INTRODUCTION
Precise and scientifically justified calculations of dynamic load coefficients guarantee efficient designs and a considerable saving of materials in the manufacture of prototypes.
The determination of the stresses caused by the dynamic loads is complex depending on factors such as contact area in the impact and the variation process of the contact forcesas a function of time. In this sense, most dynamic cases are quantify experimentally and for simple calculations, equivalent static charges are used. The determination of the coefficients of dynamic loads in structures subjected to impact actions, using analytical methods, represents a challenge due to their high complexity.
The method of finite elements, as a numerical method of computer-assisted discretization, is an alternative way to the analytical method of continuous medium analysis, which facilitates the solution of complex engineering problems, being considered a tool of undoubted practical value and great application worldwide. There are important results derived from the use of this method, among them the ones reported by Martínez et al. (2007); Liu et al. (2013) and Untaroiu et al.(2013). Also, those referred by Vavalle et al. (2013); Feng & Aymerich (2014); Nadal et al. (2014); Zhanbiao et al. (2014); Singh & Singh (2015); Zhao et al. (2015); Kong et al. (2016); Xiaofei et al.(2016) and Castro & Güiza (2017).
The objective of this work was to evaluate and compare three methodologies for determining dynamic load coefficients: the traditional analytical method (MA), the numerical simulation based on the finite element analysis (MEF) and the experimental method (Mexp), taking this last as a comparison and validation pattern of the theoretical methods.
METHODS
A multifactorial type design was used, using two factors as independent variables that correspond to the height and the impact load, with ten and three levels, respectively. The impact height levels were from 0 to 1 m with intervals of 0.1 m and the load levels were 25; 400 and 800 N.
For the three methods analyzed, the coefficient of dynamic loads was determined starting from the determination of the static deflection produced on a mechanical system taken as an object of study under the action of static charges with a magnitude equal to the weight of a body that impactsince a certain height. Once the maximum static deflections of the system under study were determined, the coefficient of dynamic loads was determined using the expression according to Pisarenko and Yakovlev (1979):
where:
kd |
- Coefficient of dynamic loads; |
δ est |
- Deflection or maximum static arrow, which also depends on the solicitation scheme and the support conditions; |
H |
- Height of fall of the body that impacts on the system under study. |
In this work, the static deflection of the system under study was determined by the three mentioned methods: the traditional analytical method of the mechanics of materials; the method of finite elements and the experimental method.
Description of the Mechanical System under Study
As a study object, a beam of square cross section (Table 1) was used in horizontal position and supported at its ends with a joint and a simple support, as shown in Figure 1. In the center of the beam, three levels of load Q (25, 400 and 800 N) were applied to provoke different levels of static deflections (δ). In Table 2, the mechanical properties of the material are shown.
TABLE 1 Description of the system under study
Cross section | Side, mm | Mass, kg | Moment of inertia, m4 | Length, mm | Acting load, N |
---|---|---|---|---|---|
Square | 39.09 | 12 | 1.95*10-7 | 1000 | From 25 to 800 at the interval of 25 |
TABLE 2 Physical mechanical properties of the beam material
Description | Value |
---|---|
Modulus of elasticity | 200 000 MPa |
Poissoncoefficient | 0.29 |
Density of mass | 7900 kgm-3 |
Limittotraction | 420.507 MPa |
ElasticLimit | 351.561 MPa |
Source: Warrendale (2001)
Determination of Static Deflections by the Traditional Analytical Method
For the case under study, consisting of a horizontal beam simply supported when the application of the load is made in the center of the beam and the maximum static arrow is given by the expression:
where:
Q |
- mg: weight of the impacting element, kg ms-2 |
l |
- length of the beam, m |
E |
- modulus of elasticity of the beam material |
J |
- moment of inertia of the section of the beam |
From the element size, the rest of the properties of the mesh are established (Table 3). In Figure 3, a 3D view of the model of the beam with the resulting meshing and boundary conditions is shown, where the restrictions (green arrows) and the statically applied load (red arrows) are represented.
TABLE 3 Characteristics of the mesh used in the analysis
Parameters | Mesh | Quality | Tolerance | Number of nodes | Number of elements | Size of elements |
---|---|---|---|---|---|---|
Description | Solid, Standard | High | 0.05 mm | 4,340 | 2,342 | 20 mm |
Description of the Experimental Method Used
The experimental determination of the static deformations that allowed determining the coefficients of dynamic loads of the system studied, under different dynamic loads, was carried out by means of electrical extensometry techniques.
