Introducción
La creciente exigencia en las propiedades de los productos terminados y en la maximización de los recursos económicos ha generado una necesidad en la industria de obtener piezas coladas de mejor calidad. Un grave problema son los defectos de contracción que ocurren durante el proceso de solidificación y posterior enfriamiento en la colada, los cuales traen aparejado el re trabajado o hasta el desecho de las piezas lo que conlleva a una pérdida de tiempo y productividad.
La aleación inoxidable austenítica ACI HK 40, de producción nacional, tiene aplicación en la industria minero metalúrgica de Cuba en la fabricación de componentes como son: tramos de ejes centrales, de brazos agitadores y de dientes rascadores para hornos de reducción del mineral laterítico, donde se requiere una atmósfera reductora con alto contenido de CO, CO2 y nitrógeno. La aleación se expone a tratamientos isotérmicos de carburización y de nitruración. En las temperaturas en que normalmente operan los hornos de 650 - 850 ºC en ocasiones, hasta 1 000 ºC, puede ocurrir la disociación del carbono y el nitrógeno presente en los gases [1].
Durante el enfriamiento en el molde, la primera fase en solidificar es la austenita sin formarse carburos. Esta solidifica en forma dendrítica, la última parte lo hace en eutéctica austenita-carburo, en regiones interdendríticas. Por esta forma de enfriamiento, la microestructura es de carburos primarios en una matriz austenítica [2, 3]. De acuerdo con [4] en ocasiones se encuentran inclusiones de sulfuro de manganeso y la forma de los carburos primarios se presenta de forma laminar y de esqueleto, encontrándose eutécticos del tipo M7C3.
Cuando el acero refractario está sujeto a esfuerzos de tensión, en este se empiezan a generar pequeñas cavidades en la microestructura conforme avanza el tiempo de operación a altas temperaturas. El problema del carburizado generalmente se manifiesta con la formación de carburos internos en la matriz, así como también en las fronteras del grano. La difusión de carbono en los aceros inoxidables promueve la formación de carburos que pueden ser de la forma M7C3, M23C6 o M3C. La carburización causa la fragilización de la aleación y también la pérdida de propiedades mecánicas [5]
Exponen en [6] que, dependiendo de los contenidos de cromo y de níquel del material fundido, su microestructura puede resultar en una distribución predominantemente ferrítica, austenítica o de fase dual, incluyendo, además, una fina distribución de carburos y otras fases intermedias en la matriz metálica cuando se adiciona carbono al sistema. En este contexto, aceros refractarios con contenido de carbono mayor que 0,20 % exhiben la presencia de algunos carburos de hierro y cromo, del tipo M23C6 y M7C3 [7], independientemente del proceso de solubilización que haya experimentado el material; estos aumentan la resistencia mecánica del material a altas temperaturas.
La precipitación de carburos en la microestructura aumenta la resistencia mecánica a altas temperaturas, mientras que la formación de fase sigma puede resultar perjudicial en aplicaciones industriales, debido a que reduce la tenacidad y resistencia a la corrosión de las aleaciones a temperatura ambiente, así como a la termofluencia a altas temperaturas de modo creciente con el tiempo y temperatura de exposición, en su rango de formación [7, 8].
La respuesta mecánica de las aleaciones depende de factores como son la composición química, el tamaño y volumen de las fases ricas en hierro, la modificación o no del silicio y el tamaño de celda dendrítica. Tanto la porosidad como muchos de estos factores se ven modificados por las mismas variables, como es la velocidad de enfriamiento y el tiempo local de solidificación. Debido a esto es prácticamente imposible determinar con precisión la influencia específica de la porosidad sobre las propiedades mecánicas del material [9].
En [1] se obtuvo un diagrama de fases y se evaluó la evolución de las fracciones de fases sólidas durante la solidificación, en condiciones de equilibrio en los rangos de temperatura y composición correspondientes a las ventanas de precipitación de las fases obtenidas en correspondencia con las propiedades mecánicas estimadas; así como el pronóstico de la evolución de la microestructura del HK 40 al someterlo a elevadas temperaturas para prevenir la precipitación de fases secundarias indeseadas como las fases sigma (σ), concluyeron que en el mismo existe presencia de fases de carburos complejos del tipo M23C6.
El trabajo tuvo como objetivo determinar los componentes metalúrgicos de la aleación HK 40 empleada en dientes de barrido luego del proceso de fundición.
