INTRODUCTION
Alcohol as a by-product of sugar cane production, is one of the most important derivative industry in Cuba. Productions are destined to satisfy internal needs of domestic fuel, pharmaceutical, food and cosmetic industries, liquor store and for exportation (de Armas et al, 2019).
Currently, alcohol demand is higher than the production possibilities in country's distilleries. The main raw material used, final sugarcane molasse, is increasingly valued due to biotechnological productions growth. For this reason, it is necessary to achieve greater energy or process efficiency in existing processes. So, it is necessary to reduce the consumption rates of both raw materials and utilities. This would lead to increasing production profitability and achieving greater possibilities of satisfying this product growing demand.
In this sense, alcohol production in two Cuban distilleries is studied, in such a way that better productive indicators are achieved. Distillery A is one of them, being designed to produce extrafine alcohol (AEF), rectified ethyl alcohol (AER) and schnapps (Díaz, 2020). The installed distillation system is composed by two columns to obtain rectified ethyl alcohol, three columns to obtain extrafine alcohol and one to obtain recovered alcohol (Díaz, 2020).
Distillery B technology, places it among the most advanced and is characterized by its high-quality productions and process energy efficiency. Its main product is extrafine alcohol, in addition distillery produces bad taste alcohols and recovers fermentation CO2 (López, 2013); (Díaz, 2015). Installed distillation system to obtain extrafine alcohol consists of only five columns: distiller, preconcentrator, hydroselector, rectifier and demethilyzer (Albernas et al., 2012); (González et al., 2016).
The identification of Distillery A technological limitations shows the need to evaluate more efficient technological schemes to achieve required quality standards and reduce energy consumption. So, the objective is to analyze extrafine alcohol distilleries A and B technologies to propose modifications to less efficient technology based on the one with the best performance.
MATERIALS AND METHODS
2.1 Characterization of extra-fine alcohol process in studied distilleries
2.1.1 Characterization of extra-fine alcohol process in distillery A
Ethanol production process includes three stages: wort preparation, fermentation and distillation-rectification (Albernas-Carvajal et al., 2014); (de Armas, 2019), (de Armas et al, 2019). In Distillery A, plant molasse at 85 °Brix is mixed with previously treated water to make initial predilution. pH is adjusted with sulfuric acid to desired value for yeast growth in mother tanks (between 3.9 and 4). A part of this wort is diluted at 16 °Brix to send it to mother tanks, while the rest is prepared at 20 °Brix and fed to fermenters, where fermented wine is obtained and fed to distillation stage (de Armas, 2019).
In distillation section, ethanol is purified until obtaining a concentration between 94 and 95 ° GL (Klein et al., 2019). The fermented batter is fed to distillation column where alcoholic vapors from the top, pass to rectifier column and vinasses are obtained at the bottom. Vinasses constitute the main process residual and are used for biogas production. In rectifier column heads and 94.5 °GL rectified ethyl alcohol are separated.
Approximately 51.2% of rectified ethyl alcohol is stored and the rest is used for its concentration to extra-fine alcohol (González et al., 2016); (Díaz, 2020). In this case, it is fed to washing column, where it is into contact with water to reduce its alcoholic concentration and facilitate the extraction of high molar mass impurities, known as amyl alcohols or fusel oil. Washed alcohol passes to second rectifier column to raise its concentration to extrafine alcohol with 96.3° GL, separating amyl alcohols that are sent to recovery column. The last stage is methyl elimination to finally obtain extrafine alcohol (González et al., 2016).
In order to increase its alcoholic concentration, the recovery column is fed with washing, final rectificating and demethylizing columns head products and the extractions carried out in final rectificating column. Depending on obtained alcohol quality, its destination is decided, as rectified ethyl alcohol or for recovered ethyl alcohol (phlegm alcohol) production.
Each of the columns in installed distillation scheme has its own condensation system with two condensers, except distillation column. All condensers use water as a cooling medium, in addition, each column consumes steam generated by the boiler, except rectifier.
