INTRODUCCIÓN
La formación de un perfil cilíndrico para obtener una tubería de acero con costura longitudinal require de la determinación previa del ancho de la lámina o fleje, de manera que cumpla con las especificaciones que solicite el cliente. Para la fabricación del tubo, el rollo de lámina de acero o galvanizado es instalado en la máquina para ser desenrollado y enderezado.
Las industrias dedicadas a la producción de tuberías por conformado en frío deforman plásticamente estos metales o aleaciones de diferentes grados, por medio de matricería o rodillos. Durante el conformado en frío, de la lámina se elaboran otros productos mediante diversos procesos de deformación (Roll Forming) y con la aplicación de soldadura. La máquina perfiladora o formadora de tubo, compuesta por rodillos, tiene la función de darle la forma al tubo a través de diferentes etapas. La longitud y el espesor dependen de las características de esta máquina.
La transformación de una lámina en un tubo con costura es el resultado de una serie de operaciones continuas que incluyen conformación, soldadura y calibración. Se realiza por un proceso gradual de curvado en la etapa de conformado hasta la forma final para ser soldada mediante el proceso de inducción de alta frecuencia (HF, por sus siglas en inglés) que entra en la categoría de soldadura por resistencia eléctrica (ERW, siglas en inglés). La deformación ejercida en la lámina debe ser distribuida uniformemente en cada paso, a fin de disminuir los esfuerzos internos que ocasionan inconvenientes en operaciones posteriores y baja calidad de los productos (Davydov et al. 2020).
Medina-Mendoza, Méndez-Macías y Herrera-Reyes (2020) refieren que en la ERW se induce una tensión a través de los bordes del tubo abierto antes del punto de cierre. Ello causa una corriente que fluye a lo largo de los bordes hasta donde estos se juntan, provocando rápido calentamiento del metal por el efecto Joule. Los rodillos de soldadura presionan el metal caliente a entrar en contacto, fuerza al metal fundido y algunas impurezas fuera del área de unión, generando una especie de forja y resultando en una de las estructuras de soldadura más fuertes.
De acuerdo con Koide, Kondo y Itadani (2006), después que la ERW es completada, aparecen una serie de microestructuras alrededor de la línea de unión de la soldadura (Figura 1). En la posición 4 el metal base no ha sido afectado por el calor. La 3 marca el inicio entre metal base y el afectado por el calor, mientras que en la 2 el metal es calentado pero no fundido. La posición 1 corresponde a la línea de unión.
Las líneas de flujo son bandas visibles producto de la operación de laminado y corren paralelas a la dirección de deformación. El ángulo y la simetría de estas líneas indican la representación de los bordes planos y paralelos en la soldadura (Scott 1996). Ha sido reportado por Li y colaboradores (2010) en la aplicación de la soldadura que las altas corrientes y las bajas velocidades de avance con arco aportan una gran cantidad de calor por cada unidad de longitud facilitando su enfriamiento lento. Adicionalmente, los espesores gruesos del metal base y su baja temperatura permiten la disipación rápida del calor y, por lo tanto, el rápido enfriamiento.
La resistencia del acero al flujo de la electricidad causa que los bordes de la tira se sobrecalienten en una zona localizada. Al ser calentados a 720 °C, el hierro comienza a transformarse de ferrita a austenita; los carburos comienzan a disolverse y el carbono a moverse dentro de los espacios de los átomos de hierro de la austenita. El carbono continúa difundiéndose hacia la parte más caliente, donde es más soluble. El calor fluye hacia el interior del borde, aumentando la temperatura y causando cambios en la estructura cristalina (Davydov et al. 2020).
Este trabajo tuvo como objetivo caracterizar las estructuras de la zona de unión soldada de un tubo fabricado con costura mediante soldadura ERW a partir de una lámina de acero galvanizado ASTM A653CS tipo B.
DESARROLLO EXPERIMENTAL
Composición química de la aleación
La Tabla 1 muestra la composición química del acero galvanizado usado para la fabricación de tubo con costura, según norma ASTM A53 Grado B (2013).
Se trata de un acero galvanizado con un recubrimiento de Zn puro y un contenido de Al aproximado de 0,2 % a 0,3 % que se adiciona al baño para mejorar sus propiedades anticorrosivas. El efecto se encuentra relacionado con la formación de una capa continua de Al2O3 que inhibe la oxidación posterior, actuando como una barrera protectora. Son suministradas en paquetes de 2,5 tm a 3 tm, aproximadamente. Las bobinas con denominación BZLI JISG 3302 vienen con peso mínimo de 4 tm. El revestimiento de zinc G40 - mínimo 120 g/m2.
