Introducción
Las tuberías de PEAD (polietileno de alta densidad) han ido sustituyendo a las de otros materiales por sus numerosas ventajas (López 2012; Pyeong et al. 2022), además de usarse en sistemas de abastecimiento de agua son empleadas para el transporte de petróleo, gas y otros fluidos industriales. Para el acoplamiento o unión de éstos cada vez se usa más la termofusión por ser más barata que la electrofusión y poder emplearse en diámetros mayores (Avrigean y Hunyadi 2014; Pyeong et al. 2022).
En Cuba se emplean actualmente tuberías de PEAD para la construcción de sistemas de abastecimiento de agua (López 2012), dichos conductos son soldados mediante termofusión. En la NC 969:2013 se establece el procedimiento para la termofusión a tope y el control visual a efectuar para garantizar su calidad. Los principales problemas que pueden presentarse son los siguientes: no linealidad del ensamblaje, fusión incompleta, expulsión del material fundido hacia el interior o hacia el exterior, agujas interrumpidas o acortadas, extremos ovalados, ciclo de soldadura incompleto (error de la máquina), entre otras (Avrigean y Hunyadi 2014), los errores pueden conducir a daños o roturas (Zhao et al. 1998), como la pérdida total o parcial del servicio del agua a la población o a entidades estatales, además, se puede poner en riesgo la vida de las personas debido a las grandes presiones a que se encuentran sometidos algunos conductos en determinados puntos de la red además de los daños materiales. Las juntas pueden constituir un eslabón débil en las tuberías de PEAD si su integridad es afectada, lo cual puede ocurrir por su contaminación por partículas finas y los defectos planos (Pyeong et al. 2022).
Los materiales y equipos a emplear en las obras se detallan en la norma cubana (NC 969: 2013), lo cual debe ser corroborado en el lugar, donde además, según el mismo documento, deben registrarse las incidencias y realizarse inspecciones y control de calidad de las uniones soldadas, lo cual es un deber del inversionista que lo hace a través de un inspector o de un representante autorizado.
Los elementos a controlar y las pruebas a realizar se indican en la norma. En condiciones de laboratorio se han determinado los principales parámetros de control, que son especificados por regulaciones (NC 969: 2013; ASTM F-2620-13 (2014); D.V.S 2207-01 (2007); ISO 21307:2017 (E)) y por los fabricantes de los equipos que se empleen, las que se realizan en ambientes controlados de temperatura y humedad (Pyeong et al 2022), sin embargo, en condiciones de campo el ambiente es diferente e influye en el control del proceso.
En Camagüey, se emplea, a pie de obra, una tabla elaborada por la Empresa de Mantenimiento y Rehabilitación de Obras Hidráulicas (EMROH s.a), donde, según en diámetro y las presiones nominales de las tuberías (dN) y (PN) respectivamente, se ofrecen la presión de soldadura, el ancho del cordón, los tiempos de calentamiento, de enfriamiento, el total de soldadura y el total de soldaduras por hora.
La NC 969:13 ofrece criterios de aceptación visual basados en defectos tales como: grietas o rajaduras, desalineación entre las partes unidas por soldadura, rebarba de soldadura superficiales disparejas, rebarba de soldadura superficiales pequeñas, falta de fusión completa de la unión soldada en todo el perímetro, porosidad superficial inadecuada, que coinciden con las recomendadas por la norma DVS-2207-1 (2007), que remiten a la DVS 2201-1 (1989) donde aparecen las causas más frecuentes de dichos defectos.
En este trabajo se identifican los defectos más frecuentes observados en las juntas de tubos de PEAD en dos obras de la provincia de Camagüey y se determinan sus causas. Se comparan valores obtenidos de la presión manométrica de la tubería para diferentes tipos de equipos y con el empleo de diferentes normas. Se demuestra la necesidad del estudio y regulación de dichos parámetros a las condiciones ambientales específicas de Cuba considerando las características de los tubos de PEAD de producción nacional y se relacionan las principales violaciones identificadas en los procesos de termofusión, todo lo cual pone en riesgo la integridad de las juntas.