Métodos y Materiales
Para determinar los componentes metalúrgicos de la aleación HK 40 empleadas en dientes de barridos luego del proceso de fundición, fueron seleccionados nueve como se muestra en la figura 1, que fueron analizados en diferentes partes según su forma geométrica.
A los dientes se les determinó el comportamiento microestructural, el tamaño de granos, el por ciento de carburos, la dureza y la porosidad.
En la tabla 1 se muestra la composición química de la aleación HK 40, obtenida en un espectrómetro de masa cuántico, ESPECTROLAB 230 con electrodo de carbón bajo arco sumergido en atmósfera de argón.
Tabla 1 Composición química de la aleación HK-40, % en masa. Fuente: autores
Grado | C | Si | Mn | P | S | Cr | Mo | Ni | Al |
---|---|---|---|---|---|---|---|---|---|
A 351 HK 40 | 0,44 | 0,54 | 0,39 | 0,02 | 0,04 | 24,1 | 0,07 | 19,5 | 0,39 |
En esta aleación, los elementos carbono, 0,44 % y cromo, 24,1 %, favorecen la formación de fase intermetálica sigma. El níquel (19,5 %), aporta resistencia a las altas temperaturas y a la corrosión con el control del crecimiento de grano debido a la presencia de cromo que, al tender a formar carburos, lo descompone y mantiene la estructura austenítica y aumento de la resistencia mecánica a alta temperatura.
El Cr forma una capa de cromita Cr203 y el C permite estabilizar la austenita, pero su afinidad termodinámica por el Cr, tiende a formar carburos, esto hace que las propiedades mecánicas y físicas además del comportamiento a la corrosión cambien.
Preparación metalográfica
Las operaciones que se realizaron para la preparación metalográfica fueron: corte, desbaste, pulido, desengrasado, lavado y ataque químico. En la figura 2 se muestran los dientes luego del corte.
El corte se realizó en una cortadora del tipo EchoRD, con mecanismo de disco refrigerado para evitar el calentamiento y no generar cambios en su microestructura. El desbaste consistió en obtener una superficie plana y semipulida. El pulido se realizó, variando la granulometría de las lijas, desde la más gruesa a la más fina, se empleó óxido de cromo añadida sobre discos provistos de paños. Una vez pulida se lavaron con agua destilada, se secaron con papel de filtro y finalmente se volvieron a lavar con tetracloruro de carbono para evitar vestigio de grasa y pastas de pulir. Se empleó las técnicas de ataque químico y manual por inmersión. El de inmersión, se realizó durante cinco segundos con el reactivo ácido clorhídrico al 50 % (50 ml HCl; 50 ml H2O), este delinea la ferrita, por lo que revela sus fronteras.
Microestructura patrón de la fundición
Para la observación de las microestructuras se empleó un microscopio óptico binocular marca NOVEL modelo NIM - 100 de fabricación china, dotado de una cámara instalada en el hardware. El análisis microestructural consistió en la observación de una muestra patrón como se muestra en la figura 3 de la aleación fundida.
Presenta una estructura austenítica en forma de collar, caracterizada por carburos alargados, preferencialmente ubicados en bordes dendríticos, rodeando a la fase austenítica y en bordes de grano con una precipitación parcial. La ferrita se encuentra ubicada también en los bordes de los granos. Este tipo de aleación es austenítica, que le proporciona resistencia a la oxidación.
Para la medición de la dureza (HV) se utilizó un durómetro digital modelo HRS-ISO (Digital Rockwell Hardness Tester), para lo cual se realizó un barrido en las diferentes zonas de los dientes de barridos (centro, borde y entre centro y borde), las que se promediaron, la carga aplicada fue de 0,49 N; en un tiempo de 15 s. El indentador empleado fue el de pirámide de diamante, con un ángulo de 136º.
Para determinar el tamaño de granos, el por ciento de carburos y la porosidad, se empleó un microscopio óptico binocular reflexivo marca echoLAB, el cual tiene acoplado una cámara que muestra los resultados en el computador.
Resultados y Discusión
Microestructura en las zonas de los dientes
El proceso de solidificación tiene importancia en las características física de la fundición, pues condiciona la transformación eutectoide posterior a través de factores como las microsegregaciones, el tamaño y la morfología de los granos. Se realizó el análisis microestructural para determinar las variaciones luego del proceso de fundición, para ello se seleccionaron tres dientes aleatoriamente 1, 4 y 9, figura 2, se escogió este procedimiento teniendo en cuenta los criterios de [10] que se realiza, cuando la población seleccionada, representa el 30 % o un por ciento superior con respecto al total de las muestras estudiadas. En la figura 4 se muestra el comportamiento de las estructuras.
