Introducción
La construcción de equipos para variados usos, que incluye la industria del níquel, son importantes aplicaciones para los materiales plaqueados. Los revestimientos se efectúan sobre aceros estructurales con los fines de prevenir la corrosión o el desgaste mediante la utilización de técnicas que abarcan una amplia gama de procesos, dentro de la cual se encuentra la soldadura por explosión.
Refieren en [1] que, el proceso para revestir una placa de metal sobre otra con el empleo de una carga de detonación, se denomina soldadura por explosivos (explosive welding). En esta distribución, las dos placas están en la configuración paralela y a una cierta distancia de separación, con la carga explosiva encima de la parte superior, denominada la placa volátil. Con frecuencia se usa una capa amortiguadora (hule o de plástico) entre el explosivo y la placa volátil para proteger su superficie. La inferior, denominada metal de soporte, descansa en un yunque para apoyo.
De acuerdo con [2], la soldadura por explosivos es un proceso de soldadura en estado sólido, donde se usa una detonación explosiva controlada para forzar dos metales juntos debido a la alta presión. La unión resultante del sistema compuesto se une de forma durable por la unión metalúrgica debido a que la colisión ocurre a alta velocidad en una forma progresiva y angular, provoca una interfase ondulada o rizada entre los dos metales, la cual fortalece la unión, debido a que aumenta el área de contacto y tiende a entrelazar mecánicamente las dos superficies.
En [3] intentaron explicar el mecanismo de formación de la ola durante la soldadura explosiva basado en el análisis de la deformación plástica de materiales en su área del contacto. Tuvieron en cuenta el hecho que, debido al fuerte impacto, ocurre una desviación significante en los materiales mientras se produce un aumento significante del área del contacto seguido por una deformación plástica irreversible, después del impacto externo el material vuelve en general a su estado inicial mientras excede la superficie de contacto, en un lado el apoyo, permanece presente, pero por el otro lado, debe volver a su estado original. Es esta relajación que puede causar la ocurrencia de la ola como el carácter de la interfase.
Debido a la ocurrencia de las olas en la interfase de la unión soldada por explosión, los autores [4, 5] coinciden en plantear que, bajo condiciones ideales de soldadura, la resistencia a la tracción y al cizallamiento del compuesto soldado es mayor que la del más débil de los componentes, debido al endurecimiento por choque y que el porcentaje de alargamiento del compuesto soldado es en cambio apreciablemente menor, así como una reducción en la resistencia a la fatiga no importante,
En cuanto a la dureza exponen en [6] que, luego de la ejecución del proceso, en ambos componentes, se ve incrementada, por el paso de la onda de choque a través de ellos, resultado de la fusión y del rápido enfriamiento. El efecto del endurecimiento interfacial, que muchas veces se encuentra en este tipo de soldadura, ha sido aprovechado en el endurecimiento de superficies de rieles [7].
También ha sido expuesto por [8] que, los problemas metalúrgicos en la soldadura por explosión no son tan severos como los asociados con los métodos convencionales por fusión, excepto aquellos relacionados con los materiales disimiles, los cuales no pueden ser soldados por medios convencionales. Sin embargo, hay algunos aspectos que están relacionados con este proceso, como el efecto de las ondas de choque, por otro lado, la relativa delgadez de las capas interfaciales, se debe a las altas velocidades de calentamiento y enfriamiento y, por consiguiente, al intervalo de tiempo extremadamente pequeño en que esta intercara permanece a alta temperatura. La deformación del grano interfacial y la formación de una onda sugieren que el mecanismo de soldadura debe ser asociado con un proceso de flujo.
La variación en los parámetros operacionales altera la velocidad de la placa volante, la velocidad de colisión, el ángulo dinámico de la curva y por consiguiente la formación de diferentes naturalezas de interfases como la ondulada, preferidas debido al endurecimiento local de las aleaciones participantes [9].
