INTRODUCCIÓN
El recargue por soldadura es una de las técnicas más eficientes para la protección de elementos de máquinas contra diferentes condiciones de desgaste (Ortiz, Cruz-Crespo y Pozo 2021), donde el proceso manual con electrodo revestido (SMAW) ofrece varias ventajas relacionadas con el costo del equipo y la disponibilidad de materiales (Paz-Triviño, Buitrago-Sierra y Santa-Marín 2020).
Entre los elementos de aleación mayormente utilizados en los consumibles de soldadura para el recargue se encuentran: C, Cr, Mn, V, Mo, W, Ni, etc., los cuales se adicionan en forma de mezcla de polvo en el revestimiento o dentro de electrodos tubulares. Estos electrodos dan como resultado menor dilución y depósitos más anchos en comparación con los electrodos revestidos convencionales (Bastien 2022).
Los aceros al vanadio tienen gran tendencia a formar carburos, los cuales impiden el crecimiento de grano, donde la adición de pequeñas cantidades, aproximadamente 0,05 %, favorece la obtención de lingotes sanos, homogéneos y de grano fino. Este elemento, cuando se encuentra disuelto, influye notablemente en la templabilidad, lográndose características mecánicas muy elevadas en los enfriamientos al aire (Oerlikon 2021).
Petranikova y demás colaboradores (2020) plantean que cerca del 40 % del vanadio se recicla de residuales de catalizadores de procesos químicos, residuos del petróleo, cenizas y escorias de arrabio que contienen vanadio.
Los catalizadores agotados de la producción de ácido sulfúrico pueden contener del 4 % al 9 % de V2O5 (Belhaj, Ben y Jeday 2018), siendo considerados desechos peligrosos (Convenio de Basilea 1989; Ley No. 81 1997). Dado los contenidos de vanadio presentes en estos residuales, ellos pueden ser aprovechados como fuente de vanadio, metal considerado estratégico en el mercado internacional, encontrándose en la lista de materias primas críticas (Petranikova et al. 2020; Mineral Commodity Summaries 2020), del cual no existen yacimientos en Cuba.
El vanadio contenido en los catalizadores agotados puede ser obtenido como una sal o como ferrovanadio, para lo cual se ha establecido que el contenido de V en el residual sea superior al 3 %. Industrialmente puede ser extraído por métodos pirometalúrgicos, en forma de aleación de vanadio, y/o hidrometalúrgicos, donde se obtiene un concentrado de vanadio (Production of Sulphuric Acid 2000; Perdomo-Gómez et al. 2021; Perdomo-González et al. 2021).
De aquí que el objetivo del presente trabajo sea realizar la evaluación del concentrado de vanadio obtenido del procesamiento químico de los catalizadores agotados procedentes de la planta Sulfometales de Pinar del Río, como carga de aleación de electrodos tubulares revestidos.
MATERIALES Y MÉTODOS
Obtención del concentrado de vanadio utilizado como carga de aleación del electrodo
Las materias primas utilizadas fueron: catalizador agotado, ácido sulfúrico, carbonato de sodio y carbón vegetal de marabú.
El catalizador agotado utilizado proviene de la Fábrica Sulfometales Patricio Lumumba, perteneciente al Grupo Empresarial “Geominsal”, Santa Lucía, provincia de Pinar del Río. La caracterización química del catalizador se muestra en la Tabla 1. El carbón utilizado es obtenido a partir de marabú por los métodos tradicionales.
Tabla 1 Composición química elemental de los catalizadores agotados procedentes de la Planta de Sulfometales
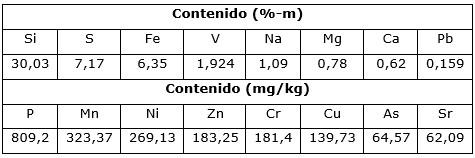
El catalizador agotado y el carbón vegetal fueron triturados hasta una granulometría por debajo de 0,1 mm. El procesamiento químico del catalizador se realiza, según Perdomo-Gómez y demás colaboradores (2021), obteniéndose el concentrado de vanadio mediante precipitación con solución de carbonato de sodio (1 mol/L) (Khorfan, Wahoud y Reda 2001); además, se adiciona carbón vegetal después de la precipitación para lo cual se mantiene la mezcla en agitación durante una hora.
