Introducción
El Aluminio-Silicio (Al-Si) es la aleación de fundición de Aluminio (Al) más utilizada debido a su amplia aplicación en componentes comerciales. La importancia de estas aleaciones según nos explica, Javidani M, Larouche D: <<…se basa en la baja contracción durante la solidificación, buena soldabilidad, bajo peso específico, excelente resistencia a la corrosión …>> [1]. Cuando estas propiedades se combinan con buenas propiedades mecánicas, el material puede aplicarse en la industria del automóvil porque permite reducir el peso del vehículo, y en consecuencia, disminuye el consumo de combustible [2].
El mayor problema del aluminio es su reducida resistencia mecánica, tanto menor cuanto mayor es su grado de pureza. Estas propiedades mecánicas se pueden incrementar mediante la adición de elementos de aleación o mediante procesos de conformado en caliente y frío. Los elementos de aleación pueden introducirse en la red del aluminio y endurecerla por solución sólida, o bien pueden hacer que la aleación sea objeto de tratamientos térmicos de solución y precipitación (maduración) y conseguir resistencias mecánicas hasta 30 veces mayores que la del aluminio puro [3].
Sin embargo, los elementos de impureza inevitables reducen seriamente las propiedades mecánicas globales del aluminio. El hierro (Fe) es una de las impurezas más dañinas en las aleaciones Al-Si, y la fase rica en Fe formada tiene un efecto perjudicial sobre la plasticidad de la aleación. En particular, la fase β-Al5FeSi (β-Fe) en forma de plaqueta no sólo fragmenta gravemente la matriz, sino que también favorece la formación de defectos de fundición, como por ejemplo porosidad por contracción, deteriorando las propiedades de la aleación [4].
Estudios realizados por Bidmeshki C, Abouei V, et al [5, 6], muestran que el hierro es la impureza más común del aluminio y sus aleaciones. No se elimina fácilmente y puede tener efectos adversos en las propiedades mecánicas, sobre todo en la colabilidad, destacándose las aleaciones de fundición a base de Al-Si. En sus investigaciones, sobre aleaciones hipoeutécticas Al-Si, con compuestos de β -Al5FeSi, concluyeron que la presencia de Fe en aleaciones Al-Si conduce a la formación de agujas.
De igual forma estudios realizados por Baldan R, et al [7], en una aleación de Al9Si hipoeutéctica de Al-Si. Planteando que el hierro es el elemento de impureza más nocivo en las aleaciones de fundición a base de Al-Si, debido a que aparece en formas de agujas groseras disminuyendo las propiedades mecánicas de piezas con este elemento, realizando ensayos a varias probetas con un contenido de Fe del 0,8 % sometida tracción, el cual fue interrumpido justo después del límite elástico. Esto resultó que la grieta se propagaba en los extremos de partícula β-Al5FeSi y posterior sobre la misma, destacando la partícula como un concentrador de tensiones. Además, demostraron, que las partículas de β -Al5FeSi dificultan el flujo del líquido eutéctico hacia el interior del molde, generando vacíos en las regiones interdendrítica, aumentando la cantidad de poros. También demostraron que el compuesto β -Al5FeSi constituye barreras potenciales para alimentación de metal líquido en una región de colada sometida a contracción. A su vez estudiaron la cantidad de fase β -Al5FeSi en la aleación y resultó que, la cantidad de microporos era proporcional al contenido Fe. Así, del mismo modo la presencia de la fase β -Al5FeSi disminuye la resistencia mecánica, principalmente el alargamiento.
Sin embargo, los autores anteriores, plantean que las aleaciones Al-Si para elementos de motores de combustión interna, el hierro es un elemento deseable que ayuda a mejorar las propiedades a alta temperatura y la estabilidad térmica de la aleación.
Para mitigar parte de los fenómenos anteriores, ocasionados por el contenido de hierro, el Manganeso (Mn) es un elemento eficaz en la modificación de compuestos intermetálicos en forma de aguja. La adición de hasta la mitad de la cantidad de hierro da lugar a la formación de algunos compuestos intermetálicos que contienen Mn en la matriz, como α-Al15(FeMn)3Si2. Concluyendo que la adición de Mn en aleaciones Al-Si cambia la morfología de los compuestos intermetálicos ricos en Fe de agujas o plaquetas a polígonos, lo que resulta beneficioso para la estructura y las propiedades mecánicas del material. Debido a esto muchos componentes de automoción que antes se fabricaban con hierro fundido utilizan ahora aleaciones de aluminio [8].
