Introducción
Una de las áreas donde ha tenido mayor impacto la biotecnología desde el punto de vista tecnológico, económico y social, es la producción de edulcorantes. En la actualidad existen diferentes tipos de edulcorantes; algunos de estos, como la sacarosa, se encuentran de forma natural en los alimentos. La sacarosa es el compuesto orgánico de mayor producción en forma pura.1 Es un disacárido compuesto de glucosa y fructosa que, mediante una reacción de hidrólisis se transforma en estos monosacáridos obteniéndose como producto el azúcar invertido.2 Dichos monosacáridos son más solubles, higroscópicos, presentan menor punto de congelación y una menor tendencia a cristalizar, lo cual justifica su uso preferencial en la industria alimentaria.3
Las principales fuentes de obtención de glucosa son a partir de almidón de maíz y de azúcar refino empleando los métodos de hidrólisis ácida, intercambio iónico e hidrólisis enzimática.4 En Cuba se lleva a cabo el proceso de inversión de la sacarosa con una tecnología que opera en régimen discontinuo. Normalmente se produce glucosa y jarabe rico en fructosa mediante hidrólisis ácida a partir del azúcar refino. Este método tiene como inconveniente el empleo de ácidos (como clorhídrico, fosfórico, cítrico) a elevada temperatura 85-90 °C, lo que puede originar productos coloreados con presencia de cenizas, bajo porcentaje de inversión, alto consumo de sacarosa, corrosión, presencia de residuos ácidos en el producto y subproductos no deseados.5
Actualmente existe una marcada tendencia a la simulación y optimización de procesos, para contribuir al análisis de alternativas para la disminución de los tiempos de operación y al incremento de los rendimientos. La simulación comprende la utilización de recursos computacionales para desarrollar modelos matemáticos con el fin de construir un modelo representativo de un proceso bajo estudio. Cada modelo de simulación se obtiene para predecir el comportamiento de una o varias operaciones unitarias. Estas herramientas pueden ser empleadas en todas las etapas del desarrollo de procesos, desde el diseño conceptual hasta la operación y posterior optimización de la planta.6 El simulador profesional SuperPro Designer facilita la modelación, diseño y optimización de procesos integrados en un amplio intervalo de industrias tales como farmacéuticas, biotecnológicas, agroquímicas, alimentarias, tratamiento de residuales y purificación de agua, entre otras. Se caracteriza fundamentalmente por contener herramientas para la estimación de balances de masa y costos en una planta dada operando tanto de forma continua como por lotes, así como también por contener herramientas de cálculo diseñadas específicamente para procesos que incluyen componentes biológicos.7
El central azucarero Argentina, ubicado en la provincia de Camagüey, está integrado por una refinería y una planta de glucosa y fructosa, resultado de una transferencia de tecnología desde Checoslovaquia. La planta de glucosa y fructosa cuenta con una tecnología simple, produciendo 250 toneladas al año de glucosa; de la sacarosa, al ser un disacárido compuesto por dos moléculas con igual fórmula química global (isómeros), al invertirse se obtienen cantidades equimolares de fructosa y glucosa. Por ello, si en la planta por cada 6 toneladas de azúcar refino se obtiene una tonelada de glucosa, el rendimiento de producción de glucosa es sólo de 33 % respecto a la glucosa que se podría obtener con la sacarosa alimentada.4,8
Algunos autores (4) evaluaron el proceso de obtención de glucosa con la tecnología existente en la planta Argentina empleando la simulación, quedando el modelo de simulación validado con errores inferiores al 5 %.9 Además, se propusieron dos alternativas de mejoras para incrementar el rendimiento de producción de glucosa, una sin inversión económica y otra con inversión, aumentando las producciones de glucosa a 1,5 t y 2,8 t por lote respectivamente con las modificaciones realizadas. Finalmente, a modo de recomendación se planteó realizar estudios para sustituir la etapa de inversión ácida en el proceso de obtención de glucosa a partir de azúcar refino por la de inversión enzimática.10
Por ello en este trabajo se simuló el proceso de inversión de la sacarosa por vía enzimática, continuando la separación de glucosa por dos métodos. En la primera alternativa se incluye una cristalización seguida de una centrifugación; en la segunda alternativa la separación se realiza en una columna cromatográfica. Ambas alternativas tienen como objetivo incrementar el rendimiento de glucosa en el proceso.
Materiales y métodos
Descripción de la tecnología de obtención de glucosa a partir de azúcar refino
Para obtener glucosa a partir del azúcar refino se empleó la tecnología propuesta en el Instituto Cubano de Investigaciones de los Derivados de la Caña de Azúcar (ICIDCA) la cual se fundamenta en realizar la inversión ácida de la sacarosa operando en régimen discontinuo.
