Introducción
El desarrollo de nuevos productos químicos en el país se ha visto limitado por la falta del ácido nítrico concentrado (98-99% en peso). Este producto lo fabrican países con un alto desarrollo industrial, como son: Alemania, Gran Bretaña, Rusia, Estados Unidos etc. y su costo (600 USD/t aproximadamente) se incrementa mucho por el pago de flete, pues para transportar dicho ácido se requieren de condiciones especiales impuestas por tratados internacionales, ya que es una sustancia muy tóxica, lo que dificulta su comercialización. Por otro lado, la importación de este producto puede verse afectada en ocasiones por las condiciones impuestas por el bloqueo económico de los EEUU a Cuba. De ahí que la producción de este producto en Cuba sea atractiva.
Es por ello que se define como objetivo general del trabajo: “Diseñar conceptualmente una tecnología para la obtención del ácido nítrico concentrado al 99% en peso a partir de ácido nítrico convencional”.
Fundamentación Teórica
El desarrollo de un diseño conceptual de un proceso se realiza de conjunto con el estudio preliminar de factibilidad técnico - económica. Lo primero es establecer un proceso de manufactura operable para la producción del producto deseado.
El primer paso en la preparación del diseño conceptual es el establecimiento de las bases para el diseño: especificaciones para el producto, disponibilidad de materias primas, tiempo de operación anual de la planta, temperatura del agua de enfriamiento, presiones de vapor disponible, combustible necesario, etc. Posteriormente se debe realizar el diagrama de flujo del proceso simplificado, mostrando los procesos que están involucrados para decidir cuales unidades de operación serán requeridas. Los flujos y condiciones de las corrientes pueden ser evaluados a partir de balances de materiales y de energía.
Una vez establecido el equipamiento necesario pueden ser determinados los requerimientos de fuerza de trabajo y servicios auxiliares. Los cálculos del diseño conceptual completan los estimados del capital de inversión y del costo total de la producción.
Una forma eficiente y eficaz de llevar a cabo el diseño conceptual es mediante el uso de las técnicas del análisis de proceso dentro de las que se encuentran: la modelación matemática, la simulación de procesos, la optimización, análisis económico, análisis Pinch entre otras. Cada una de ellas juega un rol fundamental en uno o en varios de los pasos del diseño conceptual de un proceso.
La destilación directa es una de las operaciones unitarias más utilizada para la concentración de una solución multicomponentes, pero para la concentración del ácido nítrico a partir del ácido nítrico convencional, es imposible ya que el sistema HNO3 - H2O forma una mezcla azeotrópica como se aprecia en la figura 1.
En la figura 1 se observa que existe un azeótropo en el punto de 68,4 %, que es la máxima concentración que puede alcanzar la mezcla ácido nítrico (diluido) - agua a una temperatura de 121,9 °C y presión atmosférica. Un cambio de la presión durante la destilación del ácido diluido casi no influye pues un cambio desde 0,145 atm (0,146 9 bar) hasta 1 atm (1,013 bar) cambia la composición de la mezcla desde 66,8 hasta 68,4 %.
Es por ello que para obtener concentraciones superiores al azeótropo se han desarrollado diferentes métodos como son:
Proceso del ácido sulfúrico y el nitrato de sodio: tecnología de fines del siglo XVIII donde se obtiene ácido nítrico, tratando el nitrato de sodio con ácido sulfúrico concentrado bajo calentamiento.
Separación completa (destilación extractiva) de la solución acuosa de HNO3 en sus componentes, agua y ácido nítrico, añadiendo otra (tercera) sustancia (agente deshidratante) a la solución: En trabajos realizados (1 se demostró que una manera económica de obtener ácido nítrico de elevada concentración es hacer pasar, a contracorriente, una mezcla de HNO3, H2O y Mg(NO3)2(agente deshidratante), a través de una columna empacada con el vapor subiendo desde el fondo.. Una de las tecnologías, empleando nitrato de magnesio como agente deshidratante, más extendida es la desarrollada por.2
Método de síntesis directa: prácticamente todo el ácido nítrico convencional producido industrialmente se obtiene a partir del NH3 por oxidación catalítica del mismo según la reacción:
La cantidad de agua de reacción formada es importante y cuando se desea producir ácido de elevada concentración es necesario eliminarla casi totalmente ya que como se demuestra en la bibliografía, 3,4 si no se elimina dicha agua la máxima concentración posible de ácido nítrico es del orden de 77% en peso.
