INTRODUCCIÓN
Los secadores cilíndricos horizontales rotatorios de contacto directo, en lo adelante secador, gozan de preferencia en la industria debido a su elevada productividad, a su eficacia y a la diversidad de materiales que pueden procesar (Yi et al. 2020). Tienen como desventaja el incremento de los costos de operación a causa del elevado consumo de energía, lo que ha impulsado numerosas investigaciones con el propósito de crear herramientas de predicción mediante la modelación matemática para mejorar su operación, optimizar su eficiencia y reducir el consumo energético.
La literatura especializada exhibe una variedad de modelos matemáticos que describen diversos procesos de secado; los más usuales se sustentan en las explicaciones sobre las causas o mecanismos naturales que dan lugar al fenómeno estudiado (modelos heurísticos); otros utilizan las observaciones directas del proceso o los resultados obtenidos a partir de la experimentación (modelos empíricos) y los que permiten determinar el punto exacto para resolver alguna problemática administrativa, de producción o de cualquier otra índole (modelos de optimización).
Dentro de los modelos heurísticos más utilizados en secadores se encuentran los estacionarios, que determinan los perfiles de humedad y temperatura para el sólido y el gas a lo largo del cilindro en régimen permanente; y los modelos dinámicos basados en ecuaciones diferenciales con parámetros distribuidos, que permiten obtener la evolución de la humedad y la temperatura cuando cambian las condiciones (Castaño, Rubio y Ortega 2009).
A través de los primeros modelos estacionarios para un secador, se obtuvo la expresión matemática que pronostica el contenido de la humedad del producto a partir de la temperatura del aire de secado, el contenido inicial de humedad y la velocidad de alimentación del producto (Myklestad 1963). Posteriormente, se utiliza un sistema de cuatro ecuaciones diferenciales para describir la transferencia de calor y masa en un secador de fertilizante, asumiendo que la transferencia de calor dependía de la velocidad de rotación (Sharples, Glikin y Warne 1964).
Nonhebel y Moss (1971) plantean un modelo en el cual dividen el secador en tres zonas: precalentamiento, secado constante y secado decreciente, en cada una de estas se aplican, de manera independiente, las ecuaciones de difusión de la humedad, caracterizadas por los periodos de calentamiento, de velocidad de secado constante y velocidad de secado decreciente. Con un enfoque similar, pero modificando parámetros empíricos tales como: el coeficiente de transferencia de calor, ecuaciones de tiempo de retención y pérdidas de calor, se han obtenido otros modelos, aunque aplicables solo a específicas de secado (Arruda 2008; Abbasfard et al. 2013; Souza et al. 2021; Echeeri y Maalmi 2021).
En los modelos dinámicos de secadores, las variables del sistema dependen tanto del tiempo como del espacio, siendo menos numerosos que los estacionarios. Una de las primeras evidencias de estos trabajos relaciona dos modelos: uno para el sólido y otro de forma independiente para la instalación (Reay 1979). Se desarrollan además modelos dinámicos en flujo a contracorriente, en los que el secador se divide en 10 secciones y se establecen las ecuaciones de balance dinámico de calor y de masa en cada sección (Douglas et al. 1993).
Cao y Langrish (2000) desarrollan un modelo general para un secador a contracorriente. El modelo se basó en balances de calor y masa combinados con dos modelos, uno que describe el transporte de partículas y la transferencia de calor dentro del secador y otro que describe la cinética de secado del material. En él se establecen seis ecuaciones diferenciales parciales para evaluar seis variables de estado: contenido de humedad de sólidos y temperatura del sólido; humedad y temperatura del aire, y la conservación del sólido y del aire en función del tiempo y la longitud del secador. En investigaciones más recientes otros investigadores (Parra-Rosero 2017; Ponce, Royo y García 2018; Goyal y Bushra 2018; Perazzini et al. 2021) realizan la modelación con base en los modelos existentes, introduciendo algunas variaciones en las ecuaciones empíricas para la cinética de secado, la estimación del tiempo de retención y el coeficiente volumétrico para la transferencia de calor.
Los resultados de revisión bibliográfica confirman la existencia de una gran diversidad de modelos para el secado, debido a los numerosos materiales que se secan en equipos comerciales y a los muchos tipos de equipos que se utilizan, por lo que, no existe una sola teoría de secado que comprenda todos los materiales y tipos de secadores.
