INTRODUCCIÓN
El desgaste de los martillos desmenuzadores de los molinos de caña de los centrales azucareros afecta la eficiencia de separación de la médula del bagazo, aspecto de gran importancia para la industria del papel y otros productos derivados. Esto se debe a que disminuye drásticamente las propiedades y calidad de los productos, así como el aumento de los costos de producción, debido al consumo de compuestos químicos complementarios (Diez y col., 1988). De ello aquí se deduce la importancia que reviste el incremento de la resistencia al desgaste y por tanto de la vida útil de los martillos de los desmenuzadores de bagazo para disminuir los costos por mantenimiento, consumo de materias primas y pérdidas de la calidad de la producción.
En Cuba, para el recargue de los martillos se utiliza el electrodo revestido, AWS E FeCr-A1 recomendado por la literatura para este tipo de trabajo (Böhler Welding Group, 2018). No obstante, los resultados en cuanto a la resistencia al desgaste no son satisfactorios, teniendo en cuenta que los martillos sufren un desgaste acelerado durante la explotación de los molinos.
La realización de un proceso de recargue de forma continua en cada martillo como se realiza en Cuba para garantizar productividad, puede provocar un calentamiento excesivo de la aleación que conduce a un por ciento de dilución elevado y como consecuencia, a la formación de una microestructura en el depósito no adecuada para contrarrestar el desgaste de este tipo de pieza.
A partir de los diferentes factores que pueden conducir a la obtención de una dureza y microestructura no conveniente para contrarrestar el desgaste abrasivo, en el presente trabajo se realizaron depósitos con una y dos capas sobre placas de acero S275JR, utilizado en la fabricación de los martillos desmenuzadores. El procedimiento se llevó a cabo a temperatura ambiente y con un precalentamiento de 200oC, determinándose la dureza y microestructura en cada capa. Estos resultados constituyen premisas para establecer alternativas en el procedimiento de recargue con este electrodo y garantizar el incremento de la resistencia al desgaste de los martillos desmenuzadores.
El objetivo del trabajo es evaluar el efecto del precalentamiento sobre la dureza y microestructura de depósitos obtenidos con el electrodo AWS E FeCr-A1.
2. MATERIALES Y MÉTODOS
2.1. Realización de los depósitos, consumible y metal base utilizado
Para la obtención de los depósitos se utilizó un electrodo de recargue del tipo AWS EFeCr-A1, de diámetro 4 mm y 400 mm de longitud respectivamente, cuya composición del metal aportado se muestra en la Tabla 1.
Tabla 1 Composición química del depósito (% en peso) según el fabricante (Böhler Welding Group, 2018)
2,5 - 4,5 | 0,5 - 1,5 | 1,5 | 30 - 40 | 2 | Resto |
El material base empleado fue acero S275JR en forma de chapas con las siguientes dimensiones: 100 x 50 x15 mm. Para la realización de los depósitos, se utilizó corriente directa con polaridad normal (CD -) y una intensidad de corriente entre 150 - 160 A, manteniendo la velocidad de soldadura (Vs) en el rango de 4-5 m/h. Se realizaron depósitos con una y dos capas a temperatura ambiente, y con precalentamiento de 200° C. En la Tabla 2 se indica la identificación de cada uno de los depósitos estudiados y las condiciones en las que se obtuvieron. Con el objetivo de comparar resultados, en el estudio se ha incluido una muestra extraída de la superficie de recargue de un martillo rellenado en la producción.
2.2. Preparación de muestras para análisis metalográfico
Las probetas para el estudio metalográfico se obtuvieron mediante cortes transversales de los depósitos, utilizando una tronzadora y líquido refrigerante para evitar el sobrecalentamiento. Las muestras utilizadas para determinar la dureza y estudiar el tipo de microestructura fueron debidamente desbastadas y pulidas. El ataque fue realizado por inmersión con reactivo Murakami y observadas mediante metalografía óptica (MO) utilizando un microscopio binocular marca Novel. La dureza se determinó en el centro de los depósitos y en el borde superior, con el empleo de un durómetro marca Shimatsu y una carga de 500g.
