Introducción
El proceso de galvanización en caliente consiste en la inmersión de hilos de acero o hierro en un baño de cinc fundido, con el propósito de cubrirlos con una capa protectora resistente a la corrosión. Esta barrera impide que la humedad, los cloruros y sulfuros ataquen el acero. Las etapas fundamentales son: recocido de los rollos de alambre en el horno de recocido, donde se eliminan las grasas adheridas y disminuyen las resistencias mecánicas; enfriamiento de los hilos; decapado en ácido, para eliminar los óxidos superficiales; lavado con agua, para separar los residuos de ácido y sales por arrastre; precalentamiento; galvanización; enfriamiento de la capa de recubrimiento y ovillado.
Este trabajo centra su atención en la cuba de galvanización. Las variables fundamentales son: velocidad de calentamiento, temperatura en las esquinas y centro de la cuba, tiempo de inmersión, velocidad de entrada y salida, y composición del material ferroso.1,2,3,4
La operación a bajas temperaturas (T<445 ºC) ocasiona menor fluidez del baño, menor escurrimiento y piezas más rugosas; pero si las temperaturas son muy altas (T>460 ºC), provocan menor vida útil de la cuba por desgaste, mayor formación de dross, ceniza y de un recubrimiento áspero. El tiempo de inmersión determina el espesor de la capa; la velocidad de inmersión debe ser lo más rápida posible sin que se ocasionen salpicaduras para lograr el espesor más uniforme; la velocidad de salida está relacionada con el consumo de cinc, y debe ser lenta para evitar la producción de gotas y grumos de recubrimientos.
Se denomina dross a los cristales de Fe - Zn insolubles, de apariencia arenosa, que se depositan en el fondo de la cuba con un 3% o más de hierro, las cenizas se producen por formación de óxido de cinc. Para disminuir estos efectos, se debe mantener una temperatura uniforme, evitar olas y agitación en el baño.
Un incremento de la temperatura del baño de 450ºC a 480ºC, afecta la morfología de las capas galvanizadas, las cuales adquieren apariencia de grietas en la estructura de las capas. Por otra parte, una cantidad inapropiada de silicio, fósforo, aluminio y azufre en el acero tiene un efecto adverso en el espesor y la composición de la capa, afectando las propiedades mecánicas del acero galvanizado.3,5,6,7,8,9
El baño de cinc fundido está compuesto por: cinc (98,9%), plomo (1%), hierro (0,03%), aluminio (0,002%), cadmio (0,02%), trazas de otros metales como Sn y Cu, los cuales favorecen el proceso.3,4
A partir de simulaciones numéricas, se ha analizado el efecto de los parámetros físicos, químicos y cinéticos del proceso, sobre la reducción del consumo de cinc, de energía y en la obtención de un producto con el mínimo de defectos en la superficie. Se ha realizado la modelación de la temperatura, la composición de los componentes en el baño de cinc, la velocidad de formación y ubicación del dross, utilizado las ecuaciones diferenciales parciales de Navier-Stokes, de continuidad para fluido no isotérmico, de transferencia de masa y calor, utilizando el método de volumen finito, el cual discretiza dichas ecuaciones por integración sobre un volumen de control. En pruebas industriales con monitoreo continuo, se han validado las simulaciones confirmando su importancia para el análisis de este complejo proceso.10,11,12,13
El propósito de este trabajo consistió en modelar el perfil de temperatura durante el calentamiento de una cuba de galvanización en régimen no estacionario utilizando el método de los nodos, para la posterior automatización del proceso.
Materiales y métodos
Materiales
La cuba de galvanización que se considera como modelo para determinar el perfil de temperatura, es un tanque de base rectangular de acero, espesor de 50mm, con las dimensiones 7100 x 1600 x 1350 mm (largo x ancho x profundidad), aislada térmicamente por un muro de ladrillos refractarios. En dicho muro se encuentran instaladas las resistencias eléctricas en forma de cintas, cuya potencia eléctrica máxima de operación es de 290 kW, y sin hacer contacto directo con la cuba, transfieren el calor por conducción térmica para fundir el cinc y el plomo que se encuentra en su interior.
La cuba tiene tres elementos termosensibles para medir y controlar la temperatura, dos colocados en el espacio existente entre las resistencias eléctricas y las paredes laterales de la cuba y otro en el interior del baño de cinc fundido.
