Introducción
Debido a la necesidad de cambios en la matriz energética cubana, por diferentes problemas económicos y política, a finales de la década de los años 90, fue necesario sustituir el combustible (fuel switching) en la generación de electricidad. El combustible de importación (fuel oíl), fue sustituido por crudos nacionales mezclados con combustible de importación en diferentes proporciones. Para realizar este cambio, se llevó a cabo un proceso inversionista de modernización de las instalaciones existentes. En esas primeras modernizaciones, se utilizó el quemador francés France Thermique, que cuenta con atomizadores con cámara de mezcla con un consumo elevado de vapor de atomización. Unos años después, algunos de esos quemadores fueron sustituidos por quemadores alemanes de la firma M&S, con atomizadores de menor consumo de vapor de atomización, lo cual significó una mejora en el consumo específico de las unidades. Los bloques de las centrales térmicas Carlos Manuel de Céspedes y Antonio Guiteras, disponen de sistemas de atomización más eficientes, del tipo ¨YJet¨, que, con una preparación adecuada del combustible, pudieron asimilar el cambio. Estas y otras acciones en los sistemas de preparación y manipulación del combustible, permitieron utilizar el combustible nacional en las centrales termoeléctricas del país.
Después de varios años de explotación, los problemas con la disponibilidad y las averías por fallas de tubo, se han multiplicado, debido a la obsolescencia y el deterioro de estas instalaciones, en especial de los quemadores y los lazos para el control automático del proceso de la reacción en función de la carga. Además, hay que resaltar que el proceso de combustión del crudo mejorado es complejo y requiere de cuidados especiales, debido a la agresividad de sus constituyentes, azufre (S - hasta 8 %), asfaltenos (hasta 18 %), sodio (Na - hasta 280 ppm) y vanadio (V - hasta150 ppm).
En el mercado nacional cubano, se comercializan tres variantes del petróleo crudo nacional mejorado (PCNM), que de acuerdo a su viscosidad cinemática se dividen en:
Una buena utilización del petróleo crudo nacional mejorado, requiere del control riguroso del proceso de combustión dentro del horno, unido a un adecuado empleo de aditivos, lo que define las características de los procesos sucesivos de transferencia de calor, ensuciamiento y corrosión que determinan la disponibilidad de la central termoeléctrica. El suministro desigual de aire y combustible entre quemadores, la atomización deficiente y ¨coeficientes de exceso de aire¨ elevado, minimizan el efecto del aditivo, lo que trae consigo, consecuencias graves y extremadamente costosas en términos de disponibilidad y eficiencia de la planta. Como se conoce, los tubos de las calderas durante la operación, están sujetos a condiciones adversas, como alta presión, alta temperatura, corrosión por alta y baja temperatura, cenizas volantes abrasivas y la naturaleza corrosiva propia del agua. Los fallos en tubos se producen cuando la suma de estas adversidades y sus efectos (pérdida de espesor por corrosión, alta carga térmica local - sobrecalentamiento, erosión etcétera.), supera los límites que pueden soportar los materiales de los tubos, que por lo regular son de acero al carbono y acero de baja aleación. Alrededor de 99,5 % de los metales utilizados para tubos de calderas subcríticas (hasta 600 MW), son de acero al carbono y acero de baja aleación (Ansuman, 2021).
En estos procesos de combustión ocurren lo siguientes mecanismo de corrosión, ensuciamiento y emisiones durante la combustión de los combustibles pesados.
En la combustión, el azufre del combustible reacciona con el oxígeno y forma óxido de azufre . La primera conversión de
, ocurre en el horno, en función del contenido de azufre en el combustible, el exceso de aire y la temperatura de la llama. La reacción tiene lugar si la temperatura es suficientemente alta para formar oxígeno atómico por disociación.
La segunda conversión de a
, es por el efecto catalítico en presencia de
y
que a su vez depende de la temperatura, logrando una alta conversión en el rango de 550 °C a 900 °C. Existe una fuerte dependencia de la combinación, exceso de aire y temperatura para la formación del . Por ejemplo, para 2 % de exceso de aire
, la razón de conversión de
a
a 620 °C es de 8 %, mientras que para 10 % de exceso de aire
, la razón de conversión alcanza 19 % (Poullikkas, 2004). El más eficiente efecto catalítico, es debido al pentóxido de vanadio con determinada formación de compuestos intermedios inestables, donde el
, actúa como portador de oxígeno. Esto es posible debido al incremento de las deposiciones con elevadas temperaturas, lo que propicia las condiciones favorables para la reacción. Por tanto, mientras mayor sea el contenido de vanadio en el combustible y mientras más se demore la transformación del
a una forma menos activa catalíticamente como los vanadatos alcalino-térreos, mayor será la cantidad de
formada y por lo tanto, existirán más posibilidades de formación del ácido sulfúrico (
). El
vapor, comienza su condensación a temperaturas por debajo de 150 °C aproximadamente, convirtiéndose en altamente corrosivo al atacar las superficies ferrosas. El ácido sulfúrico se condensa sobre la superficie fría del metal en la parte interna del calentador de aire, con una alta concentración que varía de 50 % a 70 %. El condensado de ácido sulfúrico, produce una película viscosa que favorece la captura de partículas del flujo de gas, dando lugar a deposiciones carbonosas pastosas. Estas deposiciones se vuelven inestables debido a su espesor, y son arrastradas fácilmente por el flujo de gases de combustión y emitidas por la chimenea como aglomerados ácidos (Poullikkas, 2004).
