Introducción
El hormigón o concreto, es un material compuesto muy utilizado en la rama de la construcción, el cual está formado principalmente por cemento, como elemento aglomerante, al que se le añaden partículas o fragmentos de un agregado, además de agua y/o aditivos. Las partículas de agregados, dependiendo básicamente de su diámetro, son los áridos (grava, gravilla y arena).
En el hormigón o concreto, el agua y el cemento son elementos que reaccionan hidráulicamente, generando una reacción química que al fraguar permite formar el cuerpo de la mezcla. Es posible reciclar diferentes residuos sólidos para incorporarlos como agregados en el hormigón con el fin de optimizar las mezclas, siendo el vidrio uno de ellos.
El empleo de materiales de construcción no convencionales en la búsqueda de soluciones a problemas de la sociedad, como la construcción de viviendas, viales, etc., reduce el incremento de los costos que ello conlleva con la sustitución parcial o total del consumo de materias primas escasas o ubicadas en sitios distantes. Catalán (2013), demuestra que la absorción de agua es prácticamente nula en el vidrio, se puede disminuir la cantidad de agua necesaria, para un determinado descenso del cono. La incorporación del vidrio en la mezcla de hormigón permite la reutilización de dicho material, considerando que una gran cantidad de vidrio de desecho es tirado directamente a la basura.
Hidalgo & Poveda (2013), manifiestan que el vidrio es empleado en reemplazo parcial de los agregados tradicionales de concreto. La mezcla utilizada en la fabricación de adoquines se diseña en base a dos granulometrías de vidrio diferentes. Las proporciones al peso de la mezcla incluyen 15, 25 y 35% de vidrio.
Rojas (2017), reporta que al utilizar un porcentaje mínimo de vidrio molido obtiene una resistencia a la compresión de 318.75 Kg7cm2 a los 28 días. Además, menciona que la adherencia del vidrio molido a la mezcla no afecta su consistencia en su estado fresco.
Vargas (2016), demuestra que la utilización del vidrio molido como parte del agregado fino para la realización de morteros es muy factible. Las muestras elaboradas con vidrio plano en su composición presentaron resistencias a la compresión mayores a las obtenidas con la mezcla patrón. Los morteros con vidrio plano pueden ser usados para rellenos, repellos, adoquines, material de agarre, etc. El aumento del porcentaje de vidrio que reemplaza a la arena en la mezcla puede permitir disminuir la cantidad de cemento a emplear, debido a que el vidrio al tener mayor tamaño de partícula, su superficie específica disminuye requiriendo menor cantidad de cemento para cubrirla. Sostiene que la compatibilidad química del vidrio y del cemento es la clave para un uso satisfactorio del vidrio reciclado molido como sustituto parcial del cemento en las mezclas de concreto. Para corroborar esto, la tabla 1 muestra los contenidos principales de estos materiales, en porcentajes de sus pesos totales.
Tabla 1 - Composición química de cemento y vidrio reciclado.
Contenido | Cemento | Vidrio |
---|---|---|
SiO₂ CaO Al₂O₃ |
20.2 61.9 4.7 |
72.5 9.7 0.4 |
Nota: SiO₂ = Dióxido de silicio; Cao = Óxido de calcio; Al₂O₃ = Trióxido de Aluminio. Adaptado de “Towards broad use of recycled glass concrete on MSU campus”, por Soroushian (2012). De esta comparación el aspecto resaltante es el alto porcentaje de silicio que contiene el vidrio lo retribuye sus cualidades puzolánicas que le van a facilitar generar sus reacciones benéficas con los hidratos del cemento.
En la actualidad una de las mayores problemáticas y preocupaciones a nivel mundial es el cuidado del medio ambiente, el reciclaje de materiales reduce la contaminación, crea nuevos productos con menos inversión de materia prima, minimiza la explotación de recursos no renovables y crear nuevas fuentes energéticas y económicas, es aquí donde el reciclaje del vidrio toma importancia para este trabajo. En el sector de la construcción el concreto es el material más usado en todo el mundo y la demanda en su producción también va en aumento, lo que implica la explotación y utilización de productos naturales para su elaboración, cemento, arena, piedra y agua. Además, el proceso para la realización del cemento requiere de mucha energía (muchas veces de fuentes no renovables) lo que genera la emisión de gases que de no ser tratados contribuyen al aumento del efecto invernadero. Ante estas dos problemáticas se buscó alternativas en cuanto a los materiales utilizados para la elaboración de concreto, siendo el vidrio reciclado una opción como sustituto de los agregados y material cementante, en experimentos por separado, la propuesta evita la descarga del vidrio reciclado en rellenos sanitarios, ya que esta opción no ofrece un manejo amigable con el ambiente debido a no biodegrabilidad del vidrio, lo que incurre también en disminución de la vida útil del relleno sanitario.
La problemática en la cual se enmarca esta investigación tiene relación con tres aspectos: Ingeniería, desarrollo tecnológico y el medio ambiente. La reducción de costos asociados a la producción de materiales de construcción, ya que el vidrio reciclado es un material descartado. Innovación, en cuanto a la reutilización de este material en el concreto, cuidado del medioambiente, asociado a la reducción del volumen de residuos sólidos generados. Mediante esta investigación se pretende evaluar el efecto del uso de vidrio reciclado en el diseño de concreto. Por tanto, se formula como problema: ¿Cuál es el efecto del uso de vidrio reciclado en el diseño de mezcla de concreto?
La Asociación de Productores de Cemento (2015), en Perú informa que el concreto es tan vital para el desarrollo de productos y sistemas, que se puede utilizar en edificios ecológicos de bajo consumo y, aun así, seguirán siendo más duraderos. Hoy en día, el concreto con su resistencia, durabilidad y excelente masa térmica, debería ser un componente clave en eco-edificios para así extenderse a lo largo del futuro.