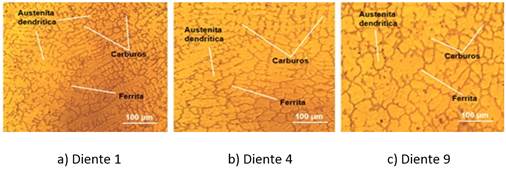
Fig. 4 Se observa que todas las estructuras presentan un comportamiento igual en cuanto a la formación de las fases (austenita, ferrita y los carburos del tipo Cr23C6).
Sin embargo, existe una tendencia a no mantener el mismo tamaño de los granos en cada uno de los dientes analizados.
Por la particularidad de presentar cromo la aleación HK 40 (24,1 %) y carbono (0,44 %) existe también la posibilidad de formación de fase sigma (σ), la cual resulta perjudicial en la función que desempeñan los dientes rascadores, debido a que reduce notablemente la tenacidad y la resistencia a la corrosión de las aleaciones a temperatura ambiente. El desequilibrio de composiciones es posible, resultando en ferrita, cuando puede transformarse en fase sigma, es en este momento en el que se encuentra retenida la austenita en una temperatura de 815 °C por un corto tiempo. También, puede afectar a la resistencia a la termofluencia durante la etapa de deslizamiento de las dislocaciones) a altas temperaturas, de modo creciente con el tiempo de exposición en su intervalo térmico de formación, reportado por [11, 12].
Comportamiento del tamaño del grano
Para determinar el tamaño de los granos se siguió el mismo procedimiento que para el análisis microestructural, teniendo en cuenta que, cuando más de un aspecto de la estructura cambia, los métodos de comparación no pueden cubrir todos los grados y combinaciones del cambio. El método depende básicamente de la clasificación de fotografías, y los errores influyen en la exactitud llegando a ser altamente dependientes de la opinión subjetiva, figura 5.
Al analizar el tamaño de los granos de los dientes, según la norma ASTM Standard E112, se determinó que, en un área de 0,842 μm, para los dientes 4 y 9, el tamaño aproximado es No. 5 y para el 1 es No. 3,5; resultados obtenidos para una observación de 1 μm/pixel. Con la determinación de este, se observa en los límites de los mismos un engrosamiento, indicativo de la precipitación de carburos de cromo. La variación del tamaño del grano tiene influencia en las propiedades finales de la aleación.
Un material que tiene un grano fino posee, a temperatura ambiente, una dureza superior, así como mayor resistencia a la fatiga y al impacto, comparado con uno de grano grueso. A elevada temperatura, las propiedades de fluencia son generalmente mejores para materiales de grano grueso, pero esta ventaja se puede equiparar con otras inferiores bajo otras condiciones de carga [13].
La forma y aspecto del tamaño de grano, así como la orientación y dirección que tienen, resultado del tratamiento termomecánico, afectan las propiedades bajo tensión y el esfuerzo inicial de fluencia. Las aleaciones endurecidas por una dispersión de óxidos, tienen mejores propiedades de esfuerzo inicial de fluencia y resistencia a la tensión cuando las pruebas se han realizado en la dirección paralela a la deformación 100, cuando la relación del tamaño de grano crece, aumentan las propiedades, según el criterio de [14]. En las tres muestras se observan precipitados, los cuales van a tener influencia sobre los resultados finales de termofluencia.
Se cuantificaron los carburos presentes, dividiéndolos en precipitados en frontera de grano y en la matriz austenítica. En la tabla 2 se muestra este comportamiento realizado para los tres dientes.