Caracterización del material del tubo
La placa o rollo pasó a los rodillos formadores donde se sometió a pasos progresivos de conformado (4 de preforma y 3 de conformado final), donde la materia prima adquirió la forma de "O". Durante el último paso, cuando el tubo se cerró completamente, se aplicó la soldadura por el proceso de resistencia eléctrica de alta frecuencia. Luego de ser obtenido el tubo soldado en toda su longitud se seleccionó un tramo, que se muestra en la Figura 2, para determinar la estructura interna y dureza del cordón.
El tubo de acero galvanizado tiene longitud de 350 mm de largo, 52 mm de diámetro y 3 mm de espesor de pared. En él se observa el cordón de soldadura longitudinal limitado por la zona fundida y la afectada por el calor.
Selección de las muestras
Las muestras se seleccionaron sobre la sección de la tubería preparada para la soldadura, como se muestra en la Figura 3. Para el desarrollo de los ensayos, los cupones fueron obtenidos tanto del cordón exterior como del interior del tubo.
La soldadura por resistencia eléctrica de la unión en la tubería se realizó a tope sin preparación de los bordes. Se consideró que en este proceso el recubrimiento de zinc y las inclusiones tienen incidencias en la estructura interna del material en el cordón, ya que el atrapamiento de óxido puede ocurrir cuando se mezcla con el baño de fusión o el material extraño presente en la superficie no es completamente removido.
Se siguió una progresión longitudinal la cual logra alta penertración en la raíz, poca escoria, buena calidad, mayor uniformidad en el cordón y permite mejor control por su rápida solidificación. La razón de esto es que permite al metal de soldadura y a la ZAC enfriarse lentamente, si la velocidad de arrastre es uniforme. El enfriamiento lento genera una microestructura con granos más finos, obteniéndose una unión dúctil y suave. Las probetas fueron extraídas del ensamble de soldadura, mecanizadas y luego sometidas a ensayos de dureza, microdureza, análisis de composición química y microscopía óptica.
Preparación metalográfica de las probetas
En la preparación metalográfica se realizó un conjunto de operaciones como son: desbaste, pulido, desengrasado y lavado (ASTM E 3 - 95 y Norma NC 10-56: 86).
El corte se realizó considerando la cara interna de las probetas, dando prioridad al área cercana a la raíz de la soldadura. Se tuvieron en cuenta tres probetas de cada sección de tubería, seleccionadas cada 120o alrededor de la circunferencia, como se muestra en la Figura 4.
Para tuberías con costura realizada con ERW, el espesor de la probeta debe ser, al menos, de un 80 % del espesor completo, en ese caso no es aceptable realizar un aplanado (NACE TMO-284 (1996). Se consideraron, además, mediciones de profundidad para los defectos, tanto internos (raíz del cordón) como para la parte externa del cordón.
La operación de desbaste y pulido se realizó variando la granulometría de los papeles abrasivos, desde la más gruesa a la más fina, del tipo No. 400, 600, 800 y 1 000 (ASTM E3-95). Se colocaron sobre una placa de vidrio, cambiando el sentido del lijado a 90º al pasar de un pliegue a otro para eliminar la capa de material distorsionado y deslizado dejado por el anterior. Las muestras se pulieron en una pulidora metalográfica, utilizando un paño de fieltro grueso y como sustancia abrasiva el óxido de cromo. Una vez pulidas las muestras se lavaron con agua destilada, secándose con papel de filtro. Se volvieron a lavar con tetracloruro de carbono (Cl4C) para evitar cualquier vestigio de grasa y pasta de pulir.
Para atacar las probetas se empleó como reactivo químico el nital al 5 %. Se vertió en una cápsula en la que se introdujo la probeta, se detuvo el ataque sumergiendo las mismas en el agua y luego se observó la superficie. Después del ataque se lavó la probeta nuevamente con abundante agua corriente, se secó con alcohol (absoluto) y al aire.
Para medir la microdureza se utilizó un microdurómetro modelo PMT 3 No. 168, objetivo acromático acoplado, y compensación libre trinocular de tubo inclinado a 30º. Se efectuaron en diferentes lugares de la muestra tres mediciones, las que se promediaron. La carga aplicada fue de 0,49 N, en un tiempo de 15 s. El indentador empleado fue el de pirámide de diamante, con un ángulo de 136º según la ASTM E 92-82.