El concreto básicamente consiste en dos componentes: el agregado y la pasta. La pasta se forma con el cemento y agua, y tiene la función de unir los agregados, que son una mezcla de piedra y arena, en una masa similar a una roca. Así entonces, el cemento es el que produce la reacción química que permite el endurecimiento de la pasta, formando el concreto, y los agregados permiten mejorar la trabajabilidad, la resistencia y la disminución de costos (Williams, 2010).
Propiedades en estado fresco
Trabajabilidad y Consistencia, es la facilidad que presenta el concreto fresco para ser mezclado, colocado, compactado y acabado sin segregación y exudación durante estas operaciones.
La consistencia está definida por el grado de humedecimiento de la mezcla, depende principalmente de la cantidad de agua usada. Se determina mediante el ensayo de Slump mediante la utilización del Cono de Abrahams.
Segregación, implica la descomposición de este en sus partes constituyentes o lo que es lo mismo, la separación del Agregado Grueso del Mortero.
Exudación es la propiedad por la cual una parte del agua de mezcla se separa de la masa y sube hacia la superficie del concreto
Contracción, es una de las propiedades más importantes en función de los problemas de fisuración que acarrea con frecuencia. La pasta de cemento necesariamente se contrae debido a la reducción del volumen original de agua por combinación química, y a esto se le llama contracción intrínseca que es un proceso irreversible.
Propiedades en estado endurecido
Elasticidad, es la capacidad del concreto de deformarse bajo carga, sin tener deformación permanente. Generalmente se conoce como Módulo de Elasticidad a la relación del esfuerzo a la deformación medida en el punto donde la línea se aparta de la recta y comienza a ser curva (Rivva, 2010).
Extensibilidad, es la propiedad del concreto de deformarse sin agrietarse.
Durabilidad, es la resistencia a los agentes externos como las bajas temperaturas, la penetración del agua, desgaste por abrasión, retracción al secado, eflorescencias, agentes corrosivos, o choques térmicos, entre otros, sin deterioro de sus condiciones fisicoquímicas con el tiempo (Abanto, 2009).
Impermeabilidad, es la característica de dejar filtrar ya sea aire o agua.
El exceso de agua deja vacíos y cavidades, después de la evaporación, y, si están interconectadas, el agua puede penetrar o atravesar el concreto. La inclusión de aire, así como un curado adecuado por tiempo prolongado, suelen aumentar la impermeabilidad (Abanto, 2009).
La resistencia del hormigón a la compresión (f’c) es “la medida máxima de resistencia a carga axial de especímenes de concreto”, es decir es la propiedad del concreto de resistir cargas aplicadas. Esta medida se expresa en kilogramos por centímetro cuadrado (kg/cm2) y también en megapascales (MPa).
La resistencia a la compresión crece continuamente con el tiempo, sin embargo, los reglamentos establecen que debe darse su valor a una edad de 28 días (Araya, 2012). El aumento paulatino de la resistencia con el tiempo suele darse siguiendo un patrón de relaciones, las cuales en los últimos años han cambiado debido a la incorporación de algunos aditivos y puzolanas en la fabricación del cemento (Tabla 2). Esta nueva composición del cemento genera un desarrollo más lento de la resistencia del concreto, principalmente en las 3 primeras semanas, pero al mismo tiempo este factor ayuda a obtener concretos más resistentes, densos y durables a mediano y largo plazo (Araya, 2013).
Tabla 2 - Desarrollo porcentual de la resistencia a la compresión en el tiempo.
Edad | Resistencia 2006-2011 | Resistencia 2012-2013 |
---|---|---|
3 7 14 28 56 365 |
55% 70% 85% 100% --- 125% |
30% 50% 70% 100% --- 125% |
Fuente: Araya (2013).
La resistencia a la compresión depende de la relación agua/cemento (a/c), de cuanto ha progresado la hidratación, del curado, de las condiciones ambientales y de la edad del concreto (Williams, 2010). No obstante, de esos factores el que más influye es la relación a/c ya que entre más agua se le agrega a la mezcla menor va a ser la resistencia obtenida (Fig. 1).
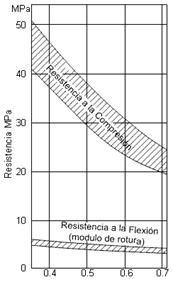
Fig. 1 - Variaciones de las relaciones A/C de concreto con la resistencia a la compresión. Adaptado de “Diseño y control de mezclas de concreto.
La Asociación de Productores de Cemento (2015), en Perú, atribuye que el concreto es el material fabricado por el hombre más utilizado en el mundo y contribuye beneficios a la sociedad, tan importantes que, sin él muchas de las cosas que vemos cotidianamente, no existirían, las principales características del concreto son:
Resistencia y durabilidad. Por su resistencia, se utiliza en la mayoría de los edificios, puentes, túneles y presas. Gana resistencia con el tiempo y no se debilita por la humedad, el moho o plagas. Las estructuras de concreto pueden soportar desastres naturales tales como: terremotos y huracanes. Un ejemplo claro son los edificios romanos con más de 1.500 años de antigüedad como El Coliseo, qué aún continúa de pie a pesar de los años gracias a la resistencia y durabilidad del concreto.
Versatilidad, el concreto se utiliza en edificios, puentes, presas, túneles, pavimentos con sistemas de alcantarillado, pistas e incluso carreteras.
Bajo mantenimiento, el concreto, siendo inerte, compacto y no poroso, no atrae a los mohos ni pierde sus propiedades con el tiempo.
Costo asequible, si comparamos con otros materiales de construcción, por ejemplo, el acero, el concreto es menos costoso de producir y sigue siendo muy asequible y duradero.
Resistencia al fuego, es naturalmente resistente al fuego ya que la concreta forma una barrea altamente eficaz para la propagación del fuego.
