INTRODUCCIÓN
Una práctica reconocida para enfrentar el desgaste es la aplicación de recubrimientos por soldadura sobre las superficies de trabajo. Con la utilización de estos procesos es factible la obtención de aleaciones con tanta o más durabilidad que las apreciadas en las piezas originales (Ortiz-Méndez, Cruz-Crespo y Espino-Rodríguez 2019; Cruz-Crespo et al. 2021).
Dentro de los procesos de recargue superficial por soldadura, la Soldadura Manual con Electrodo Revestido (SMAW, por sus siglas en inglés) constituye el de mayor uso por las ventajas que ofrece en cuanto a costo del equipamiento, posibilidad de aplicar en condiciones de campo o difícil acceso, y de utilizar en una amplia gama de composiciones de revestimientos, entre otras. El atractivo de este proceso en el recargue de componentes se enfatiza en países menos industrializados, donde la recuperación de piezas puede llegar a ser parte intrínseca de los sistemas de mantenimiento para alargar el ciclo de vida de los componentes, a tiempos incluso superiores a los nominales de diseño.
Los mecanismos de desgaste abrasivo y erosivo están presentes en un amplio espectro de aplicaciones. Son frecuentes en la manipulación y procesamiento de minerales y residuales, así como en equipos de bombeo, donde se trabaja con suspensiones abrasivas.
En el mercado se dispone de una amplia gama de consumibles que posibilitan enfrentar el desgaste abrasivo y erosivo. No obstante, la información que brindan los catálogos comerciales se limita a los aspectos generales para un rango de corriente, de acuerdo al diámetro del electrodo, y no se ofrecen informaciones de comportamiento que permitan la toma de decisiones de manera criterial para aplicaciones específicas. En esta dirección se dirigió el presente trabajo, cuyo objetivo fue establecer la influencia de la corriente de soldadura en el comportamiento metalúrgico (composición química y microestructura del metal depositado), de un electrodo comercial para recargue, destinado a soportar el desgaste abrasivo y erosivo.
MATERIALES Y MÉTODOS
Obtención de depósitos y preparación de muestras
En el proceso SMAW la velocidad de soldadura está asociada con la habilidad del soldador, y la tensión del arco (Ua) es dependiente de la corriente de soldadura (Is). Por ello, se tomó este último parámetro como variable de entrada para el estudio, manteniendo aproximadamente constante la velocidad de soldadura (Vs). En correspondencia con el diámetro de 3,2 mm del núcleo del electrodo, la corriente fue variada en un rango de 90 A a 130 A, con un valor medio de 110 A. Se utilizó corriente continua con polaridad inversa (CC+).
Los depósitos para determinar la dilución y análisis metalográfico fueron realizados sobre chapas de acero AISI 1020 de 200x75x8 mm. Previo a la deposición, los electrodos se calentaron en una estufa a 160 oC durante una hora.
El depósito (sin dilución) para análisis químico fue obtenido según lo recomendado por la norma AWS A5.13 (2000). Se utilizó la corriente media (110 A), realizando varias pasadas superpuestas sobre una chapa de 8 mm de acero AISI 1020.
Para obtener las probetas para geometría de los cordones y análisis metalográfico, los depósitos fueron cortados transversalmente en una tronzadora metalográfica. Se preparó también una muestra adicional del depósito sin dilución.
La geometría de los depósitos se determinó realizado un desbaste de acuerdo con la norma ASTM E3 (2011) hasta lija número 500, luego se realizó macroataque con nital al 3 %, en correspondencia con la norma ASTM E340 (2000).
Para el análisis metalográfico los depósitos previamente utilizados en la determinación de la geometría y la muestra del depósito sin dilución fueron pulidos con suspensión abrasiva de óxido de cromo, según la norma ASTM E3 (2011). A las muestras pulidas se les realizó ataque electrolítico con el reactivo 86, empleando una corriente de 100 mA y una tensión de 2 V, según la norma ASTM E407 (1999).
Determinación de composición química, geometría de los cordones y análisis metalográfico
La composición química media del depósito sin dilución se determinó en un equipo de Análisis Espectral de Emisión Atómica en la Empresa Planta Mecánica ¨Fabric Aguilar Noriega¨ de Villa Clara.
Para determinar los parámetros geométricos de los cordones se captaron imágenes con una escala de referencia. Las dimensiones lineales y las áreas de penetración y refuerzo de los cordones se midieron usando el programa ImageJ.