Como en el proceso de soldadura las zonas que se obtienen son de un margen de pequeños milímetros se precisó la limitación de cada una de ellas, se midió dureza en el material base (MB), en la zona afectada por el calor (ZAC) y en la interfase del cordón de soldadura. Se realizó el mismo procedimiento en ambos extremos de la soldadura.
El análisis químico del material se realizó en un espectrómetro de masa cuántico, ESPECTROLAB 230, con electrodo de carbón bajo arco sumergido en atmósfera de argón.
RESULTADOS Y DISCUSIÓN
Análisis de la composición química
Comparando los valores establecidos por las normas con los obtenidos (Tabla 2), según el análisis spectral, se observa que el acero analizado cumple con los requerimientos de la especificación para material suministrado en bobina con 0,076 % C; se puede catalogar como un acero hipoeutectoide, endurecido por refinamiento de grano y precipitación.
Análisis microestructural para el cordón exterior
El examen microestructural de la ZAC del metal base de la junta muestran distintas regiones que varían notablemente debido al ciclo térmico local experimentado durante la soldadura. Se analizaron las microestructuras de las diferentes zonas obtenidas para el depósito del cordón exterior. En la Figura 5 se muestran los resultados.
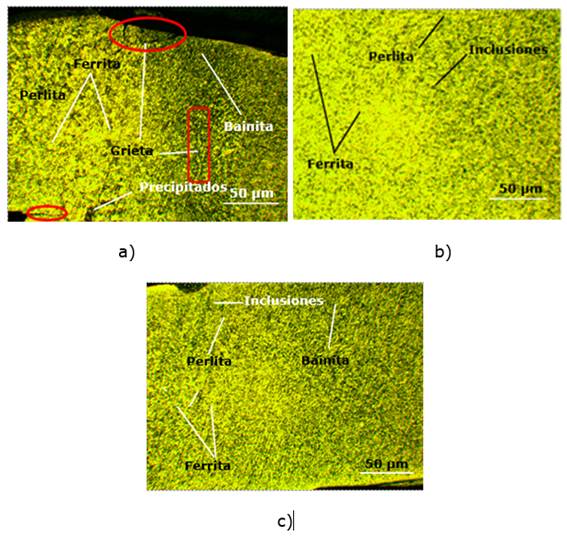
Figura 5 Microestructuras de las zonas obtenidas para el depósito para el cordon exterior. a) Zona fundida; b) Zona afectada por el calor; c) Interfase del cordón.
En la zona fundida (Figura 5a) se observa que, en la unión soldada la estructura del metal presenta granos finos, con perlitas en una matriz ferrítica equiaxial y ferrítica de granos gruesos. El mecanismo para este crecimiento se basa en la movilidad de la austenita hacia los granos de ferrita que le rodean. Esta estructura disminuye de grosor hasta desaparecer en la zona adyacente al cordón, debido al calor generado en el proceso de soldadura. La forma de los granos está controlada por la forma de la pileta líquida a través de la acción del crecimiento competitivo (los nuevos granos columnares que están creciendo compiten entre sí para crecer uno a expensas del otro según favorezca su orientación cristalográfica).
En esta zona, en el borde superior, inferior y centro, existe formación de grietas, lo cual obedece a las condiciones de transferencia de calor y desplazamiento de material en el momento que el metal alcanza la máxima temperature, desde 1 350 °C - 1400 °C y los bordes de la placa son recalcados uno contra otro, según consideraciones de Haga et al. (1979).
La ZAC (Figura 5b) está compuesta por perlita de grano fino (área oscura) en la matriz ferrítica (área clara), la formación de estas fases son producto de la descomposición de la austenita, donde la ferrita nuclea en los límites de grano de esta, cuando la temperatura empieza a decaer por debajo de la crítica A3, conforme disminuye el carbono se disuelve en la austenita restante transformándola en perlita por debajo de la crítica A1. También, producto del ciclo térmico se ha obtenido un área de bainita superior, la cual tiende a aumentar en la medida que disminuye la ferrita y el tamaño de grano se aproxima al borde exterior del tubo.
Esta bainita es producto de la transformación de la austenita durante su enfriamiento, cuando se encuentra entre los 550°C y los 400 ºC. Se considera que esta bainita superior está constituida por finas placas de ferrita de 0,2 μm de espesor y hasta 10 mm de longitud. Estas placas crecen en columnas agrupadas, las cuales son paralelas y presentan una misma orientación cristalográfica, así mismo, cada una de ellas tiene un plano de hábito cristalográfico bien definido. Se observa la presencia presumiblemente de inclusiones de sulfuro de manganeso.
