Introducción
Una de las causas principales que inutiliza las transmisiones por engranajes son los daños causados por la picadura de flancos activos de los dientes [1, 2] y debido a esto las principales normas para evaluar la capacidad de carga de engranajes cilíndricos, como AGMA 2101, ISO 6336-2 y DIN 3990-2, consideran en primera instancia la necesaria resistencia al deterioro por picadura de los dientes en ruedas de transmisiones por engranajes.
En los engranajes cilíndricos el deterioro por picadura de los flancos activos es típico de ruedas dentadas en baño de aceite y ocurre por el contacto intermitente de los dientes durante el engrane. La picadura a largo plazo puede causar grietas de fatiga superficial que generan el desprendimiento de fragmentos de material en los dientes que alteran el perfil del diente y en dependencia de la velocidad de trabajo aumentan las cargas dinámicas en el contacto entre dientes [3]. En la etapa final, el proceso de picadura superficial se intensifica provocando un deterioro progresivo y un debilitamiento del diente que puede ser la causa raíz de una evidencia de fractura en el diente.
En el año 2016, la norma ANSI-AGMA 2101-D04: Fundamental rating factors and calculation methods for involute spur and helical gear teeth reformuló la evaluación del esfuerzo de contacto en los engranajes. Algunos populares programas de computación aplicables a elementos de máquinas, como Inventor 2021 y KISSsoft, incorporaron cálculos de resistencia a picadura y fractura en engranajes según la mencionada norma, pero aun el diseño óptimo basado en ANSI-AGMA 2101-D04 no tiene presencia en calculadores de engranajes ni en la literatura especializada.
Investigaciones dirigidas a la optimización de los engranajes cilíndricos con elevada resistencia a la picadura muestran que son diferentes las vías de abordar este problema. Por ejemplo, Zheng [4] y Zhou [5] orientan el incremento de la resistencia a la picadura con mejoras en la herramienta de generación empleada en el tallado de los dientes. Por otro lado, Croccolo [6] y Sagralo [7] desarrollan mejoras en las condiciones de lubricación para aumentar la resistencia de los flancos de los dientes a la picadura. También son encontradas soluciones basadas en la optimización de la geometría de los engranajes como son los resultados de Langlois [8] con perfiles asimétricos, los desarrollos de nuevos engranajes de Azemi [9] con aplicación de técnicas CAD/CAE y con técnicas de optimización como las publicadas por el francés Mahiddini [10] que le permitieron aumentar la capacidad de resistencia a picadura de los engranajes mejorando la rigidez de unidades de ruedas cilíndricas engranadas.
La introducción de poderosos medios de cómputos con elevadas velocidades de cálculo ha permitido el empleo del método de búsqueda exhaustiva en el diseño óptimo de engranajes [11, 12]. Este método, basado en algoritmos de búsqueda exhaustiva, localiza los extremos de una función objetivo mediante una organizada evaluación de la función objetivo que permite retener en cada paso el valor extremo de la función a optimizar.
En este trabajo, se presenta un procedimiento para el cálculo de la síntesis geométrica de engranajes cilíndricos de acero con dientes rectos mediante una organizada evaluación de la función objetivo, orientada a maximizar el momento torsor aplicable al piñón con resistencia a picadura según ANSI-AGMA 2101-D04. El procedimiento permitió generar síntesis geométricas racionales de engranajes con menor esfuerzo de contacto en los dientes conjugados y establecer recomendaciones para aumentar los radios de curvatura de los flancos de los dientes que mejoran la resistencia a la picadura de los engranajes analizados.
Métodos y Materiales
Las formulaciones de la norma ANSI-AGMA 2101-D04 sirvieron como base para establecer la función objetivo (1) orientada a optimizar el momento torsor aplicable al piñón (Mt1).
Para la ejecución del procedimiento de síntesis geométrica racional de un engranaje cilíndrico de dientes rectos con contacto exterior y elevada resistencia a la picadura de los dientes fueron determinadas las variables a considerar como conocidas (ver tabla 1) y desconocidas (ver tabla 2).