Métodos
El calentamiento de la cuba se realiza por medio de las resistencias eléctricas, fijas a una pared de refractarios (Tp1). El calor se transfiere por radiación y convección libre a la pared exterior de la cuba (Tp2, L1: 230mm, zona a-b); por conducción térmica a través de la pared interior (Tp3, L2: 280mm, zona b-c); y también por conducción térmica a través del baño por todo el perímetro (L3, zona c-L). Las temperaturas (Tp4) y (Tp5) se refieren al interior de la cuba, (figura 1 a).
La temperatura inicial de la cuba es de 25ºC a 30ºC. Después de cargada con las pastillas de cinc, se conecta el sistema eléctrico que da energía a las resistencias. En las zonas de calentamiento está concebido incrementar la temperatura en tres etapas:
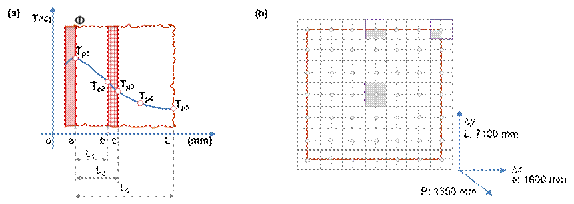
Fig. 1 Representación de la cuba de galvanización (a) Diagrama del perfil de calentamiento (b) Rejillas y nodos de la cuba
Etapa 1. Incrementar la temperatura a razón de 10(C/h desde 25ºC hasta 120(C y esperar 48h. Cuando no se ha realizado trabajo de mantenimiento en la pared de refractarios, el valor de 120(C no se toma en cuenta y se continúa calentando a razón de 10(C/h hasta 300(C, a esta temperatura se deben esperar 96h para igualar las tensiones internas que se producen entre las paredes de la cuba.
Etapa 2. Incrementar la temperatura a una velocidad de calentamiento de 20(C/h desde 300( hasta 420(C y esperar 48h a esta temperatura.
Etapa 3. Incrementar la temperatura desde 420( hasta 660ºC como máximo, a una velocidad de calentamiento de 20(C/h siempre y cuando la temperatura del cinc no alcance los 460ºC. En este caso, queda lista la cuba para la operación.
Se deben considerar los requisitos siguientes:
La temperatura en todas las paredes de la cuba debe ser aproximadamente igual.
La temperatura en las zonas de calentamiento ubicadas en el exterior de las paredes de la cuba no puede sobrepasar los 660ºC.
El gradiente de temperatura permisible entre las zonas de calentamiento exteriores de la cuba y el baño de cinc es de 200ºC como máximo.
Se utilizó el método de los nodos, el cual consiste en representar la cuba en rejillas, identificar los nodos característicos y plantear las ecuaciones según el mecanismo de transferencia de calor considerado, (figura 1 b).
Las propiedades físicas de los materiales (cinc y aire), en cuanto a la densidad (p, kg/m3), calor específico (Cp, J/kgºC) y conductividad térmica (k, W/mºC) se obtuvieron de la literatura 14,15 y con el software de estadística Statgraphics Plus 5.1 se ajustaron funciones polinomiales.
Expresiones matemáticas del perfil de temperatura
Se consideró Δx=Δy=0,178m, se despreció la transferencia de calor por conducción a través de la pared de la cuba de galvanizado (Δx=Δy >>> δ) y se plantearon los nodos: (a) esquinas exteriores, (b) laterales exteriores y (c) interior de la cuba, (Figura 2).
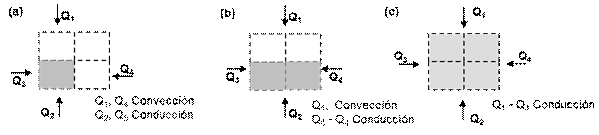
Fig. 2 Representación de los nodos: (a) esquinas exteriores, (b) laterales exteriores, (c) interiores de la cuba
El balance de calor no estacionario se representa por la ecuación (1):
donde
Q es flujo de calor (W);
Δx y Δy, variación de longitud en la dirección x, y respectivamente (m); P, profundidad de la cuba (m); p, densidad del material (kg/m3); Cp, calor específico (J/kg∙ºC); T, temperatura (ºC); Δt, intervalo de tiempo (s); ΔT, gradiente de temperatura (ºC).
El balance de calor se desarrolló para cada nodo, donde la flecha indica la dirección del flujo de calor que entra al nodo (x; y) desde el nodo opuesto; h, el coeficiente de transferencia de calor por radiación y convección libre (W/m2∙ºC); k, la conductividad térmica del cinc (W/m∙K).
Nodo: esquinas exteriores de la cuba, (figura 2 a), ecuaciones (2), (3).
