INTRODUCCIÓN
La energía, el agua y el medio ambiente tienen una relación indisoluble para cualquier proceso industrial. Por lo tanto, el agua no solo debe ser vista como elemento natural, en cuyo uso, tratamiento y distribución se consume gran cantidad de energía, sino como portador energético por excelencia desde la fase de vapor, entonces puede constituir un factor limitante en el desenvolvimiento económico de las actividades industriales (Aguilar-Ibarra y col., 2010). Algunos autores y sitios especializados que han sido consultados, reflejan que el 25% del agua es consumida en diferentes procesos industriales, que no sólo tienen un impacto marcado en el consumo de agua fresca, sino que, también contaminan severamente las diferentes fuentes de abasto con los vertimientos de sus residuales (Lobelles y col., 2016); (WWAP, 2019); (WWAP, 2020). Se conoce además que la generación de vapor, es de los procesos más consumidores de agua dentro de la refinación del petróleo (Álvarez, 2015). Entonces, la eficiencia del sistema para generarlo, la distribución adecuada y el control de su consumo, provocan un gran impacto en la eficiencia total de los complejos de refinación. En el caso de estudio, esta situación se refleja en los costos de producción del vapor, en el consumo de portadores energéticos y, en consecuencia, en la competitividad y sustentabilidad de la empresa.
En la economía energética juega un papel importante la caracterización de la situación actual en la generación, uso, economía e impacto ambiental del vapor de agua, y a la vez localizar pérdidas e ineficiencias de este sistema. Por lo que se justifican estudios que ofrezcan soluciones viables a las situaciones detectadas, para lograr que el sistema de generación de vapor de la refinería sea lo más racional posible. En este sentido, es objetivo del presente estudio evaluar una propuesta de mejora tecnológica en el sistema de generación de vapor en la Refinería Cienfuegos S.A, que permita una reducción de los costos de producción, de portadores energéticos y el impacto ambiental.
MATERIALES Y MÉTODOS
La metodología que se propone toma como base de referencia los aspectos teóricos acerca del desempeño de un proceso, así como, resultados de investigaciones precedentes (Sobrepera, 2007); (Benavides, 2010). Consta de tres etapas, cada una con un objetivo específico, sus pasos y las técnicas a utilizar para desarrollarla. Para obtener la información se aplican las técnicas referenciadas de modo simultáneo y/o combinado.
2.1 Etapa I. Identificación
En esta etapa se crea y capacita el equipo de trabajo. La capacitación está dirigida en lo fundamental a la aplicación correcta de las técnicas de búsqueda y análisis de información (Lobelles, 2012), así como el planteamiento de posibles soluciones. En esta investigación se utilizan las técnicas: Observación; Entrevista y la Tormenta o lluvias de ideas según método de Osborn (1963).
Para la revisión documental se da seguimiento al proceso tecnológico, con un análisis detallado de los datos de operación, los diagramas históricos del proceso y la base documental de estadísticas de la empresa.
2.2 Etapa II. Procesamiento y análisis de la información
Para el análisis de toda la información, de manera tal que se puedan detectar las causas que provocan el desvío de los indicadores del proceso, se proponen las siguientes herramientas generales (Sobrepera, 2007):
Análisis de Pareto: Esta herramienta permitirá conocer los mayores consumidores de vapor de agua, las mayores pérdidas o los mayores costos para este recurso.
Análisis de Causa - Efecto: Permite conocer todas las posibles causas y mediante una selección ponderada se determinan las de mayor importancia.
Diagrama de consumo vs producción: Estos gráficos pueden acercar el análisis a las condiciones reales de operación de la fábrica. Mediante la técnica de votación ponderada se determina la causa fundamental que genera la ineficiencia y sobre ella se podrán generar varias alternativas de solución que contribuyan al mejor funcionamiento del proceso.
2.3 Etapa III. Presentación del informe y toma de decisiones. Presentación de la propuesta de mejora
Se presenta a la gerencia la información necesaria para que tome las decisiones que tributen de forma más directa a minimizar el consumo de vapor de agua y del agua. Además, se hace un análisis económico de la propuesta de mejora identificada, estimando los posibles ahorros.
RESULTADOS Y DISCUSIÓN
3.1 Diagnóstico del sistema de vapor de agua y del agua.
3.1.1 Primera etapa. Identificación.
Se determina en qué forma, cómo y dónde se consume el vapor de agua y el agua por las diferentes áreas y circuitos del proceso, el siguiente listado muestra los resultados:
Destilación atmosférica. Tres circuitos consumen agua y tres consumen vapor.