2.1.2 Characterization for obtaining extrafine alcohol process in distillery B
In distillery B the process of obtaining extra-fine alcohol is carried out in the same way, but with some differences. The technology installed in this industry is designed to produce extra-fine alcohol through a distillation scheme composed of only five columns: distiller, preconcentrator, hydroselector, rectifier, and demethylizer (Albernas et al., 2012), condensing system has two condensers in each column, except in the distiller. The difference is that the main condensers of the hydroselector and rectifier columns are in turn demethylizer and distillation columns boilers, as is shown in Figure 1. In this way, the process is integrated energetically, and steam consumption from the boiler is saved, as well as the amount of cooling water necessary to condense alcoholic vapors Albernas et al., 2012).
2.2 Material and energy balances in each process
Material and energy balances were carried out at each stage for the produced wine volume (Albernas et al., 2012). A summary used equations is shown in Table 1.
Table 1 General equations used in material and energy balances
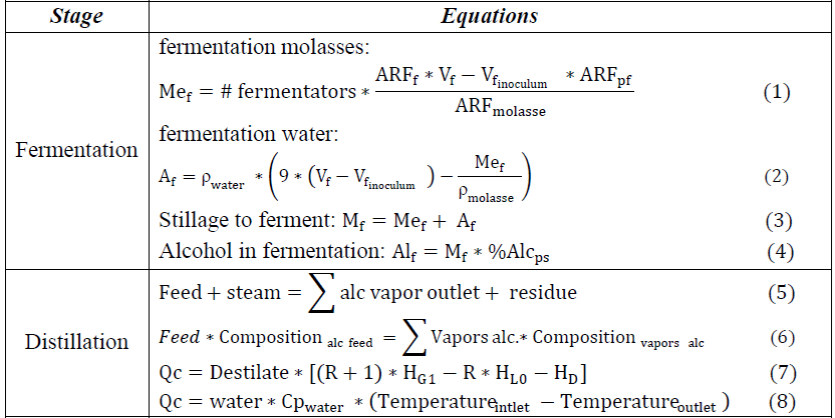
ARF f: ARF in fermentation, Vf: volume of fermentation, Vf inoculum: volume of inoculum, ARFpf: ARF in prefermentation, % Alcps: % alcoholic in seed, JF: filter juice, MeJF: molasse when using filters juice, vapors Alc outlet: alcoholic outlet vapors, Composition Alc or alc vapors: composition of alcohol in feed or in alcoholic vapors, Qc: heat evacuated by the condenser (Ec 9.54, Treybal, 1991).
From mass and energy balances in columns and primary condensers of Distillery A, the outlet currents that can generate the necessary steam in a certain column to carry out its operation are identified. To do this, the amount of water that would be used when combining the alcoholic vapors condensation - boiling with steam generation is calculated (Equation 9):
RESULTS AND DISCUSSION
3.1 Material and energy balances results
Obtained results characterize and identify productions in both distilleries. They are differentiated by the number of final products considered in them, as well as by technological system that they have installed to develop the productions. A summary of the main streams involved in the process is shown in Table 2.
Table 2 Main streams in both distillers
Molasses in fermentation (kg/d) | 187 709 | 342 000 |
Water in fermentation (kg/d) | 770 562 | 1 005 949 |
Stillage (kg/h) | 37 275 | 62 402 |
Vinasse residual (kg/h) | 45 888 | 65 595 |
Rectify alcohol (hL/d) | 1 224 | - |
Superfine alcohol (hL/d) | 500 | 900 |
Total Steam (kg/h) | 19 505 | 6 631 |
Total cooling water (m3/h) | 303.1 | 314.1 |
3.1.1 Steam and cooling water consumption index.
The steam consumption index was calculated from the generated by the boiler steam required by each column, in relation to the amount of extra-fine alcohol produced. The obtained results are shown in Figure 2.
In both technologies, the carried-out calculations show that distillation column is the major steam consumer with an index of 0.256 t steam/hL alcohol in distillery A, and 0.26 t steam/hL alcohol in distillery B. This is due to its main function is to eliminate most of the water and to separate the alcoholic vapors at the column top. Although numerically there is no great difference in these columns steam consumption, in Distillery B the necessary steam is generated in a boiler and not by a steam generator as occurs in Distillery A.