Las variaciones posibles en forma y tamaño de los materiales, de los equilibrios de humedad, de los mecanismos del flujo de humedad a través del sólido, así como en el método de transferencia de calor que se requiere para la vaporización, impiden que exista un tratamiento unificado de estos modelos (Harriot 2007), por lo que es preciso la particularización de los modelos para el secado de cada sólido y las instalaciones en donde se efectúa; considerando que el proceso de secado es un proceso a flujo continuo, en el cual no deben ocurrir variaciones significativas en sus parámetros de operación en pequeños intervalos de tiempo.
Es decir que existe un periodo relativamente largo durante el proceso de arrancada y puesta en marcha de la instalación, hasta que se estabilizan los flujos de combustible, de aire y de gases que entran al cilindro en función de la productividad nominal del secador, proceso que demora hasta 8 horas de operación. Una vez que se estabilizan todos los parámetros, se mantiene en explotación la instalación hasta que se detenga la producción por concluir con las corridas experimentales o en caso de averías.
Por lo anteriormente planteado, en la presente investigación se propone un modelo matemático en estado estacionario, para el secado de la mena laterítica de Ni en un secador cilíndrico horizontal rotatorio, a escala semindustrial.
MATERIALES Y MÉTODOS
Para establecer el modelo matemático que identifique al objeto de estudio se describió la instalación experimental, se analizaron los principales procesos que se manifiestan en el secador y se definieron las variables de interés para la modelación.
Descripción de la instalación experimental
El secador objeto de estudio está constituido por el quemador (1) al cual se le suministra combustible y aire para la atomización y la combustión. Luego, en la cámara de combustión (2), se le adiciona el aire de dilución para aumentar el volumen de gases para el secado (Figura 1). Los gases dentro de la cámara de combustión alcanzan temperaturas cercanas a los 1 773 K y al entrar en contacto con el aire de dilución se reduce su temperatura hasta valores entre los 1 123 K y los 973 K.
La mezcla de gases resultantes entra a la cámara de paso (3) por donde además se introducen, a través de la entrada del sólido, las menas lateríticas húmedas con valores de humedad entre 30 % y 40 % al tambor rotatorio (4). Es en este último donde se produce el proceso de secado por la acción de los gases calientes sobre las menas que circulan en la misma dirección.
El tambor rotatorio posee un sistema motriz acoplado al cuerpo que le permite rotar alrededor de su eje apoyado sobre rodillos. En la pared interior tiene aditamentos soldados, llamados levantadores, diseñados para garantizar una cortina de mena (sólido) por el efecto de la rotación del tambor y la gravedad. Las características técnicas y constructivas del secador analizado se muestran en la Tabla 1.
Análisis de los procesos que intervienen en el secador
En el secador intervienen, principalmente, los procesos de transferencia de calor y de masa. El calor que los gases de la combustión aportan (Figura 2) se transfiere al sólido por diversas vías y modos (Gorog, Adams y Brimacombe 1982). La mayor cantidad de calor es transferida mediante convección y radiación del gas al sólido que está en suspensión, y del gas a la superficie del sólido que se encuentra depositado en la parte inferior del cilindro (1); de igual modo el gas transfiere calor a la pared interior que no está cubierta por el sólido (2).
Una parte del calor absorbido por la pared es transferido por radiación a la superficie del sólido con la que no está en contacto (3) y, por conducción, a la superficie del sólido que está en contacto con la pared (4) (Froment y Bischoff 1990). Además, se considera la presencia de la radiación y la convección de manera simultánea debido las cavidades presentes en los sólidos porosos en los cuales se acumulan gases. Esta última condición de transferencia de calor es parte del ciclo regenerativo de la pared del cilindro al sólido (Agustini 2006).
Por último, una fracción del calor absorbido por el cilindro no se transfiere a la mena y se pierde al exterior mediante la conducción de calor de la pared interior a la exterior y por convección y radiación de la pared exterior a los alrededores (5).
Variables de interés en la modelación
Por ser el secado térmico de sólidos un proceso donde están presentes los mecanismos de transferencia de calor y de masa, se identifican como variables de mayor importancia para la modelación matemática: los flujos másicos (de gases y mena); la temperatura y las propiedades termofísicas del sólido y los gases producto de la combustión. Además, se tienen en cuenta: la velocidad de rotación y ángulo de inclinación del cilindro, el tiempo de retención de la mena en el tambor y las variables meteorológicas.
Modelo matemático del proceso de secado en secadores rotatorios
El modelo matemático desarrollado se sustenta en un sistema de ecuaciones diferenciales y ordinarias determinadas partir de los balances de energía y masa en el secador. Para su mejor análisis se dividió el objeto de estudio en dos subsistemas térmicos: el primero, constituido por la cámara de combustión, y el segundo, por el cilindro o tambor rotatorio (Figura 1) donde ocurre el proceso de secado, a los cuales se les aplican balances de masa y energía.