Fabricación del alambre tubular
Para la fabricación de los alambres tubulares se utilizó una máquina perteneciente al laboratorio de materiales del Centro de Investigaciones de Soldadura (CIS), la cual se muestra en la Figura 1A. La máquina utiliza la tecnología de fabricación de los alambres tubulares mediante el conformado y trefilado de los metales en frío a partir de una cinta de acero de bajo C (Acero SAE 1010), de 0,5 mm de espesor y 15 mm de ancho. El equipo posee un dosificador (Figura 1B) para la adición regulada de la carga al alambre tubular.
La tracción de la cinta metálica a través de los pares de rodillos se muestra en la Figura 1C, donde el alambre tubular se enrolla luego de pasar por el trefil final (diámetro=3,5 mm). Finalmente se procede a enderezar y cortar el alambre tubular a una longitud de 300 mm.
Revestimiento de los alambres tubulares
En la Tabla 2 se muestran los componentes que integran el revestimiento de los electrodos tubulares a evaluar.
El revestimiento de los alambres se realizó mediante inmersión, empleando silicato de sodio (35 %) como aglutinante. Los electrodos revestidos se dejaron secar al aire durante 24 horas, para luego secarlos en una estufa a una temperatura aproximada de 180 ºC durante dos horas.
Evaluación operativa de los electrodos
El electrodo tubular fabricado emplea un revestimiento básico a base de calcita y fluorita, minerales que comúnmente garantizan un buen comportamiento tecnológico. Para comprobar el comportamiento de los electrodos se utilizaron los criterios de un grupo expertos, evaluándose como parámetros fundamentales: el desprendimiento de la escoria, la apariencia del cordón y la estabilidad del arco.
Obtención de los depósitos para el estudio de su composición química, microestructura y dureza
Como material base se utilizaron placas de acero SAE 1010 con una dimensión de 100 x 50 x 10 mm. Los depósitos para la determinación de la microestructura y la dureza se obtuvieron depositando tres capas a temperatura ambiente. Para obtener los depósitos se utilizó CDEN (corriente directa, electrodo negativo), con valores entre 80-100 A. El rango de velocidad de soldadura empleada fue de 3-4 m/h.
Las muestras para el análisis de composición química del depósito sin dilución fueron obtenidas en correspondencia a los requisitos establecidos por las normas AWS A5.13/A5.13M (AWS A5.13/A5.13M 2010). La caracterización química del depósito se efectuó mediante espectroscopia de emisión atómica.
Preparación de las probetas para el estudio de la microestructura y dureza del depósito
Las probetas para el estudio metalográfico se obtuvieron mediante cortes transversales de los depósitos, utilizando una tronzadora y líquido refrigerante para evitar el sobrecalentamiento. Las muestras utilizadas para determinar la dureza y estudiar el tipo de microestructura fueron debidamente desbastadas y pulidas. El ataque fue realizado por inmersión con reactivo Nital al 2 % y observadas mediante metalografía óptica (MO) utilizando un microscopio binocular marca Novel.
La dureza se determinó en el centro del cordón y en la zona columnar, con un durómetro marca Shimadzu y una carga de 1 000 g.
ANÁLISIS Y DISCUSIÓN DE RESULTADOS
Concentrado de vanadio
El concentrado de vanadio se obtiene a partir del procesamiento químico de catalizadores agotados generados de la fabricación de ácido sulfúrico, lo cual permite la recuperación del vanadio contenido en el residual y de otros elementos metálicos en forma de óxidos metálicos y de sales.
Luego de la etapa de precipitación se incorpora el carbón vegetal manteniendo el sistema en agitación, lo cual garantiza un mejor mezclado entre los óxidos metálicos precipitados y el carbón, facilitando la etapa de filtración y la obtención de un producto más homogéneo, el cual será usado como carga de aleación de electrodos tubulares. El carbón vegetal favorece la reducción de los óxidos metálicos presentes en la carga de aleación durante el proceso de soldadura.