Relativamente bajas emisiones de CO2, las emisiones de CO2 de concreto y la producción de cemento son relativamente pequeñas en comparación con otros materiales de construcción. El 80% de las emisiones de CO2 de edificios no son generados por la producción de los materiales utilizados en su construcción, mientras que, en los servicios eléctricos de la edificación, las emisiones superan su ciclo de vida, por ejemplo, la iluminación, calefacción y el aire acondicionado.
Villegas (2012), define las puzolanas según hace referencia a la norma ASTM C 618 y N.T.P. 334.090 define a la puzolana de la siguiente manera, “Es un material silíceo o sílico-aluminoso, que finamente dividido y en presencia de agua, reacciona químicamente con el hidróxido de calcio para formar compuestos que poseen propiedades hidráulicas”.
Las puzolanas se clasifican en puzolanas naturales y artificiales, las propiedades físicas y químicas de las puzolanas se ven en la tabla 3.
Según la NTP 334.104 y ASTM C 618 (Cementos. Adiciones minerales del concreto: puzolana natural cruda o calcinada y ceniza volante. Especificaciones).
Definen tres clases de cenizas volantes:
Clase F: Ceniza volante producidas por la calcinación de carbón antracítico o bituminoso. Cenizas que poseen propiedades puzolánicas.
Clase N: Puzolanas naturales crudas o calcinadas, tal como las diatomitas; tufos y cenizas volcánicas, calcinadas o sin calcinar; y materiales que requieren de calcinación para inducir propiedades satisfactorias.
Clase C: Ceniza volante producida por la calcinación de carbón sub-bituminoso o lignito. Esta clase de ceniza, además de tener propiedades puzolánicas, también tiene propiedades cementicias.
Tabla 3 - Composición química de cemento.
Composición química | Clase de Adición mineral | N F C | |
---|---|---|---|
Dióxido de silicio+óxido de aluminio+óxido de fierro, mín., % Trióxido de azufre (SO₃), máx., % Contenido de humedad, máx., % Pérdida por calcinación, máx., % |
70,0 4,0 3,0 10,0 |
70,0 5,0 3,0 6,0 |
70,0 5,0 3,0 6,0 |
Nota: F = ceniza volante de carbón; N = ceniza natural; C = ceniza volante sub-bituminoso.
Adaptado de “Utilización de puzolanas naturales en la elaboración de prefabricados con base cementicia destinados a la construcción de viviendas de bajo costo.”, por Villegas (2012).
investiga la reacción puzolánica, mencionando aspectos como:
La reacción puzolánica es principalmente la producida entre el óxido de Silicio o sílice (SiO2), la Cal o Hidróxido de Calcio Ca (OH)2, conocido como portlandita y el agua, para producir Silicatos de Calcio Hidratados (CSH). Es una reacción equivalente a la que se da en el cemento portland y se obtiene un producto muy similar.
A continuación, primero se expondrá sobre la reacción de hidratación del cemento Portland en la cual se produce Ca (OH)2 y luego se tratará la reacción de la portlandita con las puzolanas.
Así la reacción de hidratación del cemento portland puede simplificarse, sin tener en cuenta la estequiometria ni las fases aluminosas, de la siguiente manera:
(SiO2 2CaO, SiO2 3CaO) + H2O ( CSH + CH
En esta ecuación el SiO2 2CaO, SiO2 3CaO (Silicato bicálsico y tricálcico) son los componentes principales del cemento portland y CSH (Silicato de Calcio hidratado) y CH (Hidróxido de Calcio, CaOH) son los productos de la reacción. Mientras que el (CSH) podría definirse como el “pegamento” del cemento y principal responsable de su resistencia e impermeabilidad, el (CH) no tiene valor cementante y se disuelve fácilmente en medios agresivos. La principal aportación de este compuesto es la de mantener un ambiente alcalino (Ph) alto que ayuda a proteger de la corrosión a las armaduras en el cemento armado. La capacidad cementante de estos compuestos es debida, entre otras cosas, a su estructura atómica.
El (CSH) posee una estructura altamente amorfa, con gran cantidad de ramificaciones que al entrecruzarse unas con otras forman un conjunto sólido, salpicado por partículas de (CH), cristalinas, y que suponen puntos de ruptura del entramado amorfo, creando puntos débiles en la estructura global (Fig. 2).
Los granos de cemento, al contacto con el agua comienzan a desarrollar unos filamentos a su alrededor que en su conjunto forma el denominado gel. Los filamentos de cada grano se van entrelazando con los pertenecientes a los granos vecinos y así se forma la estructura ramificada de la Fig. 3.
La reacción del cemento Pórtland con agua, mediante una serie de procesos da como resultado productos de hidratación y libera portlandita. Esta portlandita liberada, en presencia de materiales puzolánicos activos puede dar lugar a la formación de nuevos productos de hidratación, similares a los formados en la hidratación del cemento.
Debido a su pequeño tamaño de grano las puzolanas rellenan muy finamente los espacios vacíos dificultando la formación de los poros capilares que se generan en la hidratación del cemento. Es una reacción lenta, por lo que la liberación de calor también lo será, aportando estabilidad, pero retrasando el fraguado (Villegas, 2012).
Las puzolanas son componentes en base a óxidos de silicio y aluminio. Estos materiales por si solos no muestran ninguna propiedad conglomerante hidráulica. Pero cuando son finamente divididos y puestos en contacto con un material calcáreo, en presencia de agua, se activan los elementos precursores de Silicio y Aluminio del material puzolánico y esta muestra sus propiedades conglomerantes hidráulica. La activación puzolánica aquí señalada se refiere a la cantidad de hidróxido de calcio con la cual se puede combinar la puzolana y a la velocidad con la cual se produce esta reacción. Teóricamente la reacción de activación de una puzolana tomaría la siguiente forma.