Evaluación de la calidad de las juntas soldadas por termofusión a tope
Fusión a tope
La fusión a tope consiste en calentar los bordes cortados a escuadra de dos tuberías, una tubería y un accesorio, o dos accesorios, sosteniéndolos contra una plancha calentadora, se retira la plancha cuando se obtiene el derretimiento adecuado, se unen rápidamente los dos extremos y se deja enfriar la unión manteniendo mientras tanto la fuerza aplicada correspondiente ASTM-F2620-13 (2014).
Defectos de soldadura
Variaciones de la calidad o discontinuidad en la unión soldada (NC 969: 2013).
Tamaño mínimo del cordón despúes del calentamiento
Es el valor mínimo del cordón que debe alcanzarse después de completar el tiempo de calentamiento (ISO 21 307:2017 (E))
Procedimiento para la evaluación de los defectos presentes en las juntas y sus causas
Fue elaborado un diagrama causa efecto donde se exponen causas y subcausas que provocan juntas defectuosas DVS 2201-1 (1989).
Se procesaron estadísticamente datos de 58 juntas soldadas a tope por termofusión y los defectos registrados en éstas en 2019, en las juntas de las tuberías de PEAD de la conductora Pontezuela, en 24 km de la conductora (41 juntas) y en nuevas instalaciones de una red en el reparto Modelo-Juanito-Imán en Camagüey (17 juntas) para determinar los principales defectos presentados.
Para eliminar ruidos, relacionados con el diámetro de las tuberías, el resto de los análisis se realizaron solo con los datos del registro de control de la obra “Pontezuela” de soldaduras realizadas con dos equipos diferentes, PT-1000 y TracStar-1200, porque algunos parámetros tales como: la temperatura del elemento calefactor, las presiones de calentamiento y de unión de los tubos, el tiempo de calentamiento dependen del grosor de las paredes de los tubos. Se empleó el programa STATGRAPHICS Centurion XVI. Se determinaron, por estadística descriptiva, los valores promedio , desviación estándar (σ), coeficiente de variación (CV), valores máximos (Máx) y mínimos (Mín).
La presión manométrica de la tubería, P1, se calculó con las ecuaciones 1 y 2 (ISO 21 307:2017, ASTM-2620-13 (2014)), recomendada para equipos hidráulicos de termofusión.
Donde:
P1 |
Presión manométrica, bar |
Pif |
Presión interfacial (MPa), se toma en dependencia de la norma |
As |
Es el área de la superficie interfacial, en mm2 |
Atep |
Es el área total del pistón, en mm2, suministrada por el fabricante del equipo de termofusión |
Parr |
Es la presión de arrastre de la máquina de fusión, bar |
Se compararon los valores de temperatura y presión empleados en el proceso de termofusión con los recomendados para la soldadura de una tubería de 800 mm de diámetro nominal con las máquinas PT-1000 y TracStar 1200, relacionando éstos con los defectos observados con mayor frecuencia.
Mediante un análisis de varianza (ANOVA simple) se comprobó, para las juntas soldadas con ambos equipos, si existía alguna dependencia entre los defectos y la presión manométrica.
Se usó el análisis multivariado para determinar si existía relación entre las temperaturas empleadas en cada etapa y la presión manométrica con las dimensiones obtenidas del cordón, para PT-1000.
Desarrollo
Análisis de la ocurrencia de defectos en las juntas y sus causas
El gráfico de Pareto (figura 1) muestra que los tres defectos más frecuentes: ancho excesivo del cordón doble (AECD), diferentes espesores del cordón doble (DECD) y desalineamiento, sobrepasan el 80 % de todos los desperfectos, ello indica que si se trabaja en su solución puede mejorarse la calidad, aunque deben rechazarse aquellas soldaduras que tengan defectos (NC 969: 2013; ASTM-F2620-13 (2014)). En las figuras 2, 3, 4 y 5 se pueden observar algunos de los efectos indicados.
