Introducción
El proceso mecánico dinámico funcional que se manifiesta en las turbinas a vapor de 100 MW de potencia de generación eléctrica, presentan un carácter aleatorio, lo que los convierte en un fenómeno complejo de estudiar y cuantificar. Para identificar y comprender cuáles parámetros síntomas tienen mayor influencia en la variabilidad del comportamiento mecánico dinámico funcional de las turbinas a vapor, es necesario el análisis integrado de parámetros síntomas de la turbina, a partir de métodos como la modelación matemática y estadística. Una de las técnicas recomendadas es un modelo estadístico basado en la técnica de análisis de componentes principales la cual permitirá la determinación de los parámetros síntomas con mayor influencia en la variabilidad del proceso mecánico dinámico funcional las turbinas a vapor de 100 MW. El empleo de la modelación estadística a partir de diferentes técnicas se ha evidenciado en diversos estudios de investigación que se relacionan a continuación:
El análisis de componentes principales (PCA, Principal Component Analysis) es aplicado en este trabajo LI, Wei; et al [1] para detectar la condición del sensor monitor, en una central nuclear (NPP, Nuclear Power Plant). Para estimar la detectabilidad de fallo del modelo PCA propuesto, se calculan en el modelo las zonas de poca detección de sensores. Entonces la habilidad de diagnóstico del modelo PCA es más específica y los resultados de diagnóstico son más creíbles y fidedignos.
Y. Cardenas Escorcia, et al [2], describen la combinación de técnicas estadísticas y modelos matemáticos para desarrollar un sistema de detección de fallas en un motor de gas natural de 2 MW bajo condiciones reales de operación. El objetivo principal de este trabajo es integrar dos enfoques para relacionar los fallos con los cambios de los valores medios termodinámicos del sistema, ayudando a mantener el motor en condiciones óptimas de funcionamiento en términos de confiabilidad. El Análisis de Componentes Principales (PCA), una técnica estadística multivariante de detección de fallas, se utilizó para analizar los datos históricos del motor a gas para detectar condiciones anormales de operación, por medio de indicadores estadísticos tales como el Error de Predicción Cuadrado (SPE, Square Prediction Error) y T 2 de Hotelling.
Este trabajo [3] propone un esquema de detección y localización de fallas en los actuadores de un vehículo aéreo no tripulado (VANT) del tipo cuatrirrotor. Para ello, se considera un enfoque basado en datos haciendo uso de técnicas de aprendizaje de máquina. Primero, a través de una plataforma de vuelo de tipo giroscópica, se captan las vibraciones correspondientes a la orientación, posición angular y aceleración lineal cuando el vehículo se encuentra en vuelo estacionario en condiciones nominales. Estos datos se procesan mediante Análisis en Componentes Principales (PCA) para la extracción de características. Posteriormente, se induce una falla a los actuadores a través de un recorte en cada una de las hélices del VANT que ocasionan una reducción del empuje generado por los rotores. Estos datos se proyectan también al subespacio de componentes principales y se comparan con los datos nominales. Para discernir entre los datos nominales y los datos cuando el vehículo presenta falla, se emplea el estadístico T 2 de Hotelling.
Tripathi M, [4], el estudio mostrado se relaciona con el índice de Calidad del agua (WQI, Water Quality Index). Los datos inicialmente disponibles han sido procesados mediante la técnica de Análisis de Componentes Principales (PCA), lo cual permitió obtener la reducción del número de parámetros procesados de 28 a 9. Esto ha permitido hacer el proceso más eficiente y económicos lo cual permitió reducir drásticamente el tiempo, el costo y el esfuerzo de procesamiento. Se hizo necesario monitorear muestras para un gran número de parámetros.
Jiang Q, et al [5] presenta un estudio donde se desarrolla un análisis de correlación (LVCA) para lograr el monitoreo distribuido eficiente para los procesos a gran escala en plantas industriales. Los datos de proceso de una unidad local son primero proyectados en un subespacio variable latente dominante y un subespacio residual para caracterizar la correlación dentro de la unidad local. Entonces, el operador determina las variables de comunicación con unidades que tienen buenas perspectivas para monitorear la unidad local. Después, se realiza un análisis canónico de correlación entre las variables del subespacio dominante y de comunicación para caracterizar la correlación entre unidades. Finalmente, un monitor distribuido es establecido para cada unidad, lo cual considera la correlación dentro de la unidad local y la correlación entre unidades diferentes de operación
Este trabajo Jiang, Qingchao J, et al [6], propone un modelo PCA (Principal Component Analysis) paralela - (P-PCA - KPCA) KPCA (kernel principal component analysis) para modelar un algoritmo aleatorio (RA, Randomized Algorithm) relacionado con el plan de monitoreo y un algoritmo genético para la detección eficiente de fallos en un proceso con variables linealmente correlacionadas y no linealmente relacionadas. Ambas relaciones lineales y no lineales pueden existir entre las variables de proceso, y es imperativo monitorear un proceso con tales relaciones complicadas entre las variables. Sin embargo, el análisis de componentes principales individual (PCA) o la semilla PCA (KPCA) pueden caracterizar estas relaciones complicadas.
