Introducción
El perfeccionamiento del proceso de extrusión de aleaciones de aluminio posibilitó la elaboración de perfiles normalizados de dimensiones largas y de secciones transversales exactas, siendo de gran interés para los sectores del transporte, aeroespacial, comunicación y en especial la construcción.
Kalpakjian [1], en el 2008 planteó que existían muchas cuestiones del diseño de las matrices de extrusión que están sin respuesta aún, a pesar de no ser un proceso respectivamente nuevo que se generalizó en la década de 1894. Aunque en los últimos años, ha aumentado el número de estudios relacionados con la evaluación del desgaste y la vida útil de los moldes metálicos, utilizando diferentes métodos y tecnologías, son escasas las investigaciones realizadas para la obtención del diseño de las matrices de extrusión, que vinculan los resultados de optimización con las variables de diseño aplicada en un sistema CAD. Ejemplo de estos se muestra a continuación.
En el año 2017 Chahare AS [2] utiliza el análisis de varianza para investigar el impacto de los parámetros del proceso en la angularidad de los elementos. A través del análisis obtuvo el nivel óptimo de los parámetros del proceso para una temperatura de precalentamiento de la palanquilla de 500 ºC, una temperatura del contenedor de 400 ºC y una velocidad del pistón de 6,0 mm/seg. Los autores también determinaron que la velocidad del ariete tiene la máxima contribución, con un 59,83 %, seguida de la temperatura del contenedor y la temperatura de precalentamiento de la palanquilla. Parte de estos resultados fueron utilizados en esta investigación.
En [3], Ramya et al. (2016) investiga sobre la predicción de la carga de extrusión, la influencia de la velocidad del pistón en los parámetros del proceso, la temperatura inicial del tocho, la sección transversal de la matriz y la tensión de extrusión. Estos autores, aunque trabajaron factores geométricos del proceso no incluyeron variables cómo el ángulo de entrada, canales de salida y el espesor de la matriz.
Engelhardt en el año 2019 [4], por su parte utilizó métodos de simulación para visualizar y optimizar el flujo de material durante la extrusión de un perfil de disipador de calor con una geometría compleja, demostrando con éxito que los métodos utilizados predicen el flujo de material y, por lo tanto, podrían simplificar el proceso de diseño de herramientas; pero no incluyeron en su investigación la influencia de la fuerza de extrusión.
Existen más ejemplos con resultados similares a los analizados. En todos estos estudios se percibe que prevalece poca información sobre el tema en el campo del diseño, dónde muchas particularidades y variables del proceso están siendo investigadas aún. El objetivo de la presente investigación fue optimizar el diseño de las matrices lineales de extrusión de perfiles de aleaciones de aluminio, a partir de la geometría y las dimensiones requeridas a obtener, con vista a aumentar la vida útil de estas costosas herramientas.
Métodos y Materiales
A partir de la optimización mono-objetivo de los parámetros fundamentales, la utilización de un diseño gráfico y la disponibilidad de los softwares Matlab y Autodesk Inventor, se logró el desarrollo del diseño óptimo de la matriz de extrusión y la selección del material.
Configuración geométrica y selección del material
El proceso de extrusión en caliente siempre conlleva a una disminución de las dimensiones del perfil una vez enfriado, debido a la contracción térmica del metal. En la figura 1, se expone la configuración del perfil que se desea obtener, con sus cotas correspondientes y su ubicación en la matriz. Se determinó que la producción sería en una matriz lineal donde se obtuviera un perfil de forma simultánea, debido a que el máximo radio circunscrito del perfil no debe exceder a 140 mm.
Los materiales para dados de extrusión en caliente incluyen aceros de herramienta y aceros aleados [5, 6]. Las propiedades más importantes de estos materiales son alta resistencia al desgaste, alta dureza en caliente y alta conductividad térmica para remover el calor del proceso. Después de valorar varios materiales para la fabricación de matrices y herramentales como los aceros H11, H12 y H13, se determinó utilizar el mostrado en la tabla 1, por su alta tenacidad al impacto y resistencia al desgaste a temperaturas elevadas.
Tabla 1 Material y propiedades del herramental de matricería. Fuente: [6]
Material | Dureza (HRC) | Densidad | Módulo elástico | Coeficiente de Poissons | |
---|---|---|---|---|---|
Matriz y Contramatriz | H13 | 47 - 51 | 7,8 g/cc | 210 GPa | 0,30 |
Modelo de optimización mono-objetivo para el diseño de las matrices de extrusión
El análisis de sistemas inicia con considerar las magnitudes de entrada y las magnitudes de salida, se establece los principales indicadores junto con las magnitudes que representan el estado interno del sistema [7, 8]
En el caso de la tarea de diseño de la matriz de extrusión de aluminio se establecen como variables de decisión (el coeficiente de fricción, el ángulo de la matriz y la deformación logarítmica) ya que pueden modificarse para encontrar una mejor relación que caracterice la calidad de las soluciones posibles del indicador de eficiencia (fuerza de extrusión), como manera de asegurar su cumplimiento. En la figura 2, se muestra el análisis externo del proceso.