Reformación catalítica. Dos circuitos consumen agua y un circuito consume vapor.
Fraccionamiento de gases. Dos circuitos consumen agua y uno consume vapor.
Caldera recuperadora. Consume agua y vapor como elementos de trabajo.
Planta de endulzamiento. Consume agua.
Generación de vapor. Dos circuitos consumen agua y vapor y tres consumen vapor.
3.1.2 Segunda etapa. Procesamiento y análisis de la información.
Análisis de Pareto. Se debe resaltar que, en el análisis de Pareto de este estudio, no queda bien definida la tesis 80/20 para los costos energéticos, o sea: el 20% de los procesos incurren en el 80% de los costos. Esto indica que agua y vapor se emplean en todos los procesos tecnológicos de este esquema de refinación y que, además, se consumen en magnitudes similares. Entonces, para un mejor análisis de los resultados se confecciona el diagrama de pastel mostrado en la Figura 1.
Se comienza el análisis por los costos energéticos para cada uno de los procesos que reciben el servicio del sistema de agua y vapor de agua. La Figura 1 muestra que el proceso de generación de vapor tiene mayor impacto sobre los costos energéticos. Este representa el 18,40 % y al mismo, además, debe sumársele el costo energético del tratamiento de agua de alimentación que representa el 7,36 %, o sea, de conjunto, suman el 25,76 %. Como es lógico, respecto al volumen, el consumo mayor de agua se centra en los diferentes procesos de refinación en conjunto, que, a su vez, estos son los que aportan la mayor contaminación del agua. La eficiencia con que se utiliza ese recurso, es alcance de otro trabajo.
No obstante, de forma particular corresponde al sistema de generación de vapor un análisis detallado del mismo. En el funcionamiento de las calderas se consume fuel oil producido en el mismo proceso de refinación, así como, operan consumiendo gas residual (fuel gas) de la red de gas combustible, evitando consigo su emanación al medio. Como este es un producto residual sin valor comercial (H2, CH4, C2H6, básicamente) sigue siendo el agua el elemento de mayor valor en el proceso de generación de vapor, lo que incide directamente en los costos de producción. A esta afirmación se debe agregar que a partir del año 2012 el precio del agua se incrementó en 1,21 unidades monetarias/m3. El precio actual del agua es 1,55 unidades monetarias/m3. Esta razón motivó que para el estudio se tomara entonces el año 2018. En la Figura 2, se presenta el comportamiento del consumo de agua y de fuel oil respecto a la cantidad de vapor generado por meses del año estudiado y se muestra el índice de generación de vapor por cada m3 de fuel oil consumido.
Queda claro que el consumo de fuel oil no es significativo en comparación con el agua.
En el primer trimestre del año 2018, se observó una reducción apreciable de la producción de vapor, mientras el consumo de agua se mantuvo aproximadamente al mismo nivel. Esto se justifica por la incorporación de dos procesos de refinación a inicios del año, sin que este consumo adicional de agua, se corresponda con el proceso de generación de vapor. En el segundo y tercer trimestre del año, se observó una producción de vapor con un incremento considerable en el mes de abril; posteriormente se aprecia un incremento leve y sostenido, mientras tanto, el consumo de agua se mantuvo en constante crecimiento por cinco meses y cayó bruscamente en los meses de septiembre y octubre, cuando la producción de vapor crecía. Esto demuestra que existen consumos no asociados a la producción, que están deteriorando los índices de eficiencia. En el análisis del cuarto trimestre del año se puede observar que la producción de vapor va disminuyendo constantemente, por su lado el consumo de agua creció en noviembre y cayó bruscamente, motivado por una parada planificada. En resumen, en el año se refleja un consumo de 341 500 m3 de agua y se producen 128 600 t de vapor, lo que equivale a un índice de generación de 2,66 m3/t de vapor producido.
En el estudio se ha demostrado que en el complejo de refinación existe un elevado consumo de agua y se precisa conocer las causas que lo provocan. Para ello se tiene en cuenta los criterios recogidos en la tormenta de ideas y se elabora el diagrama de Ishikawa (Figura 3) a fin de organizar las principales causas y sub-causas que inciden en el proceso tecnológico.
La causa “Régimen de mantenimiento”, se ha podido comprobar durante la observación que no es precisamente una causa de mayor peso, pues los procesos de mantenimiento tienen un adecuado control tecnológico y una alta prioridad gerencial, por tanto, los recursos no son un problema.