Khanzadeh, M, et al [7], presentan en este estudio el desarrollo de un acercamiento estadístico de control de proceso (SPC, Statistical process Control) para detectar el proceso de cambio, tan pronto como ocurra, basado en la distribución estadística predeterminada. Para abordar estos retos, el acercamiento principal multilineal de análisis de componentes principales (MPCA, multivariate principal component analysis) permite extraer las características dimensionales bajas y residuos
En este artículo Jui-Hung L, et al [8] se presenta un análisis de rendimiento de modelos predictivos para el módulo generador que puede ser utilizado como una referencia para la mejora en el sistema de monitoreo de condición usando turbinas de viento en un parque eólico en Taiwán. Con el generador siendo un componente crítico propenso para los fallos, es importante realizar análisis de datos sobre sus parámetros que podrían servir para monitoreo de condición. La característica innovadora principal en este trabajo es la conducta de análisis de rendimiento antes del desarrollo del sistema de monitoreo de condición
Este autor Beebe Ray. [9]. Trabaja un análisis sobre el monitoreo predictivo de bombas, la información requerida para llevar a cabo el mantenimiento predictivo y la necesidad de la compilación de datos para su análisis y procesamiento. El estudio y análisis conjunto de los datos procesados redundará en conocimiento sobre la condición de éstas bombas.
Este trabajo Liu J, et al [10] propone una ventana en movimiento recursivo para el análisis de componentes principales (MWRSPCA, Moving Window Recursive Sparse Principal Component Analysis) basado en el plan de monitoreo en línea de fallos de los procesos complicados de gran escala. La industria química tiene procesos cuyas características varían dinámicamente. Establece un modelo de análisis de componentes principales basado en las matrices del bloque de la ventana en movimiento para realizar el proceso de monitoreo simultaneo de un conjunto de datos que conforman el set modelo que entrena y actualiza el modelo de monitoreo en línea, de forma tal que el modelo de monitoreo de proceso tenga una fuerte adaptabilidad para procesar dichas variables.
En la literatura consultada no consta la publicación de un modelo estadístico matemático que utilice un modelo estadístico basado en la técnica de análisis de componentes principales como método para identificar los parámetros que mayor influencia tienen en la variabilidad del comportamiento mecánico dinámico funcional de las turbinas a vapor de 100 MW de potencia.
La investigación que se realizó en este trabajo tuvo como objetivo el análisis del comportamiento mecánico dinámico funcional en turbinas a vapor de 100 MW de potencia de generación eléctrica, a partir de un modelo estadístico basado en la técnica de análisis de componentes principales como método para la reducción de dimensionalidad y como vía para identificar los parámetros que mayor influencia tienen en la variabilidad del comportamiento de las turbinas a vapor de 100 MW.
Como principal resultado se obtuvo un modelo estadístico matemático basado en la técnica de análisis de componentes principales, para el análisis del comportamiento mecánico dinámico funcional de turbinas a vapor de 100 MW, obteniéndose la reducción dimensional del problema original a partir de la obtención de las componentes principales y la determinación de los parámetros síntomas con mayor influencia en la variabilidad del proceso, por lo que se puede aseverar la factibilidad del modelo empleado en las turbinas de 100 MW.
Métodos
En esta investigación se emplearon las bases de datos que genera el sistema de monitoreado on line instalado en las turbinas a vapor de 100 MW de las centrales termoeléctricas.
El método empleado fue crear un modelo estadístico basado en la técnica de análisis de componentes principales [1, 2, 3], para el análisis del comportamiento mecánico dinámico funcional de la turbina a vapor de 100. Este modelo consiste en discriminar, de la población de datos, cuáles parámetros son síntomas de comportamiento, para posteriormente obtener una muestra de datos de trabajo a partir de la cual, se crea una muestra de datos de referencia donde será aplicado el modelo ACP.
En las centrales termoeléctricas se emplean diferentes procedimientos y técnicas para la evaluación del comportamiento mecánico dinámico funcional de turbinas a vapor de 100 MW, sin embargo uno de los problemas fundamentales es la dificultad del análisis integrado de los parámetros de proceso y tecnológicos. Se estudió la integración de parámetros síntomas [4] de la condición [5, 6] de la turbina a partir del análisis integrado de parámetros de proceso y tecnológicos, como una vía para la determinación de la condición de la turbina, definiéndose cuáles parámetros son representativos de la condición de la turbina, con la consiguiente reducción de dimensionalidad.
El control del proceso de funcionamiento y operación [7] de una unidad de 100 MW se efectuó a partir del monitoreado on line[8, 9, 10] de aproximadamente 2900 parámetros de proceso, correspondiendo a la turbina y a los sistemas tecnológicos auxiliares asociados a ésta, alrededor de 250 parámetros. Se valoró considerar que, de éstos 250 parámetros, sólo 165 tienen una significación y relación más estrecha con el proceso funcional y operativo de la turbina, mientras que para la turbina tomada como referencia, de estas 165 serán analizadas sólo 136 parámetros, teniendo en cuenta las recomendaciones de los especialistas en diagnóstico, en mantenimiento, en automática, en operación y en inspección de turbinas y basado en la experiencia cognoscitiva del trabajo con ésta turbina y de las recomendaciones del fabricante.
