Introducción
En la actualidad el sector de manufactura desempeña un papel esencial en el desarrollo de las economías mundiales y el proceso de soldadura es uno de los más importantes tanto para la fabricación y el mantenimiento de elementos dentro de todos los procesos industriales. El proceso de soldadura por arco eléctrico con electrodo revestido, SMAW, Shield Metal Arc Welding, uno de los procesos más utilizados particularmente en aplicaciones con relación a estructuras metálicas y de tuberías [1].
En un ambiente controlado a pequeña escala, la formación de poros puede ser intencional para su estudio, sin embargo, la distribución del esfuerzo que se presenta alrededor del defecto no puede ser observado empíricamente por lo que es necesario el uso de simulación para describir con precisión la distribución de tensiones alrededor de los defectos de los poros [2, 3, 4].
En el proceso de revisión bibliográfica, el número de investigaciones que se enfocan en la discusión de defectos como poros a nivel microscópico es reducido. Para empezar con el estudio es importante tener en cuenta la norma internacional que es utilizada en este tipo de procedimientos. La norma API 1104, American Petroleum Institute, establece una reglamentación sobre las discontinuidades producidas en las uniones soldadas para tuberías de oleoductos y además es reconocida a nivel mundial. Sin embargo, tal como se indica en el apéndice A de dicha norma, los criterios de aceptación de las discontinuidades están basados sobre criterios empíricos de mano de obra. No obstante, los criterios empíricos basados en la experiencia de operadores de campo no son suficiente argumento para calificar como defectuosa una unión soldada. Pocos estudios se han centrado en el análisis de la presencia de porosidades en el proceso de soldadura y en las propiedades de tracción de aleaciones de aluminio que tienen más aplicaciones de tipo aeroespacial [5-6].
La presencia de poros, grietas, quemaduras, etc., en un cordón de soldadura pueden ser de diferentes tamaños y formas, las cuales alteran cuantitativa y cualitativamente las propiedades de los materiales [7]. Por lo tanto, para definir un poro, es necesario preguntarnos en primer lugar ¿cuál es el significado de porosidad? Según la definición presentada por la AWS, American Welding Society, se lo define como el resultado del gas que queda atrapado en el metal solidificante, el cual produce una discontinuidad que puede ser esférica o alargada. La porosidad puede también ser excesiva, se dice que no es crítica a menos que las discontinuidades no causen concentraciones de esfuerzo.
Por supuesto, no siempre se puede hacer o lograr imperfecciones que pueden ser observadas de la mejor forma para lograr saber cuál será su influencia en la junta soldada, por lo que la modelación matemática y simulación han tomado mucha importancia en los últimos años. Modelos matemáticos que van desde predecir el comportamiento y optimización de posición de robots que realizan procedimientos de soldadura [8], modelos que permiten evitar posibles escenarios catastróficos por fallas en estructuras ingenieriles por presencia de poros donde se produciría una falla por fatiga [8, 9, 10] hasta el uso de software que mediante elementos finitos logra reproducir la presencia de fallas de soldadura y sus efectos, especialmente en recipientes a presión y tuberías de transporte de petróleo [2, 11, 12].
Las simulaciones frecuentemente se enfocan en el uso del análisis de elementos finitos, sea ANSYS el software elegido u algún otro, para determinar o entender de mejor manera el comportamiento de un cordón de soldadura de forma general, identificar la concentración de esfuerzos, tensiones y deformaciones [13].
Por este motivo, el estudio propuesto pretende obtener y sobre todo ofrecer a la comunidad científica resultados e información sobre la base de la experimentación y modelación de este problema que representa un riesgo real y que podría llegar ser un problema económico de presentarse fallas este tipo de fallas. La investigación permitió determinar el esfuerzo último a tracción que tanto experimental como en la simulación tuvo una diferencia inferior al 3 %, además el diámetro de los poros tuvo un comportamiento inversamente proporcional.
Métodos y Materiales
Para estudiar el efecto del diámetro de los poros en el esfuerzo a tracción de la junta soldada con material base ASTM A36, varios pasos fueron llevados a cabo, figura 1.
Es necesario una caracterización metalográfica del material base, para garantizar que el material adquirido ASTM A36, corresponde a la composición y microestructura deseada para una selección adecuada del proceso de soldadura. Para ello se prepararon dos probetas metalográficas de acuerdo con la norma ASTM E 3-11 y un ataque químico con nital al 2 % de acuerdo con la norma ASTM E 407-99. Estas muestras se consideran representativas por tratarse de la misma lámina de acero utilizada.