Tabla 1 Variables conocidas (datos) para solución del problema de la síntesis geométrica de engranajes cilíndricos de acero con dientes rectos. Fuente: autores
No. | Variables | Unidad | Descripción: |
---|---|---|---|
1 | u | Razón de engrane | |
2 | z1 | Cantidad de dientes en el piñón | |
3 | aw | mm | Distancia entre ejes de las ruedas |
4 | m | mm | Módulo |
5 | b | mm | Ancho de engranaje |
6 | ( (alfa) | ( | Ángulo del perfil de cremallera de referencia |
7 | ha* | Factor de altura de la cabeza del diente | |
8 | c* | Factor de holgura radial | |
9 | x1 | Coeficiente de corrección en dientes del piñón | |
10 | n1 | min-1 | Revoluciones por minuto del piñón |
11 | E1 | MPa | Módulo de elasticidad del material del piñón |
12 | (1 (miu1) | Coeficiente de Poisson del material del piñón | |
13 | E2 | MPa | Módulo de elasticidad del material de la rueda |
14 | (2 (miu1) | Coeficiente de Poisson del material de la rueda | |
15 | (H (sigmaH). | MPa | Esfuerzo máximo de contacto nominal |
16 | Propiedad no uniforme del material | Propiedades no uniformes del material. | |
17 | Condición de superficie | Condiciones de la superficie de contacto en los dientes | |
18 | Máquina movida y motriz | Régimen de máquina movida y motriz | |
19 | Modificar generatriz flanco del diente | Corrección en la generatriz del flanco de los dientes | |
20 | Calidad del montaje | Calidad del ajuste en el montaje de las ruedas | |
21 | s/s1 | Relación geométrica en el montaje | |
22 | QISO | Grado de precisión del engranaje | |
23 | Ama | Coeficiente A para calcular KHma | |
24 | Bma | Coeficiente B para calcular KHma | |
25 | Cma | Coeficiente C para calcular KHma |
Tabla 2 Variables desconocidas para solución del problema de síntesis geométrica de engranajes cilíndricos de acero con dientes rectos. Fuente: autores
No. | Variables | Unidad | Descripción: |
---|---|---|---|
1 | z2 | Cantidad de dientes en la rueda | |
2 | dw1 | mm | Diámetro primitivo del piñón |
3 | db1 | mm | Diámetro básico del piñón |
4 | da1 | mm | Diámetro de cresta del piñón |
5 | df2 | mm | Diámetro de fondo de la rueda |
6 | x2 | Coeficiente de corrección en la rueda | |
7 | x( (xsuma) | Corrección sumaria | |
8 | (w (alfaw) | ( | Ángulo de engranaje en plano transversal |
9 | (1 (ro1) | mm | Radio del flanco de contacto en diente del piñón |
10 | (2 (ro2) | mm | Radio del flanco de contacto en diente de la rueda |
11 | Mt1 | Nmm | Momento torsor aplicable al piñón |
12 | ZE | MPa1/2 | Factor de elasticidad |
13 | v | m/s | Velocidad tangencial en las ruedas |
14 | KV | Factor por carga dinámica. | |
15 | KH | Factor por carga concentrada en flanco del diente | |
16 | ZI | Factor geométrico de resistencia a la picadura. | |
17 | B | Factor auxiliar de cálculo del KV. | |
18 | C | Factor auxiliar de cálculo del KV. | |
19 | KHpf | Factor por ancho relativo del piñón | |
20 | KHma | Factor por calidad de la manufactura | |
21 | KHpm | Factor por ubicación del piñón | |
22 | KHmc | Factor por modificación del flanco de diente | |
23 | KHe | Factor por calidad del ajuste del montaje. | |
24 | KO | Factor por aplicación de carga | |
25 | KS | Factor por tamaño. | |
26 | ZR | Factor por rugosidad. |
En la solución de la síntesis racional geométrica del engranaje fueron consideradas las siguientes condiciones:
Engranaje cilíndrico de acero con calidad comercial.
Tratamiento térmico de normalizado con dureza volumétrica de 142 HB.
Condiciones de trabajo estable y sin perturbaciones en la maquina movida y motriz (ko = 1).
Tiempo de trabajo topado a no más de 8 horas diarias.
Ubicación de las ruedas con disposición simétrica a los rodamientos (s1/s = 0)
Engranaje protegido del ambiente por una carcasa cerrada (engranaje cerrado).
Engranajes lubricados por inmersión en baño de aceite.
Dientes sin modificación en los flancos (KHmc = 1 sin abarrilamiento central).
Engranaje de calidad comercial con grado 7mo de precisión ISO.