El también puede combinarse con los óxidos metálicos presentes, para formar sulfatos. De los sulfatos metálicos que pueden formarse, el sulfato sódico
, es el principal responsable de la corrosión de las superficies metálicas. A temperaturas elevadas, cuando alcanza su punto de fusión, la velocidad de corrosión de las sales de sodio se incrementa significativamente. El sulfato sódico funde a 888 °C, y cuando hace contacto con superficies ferrosas se produce la corrosión del hierro (Poullikkas, 2004; Носков & Пай, 2016).
El vanadio contenido en el combustible, en la combustión, reacciona con el oxígeno formando diferentes óxidos y
. Siendo el pentóxido de vanadio
, el más corrosivo, debido a que el carácter ácido, se incrementa con el grado de oxidación. En hornos con un alto coeficiente de exceso de aire y una alta temperatura, están creadas las condiciones favorables para la formación del pentóxido de vanadio. El punto de fusión del
está alrededor de 690 °C. Cuando se deposita origina efectos altamente nocivos (Documento técnico RB 7 2016):
Cataliza la reacción de oxidación del
a
. (expuesto anteriormente)
Corrosión de las superficies metálicas para formar metavanadatos de hierro ( . Una parte del pentóxido de vanadio por su reactividad forma sales (vanadatos) preferentemente con los metales alcalinos y alcalino-térreos. Los vanadatos alcalino-térreos (vanadatos de calcio y magnesio) presentan un punto de fusión elevado (de 1100 °C a 1200 °C), por lo que, generalmente, después de la combustión se encuentran en estado sólido, y son arrastrados por los gases en forma de particulado (Documento técnico RB 7 2016).
Dentro de los vanadatos alcalinos, los vanadatos sódicos, presentan punto de fusión mucho más bajo (de 350 °C a 650 °C), por lo que en una amplia zona del circuito de gases se encuentran en estado líquido. Estos vanadatos, son muy reactivos con el hierro y el óxido de hierro, a los cuales disuelven, para formar sulfovanadatos dobles, sobre todo en presencia de sulfato sódico.
Los depósitos duros que se adhieren a los tubos, no solo intervienen en el proceso de corrosión, sino que provocan el ensuciamiento y el bloqueo de los sobrecalentadores, sobre todo cuando el paso entre los tubos es estrecho. Son extremadamente difíciles de eliminar con el sistema de sopladores de hollín o durante las limpiezas. El bloqueo de los pases de gases puede ocurrir acompañado de escoria en las paredes de la cámara del horno. Si el nivel de sodio y la relación sodio/vanadio se incrementa, los problemas de corrosión y ensuciamiento a alta temperatura se multiplican.
Los compuestos resinoso-asfalténicos contenidos en el combustible nacional, se caracterizan por su gran diferencia en cuanto a la solubilidad, por ejemplo, los asfaltenos son solubles en variados disolventes orgánicos, los carbenos sólo en sulfato de carbono y los carboides no se disuelven en ningún tipo de disolvente, por lo que también se les llama coque. Khateeb et al. (2018).
En concentraciones superiores a 1 %, los carboides son propensos a separarse de la masa de combustible, formando deposiciones de coque sobre los tubos y las superficies interiores de los atomizadores. Con el incremento de la densidad de los crudos y de los combustibles residuales, la cantidad de sustancias resinoso-asfalténicas aumenta y tiene lugar un incremento de la viscosidad.
Los asfaltenos son los compuestos más macromoleculares del petróleo, por su aspecto exterior son sustancias de color pardo o negro con una densidad relativa superior a la unidad y un alto peso molecular (Rodríguez al et., 2006)
En la combustión, a medida que las gotas de combustible atomizado avanzan hacia el frente de llama, se vaporiza la fracción ligera de las mismas, combustionan los volátiles, y los asfaltenos se aglomeran y en un proceso lento, tiene lugar la combustión de los mismos. Los hidrocarburos sólidos de gran tamaño, son muy difíciles de quemar, ya que su combustión tiene lugar en fase sólida. La combustión en fase sólida, se produce por la difusión del oxígeno, a través de la superficie de la partícula. Como el tiempo de quemado de un sólido es proporcional al cuadrado de su diámetro equivalente, (y a la vez está relacionado con el diámetro de la gota), la aglomeración de los asfaltenos sólidos, se suma a la cadena de dificultades de su proceso de combustión, debido al sensible incremento del tiempo requerido para la combustión (Rodríguez et al., 2020). El residuo de carbón que se deposita en las paredes exteriores de los tubos de las calderas en forma de escoria, tiene un efecto termoaislante que provoca una pérdida en la eficiencia y bloquea el paso de los gases.