Puzolana + Cal+ agua ( Silicatos y aluminatos de Calcio hidratados
Materiales básicos en el cemento
Caliza. Es una piedra natural muy abundante y dura, compuesta básicamente por carbonato de calcio (CaCO3) La harina cruda para cemento puede alcanzar los 76-80% del total.
Arcilla. Está constituida por sílice y óxido de silicio (SiO2) en un 16.26 % y asimismo óxido de aluminio (Al2O3) y óxido de fierro (Fe2O3). La principal fuente de alcalisis en el cemento es el componente arcilloso.
Homogeneización y mezcla de la materia prima
Se mezclan gradualmente hasta alcanzar la composición adecuada. El material molido debe ser homogéneo para garantizar la efectividad del proceso de clinkerización mediante una calidad constante. Este procedimiento se efectúa en silos de homogeneización
Calcinación.
Se hace pasar a los precalentadores. Se procede a calcinar en hornos, que funcionan a altas temperaturas (hasta alcanzar los 1450 grados centígrados), de modo que se "funden" sus componentes y cambia la composición química de la mezcla, transformándose en clinker. El polvo crudo es introducido mediante sistema de transporte neumático y debidamente dosificada a un intercambiador de calor por suspensión de gases de varias etapas, en la base del cual se instala un moderno sistema de precalcinación de la mezcla antes de la entrada al horno rotatorio donde se desarrollan las restantes reacciones físicas y químicas que dan lugar a la formación del clinker.
El clinker
Luego el clinker se enfría y almacena para posteriormente, ser conducido al molino final, mezclándosele con yeso (retardador del fraguado), y los materiales apropiados para la obtención del cemento correspondiente, en cantidades que depende el tipo de cemento que se quiere obtener. Como resultado final se obtiene el cemento. El horno es el elemento fundamental para la fabricación del cemento. El clinker que egresa del horno a una temperatura de 1,200 °C pasa luego a un proceso de enfriamiento rápido por enfriadores de parrilla. Seguidamente por transportadores metálicos es llevan a una cancha de almacenamiento (Quispe, 2009).
Desde este depósito y mediante un proceso de extracción controlada, el clinker es conducido junto son el yeso a la molienda de cemento por medio de molinos de bolas a circuito cerrado o prensas de rodillos con separadores neumáticos que permiten obtener una finura de alta superficie específica. El cemento es transportado por medios neumáticos para depositarse en silos donde se encuentra listo de donde se toman las muestras para analizarlo y habiendo cumplido para ser despachado. El despacho del cemento portland que produce en la planta, se realiza en bolsas de 50 kg, bolsas de 200 kg y también a granel (Quispe, 2009).
Para la elaboración del concreto los agregados también tienen un rol de gran importancia, pues ocupan un gran porcentaje del volumen de la mezcla (entre el 65 y el 75%); lo que tiene influencia en aspectos como el económico.
Las funciones en el concreto son de ser el esqueleto, reduciendo el contenido de pasta, también les proporciona resistencia a las acciones mecánicas y reduce los cambios de volumen. La función de los agregados en el concreto es la de crear un esqueleto rígido y estable lo que se logra uniéndolos con cemento y agua (pasta).
El agua
Como se ha mencionado uno de los componentes más importantes a la hora de realizar mezclas de concreto y de morteros es el agua. Dentro de las funciones que tiene el agua en el concreto es la de hidratar el cemento y dar inicio a una serie de reacciones químicas donde se combinan cemento-agua formando una pasta; este proceso es conocido como hidratación del cemento y tiene la función de ligar a todos los agregados en forma permanente una vez que ha fraguado y se ha endurecido. Asimismo, el agua ayuda a darle trabajabilidad a la mezcla cuando está recién mezclada para poder ser transportada y aplicada en la construcción.
Con respecto a la relación A/C es primordial saber qué relación se va a usar y por qué se va a utilizar esa relación, es decir conocer cuáles son las características finales requeridas del concreto. Son varios los factores que dependen de esta relación como la resistencia a la compresión cuando el concreto esté endurecido, la trabajabilidad y la consistencia cuando el concreto esté fresco (Kostmaka, et al., 2014). También está el impacto económico en la obra, una relación A/C baja implica una mayor cantidad de cemento, lo que puede subir los costos de la obra pues el cemento es el material más caro; por lo tanto, es necesario saber cuáles son las resistencias requeridas para cada parte de la obra y manejar así las cantidades de agua y cemento adecuadas (Williams, 2010).
Según Araya (2012), para hidratar el cemento se necesita un 25% de agua, o sea una relación agua/cemento de 0,25. La trabajabilidad se logra elevando esa relación hasta valores entre 0,4 y 0,8; sin embargo, la relación A/C usualmente tiene un valor entre 0,5 y 0,6.
El agua también es necesaria para el curado del concreto y el endurecimiento del mismo. Por curado se entiende como los procesos que garanticen el agua de hidratación óptima en la mezcla, de manera que se evite la pérdida de agua.
El concreto tiene que mantener su humedad para que la hidratación y el aumento de la resistencia no se vean interrumpidos. Como se ha mencionado el concreto seguirá adquiriendo resistencia con la edad y el tiempo de curado puede influenciar en ese valor (Fig. 3).
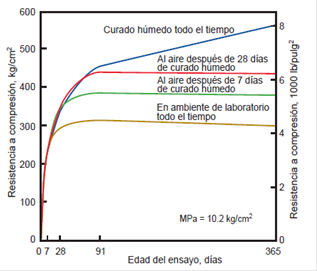
Fig. 3 - Resistencia del concreto en relación con la edad y el curado.
