Introducción
Los procesos de fundición están entre los de fabricación más antiguos que se conocen. Su uso se ha aplicado casi exclusivamente para la fabricación de piezas metálicas, extendiéndose a muchos otros materiales. La fundición por moldes metálicos permanentes (coquillas) es un método usado para obtener un producto fundido usando un molde muy durable, por acción de la gravedad o a presión, diferente a la fundición convencional en arena, donde se usa solo una vez el molde y casi siempre empleando la fuerza de gravedad para introducir el metal fluido. De los beneficios del empleo de estos moldes está el empleo repetido del mismo para obtener un gran número de piezas iguales, elevada productividad, debido a una mayor velocidad de enfriamiento se obtiene una disminución del tamaño del grano de la estructura, mejorando varias propiedades mecánicas, producen un producto con elevada precisión dimensional, cercana a la forma deseada y usando menor material fundido, reducen considerablemente el área de los talleres.
Según Roni Sahroni, et al [1], «…el diseño de los moldes permanentes para fundición puede ser considerado como arte y ciencia…»; en su trabajo diseñaron y optimizaron los alimentadores y el sistema de alimentación, usando los softwares de análisis, de un molde permanente metálico para obtener una abrazadera cuello de ganso.
Dučić, et al [2] realizaron el análisis de un molde permanente para obtener un racimo de 8 bolas de hierro fundido para el proceso de beneficio por flotación del mineral de cobre. Realizando el análisis virtual con el software MAGMASOFT, visualizaron el proceso y evaluaron la influencia de la temperatura de precalentamiento del molde y la temperatura del agua del sistema de enfriamiento, en la porosidad obtenida y el volumen de esta porosidad en el centro de las bolas. Luego elaboraron el molde y corroboraron los resultados físicamente con las bolas fundidas en el mismo.
Al igual que Dučić, Patnaik, et al [3] emplearon el software MAGMASOFT, pero esta vez para demostrar la necesidad del empleo del mismo para el cálculo y diseño de los parámetros empleados para la manufactura, en un molde metálico permanente, de la carcasa de un motor de combustión para un vehículo de dos ruedas. Los parámetros fueron calculados empíricamente e introducidos en el programa para comprobar, por simulación, la temperatura y el tiempo de llenado del molde, el aire atrapado (porosidad), la temperatura de solidificación y el enfriamiento.
Una investigación interesante realizaron Blondheim y Monroe [4], donde estudiaron la formación de porosidad en una carcasa fundida de aluminio en molde metálico a presión, apoyándose en el software MAGMASOFT, como causa fundamental de los costos de desechos. Realizaron 99 experimentos prácticamente sin variación en el proceso, obteniendo resultados positivos y negativos. Determinaron que es posible predecir por software las zonas de porosidad, pero que no se puede predecir la aleatoriedad del tamaño ni la distribución en dichas zonas.
Yang, et al [5] usaron el software ProCast para la simulación de procesos de fundición por gravedad y centrífuga. La verificación experimental indicó que los resultados de la simulación estuvieron muy acordes con los resultados experimentales.
Además Según Khan & Sheikh.[6] en su estudio comparativo entre los diferentes softwares de simulación para fundición, el ProCAST es uno de los paquetes de softwares que más posibilidades tiene y que prácticamente simula todas las características deseadas con buena precisión. En este trabajo se hará uso del mismo en su versión del año 2019.
Para el diseño de los moldes metálicos, Shahane, Aluru, Ferreira et al [7], estudiaron la importancia del régimen térmico, empleando simulación numérica, por el método de los volúmenes finitos, desarrollando y demostrando un procedimiento para obtener las temperaturas iniciales y de pared del molde, optimizando la calidad del producto a obtener.