El trabajo tuvo como objetivo determinar las microestructuras en la interfase y propiedades mecánicas de una soldadura por explosión del acero inoxidable AISI 304 y el acero al carbono AISI 1010.
Métodos y Materiales
La composición química de las aleaciones, como se muestra en la tabla 1 se determinó en un espectrómetro de masa cuántico, ESPECTROLAB 230 con electrodo de carbón bajo arco sumergido en atmósfera de argón.
Tabla 1 Composición química de las aleaciones, % en massa. Fuente: autores
Grado | C | Si | Mn | P | S | Cr | Ni | Mo | Fe |
---|---|---|---|---|---|---|---|---|---|
AISI 1010 | 0,10 | 0,13 | 0,42 | 0,023 | 0,024 | - | - | - | Resto |
AISI 304 | 0,08 | 1,00 | 1,92 | 0,045 | 0,030 | 18 | 12 | 2 | Resto |
El carbono es el elemento fundamental en el acero, ejerce una gran influencia sobre las propiedades físicas y mecánicas del mismo. Eleva su resistencia, dureza y templabilidad. El aumento en el acero para el conformado por explosión eleva de forma creciente su resistencia al desgaste.
La presencia de elementos estabilizadores como el níquel, el manganeso, el carbono y el nitrógeno son necesarios en el caso de los aceros inoxidables austeníticos para disminuir la temperatura del intervalo gamma (austenita). En el proceso de conformado en frío, estos requieren mayores cargas para el conformado que los al carbono. Su diferencia radica en el comportamiento tenso deformacional, referido a la forma de la curva tensión-deformación.
Proceso de soldadura por explosión
Teniendo en cuenta las características del proceso de conformación por explosión, para conformar el casquete esférico, la unión se realizó con una configuración paralela. En la figura 1 se muestra la forma geometría del mismo con sus dimensiones luego de unidas las dos planchas.
Preparación metalográfica
Para la unión de las planchas AISI 1010 y AISI 304, se utilizó como sustancia explosiva industrial el TECTRON 100, emulsión encartuchada en mangas de polietileno. Los parámetros de detonación del explosivo son: densidad ρ 1,15 g/cm3 (1150 kg/m3); energía específica Ee 740 kcal/kg (3 098 232 Nm/kg); velocidad de detonación Vd, que se establece en función del diámetro de la carga y la presión de detonación Pd.
Las operaciones que se realizaron para la preparación metalográfica fueron: corte, desbaste, pulido, desengrasado, lavado y ataque químico. Las muestras fueron cortadas en una fresadora vertical 6 M 12 L con número de revolución de 40 r/min y con avance de 25 mm/diente. Las dimensiones fueron de 15 x 15. Durante el corte se empleó abundante refrigeración con el objetivo de no alterar la estructura metalográfica con el calentamiento por efecto de la fricción. En la figura 2 se muestra el área de la sección del casquete de donde se realizó la selección.
Luego de cortadas y teniendo en cuenta las dimensiones y el espesor de las muestras obtenidas, se encapsularon con epoxi ROYAPOX 5050 para realizar las operaciones de desbaste y pulido y garantizar el manejo de las mismas en las operaciones sucesivas.
La selección de las muestras en esta área obedece a que, existe una primera zona que, aunque estuvo expuesta a la deformación plástica, la distribución en el tamaño del grano, debe diferir de la segunda, debido a que, en esta última, por el efecto combinado de la conformación y la explosión, debe existir la formación en el tamaño de los granos.
El desbaste consistió en obtener una superficie plana y semipulida. El pulido se realizó, variando la granulometría de las lijas, desde la más gruesa a la más fina, se empleó óxido de cromo añadida sobre discos provistos de paños. Una vez pulida se lavaron con agua destilada, se secaron con papel de filtro y finalmente se volvieron a lavar con tetracloruro de carbono para evitar vestigio de grasa y pastas de pulir. Se empleó las técnicas de ataque químico y manual por inmersión. El de inmersión, se realizó durante cinco segundos con el reactivo ácido clorhídrico al 50 % (50 ml HCl; 50 ml H2O), este delinea la ferrita, por lo que revela sus fronteras y el nital al 4 %.