Nodo: laterales exteriores de la cuba, (figura 2 b), ecuaciones (4), (5).
Nodo: interiores de la cuba, (figura 2 c), ecs. (6), (7), (8).
Tomando Δx igual a Δy, (8) se transforma en la ec. (9).
El coeficiente de transferencia de calor por convección libre, se calculó a partir del número de Nusselt (Nu), la conductividad térmica del aire (λ, W/mºC) y la longitud característica (L) para una superficie vertical, la altura, ec. (10).
El Nusselt se calculó en función de los números de Rayleigh (Ra), Prandtl (Pr) y Grashof (Gr), ecs. (11), (12), (13), (14), (15).
Donde la densidad del aire a la temperatura del gas es p (kg/m3); la viscosidad del aire a la temperatura de la pared, μ (Pa.s); la constante de aceleración de la gravedad, g (9,8 m/s2); el calor específico, Cp (J/kgºC) y el coeficiente de dilatación térmica (ΔT.
Por otro lado, el coeficiente de transferencia de calor por radiación, se determinó por las ecs. (16), (17).
En este caso el grado reducido de radiación integral es Epsilon-εr, para la pared de ladrillo refractario se asumió 0,9 y para el acero, 0,80; la constante de Stefan-Boltzmann, σ, igual a 5,67˖10-8 W/m2K4 y las temperaturas absolutas (K) reflejadas en la figura 1 a.
El algoritmo se desarrolló en una hoja de cálculo en Excel, se programaron macros para calcular la temperatura en las resistencias eléctricas (Tp1), los coeficientes de transferencia de calor y obtener los datos para la representación gráfica del perfil de temperatura.
Resultados y discusión
Se calculó el perfil de calentamiento de la cuba de galvanizado, considerando Δx=Δy=0,178m y Δt=0,011h. De acuerdo a las ecuaciones obtenidas por el método de los nodos y los modelos para la estimación de los coeficientes de transferencia de calor por convección y radiación, se obtuvieron los siguientes resultados expresados por etapas de calentamiento:
Etapa 1 de calentamiento
En la etapa 1, está concebido que la zona de calentamiento, a una temperatura inicial de 25ºC a 30ºC, incremente a razón de 10ºC/h hasta 120ºC o 300ºC, con un tiempo de espera de 48h o 96h respectivamente, y además cumpliendo con los requisitos de operación previamente expuestos.
Según las ecuaciones planteadas, a Tp1 120ºC y 9,5h de operación, en las esquinas y orillas interiores de la cuba (0≤x≤0,71; y=0,18), se alcanzó entre 36ºC y 40ºC (figura 3 a), mientras que en el centro de la cuba (0≤x≤0,71; y=3,5), donde las temperaturas son menos calientes, se obtuvo de 31ºC a 35ºC, (figura 3 b).
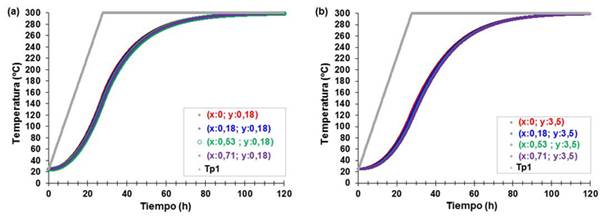
Fig. 3 Perfil de calentamiento de la cuba de galvanización, Etapa 1. Gráficos de dispersión: (a) esquina de la cuba, y=0,2; (b) centro de la cuba, y=3,5
Se simuló el calentamiento hasta Tp1 300ºC y a las 120h, se alcanzó en toda la pared y el interior de la cuba 299+/-0,11ºC, resultado que es coherente con el programa de calentamiento, donde a las 120h se espera una temperatura en el cinc de 300ºC.
Sin embargo, se debe considerar que de acuerdo al modelo obtenido, al cabo de las 112h, la temperatura en la pared fue de 299 +/-0,19ºC y en el interior de 299+/-0,17ºC, lo cual pudiera incidir en el ahorro de energía.
El calentamiento de la cuba, para el par (x; y) en función del tiempo, siguió una función polinomial de segundo orden hasta las 30h, con un coeficiente de determinación, R2, mayor que 99,93 %.
Etapa 2 de calentamiento
En la etapa 2, está concebido incrementar la temperatura a 20ºC/h, desde 300ºC hasta 420ºC (6h) y esperar a esta temperatura 48h.