La combustión, da como resultado la formación de emisiones de óxidos de nitrógeno, denominados . Los dos más importantes son el óxido de nitrógeno () y el dióxido de nitrógeno (
La formación de
, se incrementa con la temperatura, mientras que la proporción de (
, disminuye. Lo que indica que la mayor parte del
que se forma durante la combustión consiste en
, que luego se oxida en la atmosfera formando el (
. Hay tres mecanismos de reacción a través de los cuales tiene lugar la formación de los óxidos de nitrógeno:
El
- combustible: es el que se genera como resultado de la reacción entre el oxígeno del aire de la combustión y el nitrógeno contenido en el combustible. La conversión del nitrógeno del combustible a
, es altamente dependiente de la estequiometría local de la llama.
El
- térmico: se produce por la reacción del nitrógeno molecular del aire con el oxígeno del propio aire. La reacción ocurre cuando la energía térmica disponible es alta, debido a eso, su formación tiene lugar en los puntos de alta temperatura de la llama.
- rápido: Se genera a partir de la reacción del nitrógeno atmosférico con fracciones de hidrocarburos en las zonas circundantes a la llama. La reacción se favorece en las zonas ricas en combustible, donde abundan las fracciones de hidrocarburos.
El - térmico, es el mecanismo predominante en los procesos de combustión a temperaturas por encima de 1100 °C (Rodríguez et al., 2020; López et al., 2022).
En el trabajo se presentan las experiencias de los autores, relacionadas con el desarrollo de un método propio, dedicado al ajuste, centrado, alineamiento y fundición de las gargantas refractarias de los quemadores y su relación con la eficiencia del proceso de combustión con bajo ¨exceso de aire¨, lo cual es imprescindible para hacer efectiva la aplicación de aditivos químicos para el control de la corrosión y el ensuciamiento de las calderas de las centrales termoeléctricas. Se describe la incidencia que tienen los aspectos teórico-prácticos que relacionan la calidad de la atomización del combustible y su correspondencia con el esquema aerodinámico, para obtener un proceso de combustión eficiente con mínimo ¨exceso de aire¨. Además, se relacionan los parámetros que determinan el funcionamiento eficiente de los hornos prismáticos en calderas multi-quemadores, como el desbalance de aire y combustible, el tiempo requerido por la reacción de combustión y el disponible de los gases dentro del horno, para diferentes condiciones de temperatura y carga térmica, como elementos claves, para elevar la eficacia en el uso de los aditivos químicos y de este modo elevar la disponibilidad de las calderas de las termoeléctricas.
El objetivo del presente trabajo, es contribuir al esclarecimiento de la estrecha relación que existe entre la eficiencia del proceso de combustión con bajo oxígeno y los procesos sucesivos de formación de compuestos no deseados que dan lugar a:
Emisiones gaseosas que contaminan el medio ambiente
Procesos de corrosión que provocan averías en los tubos de las calderas
Formación de depósitos sobre las superficies de los tubos que afectan la transferencia de calor
Formación de compuestos sólidos, que bloquean el paso de los gases
Pérdida de eficiencia y disponibilidad de las unidades de generación de vapor
Materiales y métodos
La realización del presente trabajo, se ha basado en los reportes de los resultados obtenidos de las centrales termoeléctricas, donde ha sido aplicada la tecnología de mantenimiento desarrollada por los autores, para elevar la eficiencia de los quemadores de las centrales termoeléctricas con bajo ¨exceso de aire¨. El método permite optimizar el ajuste, centrado, alineamiento y la fundición de las gargantas refractarias, así como rectificar los ángulos de inclinación en los diferentes planos indicados en el proyecto de la caldera.
Para aplicar esta tecnología, fue necesario crear un dispositivo especial que consta de una barra que prolonga el portacañas al interior del horno, sobre la cual se instalan diferentes herramientas de medición y accesorios, que permiten comprobar con precisión, la circularidad y el centrado de las diferentes partes del quemador. El dispositivo, dispone de goniómetros para rectificar los ángulos de montaje que deben tener los quemadores, para evitar el solapamiento entre llamas, e incidencias de las llamas sobre los elementos del horno. Las gargantas refractarias son fundidas con moldes desarmables, que se instalan sobre la barra, para garantizar con exactitud sus dimensiones y ubicación axial y concéntrica al eje del quemador. TESTO (2018).