Según Bao Quoc, D, et al [9] , los productos más destacados de la tecnología de fundición son los pistones para motores de automóviles.
El objetivo de este trabajo fue obtener una pre-aleación compleja de aluminio y posteriormente la aleación correspondiente de pistones para motores Diésel, usando como elemento de aleación el silico-manganeso. El problema fundamental radica en los defectos (grietas) mostrados en el pistón obtenido, el cual en su composición química no contenía Mn, por lo que necesita ser evaluado para encontrar una solución y brindar las recomendaciones que requiera para lograr resultados satisfactorios. La única solución al problema no es la adición de Mn a la aleación, pueden existir otras soluciones al problema de las grietas ocasionadas por el intermetálico β-Al5FeSi, pero no se cuentan con otros productos auxiliares que pueden mitigar este defecto, siendo esta la limitante fundamental del estudio.
Métodos y Materiales
Para el caso que nos ocupa es transcendental analizar las funciones del componente que demanda esta aleación en particular. Las aleaciones para pistones de motores donde se emplea el petróleo como combustible, están sometidas a condiciones más severas (esfuerzos y temperaturas) comparado con las aleaciones para los pistones normales de vehículos con motores de gasolina [10].
En nuestro caso nos referiremos a las aleaciones más comunes para la fabricación de pistones fundidos de tractores. Los trabajos realizados por ingeniería inversa (RE), a pistones originales, en el Centro de Estudios Avanzados (CEA) utilizando, analizador químico, microscopio óptico y electrónico, revelaron que los pistones seleccionados para el estudio, son de una aleación hipo-eutécticas Al-Si, que su composición química se encuentra en los rangos mostrados en la tabla 1 y en la figura 1, las características metalográficas del mismo.
Tabla 1 Composición química obtenida de varios pistones fundidos de tractores YUMZ. Fuente: autores
% Si | % Mg | % Cu | % Ni | % Fe | % Mn | % Ti |
---|---|---|---|---|---|---|
10 - 13 | 0.5 -1.5 | 0.7- 3 | 0.8 - 3 | 0.3 - 1 | 0.1-0.5 | 0.05 -0.02 |

Fig. 1 Muestra obtenida de pistones originales por RE (patrón). a) Buena modificación. (α+ eutéctica-α+Sí) no presenta granos con agujas de Si. A 100X. b) Presencia de intermetálicos en forma redondeada; Si (marcas oscuras), y α-Al(FeMn)Si, gris medio, 0, 5 %HF.500X.
A su vez, para la obtención de la aleación correspondiente a estos productos, se utilizó la norma española de la tabla 2. para pistones de motores Diésel semipesados.
Tabla 2 Composición química de pistones para motores Diésel semipesados. Fuente: UNE 38 265
% Si | % Mg | % Cu | % Ni | % Fe | % Mn | % Ti |
---|---|---|---|---|---|---|
10 - 13 | 0,7-1,5 | 0,5- 1,5 | 0,5- 1,5 | 0,8 | 0,3 | 0,2 |
Al inicio de la producción de los pistones Debido a los escases de Mn, se hicieron una serie de coladas, donde los pistones presentaron defectos (grietas) posterior al maquinado, lo que provocó que retornaran a la fundición, una parte importante de los productos, para su recuperación.
Los estudios realizados en el CEA, indicaron que, la aparición del compuesto químico β-Al5FeSi, generado por la adición de Fe, era el intermetálico perjudicial, debido a la morfología en que aparece. Tal y como plantean Chen J, Liu C, Wen F, Zhou Q, Zhao H, Guan R. [11], en su estudio, para mejorar las propiedades mecánicas, en una aleación de Al-Si añadiéndole Escandio (Sc) y Circonio (Zr) en ausencia del Mn. La figura 2, es una de las muestras obtenidas de los pistones con problemas, mostrando una morfología agujosa de estos intermetálicos.
Posterior al estudio, para determinar qué provocaba las grietas y establecer que los intermetalicos aparecían en forma de agujas por ausencia del Mn; se gestiona una materia prima de Silico-Manganeso (Si-Mn) con una composición química tal y como se muestra en la tabla 3, la cual serviría para preparar una pre-aleación con una materia prima de Al puro.