El agua va a ser entonces esencial para la activación de las reacciones químicas del cemento, va a ser responsable de la trabajabilidad lograda en el concreto, de la consistencia, que el concreto se endurezca conforme avanza el tiempo y de la resistencia final que tenga el concreto.
El vidrio
Meyer, et al. (2011), definen que la composición del vidrio presenta:
Arena: 43%. Procede de la roca por meteorización (efectos externos que alteran las rocas superficiales); la silícica es la más típica, por ello se suele expresar el contenido de arena de los suelos en tanto por ciento de sílice (SiO2).
Soda: 19% Es conocida químicamente como carbonato de sodio Na2CO3. Se utiliza en la fabricación de jabón, en la depuración de aguas duras y como reactivo en varias industrias químicas destacándose la fabricación del vidrio. Dado que la soda ASH es el ingrediente para la manufactura de vidrio más caro, la capacidad de reducir la cantidad requerida a través de la adición de feldespato y sienita nefelina se hizo muy atractiva. Sin embargo, en casos donde los vidrios libres de álcalis son requeridos, la alúmina tanto calcinada como hidratada es empleada en lugar de los materiales feldespáticos con el objeto de evitar la adición de álcalis.
Dolomita: 16% Mineral compuesto por carbonato de calcio y magnesio -CaMg (CO3)2 de peso específico 2, 85-2,95 y dureza 3,5-4. Se presenta en cristales incoloros, blancos o de color rosa o amarillo, de brillo vítreo nacarado. La dolomita es un constituyente fundamental de las rocas sedimentarias carbonatadas (dolomías y calizas dolomíticas). También está presente en rocas de ambiente metamórfico, ya sea mármoles dolomíticos.
Feldespato: 9% 33 La familia de los minerales llamados genéricamente "feldespatos", comprende un grupo de aluminosilicatos relacionados entre sí, con cantidades variables de potasio, sodio y calcio y de forma menos común con otros cationes (bario, hierro, plomo, rubidio y cesio), en series de minerales en solución sólida. Los principales feldespatos comerciales son: el sódico - cálcico (albita y oligoclasa, de bajo contenido en calcio en la serie de minerales albita-anortita) y el potásico (microclino y ortoclasa), entre otros.
Casco: 12% Pedazos o desechos de vidrio.
Los agregados menores: 1% son los afinantes, colorantes y descolorantes.
Según la American Society for Testing Materials (ASTM), el vidrio es un: “Producto inorgánico de fusión, el cual se ha enfriado hasta un estado rígido, pero sin sufrir cristalización.” De manera general, existe una confusión entre vidrio y cristal. Si bien estos materiales pueden tener la misma composición, pero poseen una ordenación diferente de su estructura atómica. Mientras que en el cristal los átomos permanecen ordenados, en el vidrio estos se presentan de forma desordenada, dando lugar a lo que llamaríamos un material amorfo. La estructura del vidrio se vuelve más discontinua, este funde a menor temperatura y resulta fácil de manejar. El vidrio resultante es más económico a la hora de la fabricación (Fig. 4).
El vidrio presenta cierta transparencia, su estructura es amorfa, reduce su viscosidad en función de la temperatura, etc., por lo que este comportamiento se asemeja mucho al de cualquier líquido. Por lo que el vidrio podría ser definido más claramente como un líquido con una viscosidad tan alta que le proporcionaría un aspecto de sólido, sin serlo.
En cuanto a la composición, el principal componente del vidrio es la sílice, además del óxido de sodio, óxido de calcio, óxido de aluminio y componentes secundarios.
Las características generales de estos componentes son:
La sílice (SiO2): es el constituyente más importante conformando las tres cuartas partes de su composición, se lo obtiene de las arenas de cuarzo.
El óxido de sodio: tiene por finalidad el favorecer la formación de vidrio, rebajando su temperatura de fusión y así facilitar su elaboración, son conocidos como fundentes.
El óxido de calcio: su presencia aumenta la estabilidad química y mecánica del vidrio, por lo que desde el punto de vista funcional actúa como estabilizante.
El óxido de aluminio es un estabilizante, añadiéndole además ciertas características como: aumento de la resistencia mecánica, un mejoramiento de la estabilidad química, una elevación de la refractariedad, una disminución del coeficiente de dilatación térmica y una mejor resistencia al choque térmico.
En la composición de los vidrios, también se observan otros constituyentes minoritarios con funciones determinadas como colorantes, afinantes, decolorantes, opacificantes, etc., haciendo especial mención a los fluoruros en su papel de fluidificantes (Meyer, et al., 2011).
Acción cementante del vidrio
Se considera posible la incorporación del vidrio en la industria cementera debido a que el vidrio posee grandes proporciones de sílice y de calcio convirtiéndolo en teoría en un compuesto puzolánico o incluso del cemento, así como también comparte características con las arenas que se utilizan como agregado finoAdemás, el concreto provee una solución de largo plazo a la disposición del vidrio. La reacción Alcali-Silica (ASR, por sus siglas en inglés) es la formación de un gel el cual se expande por el concreto causando el agrietamiento del mismo de manera prematura. Shayan & Xu (2014), explican que la formación de este gel se debe a que el vidrio por tener alto contenido de sílice y una estructura amorfa es susceptible a un ataque químico de condiciones altamente alcalinas, las cuales presenta la pasta de cemento.
Esta reacción tiende a darse mayormente cuando el vidrio utilizado tiene tamaños grandes, mientras que el vidrio finamente molido no suele afectar pues por el contrario presenta propiedades puzolánicas evitando la ASR (Shao, et al., 2000). Partículas de vidrio de tamaño mayor a 1.2 - 1.5 mm son potenciales para que ocurra la ASR en el concreto, esto quiere decir que al utilizar partículas de este tamaño o mayores no necesariamente se va presentar dicha reacción, pero sí que existe el riesgo de darse por lo que se deben tomar medidas y precauciones a la hora de realizar concretos con estas características como por ejemplo agregar cenizas volátiles (Shayan & Xu, 2014).