La simulación de procesos 5 se lleva a cabo mediante el empleo de simuladores de procesos profesionales (ASPEN PLUS, ASPEN Hysys, Pro II, Chemcad etc.), los que, en la actualidad, debido a su constante desarrollo, pueden brindar soluciones rigurosas a procesos tanto en estado estacionario o transciente.
Un aspecto importante de la conservación de la energía es el establecimiento de una red de intercambio de calor opcional durante el diseño de un proceso. La tecnología pinch permite no solo la reducción del consumo de energía y capital, sino que, además, reduce la contaminación por concepto de calor generado hacia el medio ambiente.6
Materiales y métodos
De los métodos para la obtención de ácido nítrico concentrado el que más se adecua a las condiciones nuestras es la destilación extractiva utilizando como agente deshidratante el nitrato de Magnesio (Mg(NO3)2), dada la sencillez de sus manipulaciones técnicas, rendimiento, calidad del producto y mínimos costos de inversión y de operación. El simulador seleccionado para realizar el diseño conceptual del proceso fue el ChemCad v 6.0, ya que posee el método Wilson - Salt que es el apropiado para el cálculo del equilibrio del sistema HNO3-H2O Mg(NO3)2.
La simulación del proceso se realizó en estado estacionario y se estudiaron 2 alternativas de diseño: alternativa 1 (figura 2), y alternativa 2 (figura 3). Las modificaciones realizadas al caso base se realizaron con el objetivo de disminuir el consumo energético del proceso
Descripción alternativa 1
Inicialmente se carga el regenerador de solvente (tanque flash) con Mg(NO3)2 al 35 %, aquí se concentra hasta un 75 % y sale del mismo a una temperatura de 427 K (corriente 7), posteriormente se enfría hasta los 394 K (corriente 8). Esta última corriente entra a la columna concentradora por el plato 5. La corriente 1 (alimentación de HNO3 50 % en peso) y 303 K se calienta hasta los 393 K (corriente 2) y entra a la columna por el plato 11 como vapor. La solución acídica se queda a una concentración (99 % en peso) más alta que el azeótropo y se destila por la parte superior de la columna (corriente 3) enfriándose posteriormente (corriente 4) y se envía a los tanques de producto. El Mg(NO3)2(corriente 5) se saca por el fondo de la columna a una temperatura de 422 K y una concentración del 68%, esta se calienta (corriente 6) y entra al regenerador de solvente, de este sale una corriente de vapor (corriente 9) con un contenido de ácido nítrico del 0,6 % y una temperatura de 427 K posteriormente se condensa y se envía a proceso.