Fig. 2 Muestra de un semiproducto fundido con la fase β-Al5FeSi perniciosa, aumento 80μm.
Tabla 3 Composición química del Si-Mn. Fuente: autores
% C | % Mn | % Si | % P | % S | %Fe |
---|---|---|---|---|---|
2 | 65 | 15 | 0,25 | 0,04 | 18 |
Con los resultados de la composición química de los pistones originales, más la norma y los estudios de la falla elaborados por el CEA, revelando que provocaba las grietas en los pistones; se planifica la fusión de la pre-aleación, así como la aleación. La figura 3 muestra los pasos lógicos para cada etapa de la fusión de la pre-aleación, siendo estos similares para la obtener la aleación final.

Fig. 3 Diagrama de flujo para la tecnología de fusión de la pre-aleación, que se extiende para la aleación.
Para la fusión, se contaba con un horno de inducción de 150Kg de Al y crisol de grafito, tal como se muestra en la figura 4a), y para la comprobación de la composición química se empleó un Espectrómetro Multicanal Digital Modelo Belec VARIO LAB de fabricación alemana, con detectores CCD y PMT, longitud de onda: máx. 680 nm, min. 120 nm, figura 4b), preparando las muestras basados en las indicaciones del manual del equipo.
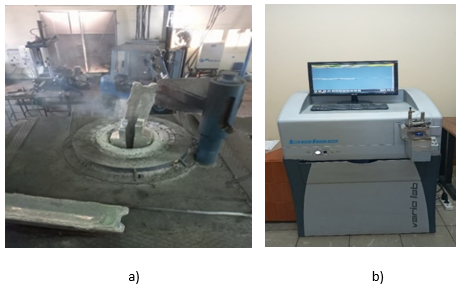
Fig 4 Muestra de los los equipos para garantizar el preceso de fusión. a) Horno de induccion cargado con barras de alumnio puro. b) Espectrómetro. BELEC VARIO LAB.
Para la adición de cada uno de los componentes para la pre-aleación, así como para la aleación final, se utiliza la ecuación (1). La masa de pre-aleación a preparar es de unos 120 kg. 95 kg de lingotes de Al +25 kg de Al-Cu (con aporte de unos 4 kg de Cu), más la cantidad de Mn (kg) contenido dentro de 8,8 Kg de Si-Mn gestionados por los autores.
Para el caso del incremento del Si Para calcular el incremento en el contenido de Si que absorbe el baño metálico debido a la adición del Si-Mn se empleó la ecuación (2).
Para lograr la materia prima necesaria de la aleación, se fundió la pre-aleación en lingotes como se muestra en la figura 5 y estos, se utilizarían como aditivos, en una aleación base para ajustar la composición química de la aleación a alcanzar. Tal como nos plantean Sathish T, et al [12] en su investigación.

Fig. 5 Muestra el manejo del metal fundido de la pre-aleación. a) vertido y traslado de la pre- aleación. b) Fundicion de la pre-alacion en lingotes.
Después de tener la pre-aleación se procede a la fusión de la aleación. El cálculo de carga se hace utilizando la expresión 1 y 2, para cada uno de los elementos químicos de la composición para pistones; teniendo en cuenta las pérdidas por oxidación. Esto depende de cada tipo de horno, la demora de la colada, las dimensiones y geometría de las cargas, etc. En hornos eléctricos de crisol (horno de mantenimiento) el cual fue empleado y se muestra en la figura 6, se pierde Al 0,5-1% y si la carga está muy oxidada se llega a 2,5%; el Si 0,5-1 %; el Mg 2-3 %; el Cu 0,05-1 %. Según nos plantea, Brough D, y Jouhara H [13], en su estudio. En la tabla 4 se muestra la composición base a la que se le realizaron los cálculos de carga.
Resultados y Discusión
Comportamiento químico y estructural
A continuación, en la tabla 5, los resultados del cálculo de carga en la pre-aleación. Estos resultados representan la condición inicial para realizar la aleación correspondiente del producto (pistón).
Tabla 5 Por cientos de Mn; Fe; Si; Cu presentados en la pre-aleación por cálculos teóricos. Fuente: autores.