Para establecer el alcance del modelo ACP se tendrán en cuenta las siguientes definiciones:
Parámetro síntoma: variable sensible, fiable y medible cuyo cambio durante el proceso tecnológico, caracteriza el comportamiento o condición de la turbina
Variable sensible, fiable y medible: sensible a los cambios del proceso, fiable por la evidencia de que el valor medido represente la realidad física del cambio del proceso y medible por la posibilidad física real y viable de la medición de la variable. El detrimento de la sensibilidad y fiabilidad del valor medido de la variable y por ende su utilidad, estará influenciada por las condiciones de instalación, explotación, calibración y mantenimiento de la automática de los sistema de monitoreado instalados en las turbinas, pero no es condición que le reste el carácter de variable sensible y fiable
Variabilidad de los valores de los parámetros síntomas: variabilidad de los valores estadísticos de primer y segundo orden (media y la varianza) de las variables de proceso, tecnológicos o dinámicos que constituyen síntomas del comportamiento mecánico dinámico funcional de la turbina
Variabilidad del proceso: variabilidad de los valores de los parámetros síntomas como resultado actual del proceso funcional
Tiempo de explotación entre mantenimientos: es el tiempo de operación de la turbina que media entre cada parada para su reparación o mantenimiento
Período de tiempo de operación normal entre mantenimientos: es el período de tiempo de funcionamiento durante el cual, la turbina mantiene la condición o desempeño esperado, indicado por el estándar de operación de los parámetros operacionales medibles
Dimensionalidad: conjunto de espacios muéstrales formado por las observaciones de cada variable analizada, donde el conjunto de observaciones de cada variable implica una dimensión
Reducción de dimensionalidad: transformaciones realizadas a conjuntos de variables que permitan reducir la cantidad de dimensiones (variables) a analizar [4]
Muestra de datos de referencia: conjunto de datos de los parámetros síntomas de proceso (grupo de instancias de medición para todas las variables, medidas en el mismo instante de tiempo) seleccionadas de una misma fuente, considerada referencia del comportamiento de la variabilidad del proceso durante el estado estable estacionario de funcionamiento de la turbina, en el período de explotación entre mantenimiento, objeto de estudio
Actualización del modelo ACP: durante el período de operación considerado volver a calcular la media, covarianza y componentes principales, incluyendo el número de componentes que deberán ser retenidas para otra muestra de datos de referencia [10]
Actualización de la muestra de datos de referencia: obtener una muestra de datos de referencia nueva, para otro grupo de instancias dentro del período de tiempo objeto de estudio, partiendo de una muestra de datos de trabajo
Parámetros síntomas que caracterizan el comportamiento mecánico dinámico funcional
Se establecen como parámetros síntomas que caracterizan y denotan condición de las turbinas a vapor de 100 MW las siguientes:
Temperatura de metales (cilindro, cojinetes, tuberías)
Temperatura, presión y flujo de fluidos (suministro, extracción, drenaje, escape)
Longitud (expansión, posición (axial) de cilindro, rotor)
Consumo (fluidos y gases)
Condiciones (vapor vivo y recalentado)
Vibración y ruido
Velocidad de rotación, posición angular y torque
Potencia, generación y vacío
Las mismas constituyen invariantes para las turbinas a vapor de 100 MW, sin embargo debe tenerse en cuenta que aunque los parámetros característicos considerados como síntomas de comportamiento son los mismos en series de máquinas iguales, aún en máquinas idénticas, los mismos parámetros pueden o no comportarse como síntomas sensibles y fiables de los cambios en el comportamiento mecánico dinámico funcional que denoten condición o estado [3, 4, 5], debido a que están presentes diferencias en cuanto a edad técnica, condiciones de montaje, condiciones y tiempo de explotación entre cada reparación, materiales empleados en las piezas de repuestos y otros recursos, calidad de las intervenciones de mantenimiento realizadas, calidad de fabricación de componentes y de las modificaciones en el diseño.
Teniendo en cuenta las recomendaciones de los especialistas y basados en el comportamiento histórico de la turbina, la experiencia cognoscitiva del trabajo con ésta turbina por parte de los especialistas y de las recomendaciones del fabricante, pueden ser identificadas como parámetros sensibles, fiables y medibles, cuyo cambio en el valor de sus lecturas representan síntomas asociados a cambios en el comportamiento mecánico dinámico funcional, los cuales denotan condición o estado de la turbina, de los 136 parámetros del proceso se muestran 34 en la tabla 1. Algunos de estos parámetros involucran más de una posición en la turbina, como por ejemplo: Temperatura metal Babbitt chumacera 1 a la 7, lado regulador y generador.
