Introducción
La dependencia de la energía hacia los combustibles fósiles, hacen necesaria la búsqueda de otras fuentes de energéticas que sean respetuosas con el medio ambiente. La sociedad actual presenta problemas de un elevado consumo energético que principalmente depende de los recursos fósiles [1]. En ese sentido, desde hace algunos años se está investigando el desarrollo de tecnologías a partir de fuentes y recursos renovables [2, 3, 4], como la biomasa lignocelulósica o la energía eólica, solar o geotérmica. La biomasa aprovechadaproviene de residuos combustibles, especialmente los de actividades agrícolas, forestales y agroindustriales. Según Nogales [5], el consumo energético mundial de la biomasa representa entre el 8 % y 14 %, siendo más notable en países en desarrollo donde se ubica en un 80 %.
La biomasa lignocelulósica se genera en el proceso de fotosíntesis, donde se combinan CO2 y H2O en presencia de luz solar,lo que da origen a productos primarios como azúcares y a O2 como subproductos. Esta biomasa está compuesta principalmente porcelulosa (38 % a 50 %), hemicelulosa(23 % a 32 %) y lignina (15 % a 25 %) [1]. Su combustión genera emisiones de dióxido de carbono (CO2), dióxido de nitrógeno (NO2) y monóxido de carbono (CO)los cualesafectan la capa de ozono, incrementan el efecto invernadero y acrecentando el calentamiento global. Se ha encontrado que la concentración media anual mundial de CO2 alcanzó 407,8 ppm en el 2018, en comparación con los 405,5 ppm registrados en el 2017 [6]. Esta realidad obliga a llevar a cabo estudios sobre fuentes energéticas y la aplicación de tecnologías que reduzcan las emisiones que pueden generar la biomasa utilizada como fuente energética.
Las principales fuentes para la producción de biocombustibles son, por tanto, materiales lignocelulósicos, como residuos de maderas y arbustos. En esa dirección, en Perú existe una alta dependencia de biomasa agraria para cocción y calor en el área rural, lo cual está asociado al empleo ineficiente y la deforestación [7]. En el caso de la región deTacna,es notable la producción de biomasa procedente del cultivo de olivos,ya que es la zona de producción por excelencia. En comparación al resto del país, Tacna produce el 80 % de las aceitunas, que son el fruto comestible del olivo. En contraparte, como producto del proceso de obtención del aceite, las aceituna y sus derivados, se generanresiduos llamados orujo y pepas,de tal forma que el manejo de estos residuos supone un problema para los productores debido a su poder contaminante, así como por el costo que implica su tratamiento.
Además, las labores culturales del olivo también generan residuos de podas, que en algunos casos se depositan en el campo como cercos y otras veces se utiliza como leña para cocinar,lo que representa un potencial contaminante y una baja eficiencia energética. Una forma adecuada de aprovechar esta biomasa residual es fabricarbriquetas que pueden ser una alterativa energética para sustituir el carbón vegetal y a la leña. Las primeras contribuyen a reducir las emisiones de gases de efecto invernadero (GEI), mientras que las segundas ayudan a evitar la deforestación y a mejorar el rendimiento energético [8]. Esto se debe a es conocido que uno de los problemas de utilizar la leña como combustible es su baja eficiencia calórica. Por estarazón,se requieren grandes cantidades de leña para generar energía, mientras que las briquetas presentan una ventaja frente al uso de leña, ya que reducen la generación de CO2en un 50 %, así como presentan concentraciones bajas de azufre (S), nitrógeno (N) y GEI, los cuales impactan en el medio ambiente [9].
Se han realizado algunas investigaciones para obtener briquetas a partir de biomasa residual [10, 11], utilizando subproductos que contienen compuestos lignocelulósicos y materiales biológicos aglutinados con varios compuestos, como gomas de carpintero y almidón. Estas investigaciones han determinado características físicas y químicas, como la friabilidad, densificación, poder calorífico. Sin embargo,son escasos los estudios que evidencien la generación de gases. Nogales [5], indica que el uso de la biomasa del orujo como fuente energética puede generar emisiones contaminantes, especialmente debido a que el material contiene compuestos oleoresinosos que generan una mayor cantidad de compuestos orgánicos volátiles, como el CO2 y el CO.En ese sentido, la reducción de emisiones debido a las características del material podría mejorarse con un pretratamiento que consiste en el lavado mecánico para disminuir los compuestos mencionados, lo que podría contribuir en la reducción de las emisiones.