Es importante destacar que esta reacción no es exclusiva de concretos en los que se utilicen vidrio como agregado ya que también puede ocurrir en el concreto convencional si los agregados utilizados contienen minerales silicios (Meyer, et al., 2011).
En cuanto a los usos del vidrio en la industria constructora, el vidrio como agregado grueso es la menos recomendable sin embargo se puede utilizar en pequeñas cantidades. Esto debido a que su naturaleza plana y alargada afecta la trabajabilidad (para agregado grueso es recomendable que se tenga una superficie rugosa), lo que genera uniones débiles entre el agregado y la pasta disminuyendo la resistencia a la compresión; además el manejo se hace más difícil pues se requiere Equipo de Protección Personal en todo momento por el riesgo a cortadura. Mezclas de concreto de este tipo no se puede realizar sin tomar en cuenta la ASR pues las posibilidades que dicha reacción suceda son mayores.
El vidrio como agregado fino es mayormente recomendado por la literatura pues no produce cambios notables en las propiedades del concreto, tiende a aumentar la resistencia a la compresión, especialmente a largo plazo, mejora las propiedades térmicas del concreto, no afecta la durabilidad del concreto, además si el vidrio es molido de manera fina éste no contribuye a la ASR. Sin embargo, la característica que mayormente se ve afectada por el vidrio es el asentamiento del concreto y la trabajabilidad, esta última se puede mejorar agregando más agua a la mezcla (Ismail & Al-Hashmi, 2009; Jani & Hogland, 2014).
Se expone entonces como objetivo general: Determinar el efecto de sustituir el cemento y agregados por separado en diferentes niveles y porcentajes de sustitución por vidrio reciclado en porcentajes de 25% y 50% de la proporción en peso, en diseños de mezcla de concreto.
Objetivos específicos
Activar mecánicamente el vidrio reciclado.
Elaborar probetas de 15×30 cm, de concreto utilizando partículas de vidrio reciclado en porcentajes de sustitución de los agregados 0%, 25%, 50%.
Elaborar probetas de 15×30 cm, de concreto utilizando polvo de vidrio reciclado en porcentajes de sustitución del cemento 0%, 25%, 50%.
Comparar la resistencia del concreto a los 28 días de curado en los diferentes niveles y porcentajes de sustitución, de las probetas de concreto utilizando vidrio reciclado.
Materiales y métodos
Por su forma la presente investigación es aplicada porque indaga actividades aglomerantes de materiales concretos como el vidrio reciclado, considerándolo un material constructivo alternativo determinado como la mezcla de concreto y evaluar el incremento de su resistencia. Por su tipología esta investigación es longitudinal y experimental. Longitudinal, porque las evaluaciones de la resistencia de las mezclas del concreto en forma de probetas se evalúan en base a sus edades de 28 días. Y es experimental, puesto que introducimos diferentes niveles de sustitución (25,50 %).
En base a lo expuesto el diseño de investigación es experimental porque contempla la medición de la resistencia a la comprensión de las probetas sustituidas por los nuevos materiales, para luego compararlas con la resistencia de probetas patrón sin sustitución.
La población lo constituye, las probetas cilíndricas elaboradas en dimensiones de 15×30 cm. La muestra lo constituye, el grupo de 50 probetas cilíndricas elaboradas en dimensiones de 15×30 cm (Tabla 4 y 5).
Tabla 4 - Diseño muestral de sustitución de agregado por partículas de vidrio reciclado.
Días de curado | Porcentaje de sustitución | 0% 25% 50% | |
---|---|---|---|
28 |
CP01, CP02, CP03, CP04, CP05, CP06, CP07, CP08, CP09, CP10. |
CA2501, CA2502, C A2503, CA2504, C A2505, CA2506, CA2507, CA2508, CA2509, C A2510. |
CA5001, CA5002, CA5003, CA5004, CA5005, CA5006, CA5007, CA508, CA5009, C A5010. |
Los residuos urbanos del vidrio reciclado se generan de diversos envases de alimentos, bebidas, e insumos médicos. Los recicladores los colectan, los clasifican por colores y los pre-trituran, por la carencia de equipo y por seguridad en los manejos iniciales de las muestras del vidrio reciclado (Fig 5 y 6).
La activación mecánica de las muestras del vidrio reciclado consistió en dos niveles de activación.
Primer nivel activación mecánica por trituración, tamaño de partícula, tamaño máximo nominal, 17 mm. Sustitución de agregados por partículas de vidrio reciclado.
Segundo nivel activación mecánica por molienda, tamaño de partícula, tamaño máximo nominal, 74 um. Sustitución de cemento por polvo de vidrio reciclado (Fig.7, 8 y 9).
Resultados y discusión
Tabla 6 - Resistencia a la compresión concreto control.
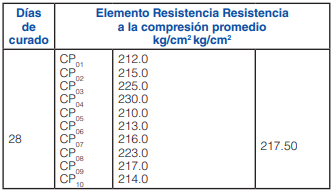
Nota: CA= Concreto control, porcentaje de sustitución 0%.
Tabla 7 - Resistencia a la compresión en probetas con sustitución de agregados al 25%.
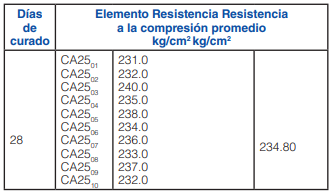
Nota: CA25= Concreto experimental, sustitución de agregado por partículas de vidrio reciclado. Porcentaje de sustitución 25%.
Tabla 8 - Resistencia a la compresión en probetas con sustitución de agregados al 50%.