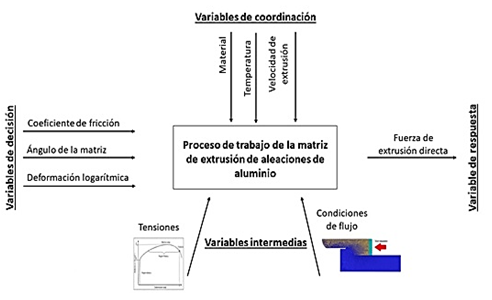
Fuente: autores
Fig. 2 Análisis externo del proceso de trabajo de la matriz de extrusión de aleaciones de aluminio.
Una vez realizado el análisis externo se procede a realizar el análisis interno del proceso de trabajo de la matriz. La ecuación (1), muestra el modelo matemático para determinar la fuerza total de extrusión, obtenido de la investigación realizada por [9].
Dónde:
Ftot: |
fuerza total de extrusión |
A0: |
área de la sección trasversal de la pieza de trabajo (tocho) |
l: |
largo de la pieza de trabajo (tocho) |
σf,m: |
tensión de flujo para un valor máximo de deformación logarítmica |
σf,0: |
tensión de flujo para un valor mínimo de deformación logarítmica |
â: |
es un valor estimado para el ángulo de la matriz |
µ: |
coeficiente de fricción |
φmax: |
deformación logarítmica máxima |
d0: |
diámetro inicial de la matriz |
El modelo se obtiene del análisis externo, que consiste en la determinación de los indicadores que caracterizan la calidad de las soluciones posibles de la tarea, la determinación de variables intermedias de interés y la estimación inicial de las variables de decisión, paso inicial para completar la descripción del proceso. En la tabla 2, se muestran los parámetros con los rangos estimados de restricciones para las variables de decisión.
Tabla 2 Rango de restricciones seleccionadas. Fuente: autores
Parámetros y restricciones | ||
---|---|---|
Deformación logarítmica (φ) | Coeficiente de fricción (µ) | Ángulo de la matriz (α) |
[0,3, 0,5, 0,7, 0,9] | [0,6, 0,8, 1, 1,2] | [18˚, 30˚, 42˚, 54˚] |
Ángulo óptimo de la matriz
Para determinar el ángulo óptimo de la matriz se utilizó la ecuación 2, obtenida por [10] y se estableció una relación de los parámetros geométricos con las restricciones estimadas del coeficiente de fricción y la deformación logarítmica. En la figura 3, se muestra los resultados obtenidos del análisis.
Ángulo óptimo de la matriz para valores mínimos de fuerza
Una vez especificados los ángulos óptimos de la matriz, se procede mediante la ecuación 3, obtenida de la investigación realizada por [11] a determinar el ángulo óptimo para los valores mínimos de fuerza. Los resultados obtenidos del análisis se muestran en la figura 4.
Tensión de flujo
La ecuación de Zener-Hollomon en tensiones simples, describe el efecto combinado de la velocidad de deformación y la temperatura sobre la tensión de flujo por deformación de los metales. La ecuación 4, precisa la tensión de flujo adaptada a este problema, utilizada por [12, 13], ecuación (4).
Resultados y Discusión
Análisis de los resultados de la optimización mono-objetivo y la simulación numérica
En la figura 3, se muestra el espacio de soluciones posibles para la selección del ángulo óptimo de la matriz.
En la figura 4, los valores obtenidos del ángulo óptimo para valores mínimos de fuerza.
En la figura 5, se describe la función de la tensión de flujo obtenida en MATLAB, para las restricciones de deformación logarítmica (φ) - [0,3, 0,5, 0,7, 0,9].
En las tablas 3 y 4, se muestran los valores óptimos de la Fuerza Total de Extrusión obtenidos mediante la optimización mono-objetivo, implementada en el software MATLAB para las prensas Shcloeman de 1600 Tn y Extral de 2500 Tn. Se creó una matriz de 4*4*4 que generó un total de 64 combinaciones. De manera metodológica se aplicaron las herramientas del software MATLAB para la optimización de la Fuerza Total de Extrusión. Se definieron las variables dependientes e independientes. En este caso las variables independientes se declararon como vectores fijos con los valores diferenciados que les correspondían. A partir de los valores que tomaron las variables se construyó una malla y sobre esa malla se declararon las formulaciones matemáticas.