Tabla 1 Parámetros síntomas del comportamiento mecánico dinámico funcional de la turbina analizada. Fuente: autores
Temperatura vapor vivo entrada válvula cuello CAP. Presión vapor vivo entrada CAP. Flujo vapor vivo entrada válvula cuello CAP. Presión vapor vivo salida válvula principal CAP. Temperatura vapor vivo entrada válvula principal CAP. Presión vapor salida CAP “A” y “B”. Temperatura vapor salida CAP “A” y “B”. Presión vapor recalentado entrada CMP. Temperatura vapor recalentado entrada “A” y “B” CMP. Temperatura vapor escape CBP. Temperatura vapor sellos alta y baja presión. Presión vapor sellos alta y baja presión. Temperatura aceite lubricación antes del enfriador. Temperatura aceite lubricación salida enfriador. Presión aceite lubricación sistema regulación. Presión aceite lubricación antes del enfriador. Presión aceite lubricación línea protección Temperatura metal Babbitt chumacera 1 a la 7, lado regulador y generador. Temperatura metal Babbitt tacones trabajo 1 al 8 (lado generador) chumacera 2. |
Temperatura metal Babbitt tacones no trabajo 1 al 8 (lado regulador) chumacera 2. Vacío condensador. Nivel de condensado en el condensador. Flujo condensado sección “A” y “B” condensador. Temperatura agua mar entrada y salida sección “A” y “B” condensador. Potencia (carga) activa generador (MW) MICRONET revoluciones turbina (rpm) Potencia (carga) reactiva generador (MVar) Frecuencia de rotación (cpm) Generación (MVar) Temperatura aceite lubricación salida chumacera 1 a la 7. Temperatura aceite cojinete axial chumacera 2 lado alta y baja presión. Temperatura metal cuerpo interior y exterior parte superior e inferior CAP, CMP y CBP, lado regulador, superior medio y lado generador. Diferencia temperatura metal exterior e interior entre parte superior e inferior cuerpo CAP, CMP y CBP, lado regulador, lado medio y lado generador. Temperatura vapor extracción 1 a la 8 |
Modelo grupal por conjunto mecánico de la turbina
La turbina será modelada en base a tres conjuntos mecánicos interconectados entre sí:
Estos modelos grupales relacionan los elementos mecánicos fundamentales de cada conjunto representado por el cilindro, rotor, chumaceras y los sistemas tecnológicos auxiliares relacionados con cada conjunto. Partiendo de los parámetros síntomas de proceso para ésta turbina, relacionadas en la tabla 1, el modelo grupal de análisis por conjunto mecánico quedó definido como la agrupación de parámetros síntomas que caracterizan el comportamiento mecánico dinámico funcional de cada conjunto mecánico, según se muestra en la tabla 2.
Tabla 2 Modelo grupal de parámetros por conjunto mecánico (cilindro - rotor - chumaceras) de la turbina de 100 MW analizada. Fuente: autores
CAP_42-parámetros | CMP_28- parámetros | CBP_23-parámetros |
---|---|---|
Potencia activa generador Micronet revoluciones turbina Temp. Vapor Vivo Entrada Válvula Cuello Presión Vapor Vivo Entrada Turbina Flujo de Vapor Vivo Presión Vapor Vivo después Válvula Principal Temp. Vapor Vivo Entrada Válvula Principal Temp. Vapor Salida CAP A y B Presión Vapor Salida CAP Presión Vapor Sellos AP Temp. Vapor Sellos AP Temp. vapor extracción 1 Temp. Babbit Tacón Trabajo 1 al 8 Temp. Babbit Tacón No Trabajo 1 al 8 Temp. Ch 1 lado regulador y generador Temp. Ch 2 lado regulador y generador Temp. Aceite Salida Ch 1 Temp. Aceite Salida Ch 2 Temp. Aceite Cojinete Axial lado AP Temp. Aceite Cojinete Axial lado MP Temp. Aceite antes Enfriadores Temp. Aceite después Enfriadores Presión de Aceite Lubricación Presión Aceite Línea Protección Presión de Aceite Regulación |
Potencia activa generador Micronet revoluciones turbina Presión Vapor Entrada CMP Temp. Vapor Recalentado Entrada CMP A y B Presión Vapor Sellos AP y BP Temp. Vapor Sellos AP y BP Temp. vapor extracción 2 a la 7 Temp. Ch 2 lado regulador y generador Temp. Ch 3 lado regulador y generador Temp. Aceite Salida Ch 2 Temp. Aceite Salida Ch 3 Temp. Aceite Cojinete Axial lado AP Temp. Aceite Cojinete Axial lado MP Temp. Aceite antes Enfriadores Temp. Aceite después Enfriadores Presión de Aceite Lubricación Presión Aceite Línea Protección Presión de Aceite Regulación |
Potencia activa generador Micronet revoluciones turbina Vacío en condensador Nivel del Condensador Temp. Vapor Escape Temp. Agua Mar Entrada Condensado A y B Temp. Agua Mar Salida Condensado A y B Presión Vapor Sellos BP Temp. Vapor Sellos BP Temp. vapor extracción 8 Temp. Ch 4 lado regulador y generador Temp. Ch 5 lado regulador y generador Temp. Aceite Salida Ch 4 Temp. Aceite Salida Ch 5 Temp. Aceite antes Enfriadores Temp. Aceite después Enfriadores Presión de Aceite Lubricación Presión Aceite Línea Protección Presión de Aceite Regulación |
Leyenda: Temp., temperatura. Ch, chumacera. AP, alta presión. MP, media presión. BP, baja presión. CAP, cilindro de alta presión. CMP, cilindro de media presión. CBP, cilindro de baja presión.
Es necesario aclarar que, en la tabla 2 se muestran reflejados 42, 28 y 23 parámetros respectivamente, pero en la práctica son muchos más, debido a que algunos de estos parámetros involucran más de una posición en la turbina, como por ejemplo: Temp. Babbit Tacón Trabajo 1 al 8.