Resultados y discusión
Las calderas de las termoeléctricas que operan con combustibles líquidos, utilizan quemadores de torbellino. Estos quemadores, para lograr el anclaje y la estabilidad de las llamas en la garganta de salida, emplean dispositivos aerodinámicos estabilizadores, que basan su funcionamiento en establecer corrientes inversas de flujo en una determinada zona, a la cual se le denomina zona de recirculación interna (ZRI). El modelo de flujo que se genera detrás de estos dispositivos resulta muy complejo, debido al alto nivel de turbulencia que se alcanza dentro de la corriente. La estructura aerodinámica que se forma detrás de los estabilizadores, está caracterizada por el grado de torbellino (S). Los métodos más usados para reducir la caída de presión en quemadores de torbellino con altos niveles de estabilidad y eficiencia, se basan en el uso de torbellinos fuertes . Las corrientes giratorias empleadas para lograr estos fines, son estudiados cuidadosamente en cámaras de combustión y quemadores (Valera-Medina & Syred, 2009; Rodríguez & Rosabal, 2017; Rodríguez, 2011; Rosabal, 2006), y hacen énfasis en sus características tridimensionales para asegurar la estabilidad e incrementar el tiempo de residencia de las partículas activas y los productos de la combustión.
En la figura 1, se presenta el esquema principal de organización del proceso de combustión de un combustible líquido. La combinación de las dos corrientes de aire, primario y secundario al pasar a través de los dispositivos estabilizadores de llama, giran de forma concéntrica al eje del quemador, y se crea la ZRI. La mezcla de aire y combustible que ha comenzado a combustionar, retorna a la raíz de llama, por el enrarecimiento provocado por la ZRI. Este flujo de partículas incandescente denominado flujo másico reverso, es el encargado de mantener un nivel adecuado de temperatura en el centro de la llama, para que la nueva mezcla fresca, se inflame y comience su reacción de combustión de forma estable. A este trabajo o función del quemador, se le denomina estabilidad del proceso de combustión. En las termoeléctricas a los dispositivos estabilizadores de llama, se les conoce como difusores. Entre los estabilizadores de llama o difusores que más se utilizan en el diseño de quemadores, están los platos estabilizadores (bluff body), y los que generan corrientes giratorias (swirlers). De forma general, los generadores de corrientes giratorias, se pueden clasificar como: axiales simples, tangenciales simples, axiales tangenciales y de voluta (Rodríguez et al., 2020). Hay que destacar que cada elemento estabilizador, está diseñado para una función aerodinámica particular, que define características especiales en la configuración de la llama y en la eficiencia del proceso de combustión, por lo que se hace imprescindible mantener todas sus dimensiones y posiciones relativas, para evitar cambios de funcionamiento no deseados (Rodríguez, 2011).
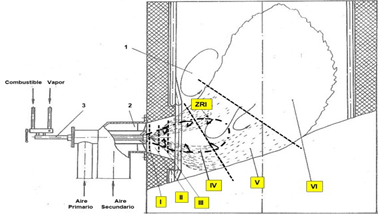
Fuente: Adamov 1989.
Fig. 1 - Esquema principal de organización del proceso de combustión dentro del horno.1 - Horno; 2 - quemador; 3 - caña de combustible; I - zona de turbulencia y suministro de aire; II- zona de distribución de gotas de combustible, calentamiento y evaporación parcial; III - zona de evaporación y combustión cinética; IV - zona de evaporación y comienzo de la combustión difusiva; V - combustión difusiva; VI - zona de post combustión (productos de la combustión).
Existen cuatro elementos básicos para lograr que una combustión sea eficiente, con bajo exceso de aire: Adamov (1989).
El diseño adecuado del quemador, que establezca la mayor compatibilidad entre la aerodinámica y la distribución de combustible en la sección de la llama.
Lograr el rango de regulabilidad requerido por la caldera, con buena estabilidad.
Asegurar gotas de combustible bien pequeñas en todo el rango de regulación.
Lograr que los elementos internos de los quemadores estén totalmente concéntricos, y sus distancias axiales relativas, estén bien reguladas (posición del atomizador de combustible, con respecto al difusor y la garganta refractaria); en el caso de hornos de quema tangencial, que los ángulos de inclinación de los quemadores, se correspondan con el proyecto original.
Los tres primeros son responsabilidad del suministrador de la caldera o en caso de que exista una actualización con cambio de quemadores, de la compañía que asuma el proyecto y el diagnóstico de los resultados esperados.
El cuarto elemento está en función de las intervenciones de mantenimiento y de la calidad con que se realicen las mismas.