Tablas 3 Valores óptimos de la Fuerza Total de Extrusión para la prensa Shcloeman. Fuente: autores
Fuerza Total de Extrusión (kN), prensa Shcloeman | |||||||||
---|---|---|---|---|---|---|---|---|---|
α= 18° | µ | α= 30° | µ | ||||||
φ | 0.6 | 0.8 | 1 | 1.2 | φ | 0,6 | 0,8 | 1 | 1,2 |
0,3 | 541,95 | 594,15 | 631,25 | 660,46 | 0,3 | 494,77 | 542,42 | 576,29 | 602,96 |
0,5 | 597,22 | 654,73 | 695,61 | 727,80 | 0,5 | 534,31 | 585,77 | 622,34 | 651,14 |
0,7 | 652,48 | 715,32 | 759,98 | 795,15 | 0,7 | 573,84 | 629,11 | 668,39 | 699,32 |
0,9 | 707,74 | 775,91 | 824,35 | 862,50 | 0,9 | 613,38 | 672,45 | 714,44 | 747,50 |
α= 42° | µ | α= 54° | µ | ||||||
φ | 0,6 | 0,8 | 1 | 1,2 | φ | 0,6 | 0,8 | 1 | 1,2 |
0,3 | 591,21 | 648,15 | 688,61 | 720,48 | 0,3 | 585,29 | 641,66 | 681,72 | 713,27 |
0,5 | 662,89 | 726,73 | 772,11 | 807,83 | 0,5 | 655,00 | 718,08 | 762,92 | 798,22 |
0,7 | 734,57 | 805,32 | 855,60 | 895,19 | 0,7 | 724,71 | 794,51 | 844,11 | 883,17 |
0,9 | 806,25 | 883,90 | 939,09 | 982,55 | 0,9 | 794,42 | 870,93 | 925,31 | 968,13 |
Tablas 4 Valores óptimos de la Fuerza Total de Extrusión para la prensa Extral. Fuente: autores
Fuerza Total de Extrusión (kN), prensa Extral | |||||||||
---|---|---|---|---|---|---|---|---|---|
α= 18° | µ | α= 30° | µ | ||||||
φ | 0,6 | 0,8 | 1 | 1,2 | φ | 0,6 | 0,8 | 1 | 1,2 |
0,3 | 920,7 | 1009,4 | 1072,4 | 1122,0 | 0,3 | 859,4 | 942,1 | 1000,9 | 1047,3 |
0,5 | 1020,1 | 1118,3 | 1188,2 | 1243,1 | 0,5 | 938,3 | 1028,6 | 1092,9 | 1143,4 |
0,7 | 1119,5 | 1227,3 | 1303,9 | 1364,2 | 0,7 | 1017,2 | 1115,2 | 1184,8 | 1239,6 |
0,9 | 1218,8 | 1336,2 | 1419,7 | 1485,3 | 0,9 | 1096,1 | 1201,7 | 1276,7 | 1335,8 |
α= 42° | µ | α= 54° | µ | ||||||
φ | 0,6 | 0,8 | 1 | 1,2 | φ | 0,6 | 0,8 | 1 | 1,2 |
0,3 | 984,8 | 1079,6 | 1147,0 | 1200,1 | 0,3 | 9771,0 | 1071,2 | 1138,1 | 1190,7 |
0,5 | 1105,5 | 1212,0 | 1287,6 | 1347,2 | 0,5 | 1095,2 | 1200,7 | 1275,7 | 1334,7 |
0,7 | 1226,2 | 1344,3 | 1428,3 | 1494,4 | 0,7 | 1213,4 | 1330,3 | 1413,3 | 1478,7 |
0,9 | 1347,0 | 1476,7 | 1568,9 | 1641,5 | 0,9 | 1331,6 | 1459,8 | 1551,0 | 1622,7 |
El diseñador puede seleccionar en dependencia de sus intereses, ya sea dando prioridad al indicador de eficiencia u otras variables de interés. En este caso se priorizó el indicador de eficiencia (Fuerza Total de Extrusión), para así disponer de un conjunto de soluciones óptimas para el diseño de la matriz.
Procedimiento para el diseño óptimo automatizado de matrices lineales de extrusión de aleaciones de aluminio
En la tabla 5, se muestra el procedimiento para el diseño óptimo de las matrices lineales de extrusión. Se basa en una secuencia definida, paso a paso, para realizar correctamente las tareas del diseño óptimo de las matrices lineales de extrusión.
Tabla 5 Procedimiento para el diseño óptimo de las matrices lineales. Fuente: autores
Modelación CAD de los elementos que componen el herramental de matricería
Una vez establecidos los resultados obtenidos mediante el modelo de optimización mono-objetivo del indicador de eficiencia, se procedió a realizar el diseño CAD de la matriz de extrusión de perfiles de aleaciones de aluminio para la obtención de perfiles machos, para la fabricación de formaletas. Se utilizó los valores óptimos de la deformación logarítmica y del ángulo óptimo para valores mínimos de fuerza obtenidos en la optimización.
Comparación con otros resultados publicados
A modo de comparación con los resultados analizados en la literatura, se puede mencionar que los ángulos óptimos reportados por Jurković Z. et al. [14, 15, 16], son menores que los obtenidos por estos autores.
Los resultados obtenidos pueden servir de referencia para cuando se realicen los estudios de desviación estándar de la velocidad y de la temperatura.
Los valores de tolerancias y de contracción térmica del aluminio son criterios utilizados según la literatura analizada, lo cual representa la principal limitación de nuestro trabajo.
Conclusiones
En el trabajo se obtuvo un procedimiento integrador para la obtención del diseño óptimo de las matrices lineales de extrusiones de aleaciones de aluminio. Se definieron los factores de mayor incidencia en el diseño y se expuso, a través de un modelo 3D, el diseño de la matriz para la obtención del perfil lateral macho de 100 mm a partir de la geometría y las dimensiones óptimas obtenidas.