Para conformar el modelo grupal presentado en la tabla 2 se tuvo en cuenta, las recomendaciones de los especialistas en diagnóstico, en mantenimiento, en automática, en operación y en inspección de turbinas, tomando como base el comportamiento histórico de la turbina, la experiencia cognoscitiva del trabajo con ésta turbina por parte de los especialistas y de las recomendaciones del fabricante. El resultado de este modelo tuvo en cuenta la disponibilidad y calidad de datos de los parámetros que finalmente resultó factible para ser modelado, durante el período analizado, por lo tanto de 136 parámetros síntomas mostrados en la tabla 1 pudieron ser utilizadas sólo 76 parámetros síntomas de los cuales se nutrieron los modelos grupales para cada conjunto mostrados en la tabla 2. De no haber existido inconvenientes en cuanto a disponibilidad y calidad de datos, el resultado de la tabla 2 hubiera coincidido con el obtenido en la tabla 1, en cuanto a cantidad de parámetros síntomas analizados.
Obtención de la muestras de datos de trabajo y de referencia para la aplicación del modelo ACP
Obtención de la muestra de datos de trabajo (pre-procesamiento)
Para la turbina tomada como referencia, en el período de operación comprendido entre el 5 de mayo del 2008 al 23 de enero del 2009, se obtuvo una muestra de datos observada de la población de 49391 instancias de medición para 228 atributos de proceso (parámetros), con una secuencia de captura de medición de cinco minutos, de las cuales fueron desechadas aquellas que no están asociadas con el funcionamiento de la turbina y aquellas que no son síntomas de comportamiento de la turbina. El acondicionamiento de la muestra de datos de trabajo observada de la población resultó en 45224 instancias de medición cotejadas para 76 atributos 45224-76, las cuales se corresponden con los parámetros que nutrieron los modelos grupales para cada conjunto mecánico, mostradas en la tabla 2 y que a su vez se corresponden con los parámetros declarados como síntomas en la tabla 1.
Para obtener la muestra de datos de trabajo fue necesario tener en cuenta el cumplimiento de los requerimientos para la instalación, calibración, mantenimiento y verificación de la instrumentación, así como del proceso de lectura y registro de datos, ya que cualquier deterioro, imperfección o fallo de la automática invalida las condiciones o inferencias que se realicen sobre los datos obtenidos de estos sistemas de monitoreado, durante el proceso de aplicación del modelo ACP.
Obtención de la muestra de datos de referencia (procesamiento)
La selección, limpieza y transformación de la muestra de datos de trabajo 45224-76, se basó en detectar los valores perdidos, erróneos, nulos y anómalos, obteniéndose una muestra de referencia 43656-76. La obtención de la muestra de datos de referencia para el modelo ACP, no tiene que cumplir con la normalidad en la distribución del conjunto de datos de los atributos, ni cumplir, con que el conjunto de datos de la muestra de referencia represente una condición normal estándar de variabilidad del proceso de la turbina (aunque pudiera tomarse ésta como referencia para otros estudios), sin embargo, no tendría sentido alguno (ni aplicación técnica), identificar los parámetros que mayor importancia y aporte tienen en la variabilidad del proceso, en los períodos de tiempo de funcionamiento en los que las instancias de medición sobrepasen los valores límites de operación segura y protección tecnológica de la turbina, por lo que ésta fue una condición para la selección de las instancias de medición que conformarán la muestra de datos de referencia.
La muestra de datos de referencia no requerió de entrenamiento ni de la verificación del volumen de datos (cantidad de instancias de medición) necesarios para conformar la muestra de datos de referencia. La verificación de que los parámetros originales hayan tenido algún grado de correlación, no constituye una condición para la aplicación del modelo ACP. Dado que el modelo ACP es invariante en el tiempo, se requierió como condición la consecuente actualización de la muestra de referencia dentro del período de explotación entre mantenimientos.
Resultados y Discusión
Aplicación del modelo ACP al modelo grupal CAP
La identificación de los parámetros que reportan mayor información sobre la variabilidad del comportamiento mecánico dinámico funcional de la turbina, se realizó en el mes de enero (posterior a un mantenimiento parcial realizado con fecha del 04/11/08 al 08/01/09 y una actualización del modelo ACP en el mismo mes de enero, por lo que para su análisis, se reducirá la muestra de referencia 43656-76 a 3209 instancias de medición que conforman éste período de operación 08/01/09 al 23/01/09, y ésta a su vez será dividida en dos períodos: 1914 instancias al período 08/01/09 al 15/01/09 y 1295 instancias al período 16/01/09 al 23/01/09 (1ra y 2da quincena de enero). Esta identificación de parámetros será realizada sólo para el modelo grupal correspondiente al cilindro de alta presión CAP_1914-42 y CAP_1295-42, siendo igual la forma de proceder para los otros dos modelos grupales expuestos en la tabla 2.
Teniendo en cuenta los resultados obtenidos en corridas de prueba para éste mismo modelo, se reducirá el número de parámetros a considerar, mostrándose en la tabla 3 los nueve parámetros que no serán considerados en los análisis posteriores y los 33 parámetros que sí serán considerados, quedando configurado el modelo grupal CAP como sigue: CAP_1914-33 y CAP_1295-33.