El análisis de las fotomicrografías se realiza en el software IMAGEJ, mediante el método de áreas se cuantifica el porcentaje de fases y el porcentaje de carbono con la siguiente ecuación 1:
La ecuación 1 es parte de la regla de la palanca indicando que el acero es hipo-eutectoide. Con la aceptación en cuanto a la composición del material adquirido se lleva a cabo la calificación de un procedimiento de soldadura WPS, welding procedure specification, bajo el proceso SMAW a fin de determinar el esfuerzo último a la tracción de probetas sin discontinuidades, para comparar con las probetas que presentan discontinuidades, mismo que fue utilizado para preparar las uniones soldadas a evaluar, la Norma API Standard 1104 especifica un total de 4 probetas para ensayos de tracción a fin de calificar un procedimiento de soldadura. Dicho procedimiento fue utilizado para preparar las uniones soldadas a evaluar (con poros). Para ello se utilizaron placas de acero ASTM A36 de 12 mm (0,5”) de espesor. Las dimensiones de las probetas se muestran en el esquema de la figura 3 cada probeta de tracción debe tener una longitud de 230 mm (9”). La junta es a tope y el tipo de preparación del ángulo de ranura en V como se observa en la figura 2.
Sin embargo, de acuerdo a la norma ASME sección IX, cuando se extraen probetas de una placa que se encuentran ubicadas de manera sucesiva, deben tener espacios libres al inicio y al final de la soldadura para ser desechados con una distancia de 25 mm a cada lado. Para cumplir con estos requisitos y teniendo en cuenta el material eliminado por procesos de corte de las probetas se ha determinado una medida de cada placa de 165 mm de ancho para la extracción de 4 probetas con una anchura de 25,4 mm y una longitud de 114 mm que sumado la dimensiones más la abertura de raíz de 2 mm da 230 mm como se muestra en la configuración de la figura 2.
Es importante cumplir con requerimientos de soldadura descritos en el WPS, entre ellos el electrodo a utilizar es un E-6010, la selección de este electrodo es por la resistencia mínima que posee 413,68 MPa (60000 psi) similar a la del acero ASTM A36 127,47 MPa (62 000 psi). Los demás parámetros tanto geométricos como eléctricos se indican en la tabla 1.
Tabla 1 Parámetros de soldadura, WPS. Fuente: autores
Pases | Proceso | Electrodo (clase) | Diámetro Electrodo mm (in) | Amperios | Voltaje | Velocidad de avance mm/min | Polaridad |
---|---|---|---|---|---|---|---|
1 | SMAW | E-6010 | 3,96 (5/32) | 65 | 22 | 80 | - |
2 | SMAW | E-6010 | 3,96 (5/32) | 130 | 23 | 80 | + |
3 | SMAW | E-6010 | 3,96 (5/32) | 130 | 23 | 80 | + |
4 | SMAW | E-6010 | 3,96 (5/32) | 125 | 22 | 80 | + |
4 | SMAW | E-6010 | 3,96 (5/32) | 125 | 22 | 80 | + |
Las discontinuidades (poros) fueron creadas incrustando esferas cerámicas (óxido de alúmina Al2O3) en el segundo pase de relleno con diámetros de 2, 3 y 4 mm. Los poros están ubicados en el centro de cada probeta como se indica en la figura 4.
La presencia de los poros con sus respectivas dimensiones se verificó con NDT, Non-Destructive Testing, utilizando métodos de inspección visual para verificar la ausencia de discontinuidades externas y de radiografía industrial para discontinuidades internas, figura 5.
Con un espesor promedio de 15,25 mm del cordón de soldadura, el tiempo de exposición a rayos x es de 2,48 minutos. De acuerdo con la ecuación 2:
Donde:
t c : |
tiempo mínimo de exposición |
f n : |
factor de corrección de la película |
f p : |
factor por tipo de película radiográfica |
f D : |
factor de corrección por distancia |
f v : |
factor de corrección por el metal a irradiar |
Los datos para la determinación del tiempo de exposición de la junta soldada utilizados son: Intensidad de exposición 5 mA, nivel de energía 140 KV, ángulo de foco 40 grados, máximo tiempo de exposición 5 minutos, f n = 2,2; f p = 1; f D = 0,25; (previo a determinar la distancia mínima entre el foco y la placa a irradiar que depende proporcionalmente al ancho de la placa, 219,8 mm), fv = 1. El equipo utilizado para radiografía industrial pertenece a la marca BELTEAU, modelo BALTOGRAPHE BF 200-10 con las características indicadas en la tabla 2.
