16 | 16,0 | ||
2A | 0,3 | 1 | 13 | 15 | 15 | 13 | 14 | 14,0 |
2 | 17 | 18 | 18 | 18 | 19 | 18,0 | ||
3A | 0,3 | 1 | 16 | 15 | 16 | 16 | 17 | 16,0 |
2 | 22 | 22 | 23 | 21 | 22 | 22,0 | ||
4A | 0,3 | 1 | 12 | 13 | 14 | 13 | 14 | 13,2 |
2 | 15 | 16 | 15 | 14 | 15 | 15,0 | ||
5A | 0,3 | 1 | 21 | 22 | 20 | 21 | 22 | 21,2 |
2 | 23 | 24 | 24 | 25 | 24 | 24,0 | ||
1B | 0,7 | 1 | 25 | 24 | 26 | 26 | 25 | 25,2 |
2 | 32 | 31 | 32 | 30 | 31 | 31,2 | ||
2B | 0,7 | 1 | 26 | 26 | 27 | 25 | 27 | 26,2 |
2 | 35 | 36 | 36 | 35 | 35 | 35,4 | ||
3B | 0,7 | 1 | 29 | 30 | 29 | 30 | 28 | 29,2 |
2 | 37 | 38 | 37 | 37 | 36 | 37,0 | ||
4B | 0,7 | 1 | 19 | 18 | 19 | 17 | 19 | 18,4 |
2 | 26 | 26 | 25 | 25 | 26 | 25,6 | ||
5B | 0,7 | 1 | 31 | 30 | 31 | 29 | 31 | 30,4 |
2 | 39 | 38 | 38 | 39 | 39 | 38,6 |
La dureza en los cordones obtenidos con electrodos con cintas de 0,3 mm de espesor del revestimiento (1A, 2A, 3A, 4A, 5A), para la primera pasada varía de 14,2 a 22 HRC, en la segunda pasada de 15 a 24 HRC. Mientras en los cordones donde se emplearon electrodos con cintas de 0,7 mm de espesor del revestimiento (1B, 2B, 3B, 4B, 5B), la dureza en la primera pasada fue de 18,4 a 30,4 HRC, y en la segunda pasada de 25,6 a 38,6 HRC.
Se pudo constatar que los electrodos que tuvieron un revestimiento periférico con cintas de 0,3 mm de espesor en el revestimiento, no fueron capaces de lograr durezas en el metal depositado en la segunda pasada del orden de 25 HRC, debido a que la cantidad de elementos aleantes aportados es insuficiente para provocar una apreciable modificación de la composición química del depósito. Sin embargo, en el metal depositado por electrodos con revestimientos periféricos con cintas de 0,7 mm de espesor, si se aprecia un significativo incremento de la dureza, logrando valores por encima de 30 HRC.
La aplicación al electrodo AWS E6013 de un revestimiento periférico constituido por una cinta, en la cual se han introducido componentes, tales como la cromita y el grafito, modificó favorablemente la composición química y la dureza del metal depositado. Ya que estos componentes al ser fundidos por la acción del arco eléctrico son capaces de alear el cordón de soldadura con Cr y C [11, 14, 15]. Los mejores resultados se obtuvieron con cintas de 0,7 mm de espesor, debido a una mayor cuantía de los componentes en el revestimiento. Estos resultados son comparables con electrodos comerciales como el INDURA BUIL UP 24, con el cual se obtiene una dureza de 18 a 31 HRC en la primera capa y de 21 a 33 HRC en la segunda. Además, los contenidos de C y Cr no son elevados, 0,12 % y 1,05 % respectivamente.
Por otra parte, la utilización de componentes en forma de aleaciones en la composición del revestimiento, por ejemplo FeCr, debe incrementar el grado de aleación del cordón de soldadura y la cuantía de Cr, aspecto beneficioso para aumentar la resistencia al desgaste adhesivo [8].
La importancia del trabajo radica en la posibilidad de convertir electrodos comerciales E6013, en electrodos para recargue mediante la adición de un revestimiento periférico en forma de cinta con determinada carga de elementos de aleación. Esta acción es realizada por el propio soldador a partir de identificar el tipo de desgaste que debe resistir la pieza.
Conclusiones
Durante la fusión del electrodo con el revestimiento periférico tipo cinta se garantiza la reducción carbotérmica de la cromita, a partir del calor aportado por el arco eléctrico, contribuyendo a alear el cordón de soldadura con Cr (hasta 0,513 %). Los contenidos de Cr (0,323 a 0,513 %) y C (0,481 a 0,567 %) obtenidos en los cordones de soldadura a partir del revestimiento periférico con cintas de espesor 0,7 mm, así como la dureza (25,6 a 38,6 HRC) en la segunda pasada, hacen posible que los electrodos correspondientes según la variante, puedan emplearse para el recargue de piezas expuestas a desgaste adhesivo, a partir de la comparación con electrodos similares, comercializados en el mercado internacional.