Tabla 3 Parámetros considerados y no considerados en el análisis del modelo grupal CAP. Fuente: autores
Modelo CAP_42 9 parámetros no considerados | Modelo CAP_33 33 parámetros considerados |
---|---|
Temp. Vapor Vivo Entrada Válvula Cuello Presión Vapor Vivo Entrada Turbina Flujo de Vapor Vivo -Presión Vapor Vivo después Válvula Principal Temp. Vapor Vivo Entrada Válvula Principal Temp. Vapor Salida CAP A y B Presión Vapor Salida CAP Temp. Aceite antes Enfriadores |
Potencia activa generador Micronet revoluciones turbina Presión Vapor Sellos AP Temp. Vapor Sellos AP Temp. vapor extracción 1 Temp. Babbit Tacón Trabajo 1 al 8 Temp. Babbit Tacón No Trabajo 1 al 8 Temp. Ch 1 lado regulador y generador Temp. Ch 2 lado regulador y generador Temp. Aceite Salida Ch 1 Temp. Aceite Salida Ch 2 Temp. Aceite Cojinete Axial lado AP Temp. Aceite Cojinete Axial lado MP Temp. Aceite después Enfriadores Presión de Aceite Lubricación Presión Aceite Línea Protección Presión de Aceite Regulación |
Leyenda: Temp., temperatura. Ch, chumacera. AP, alta presión. MP, media presión. CAP, cilindro de alta presión.
La obtención de los componentes principales se realizó de la siguiente forma:
Se calcularon 33 vectores propios (igual cantidad que la dimensión del problema) para el modelo grupal CAP, cuyas coordenadas son los coeficientes para transformar los atributos originales (parámetros) en los nuevos componentes.
Los valores propios (componentes) son ordenados de mayor a menor en función de la dirección de máxima variabilidad de la varianza capturada (según el vector propio asociado).
En la tabla 4 se muestran los valores propios calculados para cada componente, el porcentaje total de varianza capturada por cada valor propio, la suma acumulada de los valores propios y el porcentaje acumulado de la varianza total capturada por cada valor propio, para los modelos grupales CAP_1914-33 y CAP_1295-33 respectivamente.
Tabla 4 Valores propios de la matriz de correlación. Modelo CAP_1914-33 y CAP_1295-33. Fuente: autores
CAP_33 x 1914_enero1ra_08/01/09 al 15/01/09 | CAP_33 x 1295_enero2da_16/01/09 al 23/01/09 | ||||||||
---|---|---|---|---|---|---|---|---|---|
Valor propio | % Varianza total | Valor propio acumulado | Acumulado % | Valor propio | % Varianza total | Valor propio acumulado | Acumulado % | ||
1 | 12,7552199 | 38,6521815 | 12,7552199 | 38,6521815 | 1 | 11,6509357 | 35,3058657 | 11,6509357 | 35,3058657 |
2 | 5,10409589 | 15,4669572 | 17,8593158 | 54,1191387 | 2 | 6,16510672 | 18,6821416 | 17,8160424 | 53,9880073 |
3 | 4,05496982 | 12,2877873 | 21,9142856 | 66,4069261 | 3 | 5,00617190 | 15,1702179 | 22,8222143 | 69,1582252 |
4 | 2,46933696 | 7,48283928 | 24,3836226 | 73,8897653 | 4 | 2,22727744 | 6,74932557 | 25,0494917 | 75,9075507 |
5 | 1,66272625 | 5,0385644 | 26,0463488 | 78,9283297 | 5 | 1,83758516 | 5,56843987 | 26,8870769 | 81,4759906 |
6 | 1,11815153 | 3,38833797 | 27,1645003 | 82,3166677 | 6 | 1,37734568 | 4,17377480 | 28,2644226 | 85,6497654 |
7 | 1,05546906 | 3,1983911 | 28,2199694 | 85,5150588 | 7 | 1,08838659 | 3,29814120 | 29,3528092 | 88,9479066 |
8 | 1,01976950 | 3,09021061 | 29,2397389 | 88,6052694 | 8 | 0,82976432 | 2,51443733 | 30,1825735 | 91,4623439 |
9 | 0,92243744 | 2,79526498 | 30,1621764 | 91,4005344 | 9 | 0,59785359 | 1,81167754 | 30,7804271 | 93,2740215 |
10 | 0,56802925 | 1,72130075 | 30,7302056 | 93,1218351 | 10 | 0,4695185 | 1,42278333 | 31,2499456 | 94,6968048 |
11 | 0,51460931 | 1,55942216 | 31,2448149 | 94,6812573 | 11 | 0,42184186 | 1,27830867 | 31,6717874 | 95,9751135 |
12 | 0,47552011 | 1,44097002 | 31,7203350 | 96,1222273 | 12 | 0,33496000 | 1,01503030 | 32,0067474 | 96,9901438 |