La Figura 2 muestra fotos del carbón vegetal, del concentrado de vanadio obtenido y de la mezcla del concentrado con carbón sin calentar y después de un calentamiento a 450 ºC, donde se aprecia la presencia de partículas oscuras distribuidas dentro del concentrado, lo cual evidencia el grado de mezclado en el producto obtenido.
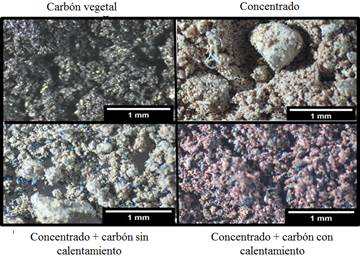
Figura 2 Foto del carbón vegetal y concentrado usado como carga de aleación del electrodo tubular revestido.
La cantidad de carbón adicionada responde a la estequiometria de las reacciones químicas redox que deben ocurrir entre los óxidos presentes en el concentrado de vanadio y el carbono, durante el proceso de soldadura, del cual se adicionó un 30 % en exceso. El proceso de reducción de los óxidos debe transcurrir de acuerdo a la reacción I.
MxOy + yC = xM + yCO (I)
Comportamiento tecnológico del electrodo fabricado
De manera general, las propiedades tecnológicas del electrodo: desprendimiento de la escoria, apariencia del cordón y estabilidad del arco, se comportaron de manera satisfactoria. Un resumen de estas propiedades, durante el proceso de evaluación de los electrodos obtenidos, se muestra en la Tabla 3.
La estabilidad del arco eléctrico, durante el proceso de soldadura, se logra por la existencia de un medio altamente ionizado en la columna del arco, debido al empleo en el revestimiento de minerales, cuyos componentes mayoritarios se caracterizan por un bajo potencial de ionización (García 2013), como es el caso de la calcita (Ca2+= 6,11 eV); también se ve favorecida por la estructura laminar y conductividad eléctrica del grafito, la que aumenta con la temperatura (Pastor 2016). Asimismo, la utilización de silicato de sodio como aglutinante es otro aspecto que favorece la estabilidad del arco, considerando que el Na+ (5,138 eV) (García 2013) presenta bajo potencial de ionización.
La evaluación en cuanto al desprendimiento de la escoria es aceptable, donde la utilización de un 10 % de fluorita para garantizar la limpieza del baño fundido ha jugado un papel fundamental.
Como resultado negativo en cuanto a la sanidad del cordón de soldadura, se tiene la alta porosidad observada en el cordón (Figura 3), la que afecta la uniformidad y apariencia del depósito.
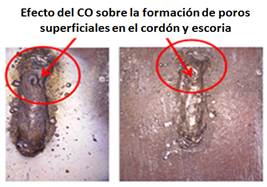
Figura 3 Cordón de soldadura obtenido con el electrodo fabricado, con escoria (izquierda) y sin esta (derecha).
Sobre este resultado hay que considerar como una posible causa que el concentrado de vanadio utilizado como carga de aleación se encuentra en forma de óxidos de vanadio, de hierro, etc., lo que implica que los procesos de reducción por el C en el baño fundido generan considerable cantidad de CO, el cual queda atrapado en el metal del cordón de soldadura durante la solidificación.
Además del posible efecto del CO sobre la porosidad, la aparición de poros en el cordón pudiera deberse a fenómenos asociados al carbón vegetal utilizado en la mezcla con el concentrado de vanadio, el cual, al producirse mediante pirolisis de la madera, queda con pequeñas cantidades de residuos orgánicos, cenizas contenidas originalmente en la madera, gases de combustión, cierta cantidad de productos químicos, entre otros (FAO 1983; Manual del carbón activo 2022). Entre las sustancias volátiles presentes en los carbones se destacan alquitranes, ácido acético, ácidos piroleñosos, entre otros (Manual del carbón activo 2022).