La adquisición de imágenes metalográficas se realizó en un microscopio óptico metalográfico marca NEOPHOT 32, con una cámara digital acoplada. Las imágenes fueron tomadas en el centro del área depositada.
RESULTADOS Y DISCUSIÓN
Comportamiento de la geometría de los depósitos en función de la corriente
Los parámetros geométricos de los depósitos determinados a partir de las macrografías con el empleo del programa ImageJ, así como el Coeficiente de Dilución (() ((=Ap/(Ap+Ar)(100) determinado en base a las áreas de penetración (Ap) y refuerzo (Ar) se muestran en la Tabla 1. Se advierte que con el aumento de la corriente aumenta la penetración del cordón de la corriente mínima para la corriente media, lo cual es esperado, ya que al aumentar la corriente aumenta la energía de entrada. El aumento posterior de la corriente de 110 A para la de 130 A, no manifiesta prácticamente variación de la penetración, lo que pudiera estar asociado a que ha ocurrido un aumento de la masa de metal depositado en la unidad de tiempo, limitando la incidencia directa del arco sobre el fondo de la posa de fusión. La disminución de la penetración con el aumento de la deposición corrobora resultados de trabajos previos (Cruz-Crespo, Scotti & Rodriguez-Perez 2008), (Tabla 1).
La Tabla 1 evidencia que el ancho del depósito, como era de esperar fue mayor según aumentó la corriente. En este caso, una mayor corriente de soldadura condiciona un aumento de la tensión del arco, y consecuentemente de su longitud, que hace que el cono se amplíe y con ello la isoterma de la línea de fusión. Al mismo tiempo, el aumento de la corriente y la tensión inciden con carácter creciente sobre la energía de entrada que se refleja en el área superficial (el ancho) de la posa de fusión, asociado esto también al crecimiento de la masa de metal que se deposita al elevarse la corriente.
Con el aumento de la corriente disminuye el refuerzo (Tabla 1), lo cual podría estar asociado a dos factores simultáneos que facilitan la distribución lateral del metal, vinculados a la energía de entrada: una mayor permanencia de la posa de fusión en estado fundido y un mayor sobrecalentamiento del metal, que hace disminuir la viscosidad. Adicionalmente, al aumentar la corriente la presión del arco sobre el metal fundido aumenta, favoreciendo su distribución lateral. Al aumentar la corriente, también lo hace el coeficiente de dilución (Tabla 1), lo que se asocia al aumento de la energía de entrada del proceso.
Comportamiento de la composición química de los depósitos en función de la corriente
La Tabla 2 muestra la composición química del depósito sin dilución, así como la obtenida en base a los valores de dilución para las diferentes corrientes, y la composición química sin dilución (, donde X es el contenido en por ciento del elemento en el depósito, XA y XB son los contenidos en por ciento del elemento en el material de aporte y en el metal base, respectivamente).
De acuerdo con los valores de los elementos de aleación en los depósitos, estos se corresponden a fundiciones blancas de alto cromo del sistema ternario Fe-Cr-C, las cuales clásicamente son empleadas en el enfrentamiento al desgaste abrasivo y erosivo según varios autores (Chung et al. 2011; Chatterjee & Pal 2003, 2006; Cruz-Crespo et al. 2021).
Se observó que con el aumento de la dilución, los contenidos de los elementos de aleación en el depósito disminuyen, lo que significa que hay un menor aprovechamiento del sistema de aleación del electrodo, lo cual evidentemente tiene reflejo en la microestructura del depósito y consecuentemente en su desempeño ante el desgaste.
Comportamiento de la microestructura de los depósitos en función de la corriente
La Figura 1 muestra las microfotografías del depósito sin dilución y de la zona central de los correspondientes a las tres corrientes empleadas. Los depósitos sin dilución y para la corriente de 90 A, que también experimenta muy poca dilución (Tabla 2), corresponden a una aleación hipereutéctica con presencia de grandes carburos primarios de morfología hexagonal en su sección transversal, característicos de carburos M7C3, rodeados de una matriz eutéctica de pequeños carburos M7C3 y austenita (Figuras 1a y 1b). Para el caso de la corriente de 110 A, la aleación presenta esporádicos pequeños carburos, rodeados de una matriz eutéctica que representa un alto porcentaje de la microestructura (Figura 1c). O sea, que en este caso la aleación es aun hipereutéctica pero se ubica en la vecindad de la región eutéctica. Para la corriente de 130 A (Figura 1d), se observa una microestructura con alto predominio de la eutéctica, caracterizada por un refinamiento de la microestructura.