Con base a las consideraciones anteriores, el objetivo de la investigación es evaluar el nivel de emisiones de CO2 y CO, así como del poder calorífico de las briquetas elaboradas a partir de los residuos del olivar que incluyen los residuos de poda, las pepas de aceituna, así como el orujo lavado (L) y sin lavar (SL), con el propósito de determinar los efectos del pretratamiento sobre los parámetros evaluados.
Materiales y métodos
Determinación de poder calorífico
La fabricación de las briquetas se realizó empleando las pepas y orujo de aceituna junto con las podas de olivo.Los dos primeros se obtuvieron de una empresa local dedicada al proceso de trasformación de las aceitunas, mientras que las podas se acopiaron de un fundo ubicado en la zona productora de olivos en la zona conocida como La Yarada (18°17′08″S 70°26′20″O). Inicialmente, las podas se redujeron de tamaño con un cepillo eléctrico de 750 W, luego se trituraron en un molino de martillos de 60 HP.De manera similar, el orujo y la pepa de aceituna se trituraron en el mismo molino.
Posteriormente,se tamizó toda la biomasa utilizando una malla equivalente a 10 mesh. El pretratamientose realizó mediante un lavado mecánico durante un tiempo de 3 horas con agitación constante.Esta operación se repitió tres veces, utilizando una muestra de 200 g en 1 L de agua. Las briquetas se formaron en un equipo específico para tal propósito,accionado con una prensa hidráulica.La cantidad de mezcla por briquetas fue 200 gr y se aplicó una presión de 102 kgf/cm2, obteniéndose piezas con un diámetro de11 cm y una altura de 10 cm. El diseño estadístico empleado fue completamente al azar, con cuatro repeticiones.
Los tratamientos se formularon con diferentes proporciones de los componentes, que se mezclaron de la siguiente manera: T1: 5 % de pepa + 5 % de Orujo + 70 % de poda, T2: 10 % de pepa + 5 % de Orujo + 80 % de poda, T3: 5 % de pepa + 10 % de Orujo + 80 % de poda, T4: 10 % de pepa + 10 % de Orujo + 70 % de poda.Adicionalmente se utilizó 15 % almidón de papa como aglutinante en forma de engrudo para todos los tratamientos.
Para determinar el poder calorífico, se realizó por análisis inmediatode acuerdo con la ecuación de Goutal [12].El poder calorífico se calculó como el poder calorífico superior, que es la cantidad total de calor desprendido en la combustión completa por unidad de volumen de combustible cuando el vapor de agua está condensado, para ello se tuvieron en cuenta el porcentaje de humedad, materiales volátiles, cenizas y carbono fijo en base seca, según la ecuación (1).