Tabla 2 Características técnicas del equipo generador de rayos x. Fuente: autores
Alimentación de la red | 10A - 50Hz (60Hz ante demanda) monofásico + tierra 220 V (200 - 240 V)-2 500 VA |
Alto voltaje mínimo útil | 40kV |
Alto voltaje máximo útil | 220 kV reales a 10 mA |
Fuente | 3,2 x 3,2 mm |
Angulo de Haz | 40 grados |
Funcionamiento ininterrumpido de 220 kV/10mA | ½ hora sin circulación de agua, limitado con circulación de agua |
Una vez obtenidas las probetas y verificado los diámetros de las discontinuidades (poros) se realiza el ensayo de tracción a una velocidad de 1 mm/s. Los ensayos se realizaron en el LAEV (Laboratorio de análisis de esfuerzos vibraciones de la Escuela Politécnica Nacional. Quito, Ecuador), la maquina universal es de marca Tinius Olsen modelo SuperL 120 con capacidad 120 000 lbf.
Este ensayo permite definir la carga máxima a la tracción. Con el área inicial, fácilmente se puede determinar el esfuerzo último a tensión teórico según la ecuación 3:
Donde:
F: |
fuerza máxima de resistencia a tensión, N |
A: |
área de la sección transversal inicial de la probeta, mm2 |
Al ensayar 4 probetas con cada diámetro de poro, se determina una media aritmética, con su respectivo coeficiente de variación. Además, para comparar el esfuerzo último de las probetas con discontinuidades vs probetas sin discontinuidades se utiliza los resultados obtenidos en la calificación del WPS ya que dichas juntas no tenían discontinuidades. Con este dato se compara las probetas con discontinuidades y se verificó la tendencia de disminución de resistencia al variar el tamaño de los poros.
Los resultados obtenidos en los ensayos destructivos de tracción se verificaron, validaron y extrapolaron mediante simulaciones. Para validar los resultados de la simulación, inicialmente se utilizaron las simulaciones con los mismos tamaños de las discontinuidades con los que se hicieron los ensayos experimentales de tracción. Una vez validados los resultados se simulan probetas con más dimensiones de discontinuidades (poros) en el cordón de soldadura para obtener curvas con líneas de tendencia.
Para realizar las simulaciones se utilizó el Software ANSYS Workbench 16.1, en donde se planteó un modelo de análisis dinámico explicito mediante la plataforma LS-DYNA. El procedimiento seguido fue el siguiente:
El problema se ha definido como la elaboración similar al ensayo de tracción experimental mediante ANSYS, el pre-proceso consta de varios pasos, entre ellos:
La definición de geometría, tanto de la probeta como del poro en el cordón de soldadura, imitando su forma y dimensiones a las probetas físicas. Se utiliza el software Solidworks, figura 6.
Definición de malla: para ensayos de esfuerzo axial, se manejan elementos tetraedros de 10 nodos de tamaño 1 mm. En la probeta total (el recurso computacional es limitado). De acuerdo a estudios realizados previamente por autores para análisis de estado de tensiones en cuerpos con cargas uniaxiales se utilizan mallas con elementos tetraédricos de 10 nodos o hexaedros de 20 nodos [14].
El uso de análisis de elementos finitos (ANSYS) para evaluar y simular procedimientos de soldadura con presencia de imperfecciones, ha sido utilizado exitosamente con aleaciones de aluminio, titanio y acero [15, 16] figura 7. Definición del modelo físico: como el material seleccionado para el tema de investigación es un acero estructural se considera los siguientes parámetros principales: comportamiento bilineal isotrópico, esfuerzo de fluencia de 248,21 MPa (36000 psi), módulo tangente de 1,45E9 de acuerdo con la base de datos de ANSYS 16.1.
Este programa presenta la facilidad de reproducir la probeta con el cordón de soldadura y su discontinuidad, aproximándose lo más cerca a la realidad. Finalmente, para simular los ensayos de tracción se considera el funcionamiento de la Máquina Universal que tiene un cabezal fijo y un cabezal móvil. Para ello se ha introducido como condiciones de contorno un soporte fijo en un extremo de la probeta y un desplazamiento móvil al otro extremo con una magnitud sobredimensionada de 50 mm para lograr identificar visualmente la fractura de las muestras. El solver es LSDYNA a partir del documento generado en Ansys Workbench, y la visualización de resultados en LS-Prepost a fin de restringir recurso computacional.