RESULTADOS Y DISCUSIÓN
3.1. Análisis de la microestructura y la dureza en los depósitos sin precalentamiento
En la Figura 1 se presenta la microestructura obtenida en la aleación del recargue en el borde superior y en el centro, para el caso de las muestras obtenidas a temperatura ambiente.
De acuerdo a resultados obtenidos por Almeida, (2016), para los depósitos de recargue, cuya composición se corresponde con la del electrodo AWS EFeCr-A1, donde no hay dilución, se obtiene una microestructura que se ubica en la región hipereutéctica. Para estos depósitos de recargue, aunque la velocidad de enfriamiento es superior a las de equilibrio, se puede tomar como referencia y señalar que al enfriarse la aleación se forman carburos del tipo M7C3 durante la cristalización primaria a altas temperaturas.
Los depósitos realizados, al emplear electrodos de 4 mm de diámetro que exigen una intensidad de corriente en el orden de los 150 A, se obtuvo una dilución significativa. Este fenómeno tiene un efecto en la microestructura, al obtenerse una aleación en la capa de recargue con menor contenido de C y Cr a la que aporta el consumible. En este sentido, cuando se realiza el recargue en una sola pasada (Figura 1, M1) la aleación se ubica en la región hipoeutéctica, donde la austenita es el resultado de la cristalización primaria y por su cercanía a la transformación eutéctica y las condiciones de desequilibrio termodinámico es ésta la que predomina en la microestructura.
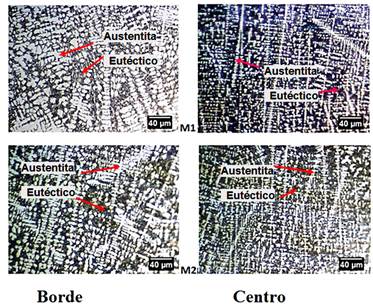
Figura 1 Microestructura obtenida en la capa de recargue sin precalentamiento, en el borde de la capa de recargue y en el centro M1- Una sola capa, M2- Dos capas
Como se observa en la Figura 1 (M1), la zona blanca es la predominante y se corresponde con la austenita, tanto para la zona del borde superior del depósito como para la zona central de la capa de recargue. La zona interdendrítica correspondiente a la red eutéctica en este caso, es la que influye en que el valor de la dureza sea de 659 HV para el borde superior de la capa de recargue, como se aprecia en la Tabla 3.
Tabla 3 Valores de dureza en la capa de recargue
|
|||
---|---|---|---|
M1 | 659 | 652 | |
M2 | 723 | 635 | |
M1C | 510 | 506 | |
M2C | 572 | 540 | |
MO | 525 | 515 |
En la microestructura obtenida en el depósito con dos capas (Figura 1, M2), la morfología es similar, con la diferencia de que aumenta el área de la zona eutéctica, debido a que es menor el efecto de la dilución y como consecuencia, los contenidos de C y Cr son superiores. Este aumento en el por ciento de C y Cr se corresponde con el incremento de la dureza, alcanzando en el borde superior un valor de 723 HV. Estos resultados son similares a los obtenidos por (Chotěborský et al., 2008) y (Liu et al., 2016), quienes concluyen que para las aleaciones de recargue, utilizando el sistema Fe-Cr-C, el por ciento de C es definitorio. Cuando el contenido de este elemento es relativamente bajo (aleación hipoeutectoide), la estructura primaria que solidifica en el depósito es la austenita, y la resistencia al desgaste abrasivo es baja.
3.2. Análisis de la microestructura y dureza en los depósitos obtenidos con precalentamiento
Al observar los resultados de la microestructura mostrados en la Figura 2 (M1C) se aprecia, que de forma general la morfología es similar a la obtenida en el depósito realizado sin precalentamiento; sin embargo, es significativa la cantidad de austenítica primaria, que se atribuye a una menor velocidad de enfriamiento.