Condiciones medias de rugosidad en los flancos (ZR = 1).
Ruedas con asentamiento previo durante el montaje (KHe = 0.8).
Ruedas dentadas elaboradas por generación con parámetros de herramienta de corte y módulo normalizados según ISO.
En casos donde la aplicación del procedimiento para obtener la síntesis racional geométrica de un engranaje cilíndrico de acero de dientes rectos con ejes paralelos y contacto exterior difiera de las declaradas anteriormente pueden ser empleadas las orientaciones brindadas en ANSI-AGMA 2101-D04 (reafirmada en marzo 16, 2016).
A continuación, las figuras 1, 2 y 3 muestran el procedimiento de cálculo generado en el presente trabajo para la solución del problema asociado con la síntesis geométrica racional de un engranaje cilíndrico de dientes rectos con contacto exterior y elevada resistencia a la picadura de los dientes de las ruedas.
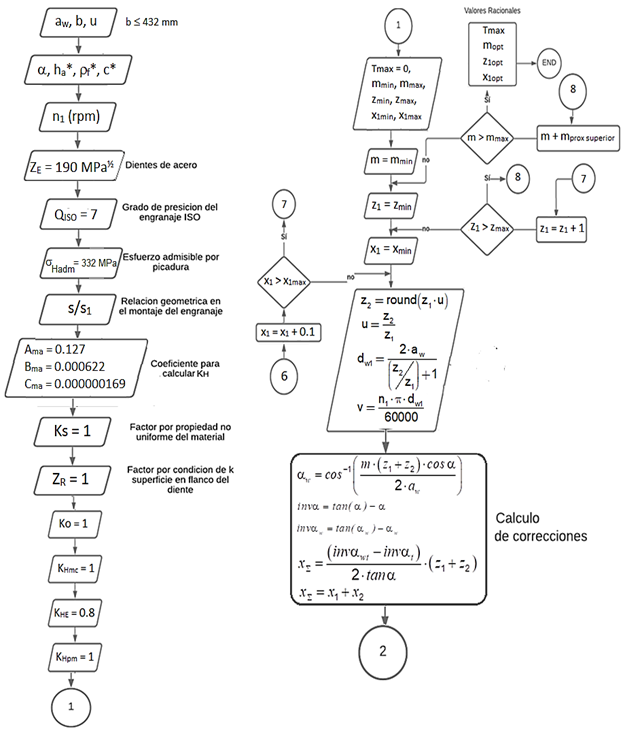
Fig. 1 Primera etapa del procedimiento de cálculo correspondiente a la generación de las variables básicas (modulo, cantidad de dientes en las ruedas y coeficientes de corrección).
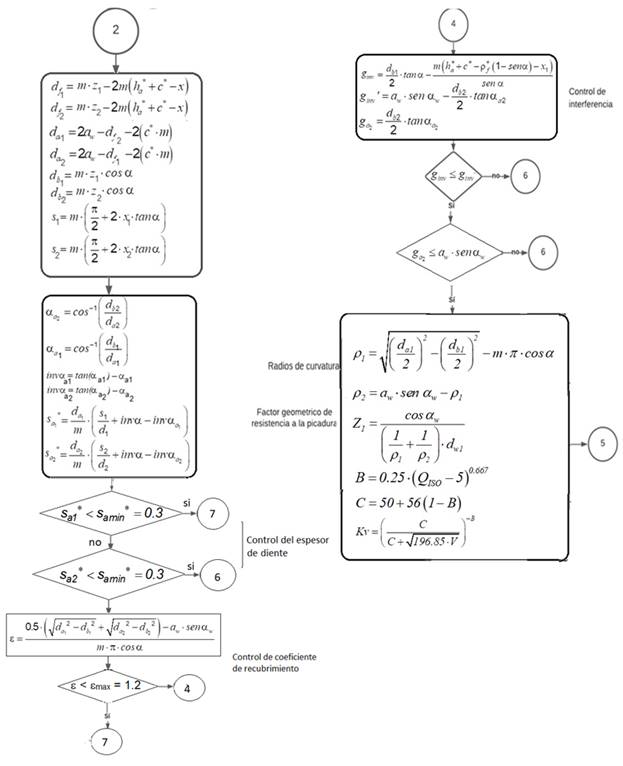
Fig. 2 Segunda etapa del procedimiento de cálculo correspondiente al completamiento de la geometría de las ruedas y exclusiones de las geometrías inadmisibles según espesor del diente, coeficiente de corrección e interferencia de los dientes.