On the underside of the center of the beam studied,strain gauges were placed (Figure 4) configured in a quarter of Wheatstone bridge, with the aim of obtaining voltage signals proportional to the unitary deformation (considering the deformations within the elastic limit of the material), produced by static charges of different magnitude. The static charges were obtained by placing weights of 25 N; 400 N and 800 N in the center of the beam and recording the output voltage (eest) of the measurement system. In a similar way, the output voltage (edin) produced by the same applied loads was recorded, dropping the same weights from different heights between 0.1 and 1 m to the center of the beam. For each treatment, three repetitions were made. The quotient of the voltages obtained, for each of the loads and heights applied, allowed obtaining the coefficient of dynamic loads in each case, applying the expression:
where
eest |
- is the voltage registered under the action of the loads applied in static form; |
e din |
- is the maximum voltage under the action of the loads applied dynamically (when dropping the weights from different heights); |
ε est and ε din |
- are the unit deformations corresponding to the static and dynamic loads, respectively; |
σ est and σ din |
- are normal stresses corresponding to static and dynamic loads, respectively. |
The signals coming from the strain gauges (of the order of the mV), were processed in a dynamic amplifier, model KYOWA-YA-520 with amplification modules of type DPM-602B, being amplified up to voltage levels between ± 5V.
The analog signal coming from the amplifier (Figure 5) was digitalized in an analog-digital converter model NATIONAL INSTRUMENTS - NI USB-4431 and introduced at a rate of 100 samples per second in a laptop computer for further statistical processing.
RESULTS AND DISCUSSION
Figure 6 shows one of the outputs of the static analysis by the MEF to determine the unit deformation of the beam under study. When the beam is subjected to 800 N static load, it is observed that the value of the unit strain is 86.976 μstrain, while the result of the stress for that same load value is shown in Figure 7, where it reached a value of 17.3952 MPa.
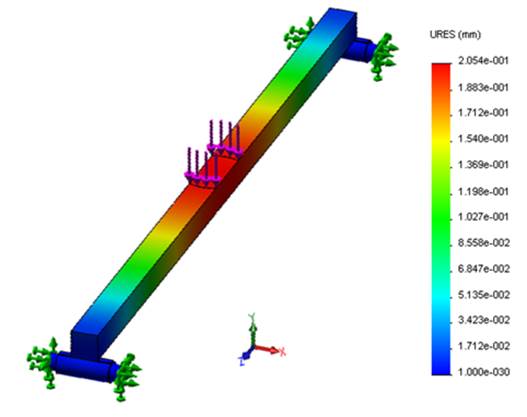
FIGURE 8 Deflection of the beam in the vertical direction for a static load of 800 N by analysis with the finite element method.
Experimental Evaluation of the Numerical Simulation
Figure 9 shows two graphs with the cumulative distribution of the deformations predicted with the model analyzed by the MEF and the experimental results. The data obtained showed that the maximum distance between the accumulated distributions of the two samples is 0.03125 μstrain, where the approximate p-value obtained is greater than 0.05, so there is no statistically significant difference between the two distributions for a confidence level of 95%. It was observed that the data obtained for the stresses predicted with the model analyzed by MEF and those calculated from experimental tests coincide with the results obtained for the deformation, this is because the stresses are calculated from the deformations using the law of Hooke.
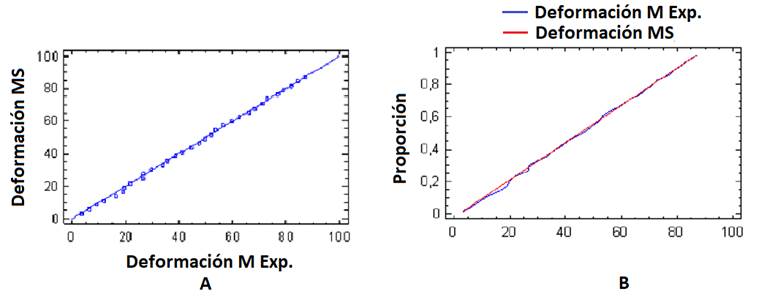
FIGURE 9 Accumulated distribution (A) and distribution function (B) between the deformations predicted by the simulation and those obtained experimentally.
Figure 10 shows the cumulative distribution graph to compare the deflections predicted with the model analyzed by MEF and the experimental results, which shows that the maximum distances between the accumulated distributions of the two samples are of 0.09375 mm. For the behavior of the predicted and experimental deflection values, an approximate p-value of 0.998965 was obtained. Since it is greater than 0.05, there is no statistically significant difference between the two distributions for a 95% confidence level.
Result of the Coefficients of Dynamic Loads by the Three Methods Studied
Table 4 shows the results of the determination of the dynamic load coefficients by the different methods studied and the relative difference between the methods and the experimental results. It can be seen that the relative difference of the MEF ranged between 3.479 and 5.112%, being substantially lower than the values obtained by the analytical method (MA), which ranged from 21.820 to 27.201%.
The dynamic load coefficients reached values of 391.203 for the analytical case (MA), of 501.001 for the experimental case and a value of 528.047 for when the dynamic load coefficients were calculated from the data obtained via numerical simulation by the method of the finite elements (MEF), with a load of 25 N. The highest values of the coefficients of dynamic loads in the three calculation methods were recorded for the highest height studied (1 m) and with the lowest of the loads applied (25 N). For the same impact height it was determined that the highest values of dynamic load coefficients were recorded for the lower mass impact loads (25 N). At the same impact height, the lowest dynamic load coefficients were obtained while the impact load was greater. The case that the highest coefficient values of dynamic loads were recorded for the lower load is because the increase in the mass of the hitting element causes greater deflections, therefore, the coefficient of dynamic loads decreases, due to its inversely proportional relationship.