La tecnología de mantenimiento desarrollada por los autores, corrige los errores en el centrado de los elementos internos de los quemadores y sus gargantas refractarias. La nueva tecnología permite ajustar la concentricidad de todos los elementos que conforman el quemador, incluyendo la garganta refractaria, y en adición mide la circularidad de todos los elementos cilíndricos y cónicos, para lo cual se han establecido límites permisibles en cada caso. Para garantizar la concentricidad de las gargantas refractarias con respecto al eje de la llama, su fundición se realiza con un molde metálico desarmable, que se monta sobre una barra que prolonga el eje del portacañas al interior del horno; en casos especiales donde el refractario es una pared delgada que cubre el cono conformado por los tubos de la caldera, de igual forma sobre la barra se instala un raspador rotatorio con movimiento alternativo, que permite con precisión la fundición del cono refractario. La tecnología puede ser utilizada para el mantenimiento sistemático de restitución de los parámetros de eficiencia de los quemadores existentes o en el montaje de nuevas instalaciones de quemadores.
Al terminar los trabajos de fundición de las gargantas refractarias, es necesario realizar el ajuste fino referido a las posiciones relativas del atomizador con el difusor Figura 2 (dimensión A), y del difusor con la garganta refractaria Figura 2 (dimensión B). Esto es necesario en cada mantenimiento para evitar errores en la posición de salida del aerosol y garantizar la ubicación correcta del esquema aerodinámico (ZRI), con respecto a las corrientes específicas de distribución del combustible atomizado (), en la sección de la llama. Es importante que el aire y el combustible se encuentren de forma proporcional y estequiométrica en el punto de diseño, para lograr la eficiencia del proceso de combustión con mínimo ¨exceso de aire¨. Uno de estos elementos fuera de lugar, crea considerables dificultades en el mezclado, lo que genera inquemados, hollines, alargamientos en la llama, deposiciones de escoria en el refractario y sobre los atomizadores. Cuando esto sucede, la solución disponible por el operador, es el incremento del coeficiente de exceso de aire, para mejorar la intensidad en el mezclado y el agotamiento del carbono.
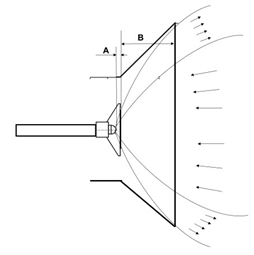
Fuente: elaboración propia.
Fig. 2 - Posición relativa del atomizador con respecto a la garganta refractaria y al difusor.
Cañas de combustible, atomizadores y el proceso de atomización.
Las cañas de combustible, deben ser sometidas a prueba hidráulica al menos una vez por año, para evitar pases interiores entre el combustible y el vapor de atomización; así como semanalmente es necesario controlar el flujo de combustible y el tamaño de las gotas que salen de los atomizadores, como parámetros principales, que definen el límite de retiro o momento de sustitución de estos importantes elementos. La presencia de gotas grandes, provoca combustión tardía, genera inquemados y residuos carbonosos que pueden actuar como base de adhesión de residuos salinos. Por otra parte, un atomizador con exceso de flujo, crea desbalances de combustible entre quemadores. Otro elemento de vital importancia es el acabado de la superficie interior de los agujeros de los atomizadores, que no siempre satisface los requerimientos técnicos establecidos por las normas; cuando esto sucede los atomizadores deben ser retirados.
La eliminación periódica del agua que acompaña al combustible, es un requerimiento imprescindible para minimizar la formación de sulfatos y vanadatos sódicos durante la combustión.
El vapor que se utiliza para la atomización del combustible debe cumplir los siguientes requisitos:
No es admisible la presencia de agua en el vapor de atomización, por lo que se requiere de un sobrecalentamiento de 5 °C a 11 °C.
La temperatura del vapor de atomización no debe superar 260 °C, para evitar depósitos de carbón residual por craqueo, que tupe los atomizadores.
Para garantizar vapor seco en el atomizador, es fundamental el aislamiento térmico de las tuberías y disponer de un adecuado trampeo del condensado.
El otro aspecto que no puede perderse de vista durante el proceso de preparación del combustible que va a ser quemado, es el control riguroso de la temperatura de calentamiento para lograr la viscosidad adecuada, lo cual debe ir acompañado de un cuidadoso filtrado para evitar que partículas sólidas pasen al interior de los atomizadores.