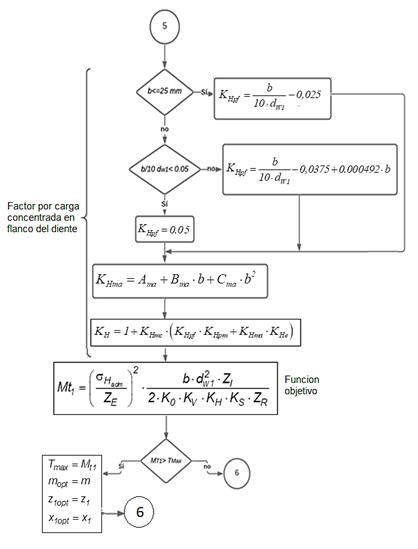
Fig. 3 Tercera y última etapa del procedimiento de cálculo correspondiente al cálculo del momento torsor aplicable en el piñón por resistencia a la picadura y retención de los valores óptimos que maximizan la función objetivo (engranaje con síntesis racional).
El importante destacar que el procedimiento de cálculo presentado en este trabajo es aplicable para engranajes cilíndricos con dientes rectos de acero, flancos perfilados con curvas de evolventes generadas mediante tallado con fresa madre, ancho de engranaje menor de 432 mm (17 pulgadas) y suficiente resistencia a la fractura de los dientes.
Resultados y Discusión
En base al procedimiento desarrollado fue elaborado un procedimiento en Excel que permitió evaluar la influencia de la geometría del engranaje en el momento máximo permisible en el piñón por resistencia a picadura.
Las soluciones para engranajes con coeficientes de corrección diferentes a cero (x 1 ( 0 y x 2 ( 0) fueron tipificadas con distancias entre ejes (a w ) de 60, 70, 80, 90, 100, 125, 160, 200, 250, 315, 400 y 500 mm, razones de engrane (u) de 1, 2 y 4, con módulos (m) de 1; 1,25; 1,5; 2; 2,5; 3; 4; 5; 6; 8; 10; 12; 16; 20; 25; 32; 40 y 50 mm y ancho relativo a la distancia entre ejes de ruedas de ( BA = 0,4; con posibilidad de aplicar valores de coeficientes de corrección en piñón (x 1 ) entre 0 y 2 con incrementos de 0.1.
Las soluciones para engranajes cilíndricos de acero con dientes rectos, ejes paralelos y contacto exterior fueron aceptadas con distancias entre ejes y razones de engrane exactas. También fue considerado el cumplimiento de los siguientes índices de calidad geométrica:
El espesor de cresta del diente es mayor que el 30% del módulo (sa ( 0.3 m).
El coeficiente de recubrimiento es igual o mayor a 1.2 (( ( 1.2).
No debe ocurrir interferencia en el contacto entre los dientes.
La tabla 3 muestra parámetros geométricos de engranajes cilíndricos de dientes rectos con ejes paralelos y contacto exterior en casos de engranajes con coeficientes de corrección diferentes a cero para el piñón y la rueda.
