INTRODUCCIÓN
La disminución de combustibles fósiles ha obligado a todos los países a insertarse en la búsqueda de nuevas fuentes de energía para sustituir al petróleo. El etanol representa una fuente de energía renovable en el sector del transporte de varios países a nivel mundial, donde se ha empleado en mezclas de etanol-gasolina, como un sustituto de la gasolina convencional (Thammasittirong y col., 2017). El bagazo generado a partir de la caña de azúcar es uno de los principales residuos lignocelulósicos, según (Albernas-Carvajal y col., 2016), por cada tonelada de azúcar se obtiene de 0,27 a 0,3 toneladas de bagazo, que es principalmente utilizado en los generadores de vapor como combustible.
La composición del bagazo de caña de azúcar es de 50% de celulosa, 25% hemicelulosa, 20% de lignina y el 5% de otros componentes (Oliva y col., 2004). Regularmente, los polisacáridos de celulosa y hemicelulosa no son directamente accesibles debido a la fuerte protección de lignina, por lo que la aplicación de pretratamientos es necesaria para la degradación de estos compuestos a azúcares monosacáridos (glucosa, fructosa, xilosa) y posterior utilización como fuente fermentable.
Los pre-tratamientos pueden ser físicos, químicos o enzimáticos. En el caso de los físicos, principalmente, involucran la reducción de tamaño y la explosión con vapor. Por su parte, los químicos alteran la estructura de la biomasa con solventes que promueven la degradación de la celulosa, hemicelulosa y lignina. Mientras, los enzimáticos están asociados al empleo de determinadas enzimas para degradar la hemicelulosa y la lignina (Ferrer y col., 2002). Otros autores como (Albernas y col., 2017; Souza y col., 2018), también han analizado la combinación de métodos de pre-tratamientos para maximizar el rendimiento de etanol del bagazo de caña de azúcar.
En Ecuador, reportes del Centro de Investigación de la Caña de Azúcar del Ecuador-CINCAE mencionan que se cosechan anualmente de 81 000 ha de caña para la producción de azúcar y etanol, y 50 000 ha se destinan para producción de panela y alcohol artesanal (Carvajal-Padilla y col., 2021). En la provincia de Pastaza actualmente la caña de azúcar y sus derivados representan un rubro importante en la economía zonal, a través del cultivo, procesamiento, transportación y comercialización, según datos de la Asociación de Cañicultores de Pastaza - ASOCAP. Pero, la utilización del bagazo es limitada y es arrojado sobre el campo de siembra o callejones para su descomposición (Carvajal-Padilla y col., 2021).
El diseño exitoso y la evaluación de procesos son tareas difíciles que pueden ser facilitadas por el uso de herramientas avanzadas de diseño y simulación de procesos asistidos por computadora. El simulador comercial SuperPro Designer® versión 10.0, desarrollado por Intelligent, Inc (Intelligen Inc, 2013), es muy útil en el diseño y evaluación de procesos, pues define las características de procesamiento, los requisitos de energía, parámetros de los equipos para escenarios operativos específicos. Adicionalmente, realiza balances de materiales y energía, combina diferentes modelos de operaciones unitarias y analiza criterios económicos y ambientales de procesos integrados.
El objetivo del presente artículo es diseñar el proceso de obtención de etanol carburante mediante hidrólisis enzimática del bagazo de caña de azúcar. El diseño y la simulación de proceso se realizará en el simulador comercial SuperPro Designer.
MATERIALES Y MÉTODOS
2.1 Caracterización de la industria panelera en Pastaza
La provincia de Pastaza, ubicada en la Amazonía ecuatoriana, es la provincia más grande de Ecuador, por lo tanto es una de las principales productoras de caña de azúcar en país, cuenta con 4500 ha (Abril y col., 2013). Las unidades de producción de caña de Pastaza, agrupan de 1324 ha (29,4% del total de superficie cultivada). Se asume que el 30% es destinado para tallo fresco y el 70% utilizado para la elaboración de panela y aguardiente. Además, se estima que por cada tonelada de caña de azúcar se produce el 34% de bagazo y el 3,5% de cachaza.