Exceso de aire
Lograr que la caldera trabaje con bajo ¨exceso de aire¨, es fundamental para elevar la eficiencia y reducir el ensuciamiento y la corrosión a partir del uso de aditivos químicos. Las calderas multi-quemadores de las centrales termoeléctricas, requieren de un control preciso de la cantidad de aire que llega a cada quemador. No deben existir diferencias en cuanto al flujo de aire entre un quemador y otro, sin embargo, en la práctica esto no sucede así, ya que depende de la caída de presión que tiene lugar en cada uno de los conductos que entregan el flujo de aire a cada quemador. Por eso es importante la medición individual y la regulación automática del flujo de aire por quemador, lo que evita los dañinos desbalances de aire dentro del horno. El desbalance de aire conduce a que, algunos quemadores trabajen con altos coeficientes de exceso de aire (lo cual minimiza el efecto de los aditivos químicos), mientras que otros lo hagan con defectos de aire (). El defecto de aire, da lugar a llamas reductoras (combustión subestequiométrica) lo que incrementa la razón de corrosión de las pantallas de agua de las zonas afectadas. Cuando se queman combustibles con alto azufre y no hay presencia de oxígeno libre, puede ocurrir la corrosión por sulfuro. La formación de
(ácido sulfhídrico) durante la combustión y la presencia de azufre atómico (S), interactuando con las superficies metálicas de calentamiento de los tubos, forma
(sulfuro de hierro) y
(sulfuro de hierro II) (Носков & Пай, 2016). Además, las llamas reductoras incrementan el contenido de inquemados, la formación de hollines, escoria, y compuestos carbonosos. Un horno con desbalance de aire, no logra el control del ensuciamiento y la corrosión, a pesar de que se le suministren buenos aditivos químicos.
Como se muestra en el diagrama de la Figura 3, el uso más eficiente y rentable del combustible ocurre, cuando la concentración de alcanza su valor máximo en los gases de escape. Teóricamente, eso solamente sucede cuando en el aire existe el
suficiente para reaccionar con todo el carbono del combustible (
). Sin embargo, en el diagrama se puede observar que, para valores de
, hay presencia de monóxido de carbono
, lo que indica la existencia de un proceso de combustión incompleta. Esto se debe a que, en la práctica, siempre existen deficiencias propias del proceso de mezclado, relacionadas con la aerodinámica y la atomización del combustible. Por eso, para lograr la combustión completa, es necesario disponer de un volumen de aire en exceso. El exceso de aire, depende del tipo de combustible y del diseño del quemador. El monóxido de carbono (CO), es un sensible indicador de combustión incompleta, su concentración debe ser de 0 ppm a 400 ppm por volumen. El ajuste del exceso de aire en los quemadores debe ser tal, que garantice la concentración de CO mínima en los gases de salida.
Altos valores de exceso de aire, incrementa las pérdidas en los gases de salida, por lo que el coeficiente de exceso de aire para mantener la combustión en el rango de operación óptima, debe ser lo más pequeño posible. Para condiciones reales de plena carga, cuando
, están presentes las perdidas térmicas por incombustión química (
), que como se explicó anteriormente, se debe a las imperfecciones del proceso de mezclado. Al valor de
donde
, se le denomina coeficiente de exceso de aire crítico (
). Al valor de donde la sumatoria de todas las perdidas térmicas de la caldera (
) se hace mínimo, se conoce como coeficiente de exceso de aire óptimo
. Como el coeficiente de exceso de aire del horno
, la pérdida
, no es significativa. Entonces el cálculo de la sumatoria de las perdidas térmicas, se realiza por:
, donde
- pérdida de calor en los gases de salida, y
- pérdida de calor por enfriamiento externo de la caldera. Para cargas inferiores a la nominal, disminuye la energía del mezclado, baja la temperatura y se incrementan las perdidas térmicas, sin embargo, el exceso de aire en el horno tiende a mantenerse en el rango de los límites normados hasta 75 % de la carga nominal. Para cargas inferiores a 75 %, el exceso de aire en el horno tiende a incrementarse a medida que disminuye la carga (Bhatia 2022; Reznikov & Lipov, 1987). Por otra parte, las infiltraciones de aire frieron, en las superficies de intercambio (en las calderas de tiro balanceado), se incrementan siempre para cargas inferiores a la nominal.
Recirculación de gases
Efectos vinculados con la recirculación de gases por la parte inferior del horno, o a través de los quemadores: Reznikov & Lipov (1987).
Se modifica la distribución de temperatura de los gases dentro del horno, y disminuye la absorción de calor en las pantallas de tubos (tiene lugar una reducción de temperatura del metal de los tubos).
Se reduce la temperatura en la zona de reacción y por consiguiente disminuye la formación de
térmico y de oxígeno atómico por disociación, que como se explicó anteriormente este último interviene en la primera conversión de
; además una disminución de la temperatura contribuye a reducir la formación de pentóxido de vanadio.
Se incrementa la temperatura de los gases a la salida del horno y la absorción de calor en la zona de convección, lo que facilita el control de la temperatura del vapor vivo y recalentado.