Tabla 3 Soluciones de máxima capacidad de carga para engranajes cilíndricos de acero de dientes rectos con corrección del perfil en flancos de evolvente. Fuentes: autores
Solución | aw (mm) | b (mm) | u | m | z1 | x1 | x( | sa1 (mm) | ( | (1 (mm) | (2 (mm) | (red (mm) | Mt1 (Nm) |
1 | 60 | 24 | 1 | 2,5 | 23 | 1,2 | 1,144 | 0,33 | 1,23 | 13,08 | 13,00 | 6,5 | 10,5 |
2 | 2 | 1,25 | 31 | 1,5 | 1,565 | 0,33 | 1,24 | 9,18 | 15,7 | 5,8 | 6,3 | ||
3 | 4 | 1 | 24 | 0,9 | 0 | 0,32 | 1,46 | 5,17 | 15,3 | 3,9 | 2,6 | ||
4 | 70 | 28 | 1 | 2,5 | 27 | 1,1 | 1,125 | 0,43 | 1,3 | 14,78 | 14,83 | 7,4 | 16,2 |
5 | 2 | 1,5 | 30 | 1,5 | 1,874 | 0,38 | 1,21 | 10,60 | 19,01 | 6,8 | 10,0 | ||
6 | 4 | 1,25 | 22 | 1 | 1,064 | 0,31 | 1,35 | 6,03 | 20,92 | 4,7 | 4,1 | ||
7 | 80 | 32 | 1 | 4 | 19 | 0,7 | 0,747 | 0,58 | 1,20 | 14,10 | 21,95 | 8,6 | 23,9 |
8 | 2 | 2 | 26 | 1,2 | 1,089 | 0,31 | 1,31 | 11,88 | 20,17 | 7,5 | 14,3 | ||
9 | 4 | 1,25 | 25 | 1,2 | 1,626 | 0,34 | 1,28 | 7,09 | 24,7 | 5,5 | 6,2 | ||
10 | 90 | 36 | 1 | 2 | 43 | 1,6 | 2,305 | 0,61 | 1,20 | 19,24 | 20,38 | 9,9 | 34,8 |
11 | 2 | 2 | 29 | 1,5 | 1,675 | 0,31 | 1,22 | 13,83 | 23,8 | 8,7 | 20,9 | ||
12 | 4 | 1 | 35 | 1,6 | 2,746 | 0,45 | 1,21 | 8,17 | 28,4 | 6,3 | 9,0 | ||
13 | 100 | 40 | 1 | 2 | 48 | 1,7 | 2,277 | 0,58 | 1,24 | 21,63 | 21,52 | 10,8 | 46,7 |
14 | 2 | 1,5 | 43 | 1,7 | 2,514 | 0,5 | 1,24 | 14,87 | 26,77 | 9,6 | 28,0 | ||
15 | 4 | 1 | 39 | 1,8 | 2,723 | 0,37 | 1,20 | 9,36 | 30,71 | 7,2 | 12,5 | ||
16 | 125 | 50 | 1 | 3 | 40 | 1,5 | 1,898 | 0,54 | 1,25 | 26,98 | 26,96 | 13,5 | 89,5 |
17 | 2 | 3 | 27 | 1,3 | 1,283 | 0,31 | 1,28 | 18,81 | 32,08 | 11,8 | 53,6 | ||
18 | 4 | 1,25 | 39 | 1,8 | 2,723 | 0,37 | 1,20 | 11,70 | 38,39 | 9,0 | 24,0 | ||
19 | 160 | 64 | 1 | 3 | 51 | 1,4 | 2,684 | 0,80 | 1,20 | 31,92 | 38,29 | 17,4 | 184,2 |
20 | 2 | 2 | 52 | 1,9 | 2,178 | 0,42 | 1,30 | 24,3 | 39,82 | 15,1 | 109,7 | ||
21 | 4 | 1,5 | 42 | 1,6 | 1,761 | 0,34 | 1,34 | 14,73 | 46,06 | 11,2 | 48,5 | ||
22 | 200 | 80 | 1 | 6 | 32 | 1,3 | 1,518 | 0,48 | 1,26 | 42,92 | 43,39 | 21,6 | 349,1 |
23 | 2 | 3 | 43 | 1,7 | 2,414 | 0,5 | 1,24 | 29,74 | 53,55 | 19,1 | 210,5 | ||
24 | 4 | 2 | 39 | 1,8 | 2,723 | 0,37 | 1,20 | 18,72 | 61,42 | 14,4 | 94,5 | ||
25 | 250 | 100 | 1 | 6 | 40 | 1,5 | 1,898 | 0,54 | 1,25 | 53,96 | 53,92 | 27,0 | 662,0 |
26 | 2 | 6 | 27 | 1,3 | 1,282 | 0,31 | 1,28 | 37,62 | 64,15 | 23,7 | 398,6 | ||
27 | 4 | 2,5 | 39 | 1,8 | 2,723 | 0,37 | 1,20 | 23,40 | 76,78 | 17,9 | 179,9 | ||
28 | 315 | 126 | 1 | 10 | 30 | 1,2 | 1,744 | 0,58 | 1,20 | 64,73 | 75,82 | 34,9 | 1302,3 |
29 | 2 | 6 | 34 | 1,6 | 1,652 | 0,31 | 1,25 | 48,84 | 79,77 | 30,7 | 781,0 | ||
30 | 4 | 3 | 41 | 1,8 | 2,713 | 0,39 | 1,22 | 29,32 | 96,10 | 22,5 | 347,3 | ||
31 | 400 | 160 | 1 | 12 | 32 | 1,3 | 1,518 | 0,48 | 1,26 | 85,83 | 86,77 | 43,1 | 2503,7 |
32 | 2 | 6 | 43 | 1,7 | 2,414 | 0,50 | 1,24 | 59,49 | 107,1 | 38,2 | 1519,0 | ||
33 | 4 | 4 | 39 | 1,8 | 2,723 | 0,37 | 1,20 | 37,45 | 122,8 | 28,7 | 687,7 | ||