Resta entonces centrar el análisis y las acciones en las tres causas restantes y sus respectivas sub-causas. Para esto se aplicaron las técnicas de la metodología de diagnóstico, señaladas anteriormente.
Con todas las deficiencias detectadas (causas), se realizó un detallado análisis para definir las de mayor impacto durante la operación. Se realizó una selección de las causas a fin de aplicar la votación ponderada para determinar sobre cuáles se debe trabajar con vistas a reducir los consumos de agua y vapor de agua. El listado de causas seleccionadas se presenta a continuación y en la Tabla 1 se presenta dicha votación.
Sistema de generación de vapor sobredimensionado, que lo convierte en el mayor consumidor de agua.
No se tienen herramientas para estimar los costos medioambientales.
El complejo de refinación no ha implementado una estrategia encaminada al control y uso racional del agua y el vapor.
Insuficiente capacitación del personal que trabaja con el recurso agua.
Pocos medios de medición y control del consumo de agua.
No existe cultura de uso y reuso del agua en la empresa.
No están bien definidos los indicadores de eficiencia y eficacia del uso del agua.
No existen estrategias que permitan la aplicación de técnicas novedosas sobre el uso racional del agua.
No existen incentivos que motiven al personal a usar eficientemente del agua y el vapor de agua.
La gerencia no ha identificado dentro de sus prioridades la filosofía del uso racional del agua.
Tabla 1 Resultados de la Votación Ponderada por los especialistas
Especialista 1 | 5 | 4 | 2 | 3 | 1 | |||||
Especialista 2 | 5 | 2 | 4 | 3 | 1 | |||||
Especialista 3 | 4 | 3 | 5 | 2 | 1 | |||||
Especialista 4 | 4 | 2 | 5 | 1 | 3 | |||||
Especialista 5 | 5 | 4 | 2 | 3 | 1 | |||||
Suma | 23 | 5 | 18 | 2 | 5 | 16 | 1 | 4 | 1 | 1 |
Frecuencia de puntuación | 5 | 2 | 4 | 1 | 3 | 5 | 1 | 2 | 1 | 1 |
Orden de prioridad | 1 | 5 | 2 | 7 | 4 | 3 | 8 | 6 | 9 | 10 |
Como puede observarse en la Tabla 1, las causas 1, 3 y 6 recibieron las puntuaciones más elevadas, en ese orden; les siguen las causas 2 y 5, pero la causa 5 fue punteada más veces, el resto de las causas presentan menor puntuación y totales, por consiguiente, la selección de causas se plantea según el siguiente orden:
Sistema de generación de vapor sobredimensionado, que lo convierte en el mayor consumidor de agua.
El complejo de refinación no ha implementado una estrategia encaminada al control y uso racional del agua y el vapor.
No existe cultura de uso y reuso del agua en la empresa.
Pocos medios de medición y control del consumo de agua.
No se tienen herramientas para estimar los costos medioambientales
3.1.3 Tercera etapa. Presentación de informe y toma de decisiones. Propuesta de mejora
Terminado el diagnóstico del sistema de agua y vapor, se pudo comprobar el excesivo consumo de ambos y las causas fundamentales que lo provocan. Por consiguiente, la gerencia está en condiciones de tomar las decisiones más viables para reducir esos consumos. También se demostró el sobredimensionamiento del sistema de generación de vapor, entonces, sobre él recae la propuesta de mejora tecnológica.
3.1.4 Características generales del sistema de generación de vapor:
En el área de generación de vapor se registran tres calderas convencionales de 25 toneladas cada una. Normalmente permanece una operando y otra de reserva. Estas pueden trabajar en cinco rangos diferentes de flujos de vapor en toneladas/horas, a saber: 8,05 t/h; 10,51 t/h; 12,43 t/h; 15,53 t/h y 17,29 t/h. Para el estudio se seleccionó el rango de producción de vapor de 12,43 t/h, porque habitualmente se trabaja con el objetivo de completar la demanda del proceso de refinación, aproximadamente 20 t/h, con las 8-9 t/h de vapor que se producen en la caldera recuperadora. En la Tabla 2 se muestra la evaluación realizada mediante la metodología de Torres (1991).