Descripción alternativa 2
Como se puede apreciar en la figura 3 esta alternativa se diferencia de la anterior en que se mejora notablemente el uso de la energía en el proceso (mediante un estudio Pinch) y para lograrlo se hizo necesario introducir algunos intercambiadores de calor (IC) como se observa en la figura 3. En este caso una carga inicial de Mg(NO3)2 al 35 % en peso se concentra en el tanque flash hasta un 75% en peso, alcanzando una temperatura de 427 K (corriente 14) que pasa al IC 3 donde se enfría al intercambiar con el ácido nítrico al 50% (corriente 7), posteriormente se enfría en el IC 9 hasta alcanzar los 394 K temperatura a la que debe entrar a la columna concentradora por el plato 5. La solución salina comienza a absorber agua del ácido nítrico al 50 %. Este ácido viene a una temperatura de 303K (corriente 1) e intercambia con los IC 1, 2, 3 y 4, y las corrientes 10, 11 y 14 hasta alcanzar una temperatura de 394K para entrar a la columna como vapor al plato 11. La solución acídica se queda a una concentración más alta que el azeótropo (99 % en peso) y se destila por la parte superior de la columna (corriente 3), posteriormente se enfría (IC 7 corriente 4) y se envía a tanque de almacenamiento (una parte se refluja a la columna). El Mg(NO3)2 (corriente 5) se saca por el fondo de la columna a una temperatura de 422K y concentración 68% y se enfría en el IC 8 (corriente 6) antes de entrar al Flash para ser regenerado. Del tanque Flash sale por el tope vapor con un contenido de ácido nítrico diluido al 0.6% y temperatura de 427K (corriente 10). Las corrientes 10 y 11 es el nítrico proveniente del Flash y la 14 es al 75% que sale de este tanque. Finalmente, los vapores de nítrico (corriente 12) son condensados en el IC 10 (corriente 13) y enviados a proceso.
Modelo matemático para el cálculo del equilibrio líquido - vapor en el sistema HNO3 - H2O -Mg(NO3)2
Uno de los aspectos teóricos más importantes del trabajo es el modelo para el cálculo del equilibrio de fases del sistema HNO3 - H2O - Mg(NO3)2, pues la presencia de una sal disuelta en una mezcla de solventes puede frecuentemente significar cambios importantes en el equilibrio líquido - vapor y en el caso de un sistema azeotrópico puede conducir a la eliminación total del mismo como se observa en la figura 4.
Como se puede apreciar en la figura 4 se observa que un incremento en la concentración del nitrato de magnesio mueve el punto azeotrópico hacia concentraciones bajas de la fase líquida y finalmente a una concentración del 60% en peso del nitrato de magnesio desaparece el punto azeotrópico.
Para poder simular este comportamiento fue necesario recurrir al modelo Wilson Salt el que describe la interacción sal - solvente, y que es calculada a partir de los puntos de burbuja de los solventes individuales contenidos en la sal dada, a la presión del sistema.
Cálculo de la torre de destilación (columna concentradora)
Resulta evidente que el equipo más importante del proceso de concentración es la torre de destilación y para poder diseñarla se recurrió a la simulación de la misma. Chemcad ofrece métodos rápidos y rigurosos para el cálculo y diseño de equipos de separación y dentro de los métodos rigurosos, el simulador posee 2 métodos: Inside-Out y otro denominado Correcciones simultáneas (SCDS por sus siglas en inglés). Este último fue el seleccionado pues de acuerdo a recomendaciones de los diseñadores del Chemcad, debe utilizarse para sistemas altamente no ideales, como lo es el nuestro. En el método SCDS es necesario especificar: el número de bandejas, el perfil de presión, todas las corrientes de entrada y platos de alimentación, tipo de condensador, modelo de simulación, si hay o no destilación reactiva etc. Estas especificaciones son suficientes para calcular completamente todas las salidas. Una discusión general del método puede encontrarse en.7
En los procesos de destilación extractiva es de gran relevancia el reflujo a la torre, pues no siempre un incremento de este se traduce como un aumento en la separación de los componentes. Para una relación solvente/alimentado fresco, existe una razón de reflujo óptima, la que da un balance entre los beneficios inherentes del reflujo y el efecto de la concentración del solvente en las volatilidades.
Otra forma de lograr condiciones óptimas operación de la torre es la debida ubicación de los platos de la alimentación y del solvente. Por las razones antes mencionadas se decidió optimizar la relación de reflujo (minimizar la relación de reflujo para disminuir la energía consumida en el condensador y el rehervidor y además el diámetro del a columna).
El Chemcad brinda la opción Optimization que permite maximizar o minimizar una variable (función objetivo) de una corriente o de una operación unitaria, a partir de variables independientes y restricciones (variables dependientes que se restringen).
En este trabajo se toma como función objetivo, minimizar la relación de reflujo y como variables independientes la ubicación de los platos de la alimentación y del solvente.