34 | 500 | 200 | 1 | 12 | 40 | 1,5 | 1,898 | 0,54 | 1,25 | 107,9 | 107,8 | 53,9 | 4660,0 |
35 | 2 | 12 | 27 | 1,3 | 1,283 | 0,30 | 1,28 | 75,25 | 128,3 | 47,4 | 2824,6 | ||
36 | 4 | 5 | 39 | 1,8 | 2,723 | 0,37 | 1,20 | 46,81 | 153,6 | 35,9 | 1287,1 |
Las soluciones de síntesis racional para máxima resistencia a picadura fueron limitadas por las condiciones de bajo coeficiente de recubrimiento, dientes puntiagudos e interferencia en el contacto. Los resultados mostrados en la tabla 4 indican que los valores de torque máximos admisibles en el piñón dependen mayormente del valor límite elegido para el espesor de cresta de los dientes y del coeficiente de recubrimiento. Es decir, pueden ser obtenidas síntesis geométricas de engranajes con mayor capacidad de resistencia, pero deben aceptarse valores más bajos de los límites del espesor de cresta y coeficiente de recubrimiento que los declarados para la aplicación del procedimiento presentado en este trabajo.
Tabla 4 Motivos que limitaron el valor máximo del momento torsor en el piñón. Fuente: autores
Motivo del valor límite del MT1 | Cantidad (%) |
---|---|
Bajo coeficiente de recubrimiento (( < 1,2) | 13 (36 %) |
Aguzado del diente del piñón (sa1 < 0,3) | 11 (31 %) |
Interferencia | 5 (14 %) |
Máximo momento Mt1 | 7 (19 %) |
En general, se observa que la geometría racional con mayor radio de curvatura mejora la resistencia a la picadura de los flancos activos de los engranajes, hecho explicable por la relación directa entre el máximo momento Mt1 en el piñón por resistencia a picadura y el radio de curvatura equivalente (red de los flancos de dientes en contacto. Las ecuaciones (2) y (3) muestran la referida relación.
La figura 4 muestra el antes referido comportamiento del máximo momento torsor en el piñón Mt1 con dependencia del radio de curvatura equivalente ( red de los flancos activos de los dientes en contacto para engranajes con razones de engranaje u de 2 y 4, según la geometría reportada en la tabla 3. En general para engranajes con distancia entre ejes de ruedas mayores a 125 mm, las soluciones con mayores módulos y distancias interaxial favorecen el incremento de la resistencia del engranaje a la picadura de sus dientes. Este resultado es obvio, pues el aumento de las dimensiones de las ruedas favorece un aumento de los radios de curvatura en los flancos de evolvente de los dientes.
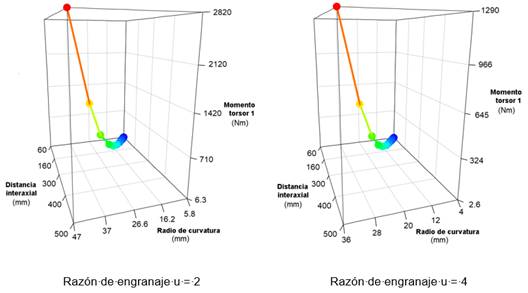
Fig. 4 Relación entre el máximo momento torsor en el piñón Mt1, la distancia interaxial del engranaje aw y el radio de curvatura equivalente ((red) de los flancos activos de los dientes en contacto.
Por otra parte, mayores módulos y cantidades de dientes en el piñón alrededor del promedio de las soluciones racionales, figura 5, aumentan los diámetros básicos de las ruedas y la curvatura de los flancos en los dientes del piñón. Todo esto, se favorece con la aplicación de coeficientes de corrección positiva en el piñón (x1 ( 0) que permiten obtener flancos de dientes con amplias curvas de evolvente y radios de curvatura mayores.