A partir del diagrama de Pareto se organizan los defectos, causas y subcausas que provocan juntas defectuosas en un diagrama de Ishikawa (ver Figura 6). Las subcausas, en el caso de las dos más importantes ocurren por problemas de temperatura y presión, el desalineamiento por deficiente operación (Tariq et al. 2012; NC 969: 2013; ASTM-F2620-13 (2014); DVS 2201-1 (1989); Avrigean y Hunyadi 2014).
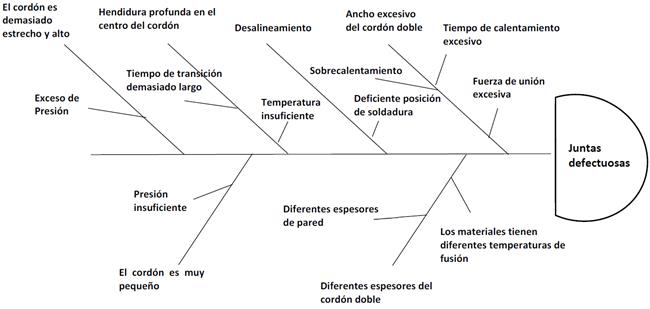
Figura 6 Causas que ocasionan defectos en las juntas por soldadura a tope por termofusión de tuberías de PEAD
Presiones manométricas determinadas
Las presiones manométricas se calcularon para los datos que se presentan en la tabla 1 para una tubería de PEAD, PN-6, SDR: 26.
Los soldadores utilizan una tabla “Parámetros de tiempos de soldadura a tope según el diámetro del tubo” (Empresa de Mantenimiento y Rehabilitación de Obras Hidráulicas (EMROH s.a)), donde los valores recomendados para la tubería antes mencionada se exponen en la tabla 2. En la tabla 3 se ofrece el tamaño mínimo de cordón recomendado para ese mismo tubo en otras normas, obsérvese la diferencia.
Se recomienda una presión interfacial de 0,41 a 0,62 MPa ASTM-F2620-13 (2014), dependiendo de los parámetros asumidos, a partir de lo recomendado por los fabricantes y las normas internacionales, se obtendrán valores diferentes, en este caso el valor de la empleada en las obras para el cálculo de la manométrica, como se muestra en la tabla 1, es de 0,517 MPa, más cercana a la recomendada por ASTM D- 26577.
Tabla 1 Datos empleados para el cálculo de las presiones manométricas
dn (mm) | DI (mm) | en (mm) | Pif(MPa) | Atep (cm2) | |
PT- 1000 | TracStar 1200 | ||||
800 | 738,4 | 30,77 | 0,517 | 41, 20 | 202,7 |
Tabla 2 Parámetros de tiempos de soldadura a tope para tubo de PEAD, (EMROH s.a)
dN/PN/SDR | P1 (MPa) | Cordón (mm) | Tiempo de calentamiento (min) | Tiempo de enfriamiento (min) | Tiempo total de la soldadura (min) |
---|---|---|---|---|---|
800/6/26 | 5,02 | 4,6 | 4,8 | 37 | 41,8 |
*SDR: Relación entre el diámetro del tubo y el espesor de la pared (NC 969:2013)
Tabla 3 Tamaño mínimo de cordón para las juntas del diámetro de tubo evaluado
dN (mm) | 800 | Referencia |
---|---|---|
Tamaño de cordón mín. (mm) | 11 | ASTM-F2620-13 (2014) |
5,59 | (ISO 21307: 2017 (E)) |
Tiempos de soldadura recomendados
Los tiempos que recomiendan para la tubería dN 800 mm (tabla 4), son para un espesor de 30,77 mm, la tubería cubana tiene un espesor de 30,6 mm, como mínimo (NC 969:2013).
Según la norma DVS 2207-1 (2007) el tiempo t1 es de 10 s para tuberías de 355 mm y más de 2 min para tuberías de 900 mm o más, muy inferior a la recomendada por los fabricantes. La (EMROH s.a) aconseja 4,8 min.