Mn | Fe | Si | Cu |
---|---|---|---|
4,44 % | 1,2 % | 1 | 3,11 % |
Durante la fusión de dicha pre-aleación se extrajo dos muestras, para analizar el comportamiento químico y los por cientos que contenía de cada elemento, profundizando en el Mn y el Cu.
En la primera toma de muestra aún el Si-Mn no ha quedado totalmente fusionado en la pre-aleación, sin embargo, en la tabla 6 y figura 7 se expresa el valor del Mn con un 2,030 %.
Una vez derretido el Si-Mn se extrae la segunda y última muestra, su composición química se representa en la tabla 6. Como se puede apreciar, los cálculos de carga no corresponden a la cantidad de Mn en la pre-aleación obtenida por fusión. Lo cual se tendrá en cuenta, y se utilizará las composiciones de la tabla 6 para los siguientes cálculos, más las tomas de muestras en la aleación para controlar y garantizar la composición que se necesita.
Tabla 6 Resultado de las muestras tomadas. Fuente: autores
No. de muestras tomadas | % Si | % Fe | % Cu | % Mn | % Mg | % Cr | % Ni |
---|---|---|---|---|---|---|---|
1 | 0,784 | 0,546 | 3,151 | 2,030 | 0,009 | 0,0260 | 0,022 |
2 | 1,316 | 1,319 | 4,500 | 2,758 | 0,003 | 0,0034 | 0,009 |

Fig. 7 Resultados de la primera muestra de la prealeación, obtenida en el Espectrómetro BELEC VARIO LAB.
En el proceso de fusión de la aleación, La colada se hizo en el horno de mantenimiento, por ser poca la cantidad de metal en la prueba y de pistones a obtener (35 pistones y unos 140 Kg de aleación) los resultados de las diferentes muestras analizadas químicamente se muestran en la tabla 7, donde se puede observar la disolución de cada componente en el tiempo.
Tabla 7 Resultados de las diferentes muestras tomadas en el proceso de fusión de la aleación. Fuente: autores
Muestras | Si % | Fe % | Cu % | Mn % | Mg % | Cr % | Ni % | Tiempo (horas) |
---|---|---|---|---|---|---|---|---|
1 | 5,58 | 0,380 | 1,175 | 0,127 | 0,044 | 0,005 | 0,706 | 0,40 |
2 | 5,88 | 0,335 | 2,039 | 0,221 | 0,033 | 0,008 | 0,937 | 1,06 |
3 | 6,84 | 0,384 | 1,664 | 0,246 | 0,029 | 0,006 | 0,729 | 1,30 |
4 | 6,78 | 0,378 | 1,918 | 0,266 | 0,031 | 0,007 | 0,717 | 2,07 |
5 | 8,05 | 0,382 | 1,919 | 0,288 | 0,028 | 0,007 | 0,712 | 2,38 |
6 | 9,52 | 0,410 | 1,623 | 0,265 | 0,372 | 0,006 | 0,613 | 3,20 |
7 | 10,28 | 0,416 | 1,661 | 0,274 | 0,365 | 0,006 | 0,625 | 4,80 |
8 | 10,30 | 0,402 | 1,748 | 0,270 | 0,503 | 0,006 | 0,652 | 4,29 |
9 | 10,67 | 0,442 | 1,538 | 0,258 | 0,713 | 0,006 | 0,609 | 4,46 |
10 | 10,30 | 0,423 | 1,575 | 0,274 | 0,782 | 0,006 | 0,602 | 4,57 |
11 | 10,56 | 0,496 | 1,830 | 0,295 | 0,907 | 0,007 | 0,738 | 5,00 |
12 | 11,74 | 0,42 | 1,517 | 0,3 | 0,436 | 0,007 | 0,886 | 5,30 |
En el gráfico de la figura 8, se pueden valorar los resultados de los elementos de mayor interés (Mn y Fe) para la aleación que se desea obtener. De estos resultados se deduce que la tendencia al incremento a disolver ambos elementos, aumentando en el tiempo de una forma lineal. Sin embargo, hubo resultado de los análisis de la composición química que mostraron cierta tendencia a las perdidas, esto pudo ser responsabilidad de mantener mucho tiempo la aleación en el proceso de fusión y por esta razón haya oxidado parte de estos elementos, como plantea, Capuzzi S, et al [14] en su revisión sobre la fusión de chatarra de Al.