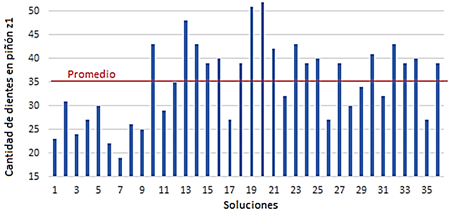
Fig. 5 Cantidades de dientes en piñón con síntesis geométrica racional para resistencia a picadura.
Observando soluciones de síntesis racional para un engranaje con valores establecidos de distancia interaxial, ancho de engrane y razón de engranaje, puede afirmarse que aumentos progresivos del módulo con combinaciones adecuadas de numero de dientes y coeficientes de corrección generan geometrías internas mejoradas para el engranaje. La figura 6 muestra esta tendencia.
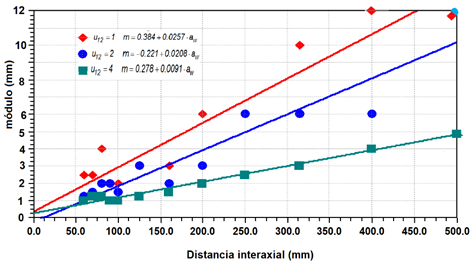
Fig. 6 Comportamiento del aumento del módulo y la distancia interaxial en las soluciones de geometría racional para engranajes cilíndricos de dientes rectos de acero con coeficientes de corrección.
La tabla 5 muestra soluciones geométricas para un engranaje con distancia interaxial de 315 mm, ancho de 126 mm y razón de engranaje de 2. En este caso la mejor solución corresponde a m = 6 y fue limitada por aguzado de los dientes del piñón. En general, la solución racional para engranajes con corrección ocurre con coeficientes de corrección que generan ángulos de engranaje alrededor de 24º.
Tabla 5 Soluciones racionales para un engranaje con corrección, distancia interaxial de 315 mm, ancho de 126 mm y razón de engranaje de 2. Fuente: autores
m (mm) | z1 | x1 | (w (() | ( | (1 (mm) | (2 (mm) | (red (mm) | Mt1 (Nm) | Limite |
---|---|---|---|---|---|---|---|---|---|
1 | 206 | 2,6 | 22,81 | 1,35 | 40,7 | 81,4 | 27,1 | 706,6 | Interferencia |
1,25 | 165 | 2,4 | 22,64 | 1,43 | 41,7 | 79,6 | 27,4 | 713,2 | Interferencia |
1,5 | 137 | 2,3 | 23,14 | 1,36 | 42,1 | 81,7 | 27,8 | 721,5 | Interferencia |
2 | 102 | 2,2 | 24,10 | 1,23 | 42,7 | 85,9 | 28,5 | 735,7 | Interferencia |
2,5 | 82 | 2 | 23,46 | 1,35 | 44,4 | 81,0 | 28,7 | 743,1 | Interferencia |
3 | 68 | 1,9 | 24,10 | 1,29 | 44,7 | 83,9 | 29,2 | 751,7 | Interferencia |
4 | 51 | 1,8 | 24,10 | 1,28 | 46,7 | 81,9 | 29,7 | 766,7 | Interferencia |
5 | 41 | 1,3 | 23,50 | 1,30 | 48,7 | 76,7 | 29,8 | 771,9 | Aguzado |
6 | 34 | 1,6 | 24,10 | 1,25 | 48,8 | 79,8 | 30,3 | 781,0 | Aguzado |
8 | 26 | 1,0 | 21,45 | 1,43 | 45,8 | 69,4 | 27,6 | 725,4 | Aguzado |
10 | 21 | 0,8 | 20,00 | 1,46 | 43,9 | 63,8 | 26,01 | 690,4 | Aguzado |
12 | 17 | 0,8 | 24,10 | 1,30 | 41,2 | 87,5 | 28,00 | 721,5 | Aguzado |
La figura 7 muestra los esfuerzos de contacto en engranajes con geometría reportada en la tabla 5 y corrobora que el menor esfuerzo de contacto y por consiguiente la mayor resistencia a la picadura se observa en el engranaje con módulo 6, que es también el engranaje con máximo torque (MT1 = 781 Nm) aplicable en el piñón observable en la tabla 5 por la condición de máxima resistencia a la picadura.