TABLE 4 Relative differences of the dynamic load coefficients by both methods métodos
Impactheight; m | Impact load; N | Coefficients of dynamicloads | Relativedifference | |||
---|---|---|---|---|---|---|
(MA) | (M Exp.) | (MEF) | MA-MExp; % | MEF- MExp; % | ||
0.1 | 25 | 124.397 | 159.117 | 167.62 | 21.820 | 5.344 |
400 | 31.864 | 42.897 | 45.141 | 25.720 | 5.231 | |
800 | 23 | 31.099 | 32.22 | 26.043 | 3.605 | |
0.2 | 25 | 175.51 | 224.61 | 236.704 | 21.860 | 5.384 |
400 | 44.637 | 60.243 | 63.417 | 25.905 | 5.269 | |
800 | 32 | 43.555 | 45.141 | 26.530 | 3.641 | |
0.3 | 25 | 214.725 | 274.863 | 289.677 | 21.879 | 5.390 |
400 | 54.44 | 73.555 | 77.441 | 25.987 | 5.283 | |
800 | 38.794 | 53.115 | 55.057 | 26.962 | 3.656 | |
0.4 | 25 | 247.787 | 317.229 | 334.335 | 21.890 | 5.392 |
400 | 62.704 | 84.777 | 89.265 | 26.037 | 5.294 | |
800 | 44.637 | 61.174 | 63.417 | 27.033 | 3.667 | |
0.5 | 25 | 276.916 | 354.555 | 373.679 | 21.898 | 5.394 |
400 | 69.986 | 94.664 | 99.682 | 26.069 | 5.301 | |
800 | 49.785 | 68.275 | 70.782 | 27.082 | 3.672 | |
0.6 | 25 | 303.251 | 388.3 | 409.25 | 21.903 | 5.395 |
400 | 76.569 | 103.603 | 109.1 | 26.094 | 5.306 | |
800 | 54.44 | 74.694 | 77.441 | 27.116 | 3.678 | |
0.7 | 25 | 327.468 | 419.331 | 441.96 | 21.907 | 5.396 |
400 | 82.623 | 111.823 | 117.76 | 26.113 | 5.309 | |
800 | 58.72 | 80.598 | 83.565 | 27.145 | 3.681 | |
0.8 | 25 | 350.009 | 448.215 | 472.406 | 21.910 | 5.397 |
400 | 88.258 | 119.474 | 125.821 | 26.128 | 5.312 | |
800 | 62.704 | 86.093 | 89.265 | 27.167 | 3.684 | |
0.9 | 25 | 371.468 | 475.343 | 501.001 | 21.853 | 5.398 |
400 | 93.55 | 126.66 | 133.393 | 26.141 | 5.316 | |
800 | 66.446 | 91.254 | 94.618 | 27.186 | 3.686 | |
1 | 25 | 391.203 | 501.001 | 528.047 | 21.916 | 5.398 |
400 | 98.556 | 133.457 | 140.554 | 26.151 | 5.318 | |
800 | 69.986 | 96.136 | 99.682 | 27.201 | 3.689 |
Figure 11 shows the behavior of the dynamic load coefficients by the three methods studied for an impact load of 400 N. The range of impact heights was from 0.2 to 1 m. It is observed that the behavior curve obtained by the MEF was the closest to that obtained by MExp. The results obtained by numerical simulation (MEF), gave better results and this is due to the advantage that the finite elements method offers before the analytical methods, which allows simulating the system more realistically, taking into account a greater number of factors during the simulation. The analytical processes are simplified and they are of great practical value to design innumerable systems, but theydo not allow knowing the detailsof the structural behavior under real actions.
Coinciding with the results obtained, Aparicio & Casas (1987)point out that in the interpretation of the results of tests of impact loads, it is important to know aspects that are not considered in the analytical studies. It is also vital to know the details of the phenomenon when they take into account the deflection of automobile structures to see their impact on the comfort and safety of passengers (Álvarez et al., 1983). On the other hand, Beltrán and Cerrolaza (1989), state that it is necessary to resort to more sophisticated calculation models that allow reproducing more accurately the real behavior of different systems.
CONCLUSIONS
The numerical simulation compared with experimental data for deformations and stresses reached a p-value greater than 0.05, so there was no statistically significant difference between the two distributions for a confidence level of 95%.
For the deflections predicted through the model analyzed by MEF and the experimental results, an approximate p-value of 0.99 was reached, so there was no statistically significant difference between the two distributions.
The relative difference between the coefficients of dynamic loads by experimental method (MExp.) and by numerical simulation (MEF) ranged between 3.479 and 5.122%, being substantially lower than the values obtained by the analytical method (MA), which reached values from 21.820 to 27.201%.