En esta zona se observa el tamaño de grano más pequeño lo que parece indicar que las altas temperaturas y deformación ejercida por la presión del rodillo en los bordes de la placa generaron las condiciones para el desarrollo de mecanismos tales como recristalización dinámica o interdinámica, dando como resultado una zona de refinamiento de grano, según consideraciones expuestas (Sabzi et al. 2018).
En la interfase del cordón (Figura 5c) se ha obtenido un tamaño de grano grueso recristalizado, provocado por un aumento de la temperatura mayor a la temperatura A3. Aquí la distribución de los granos de la ferrita y la perlita no es uniforme debido a la alta tasa de calor aportado a la junta durante el soldeo que impide una rápida difusión del carbono y un crecimiento lento de granos de austenita. Adyacente a esta primera zona se da otra de grano fino, más parecido al grano que ha sido normalizado. Esta zona de grano fino se crea entre las temperaturas A1 y A3 en donde están presentes ferrita + austenita; la austenita durante el enfriamiento se descompone en granos finos de ferrita + perlita (Lambert et al. 2004).
Análisis microestructural para el cordón interior
La soldadura por resistencia eléctrica (ERW) actúan también, en cierta medida, sobre las estructuras de las zonas de trasformación del metal base en una sucesión de capas alternadas de zonas afectadas y parcialmente normalizadas, distribuidas en un volumen muy reducido, entremezcladas y muy complejas debido al tratamiento térmico. En la Figura 6 se muestran las zonas obtenidas en el depósito del cordón interior.
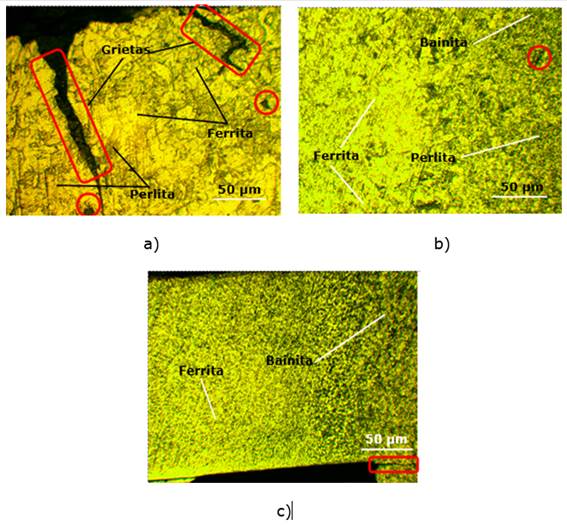
Figura 6 Microestructuras obtenidas en el depósito del cordon interior. a) Zona fundida; b) Zona afectada por el calor; c) Interfase del cordón.
En la zona fundida (Figura 6a), se caracteriza por la formación de un perfil de ferrita y perlita, la ferrita forma una red alrededor y en los límites de grano de la perlita (áreas oscuras) y ferrita (áreas claras alargadas) que ingresan desde el límite de grano hacia el interior de la perlita. Aunque en esta zona no se ha sobrepasado la temperatura de transformación, esta y el tiempo de permanencia son lo suficientemente altos como para generar un crecimiento del tamaño de grano, debido a que en esta zona el ciclo térmico es de menor intensidad.
Se observa que, esta zona es de ancho irregular, presenta discontinuidad, producida por materiales extraños atrapados (óxidos formados (círculos rojos) y no expulsado en el momento de la forja, así como la formación de grietas, presumiblemente formada por la presión de los rodillos e indicativo de que los bordes exteriores de la placa en la zona adyacente al diámetro exterior del tubo alcanzan mayor temperatura que en esta área.
El metal de soldadura y la zona afectada por el calor (Figura 6b) llegan a ser más complejos durante la soldadura, ya que una porción de esta zona es recalentada por el ciclo térmico. La microestructura está constituida por granos de ferrita ligeramente deformados, cuyo tamaño es aparentemente inferior al observado en el metal base. La perlita que originalmente era laminar, experimentó una esferoidización, debido a las temperaturas alcanzadas (alrededor de 720 °C) durante el proceso de soldadura; dicha esferoidización se desvanece a medida que aumenta la distancia desde el límite de la zona, coincidente con Sabzi y otros investigadores (2018).