En dos tanques cilíndricos enchaquetados verticales de 6 m3 de volumen con tapas semiesféricas se adicionan 6 000 kg de azúcar refino y 750 L de agua dura a 25 °C. Se emplean agitadores de hélice para obtener una disolución que debe tener 77-78 ºBrix y temperatura 85-90 ºC. Posteriormente ocurre el proceso de inversión en el mismo tanque disolutor. Para ello se adicionan 600 mL de ácido fosfórico al 85 % volumétrico por cada tonelada de azúcar refino disuelta; se mantiene la disolución en agitación durante cuatro horas, tiempo necesario para que ocurra la inversión.
La disolución de azúcar invertida pasa a una batería de siete cristalizadores de capacidad de 45 m3 de volumen. Los cristalizadores tienen enfriamiento por aire del ambiente, mediante convección libre hasta alcanzar 33 °C. El objetivo de esta etapa es lograr la cristalización de la mayor cantidad de glucosa presente. Para contar con un pie de semilla de glucosa se adicionan 126 kg de glucosa por cristalizador. La masa se considera agotada, cuando al determinar el rendimiento en cristales se obtengan valores de 22-23 %. La masa de la primera cristalización pasa por dos filtros prensa de 44 y 46 marcos respectivamente de 1 m2 de área. En este punto se efectúa la separación de torta y licor. La torta contiene la glucosa y el licor obtenido es el jarabe rico en fructosa que debe tener 74-75 °Brix.
La glucosa que sale del filtro pasa a un tanque de 6 m3 de capacidad donde se funde la glucosa hasta obtener una disolución de 74-76 °Brix y temperatura 65-70 °C. La glucosa fundida pasa a una batería de cinco cristalizadores de capacidad de 12 m3 y ocurre el enfriamiento por la acción del aire del medio, mediante convección libre hasta alcanzar aproximadamente una temperatura de 34 °C. Estos cristalizadores contienen un pie de semilla de glucosa, al alimentarse 126 kg de glucosa por cristalizador. Cuando la masa esté agotada debe lograrse un rendimiento en cristales de 26-27 %. La masa obtenida pasa por gravedad al mezclador de la centrífuga, donde se separa la glucosa cristalina con 7-8 % de humedad y 89-90 % de pureza del sirope de glucosa 63-65 °Brix. La glucosa cristalina se envasa en sacos de nylon multicapa de 34 kg. La glucosa producida en esta planta se envía como materia prima para la fábrica de sorbitol, el que tiene como destino final su empleo como aditivo en las producciones que desarrolla la empresa Suchel S.A.
Simulación de las alternativas de mejoras
A partir de los resultados de Díaz y colaboradores 4 y utilizando el modelo de simulación validado se sustituyó la hidrólisis ácida por la hidrólisis enzimática empleando la enzima invertasa 8,11) y se desarrollaron dos alternativas, una manteniendo el método de separación de glucosa actual, cristalización-centrifugación y otra sustituyéndolo por la separación cromatográfica.Por consiguiente, las alternativas a estudiar serán:
Alternativa 1 (Hidrólisis enzimática + cristalización-centrifugación).
En la figura 1 se presenta el diagrama de flujo del proceso propuesto.
Para la simulación del proceso de obtención de glucosa se empleó el programa SuperPro Designer v10.0. Para la operación se seleccionó el modo discontinuo y el tiempo de operación de 330 días al año. Posteriormente se pasó a la selección de los componentes del sistema. Se crearon tres componentes hipotéticos por no existir en la base de datos del simulador; algunas de sus propiedades se reportan en la tabla 1.
Los restantes componentes del sistema se encuentran en la base de datos del simulador: sacarosa, glucosa, agua, oxígeno, nitrógeno y ácido clorhídrico.
Para la simulación de los equipos en los que ocurren reacciones químicas, se seleccionó el módulo tanque de mezclado. Al módulo de preparación se alimentan cuatro corrientes: sacarosa, agua, enzima invertasa y ácidoclorhídricopara la disolución, todas a 25 ºC y 101,3 kPa. La reacción tiene un 95 % de conversión para la inversión enzimática.(11) El flujo de cada corriente se reporta en la tabla 2.
Para la etapa de cristalización se seleccionó el módulo de reactor estequiométrico pues mediante la reacción química de glucosa cristalina (representando el pie de semilla) se obtiene dextrosa (siendo este el producto de interés), para así llevar a cabo el proceso de cristalización y obtener por cada molécula de glucosa una molécula de dextrosa. Se empleó el módulo de filtrado, almacenamiento y centrifugación para la simulación de cada una de las operaciones correspondientes.
Reacción en el reactor estequiométrico:
1 Glucosa = 1 Dextrosa (1)
Como información se introduce la extensión de la reacción en el reactor, expresada como porcentaje de conversión (23 % para la primera etapa de cristalización y 27 % para la segunda etapa de cristalización.