Análisis metalográficos del pistón después de fundidos
Se trabajó en el Laboratorio de Metalografía de la Facultad de Ingeniería Mecánica de la Universidad Tecnológica de La Habana en conjunto con el CEA y Centro de Investigaciones Metalúrgicas (CIME). con muestras de la aleación de aluminio recién obtenida.
En la figura 9a), se muestra la metalografía de la aleación, destacándose Cristales de silicio embebidos en una matriz de aluminio bien modificada. Se puede ver patrón dendrítico de los cristales de Si en forma no aguda. Esto garantiza cierta resistencia mecánica como nos explica, Campbell J. [15, 16], en su investigación sobre el comportamiento de este grupo de aleaciones; además si lo comparamos con el patrón de la figura 1a), tienen cierta similitud en la morfología de los granos de Si. También, si comparamos las figuras 1b) y la 9b) encontramos cierta analogía morfológica, entre lo obtenido y el patrón de referencia; a su vez presenta semejanza con los estudios realizados por Berlanga Labari, C. et al, [17].
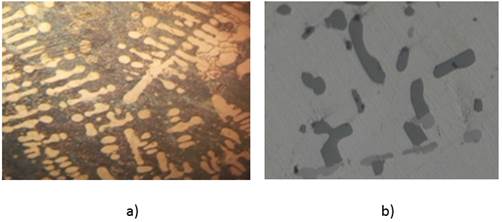
Fig. 9 Muestra de la microestructura de la aleación. a) Cristales de silicio embebidos en una matriz de aluminio de forma redondeada, 200X. b) Presenta forma redondeada de los intermetálicos; Si (marcas oscuras), y α-Al(FeMn)Si, medio gris 0,5 %HF.500X.
Los ensayos realizados en los laboratorios fueron de las formas siguientes : la superficie de la muestra fue desengrasada con acetona de calidad técnica y sometida al ataque químico (H3P04) seguido de enjuague y secado final. La observación de la superficie del material de la muestra ensayada se realizó con aumento de 500X. Destacándose un intermetálico de α-Al(FeMn)Si. de color gris oscuro. Tal y como expone, Szklarz Z, et al, [18]. observando la superficie de una aleación de Al2017. Sus análisis revelaron que la fase gris oscuro, es una mezcla de elementos AlSiMnFeCu la cual coincide con los resultados de este trabajo, mostrados en la figura 10.

Fig. 10 Se puede observar el constituyente de AlFeMnSi de un color negro y el Si de color gris claro. 500X con ataque(H3P04).
La figura 11 muestra la microscopia electrónica. En ella se observa un Intermetálico con morfología no puntiaguda, cosa que se puede valorar y comparar con los resultados de la figura 2. En la imagen se señalan las zonas a las cuales se le determinó la composición química, estas tiene similitud con las imágenes mostradas en los estudios de [18] donde se destaca la forma de estos compuestos cuando se añade Mn u otro elemento que transforma la fase β-AlFeSi en una fase no perjudicial, con morfología redondeada o estrellada.

Fig.11 Muestra de un semiproducto fundido con faces α o δ Según [19] no perniciosa, 80μm.
De lo anterior se valida la función del Mn en las aleaciones para pistones de motores Diésel, lo cual dio buenos resultados, debido a que se está utilizando la aleación en la fabricación y reparación de los motores de tractores YUMZ sin rechazo alguno.
Conclusiones
El itinerario tecnológico expuesto en la figura 3 para llevar acabo los dos procesos de fusión; de la pre-aleación y la aleación correspondientes a una aleación de Al, partiendo de una materia prima de referencia y Si-Mn, proporcionando una descripción lógica, la cual tuvo aceptación en los resultados alcanzados.
Los resultados de los laboratorios muestran una concordancia con la bibliografía estudiada, logrando eliminar las grietas que aparecen en pistones de aleación de Al para motores de combustión interna.
Queda demostrada la influencia del Mn en estas aleaciones, para la transformación de la fase β-AlFeSi en Al(Fe,Mn)Si no perniciosa (α o δ) con una tendencia morfológica al redondeo.
En este estudio se comprobó que la disolución del Si-Mn en un horno eléctrico de mantenimiento es lento, lo cual no es recomendable, debido a la demora que implica esto, repercutiendo en pérdidas por oxidación de algunos elementos químicos, para la aleación.