Balance de masa en la cámara de combustión
La modelación de la combustión se basa en la termodinámica de equilibrio, donde se consideran las reacciones químicas entre los elementos combustibles al mezclarlo con el oxígeno presente en el aire a cierto valor de presión y temperatura, que generan nuevos elementos gaseosos y liberan calor durante la reacción. Teniendo en cuenta que la combustión en la cámara se realiza con un exceso de aire, los compuestos resultantes de la combustión son los siguientes: CO2, N2, H2O, SO2 y O2. Considerando lo antes declarado se establece la ecuación 1 para el balance de la combustión.
Los prefijos (x
n
) que aparecen en los elementos que forman la ecuación anterior, son las fracciones molares () de cada una de los elementos que componen la ecuación.
A partir de la conservación de los átomos de los elementos químicos que componen la ecuación 1 se calculan los productos de la combustión y el flujo de los gases de la combustión
(2).
El flujo de gases entregados al tambor se determina a través de la suma del flujo generado por la combustión más el aire de dilución (3).
Siendo el flujo de aire de dilución (kg/s) y
el flujo de gases a la entrada del tambor (kg/s).
Balance de masa y energía en el tambor
Para determinar el modelo en el tambor se partió de la división del tambor cilíndrico en un número finito de elementos volumétricos dispuestos en serie, donde cada elemento está limitado longitudinalmente por dos secciones: sección de entrada (subíndice x) y sección de salida (subíndice x + dx).
Balance de masa en el gas y la mena
Aplicando el balance de masa a la mena y al gas en cada uno de los volúmenes de control se obtienen las ecuaciones 4 y 5:
Donde: son los flujos másicos de mena y del gas a la entrada y a la salida del volumen de control (kg/s) y
es el flujo másico de agua que se evapora de la mena (kg/s).
Según Castaño, Rubio y Ortega (2009) el flujo másico del agua que se evapora del sólido se determina mediante la ecuación .
Donde: R s es la ratio de secado (kg/(kg·s)) y M s(dx) es la masa de mena en el dx (kg) la cual se determina por ecuación 7 en función del flujo de mena y el tiempo de paso de esta por el volumen de control diferencial (t dx ) (Mujumdar, Ganesh y Kulkarni 2007).
Aplicando el balance de masa, pero en este caso para determinar la humedad de la mena y del gas, se obtienen las ecuaciones 8 y 9.
Siendo las humedades del sólido y el gas a la entrada y salida del volumen de control (kg/kg).
Para determinar la ratio de humedad, ya sea de la mena o del gas, se emplea la ecuación 10.
Para caracterizar la variación de la humead en la mena y el gas se plantean las ecuaciones 11 y 12 (Abbasfard et al. 2013). Para determinar la velocidad de evaporación del agua se emplea la expresión 13.
En la ecuación 13, k es la constante cinética de secado del material a secar (s-1) la cual se obtiene de forma experimental (Zalazar-Oliva 2021). H s(x) y H e son los contenidos de humedad en la condición inicial y la humedad de equilibrio, respectivamente (kg/kg).
Balance de energía al gas y a la mena
Aplicando el balance de masa y energía al gas y a la mena se obtienen las ecuaciones 14 y 15.
Los términos T
g
, T
s
y T
w
son las temperaturas del gas, de la mena y del gas a la pared (W/(m2·K)); son los coeficientes de transferencia de calor por radiación del gas a la mena y del gas a la pared, respectivamente, (W/(m2·K));
identifica a la transferencia de calor por conducción de la pared exterior al aire (W/(m2·K)). En la ecuación se tienen, además, los términos
los cuales representan las áreas de transferencia de calor del gas al sólido, del gas a la pared y de la pared cubierta (m2).
Balance de energía en la pared
Para determinar la temperatura de la pared se tiene en cuenta que el espesor de la pared del cilindro es mucho menor que el diámetro y la longitud del secador. En este contexto se asume que la temperatura de la pared interior es igual a la temperatura de la pared exterior. Partiendo de esta suposición se aplica el balance de energía y se obtiene la ecuación 16.
Siendo el coeficiente de transferencia de calor por convección de la pared exterior al aire; (W/(m2·K)),
el coeficiente de transferencia de calor por radiación de la pared exterior al aire; (W/(m2·K)) y
el área de la pared exterior (m2).
La convección entre el gas y el mineral en el interior del tambor se determina por la ecuación 17, recomendada por Agustini (2006) para transferencia de un flujo de gas y un sólido en el interior de un cilindro.