Al aplicar el algoritmo de cálculo, en las esquinas y orillas interiores de la cuba (0≤x≤0,71; y=0,18), a las 48 horas de operación se alcanzó 418,5+/-0,1ºC (figura 4 a), mientras que en el centro (0≤x≤0,71; y=3,5), donde las temperaturas son inferiores, se obtuvo 417,4+/-0,19ºC, valores aproximados a la norma de operación, (figura 4 b).
Etapa 3 de calentamiento
Está determinado para la etapa 3, un incremento de la temperatura en la zona de calentamiento de 420ºC a 660ºC como máximo, a razón de 20ºC/h, siempre y cuando el cinc en el interior de la cuba no alcance los 460ºC.
El perfil de calentamiento simulado muestra que a las 5,3h de iniciada la etapa 3, a Tp1 igual a 526ºC y Tp2 de 471ºC, es posible alcanzar la temperatura máxima de 461ºC en las esquinas interiores de la cuba (x: 0,18; y: 0,18) y en los bordes interiores entre 454ºC y 461ºC; en cambio, se obtiene en el centro la temperatura mínima de 436ºC (x: 0,71; y: 3,5) poseyendo una diferencia con respecto a la temperatura en la resistencia (Tp1) y la pared (Tp2) de 90ºC y 34ºC, respectivamente, (figura 5 b, d).
Así mismo, a las 5,9h, a Tp1 igual a 538ºC y Tp2 de 480ºC, se obtiene en las esquinas las temperaturas superiores, entre 460ºC y 471ºC; en cambio, en el centro se obtuvieron las temperaturas inferiores, entre 440ºC y 460ºC.
Este resultado sugiere que el intervalo de 526≤Tp1≤538ºC es el más conveniente para finalizar la operación de calentamiento de la cuba.
En la figura 6 se muestra el perfil de temperatura Tp1 y Tp2, y el coeficiente de transferencia de calor (α). La mayor diferencia de temperatura entre la fuente externa de calor (Tp1) y la temperatura mínima en el interior de la cuba se obtuvo en el intervalo de tiempo 27,3≤Δt≤27,8h con 188,3≤ΔT≤190,6ºC.
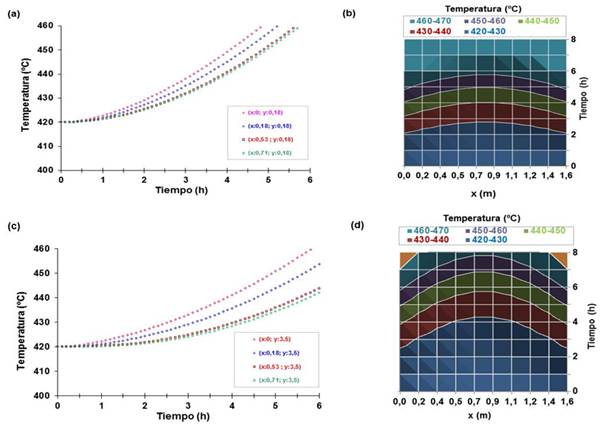
Fig. 5 Perfil de calentamiento de la cuba de galvanización, Etapa 3. Gráficos de dispersión: (a) esquina de la cuba, y=0,2; (c) centro de la cuba, y=3,5. Gráficos de contorno: (b), (d) esquina y centro de la cuba respectivamente
Conclusiones
Se modeló el perfil de calentamiento de una cuba de galvanización a régimen no estacionario utilizando el método de los nodos, considerando los mecanismos de transferencia de calor por radiación, convección libre y conducción, obteniendo una correspondencia satisfactoria entre el tiempo de operación establecido y el predicho por el modelo.
Se estimó que el intervalo de temperatura entre 526ºC a 538ºC en la fuente de calor es probablemente el más conveniente para finalizar la operación de calentamiento de la cuba; y el intervalo de tiempo de 27,3h a 27,8h, el crítico en cuanto a alta diferencia de temperatura entre la fuente de calor externa y el interior de la cuba.
Nomenclatura
Cp: Calor específico (J/kg˖K)
Fo: Número de Fourier Fo=k/(ρ˖cp)
h: Coeficiente de transferencia de calor (W/m2˖ºC)
k: Conductividad térmica (W/m˖ºC)
T: Temperatura (ºC)
x, y, z: Ejes referidos al ancho, lago y profundidad de la cuba, respectivamente
α: Coeficiente de transferencia de calor (W/m2ºC)
δ: Espesor de la cuba (m)
ΔX, ΔY: Variación de la longitud según eje (m)
ρ: Densidad (kg/m3).