2.2 Criterios metodológicos para el diseño y/o simulación del proceso
Los criterios considerados para el diseño de proceso fueron los procedimientos secuenciales propuestos por (Pérez y col., 2012), mientras para la simulación se consideraron los pasos definidos por (Julián-Ricardo y col., 2018). Se empleó el programa SuperPro Designer V.10.0 para el diseño y simulación del proceso. Se definió el modo de operación continuo (operación anual de 7 920 horas, 24 horas en 330 días). Se registraron convenientemente los componentes y mezclas a partir de la base de datos que presenta el software. Los compuestos que no se encontraba en la base de datos, fueron registrados e introducidas sus propiedades físicas, constantes, y las dependientes de la temperatura, al igual que en el estudio de (Julián-Ricardo y col., 2018).
2.3 Consideraciones para el diseño de procesos
Los costos asociados con el equipamiento, las materias primas y el precio de venta de los productos fueron consultados en los valores nacionales y partidas en el mercado internacional, así como en la base de datos interna del simulador. Los costos operacionales de los servicios auxiliares (agua de enfriamiento, electricidad o salario) se estiman de acuerdo con el mercado y los precios en Ecuador. El tiempo de vida del proyecto se considera de 10-20 años (Poveda-Ramos, 2003). Se considera una tasa de interés del 7 % para determinar el Valor Actual Neto (VAN) (Fajardo y col., 2019). Para conocer la cantidad de materia prima en el cual el VAN cambia de negativo a positivo, se tabuló y se calculó utilizando la macro Solver del programa Microsoft Excel. Se estableció un tiempo de 30 días al año para efectuar el mantenimiento de los equipos, accesorios y sistemas auxiliares de la planta.
RESULTADOS Y DISCUSIÓN
3.1 Producto demandado
El etanol constituye una fuente renovable de energía. Su mezcla con gasolina o petróleo proporciona un combustible de mejor calidad, principalmente porque es utilizado para oxigenar la gasolina. En Ecuador desde el 2010 como parte del programa piloto “Ecopaís” se ha comenzado a emplear hasta el 10% de bioetanol anhidro, en las gasolinas según (Decreto Ejecutivo 675, 2015). La demanda nacional de gasolina es de 14 943 000 barriles/año, lo que corresponde a 6 500 000 L /día. La demanda de etanol anhidro es de 650 000 L /día, por lo que no se puede cubrir la demanda de etanol, con la producción existente de caña, pues de cada hectárea de caña se puede obtener entre 5 000 y 6 000 L de etanol anhidro. La producción de etanol no supera la demanda, lo que requiere de su importación.
3.2 Selección de la tecnología y esquema tecnológico definido
La tecnología seleccionada para la obtención de etanol constó de varias operaciones tecnológicas: acondicionamiento del bagazo, pretratamiento ácido, básico, organosolvente, complementado con la adición de celulasas en una subetapa de hidrólisis enzimática. Luego, la fermentación, posteriormente el proceso de separación (destilación, rectificación) y finalmente, la deshidratación por separación cromatográfica.
El proceso inicia con el acondicionamiento del bagazo de caña (66,667% del bagazo consumido), se empleó el lavado, la reducción de tamaño, tamizado para la obtención de partículas homogéneas y el transporte del bagazo hacia el pretratamiento (Figura 1A). El 33,33% del bagazo consumido se destina a la producción de vapor y electricidad (Figura 1B). Este proceso consta de un horno y generador de vapor. El proceso de conversión de biomasa en etanol implica un pretratamiento para eliminar la lignina y los azúcares libres, seguido de la sacarificación enzimática y la fermentación (Shields y Boopathy, 2011).