En el depósito con una capa, tanto en el centro como en el borde superior, la austenita primaria de forma dendrítica ocupa mayoritariamente el área de la microestructura, lo que determina que la dureza sea de 506 HV en el centro y 510 HV en el borde superior, las mínimas observadas como se aprecia en la Tabla 3.
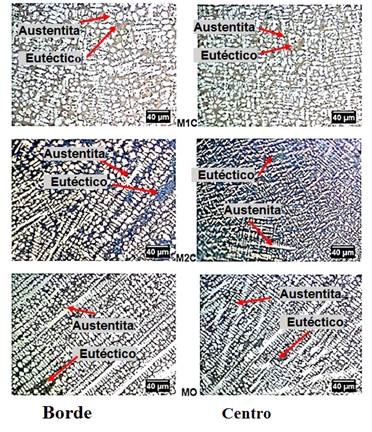
Figura 2 Microestructura obtenida en la capa de recargue con precalentamiento, de 200°C en el borde de la capa de recargue y en el centro M1C- Una pasada y precalentamiento, M2C- Dos pasadas y precalentamiento, MO- Martillo rellenado en los centrales
De forma similar, la aleación es del tipo hipoeutectoide, pero con un contenido de C y Cr mucho menor, debido a que el por ciento de dilución es mayor, resultado del precalentamiento empleado. En los depósitos realizados en condiciones de recargue similar, pero con dos pasadas (Figura 2, M2C), disminuye ligeramente la cantidad de austenita y como consecuencia aumenta el área que ocupa la zona eutéctica, incrementándose el valor de la dureza hasta los 572 HV, como se muestra en la Tabla 3 para el borde superior del depósito.
3.3. Análisis de la microestructura y dureza de recubrimientos de martillos rellenados en condiciones de producción
En la Figura 2 (MO), se puede observar la microestructura de la capa de recargue para una muestra extraída de un martillo rellenado en condiciones de producción. Es significativo que la fase predominante es la austenita, y la zona eutéctica ocupa un área mucho menor que la observada en la microestructura de las muestras de depósitos obtenidos en el presente trabajo. La dureza máxima que se alcanza en el depósito, en la zona cercana al borde superior, es de 525 HV, lo cual corrobora que la fase que prevalece es la austenita, cuya resistencia al desgaste abrasivo es baja según la literatura (Ortiz y col., 2019) y (Rodríguez y col., 2019). Esto confirma que durante el recargue de los martillos en los talleres del sector azucarero, al no emplearse una secuencia de deposición adecuada, los martillos alcanzan una temperatura elevada. Estos valores de temperatura en la superficie de los martillos durante el proceso de recargue, hace que el coeficiente de dilución sea considerable y por tanto, en la capa de recargue se obtiene un menor por ciento de los elementos de aleación que aporta el electrodo AWS EFeCr-A1. Lo anteriormente explicado ratifica que el deterioro prematuro de los martillos desmenuzadores de los molinos de los centrales azucareros, es consecuencia de la no aplicación de un procedimiento apropiado de recargue utilizando el electrodo AWS EFeCr-A1.
CONCLUSIONES
La dureza obtenida en los depósitos de recargue donde se realizaron dos capas fue superior, tanto en el centro de la capa de recargue como en el borde superior, lo que indica que en la medida que se reduce el efecto de la dilución con el metal base, es posible garantizar una aleación más competente ante el desgaste abrasivo.
El empleo de precalentamiento hace descender la dureza de los depósitos, ya que disminuye la velocidad de enfriamiento y en consecuencia favorece los procesos difusivos que estabilizan la austenita. Por ello, el procedimiento a emplear en el recargue de los martillos desfibradores no debe considerar la aplicación de precalentamiento.
El procedimiento empleado para el recargue de los martillos desmenuzadores de los molinos en las condiciones de producción de los centrales azucareros, utilizando el electrodo AWS EFeCr-A1, no garantiza que en la microestructura del depósito, el área que ocupa la zona eutéctica de elevada dureza sea la adecuada.