Microestructura patrón de las aleaciones
Para la observación de las microestructuras se empleó un microscopio óptico binocular marca NOVEL modelo NIM - 100. El análisis microestructural consistió en la observación de una muestra patrón como se muestra en la figura 3 de las aleaciones.
En la figura 3, correspondiente al AISI 1010, se observa una proporción de ferrita (blanca) y una pequeña cantidad de perlita (negro), la distribución de los granos es en una matriz ferrítica, la microestructura, está compuesta por una estructura de matriz austenítica, con presencia de granos austeníticos equiaxiales de diversos tamaños y de fase martensítica, figura 3a.
Para la medición de la dureza (HV) se utilizó un durómetro digital modelo HRS-ISO (Digital Rockwell Hardness Tester), para lo cual se realizó un barrido en las diferentes zonas de los dientes de barridos (centro, borde y entre centro y borde), las que se promediaron, la carga aplicada fue de 0,49 N; en un tiempo de 15 s. El indentador empleado fue el de pirámide de diamante, con un ángulo de 136º.
Mallado del modelo para los elementos finitos
La resolución de cualquier problema ya sea mecánica o de cualquier otro tipo mediante el método de los elementos finitos requiere definir previamente el mallado de los elementos. En la figura 4 se muestra las dimensiones para el mallado de la soldadura disímil por explosión del acero AISI 1020 y del acero AISI 304 y en la 4a, el modelo mallado.
Los elementos a deformar se consideran placas finas, cuyo grosor es pequeño comparado con las otras dimensiones. Una placa de este tipo, sometida a pequeños desplazamientos puede analizarse tomando en cuenta que, con aproximaciones, las deformaciones varían linealmente a través de ella, el esfuerzo normal (fuera del plano) y las deformaciones por cizallamiento son despreciables y la tensión normal fuera del plano y el esfuerzo de cizallamiento en la dirección x; y son pequeños comparados con la tensión normal en el plano y el esfuerzo cortante.
Resultados y Discusión
Microestructuras de la unión disímil
Se realizó el análisis microestructural para determinar las variaciones luego del proceso de soldadura por explosión entre el acero AISI 1010 y el AISI 304. Para caracterizar cada una de las estructuras se efectuó observaciones a diferentes distancias: 5, 7, 15 y 25 mm. En la figura 5 se muestra el comportamiento obtenido según el procedimiento realizado.
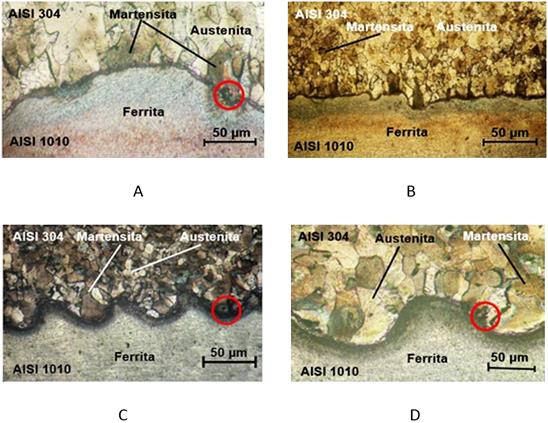
Fig. 5 A. Zona a 5 mm de la explosión. B.Zona a 7 mm de la explosión. C. Zona a 15 mm de la explosión. D. Zona a 25 mm de la explosión.
En las estructuras obtenidas de la unión disímil entre los aceros AISI 1010 y 304, la parte superior se corresponde con el acero AISI 304, está compuesta por fases de austenítica y martensita con diferentes tamaños de granos según sea la distancia en la que ocurrió la detonación, en la parte inferior que es la del acero AISI 1010 la morfología es de granos de ferrita de granos exquiaxiales de pequeños tamaños, los cuales se reducen en la medida que se acercan a la interfase de la unión. Entre ambas aleaciones existe una línea que la divide, donde se ha formado una red de carburos M7C3 o M23C6 (círculos rojos).