Donde
Cf |
contenido de carbono fijo (%) |
V |
contenido de materia volátil (%) |
A |
coeficiente obtenido de la relación siguiente: A = V/ (V+C) |
V |
contenido de materia volátil (%) |
C |
contenido de cenizas (%) |
El Carbono Fijo se determinó de acuerdo a la norma ASTM D - 3172 empleando la ecuación (2):
El cálculo delmaterial volátil se realizó de acuerdo con la norma ASTM D - 1762 S. se pesaron 2 g de muestra que fueron acondicionados en un crisol y se colocaron en la entrada de una mufla a una temperatura de 950 °C y se dejó por 7 min. Posteriormente, se enfrió en una desecadora durante 25 min, registrando los pesos obtenidos. Finalmente, se aplicó la siguiente ecuación (3):
Donde:
Pi |
peso inicial de la muestra de carbón (g) |
Pf |
peso final de la muestra (g) |
H |
contenido de humedad (%) |
Las cenizasse determinaron pesando 2 g de muestra carbonizada en una cápsula de porcelana, la cual fue sometida a la mufla a 450 °C por 2 h hasta lograr su incineración total. Luego, se colocó en la desecadora por 30 min. El contenido de ceniza se determina utilizando la ecuación (4):
La humedad se determinó pesando 10 g de muestra y luego secándola en una estufa a 103 °C hasta obtener un peso constante, posteriormente, se pesó la muestra final. El porcentaje de humedad se calcula utilizando la ecuación (5):
Determinación de emisiones de CO2 y CO
Para evaluar las emisiones de monóxido de carbono (CO), se midieron utilizando un sensor MQ-7 marcaHanweiElectronics, con un rango de medición 20 a 2000 ppm. Por otro lado, las mediciones deCO2se realizaron utilizandoun módulo adaptado con un sensor de calidad de aire BME 680 de la marca Bosch con rango de emisión de 0 a 9999 ppm. Las mediciones se llevaron a cabo siguiendo el procedimiento descrito por Bastidas-Barranco [8] por triplicado. Para ello.Para ello,se llevó a cabo la combustión de 20 g de muestras de briqueta por cada prueba [13].
Resultados y discusión
Emisiones de CO y CO2
La evolución del nivel de emisiones de CO2generado durante la combustión de briquetas de residuos de olivar que contenían orujo de aceituna lavado y sin lavar se muestra en la figura 1. La evolución de las emisiones de CO en ambos tipos de tratamientos es similar al inicio y durante la combustión. Inicialmente, el nivel de emisiones fue en promedio 420 ppm, luego comenzó a incrementarse hasta el tercer minuto, alcanzando valores máximos de 9964,82 ppm y 9929,71 ppm en el T2 que contenía orujo lavado (T2L) y sin lavar (T2SL) respectivamente. A medida que la combustión avanzaba, se observó que los valores disminuyeronhasta un mínimo de 412 ppm.
Las formas de las curvas fueronsimilares en todos los tratamientos,diferenciándose enlos valores máximos. La divergencia entre estos valores estaría relacionadacon la variación en la composición; en los tratamientos donde la proporcióndel orujo y el pepa de aceituna era mayor (T2 y T4), se observaronniveles más altos de CO2, a diferencia de los demás tratamientos. Por lo tanto, la evolución de las emisiones por tratamiento, considerando la adición de orujo lavado (L) y sin lavar (SL), mostró claramente que no existen diferencias. Al respecto, en una investigación realizada porNogales [5], al comparar este tipo de emisiones en orujo de aceituna lavada y sin lavar, se encontraron reducciones moderadas en las emisiones de CO2.
También conviene destacar que la media geométrica de CO2(1390 ppm) es ligeramente inferior a la determinada en carbón vegetal (1432ppm), aunque superior en el caso de briquetas de hueso de palta (480 ppm) [14]. En esa línea, algunos autores [15, 16], también coincidenen que las briquetas elaboradas a partir de biomasa generan emisiones más bajas que el carbón.
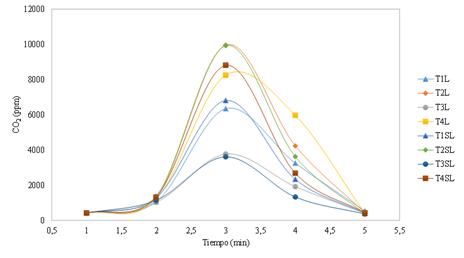
Fig. 1 Influencia del orujo lavado (T1L, T2L, T3L, T4L) y orujo sin lavar (T1SL, T2SL, T3SL, T4SL) en el nivel de emisiones de CO2 según tratamientos en briquetas de residuos del olivar
Patrones ligeramente diferentes se encontraron en la evolución del CO (véase figura 2), no obstante, se identificó que al inicio los valores fueron bajos con una media de 7,17 ppm, alcanzado promedios máximos de 13,70 ppm. Al finalizar, los 3 min, después de 5 min, las emisiones promedio fueron de 4 ppm.A diferencia del CO2, el CO se genera con mayor velocidad en las briquetas de residuos del olivar debido a la liberación de compuestos volátiles, principalmente contenido en el orujo de aceituna. Aunqueno existe un patrón definido, se observa que los tratamientos que contenían orujo sin lavar (T1SL, T3SL, T4SL) presentaron valores más altos en comparación con los tratamientos similares que contenían orujo lavado. Sin embargo, dichas diferencias no serían estadísticamente significativas.