Alternativa 2 (Hidrólisis enzimática + separación cromatográfica)
En la figura 2 se presenta el diagrama de flujo para la alternativa 2
Para la simulación de la separación cromatográfica se seleccionó el módulo de cromatografía y para la evaporación el módulo evaporador. Para la simulación de la operación de separación cromatográfica se alimentan tres corrientes al módulo, agua, hidróxido de sodio y una solución de cloruro de sodio a 0,5 mol/L. Todas las corrientes adicionadas se alimentan a 25 ºC y 101,3 kPa. Los flujos de las corrientes de entrada se presentan en la tabla 3.
Resultados y discusión
Una vez simulada la alternativa de mejora 1, (figura 3), se realizó la comparación entre el caso base de estudio 4 y la alternativa 1.
Los resultados se recogen en la tabla 4.
Se puede apreciar que con la alternativa 1 el incremento en el porcentaje de inversión provoca el aumento del flujo de torta de glucosa, de la glucosa final y de la pureza del sirope de fructosa. Otro aspecto favorable es que el tiempo de inversión disminuye a 2 h. Con esta alternativa se aumenta el rendimiento de producción de glucosa en 1,48 veces.
Además, con la sustitución dela hidrólisis ácida por la enzimática, disminuye el nivel de corrosión del equipamiento industrial y se obtiene una pureza del sirope de fructosa superior.
No obstante, esta alternativa mantiene la desventaja de que el rendimiento del proceso de cristalización continúa siendo bajo y el tiempo del proceso es alto. Con el propósito de solucionar estos problemas se consideró modificar la operación de separación de glucosa invirtiendo en nuevos equipos. Esto dio lugar a la alternativa 2, cuya simulación se presenta en la figura 4.
En la tabla 5 se presenta la comparación entre los resultados de ambas alternativas.
Como se puede apreciar con el cambio del sistema de separación de glucosa, de cristalización-centrifugación a separación cromatográfica, aumentan el flujo de torta de glucosa y la glucosa final. Aunque el flujo de licor de fructosa disminuye, aumenta la pureza del sirope. Los consumos de agua y vapor aumentan debido al empleo de la columna cromatográfica y el evaporador respectivamente. La electricidad disminuye ya que disminuye la cantidad de equipos para el proceso y por tanto la cantidad de bombas necesarias. Con esta alternativa la duración de un lote de producción de glucosa disminuye a 2 días, teniendo una duración de 53 días en el caso base, lo que posibilita hacer 159 lotes más en el año. La producción de glucosa aumenta 2,3 veces con respecto a la alternativa 1, lo que evidencia el aumento del rendimiento de la producción.
Una vez comprobado que se alcanza el objetivo técnico se procedió a calcular la factibilidad económica.
Para la alternativa 1, que no conlleva inversión, se evaluó la relación beneficio/ costo de su implementación. Los beneficios están dados por los ingresos totales que se obtienen con la venta de glucosa y fructosa. El costo de esta alternativa está dado por el consumo de agua, electricidad, vapor y las materias primas; azúcar refino y la enzima invertasa. En la tabla 6 se muestran los resultados.
Tabla 6 Consumo y costo por compra de los insumos empleados para la implementación de la alternativa 1
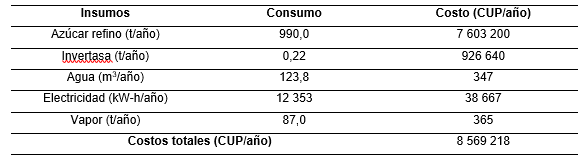
El costo de la implementación de la alternativa 1 es de 8 569 218 CUP/año, mientras que el beneficio está dado por la venta de la glucosa y fructosa producida que corresponde a 11 018 205 CUP/año. La alternativa es económicamente factible ya que la relación beneficio/costo es mayor que 1.
La alternativa 2 lleva inversión, de donde para realizar el análisis económico se calculó el costo de adquisición del equipamiento tecnológico (CAET). Para realizar el cálculo del costo de inversión se utilizó el método de Hand ya que se modifica una planta existente.12 Los resultados se muestran en la tabla 7.
Los ingresos correspondientes a la venta de la glucosa cristalizada y del jarabe de fructosa, para un año de 330 días laborables, con jornadas de 8 h, así como los egresos correspondientes a la alternativa 2 se presentan en la tabla 8.
Para conocer si la alternativa 2 es económicamente ventajosa, se calcularon los indicadores económicos quese presentanen la tabla 9. Se consideró una tasa impositiva de 35 %, una tasa de interés de 12 %, un horizonte de planeación de 5 años y un tiempo de vida útil del equipamiento de 10 años. Los indicadores calculados avalan la realización de la inversión.13
Conclusiones
Se propusieron dos alternativas de mejoras para incrementar el rendimiento de producción de glucosa a partir de la hidrólisis enzimática de la sacarosa, aumentado las producciones de glucosa a 1,5 y 3,5 t por lote respectivamente con las modificaciones realizadas. La producción anual se incrementa en 484 y 1 115 t de glucosa respectivamente. El análisis económico para ambas alternativas de mejoras arroja indicadores que apoyan el cambio de tecnología.