En la (Figura 2A), se muestra el diagrama de flujo del pretratamiento del bagazo. Como se puede apreciar en la (Figura 2A), en el proceso de pretratamiento se aplica la hidrólisis ácida, básica y enzimática, y el posterior filtrado en cada una de las etapas. En este proceso la estructura de la fibra se rompe o se fracciona en sus componentes principales (celulosa, hemicelulosa y lignina) como plantea (Albernas y col., 2017). La hidrólisis ácida de la lignina produce furfural, mientras de la hidrólisis básica y enzimática de la celulosa y hemicelulosa se obtienen azúcares fermentables (glucosa, xilosa) como productos. El bagazo hidrolizado es llevado a la siguiente etapa.
La corriente del bagazo hidrolizado contiene azúcares fermentables (xilosa, glucosa) y agua. Como se muestra en la (Figura 2B), estos azúcares fermentables pasan a la etapa del mezclado, seguidamente se pasa a la etapa de pre-fermentación con adición de aire a través de un compresor, de este proceso se obtiene un sustrato idóneo para la fermentación total de los azúcares y un residual de CO2. Posteriormente, en la etapa de fermentación de los azúcares se realiza mediante cepas de levaduras u otros microorganismos que metabolizan la glucosa en etanol y CO2 (Ishola, 2014). De la etapa de almacenamiento se separa del mosto el alcohol etílico de los demás productos de la fermentación. A continuación, el producto obtenido en la fermentación entra en el intercambiador de calor, seguidamente es sometido al primer proceso de destilación del cual se obtienen residuos como las vinazas, de manera inmediata el producto del primer destilado entra a un proceso de rectificación que recircula al intercambiador de calor y finalmente pasa al enfriamiento y se obtiene alcohol (Figura 2B). Este etanol pasa a una etapa de deshidratación para obtener etanol con un grado de pureza de 99% por separación cromatográfica.
3.3 Estimación de la capacidad
El etanol tiene una elevada demanda, desde combustible para la mezcla o remplazo del petróleo y sus derivados (65% de la producción mundial), hasta un 35% en otras industrias. El rendimiento de etanol a partir del jugo de caña se reporta en 75 L/t de caña (Montoya y col., 2005). A partir de las hectáreas que pertenecen a las unidades de producción de caña de Pastaza que son destinadas a la producción de alcohol y panela, y estimando un rendimiento de 70,3 t/ha de producción de caña se obtuvo la cantidad de bagazo tentativo de producción diaria de 178 t/día.
3.4 Macrolocalización
Una correcta macrolocalización de la planta permite una disminución de los recursos de transporte de las materias primas. La disponibilidad del bagazo de caña de azúcar procede de las parroquias Tarqui, San José, Fátima y Puyo que representan la mayor producción de caña. En las parroquias de las Américas, Tarqui y Puyo se produce aguardiente y panela (GADPPz, 2012).
3.5 Balances de masa y energía
Los balances de masa y energía se realizaron por medio del programa computacional Superpro Designer. Se determinaron los indicadores medioambientales para 36, 54, 72, 90, 108, 126 y 144 t/día de bagazo a partir de las cantidades de los materiales a granel, las cantidades del consumo de facilidades auxiliares y los residuos generados del proceso, en relación a la cantidad de etanol producido. Este análisis mostró materiales a granel a exclusión del nitrógeno, oxígeno y vapor alcohol etílico (30% p/p) que presentan incrementos graduales con respecto al bagazo de la caña de azúcar. Estos componentes son usados principalmente en la etapa de hidrólisis, lavado, hidrolizado y fermentación por lo que es indispensable el acondicionamiento del sustrato ya fermentado. La producción de etanol se encontró entre 993 289 L /año, para la capacidad de 36 t de bagazo y 3 971 830 L /año, para 144 t de bagazo.
3.6 Disponibilidad y consumo de materia prima
La disponibilidad de bagazo de caña en la provincia de Pastaza es de 178 t/día de bagazo (Tenemaza, 2018). Se puede mencionar que existe la disponibilidad de la materia prima pues es mayor para cada una de las cantidades realizadas en la simulación. Existe un sobrante de 44 t/día, el cual puede ser utilizado en los generados de vapor de la planta.