En la interfase del cordón (Figura 6c), la estructura es de ferrita+perlita, pero de menor tamaño de granos. La microestructura en la región de transición entre la ZF y la ZAC se compone de una mezcla de granos pequeños (de la zona de refinación) con pequeñas islas de perlita y otra parte la componen granos de ferrita proeutectoide de la ZAC y colonias de perlita esferoidizada; dichos granos de ferrita y colonias de perlita esferoidizada están orientados en la dirección hacia donde ocurrió el desplazamiento de metal durante la soldadura.
Por los resultados obtenidos del cordón interior y exterior, se confirmaría que como resultado de mayor temperatura en el diámetro exterior, el ancho de la ZAC es también mayor hacia el borde exterior, sin embargo, también podría indicar que dada la forma en que entran en contacto los bordes, esto significa que, en el momento de formar el tubo los bordes inferiores, o correspondientes al diámetro interno, están más próximos uno con otro que en la zona del exterior, generando menor presión en los exteriores y, por ende, hubo menos desplazamiento de material, dejando en la zona exterior más metal calentado a la temperatura de recalcado.
Comportamiento de la dureza en relación al tamaño de grano
En el análisis de la dureza realizado a diferentes distancias en relación al tamaño de grano, se consideró el barrido en la zona superior y en la zona inferior del cordón (pileta). En la Tabla 3 se muestra los resultados obtenidos de los ensayos de dureza Vickers realizados en cada una de las zonas de estudio. Se realizaron tres barridos en la probeta, el primero hacia la superficie exterior, el segundo en el centro y el tercero hacia la superficie interior del espesor del tubo.
Los valores de microdureza obtenidos en las tres zonas para los barridos ejecutados en cada probeta permitieron determinar la dureza, que posibilita una comparación entre los valores obtenidos en el metal base y el metal de soldadura, así como en la zona afectada por el calor, la cual presenta mayor variación de esta propiedad gracias a los cambios microestructurales.
El espesor de cada ZAC, medido en tres puntos, se observa que, en el lado interior del tubo la longitud total oscila entre los 6,45 mm y 7,0 mm; a la mitad se encuentran valores desde 3,8 mm hasta 4,17 mm y en el lado exterior desde 7,0 mm hasta 7,5 mm. Esto confirma que, como resultado de mayor temperatura en el diámetro exterior, el ancho es también mayor hacia el borde exterior, sin embargo, también podría indicar que, dada la forma en que entran en contacto los bordes, en el momento de formar el tubo los inferiores, o correspondientes al diámetro interno, están más próximos uno con otro que en la zona del diámetro exterior, generando menor presión en los exteriores y, por ende, menos desplazamiento de material, dejando en la zona exterior más metal calentado a la temperatura de recalcado, según Bhatti y demás colaboradores (2015).
A medida que el tamaño de grano en el espesor de la soldadura es más pequeño, la tenacidad es mayor aún, cuando para la zona media, el tamaño de grano es más grande que en la zona inferior, por lo tanto, la tenacidad es mayor en esta área; la diferencia en el ancho de la línea ferrítica se debe a que en la zona inferior es mayor, lo que causa una disminución en las propiedades mecánicas, criterio expuesto por Davydov y otros investigadores (2020).
La dureza, como propiedad mecánica, puede proveer una estimación por fragilización de las diferentes sub regiones de la ZAC de un acero. Para aceros de alta resistencia y baja aleación, una mayor que 350 HV (dureza Vickers) puede ser considerada excesiva y llevar a la fragilización y sensibilidad a la fisuración en esta zona, según Modenesi, Marques y Santos (2012). Como los resultados de microdureza presentados en la Tabla 3 no exceden este valor, se puede plantear que, aunque sea rápido el enfriamiento durante el proceso de soldadura, este acero no es susceptible a la formación de estructuras frágiles en la ZAC.
CONCLUSIONES
El cordón superior obtenido con soldadura por resistencia eléctrica en el tubo galvanizado presenta estructura de granos finos, con perlitas en una matriz ferrítica equiaxial y ferrítica de granos gruesos y en el interior un perfil de ferrita y perlita; la ferrita forma una red alrededor y en los límites de grano de la perlita, asociado a la diferencia de temperaturas en ambas zonas.
En el cordón exterior y en el interior existe la presencia de grieta, provocado por las condiciones de transferencia de calor y desplazamiento de material en el momento que el metal alcanza la máxima temperatura desde 1 350°C - 1400 °C y los bordes de la placa son recalcados uno contra otro.
En las zonas de la unión soldada la dureza varía entre 243 HV y 253 HV, no obstante, con estos valores en las zonas de la soldadura, en el tubo de acero galvanizado no debía existir la presencia de grietas.