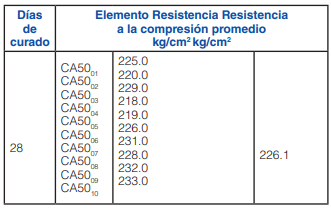
Nota: CA50= Concreto experimental, sustitución de agregado por partículas de vidrio reciclado. Porcentaje de sustitución 50%.
Tabla 9 - Resistencia a la compresión en probetas con sustitución de cemento al 25%.
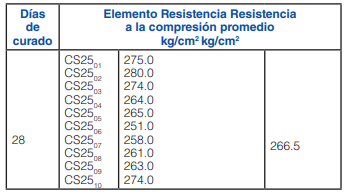
Nota: CS25= Concreto experimental, sustitución de cemento por polvo de vidrio reciclado. Porcentaje de sustitución 25%.
Tabla 10 - Resistencia a la compresión en probetas con sustitución de cemento al 50%.
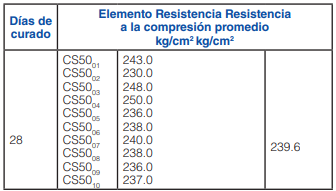
Nota: CS50= Concreto experimental, sustitución de cemento por polvo de vidrio reciclado. Porcentaje de sustitución 50%.
En la bibliografía consultada, se detalla que la composición química del cemento presenta los siguientes óxidos: CaO 60-67% SiO217-25% Al2O38% Fe2O30.5-6%
El proceso de fusión (Tabla 6) de la materia prima que ha de dar origen al Clinker se forman silicatos cálcicos, aluminatos cálcicos y ferritos de composición compleja. De ellos los componentes básicos del cemento son los silicatos cálcicos. La fórmula de composición de los cuatro compuestos principales, así como la forma abreviada de los mismos es:
Silicato Tricálcico: 3CaoSiO2=C3S 30-60 %
(Alita). Favorece un rápido endurecimiento del cemento. Al endurecer a gran velocidad, contribuye en forma importante a las resistencias mecánicas iniciales. Su contribución a la resistencia mecánica final no es tan importante en comparación con el silicato bicálcico.
Silicato Bicálcico: 2CaoSiO2=C2S 15-37 %
(Belita). Su contribución en el desarrollo de la resistencia inicial es poco. Fuente principal del desarrollo de la resistencia en el tiempo.
Aluminato Tricálcico: 3Cao Al2O3=C3A 7-15 %
Contribuye al desarrollo de resistencia durante las primeras 24 horas. Posteriormente su aporte a la resistencia es prácticamente nulo.
Ferroaluminato Tetracálcico: 4CaO.Al2O3.Fe2O3=C4AF 8-10 %
(Fase ferrítica). Papel aún no definido. La resistencia disminuye con el aumento de este compuesto, ligera tendencia a la contracción, no siempre acompañada de la formación de grietas capilares, durante los procesos de fraguado y endurecimiento.
Al analizar la composición química del vidrio reciclado podemos apreciar
79.647% de SiO2 (Dióxido de Sílice), es un compuesto de silicio y oxígeno, llamado comúnmente sílice. Este compuesto ordenado espacialmente en una red tridimensional (cristalizado) forma el cuarzo y todas sus variedades. Si se encuentra en estado amorfo constituye el ópalo, que suele incluir un porcentaje elevado de agua, y el sílex. Es uno de los componentes de la arena. Siendo los compuestos difícilmente solubles, se produce un precipitad cuando se mezcla una solución que contienen sílice con otra que contiene cal, produciéndose un cuerpo sólido. La presencia de este compuesto en alto porcentaje en nuestro material es un indicador de que nuestro material podría ser considerado cementante.
1.337% de Al2O3 (Trióxido de Aluminio), conocido como Alúmina, es un polvo blanco de elevada dureza y resistencia media. Está presente en la naturaleza en forma de corindón y de esmeril. Su obtención puede realizarse de forma sintética a partir de la bauxita. Dada su gran dureza y elevado punto de fusión el óxido de aluminio suele utilizarse como: Aislante térmico, dispositivo refractario, esmaltes y cerámicas (proporciona dureza). Rivva (2010), menciona que la alúmina reacciona con la arcilla, además puede unirse en combinación geliforme con la cal y el agua. A su vez menciona que un material cementante debe tener entre 3-8 %, siendo esto un déficit en nuestro material para ser considerado cementante.
7.465% de CaO (Óxido de Calcio), conocido como cal, es el componente más importante del cemento, se puede encontrar en la naturaleza de la aglomeración del agua marina, la cual posee concentraciones de carbonato de calcio y magnesio. Existe déficit en nuestro material al ser menor que el mínimo 60%, lo cual tal como indica Rivva (2010), en el análisis de las combinaciones cal-sílice, se presentan condiciones distintas ya que se entra en el campo de las dimensiones coloidales a las cuales se debe en parte a la alta resistencia de los cementos.
Al analizar los resultados del concreto control, se observa que la resistencia a la compresión promedio a una edad de 28 días, es de 217.50 kg/cm2.
En la tabla 7 se aprecia que una sustitución del 25 % del agregado por el vidrio reciclado, a los 28 días de edad, alcanzando una resistencia de 235.60 kg/cm² superando al patrón en 8.0%. En la tabla 8 se aprecia que una sustitución del 50 % del agregado por el vidrio reciclado, a los 28 días de edad, alcanzan una resistencia de 266.10 kg/cm² superando al patrón en 4.0%. De la comparación de las resistencias con respecto a los niveles de sustitución del agregado por las partículas de vidrio reciclado, queda claro que el mejor desarrollo de las resistencias de las probetas sustituidas corresponde al nivel de sustitución del 25 %.