Aravind, Ragupathi, et al [8], realizaron la simulación con el software MAGMASOFT para determinar los factores que probocaban los defectos en el cuerpo de una bomba de aluminio, fundida en molde metálico por gravedad. Identificaron los problemas y después de varias simulaciones llegaron a la conclusión de que no bastaba con hacer modificaciones en los parámetros de trabajo, por lo que, además, hicieron modificaciones como introducir un núcleo o macho en la parte superior del molde para permitir la salida de los gases durante la solidificación; así mismo incrementaron de 7mm a 20mm el espesor de un nervio de la pieza que actúa como mazarota, todo lo anterior permitió disminuir completamente la porosidad, lo cual validaron obteniendo la pieza fundida con las modificaciones realizadas.
Como criterios de diseño se tiene que la disminución del espesor provoca una disminución de la capacidad térmica de la coquilla y de acuerdo con esto, se eleva la temperatura de la misma, por otro lado, un espesor mayor aumenta la duración de la coquilla, pero dificulta la colada al aumentar la velocidad de enfriamiento, y por lo tanto disminuir la fluidez; además, aumenta el peso y su costo.
El objetivo del siguiente trabajo es diseñar y manufacturar un molde metálico para obtener semiproductos de aluminio para maquinado a partir de las necesidades de insumos del laboratorio de fundición y la necesidad de semiproductos para el taller de maquinado de una universidad para la impartición de las prácticas de laboratorios de Ingeniería Mecánica e Ingeniería Industrial.
Métodos y Materiales
La manufactura de la coquilla debe permitir la aplicación de los métodos modernos de elaboración mecánica con gastos mínimos de trabajo, materiales, y tiempo; esto debe cumplirse tanto para la obtención del semiproducto de fundición como para la elaboración posterior de la pieza.
Se toma como referencia lo planteado por Perez Sajudo, et al [9], «…la tecnología se desarrolla a partir de un plano de la pieza, en la cual aparece la información necesaria con la que debe quedar la pieza de acabado final…» A su vez propone una metodología para obtener las dimensiones de la coquilla la cual utilizaremos para nuestro diseño:
Análisis de las características constructivas de la pieza.
Posición de la pieza en el molde y selección del plano de división.
Cálculo de las sobremedidas de maquinado.
Determinación de las inclinaciones de salidas.
Contracción de fundición.
Cálculo del sistema de alimentación.
Mazarotas.
Diseño del molde.
Partiendo del plano de la pieza, la pieza se colocará de forma vertical con la parte de mayor módulo hacia arriba como se muestra en la figura1 a), para garantizar la solidificación dirigida; y sobre esta, la mazarota. A su vez de determina el plano de división con facilidad ya que la pieza es cilíndrica y tiene salidas naturales y obtenemos el semimolde derecho (SD) y el izquierdo (SI).
Los Márgenes de maquinado y las contracciones, determinan la magnitud de las sobremedidas. Para el caso que se propone, queda de la siguiente forma [9]:
El margen de maquinado es de 2 mm al radio.
Contracciones: Aleaciones de Al-Si se contraen alrededor de (0,7 al 0,84 %) de forma libre. Aumentar al diámetro mayor (dm) y a las demás superficies de revolución 4 mm + 0,07(dm).
En el caso de las longitudes, aumentar a las longitudes 2 mm + 0.07(L).
En el caso de la modelación, para seccionar la pieza en partes como se aprecia en la figura 1 derecha, los cálculos los volúmenes (V), módulos (M) y áreas de transferencia de calor (A), se utilizó un editor gráfico.