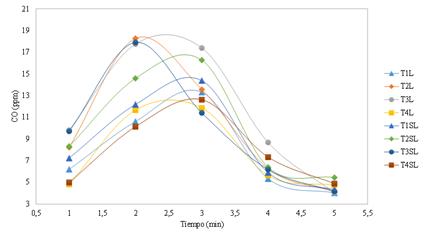
Fig. 2 Influencia del orujo lavado (T1L, T2L, T3L, T4L) y orujo sin lavar (T1SL, T2SL, T3SL, T4SL) en el nivel de emisiones de CO según tratamientos en briquetas de residuos del olivar
La relación entre CO / CO2es un indicador de combustión, tal como afirma Bastidas-Barranco [8]. El CO procede de una combustión incompleta, lo cual reduce el poder calorífico y disminuye el rendimiento de la combustión. Es altamente toxico, ya que al ser inhalado se combina en la hemoglobina, inhibiendo la absorcióndel oxígeno necesario. Por otro lado, el CO2 no es un gas tóxico y se produce en el proceso de combustión.
En la figura 3, se observa que la relación entre CO/CO2es mayor en los tratamientos que contenían orujo sin lavar (T1SL, T2SL, T4SL), mientras que el tratamiento que contenía orujo lavado (T3L) mostró el valor medio más alto.Esto indica que durante el proceso de combustión de las briquetas compuestaspor10 % pepa de aceituna, 15 % de Orujo y 75 % de poda de olivose generan 0,0097 ppm de CO por cada ppm de CO2. Por lo tanto, como señala Bastidas-Barranco [8], existen factores de diseño de las briquetas que dificultan su combustión completa, lo cual puede ser mejorado, entre otros, mediante el control del flujo de aire y confinamiento de gases calientes.

Fig. 3 Relación de emisiones de CO/CO2 (ppm/ppm) para briquetas de residuos de olivar.Las medias entre pares de tratamientos con adición de orujo lavado (10 % pepa de aceituna+15 % de Orujo+75 % de poda de olivoL) y orujo sin lavado (SL) no difieren entre sí al 5 % de significancia por la prueba de Tukey
Poder calorífico
Según se observa en la tabla 1, los resultados del análisis de varianza indicaron diferencias significativas (p < 0,05) únicamente en el tratamiento formulado con un 10 % de pepa de aceituna, un 15 % de Orujo y un 75 % de poda de olivo (T3), donde el segundo componente (orujo) se encontraba tanto lavado como sin lavar. Estadísticamente, no se encontró influencia del lavado de orujo en el poder calorífico en los demás tratamientos. De manera similar, no se encontraron diferencias significativas al compararlos tratamientos que contenían orujo lavado (L) ni al comparar los tratamientos con orujo sin lavar (SL).
Sin embargo, a medida que se incrementaba la proporción de pepa de aceituna en la composición de las briquetas con orujo lavado (L) y sin lavar (SL), el potencial calorífico aumentaba, aunque no de manera significativa (p > 0,05). Por otro lado, los tratamientos que contenían orujo sin lavar (SL) sí mostraron diferencias según la prueba de Tukey, En ambos casos, el tratamiento T4 presentó el mayor poder calorífico (5924,33 ± 283,55 kcal/kg), seguido en orden decreciente por los tratamientos T2, T1 Y T3,respectivamente. Es importante subrayar que el poder calorífico en todos los tratamientos es considerablemente superior al mínimo establecido por la NTC 2060 para briquetas que no sean fabricadas con carbón, el cual es de 2 987,57 kcal/kg (12 500 kJ/kg), así como a los valores exigidos por las normas alemanasDIN-51731/Plus y austriacas ONORM M7135, que establecen valores mayores a 4299,23 kcal/kg [17].