Diseño de la torre de destilación (columna concentradora)
Una vez calculada la torre (número de platos, ubicación de los platos de entrada para la alimentación y el solvente, la relación de reflujo etc. se pasó al diseño de la misma. Lo primero fue seleccionar el tipo de platos, en nuestro caso se escogió platos perforados (sieve tray) (por ser sencillos y baratos). El cálculo hidráulico para este tipo de platos es tratado en el Chemcad de la manera definida por la referencia.8
Diseño de los equipos de intercambio de calor
Al igual que en el caso de la torre de destilación los equipos de intercambio de calor son previamente calculados mediante la simulación en estado estacionario, y posteriormente se realiza el diseño de los mismos.9 El módulo heat exchanger puede usarse para simular un intercambiador de calor con una o dos corrientes de entrada. Para el diseño de IC del tipo tubo y coraza Chemcad posee un módulo integrado particular para el diseño de los mismos y es el CC-TERM, este módulo sirve también para la evaluación de intercambiadores de este tipo.
La utilización del CC-THERM permite diseñar de forma óptima los IC de tubo y coraza, calculando tamaño óptimo de la coraza, número de pasos por los tubos, número el corte de los bafles, entre otras dimensiones.
Procedimiento para la realización del análisis Pinch
Otro aspecto importante en el presente trabajo fue la realización de un análisis Pinch con el objetivo de mejorar la eficiencia energética del proceso y el resultado del mismo dio origen a la concepción de la alternativa 2 anteriormente explicada. Para llevar a cabo dicho análisis se siguió, el procedimiento siguiente: (explicado a grandes rasgos):
Identificación de las corrientes frías y calientes sus datos térmicos.
Selección valor inicial de ∆Tmin (se tomó 20) recomendado por.10
Construcciones de curvas compuestas (perfiles de temperatura - entalpía de la disponibilidad del calor en el proceso) para determinar el punto Pinch.
Estimación de costo mínimo de energía.
donde:
QU = Rendimiento del servicio auxiliar U, kW
CU = Costo unitario del servicio auxiliar U, $/kW
U = Número total de facilidades auxiliares usadas
Estimación del capital de inversión para la red de intercambio de calor.
Estimación del valor del ∆Tmin óptimo
Estimación de los objetivos prácticos para el diseño de la red
Diseño de la red de intercambio de calor.
Cuando se aplica este procedimiento se obtiene, además de una mayor eficiencia energética, un área mínima de la red de intercambio de calor y por lo tanto un número mínimo de intercambiadores de calor, minimizando el costo de inversión.
Consideraciones para el análisis económico
Este análisis tiene como objetivo determinar cuál de las 2 alternativas es mejor desde el punto de vista económico. Por otro lado, se tiene que en un análisis de alternativas existen 2 posibilidades para saber cuál es la mejor de ellas, la que tiene menor costo inicial y mayores costos de operación o la de costo inicial más elevado y en lo adelante menores costos. Es por ello que el método a seleccionar deba tener en cuenta el valor del dinero en el tiempo y ese método es el del valor actual neto (VAN) y la Tasa Interna de Retorno (TIR) que fue el escogido en este trabajo.11,12
Resultados y validación
Validación de modelo Wilson Salt. Esta se realizó a partir del cálculo de la desviación existente entre la composición del ácido nítrico en la fase vapor obtenida experimentalmente y la determinada por el modelo. En la tabla 1 se muestran los 6 resultados de mayores desviaciones.
donde:
N es el número total de puntos
Para el sistema binario ácido nítrico - agua la desviación siempre estuvo por debajo de 0,31, con un valor promedio global de 0,14. Al introducirse la sal de magnesio a una concentración del 60 % en peso el sistema se comportó como se esperaba, es decir se logró romper el azeótropo de forma similar a como ocurre en la realidad. De aquí se asumió que el modelo era adecuado para su empleo en la simulación. Resultados representativos se muestran en las figuras 5 y 6.