Para lograr una solidificación dirigida y la comprobación de que se cumplan las condiciones de obtención de una pieza con calidad, se emplearon las ecuaciones (1) y (2) [9]:
Cálculo del volumen de rechupe
Donde:
Maz |
Módulo de la mazarota |
M IV |
Modulo de la pieza en sección IV. |
V MAZ |
Volumen de la mazarota. |
U |
Aprovechamiento de la mazarota (%). |
% Re |
Volumen de rechupe. |
Vp |
volumen de la pieza (dm3). |
Cálculo del sistema de alimentación [10]
De igual forma, para realizar el cálculo del sistema de alimentación se emplearon los criterios obtenidos de F c : área de control, sección del tragadero (cm2), ecuaciones (3), (4) y (5):
Donde:
G |
peso del metal fundido que pasa por el tragadero (kg). |
K e |
velocidad específica de vertido (kg/s • cm3). |
V e |
volumen espacial (cm3). |
t |
tiempo de colada (s). |
S |
coeficiente que está en función del espesor medio de la pieza. |
α y b |
coeficientes que están en función del tipo de material a emplear, sus valores son 0,08; 0,15 respectivamente. |
Relación de las áreas para la colada [10]
Para los moldes metálicos la relación entre las secciones de las diferentes partes del sistema de alimentación (alimentador, escoriador y tragadero) se rige por la relación entre sus áreas. En este diseño no hay presente un escoriador, por lo que solo se toma la relación entre el tragadero y el alimentador Fa : Ft = 1,1 : 1. Por criterios se considera que, a consecuencia del rápido enfriamiento de la masa fundida en el molde metálico, los alimentadores en los moldes metálicos se hacen con una sección mayor que la que se emplea en moldes de arena, pudiendo ser de hasta 50 % mayor.
Diseño de la Coquilla
Partiendo de los resultados de las expresiones anteriores se tiene las dimensiones de los semiproductos que se deben obtener por función. Estos semiproductos reproducen la cavidad interior de la coquilla. En este caso se decide colocar dos semiproductos dentro del molde, uno cilíndrico y otro escalonado. En la figura 2 se observa el modelo en 3D de los semiproductos unidos por un sistema de alimentación común junto a sus respectivas mazarotas.
Régimen térmico de la coquilla [11]
En este caso, la ecuación de balance de calor para el sistema fundición - es la ecuación (6). La temperatura calorimétrica media del sistema permanece constante siempre que la pérdida de calor al medio ambiente desde la superficie del molde de enfriamiento no afecte significativamente al proceso de solidificación.
Para la solidificación de piezas fundidas, la cantidad de calor eliminado (𝑄env) de la superficie exterior del molde en enfriamiento varía con el tiempo (𝜏) y se puede calcular mediante la fórmula (7).
Donde:
L CR |
calor de cristalización del metal, J/kg. |
𝜌M, 𝜌mo |
densidad de la aleación y del material del molde, kg/m3. |
𝑉𝑂, 𝑉Mo |
volumen de la colada y del molde de enfriamiento, m3. |
𝑐m , 𝑐mo |
capacidad calorífica de la aleación y del material del molde, J/(kg⋅K). |
𝑇P |
temperatura de colada de la aleación, K. |
𝑇𝐶𝑅 |
temperatura de cristalización de la aleación, K. |
Tmo0 |
temperatura inicial de vertido, K. |
α3 |
el coeficiente de transferencia de calor desde la superficie exterior del molde de enfriamiento hasta el medio ambiente, W/(m2K). |
Fsur |
el área de superficie del molde de enfriamiento, m2. |
Tsur,Tenv |
la temperatura de la superficie exterior del molde y el medio ambiente, K. |
El flujo de calor del frente de cristalización se gasta en calentar el molde de enfriamiento y se libera en el ambiente a través del borde de metal endurecido, ecuaciones (8) y (9):
Donde:
α1 |
el coeficiente de transferencia de calor en el frente de cristalización, W/(m2K). |
δmo |
espesor de la capa de molde calentada, m. |
λm , λmo |
la conductividad térmica del metal y molde respectivamente, W / (m K). |
α2 |
se puede determinar a partir de las resistencias térmicas del espacio de gas y la capa de pintura. |
δmo |
es el espesor del borde de metal endurecido. |
Material del molde
Los materiales de fundición típicos con alta resistencia son la fundición gris (GCI) y la fundición de grafito vermicular (VGI). La fundición gris se ha utilizado muchos años debido a su excelente conductividad térmica, colabilidad y el mejor compromiso entre viabilidad y costo [12]
En el trabajo se utilizó una fundición gris laminar (FGL) según la muestra extraída de los semi productos, analizadas en el microscopio óptico a 200X como se observa en la figura 3, sin ataque, la que corresponde a una FGL según norma ASTM A-247 e ISO945-1975 (E), presentando la misma, una morfología del grafito con forma F-I. Los tamaños de las inclusiones de grafito varían entre T-2/3 a 3/4.