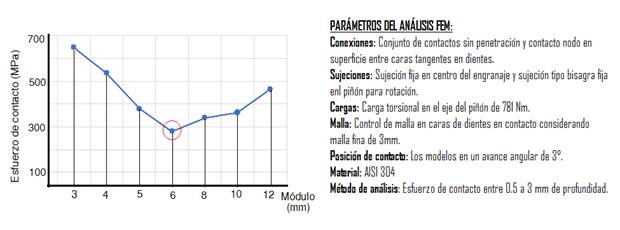
Fig. 7 Esfuerzos de contacto obtenidos con MEF en engranajes con geometría reportada en tabla 5 y momento torsor aplicado en el piñón de Mt1 = 781 Nm.
En general, los resultados de la síntesis geométrica racional derivados del procedimiento presentado fueron validados mediante modelos de elementos finitos (MEF). Las ruedas dentadas engranadas y modeladas mediante MEF con mayor capacidad de resistencia a la picadura (menor esfuerzo de contacto) reportaron coincidencia con la geometría de los engranajes con síntesis geométrica racional.
Finalmente, pudo ser corroborado que soluciones racionales de engranajes con aplicación de coeficientes de corrección mejoran alrededor del 26 % su resistencia a la picadura con relación a engranajes normales. La tabla 6 muestra los aumentos en resistencia a la picadura para engranajes con coeficientes de corrección positivos. Estos resultados, corroboran lo declarado por Niemann [13] para engranajes con 18 y 54 dientes que reportaron 30% de incremento de la resistencia a la picadura con respecto a engranajes normales.
Tabla 6 Momento máximo en piñón para engranajes normales x1=x2=0 y con corrección x1 ( 0. Fuente: autores
aw (mm) | b (mm) | u | Mt1 (Nm) con x1 = x2 = 0 | Mt1 (Nm) con x1 ( 0 | % de incremento de resistencia a picadura aplicando coeficientes de corrección, |
---|---|---|---|---|---|
60 | 24 | 1 | 8,6 | 10,5 | 22,1 |
2 | 5,0 | 6,3 | 26,0 | ||
4 | 1,9 | 2,6 | 36,8 | ||
70 | 28 | 1 | 14,5 | 16,2 | 11,7 |
4 | 3,1 | 4,1 | 32,3 | ||
80 | 32 | 1 | 20,0 | 23,9 | 19,5 |
4 | 4,7 | 6,2 | 31,9 | ||
90 | 36 | 1 | 28,3 | 34,8 | 23,0 |
2 | 16,6 | 20,9 | 25,9 | ||
4 | 6,8 | 9,0 | 32,4 | ||
100 | 40 | 1 | 38,5 | 46,7 | 21,3 |
4 | 9,3 | 12,5 | 34,4 | ||
125 | 50 | 1 | 73,9 | 89,5 | 21,1 |
4 | 18,2 | 24,0 | 31,9 | ||
160 | 64 | 1 | 151,4 | 184,2 | 21,7 |
4 | 37,9 | 48,5 | 28,0 | ||
200 | 80 | 1 | 288,3 | 349,1 | 21,1 |
4 | 72,9 | 94,5 | 29,6 | ||
250 | 100 | 1 | 546,6 | 662,0 | 21,1 |
4 | 139,4 | 179,9 | 29,1 | ||
315 | 126 | 1 | 1054,8 | 1302,3 | 23,5 |
2 | 634,2 | 781,0 | 23,1 | ||
4 | 271,3 | 347,3 | 28,0 | ||
400 | 160 | 1 | 2067,2 | 2503,7 | 21,1 |
4 | 535,7 | 687,7 | 28,4 | ||
500 | 200 | 1 | 3847,6 | 4660,0 | 21,1 |
4 | 1004,0 | 1287,1 | 28,2 |
Conclusiones
Fue desarrollado un procedimiento de cálculo para la solución del problema asociado con la síntesis geométrica racional de un engranaje cilíndrico de dientes rectos con contacto exterior y elevada resistencia a la picadura de los dientes de las ruedas. Fue observado que la geometría racional con mayor radio de curvatura mejora la resistencia a la picadura de los flancos activos de los engranajes. Para engranajes con distancias interaxiales definidas fueron reportados aumentos en la resistencia a la picadura en síntesis geométricas con una cantidad de dientes en el piñón alrededor de 35 y ángulos de engranaje de 24(.