13 | 0,30625348 | 0,92804084 | 32,0265885 | 97,0502682 | 13 | 0,22503981 | 0,68193882 | 32,2317872 | 97,6720826 |
14 | 0,22643522 | 0,68616732 | 32,2530237 | 97,7364355 | 14 | 0,19969640 | 0,60514060 | 32,4314836 | 98,2772232 |
15 | 0,17499969 | 0,53030208 | 32,4280234 | 98,2667376 | 15 | 0,14954681 | 0,45317215 | 32,5810305 | 98,7303953 |
16 | 0,12828454 | 0,38874104 | 32,5563079 | 98,6554786 | 16 | 0,08690932 | 0,26336159 | 32,6679398 | 98,9937569 |
17 | 0,11196029 | 0,33927362 | 32,6682682 | 98,9947522 | 17 | 0,07849810 | 0,23787303 | 32,7464379 | 99,2316299 |
18 | 0,08864167 | 0,26861112 | 32,7569099 | 99,2633633 | 18 | 0,05940086 | 0,18000260 | 32,8058387 | 99,4116325 |
19 | 0,05884345 | 0,17831347 | 32,8157533 | 99,4416768 | 19 | 0,03879842 | 0,11757096 | 32,8446372 | 99,5292035 |
20 | 0,04030917 | 0,12214901 | 32,8560625 | 99,5638258 | 20 | 0,03091756 | 0,09368957 | 32,8755547 | 99,6228931 |
21 | 0,03360612 | 0,10183672 | 32,8896686 | 99,6656625 | 21 | 0,02404817 | 0,07287324 | 32,8996029 | 99,6957663 |
22 | 0,02443781 | 0,07405396 | 32,9141064 | 99,7397165 | 22 | 0,02120583 | 0,06426010 | 32,9208087 | 99,7600264 |
23 | 0,02159847 | 0,06544992 | 32,9357049 | 99,8051664 | 23 | 0,01718371 | 0,05207186 | 32,9379924 | 99,8120983 |
24 | 0,01675205 | 0,05076378 | 32,9524570 | 99,8559302 | 24 | 0,01560789 | 0,04729663 | 32,9536003 | 99,8593949 |
25 | 0,01567301 | 0,04749398 | 32,9681300 | 99,9034242 | 25 | 0,01227795 | 0,03720590 | 32,9658783 | 99,8966008 |
26 | 0,00969827 | 0,02938869 | 32,9778282 | 99,9328129 | 26 | 0,01053668 | 0,03192933 | 32,9764149 | 99,9285301 |
27 | 0,00865410 | 0,02622455 | 32,9864824 | 99,9590374 | 27 | 0,01015051 | 0,03075913 | 32,9865655 | 99,9592893 |
28 | 0,00736598 | 0,02232114 | 32,9938483 | 99,9813586 | 28 | 0,00822537 | 0,02492537 | 32,9947908 | 99,9842146 |
29 | 0,00239569 | 0,00725967 | 32,9962440 | 99,9886182 | 29 | 0,00202672 | 0,00614158 | 32,9968175 | 99,9903562 |
30 | 0,00148870 | 0,00451121 | 32,9977327 | 99,9931294 | 30 | 0,00124877 | 0,00378415 | 32,9980663 | 99,9941404 |
31 | 0,00102608 | 0,00310933 | 32,9987588 | 99,9962388 | 31 | 0,00073856 | 0,00223805 | 32,9988049 | 99,9963784 |
32 | 0,00080388 | 0,00243600 | 32,9995627 | 99,9986748 | 32 | 0,00071070 | 0,00215362 | 32,9995156 | 99,9985320 |
33 | 0,00043732 | 0,00132522 | 33 | 100 | 33 | 0,00048443 | 0,00146797 | 33 | 100 |
Puede observarse que para ambos modelos (1ra y 2da quincena de enero) con sólo los primeros seis componentes de los 33 calculados, se captura más del 80 % de la varianza total que aportan los 33 parámetros originales, es decir, no hubo cambios significativos en la varianza total capturada por los primeros valores propios de ambos modelos, este hecho ejemplifica la reducción dimensional del problema o mejor dicho la determinación de la dimensión real del problema analizado. La selección de los componentes principales se realizó teniendo en cuenta los criterios, expuestos en. El primer cambio de pendiente evidente ocurre en el 6to y 5to componente, mientras que el segundo cambio de pendiente ocurre en el 9no y 8vo componente, para los modelos CAP_1914-33 y CAP_1295-33 respectivamente. En la figura 1 se grafican los componentes de este análisis. Se considerará para posteriores análisis los valores propios retenidos que explican hasta el 91 % de la varianza total capturada (8vo y 9no componentes principales respectivamente).
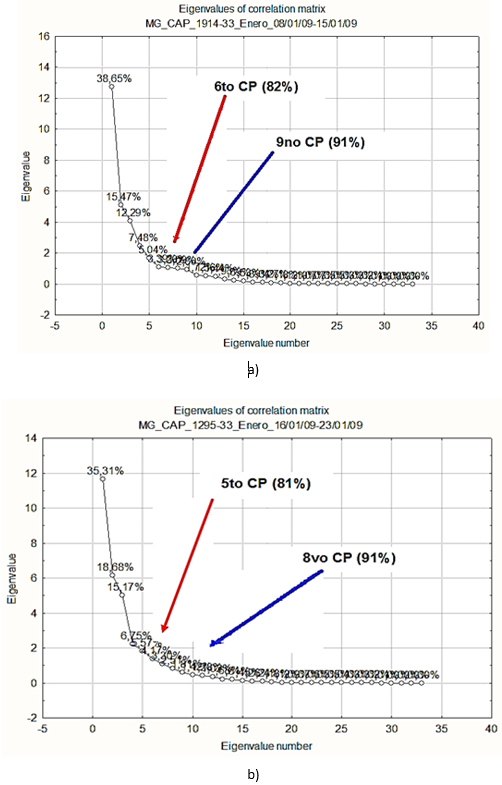
Fig. 1 Representación gráfica (screen plot) de los valores propios de cada componente: a) Modelo CAP_1914-33, b) Modelo CAP_1295-33.