Tabla 2 Por ciento de carburos en los dientes. Fuente: autores
Muestras | AA (mm2) | ACCr (mm2) | % A | % CCr |
---|---|---|---|---|
Diente 1 | 13 985,84 | 1 064,20 | 86,07 | 6,50 |
13 995,65 | 1 084,39 | 85,45 | 6,80 | |
13 945,58 | 1 104,46 | 86,90 | 7,12 | |
Diente 4 | 13 737,69 | 1 312,35 | 83,43 | 8,46 |
13 696,10 | 1 353,94 | 80,25 | 8,73 | |
13 673,71 | 1 376,33 | 82,45 | 8,87 | |
Diente 9 | 12 343,54 | 2 706,50 | 71,15 | 17,45 |
11 993,50 | 2 856,50 | 78,54 | 18,95 | |
11 493,31 | 3 056,41 | 73,24 | 20,65 |
Leyenda: AA: Área de la austenita. ACCr: Área de los carburos de cromo. % A: porciento austenita. % CCr: porciento de carburos de cromo
Al estimar el por ciento de carburos en cada uno de los dientes se observa que, el No.9 presenta una mayor presencia de los mismos en la matriz, con lo cual se puede plantear que, en términos de fundición, independientemente que los mismos fueron obtenidos bajo las mismas condiciones fue diferente el proceso de solidificación, por lo tanto, el aumento de esta fase en la microestructura disminuye la cohesión intergranular, causando, así, un deterioro de las propiedades. La dispersión de los puntos experimentales debe su origen a los defectos de fundición de las piezas.
Los precipitados en frontera de grano son continuos con un espesor promedio de 10 micras y alrededor de todos los granos, los precipitados en la matriz son esféricos con tamaños de 2 a 5 micras y generalmente se encuentran más cerca de las fronteras de los granos que en el centro de estos. En este contexto, aceros refractarios con contenido de carbono mayor que 0,20 % exhiben la presencia de algunos carburos de hierro y cromo, del tipo M23C6 y M7C3 independientemente del proceso que haya experimentado el material; estos carburos aumentan la resistencia mecánica del material a altas temperaturas, según ha sido reportado en trabajos previos por [7].
Determinación de la porosidad
Las propiedades mecánicas y físicas de los dientes están influenciadas por la calidad del baño fundido, la composición química de la aleación y la microestructura del producto colado. La calidad de baño se mejora con los tratamientos de metal líquido realizados para controlar el gas de hidrógeno, óxidos e inclusiones, controles de temperatura, refinación y modificación. En la tabla 3 se muestran los resultados de la porosidad.
Tabla 3 Resultados de la porosidad en los dientes. Fuente: autores
Dientes | Parámetros | Valor | % O | % N | % H | % Poros |
---|---|---|---|---|---|---|
D1 - D9 | Temperatura liquidus (ºC) | 838,68 | 0,005 | 0,0250 | 0,0025 | 0,91 |
Temperatura solidus (ºC) | 715,55 | 0,004 | 0,0210 | 0,0008 | ||
Tiempo inicio solidif. (s) | 37 | 0,001 | 0,0080 | 0,0006 | ||
Fin solidificación (s) | 180 | 0,001 | 0,0080 | 0,0008 | ||
Tiempo solidificación (s) | 120 | 0,001 | 0,0080 | 0,0008 |
En la determinación de la temperatura y fracción de líquido, para un tiempo de 180 segundos luego del llenado e inicio del proceso de solidificación del diente donde queda aislado del sistema de alimentación, en ese instante el modelo presenta una temperatura de 715,55 °C en el centro de la placa superior. Los resultados obtenidos de la porosidad está avalado por que, en el interior de la pieza fundida se encontraron poros de diferentes formas y tamaños, los cuales estaban interconectados entre sí, se observaron poros pequeños localizados en la zona interdendrítica de la microestructura, los cuales se forman entre los brazos de las dendritas que van solidificando, microporos agrupados alrededor de un poro central de mayor tamaño, localizado entre la fase ferrita-carburo y de mayor tamaño, ocasionados por los gases atrapados en el interior de la matriz, los cuales están rodeados por otros de menor tamaño.
La presencia del nitrógeno origina dificultades en los aceros por comunicarles fragilidad y reducir la ductilidad, en el hierro gamma (austenita) la solubilidad es mayor que en el delta. Es un elemento estabilizador de la austenita y produce efectos análogos a los del carbono, reduce la tendencia a la corrosión por picaduras, el hidrógeno aumenta la solubilidad al elevarse la temperatura del metal fundido y al solidificarse el hierro disminuye la misma, al seguir enfriándose, tiene mayor disminución. Por otro lado, el contenido de oxígeno en el acero líquido aumenta a medida que el % C disminuye, depende de la condición de equilibrio en relación con el contenido de carbono, figura 6.
En la tabla 4 se muestran los resultados de las porosidades.