La interfase presenta una modificación de la microestructura en la línea de fusión con refinamiento de grano, un crecimiento marcado por los límites de grano y en el interior existen pequeños subgranos. Existe la disminución del tamaño de los granos por la compactación dinámica cerca de la línea de fusión, mientras que, en el centro, la microestructura es equiaxial debido a la solidificación constitucional del cordón después de realizado la explosión. Se muestra una morfología en forma de ola, para 5 mm, estas tienen un comportamiento ondulado no profundo, lo cual puede estar asociado a la presión al inicio de la detonación, para las demás distancias, la formación es en forma de cresta, con mayor deformación de la estructura, lo que demuestra que, en la medida que el chorro de reacción interactúa entre los dos materiales, se logra el compactamiento metalúrgico.
La estructura ondulada mostrada durante la soldadura explosiva, la energía mecánica desencadenada por el impacto produjo una deformación plástica en la interfase. La amplitud y longitud de onda de la morfología ondulada permite estimar el grado de deformación durante el choque de ambas placas. La transición de una interfase ondulada a uno recto se relaciona con una disminución en la tensión plástica y con la disminución de la velocidad de impacto, debido a alta fuerza de las tensiones, según [10].
La placa volante está sujeta a una intensa ola de tensión con la detonación de la capa explosiva en el contacto con ella y como consecuencia esta y la base experimenta una ola de tensión que es el resultado de la alta velocidad impacto. Estas intensas olas dan lugar a los cambios metalúrgico y como resultados en un aumento en la dureza, reportado en trabajo previo de [9-10].
Análisis microestructural en la zona afectada por el calor
Se realizó el análisis microestructural en la zona afectada por el calor de la unión soldada. En la figura 6 se muestra el comportamiento obtenido en esta zona medida a diferentes distancias.
Las microestructuras obtenidas en esta zona mantienen la misma tendencia en cuanto a la formación de fases, la austenita y martensita para el AISI 304 y la ferrita equiaxial para el AISI 1010, sin embargo, en cuanto al tamaño de los granos, estos son mayor en esta zona. En esta área existe un volumen de carburos (círculos rojos), los cuales se encuentran ubicados, tanto en la línea de interfase, como en el AISI 304.
En la zona afectada por el calor, el comportamiento descrito por la ola está asociado al comportamiento tenso deformacional de ambas aleaciones, donde el material de mayor ductibilidad, el AISI 304, se introduce por efecto de la difusión en el acero AISI 1010, permitiendo que, por los átomos del mismo se difunda las estructuras en los del material de mayor dureza. La ocurrencia del fenómeno se debe a la presión de detonación y la energía cinética que permite la difusión a nivel interatómico para lograr la unión metalúrgica entre ambas aleaciones, según criterio reportado en [2, 3, 4, 5].
Se analizó la dureza obtenidas en las zonas para las diferentes distancias. En la figura 7 se muestra el comportamiento obtenido.
En los valores de dureza de las diferentes zonas, esta tiene un comportamiento más alto en el acero AISI 304 en relación al acero AISI 1010. Al efectuar la soldadura por explosión, la formación de carburos en el acero inoxidable tiende a incrementar esta propiedad, no así con el acero al carbono, donde los tenores de carbono y manganeso no permiten un aumento por el tratamiento. Por otro lado, el grado de deformación plástica y la fusión metalúrgica que se origina en la interfase, pueden acrecentar la dureza en las diferentes áreas de la unión por el apilamiento de los granos. Por otra parte, el estado de tensiones en el grano, activan otros sistemas de deslizamiento que interactúan con él o los ya existentes, este mecanismo dificulta la movilidad de los átomos y origina el fenómeno conocido como endurecimiento latente, lo que fue expuesto por [2].