Para determinar la composición química del semiproducto, se realizó un análisis espectral empleando para el mismo un espectrómetro multicanal digital, modelo SPECTROLAB, No de serie 6536/94. La composición química se muestra en la tabla 1.
Tabla 1 Composición química de la muestra del semiproducto para fabricar la coquilla. Fuente: autores
% C | % Si | % Mn | % Cr | % P | % Cu |
---|---|---|---|---|---|
3,32 | 2,14 | 0,535 | 0,117 | 0,151 | 0,135 |
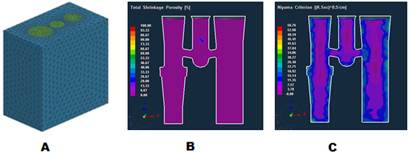
Fig 4 Imagen en 3D del molde mallado (A), resultados de la porosidad (B) y del criterio de Niyama (C).
Se tomó en cuenta los resultados de Yang et al, [4] que usaron un software de simulación de procesos de fundición 3D, para simular los procesos de fundición por gravedad y centrífuga. Con los resultados de los cálculos teóricos anteriores se procede a la simulación del molde utilizando el software anterior. La simulación muestra, entre otros resultados, las áreas de posibles defectos y las temperaturas máximas alcanzadas por el molde y la pieza. En el proceso de simulación, el software realizó los cálculos con un total de 54311 elementos, de ellos, 6020 en la superficie (2D) Molde Pieza y 48291 en el volumen (3D). Entre los resultados satisfactorios obtenidos de la simulación, mostrados en la figura 4, se observa que el mayor porciento de porosidad aparece en el sistema de alimentación, por otra parte, según el criterio de Niyama, prácticamente no hay zonas defectuosas en la pieza. Con estos resultados se procede a la construcción del molde, trazando una ruta operacional para cada máquina herramienta convencional empleada
Para el desbaste, se utilizó una limadora Modelo (B665-TH) de fabricación rusa. En la figura 5 se muestra la secuencia de desbaste utilizada.
Para lograr mejores requisitos de paralelismo y perpendicularidad, se instalan en la fresadora Modelo (Heckert) de fabricación alemana, sujetos por una mordaza como se muestra en la figura 6.
Con el objetivo de mejorar los requisitos antes mencionados y aumentar la hermeticidad entre las caras del molde que están en contacto y que contienen la cavidad interior, se procede al rectificado de estas superficies.
Seguidamente se hace al trazado (manual), taladrado, roscado y se sujetan ambos bloques por medio de los agujeros roscados con tonillos con cabeza cilíndrica y hexágono embutido.
Posteriormente se elaboran las cavidades interiores en un torno paralelo SNB 400 de fabricación rumana.
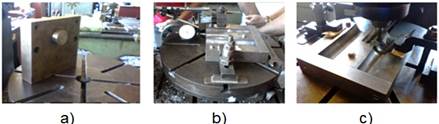
Fig. 7 Dispositivo para el centrado: a), instalación en la mesa divisora, b) elaboración de alimentadores, c).
La elaboración de los alimentadores se realizó en una fresadora (FB25U) de fabricación rumana. Para la correcta ubicación en la máquina, se prepara un dispositivo para garantizar la mejor coaxialidad entre el centro de rotación de la mesa divisora y la altura a la que se interceptan los alimentadores, en la figura 7 a) se puede apreciar el dispositivo colocado en el dorso del molde, la fijación en la figura 7 b) y el proceso de elaboración y de medición en la figura 7 c).
Resultados y Discusión
Después de construida la coquilla se decidió hacer diferentes pruebas tecnológicas en el taller de fundición. Una vez obtenidos los semiproductos en la coquilla, se tomó una muestra para realizarle un análisis químico de comprobación, cuyo resultado se muestra en la tabla 2, comprobando la coincidencia con el tipo de aleación de la norma ASTM A356.0 con un rango de fusión de 560-610 ºC.