Resultados y Discusión
La identificación de fases en el acero ASTM A 36 devuelve los siguientes resultados, figura 8:
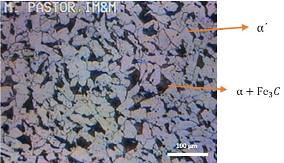
Fuente: autores
Fig. 8 Microestructura del acero ASTM A 36. El componente blanco es ferrita proeutectoide; el componente oscuro es perlita. (Decapante: 2% nital; amplificación 222X.).
Los granos claros son ferrita proeutectoide que se han formado sobre la temperatura eutectoide y el área oscura representa la perlita laminar, una mezcla fina de ferrita eutectoide y carburo de hierro o cementita (Fe3C). Típico de un acero hipoeutectoide con bajo a medio porcentaje de carbono, utilizado principalmente para el campo estructural. La fotomicrografía tiene medidas de 802,02x 598,38 micras, obteniendo un área de 479 912,7276 µm2. El área de la perlita (parte de color negro), es igual a 149 013,06 µm2. Con la ayuda del software ImageJ, el área total y el área de la perlita se determinó el área de la ferrita proeutectoide, y con ello sus porcentajes correspondientes. Mediante el método de áreas se ha determinado un porcentaje de perlita del 31,05 % y un porcentaje de ferrita proeutectoide del 68,95 %. Según la ecuación 1 el porcentaje en peso de carbono de la placa es de 0,26 % correspondiente a un acero hipoeutectoide.
Con este resultado se comprueba que las fases presentes y el porcentaje de carbono corresponden a que el acero adquirido es un acero estructural ASTM A 36. Además, obteniendo un valor promedio de esfuerzo último a la tracción de 65 565 psi de acuerdo con el informe técnico del LAEV (Laboratorio de análisis de esfuerzos y vibraciones de la Escuela Politécnica Nacional).
La tabla 3 muestra los resultados de los ensayos físicos en el laboratorio. Se puede observar que los poros de 2 y 3 mm producen una disminución en la resistencia a la tracción de apenas el 1 y 2 %, respectivamente respecto al esfuerzo último a tracción del acero estructural (65,5 ksi). Estas caídas podrían considerarse como nulas cuando se presenta un poro en el cordón de soldadura (El alcance de este trabajo es de una discontinuidad en el cordón de soldadura). Mientras que, los poros de 4 mm producen una reducción del 9 % que ya es considerable. Además, en todos los ensayos se tiene un coeficiente de variación menor al 1 % que indica su gran confiabilidad. La nomenclatura utilizada para la identificación de las probetas es POROX-TY, donde X significa el diámetro en mm del poro, T significa tracción y Y el número de probeta correspondiente a cada diámetro de poro.
Tabla 3 Resultados de los ensayos de tracción. Fuente: autores
Identificación | Ancho promedio (mm) | Espesor Promedio (mm) | Carga máxima registrada (N) | Resistencia a la tracción (MPa) | Resistencia promedio (MPa) | Coeficiente de Variación (%) |
---|---|---|---|---|---|---|
Poro2-T1 | 25,61 | 11,75 | 134443 | 446,8 | 446,1 | 0,58 |
Poro2-T2 | 25,91 | 11,98 | 139323 | 448,8 | ||
Poro2-T3 | 25,70 | 12,04 | 138033 | 446,1 | ||
Poro2-T4 | 25,67 | 11,63 | 132148 | 442,6 | ||
Poro3-T1 | 26,17 | 12,01 | 139776 | 444,7 | 444,2 | 0,15 |
Poro3-T2 | 25,78 | 11,46 | 130978 | 443,3 | ||
Poro3-T3 | 26,11 | 12,15 | 140862 | 444,0 | ||
Poro3-T4 | 26,19 | 11,73 | 136618 | 444,7 | ||
Poro4-T1 | 26,03 | 11,99 | 128465 | 411,6 | 409,9 | 0,64 |
Poro4-T2 | 26,15 | 11,69 | 125831 | 411,6 | ||
Poro4-T3 | 25,71 | 11,79 | 123100 | 406,1 | ||
Poro4-T4 | 26,05 | 12,04 | 128669 | 410,2 |
Las probetas con poros de 2 y 3 mm fallaron en el material base, mientras que, las probetas con poros de 4 mm fallaron en la junta soldada. Esto, juntamente con la disminución del 9 % de la resistencia, se demuestra que los poros de 4 mm generan una concentración de esfuerzos significativa. En la práctica es muy común encontrar poros con diámetros al azar, pero en comparación con la Norma API 1104 un poro de 4 mm es ya considerado como un defecto.