Donde: es flujo másico de los gases que cruzan la sección transversal del cilindro; (kg/(h·m2)). Según Agustini (2006) el coeficiente de transferencia de calor por radiación del gas al sólido se estima a partir de expresión 18.
Donde: es la emisividad efectiva. Considerada por Agustini (2006) como un parámetro, que toma valores entre 0,5 y 0,35 para temperaturas del gas de 1 273 K y 2 273 K, respectivamente, y depende del diámetro del horno, la concentración de gases de la combustión, del polvo, el hollín, la emisividad del gas y la emisividad de la superficie.
Las correlaciones empleadas para determinar los coeficientes de transferencia de calor por convección () y radiación (
) del gas a la pared descubierta se muestran según 19 y 20.
La transferencia de calor por conducción de la pared al sólido (h ws_con ) se determinó mediante la ecuación 21.
Donde: es la conductividad térmica de la mena laterítica (W/(m·K));
la difusividad térmica del mineral (m2/s), R el radio del cilindro,
corresponde a la velocidad de rotación del tambor (1/s) y
al ángulo de llenado (º) ecuación 22.
El coeficiente de transferencia de calor por radiación de la pared al sólido se calcula mediante la expresión 23.
Diseño de experimento
Para la validación del modelo se empleó un diseño de experimento multifactorial. En el mismo se analizaron dos factores: flujo de mena (kg/s) con tres niveles (0,35; 0,39 y 0,43) y flujo de combustible (kg/h) con dos niveles (26 y 29); para cada experimento se hicieron siete réplicas de forma aleatoria, para un total de 42 pruebas.
Validación de los modelos matemáticos
Para validar el modelo propuesto se compararon los resultados experimentales con los obtenidos mediante el modelo para iguales condiciones de trabajo. Luego se calcularon los errores relativos puntuales y promedios (ecuación 24 y 25), teniendo como criterio de aceptación que este último fuera inferior al 10 %. Las variables empleadas en la validación fueron, la humedad de la mena, la temperatura del gas y de la mena a la salida del secador.
Siendo E: Error relativo puntual entre los valores experimentales y los teóricos (%); el valor promedio de la variable obtenida de forma experimental (adimensional);
valor promedio de la variable obtenida de forma teórica (adimensional)
error relativo promedio entre los valores experimentales y los teóricos (%) y N el número de determinaciones (adimensional).
RESULTADOS Y DISCUSIÓN
Resultados de la experimentación
Con el modelo matemático establecido se determinó el comportamiento de las principales variables que intervienen en el secado. El modelo se resolvió aplicando el método numérico de Runge-Kutta cuarto orden. Las propiedades termofísicas de la mena se tomaron según lo propuesto por varios investigadores (Zalazar-Oliva et al. 2019; Zalazar-Oliva et al. 2021).
La Tabla 2 resume los resultados experimentales, se exponen los valores de temperatura del gas, de la mena y la humedad de la mena a la salida del secador en función del flujo de mena y de combustible alimentado. Además, se relacionan los valores de las variables obtenidas de forma experimental y los valores teóricos calculados con el modelo matemático para iguales condiciones. En esta se comprueba que los errores relativos puntuales para la humedad de la mena varían entre 0 % y 10 %. Vale destacar que, de los errores calculados, el 69 % son inferiores al 6 %. Por otro lado, se determinó que error relativo promedio es de un 3,9 %.
Se observó, además, que los errores relativos puntuales entre los valores de las temperaturas obtenidas de manera experimental y teórica, tanto para el gas como para la mena, son inferiores a 6 %.
Tabla 2. Resultado de la experimentación y validación
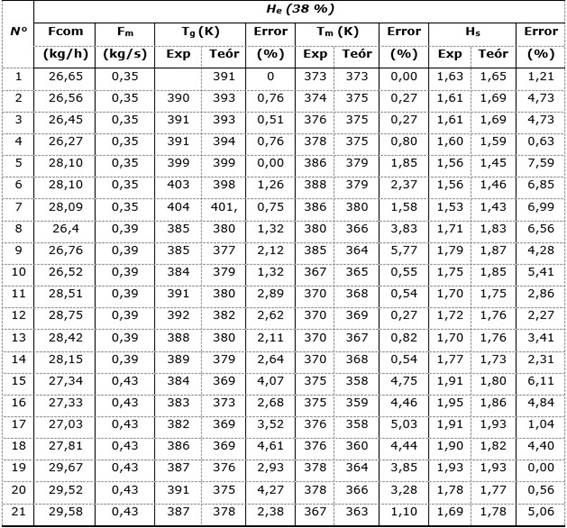
F com : flujo del combustible; F m : flujo de mena; T g : Temperatura de los gases a la salida; Error: El error relativo puntual; T m : Temperatura de la mena a la salida; H s : humedad de la mena a la salida. Teniendo en cuenta la distribución de los errores relativos puntuales calculados, se confirma que el modelo matemático establecido en el presente trabajo tiene una exactitud adecuada y, por tanto, es válido para aplicar en el proceso de secado de menas lateríticas de Ni.