Tabla 4 Tiempos recomendados para las etapas de termofusión a tope para tubos de dN 800 mm, PN 6
Equipos | t1 (min) | t2 (min) | t3 (min) | t4 (min) | t5 (min) | tTOTAL (min) |
---|---|---|---|---|---|---|
PT-1000 | 3,59 | 5,641 | 0,118 | 0,238 | 33,77 | 43,36 |
TracStar-1200 | 3,59 | 6,12 | 0,120 | 0,24 | 33,60 | 43,75 |
DVS 2207-1 | 1,75 | 5,4 | 0,33 | 13,2 | 30 | 50,68 |
ISO | 6,12 | 13,2 |
Donde:
t1 |
es el tiempo para la formación del cordón inicial |
t2 |
es el tiempo de calentamiento |
t3 |
es el tiempo de retirar la placa |
t4 |
es el tiempo para alcanzar la presión de soldadura |
t5 |
es el tiempo de enfriamiento |
La temperatura empleada para soldar es de 210 0C.
Cálculo de la presión manométrica
Se calculó la presión manométrica P1, por las ecuaciones (1) y (2) para PT-1000, usando los valores recomendados por DVS 2207-1 (2007), los resultados se ofrecen en la tabla 5, obsérvese la diferencia entre las presiones manométricas obtenidas, entre sí y con la recomendada por la (EMROH s.a).
Tabla 5 Presión manométrica calculada según otras normas
Norma | Pif (MPa) | P1 (MPa) |
---|---|---|
D.V.S 2207-1 | 0,15 | 2,09 |
ASTM D- 26577 | 0,52 | 9,54 |
Análisis de los parámetros de presión y tiempo de soldadura empleados con los equipos
Con PT-1000
Al procesar los datos del registro de control de las soldaduras de tubos de dN 800 mm, PN 6 en la construcción de la conductora “Pontezuela” se obtuvo, que al soldar con el equipo PT-1000 la presión manométrica aplicada fue variable, entre 18 y 72 bar (1,8 -7,2 MPa), la promedio fue de 5,5 MPa; la de arrastre promedio fue de 1,97 MPa, con valores entre 0,7 y 3,2 MPa. Los tiempos promedio t1 y t2 fueron de 4,44 min y 6,53 min respectivamente. Los tiempos t3, t4 y t5 fueron de 0,107 min, 0,241 min y 33,58 min respectivamente. El tiempo total fue de 44,84 min (ver tablas 5 y 6).
Tabla 6 Presiones de arrastre y manométricas, en bar, aplicadas con dos equipos en la soldadura a tope por termofusión en la obra “Pontezuela”
Equipo | N | Pa | P1 | ||||||||
---|---|---|---|---|---|---|---|---|---|---|---|
|
σ | CV (%) | Mín | Máx |
|
σ | CV ( %) | Mín | Máx | ||
PT-1000 | 26 | 19,77 | 7,76 | 39,27 | 7 | 32 | 55,38 | 21,82 | 39,40 | 18 | 72 |
TracStar 1200 | 15 | 17,73 | 1,39 | 7,82 | 16 | 21 | 50,95 | 1,02 | 2,00 | 49 | 52 |
Con TracStar-1200
Al soldar con el equipo TracStar-1200 la presión manométrica aplicada fue variable, entre 49 y 52 bar (4,9-5,2 MPa), la promedio fue de 5,01 MPa; la de arrastre de 1,77 MPa, con valores entre 1,6 y 2,1 MPa. Los tiempos promedio t1 y t2 fueron de 4,2 min y 4,8 min respectivamente. Los tiempos t3, t4 y t5 fueron de 0,1 min, 0,22 min y 37 min respectivamente. El tiempo total fue de 46,32 min (ver tablas 6 y 7).
Parámetros de soldadura a los que se observaron defectos
Como los parámetros que más inciden en los defectos, con excepción del desalineamiento, son la temperatura, la presión manométrica y los tiempos de formación del cordón y de calentamiento, se analizó a qué valores de éstos se presentaron.