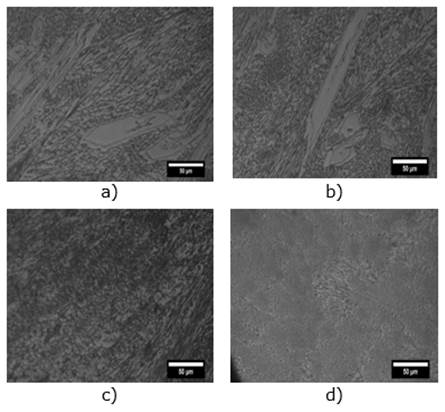
Figura 1 Microestructura de los depósitos. a) Depósito sin dilución, b), c), d) Depósitos de 90 A, 110 A y 130 A, respectivamente.
Las composiciones de las aleaciones del depósito sin dilución y los diluidos (Tabla 1) fueron recalculadas a 100 % del sistema ternario Fe-Cr-C y fueron ubicadas en ese sistema de equilibrio de fases (Figura 2). De acuerdo con la ubicación en el sistema, se advierte correspondencia con las microestructuras de la Figura 1. La aleación del depósito sin dilución y del de 90 A se ubican en la región hipereutéctica, donde los carburos Cr7C3 se forman durante la cristalización primaria a altas temperaturas. Por su parte, la aleación del depósito de 110 A se ubica también en la región hipereutéctica, pero en un punto muy próximo a la autéctica, por lo que, con relación a las aleaciones anteriores, se caracteriza por menor presencia de carburos primarios, predominando la presencia de la mezcla eutéctica. Por su parte, la aleación del depósito 130 A se ubican en la región hipoeutéctica, pero por las condiciones de desequilibrio y la cercanía a la línea de la transformación eutéctica, esta predomina en la microestructura.
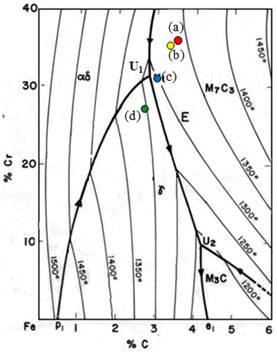
Figura 2 Superficie “líquidus” del diagrama Fe-Cr-C (Albertin, Neto & Teixeira 2011). Punto (a) Fe-60,35 %; C- 3,78 %; Cr-35,87 %. Punto (b) Fe-61,71 %; C- 3,65 %; Cr-34,64 %. Punto (c) Fe-66,25 %; C- 3,24 %; Cr-30,51 %; Punto (d) Fe-69,27 %; C- 2,96 %; Cr-27,77 %.
En correspondencia con la composición y la microestructura, los depósitos para los tres niveles de corriente de soldadura son apropiados para el desempeño al desgaste abrasivo y erosivo, enmarcándose dentro de la designación AWS EFeCr-A4 (AWS A5.13, 2000). Desde este punto de vista, el mejor depósito sería el obtenido con 90 A (Tabla 2, Figuras 1 y 2); sin embargo, este depósito tuvo muy poca penetración (Tabla 1), lo que significa que hay poca adherencia y puede ocurrir desprendimiento. De este modo, se asume como más recomendable el empleo de la corriente en el entorno de 110 A.
CONCLUSIONES
El aumento de la corriente aumenta la dilución, haciendo que disminuya el contenido de los elementos de aleación del depósito y que la microestructura pase de una fundición blanca de alto cromo de tipo hipereutéctica, con presencia de carburos primarios y matriz eutéctica, a una aleación hipoeutéctica con presencia predominante de la eutéctica.
Con acuerdo a la composición química, caracterizada por valores de carbono en el entorno de 3 % y 3,5 % de carbono y valores de cromo que superan el 25 %, todos los depósitos responden a la designación AWS EFeCr-A4 y son apropiados para el enfrentamiento al desgaste abrasivo y erosivo.
Se considera como más apropiado el depósito obtenido con corriente de 110 A, ya que el de 90 A presenta muy poca penetración y podría sufrir desprendimientos por falta de adherencia con el sustrato.