La reducción de la dimensionalidad persigue obtener componentes en la dirección que explica la máxima varianza (variabilidad de los parámetros), por lo que los parámetros que mayor peso o aporte tengan en las primeras componentes principales retenidas, serán las de mayor importancia para ejercer su control y vigilancia dentro del período de explotación, al estar asociadas a causas del comportamiento del proceso. Por lo tanto, cambios en la estructura de correlación de estos parámetros se deberá a cambios en el comportamiento mecánico dinámico funcional de la turbina. Al no haber cambiado significativamente la dimensión del problema, puede presuponerse en primera instancia que la estructura de correlación entre los parámetros originales de ambos modelos grupales se mantiene con poco cambio.
Determinación de los parámetros síntomas con mayor influencia en la variabilidad del proceso
La determinación de los parámetros síntomas originales (correspondientes a los componentes principales seleccionados) que tendrán mayor variabilidad y por ende, mayor influencia, peso o representatividad en el comportamiento mecánico dinámico funcional de la turbina, podrán ser determinados a partir del cálculo de la contribución que cada parámetro realiza a cada componente principal (Variable contributions, based on correlations Spreadsheet).
Debido a que el análisis se basa en la matriz de correlación, las contribuciones de cada parámetro, son interpretadas como las correlaciones de los respectivos parámetros originales con cada uno de los componentes. La actualización requerida por el modelo ACP permite comparar el estado actual de variabilidad respecto al precedente (1ra y 2da quincena), donde los cambios en los valores de los parámetros que mayor aporte tuvieron a la varianza total (variabilidad del proceso), permitirá establecer, los parámetros que están sufriendo cambios en su variabilidad y su posterior asociación a una causa. Se puede observar en la tabla 5 los valores que representan la contribución que realiza (en cuanto a peso) cada variable original, referida a cada componente obtenido (expresada en porcentaje), para el modelo grupal CAP_1914-33 del período 08/01/09 al 15/01/09 y CAP_1295-33 del período 16/01/09 al 23/01/09 respectivamente. En la tabla 5 se muestran los parámetros que mayor influencia tienen en la variabilidad del proceso.
Tabla 5 Parámetros que mayor influencia tienen en la variabilidad del proceso. Fuente: autores
CAP_1914-33 | CAP_1295-33 | ||||
CP 1 | CP 2 | CP 1 | CP 2 | ||
Var1_Potencia activa generador | 6,75 | 0,60 | 7,84 | 0,27 | |
Var5_Temp. vapor extracción 1 | 5,06 | 0,80 | 7,78 | 0,25 | |
Var6_Temp. Babbit Tacón Trabajo 1 | 7,46 | 0,03 | 8,07 | 0,36 | |
Var7_Temp. Babbit Tacón Trabajo 2 | 7,26 | 1,05 | 7,79 | 0,80 | |
Var8_Temp. Babbit Tacón Trabajo 3 | 6,92 | 1,54 | 7,57 | 0,84 | |
Var9_Temp. Babbit Tacón Trabajo 4 | 6,41 | 2,12 | 7,97 | 0,37 | |
Var10_Temp. Babbit Tacón Trabajo 5 | 6,01 | 0,05 | 7,67 | 0,05 | |
Var13_Temp. Babbit Tacón Trabajo 8 | 6,02 | 2,61 | 5,78 | 0,06 | |
Var17_Temp. Babbit Tacón No Trabajo 4 | 5,09 | 3,20 | 1,87 | 10,75 | |
Var29_Temp. Aceite Cojinete Axial lado MP | 6,77 | 0,02 | 6,62 | 2,41 |
Leyenda: Temp., temperatura. MP, media presión. CAP, cilindro de alta presión.
Es notable que los mismos parámetros mantuvieran su importancia, comparando el modelo correspondiente a la 1ra quincena de enero respecto a la 2da, pero además es significativo que sólo tres de ellos disminuyeron su variabilidad mientras que el resto aumentaron. El nivel de importancia reflejado por cada parámetro en su contribución al componente principal viene dado porque son los parámetros que mejor expresan la captura de la variabilidad del proceso, dado por el grado de dispersión de los valores de la variable computada en su varianza. Por lo tanto esta variabilidad del proceso está asociada con el comportamiento del proceso de la turbina y constituye un resultado cualitativo para análisis posteriores de diagnóstico. El aporte de éstos parámetros pudiera ser considerado irrisorio e insignificante al observar fríamente su valor numérico, sin embargo es todo lo contrario.
El primer componente principal reúne la máxima variabilidad (dispersión) del proceso y los parámetros originales involucrados son los que mayor aporte tienen a esa dispersión y en cuanto a la cantidad aportada como valor numérico, debe notarse que son 33 parámetros originales los que están aportando a la dispersión, por lo tanto, el valor no puede ser elevado, si se tiene en cuenta que la turbina tomada como referencia recibió un mantenimiento parcial en fecha 04/11/08 al 08/01/09, que antecede a la fecha de análisis de ambos modelos grupales, además de que, un valor muy elevado de la variabilidad de un parámetro respecto a los demás, representaría una condición técnica o de operación asociada a parámetro en particular, al cual habría que prestarle atención.
Conclusiones
Se obtuvo la reducción dimensional del problema original a partir de la obtención de las componentes principales y la determinación de los parámetros síntomas con mayor influencia en la variabilidad del proceso.
Las componentes principales sintetizan el mayor porcentaje de la variabilidad del comportamiento mecánico dinámico funcional de la turbina, por lo que se identifican los parámetros síntomas originales (que forman parte de éstos componentes principales) que mayor variabilidad tienen durante el proceso.