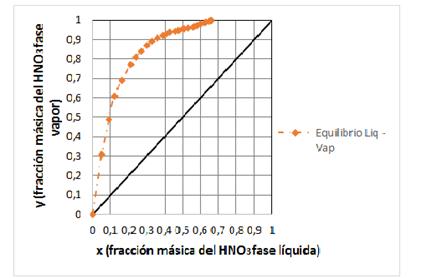
Fig.5 Comparación entre los valores de Wilson Salt y los experimentales para el equilibrio líquido-vapor del sistema ácido nítrico- gua a 1 atm
Diseño conceptual de las alternativas
Una vez definidas las especies químicas que intervienen en la producción del ácido nítrico al 99 %, el modelo a emplear para los cálculos del equilibrio líquido-vapor, los modelos para el cálculo de las propiedades físicas y de transporte y las operaciones unitarias a utilizar en ambas alternativas se procedió a realizar la simulación de cada una de ellas en estado estacionario. Los resultados de los balances de masa y energía se muestran en la tabla 2.
De la tabla anterior puede observase que la tecnología propuesta en ambas alternativas, permite obtener ácido nítrico concentrado al 99% en peso. Por otro lado, el ácido nítrico en la corriente de fondo de la columna en ambas alternativas es muy bajo, 0,06 % en peso, lo que significa que las pérdidas de ácido (ácido que permanece con el solvente gastado en el fondo de la columna y se pierde cuando el solvente es reconcentrado) no son significativas.
Resumen del equipamiento utilizado
Una vez realizada la simulación se pasó al dimensionamiento del equipamiento utilizado, como son: columna de destilación, separador flash y equipos de intercambio de calor y bombeo.
En la tabla 3 se muestra un resumen de las características de diseño de la columna de destilación en ambas alternativas
Columna de destilación
De la tabla anterior se debe señalar que tanto el rehervidor como el condensador de la columna se consideran etapas de la misma, además la relación de reflujo es el mínimo obtenido a partir de la optimización de la columna, también los platos de alimentación tanto del solvente como del alimentado son etapas óptimas. Las diferencias entre ambas columnas aparecen en negrita y en cursiva en la tabla y como puede verse no son relevantes.
Tanque Flash
El tanque Flash es donde ocurre la reconcentración del nitrato de magnesio y es el mismo para ambas alternativas. Ver tabla 4.
Equipos de bombeo
Las bombas 1,3 y 4 de la alternativa 2 consumen mayor potencia que sus equivalentes de la alternativa 1 debido al incremento de presión al cambiar el arreglo de la red de intercambio de la alternativa 2. Ver tabla 5.
Equipos de intercambio de calor
En la tabla 6 se muestra un resumen de las características y dimensiones principales de los equipos de intercambio de calor (tipo tubo y coraza para enfriadores y calentadores) de ambas alternativas
Todos los equipos de intercambio de calor fueron diseñados óptimamente, conservando la relación preferida de diámetro exterior/diámetro interior del tubo.
Resultados del análisis Pinch
Para poder elaborar la alternativa 2 fue necesario conocer de antemano los principales requerimientos de energía a partir del análisis Pinch, resultando ser los siguientes:
Requerimientos de servicios de calentamiento: 708,06 kW
Requerimientos de servicios de enfriamiento: 313,76 kW
Con estos resultados se logra disminuir en un 14 % el consumo de energía (tanto para calentamiento como en enfriamiento) en la alternativa 2 con respecto a la alternativa 1.
Resultados del análisis económico
En la tabla 7 se presentan los resultados del análisis económico luego de haber aplicado el método del VAN y en la misma se muestran los valores obtenidos para el año 10 para ambas alternativas. Como puede apreciarse de la tabla la tasa interna de retorno (TIR) en ambos casos supera el 15 % (tasa mínima atractiva para la industria química cubana), es decir ambas alternativas son atractivas para invertir en las mismas. Desde el punto de vista de costos la alternativa 2 es la mejor pues el VAN es mayor, con una diferencia de $217 902,02.