Tabla 4 Tamaño de las microcavidades en los dientes. Fuente: autores
Dientes | Tpc(µ) | Dcav | Ubcav | Tcav |
---|---|---|---|---|
D-1 | 4 | 400 | Frontera | 6,23 |
D-2 | 10 | 750 | Frontera | 9,34 |
D-3 | 12 | 1850 | General | 22,34 |
D-4 | 6 | 425 | Frontera | 7,11 |
D-5 | 6 | 425 | Frontera | 7,11 |
D-6 | 5 | 350 | Frontera | 5,43 |
D-7 | 4 | 400 | Frontera | 6,23 |
D-8 | 13 | 2250 | General | 26,57 |
D-9 | 8 | 2000 | General | 13,38 |
Leyenda: Tpc: tamaño promedio de las cavidades; µ. Dcav: densidad de las cavidades; cm/mm2. Ubcav: ubicación de las cavidades. Tcav: tamaño de las cavidades; µm
La porosidad que se presenta en los dientes 2, 3 y 8 son las mayores encontradas en relación a los demás, siendo el 8 el más afectado con tamaño de cavidad de 26,57 µm, aunque en los otros existe la presencia de estos defectos en menor escala y cuantía. Estas cavidades encontradas, presumiblemente estén asociadas a la forma geométrica, ubicándose en la parte superior el cuello y en los cambios bruscos de sección, que inhibe la secuencia de solidificación según el criterio de fracción de líquido, la cual ayuda a entender que la porosidad se origina por la realimentación del cuerpo inferior.
Este defecto en piezas coladas es ocasionado por dos fenómenos. Uno de ellos es la disminución de la capacidad de disolver gases que quedan atrapados durante la solidificación, denominado porosidad por gas. El otro es debido a una deficiencia en la alimentación requerida para compensar la contracción del metal durante la solidificación y el enfriamiento, y se lo denomina porosidad por contracción.
Cuando el poro de gas aparece en la zona pastosa, luego de la coherencia dendrítica, este es atrapado. Cuando el flujo del metal se bloquea a través del frente de solidificación, el poro se convierte en un punto de inicio de la microcontracción. Así, la formación de micro contracciones depende de la nucleación y crecimiento de micro poros, según el criterio expuesto por [2].
Se analizó la dureza obtenida en los dientes en bruto de colada (Bcolada) a partir del barrido realizado en las diferentes zonas. En la tabla 5 se muestra el comportamiento obtenido.
Tabla 5 Comportamiento de la dureza. Fuente: autores
Muestras | BColada | HV1 | HV2 | HV3 | HVP |
---|---|---|---|---|---|
D-1 | 170 | 168 | 170 | 170 | 169,0 |
D-2 | 170 | 167 | 173 | 172 | 170,6 |
D-3 | 173 | 170 | 173 | 171 | 172,0 |
D-4 | 171 | 171 | 170 | 171 | 169,5 |
D-5 | 171 | 168 | 169 | 169 | 168,5 |
D-6 | 170 | 172 | 172 | 172 | 172,0 |
D-7 | 172 | 170 | 170 | 171 | 170,5 |
D-8 | 170 | 173 | 173 | 172 | 172,5 |
D-9 | 172 | 172 | 172 | 171 | 171,5 |
En el barrido de dureza efectuado en las diferentes zonas de los dientes se puede observar que, para un valor inicial de 170 HV, en bruto de colada, esta propiedad tiende a mantenerse estable en todos los dientes, lo cual permite plantear que, por causa de esta propiedad no ocurre el efecto de la fractura de los dientes rascadores de los brazos de barrido. El comportamiento de los materiales en fractura indica un mecanismo combinado dúctil-frágil que aumenta su carácter de fragilidad a mayores contenidos relativos de fase sigma.
Conclusiones
En los dientes analizados las microestructuras obtenidas presentan fases austenita, ferrita y carburos del tipo Cr23C6, pero con variaciones en el tamaño del grano con número de 3,5 y de 5 respectivamente, lo cual está asociado al proceso de solidificación.
Se determinó que, a una temperatura de 715,55 ºC, correspondiente a la del sólido para el diente fabricado de la aleación HK 40, existen poros con una cavidad de 26,57 µm, siendo esta la mayor encontrada en la los mismos, independientemente que en los demás exista también presencia de ellos, atribuible a la forma geométrica de la pieza.
En el barrido de dureza realizado en los diferentes dientes fabricados de HK 40 se determinó que los mismos mantienen la misma tendencia de dureza en cada uno, por lo tanto, esta propiedad, aunque exista carburos de cromo, no debe provocar su rotura en servicio.