Resultados del Método de los Elementos Finitos
Las simulaciones numéricas identifican los factores como el nivel de tensión inducido en las placas y la dirección de la tensión en la zona de la colisión, independientemente de las características de los materiales, el chorro de reacción logra el proceso de soldadura. En la figura 8 se muestra el comportamiento de la deformación plástica.
La máxima deformación en el proceso de soldadura por explosión y embutición del AISI 304 y del AISI 1010, se encuentra en el radio inferior del elemento y su valor es de 4470 x 10-3 mm, esta deformación plástica se expanden progresivamente por los demás radios de la estampa hasta lograrse la conformación del casquete esférico. El proceso se ha desarrollado por el efecto de la deformación.
Los valores obtenidos son de 1117 x 10-3, cerca del pisa plancha; 2235 x 10-3 mm, en el radio de curvatura, hasta llegar a la mayor en el fondo del casquete.
Con la deformación plástica se comprueba que, el área donde ocurre la mayor deformación y, estricción es el fondo de la pieza. En esta ya embutida por efecto del explosivo, como dos cuerpos pegados de diferentes materiales no se separan, aunque sus deformaciones sean diferentes, por lo que el material es considerado como uno solo, teniendo en cuenta que la embutición no es profunda no existe una gran deformación y la velocidad de desplazamiento de la onda explosiva, no se considera elevada.
Se analizó las tensiones obtenidas del proceso de simulación. En la figura 9 se muestran las tensiones de Von Misses obtenidas.
Al analizar las tensiones, se encuentra en el orden de los 1815 x 10012 MPa. En el proceso de soldadura por explosión y conformación, se observa que, la zona anular está sometida a un esfuerzo de tensión radial y a uno anular de compresión, mientras que la pared a uno de tensión. El modelo elastoplástico obtenido y considerado para cada capa, por ser dos materiales soldados, se asume que la adhesión de las mismas es perfecta y por esta razón, la tensión entre las superficies de contacto es uniforme, criterio de [11].
En la figura 10 se muestra el comportamiento obtenido de la deformación unitaria del proceso de explosión y conformación entre el acero AISI 304 y el AISI 1010.
La deformación unitaria obtenida es producto de la fuerza inicial de tensión, la cual es cero al inicio del proceso y se incrementa gradualmente hasta llegar a 6129 x 10000 mm, con tensiones de 1815 x 10012 MPa, todas estas solicitaciones ubicadas preferencialmente en el área cercana al pisa plancha y en el fondo del casquete. En ambos casos, la deformación unitaria será igual a la misma en una dirección menos en sentido transversal a la anterior. Durante la conformación, esta deformación unitaria en el casquete es la misma que se obtiene en el radio, criterios de [12].
Conclusiones
Por efecto del choque explosivo entre el acero al carbono AISI 1010 y el austenítico AISI 304, la unión metalúrgica se logra con una interfase ondulada, la cual difiere de su formación en dependencia de la distancia en que ocurre la detonación, lo cual favorece el compactamiento metalúrgico.
Las microestructuras obtenidas en ambas aleaciones luego de la soldadura por explosión entre las dos aleaciones, para el AISI 1010 es de ferrita equiaxial y en el AISI 304 es de austenita y martensita, pero con una formación de tamaño de granos más pequeños, modificados por la onda de choque expansiva del explosivo, quien generó en el AISI 304 la presencia de carburos del tipo M7C3 o Cr23C6.
Por efecto de la deformación plástica generada por la onda de choque del explosivo entre el acero al carbono y el austenítico, en la interfase de ambas, existe variaciones en la dureza, de 300 HV para el primero y de 450 HV para el segundo, lo cual está vinculado al apilamiento de los granos y a la formación de los carburos.
Mediante los elementos finitos se determinó que, durante la conformación del casquete esférico por explosión, la mayor deformación ocurre en el radio inferior (fondo), la cual se expande a los demás radios en la medida que ocurre la detonación, quien también provoca tensión radial y anular de compresión en el centro y las paredes de la estampa.