Se incrementa el tiempo de permanencia de los gases dentro del horno (ver Fig. 4), lo cual es favorable para el agotamiento del carbono de un combustible pesado con alto contenido de asfaltenos, como el crudo mejorado.
Tensión térmica volumétrica, tiempo de permanencia de los gases dentro del horno y el tiempo requerido para la combustión.
La potencia térmica
es la característica fundamental de un horno y se puede obtener por la fórmula 1. La potencia térmica, consiste en la cantidad de calor que se desprende en la cámara del horno durante la combustión de
de combustible, con un poder calorífico determinado
.
(1)
Al relacionar el calor que se desprende en la zona de combustión (potencia térmica), con la sección del horno , se obtiene una importante característica de cálculo, conocida como tensión térmica de la sección de la cámara del horno
. Los valores máximos permisibles de
, están normados y dependen del combustible y de la organización del proceso de combustión dentro del horno. El valor de
, determina la velocidad de los gases en la sección del horno y a su vez el nivel de temperatura de estos cerca de las pantallas de tubos, lo que está directamente relacionado con el ensuciamiento y las incrustaciones. El otro elemento importante en el diseño y rediseño de los hornos, sobre todo cuando van a ser sometidos a un cambio de combustible (fuel switching), es la tensión térmica volumétrica
(formula 2), que no es más que la energía liberada en el volumen del horno
.
(2)
Los valores de , también están normados y determinan la tensión térmica sobre las pantallas de tubos y el tiempo de permanencia promedio de los gases dentro de la cámara del horno. El tiempo de permanencia del volumen de los gases dentro del horno
, tiene que ser mayor o igual al tiempo necesario para que las gotas de mayor tamaño puedan quemarse completamente
. La condición
, se corresponde con el valor máximo permisible de
que puede tener el horno. El valor de
puede ser obtenido por la fórmula 3.
(3)
En la Figura 4, se presenta el tiempo de permanencia de los gases dentro de un horno , en función de la tensión térmica volumétrica
para diferentes temperaturas de los gases. Como se puede observar
, se incrementa con la disminución de la tensión térmica volumétrica, para cualquier temperatura en los gases. Por otra parte, una disminución de la temperatura de los gases dentro del horno, para cualquier valor de
, incrementa el tiempo de permanencia de estos en el interior del horno.
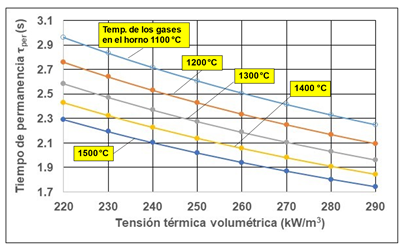
Fuente: Elaboración propia.
Fig. 4 - Comportamiento del tiempo de permanencia de los gases dentro del horno , en función de la tensión térmica volumétrica
, para diferentes temperaturas de los gases dentro de la cámara de un horno con tiro balanceado y
El tiempo requerido para la combustión , de diferentes diámetros de gotas de un mazut con bajo contenido de asfaltenos, en función de la temperatura de los gases en la zona de reacción se presenta en la Figura 5.
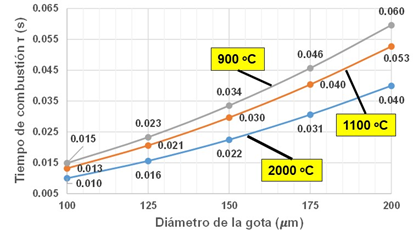
Fuente: elaboración propia.
Fig. 5 - Comportamiento del tiempo requerido para la combustión de diferentes diámetros de gota, de un mazut para diferentes temperaturas de los gases en la zona de la reacción.
Como se puede observar, el incremento del diámetro de la gota, para la misma temperatura en la zona de la reacción, es directamente proporcional al incremento del tiempo requerido para la combustión . Así como, la disminución de la temperatura de los gases en la zona de la reacción, para el mismo diámetro de gota, incrementa el tiempo de combustión, y este incremento se hace mayor para las gotas de mayor tamaño.
De las Figura 4 y 5, se puede arribar a las siguientes consideraciones:
El incremento del tiempo de permanencia
de los gases dentro del horno, debido a la disminución de la temperatura de los mismos, contribuye al agotamiento del carbono y a la eficiencia del proceso de combustión, de ahí la importancia que tiene la recirculación de gases, sobre todo para la combustión de hidrocarburos con alto contenido de asfaltenos (ver figura 6).
La disminución del diámetro de la gota, incrementa la eficiencia del proceso de combustión, ya que disminuye el tiempo requerido para la reacción
. Mantener gotas pequeñas en el aerosol es importante, incluso en condiciones desfavorables de significativa disminución de temperatura de la zona de reacción; como se puede observar en la Fig. 5, el incremento de
de una gota de 200
, para una disminución de temperatura en la zona de reacción de 2000 °C a 900 °C, es de 0,02 s, mientras que, el incremento del
de una gota de 100
con igual disminución de la temperatura en la zona de reacción, es de 0,005 s (4 veces menor).