Valores de presión manométrica a los que aparecieron defectos al realizarse la soldadura a tope por termofusión
En la figura 7 puede observarse que al soldar con la máquina PT-1000 no apareció ningún defecto cuando se aplicaron presiones manométricas entre 24 y 32 bar (2,4 MPa y 3,2 MPa). Los más frecuentes surgieron a presiones entre 68 y 72 bar (6,8 MPa y 7,2 MPa), cayó también dentro de ese intervalo el defecto cordón demasiado estrecho y alto, que se presentó cuando se aplicó una presión de 7 MPa. Cuando se usó una presión de 1,8 MPa se obtuvo un cordón muy pequeño.

Figura 7 Presiones manométricas a las que aparecen los distintos defectos cuando se hicieron las juntas soldadas con la máquina PT-1000
En el registro de control de las juntas soldadas con el equipo TracStar-1200 todas presentaron algún defecto, algunas más de uno. Los tiempos aplicados fueron los mismos en todos los casos, según los reportes.
Es evidente, ver figura 8, que hubo un mejor control de la presión aplicada con la máquina TracStar-1200, la presión manométrica promedio aplicada fue de 51 bar (5,1 MPa), los defectos apreciados aparecieron a presiones 50 ≤ P 1 ≤ 52 bar (5,0 MPa - 5,2 MPa).
La presión manométrica aplicada recomendada por la (EMROH s.a), de 5,02 MPa, fue superada por ambos equipos, entiéndase soldadores, principalmente por el de PT-1000. Con TracStar-1200 es más cercana; sin embargo, los defectos AECD, DECD y CDEA aparecen a partir de 6,8 MPa cuando se operó con el primer equipo (ver figura 3) y a partir de 5,0 MPa cuando se trabajó con el segundo donde se apreciaron AECD y DECD (ver figura 4), esto pudiera deberse también a un sobrecalentamiento ASTM-F2620-13 (2014), 200-2200C (DVS 2207-1 (2007)), 215 ± 150C (ISO 21307: 2017 (E)). CMP se observó a una presión de 1,8 MPa, muy por debajo de la adecuada, al soldar con PT-1000.
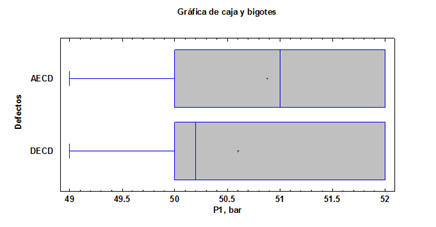
Figura 8 Defectos registrados a las presiones manométricas empleadas para soldar con el equipo TracStar-1200
El ancho excesivo del cordón doble, considerado como defecto en las inspecciones, no aparece entre los reconocidos en las normas, sin embargo, el exceder al recomendado es un indicador de aplicación de excesiva fuerza, lo cual se comprobó en el caso de PT-1000, también que se excede el tiempo de calentamiento. Si los componentes se unen con demasiada fuerza, el material derretido puede ser desplazado fuera de la unión y hacer que entre en contacto material frío, formando una unión “fría” ASTM F-2620-13 (2014). Se ha demostrado que durante el proceso de soldadura ocurre una reestructuración de las fases cristalinas, lo que conduce a mejores propiedades mecánicas y técnicas. Después de un año se produce una relajación, tanto en la fase amorfa como en la cristalina y la cristalinidad se ve seriamente afectada por la presión de soldadura (Santonocito et al. 2021).
Los diferentes espesores de pared en el cordón de soldadura se deben a un exceso de presión, de tiempo de calentamiento y de temperatura (Tariq et al. 2012).
En la tabla usada para los trabajos de soldadura en obras (EMROH s.a) sólo se hace referencia a la presión de soldadura, sin embargo, después de formado el cordón inicial se continúa el calentamiento a una presión menor (Zhao et al. 1998).
Evaluación de la temperatura empleada para soldar
La temperatura empleada para soldar es de 2100C, adecuada, de 2040C a 2320C según ASTM-F2620-13 (2014), 200-2200C (DVS 2207-1 (2007)), 215±150C (ISO 21307: 2017 (E)), pero si se compara con la recomendada, específicamente para el espesor mínimo de pared de 30,6 mm, de 2020C, para el máximo, de 33,8 mm se indica aun menor temperatura (DVS 2207-1 (2007)), resulta alta, considerando además las temperaturas ambientales de Cuba, esto contribuye, como se señaló antes, a que aparezcan diferentes espesores de pared en el cordón de soldadura.