En el caso del uso de los carbonos como combustible doméstico, valores bajos de materia volátil dificultan el encendido, sin embargo, se tendrá una combustión limpia, ya que un alto contenido de volátiles produce demasiado humo durante la combustión y se genera más carbonilla (De la Cruz et al. 2020). Este comportamiento ocurre durante el proceso de soldadura, alterando la composición de la mezcla de gases generados, afectando de esta manera la apariencia del cordón obtenido.
Para resolver esta deficiencia puede calentarse la mezcla concentrado/carbón vegetal a temperaturas por encima de los 450 ºC, disminuyendo el contenido de volátiles presentes; además, en dependencia de la temperatura alcanzada deben desarrollarse procesos de reducción en estado sólido de los óxidos metálicos presentes en la mezcla, lo que disminuye el contenido de C, aumentando el nivel de metalización del concentrado.
Composición química del depósito
En la Tabla 4 se muestra la composición química del metal aportado por el electrodo fabricado, donde se puede apreciar como elementos fundamentales en el depósito el V, Cr y Mo, cuyos valores pueden tener un efecto positivo sobre las propiedades del metal depositado.
Como resultado, se obtuvo que la presencia de elementos de aleación en el depósito son consecuencia de los procesos de reducción de los óxidos metálicos incorporados a la carga del electrodo con la mezcla concentrado/carbón, bajo las altas temperaturas del arco eléctrico y la presencia de un agente reductor (carbono), procedente del grafito y del carbón vegetal.
El carbono adicionado al revestimiento en forma de grafito también es importante, como fuente de C, para favorecer la presencia en la capa de recargue de determinadas microestructuras, por ejemplo; la martensita, la que favorece la resistencia al desgaste por abrasión (Chotěborský et al. 2008). No obstante, el valor obtenido en el depósito (0,19 %) no tiene influencia significativa sobre la microestructura.
Los bajos niveles de carbono en el depósito pueden estar asociados a la descomposición parcial de los óxidos que interactúan con el C durante el proceso de soldadura formando CO. La disminución de la transferencia del elemento metálico al cordón puede deberse a que el óxido del elemento en cuestión no fue reducido a su estado elemental quedando en un estado de oxidación intermedio, tal como se muestra en las reacciones siguientes:
MxOy = xMO+ (y-x)/2 O2 (II)
xMO + xC = xM + xCO (III)
MxOy + (y-x)/2 C= xMO + (y-x)/2 CO2 (IV)
MxOy + (y-x) C= xMO + (y-x) CO (V)
En cuanto al resto de los componentes del depósito puede señalarse que los niveles de reducción fueron bajos, en tanto los del Cr fueron elevados, dado esto por la mayor afinidad del V por el oxígeno con relación al cromo, lo cual favorece las pérdidas de este elemento. Si se conjugan todos estos fenómenos en sólo uno puede plantearse que el proceso de soldadura se ha desarrollado bajo condiciones altamente oxidantes, desplazando el equilibrio hacia la formación de CO2 y hacia la re-oxidación del vanadio, lo cual incrementó considerablemente las pérdidas de los elementos de aleación que debieron pasar al depósito.
La utilización de la fluorita y caliza en el revestimiento del electrodo en un 80 %, también ha sido un factor significativo sobre la presencia de los elementos señalados en el cordón, debido a que puede incrementar la fluidez y basicidad de la escoria. Una escoria con buena fluidez facilita la velocidad de las reacciones y los intercambios entre la escoria y el metal. Según Volshenco y demás investigadores 1988, un aumento de la basicidad, disminuye la actividad química de la escoria, aumentando la reducción y transferencia de los elementos metálicos al cordón de soldadura.
No obstante a lo señalado anteriormente, los resultados en cuanto a la composición química del depósito de soldadura despiertan grandes perspectivas sobre la aplicación del concentrado de vanadio, obtenido del procesamiento de catalizadores agotados, como carga de aleación para el desarrollo de electrodos destinados al recargue, fundamentalmente por la presencia del V, Cr y Mo.
