INTRODUCCIÓN
Los equipos dedicados a la explotación minera en Cuba realizan una intensa actividad en extensos períodos de tiempo, lo que provoca desgastes, deterioros y averías de sus piezas. En economías de consumo, la solución inmediata es su sustitución por nuevo equipamiento, pero en economías en desarrollo se precisa de la capacidad creativa y la inventiva de los profesionales técnicos.
Entre los equipos más empleados aparecen los cargadores frontales de transporte, por eso las paredes y las cuchillas de sus cubos, son unas de las piezas más proclives a presentar defectos, y su recuperación inmediata constituye una necesidad para mantener la producción.
En estos casos, lo ideal es que existan planes para efectuar los diferentes tipos de mantenimiento (Uzcátegui 2014; Ferrer 2015; Mescua y Li 2016; Aviles 2016; Saavedra 2016; Soria 2017; Carhuamaca 2018; Lizcano 2019; Quincho 2019; Jiménez 2021), pero en la minería cubana, las limitaciones económicas afectan la capacidad de posesión de un amplio arsenal de equipos, así que los que existen se sobreexplotan mientras pueda alargárseles su vida útil, independientemente de que esté prevista su etapa de mantenimiento.
Específicamente, entre las múltiples funciones del mantenimiento, el presente trabajo se ajusta a la que pretende alcanzar o prolongar la vida útil del bien a partir del mantenimiento correctivo (o contra la rotura) o mantenimiento por averías (reparación). Aunque su nomenclatura difiere, su fin es el mismo: el reacondicionamiento o sustitución de partes en un equipo una vez que han fallado, es decir, consiste en la reparación de la falla (falla funcional) de manera urgente.
Sobre este tema existen investigaciones precedentes en que se realizan valoraciones económicas y técnicas para el reemplazo de equipos industriales y mineros (Viveros, González y Rodríguez 2004; García, Ulloa y Belete 2013; Huisa 2017; Soria 2017) y para el reemplazo de cargadores frontales (Carhuamaca 2018), que son relevantes desde el punto de vista de sus criterios teóricos y hasta prácticos, pero por las condiciones económicas sólo son aplicables cuando se requiera la sustitución del equipo por modernización o por pérdida total de su vida útil.
Otras investigaciones se ajustan más a los intereses de esta investigación, por abordar la sustitución de partes técnicas (Pérez, Adrián y Simeón 2019; de la Vara y Córdova 2021) y el desgaste en componentes del cargador frontal (Carhuamaca 2018), pero entre esos componentes (inyectores, baterías, bombas de inyección, arrancador, turbo, alternador) no figuran las abordadas en este trabajo.
Fuentes, Villanueva y Estupiñán (2018) sí se refieren a desgastes en componentes de cargadores frontales de transporte, similares a los dañados en los equipos objeto de estudio (planchas, esquineros, cubos), sin embargo, ellos se limitan a los daños en los dientes y entre-dientes.
Ello condujo a plantear el objetivo de proponer un procedimiento para la sustitución de las planchas de las cuchillas de los cargadores frontales de transporte utilizadas en la empresa minera Comandante Ernesto Che Guevara, de Moa, Cuba, a fin de alargar la vida útil de estos equipos.
MATERIALES Y MÉTODOS
La investigación se desarrolló en la Base de transporte de la empresa Comandante Ernesto Che Guevara, Moa, Cuba. A través del mantenimiento preventivo planificado se detectaron las deficiencias de los cargadores frontales de transporte en desuso por averías (Figura 1).
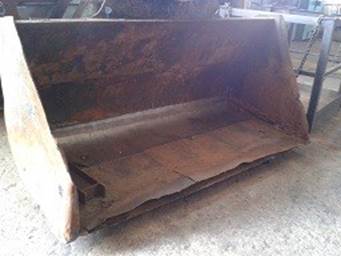
Figura 1 Deformaciones en las paredes laterales y desunión de las planchas por pérdida de las cuchillas en uno de los cubos.
El reemplazo de piezas dañadas se realizó siguiendo las pautas para la fabricación de piezas y agregados según la documentación tecnológica:
Defectado del equipo
Selección del material y la pieza bruta
Selección de las bases tecnológicas
Selección del proceso tecnológico típico o grupo correspondiente
Determinación del contenido y la secuencia de las operaciones tecnológicas
Determinación de la dotación de equipos, útiles y dispositivos tecnológicos e instrumentos de medición
Cálculo de los regímenes tecnológicos para las etapas del proceso productivo
Cálculo de las normas de trabajo y consumo de materiales
Determinación del cargo, oficio y categoría del trabajo de los ejecutores
Definición de los puntos de inspección para el control del proceso según se establece en el actual procedimiento
Definición de los ensayos físicos, químicos o mecánicos por etapas del proceso productivo por etapas
Organización y distribución de las diferentes unidades productivas y medios tecnológicos que lo componen
Elaboración de la carta de ruta tecnológica
Diseño de herramientas y dispositivos especiales necesarios para el proceso de fabricación.
RESULTADOS Y DISCUSIÓN
Las mayores afectaciones se encontraron en las planchas de las cuchillas de los cubos de los cargadores frontales. En virtud de ello se propone un procedimiento para la sustitución de estas planchas en los cargadores de la empresa minera del níquel en Moa.
Procedimiento propuesto para la sustitución de planchas
Defectar los cubos para determinar las zonas dañadas o en mal estado.