Tabla 2 Composición química de la muestra del aluminio para fundir los semiproductos. Fuente: autores
% Si | % Fe | % Mn | % Mg | % Zn | % Cu |
---|---|---|---|---|---|
6,93 | 0,289 | 0,107 | 0,290 | 0,193 | 0,300 |
Para las mediciones de temperaturas durante todas las pruebas, se contaron con dos pirómetros láser manuales de los tipo PT300B; TI 120 con rangos de temperaturas entre 500 ºC - 1200 ºC y -20 ºC - 500 ºC respectivamente. Se realizaron las siguientes mediciones: temperatura de calentamiento de la coquilla, temperatura del metal vertido y temperatura de la coquilla entre coladas; para de esta forma comprobar los valores del diseño y brindar de una forma, lo más aproximada posible, los parámetros reales de trabajo de la coquilla.
Se realizaron 13 experimentos donde los mejores resultados se obtuvieron a partir de la octava colada en adelante, con una temperatura de precalentamiento y temperatura entre coladas de la coquilla entre 190-240 ºC y la temperatura del metal líquido entre 630-690 ºC, todo el tiempo sin el empleo de pintura en la coquilla. En la tabla 3 se puede observar el rango de los parámetros, que entendemos, a los que se debe explotar la coquilla, obtenidos como resultado de los experimentos.
Tabla 3 Resumen de los parámetros a los cuales se deben mantener la coquilla para una correcta explotación en las condiciones que se hicieron las pruebas. Fuente: Autores
Tsur (oC) | Tp (oC) | (ciclo (min) |
190-240 | 630-690 | 2-2,3 |
En la figura 8a) se aprecia la configuración de una de las partes de la pieza obtenida. Adicionalmente se maquinaron varias de dichas piezas, mostrando una excelente maquinabilidad y acabado superficial, además de un corte central para validar los resultados del software de ubicación de la cavidad del rechupe, que coincide con los resultados simulados, figura 8b)
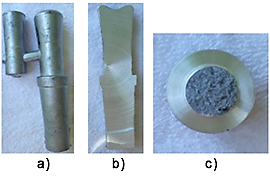
Fig. 8 Semiproducto fundido: a), semiproducto seccionado, b), parte de pieza fracturada c).
También presenta un aspecto a la fractura de un grano reducido, figura 8C, similar a lo planteado por Roni Sahroni et al, [1], apreciable en la maquinabilidad con una viruta fraccionada, debido a una mejora del material a sus propiedades mecánicas por la velocidad de enfriamiento. Por lo que cumple con el objetivo de un molde metálico y con los resultados del diseño teórico sin necesidad de realizarle un ajuste posterior al molde.
Este trabajo sirve de referencia para el proceso de diseño, selección de material y manufactura de moldes metálicos para fundición por gravedad de aleaciones metálicas.
Al igual que Aravind [8] y que Yang, et al [5], este último con el mismo software empleado en este trabajo, se obtuvieron congruencias entre los resultados simulados y experimentales, todos en piezas de aluminio fundidas en moldes metálicos. A diferencia de Blondheim y Monroe [4], no se obtuvieron resultados contrarios a los simulados, aunque la cantidad experimentada en este trabajo fue mucho menor a la de estos autores.
Conclusiones
Partiendo del plano de la pieza, usando las metodologías y ecuaciones conocidas de diseño y las técnicas convencionales de manufactura, se logró el diseño, fabricación y comprobación de un molde metálico para la obtención, por fundición por gravedad, de semiproductos de aleación de aluminio.
Las técnicas de diseño por software devuelven resultados que concuerdan con los experimentales obtenidos, validando positivamente los resultados de la simulación.
Quedaron establecidos los parámetros de explotación del molde metálico a partir de los resultados prácticos, los tiempos logrados coincidieron con los calculados teóricamente.