De forma similar,al compararlos con otros tipos de briquetas fabricadas con coco, carbón cascarilla y aglomerante (4071,13 kcal/kg) [18], tronco y hojas de Ulexeuropaeus(4590,04 kcal/kg) [19], así como aserrín y corteza de pino (4 200 kcal/kg) [20], se puede observar que el poder calorífico de las briquetas fabricadas con residuos del olivar muestra gran potencial energético para ser usado como biocombustible, en comparación con el potencial que poseen otros materiales similares, incluso al compararlo con el poder calorífico de los residuos leñosos del olivo (4600 kcal/kg). Estas briquetas presentan un poder calorífico mínimo un 16% superior y cercano al 80 % del poder calorífico del carbón vegetal, el cual teóricamente se encuentra en el orden de los 7000 kcal/kg dependiendo del material utilizado.
Tabla 1 Poder calorífico (kcal/kg) de briquetas de residuos de olivar según tratamientos con adición de orujo lavado (L) y orujo sin lavado (SL).
Tratamientos | L ( X̅ + SD) | SL ( X̅ + SD) | Diferencias (L - SL) |
---|---|---|---|
10 % pepa de aceituna+10 % de Orujo(L/SL)+80 % de poda de olivo (T1) | 5686,62±285,35 | 5693,61±283,83a | -6,99 |
15 % pepa de aceituna+10 % de Orujo(L/SL)+75 % de poda de olivo (T2) | 5917,26±212,80 | 5919,45±211,29ab | -2,19 |
10 % pepa de aceituna+15 % de Orujo(L/SL)+75 % de poda de olivo (T3) | 5496,62±2,01 | 5502,22±52,31b | -5,60* |
15 % pepa de aceituna+15 % de Orujo(L/SL)+70 % de poda de olivo (T4) | 5924,33±283,55 | 5926,88±283,67b | -2,54 |
En la tabla:
X̅ representa la media de los tratamientos, SD indica la desviación estándar. Las letras a y b representan diferencias significativas entre los tratamientos. Existe una diferencia significativa (*) en el tratamiento T4 con un nivel de significancia del 5% (p < 0,05).
Dado los hallazgos, sería relevante establecer nuevas formulaciones en futuras investigaciones con el fin de profundizar en las emisiones y optimizar el poder calorífico al aumentar el orujo de aceituna antes de realizar una afirmación concluyente. Esto se debe a que, en caso de un posible escalamiento industrial del producto, elpretratamiento podría generar un problema ambiental adicional relacionado con los residuos líquidos resultantes del lavado. Además, es importante estimar el costo-beneficio del proceso de fabricación en relación al poder calorífico obtenido.
Conclusiones
Las briquetas fabricadas a partir de residuos del olivar que contenían orujo lavado no presentaron diferencias significativas entre los tratamientos en cuanto al nivel de emisiones ni el poder calorífico. En consecuencia, el lavado de los orujos no influye sobre estos dos parámetros. Así mismo, el poder calorífico de todos los tratamientos mostró valores aceptables, que son muy superiores a las exigencias de algunas normativas, por lo tanto, los residuos del olivar tendrían el potencial para ser considerados como una fuente de energía alternativa.
Es necesario realizar investigaciones futuras que se enfoquen en nuevas formulaciones para profundizar en las emisiones y optimizar el poder calorífico, particularmente al aumentar la proporción de orujo de aceituna. Sin embargo, antes de realizar afirmaciones concluyentes, se deben considerar los posibles problemas ambientales asociados al pretratamiento, como la generación de residuos líquidos derivados del lavado. Además, es crucial estimar el beneficio costo del proceso de fabricación en relación con el poder calorífico obtenido, a fin de evaluar la viabilidad económica de la producción a gran escala de estas briquetas.