Dicha caldera recuperadora debe consumir entre 13-15 m3/h de agua, equivalentes a 9360-10 800 m3/mes, para entregar entre 8 - 9 t vapor/h, o sea, 5760-6480 t vapor/mes (Landestoy, 2010). Pero ni su producción, ni su costo energético, ni su consumo de agua son reflejados en este informe porque esta caldera está fuera de operación. La capacidad de diseño de la caldera recuperadora es de 25 t/h. Entonces se propone realizar una rehabilitación total de la misma para que trabaje a plena capacidad, lo cual sería suficiente para satisfacer la demanda de vapor del proceso tecnológico con una reserva adicional de 5 t/h. Adicionalmente disminuiría el consumo de energía, los costos de producción, el consumo de reactivos, el consumo de agua y las emanaciones al medioambiente. La fundamentación se demuestra con una evaluación termoeconómica de la producción de vapor mediante la metodología de Torres (1991); también mostrada en (Silva, 2015); (Ríos, 2016) a modo de comparar los sistemas de producción existente (Ver Tabla 2).
El costo exergo económico del flujo de vapor de agua, se considera como el aporte de dos contribuciones: La primera, procede del costo monetario de la exergía de los recursos involucrados en el proceso: su costo exergético. La segunda, el resto de los costos originados en el proceso productivo asociado a su obtención, tales como, costos de amortización, operación y mantenimiento.
Tabla 2 Resultados de la evaluación termoeconómica de cada variante, justificación de la propuesta presentada
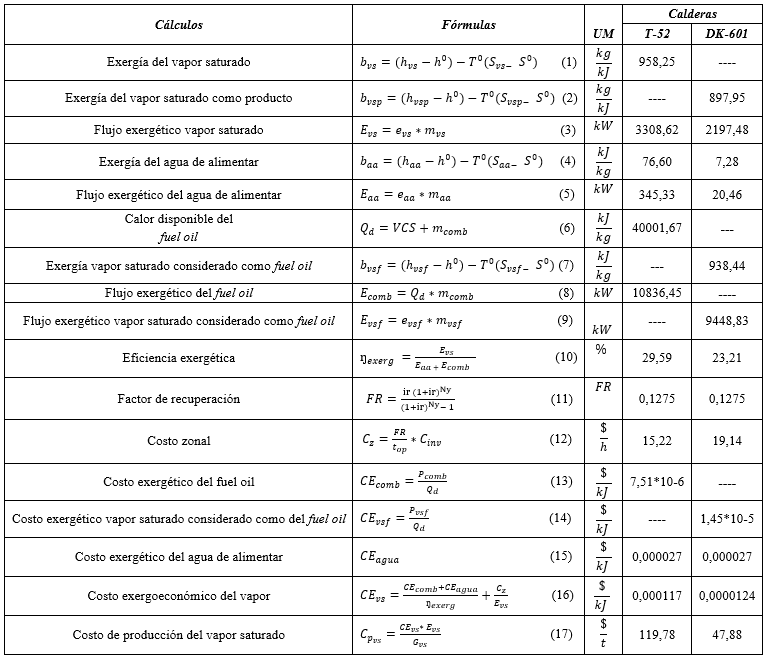
En este análisis, se mezclan parámetros termodinámicos como la exergía del agua y el combustible y la eficiencia exergética de la instalación. Como parámetros económicos los precios del agua y el combustible, dentro del costo zonal, el costo de la inversión, el factor de recuperación de la inversión; además están presentes los flujos de cada una de las corrientes implicadas.
En la Figura 4, se muestra como disminuye el costo de producción del vapor a medida que aumenta la capacidad de producción de ambas calderas, al mismo tiempo que aumenta la eficiencia exergética de las mismas. Sin embargo, es evidente cuanto más económico resulta la producción de vapor en la caldera recuperadora y cuanta mayor eficiencia aporta al sistema de generación, pues recupera el calor residual de los gases de escape de los hornos de refinación para producir vapor, sin consumo de combustible convencional. Esto además reporta por consiguiente un menor impacto ambiental. En este análisis del gráfico queda demostrada la objetividad de la propuesta de mejora.
CONCLUSIONES
La evaluación general del sistema de producción de vapor, acorde a las premisas establecidas en el presente estudio, permitió definir que:
El diagnóstico demostró un elevado consumo de agua en el año estudiado (341 500 m3/año) y se identificó al área de generación de vapor como la más consumidora de agua con un índice de consumo de 2,66 m3 agua/t de vapor producido. Estos resultados son elementos claves para la toma de decisiones.
La evaluación termoeconómica de la propuesta de mejora, muestra una reducción de 71,90 $/t de vapor producido, lo que demuestra la conveniencia de la reparación de la caldera recuperadora. En ella se estima una disminución del impacto ambiental, pues no hay consumo de combustible convencional.