Microestructura del depósito obtenido con el electrodo
En la Figura 4 se presenta la microestructura obtenida en el centro y en la zona columnar del depósito, cuyas morfologías son diferentes, así como la dureza (187 Hv y 208 Hv), tal como se aprecia en la Tabla 5. La microestructura observada en el centro del cordón se caracteriza por la presencia de ferrita de grano fino, dado por el efecto del V aportado por el electrodo.
En esta zona del depósito, la presencia de pequeños carburos de V formados durante la solidificación frena el crecimiento del grano austenítico (Kumar 2019), fenómeno que determina la presencia de la ferrita de grano fino a temperatura ambiente, como se observa en la Figura 4. Otro factor que determina una morfología diferente a la ferrita acicular es que en la zona del centro del depósito la aleación se enfría lentamente, causa que limita la formación de una microestructura acicular, de acuerdo con lo reportado en la literatura (Chai, Su y Yang 2014).
Por otra parte, la formación de la ferrita en la microestructura en el centro del cordón está también favorecida por la presencia del Cr y el bajo contenido de C, el cual reduce la trasformación de la austenita a perlita durante el enfriamiento (Denise, Susanne y Christian 2017).
En el caso del depósito obtenido con el electrodo fabricado en la zona columnar (Figura 4) no se distingue la presencia de ferrita de tipo widmastatten y de contorno de grano. Además, la ferrita poligonal no tiene un contorno bien definido, aunque sí se observa la presencia de ferrita acicular, en correspondencia con la dureza obtenida en dicha zona (208 HV), la cual se muestra en la Tabla 5. Este resultado se debe a la influencia de los elementos presentes en el sistema de aleación que caracterizan al depósito, cuya composición se ofrece en la Tabla 4.
Relacionado al efecto de los elementos de aleación sobre la formación de la ferrita acicular, de acuerdo a la composición del cordón obtenido con el electrodo tubular fabricado (Tabla 4), hay que considerar como significativo el efecto del 0,19 % de V, como uno de los elementos que aporta el electrodo tubular fabricado. Estas cantidades son suficientes para promover en la costura la formación de ferrita acicular.
El V, al ser un fuerte formador de carburos (VC), disminuye la cantidad de C en la austenita limitando la presencia de otros tipos de microestructuras aciculares como la martensita o bainita. De igual forma, puede favorecer la nucleación de la ferrita acicular, ya que los pequeños VC pueden constituir núcleos para generar la formación de ferrita acicular (Aleksandar et al. 2017). Por otro lado, en el depósito aparece una cantidad apreciable de Mo, el cual es también un elemento que favorece la formación de ferrita acicular y bainita, aún en bajos contenidos (Capdevila et al. 2006).
Independientemente a los bajos niveles de C, la presencia de V, Cr y Mo, unido a las características de la microestructura observada en las diferentes zonas del cordón de soldadura, permiten evaluar otras posibles aplicaciones de los electrodos desarrollados, siendo factible incluso evaluar usos de estos consumibles en procesos de soldadura en condiciones subacuática mojada, dado sobre todo por los niveles de ferrita acicular observados y los relativamente bajos valores de dureza obtenidos en el cordón.
CONCLUSIONES
El comportamiento tecnológico de los electrodos fabricados se caracteriza por un buen desprendimiento de la escoria, una excelente estabilidad del arco y una deficiente apariencia del cordón, la cual es consecuencia de las complejas reacciones, fundamentalmente de tipo redox, que se producen durante la soldadura, provocando el desprendimiento de gases.
La presencia de ferrita acicular en la zona columnar del depósito se debe esencialmente a la presencia de V y Mo, sin embargo, la morfología en el centro del cordón (ferrita de grano fino) es diferente debido a la menor velocidad de enfriamiento en esta zona, comportamiento que se corresponde con los valores de dureza obtenidos para cada una de las zonas del cordón.
La presencia en el cordón de soldadura de los elementos de aleación V, Cr y Mo avala las potencialidades de uso del concentrado de vanadio, obtenido de la lixiviación ácida de catalizadores agotados de la fabricación de ácido sulfúrico, como carga de aleación de electrodos tubulares destinados al recargue de piezas.