Otro factor que incide en ese defecto es una característica inherente al material del tubo, que es el índice de fluidez, que es uno de los criterios que se tienen en cuenta al momento de realizar este tipo de soldaduras, debido a que define la compatibilidad de ésta cuando se hace entre tubos de polietileno fabricados con materiales de diferentes índices de fluidez (Pokharel et al. 2016). Se ha comprobado el agrietamiento por tensión a través de un proceso de crecimiento lento de grietas en la junta soldada de dos partes de PEAD con distintos índices de fluidez y luego su fallo ante una carga cíclica (Tariq et al. 2012). Los de manufactura cubana pueden diferir, aun cumpliendo con las normas establecidas, de los usados por los fabricantes de los equipos al recomendar presiones de soldadura y alturas de cordón. Para PE 100 debe ser de 0,2 a 1,4 g/10 min con una máxima desviación de ± 20 % a 1900C con una densidad de 930 kg/m3 a una temperatura de 230C (BS ISO 4427-1:2007), la NC 969:2013 establece para éstas tuberías, con 5 kg de 0,45 g/10 min con una densidad de 954 kg/m3 a una temperatura de 230C.
Determinación de los tiempos aplicados en las etapas del proceso de soldadura a los que aparecen los defectos
Defectos observados a los tiempos de formación del cordón inicial aplicados
Los principales defectos surgieron a t1 > 4 min. AECD se presentó a valores entre 4 ≥ t 1 ≤ 4,7 minutos mientras que DECD entre 4 ≥ t 1 ≤ 4,2, el resto de los defectos también aparecieron dentro del primer intervalo, pero a t 1 < 4,79 min (ver figura 9).
Defectos observados a los tiempos de calentamiento aplicados
Son muy variables los tiempos de calentamiento (t2) que se usaron al soldar con la máquina PT-1000; los principales defectos, AECD y DECD, se apreciaron al aplicar tiempos entre 6 y 7 min (6,5 min como promedio), sin embargo, no se encontró ningún defecto entre 6,1 y 6,25 min. El resto de los defectos aparecieron a 6,5 min CMP, que se corresponde con el promedio empleado, 6,8 min HPC y 7,1 min CDEA (ver figura 10).
Con PT-1000 se obtiene un ancho promedio del cordón de soldadura de 27 mm, con TracStar-1200 de 30 mm. Con el primer equipo hay mayor dispersión de esta característica, está entre 17 mm y 29 mm, con el segundo el valor se encuentra entre 28 mm y 31 mm, o sea, es mayor (ver figura 11).
Se realizó un análisis de varianza, comparando las medias de los defectos producidos a diferentes presiones en los equipos PT-100 y TracStar. Como se aprecia en la tabla 8, por el valor de la probabilidad, para el PT-100 hay diferencias significativas entre las presiones manométricas aplicadas por el equipo PT-1000, no así en el caso de TrancStar-1200.
Tabla 8 Análisis de varianza simple, dependencia de los defectos relacionados con la presión aplicada por equipo
Equipo | Probabilidad |
---|---|
PT-1000 | 0,0000 |
TracStar-1200 | 0,9369 |
Observaciones realizadas en las obras
En las inspecciones realizadas a las obras durante su ejecución fueron detectadas algunas violaciones en el procedimiento, ellas son: Soldaduras realizadas expuestas al medio, no se protegía la entrada de las tuberías, no se utilizaron los caballetes idóneos como soporte y guía de los tubos a soldar, en su lugar se emplean tramos de tubos mal formados; no se contó con pirómetro u otro dispositivo medidor de temperatura superficial antes de realizar la primera unión del día y periódicamente a lo largo del día; en el banco de soldadura generalmente usaban una sola mordaza para la realización de ésta; poca experiencia y capacitación del operador de la PT-1000, requisito establecido para la actividad; el equipo PT-1000 presentaba problemas con el mando de control eléctrico.