In general, there is a notable difference in terms of total vapor rates of both technologies. Distillery A consumes 0.566 t steam/hL of alcohol, while distillery B only needs 0.172 t/hL from the steam generator, marking a difference of 0.394 t/hL. The results show how this latter distillery is more energy efficient than Distillery A in this regard. This is influenced by the two boilers present in Distillery B, one in distillation column, using the steam from the rectifier, and the other in demethylizer that operates with the steam from hydroselector column.
On the other hand, the cooling water consumption rates were determined in relation to the alcohol amount required in distillation stage in both distilleries. The obtained results appear in Figure 3.
From the obtained results, the total cooling water consumption rate in Distillery A is 13.34 m3 of water/hL of alcohol produced, being higher than that Distillery B which requires 6.98 m3 of water/hL of alcohol. This value is influenced by the presence of two boilers where the alcoholic vapors condense at the outlet of the abovementioned columns. However, in distillery A, each column has its own condensation system made up of two condensers and, therefore, requires more water (6.36 m3/hL) to condense the vapors from the top.
3.2. Proposals for technological changes
Because the explained above differences, changes in the technological system of Distillery A can be proposed, which improve consumption rates in it and, in turn, have a positive impact on total production costs. In this case, it is proposed to achieve a reduction in the steam generated by the boiler consumption and in cooling water in distillation. Using mass and energy balances, heat evacuated by the primary columns condensers is calculated, as well as the necessary steam to carry out the operation (Table 3).
Table 3 Energetic behavior in distillery A
Distillation | - | 13 046 |
Rectification | 84 719 | - |
Washing | 175 167.21 | 1 568 |
Final rectification | 309 428.83 | 4 234 |
Demethylation | 42 149.76 | 323.78 |
Recuperation | 49 196.74 | 333.05 |
Knowing these values, which outlet current in one column can generate the steam that is consumed in another, as well as the amount of needed water are determined. Observing the amount of necessary water to carry out the condensation - boiling (Figure 4), the required steam by distillation column and final rectifier cannot be generated by the evacuated heat in any of primary condensers. Likewise, the demanded steam in washing column can only be generated by the alcoholic vapors of final rectification column. Whereas, steam from the demethylizer and recuperator can be obtained by the alcoholic vapors heat from the rectifier, washer or final rectifier columns.
From these results, a possible distribution between columns can be selected, also considering the installed scheme in distillery B. It is proposed to generate steam in washing column with the condensation of alcoholic vapors from final rectifier. Steam in demethylizer can be generated with the vapors coming out from the washing column, and in recuperator would be obtained with the alcoholic vapors from the rectification column (Table 4).
Table 4 Columns selection for steam generation by condensation - boiling
|
||
---|---|---|
Washing | Final rectifier | 4.44 |
Demethylizer | Washing | 7.98 |
Recuperator | Rectifier | 2.15 |
Proposed distribution schema is showed in Figure 5.
The results have a significant impact on cooling water consumption of these columns in current operating conditions, and its decrease is summarized in Table 5.
Table 5 Decrease in cooling water consumption in distillery A
|
|
|
|
|
---|---|---|---|---|
Rectifier | 42.83 | 9.57 | 0.84 | 0.19 |
Washing | 80.39 | 14.88 | 3.86 | 0.71 |
Final rectifier | 134.30 | 9.09 | 6.45 | 0.44 |
These values indicate that approximately 178 m3/h of water is no longer consumed for cooling, decreasing from 13.34 m3/hL to 8.63 m3/hL of produced alcohol, which represents a reduction of 35.3%.
On the other hand, steam consumption also drops from 19.5 t / h to 17.28 t/h, for a ratio of 0.45 t steam/hL of alcohol, which represents a reduction of 18.9%. Boiler generated steam is consumed only by distillation and final rectifier columns. This index for alcohol production allows that the need for steam is in reported interval by Pérez et al., (2005).
CONCLUSIONS
Distillery A has a higher steam consumption rate (0.566 t/hL) compared whit Distillery B (0.172 t/hL), as well as a higher consumption of cooling water rate (13.34 m3 of water/hL), while in distillery B it is 6.98 m3 of water/hL.
Proposed redistribution scheme in Distillery A reduces cooling water consumption rate by 35.3%, reaching the value of 8.63 m3 water/hL of alcohol.
Proposed scheme reduces steam consumption by 18.9%, bringing it to 0.46 t/hL and consuming boiler generated steam only by distillation and final rectifier columns.