En comparación con los resultados obtenidos por otros autores se puede observar que las resistencias a la comprensión de las mezclas realizadas en este estudio estuvieron por debajo de las obtenidas por los autores citados. Si bien, las características de cada estudio son diferentes y por lo tanto los resultados siempre van a diferir, se puede realizar una pequeña comparación, especialmente con el estudio de Ismail & Al-Hashmi (2009), el cual tenía condiciones similares al presente, el estudio de este autor obtuvo una f’c de 468 kg/cm2 para una proporción de 20% vidrio y 80% arena en el agregado fino, valor muy elevado en comparación al obtenido en este estudio. No obstante, varios autores afirman que entre mayor sea la proporción de vidrio dentro de los agregados la resistencia la comprensión va a tender a disminuir (Jani y Hogland, 2014). Razón por la cual es importante continuar este estudio buscando la relación de vidrio-arena en donde las características del concreto sean las óptimas, incluyendo la resistencia a la comprensión y la consistencia de la mezcla.
En la tabla 9, la resistencia de las probetas con sustitución del 25 % del cemento por polvo de vidrio reciclado a los 28 días alcanzaron una resistencia de 266.50 kg/cm², que supera al patrón en 22.50 %. En la tabla 10 y 11, para las muestras con sustitución al 50 % con polvo de vidrio reciclado alcanza una resistencia a los 28 días de 239.60 kg/cm², superando al patrón en 10.1 %. De la comparación de las resistencias con respecto a los niveles de sustitución del cemento por polvo del vidrio reciclado, queda claro que el mejor desarrollo de las resistencias de las probetas sustituidas corresponde al nivel de sustitución del 25 %. Una probable explicación de este resultado sería que, a esta proporción, los altos contenidos de silicio y calcio contenidos en el vidrio reciclado complementarían en proporciones óptimas al 90% del cemento aún presente en las mezclas del concreto sustituido. Comparando nuestros resultados con los antecedentes reportados a nivel internacional, se tiene que para un 10 % de sustitución del cemento por polvo de vidrio reciclado en mezclas de concreto, el grupo de Vijayakumar, et al. (2013), reportan para una edad de 28 días una resistencia de 305.7 kg/cm², que es del mismo orden de nuestro resultado que fue de 306.43 kg/cm². Este es un resultado alentador, teniendo en cuenta que el tamaño de partícula del grupo de Vijayakumar 76µm y por lo tanto más reactivo puzolánicamente. Soroushian (2012), reporta un nivel de sustitución de 10%, alcanzando una resistencia a la compresión de 421.80 kg/cm².
Esta diferencia se explica debido a que el tamaño de partícula del material activado de Soroushian (2012), fue menor a 46 µm, muy inferior y por ende más reactivo que el tamaño de partícula del nuestro que fue tan solo de 150 µm. La resistencia de las probetas con sustitución del 5 % del cemento por polvo de vidrio reciclado a los 28 días alcanzaron una resistencia de 263.82 kg/cm², que supera a la patrón en 14.48 %. Para las muestras con sustitución al 10 % con polvo de vidrio reciclado alcanza una resistencia a los 28 días de 306.43 kg/cm², superando al patrón en 32.97 %; por último, en sustitución del 15 % del cemento por el polvo de vidrio reciclado, a los 28 días de edad, alcanzan una resistencia de 276.03 kg/cm² superando al patrón en 19.77%. De la comparación de las resistencias con respecto a los niveles de sustitución del cemento por polvo del vidrio reciclado, queda claro que el mejor desarrollo de las resistencias de las probetas sustituidas corresponde al nivel de sustitución del 10 %.
El análisis para el caso del vidrio se sustenta en la figura 10. En esta figura se tomarán las resistencias alcanzadas a los 28 días con los diferentes niveles de sustitución de 25 %, 50 % del cemento por el polvo de vidrio reciclado y del 25% y 50% del agregado por las partículas de vidrio reciclado.
Concreto Control: 217.50 kg/cm2
Fase uno de sustitución: Cemento por polvo de vidrio reciclado
Concreto sustituido cemento en 25%: 266.50 kg/cm2
Concreto sustituido cemento en 50%: 239.60 kg/cm2
Fase dos de sustitución: Agregado por partículas de vidrio reciclado
Concreto sustituido agregado en 25%: 234.80 kg/cm2
Concreto sustituido agregado en 50%: 226.10 kg/cm2
Conclusiones
El vidrio reciclado ha sido activado mecánicamente por proceso de molienda a un tamaño de partícula de 74 um, valor alcanzado muy cercano al tamaño de partícula del cemento 40 um.
Los resultados obtenidos muestran que el vidrio reciclado particulado ha sido capaz de sustituir satisfactoriamente al agregado en porcentajes de 25 y 50 % en mezclas de concreto. Considerando que el vidrio reciclado ha logrado sustituir a los agregados áridos, estaríamos ante un material que se obtuvo a partir de residuos, alivianando así la gestión de residuos sólidos en la localidad, así como la disminución en cuanto al costo del concreto.
Los resultados obtenidos muestran que el polvo de vidrio reciclado ha sido capaz de sustituir satisfactoriamente al cemento en porcentajes de 25 y 50 % en mezclas de concreto. Considerando que el polvo de vidrio reciclado de 74 um, ha logrado sustituir al cemento Portland de 40 um, estaríamos ante un material que se obtuvo a partir de residuos, a relativas bajos tiempos de trituración que el cemento, ello implica una contribución hacia un bajo costo y menor contaminación.
Del nivel de sustitución los mejores resultados para las resistencias en compresión obtenidas son: 25 % para el polvo de vidrio reciclado (266.50 kg/cm2) y 25% para el vidrio reciclado particulado (235.60 kg/cm2), en sustitución del cemento y agregado respectivamente, frente al concreto control de 217.50 kg/cm2.
La inclusión de vidrio reciclado en diseño de mezcla de concreto ha sido óptima en los diferentes niveles de sustitución y porcentajes.