3.7 Compatibilidad ambiental
Se identificó que los residuos generados durante la producción de bioetanol carburante. Según (Zúñiga y Gandini, 2013), plantea una solución para cada uno de los residuos del proceso de bioetanol carburante. Las cenizas de combustión pueden utilizarse como regeneradores de suelos ácidos en agricultura y silvicultura debido a que son completamente inocuas. El licor post-fermentativo generado puede emplearse en la recirculación de aguas utilizadas para refrigeración. Las vinazas generadas durante la obtención de bioetanol carburante pueden ser empleadas como uso potencial de fertilizante en irrigación de cultivos y tratamientos biotecnológicos, además, la aplicación de tratamientos biológicos, pueden reducir significativamente los valores de demanda química de oxígeno (DQO) y demanda bioquímica de oxígeno (DBO5).
En lo relativo a los límites máximos permisibles para descargas a cuerpos de agua, se consideraron los valores a cumplir de DBO5 100 mg/L, DQO 200 mg/L y los sólidos totales en 1600 mg/L, que rige el Acuerdo Ministerial 097-A (Ministerio del Ambiente de Ecuador, 2015). En el caso de las emisiones gaseosas, en dicha normativa no aparecen las emisiones para procesos de alcohol, pero se establecieron comparaciones con los límites máximos permisibles de concentraciones de emisión de contaminantes al aire para bagazo en equipos de combustión de instalaciones de elaboración de azúcar, donde el material particulado y las emisiones de NOx no deben exceder los 120 y 700 mg/Nm3, respectivamente (Vinos-Aldana, 1988). La Tabla 1, muestra las cantidades de residuos generadas por cada capacidad de bagazo simulada.
Tabla 1 Cantidad de residuales que se generan por capacidad de bagazo simulada
36 | 54 | 72 | 90 | 108 | 126 | 144 | |
---|---|---|---|---|---|---|---|
Residuos | |||||||
Cenizas, t | 145 | 217 | 290 | 362 | 434 | 507 | 580 |
Residuos líquidos, m3 | 114450,9 | 119047,39 | 123642,85 | 128238,33 | 141453,47 | 137430,27 | 150645,42 |
Vinazas, m3 | 3737,75 | 5606,71 | 7475,74 | 9344,83 | 11213,97 | 13833,20 | 14952,45 |
CO2, t | 19888021 | 29829876 | 37770306 | 49709328 | 59648101 | 69631225 | 79518529 |
3.8 Determinar la capacidad y costos de adquisición de los equipos
A partir de los resultados de los balances de masa y energía, se determinó la capacidad de los equipos y cantidad necesaria para el proceso tecnológico de etanol en función de la disponibilidad del bagazo. Los parámetros de diseño de los equipos se obtuvieron de las ecuaciones de diseño de cada una de las operaciones y procesos unitarios que intervienen en el proceso tecnológico de obtención de etanol (Figura 1 y 2).
En la (Figura 3A) se muestra el costo de adquisición de los equipos con respectos a las diferentes cantidades de materia prima de 36, 54, 72, 90, 108, 126 y 144 t/día de bagazo. Como se puede apreciar, se evidencia el aumento del costo en función de la cantidad de bagazo de caña a procesar, esto está asociado a que los costos de los equipos dependen directamente de los parámetros de diseño como caudales, temperaturas, presiones, potencias, entre otros que caracterizan a cada equipo y esto caracteriza la fiabilidad de los equipos.
3.9 Análisis económico de inversión y producción
El costo directo se estimó en función de los costos de adquisición del equipo, instalación, tubería de proceso, instrumentación, aislamiento eléctrico, edificios, mejora de patio e instalaciones auxiliares. Mientras, el costo indirecto total de la planta agrupó los reglones de ingeniería y construcción.