La figura 9 muestra un ejemplo de fractura, en las simulaciones de los poros con diámetros 6 y 3 mm (0,24” y 0,12”). En el cordón de soldadura (las primeras dos imágenes son de 6 mm de diámetro de poro)
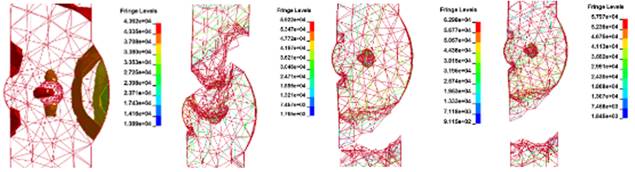
Fuente: autores
Fig. 9 Fractura en la simulación realizada a las probetas con porosidades de 6 y 3 mm respectivamente.
En la figura 9 se observa que los poros de 6 mm se convierten en concentradores de esfuerzo, comportándose como iniciadores de la fractura en la probeta. Por el contrario, el poro de diámetro 3 mm, se aprecia que la fractura inicia y se propaga en el material base (en el cambio de sección entre el material base y el refuerzo de soldadura). El modelo utilizado es el de modo de apertura, en el cual las caras de la discontinuidad se separan paralelamente entre sí, se supone que en este modo sólo se desarrollan tensiones de tracción.
En la figura 10 se considera la comparación entre el esfuerzo ultimo experimental vs simulación realizada a las probetas con poros proporcionado por el software LS-PrePost4.2 (BETA) para las diferentes dimensiones de las porosidades simuladas.

Fuente: autores
Fig. 10 Diagrama esfuerzo-deformación de la simulación realizada a las probetas con poros.
Los resultados obtenidos en la simulación y los del ensayo de tracción son muy similares. Además, se puede observar que el porcentaje de error entre la simulación y el ensayo de tracción es menor al 3 % de acuerdo con la tabla 4. Con estos resultados se puede aseverar que los valores obtenidos en la simulación son válidos y pueden ser extrapolados a distintos tamaños de poros, siempre y cuando se mantengan las condiciones ingresadas para la simulación.
Tabla 4 Comparación de los esfuerzos últimos a la tracción y % de error. Fuente: autores
Dimensión del defecto (mm) | Esfuerzo a tracción último experimental (MPa) | Esfuerzo a tracción ultimo simulación (MPa) | Porcentaje de error % |
---|---|---|---|
2 | 446,77 | 436,41 | 2,32 |
3 | 444,91 | 437,10 | 1,75 |
4 | 410,52 | 415,01 | 1,09 |
6 | 372,19 | ||
8 | 339,74 |
En la figura 11 se muestra la línea de tendencia que tiene el esfuerzo último en función del diámetro de los poros. La línea de tendencia tiene un valor de coeficiente de determinación R2 de aproximadamente 0,99. Al ser este valor cercano a 1, se puede afirmar que los diámetros de los poros son inversamente proporcionales a la resistencia a la tracción. También se puede evaluar la ecuación que predeciría la caída de la resistencia en función del tamaño de los poros, se muestra la ecuación de la resistencia a la tracción última en MPa en función del diámetro de los poros en milímetros. Los poros de 2 mm de diámetro no presentan una concentración de esfuerzo significativo, y los poros mayores a 8 mm no es común encontrar en soldaduras de placas de espesor de 12,7 mm (0,5”).
Conclusiones
Se obtuvieron poros de soldadura descritos en la Norma API 1104 en forma experimental de distintas dimensiones mediante la inclusión de cerámicos (óxidos de alúmina), verificando su tamaño y geometría.
Fue verificada la ausencia de discontinuidades externas mediante inspección visual y discontinuidades internas mediante radiografía industrial.
La línea de tendencia demostró que si se supera ligeramente el tamaño del defecto considerado en la norma API 1104 la variación en la resistencia a la tracción será mínima. Por ejemplo, un poro de 4 mm produce una caída en la resistencia de apenas 5 % (esto con respecto a los resultados de simulaciones). Este resultado permitiría que un fiscalizador decida si se procede o no a reparar un cordón de soldadura.