En la figura 12 se pueden apreciar condiciones inapropiadas para la realización de las soldaduras.
Observaciones en el modelo de control
En los registros de control se reflejó lo siguiente:
PT-1000: En dos reportes señalan que la temperatura del equipo se obtiene por experiencia porque el banco con que están soldando no tiene registrador de temperatura.
PT-1000: En tres reportes indican que detectaron por muestreo en la tubería diferentes espesores, que oscilan entre 30,6 a 37 mm.
En los modelos de control no se registra el espesor de pared y este puede variar, según NC 969:2013, e influir en los resultados obtenidos, porque la presión de arrastre depende de esa característica (ver ecuación 2). Si asumen la presión de soldadura indicada en la Tabla (EMROH s.a) o en cualquier otro documento es imposible, con espesores variables, obtener un ancho de cordón uniforme, se recomienda consultar a los fabricantes al respecto ASTM F-2620-13 (2014). Se requiere medir el espesor y calcular la presión de arrastre, la cual, en este caso se acercó más a la correspondiente al mínimo espesor de 30,6 mm (NC 969:2013), para el tipo de tubería analizada en este trabajo la misma norma ofrece un espesor máximo de 33,8 mm y en el manual del equipo TracStar-1200, por ejemplo, los dan para un espesor de 30,77 mm. Fueron reportados espesores de tubería de 30,6 a 37 mm, sin embargo, para dN 800 mm, PN 6 SDR 26 el espesor mínimo es de 30,6 mm y el máximo de 33,8 mm, pudieran haber sido de mayor presión nominal (NC 969:2013).
La temperatura para soldar debe ajustarse a las condiciones climáticas de Cuba y a las características de los tubos de producción nacional. La inexistencia de un pirómetro puede también haber afectado, esto impide garantizar que se alcance la temperatura adecuada en las placas calentadoras como se pide (NC 969:2013, DVS 2207-1 (2007), ASTM F-2620-13 (2014)).
Las condiciones inapropiadas observadas en el proceso de soldadura a tope, específicamente en el soporte y fijación, son las responsables del desalineamiento en las juntas (NC 969:2013, DVS 2207-1 (2007), ASTM F-2620-13 (2014)). Otras como la poca experiencia y capacitación del operador de la PT-1000 y los problemas con el mando del control eléctrico de dicho equipo explican la variabilidad de los resultados obtenidos (DVS 2207-1 (2007); NC 969:2013; ASTM F-2620-13 (2014)).
Las exposiciones directas al medio de las soldaduras propician la contaminación de las juntas con partículas lo cual compromete su integridad sin poder muchas veces apreciarse por control visual (Pyeong et al. 2022).
Para evitar el efecto chimenea en diámetros grandes, que se produce al entrar corrientes de aire por una boca del tubo, se deben tapar ambos extremos de los conductos a soldar hasta concluir la etapa de unión-enfriamiento, luego deben removerse las cubiertas para el proceso de enfriamiento de las juntas fusionadas (Zhao et al. 1998).
Si se excede el tiempo de enfriamiento antes de la fusión de las tuberías se producen defectos de fusión en frío en la unión lo que conduce a menor calidad de sus propiedades mecánicas y se afecta la vida útil de ésta, esto no puede apreciarse a simple vista (Pokharel et al. 2016).
Conclusiones
Los principales defectos detectados fueron un ancho excesivo del cordón doble, diferentes espesores del mismo y desalineamiento.
Las principales causas de la aparición de los defectos mostrados son: un exceso de presión manométrica, temperatura y tiempo de formación del cordón inicial aplicados.
Se asumen valores de presión interfacial que pudieran no corresponderse con las características de los tubos de PEAD de producción nacional y sin considerar los diferentes espesores de pared de tubos del mismo diámetro.
Se violan requisitos exigidos por las normas, en el entrenamiento de los operadores, la disponibilidad de instrumentos y accesorios para asegurar la calidad de las juntas soldadas.
Existen condiciones para la existencia de soldaduras en frío, contaminación de las juntas que comprometen su integridad y no se aprecian a simple vista.