El incremento de la temperatura de los gases en la zona de reacción, reduce el tiempo de combustión de cualquier diámetro de gota, a la vez que, provoca una disminución del tiempo de permanencia de los gases dentro del horno, que se hace mayor a medida que se incrementa la tensión térmica volumétrica
del horno. De ahí la importancia que tiene conocer el efecto de interacción de estos tres elementos (temperatura de los gases en la zona de reacción, diámetro de la gota y tensión térmica volumétrica), para lograr un funcionamiento adecuado de los sistemas de combustión. Por ejemplo, la norma rusa para el diseño de los hornos prismáticos establece valores de 210
a 290
, y la caldera rusa BKZ-340-140/29M de las unidades de 100 MW, fue diseñada con valores cercanos a 290
(horno con alta tensión térmica volumétrica), lo que representa una limitación importante en cuanto al
de los gases dentro del horno, para la quema de un combustible con alto contenido de asfaltenos (ver Figura 4).
Como se explica anteriormente, la presencia de asfaltenos en los combustibles, incrementa el tiempo requerido para la reacción de combustión . Según los resultados de las investigaciones realizadas por (Khateeb et al., 2018; Andreas, 2004).a partir de los análisis termogravimétricos (TGA - por sus siglas en inglés) a tres muestras de fuel oíl pesado HFO (Heavy Fuel Oil), con concentraciones de asfaltenos de 8 %, 16 % y 24 % en peso y utilizando la técnica de la combustión de la gota suspendida (con un diámetro entre 720
y 750
y una corriente de aire de 20 slpm a 950 K), se demuestra que:
El incremento del contenido de asfaltenos de 8 a 24 %, provoca un retardo en el inicio de la descomposición térmica de la masa de combustible, quedando al final del proceso un residuo de 2,4 %.
El proceso de combustión se divide en 7 etapas - 1 precalentamiento; - 2 inicio de la llama; - 3 evaporación interior; - 4 descomposición térmica; - 5 solidificación; - 6 pre-ignición del coque; - 7 combustión del coque, (ver Fig. 6).
El incremento del contenido de asfáltenos eleva el tiempo de duración de seis de las siete etapas. El tiempo de la etapa de evaporación interna por el contrario disminuye.
El incremento de la concentración de asfaltenos de 8 % a 24 % en peso, eleva el tiempo total de combustión
en 40 %, para el mismo tamaño de la gota. Así mismo el tiempo de retardo de la ignición crece 26 %.
En la Figura 6, se muestra una ventana ampliada de los resultados antes expuestos, como se puede observar el aumento en la concentración de asfaltenos no afecta el rango de temperatura donde se desarrolla cada etapa de combustión; solo modifica o cambia el inicio de encendido y quema de la gota.
Fuente: Khateeb et al. (2018).
Fig. 6 - Ventana ampliada del perfil de temperatura de gotas suspendidas para HFO8, HFO16 y HFO24, que muestra las etapas de combustión. El diámetro inicial de la gota es de 750 , la temperatura del flujo de aire es de 950 K, y la velocidad 8,2
.
La temperatura de ignición es casi la misma para las tres muestras, alrededor de 775 K, sin embargo, la ignición del HFO16 y del HFO24, tuvo lugar en momentos posteriores a la del HFO8, lo que significa que el incremento en la concentración de asfaltenos en el combustible, eleva la duración de la etapa de precalentamiento hasta la aparición de la llama.
Conclusiones
El uso de la tecnología para el ajuste centrado y alineamiento de los elementos internos y las gargantas refractarias, desarrollada por los autores, puede ser una contribución a la solución de una parte importante de los principales problemas que hoy presentan las instalaciones de quemadores en las centrales termoeléctricas. Es imprescindible el control automático riguroso y seguro del proceso de combustión, para lograr un nivel mínimo de oxígeno, con una distribución homogénea del calor dentro del horno, sin desbalance aire/combustible entre quemadores, como única vía para obtener el aprovechamiento adecuado de los aditivos químicos.
Por el papel tan importante que juegan los atomizadores en la eficiencia, la eficacia y la disponibilidad de la central termoeléctrica, hay que dedicar la mayor atención al control de la calidad de fabricación de estos elementos. Además, las facilidades existentes en las termoeléctricas, para el mantenimiento de las cañas de combustible y la evaluación isotérmica sistemática de los atomizadores, deben disponer de los recursos necesarios para certificar cada aerosol (flujo, presión, diámetro promedio de la gota, ángulo de apertura, calidad de la distribución de combustible etcétera) dentro del diapasón de presiones que cubre la reusabilidad de los quemadores.