Desmontar las partes dañadas de los cubos con chipi jama o mediante el corte con electrodos de carbón, cuidando que no sufran deformaciones ni pérdida de las dimensiones generales.
Esmerilar todas las superficies para eliminar las impurezas o incrustaciones surgidas producto del corte que impidan una buena soldabilidad entre las partes y las piezas a ensamblar.
Escoger las planchas metálicas de acero (laminado en caliente de acero en calidad ASTM A36) para laterales de 8 mm a 10 mm, y de 10 mm a 12 mm de espesor para pisos.
Trazar y cortar todas las piezas según las dimensiones en el defectado: una de 477mmx460mmx8mm y la otra de 2900mmx 350mmx8 mm.
Biselar los laterales de las planchas en forma de «V» y con tacón de 1mm a 2 mm de espesor para garantizar una mejor penetración de la soldadura de ambos materiales.
Ensamblar punteando las planchas en pisos y laterales con el empleo de tranques para prevenir deformaciones o desviaciones y mantener la linealidad, la perpendicularidad entre las piezas a ensamblar y las dimensiones generales del cubo.
Limpiar las superficies a soldar retirando cualquier material contaminante.
Soldar todas las piezas con electrodo revestido E- 6010 Ø 3, 2 mm para el primer pase o cordón de raíz y revestir con electrodo AWS E 7018 Ø 3, 2 mm (el más confiable por su capacidad para resistir hasta 70 000 libras por pulgadas cuadradas) utilizando corriente directa polaridad invertida (CDPI). Encender el arco suavemente mediante el método del rayado o de contacto, según se prefiera, se mantiene un arco corto y se inclina ligeramente el electrodo en la dirección del avance (electrodo al positivo+).
Ensamblar las cuchillas.
Soldar las cuchillas con electrodos AWS E-312 D 3,2 mm, pues estos propician mejor unión entre materiales diferentes (cuchillas de acero al manganeso de difícil soldabilidad con acero al carbono de las planchas).
Mientras que en países desarrollados se reemplaza el equipo averiado o con fallas para obtener ventajas económicas, técnicas o tecnológicas, para un país en vías de desarrollo la sustitución de partes técnicas constituye una necesidad para el ahorro de recursos y una acción válida y confiable.
Con este procedimiento se logró reparar los cubos de los cargadores frontales de transporte (Figura 2) a partir de la sustitución de las partes dañadas adaptando las cuchillas de otros equipos de la mina a los equipos de transporte, así como de las paredes laterales y del piso. Esto permitió alargar la vida útil de estos equipos y, por consiguiente, disminuir el parque de aparatos en desuso.
Los cargadores se reincorporaron a la mina, a la Planta de Preparación de mineral, Planta de Recuperación de amoníaco y cobalto y a la Planta de Calcinación para utilizarlos en las labores mineras y de limpieza y recogida de escombros en todas las áreas de la empresa Comandante Ernesto Che Guevara y en el municipio de Moa.
La recuperación de los equipos utilizando esta vía es factible puesto que se utilizan materiales similares a los que emplea originalmente el fabricante, lo cual facilita que retornen a las actividades productivas. Disminuye asimismo las posibilidades de ocurrencia de accidentes por equipos defectuosos y se reduce el tiempo muerto en la producción y en su mantenimiento. Pudieran también utilizarse planchas de materiales diferentes a los descritos, como: níquel, acero dulce, acero laminado o acero de aleación.
La aplicación de la propuesta propicia la reducción de los gastos de mantenimiento y reemplazo de los cargadores dañados. En el momento de la aplicación su costo de producción fue: 1240,69 cup y el monto ahorrado: 14 759,31 cup en relación con 16 000 cup que costaría si lo efectuara la empresa dedicvada a la recuperación y reparación de equipos de la industria del níquel. Actualmente la tonelada de acero ASTM A36 cuesta $900-$920.
El procedimiento puede extenderse a cualquier taller de fabricaciones mecánicas donde existan los procesos de pailería y soldadura. En este caso, se aplicó el mantenimiento correctivo por la sustitución de partes dañadas cuando el equipo ha dejado funcionar por el exceso de afectaciones a sus componentes; sin embargo, la empresa ha de trabajar por implementar, con sistematicidad, su plan de mantenimiento predictivo adaptado a las condiciones económicas específicas, para evitar afectaciones graves.
Se considera que deben continuarse las investigaciones para la búsqueda de estrategias de trabajo con el apoyo de herramientas tecnológicas que favorezcan el control y monitoreo sistemático a las partes técnicas de los equipos para garantizar su operacionabilidad y disponibilidad siempre que se requiera; además, que contribuyan a predecir la confiabilidad operacional, los modos de fallas, los criterios de riesgo, los sistemas más críticos y la necesidad de recursos materiales para sucesivas etapas del ciclo de mantenimiento.
Con el mantenimiento predictivo disminuye también el costo de mano de obra y de materiales, pues las acciones de reemplazo se realizan según las condiciones de los equipos.
CONCLUSIONES
El procedimiento propuesto para la sustitución de piezas de cargadores frontales permite obtener un resultado confiable, seguro y ventajoso en el orden productivo, técnico y económico que puede aplicarse a otras empresas con similares condiciones y que puede extenderse a otras partes del equipo tras adaptarlo a sus especificidades.
Se hace evidente la necesidad de implementar acciones de mantenimiento más sistemáticas y constantes para evitar paros por averías e incremento del parque automotor en desuso y, como consecuencia, afectaciones a la producción y a la economía.