El costo de inversión se encuentra entre $ 8 136 000, para la capacidad de 36 t, hasta $11 294 000 para la capacidad de 144 t. Por su parte, el costo de operación anual fue analizado a partir de la capacidad de producción de la planta (Figura 3B). Se evidencia el incremento del costo anual en dependencia del aumento de la capacidad de bagazo. Como se menciona en el estudio de (Aburto y col., 2008) la inversión total necesaria para la planta de bioetanol está determinada por las operaciones de pretratamiento e hidrólisis enzimática (sacarificación). Esto conlleva que el volumen de los azúcares fermentables producidos en las operaciones mencionadas impacta de manera importante en el tamaño de los equipos subsecuentes y por los tanto en la inversión del capital. Los subproductos podrían recircularse a los mismos procesos o venderlos para generar beneficios económicos.
3.10 Factibilidad económica
El estudio de la factibilidad económica y la rentabilidad se determinó a través del valor del VAN. La (Figura 3C) muestra los valores del VAN para las diferentes cantidades de bagazo simuladas. Al analizar la (Figura 3C), se puede apreciar que las capacidades de la tecnología 36 t y 54 t de bagazo de caña reportan VAN negativo, por lo que estas cantidades no son procesos rentables (García y col., 2019; Pérez y col., 2012). Por lo tanto, se realizó nuevamente la estimación de nuevas cantidades de bagazo y se simularon 72 t, 90 t, 108 t, 126 t y 144 t de bagazo de caña y una tasa interna de retorno (TIR) se encontró entre de 9,14% para 72 t hasta 31,33% en 144 t de bagazo.
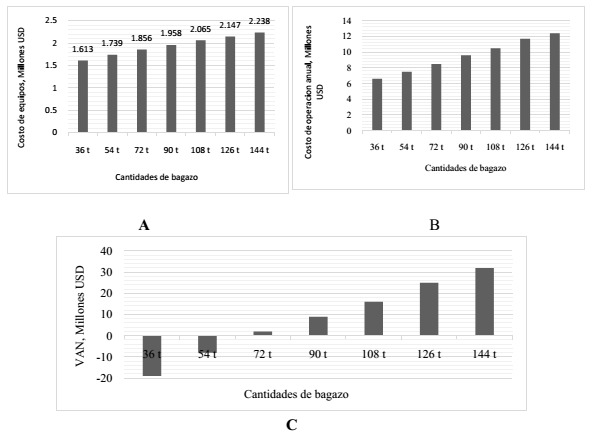
Figura 3 Costos totales de adquisición de equipos (A), costo de inversión en función de las cantidades de bagazo simuladas (B) y análisis de VAN a las diferentes cantidades de bagazo simuladas (C)
Las cantidades alternativas de consumo de bagazo rentables de acuerdo con los indicadores dinámicos económicos es de 7,02 años para 72 t hasta 2.38 años en 144 t de bagazo. Estos valores permiten identificar si la inversión es recuperable en el menor tiempo posible.
3.11 Análisis de nuevas capacidades
A partir del análisis de las diferentes capacidades de la planta y según el análisis técnico económico y medioambiental, se determinó que la capacidad con mayores réditos económicos es de 144 t de bagazo (Figura 3C), que presenta un mayor VAN ($32 333 000) y TIR (31,3%) y el tiempo de retribución es el menor (2,38 años). Además, estos criterios se analizaron en las etapas de macrolocalización y la disponibilidad de los equipos. Adicionalmente, se puede producir etanol carburante a partir del etanol etílico o aguardiente producido en las 23 destilerías de la provincia. Este producto presenta 60 oGL, el cual puede ser incorporado en la etapa de rectificación y deshidratación hasta alcanzar el contenido de alcohol requerido para el etanol combustible.
CONCLUSIONES
Las cantidades de materias primas que se encuentran entre 64 t hasta 144 t presentan los mayores índices de rentabilidad, es decir se puede seleccionar entre el rango de indicadores económicos rentables según la inversión. La inversión mínima para iniciar la planta de obtención de bioetanol carburante es de $ 8 136 000 y la inversión máxima es de $11 294 000 según los mayores índices de rentabilidad. Las cantidades inferiores a 54 t presentan indicadores económicos negativos.