Modelación de los parámetros de operación
La relación entre el coeficiente de llenado y el tiempo de paso con el flujo de mena se muestra en la Figura 3. Para los flujos de mineral entre 1 t/h y 1,5 t/h y tiempos de retención entre 15 min y 22 min se obtienen valores del coeficiente de llenado entre 8 % y 16 %.
La Figura 4 muestra el comportamiento de la temperatura del gas, del mineral (la mena) y la temperatura de la pared en el interior del secador. También se representa la variación de la humedad en función de la longitud en el interior del secador. Se observa que el gas experimenta un descenso de su temperatura desde 1 123 K hasta valores próximos a los 373 K en la salida del secador.
Se debe resaltar que en los primeros metros es donde el gas experimenta mayor descenso de temperatura resultado de la mezcla de este con el flujo de mena que entra al secador a temperatura ambiente (entre 295 K y 301 K) y concentraciones de humedad entre 30 % y 38 %. En cambio, la temperatura de la mena va incrementándose gradualmente en los primeros metros hasta valores cercanos a los 368 K para luego permanecer casi constante alcanzando un equilibrio térmico entre la temperatura del gas y de la pared.
Se determinó que en la primera mitad del secador la humedad de la mena disminuye desde los valores de entrada hasta valores entre 4 % y 6 %. A partir de la segunda mitad, la variación de la humedad no es tan acentuada y muestra un comportamiento asintótico. Tal comportamiento se asocia a las etapas de secado. Se puede afirmar que en los primeros metros del secador intervienen los periodos de calentamiento y velocidad de secado constante. En esta etapa se evapora la humedad libre de la mena, predominan las condiciones externas y el sólido tiene un comportamiento no higroscópico.
A partir de la segunda mitad del secador inicia el período de rapidez decreciente donde se evapora la humedad ligada a la mena y predominan las condiciones internas y externas simultáneamente. La temperatura de la mena sobrepasa la del bulbo húmedo debido al descenso de la velocidad de secado, se rompe el equilibrio térmico que mantiene estable la temperatura y una parte considerable del calor se emplea en el calentamiento del sólido.
La modelación del comportamiento de la humedad de la mena a la salida, a partir de la variación del flujo de mena, la humedad del mineral a la entrada y la velocidad de rotación del tambor, manteniendo las demás condiciones de operación constantes, demostró la proporcionalidad entre ellas (Figura 5).
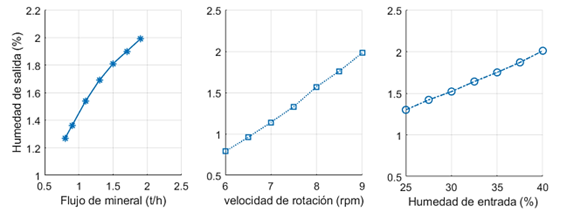
Figura 5 Influencia del flujo, velocidad de rotación y la humedad de entrada del mineral en la humedad mineral a la salida del secador.
Como se muestra en la Figura 5 existe un comportamiento lineal entre la humedad de salida de la mena con la velocidad de rotación del secador y la humedad de entrada. Mientras que la relación entre la humedad de salida y el flujo de mena muestra un comportamiento logarítmico, siendo la velocidad de rotación la variable que mayor efecto ejerce sobre la humedad de la mena a la salida.
CONCLUSIONES
No existe una sola teoría de secado que incluya todos los materiales y tipos de secadores, siendo necesarios trabajos como este.
El modelo físico-matemático propuesto es capaz de predecir los valores de la temperatura de la mena, la temperatura del gas y la humedad a la salida del secador con un error relativo puntal inferior al 10 %.
Queda demostrado que cuando la mena ha recorrido aproximadamente el 60 % de la longitud del cilindro, ha perdido más del 80 % de la humedad de entrada, para valores de entrada entre 28 % y 36 % a la entrada.
Se comprueba que existe una relación linealmente dependiente entre la humedad de salida de la mena con la velocidad de rotación y la humedad de entrada.