INTRODUCCIÓN
Las averías o fallas en los tubos de las paredes de agua (pantallas) del horno y de los sobrecalentadores de la central termoeléctrica de Cienfuegos “Carlos Manuel de Céspedes”, aparecen reportadas desde el año 1980, es decir, casi desde el arranque de las unidades 3 y 4. Las fallas que se presentan pueden estar originadas por distintas causas: 1. Termofluencia. 2. Termofluencia en presencia del adelgazamiento de fabricación en la pared (Durante el doblado de los codos fundamentalmente). 3. termofluencia en presencia del adelgazamiento de la pared en presencia del fenómeno erosión - corrosión. (Durante la explotación). 4. Colapsación plástica. 5. Fatiga. Sin embargo, en estos más de 35 años en que vienen ocurriendo las fallas en los tubos mencionados no se ha logrado establecer y aplicar una metodología, que tomando en cuenta los parámetros geométricos constructivos de fabricación o de explotación como lo son: El adelgazamiento de los tubos durante el doblado en el caso de las curvas o el fenómeno de erosión corrosión durante la explotación, material, temperaturas, etc. que permita establecer un pronóstico de vida de los tubos, específicamente en este caso para la avería por termofluencia contemplando los aspectos mencionados, que conduzca al esclarecimiento de las verdaderas causas de las fallas, cuáles pueden ser controlables y cuáles no y por consiguiente a la aplicación de las medidas correctivas necesarias y que además contribuya a realizar una adecuada selección del material de los tubos a adquirir para la central. En el mismo se aspira a incorporar en la metodología ya creada por (Rivero, 2012), (Goytisolo, 2012), para la determinación del tiempo de vida útil de los tubos por termofluencia, la influencia en la misma del adelgazamiento inicial de la pared y la presencia de una razón de adelgazamiento en el tiempo, manteniendo para el cálculo de las tensiones la influencia de la temperatura en las propiedades físicas y mecánicas de los aceros y la diferencia de temperatura entre la superficie exterior e interior de los tubos. La Metodología así perfeccionada se aplicará al pronóstico de vida útil de los tubos de las calderas de la termoeléctrica de Cienfuegos (CMC) para los aceros AISI 210 A1 y AISI 213 T91 que se están investigando para analizar la influencia del adelgazamiento de la pared. El objetivo del presente trabajo es establecer una metodología de cálculo que permita pronosticar la vida útil por termofluencia en presencia o no del fenómeno de adelgazamiento de la pared en los tubos de las calderas.
MATERIALES Y MÉTODOS
2.1 Aspectos Microscópicos de las fracturas por termofluencia.
Un metal o aleación a temperatura ambiente, no sufre deformación plástica si un esfuerzo aplicado es menor que la tensión límite del material. Sin embargo, si la temperatura de estos materiales se aumenta, es posible que comiencen a deformarse plásticamente aún cuando los esfuerzos aplicados sea pequeños y finalmente fallará. Entonces, se dice que el material falló por termofluencia, la deformación plástica que sufre el material depende de la temperatura y del tiempo que la fuerza esté aplicada (Coltters, 2013). Por lo general, los tubos de calderas se rompen o se curvan debido al sobrecalentamiento de larga duración, en estas condiciones la temperatura del metal pude sobrepasar los límites de diseño durante días, semanas, meses o más tiempo. Debido a que el acero pierde mucha resistencia mecánica a temperaturas elevadas, las probabilidades de una rotura causada por la presión de trabajo interna aumentan a medida que se eleva la temperatura. En la Figura 1 se muestra un tramo de tubo averiado de las calderas de la termoeléctrica.
La Figura 2 muestra esquemáticamente un resumen de las etapas de la transformación de la microestructura de un material sometido a termofluencia según (Coltters, 2013).
La primera etapa, fluencia primaria, corresponde a una zona de velocidad de fluencia decreciente, es decir, la pendiente de la curva disminuye con el tiempo. Esto indica el hecho de que las transformaciones en la estructura cristalina, actúan para retardar los procesos de deformación.
La segunda etapa, fluencia secundaria, corresponde a un período de velocidad constante, como resultado de un equilibrio entre los procesos en competencia de endurecimiento por deformación y recuperación (o restauración). Durante esta etapa, los planos de deslizamiento se doblan desarrollando pliegues (kinks) y, eventualmente, resulta una estructura subgranular. Eventualmente, se alcanzará un punto en donde el aumento en la velocidad de termofluencia, causada por la elevación del esfuerzo, vencerá el endurecimiento por deformación (es decir, se desarrolla un proceso de ablandamiento, a velocidad mayor que el endurecimiento). En este punto comienza la última fase.
En la tercera etapa, fluencia terciaria se produce una aceleración de la velocidad de fluencia hasta la rotura final del tubo. Este tipo de rotura se denomina frecuentemente ruptura, y se produce debido a cambios microestructurales y/o cambios metalúrgicos; por ejemplo, la separación de los bordes de grano y la formación de fisuras internas, cavidades y huecos.
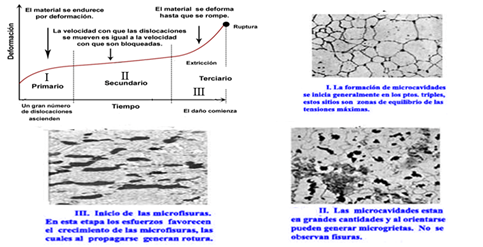
Figura 2 Cambios en la estructura debido a las tensiones actuantes, que favorecen el crecimiento de las microfisuras en la termofluencia.
2.2 Consideración de la diferencia de temperatura entre la superficie interior y exterior de la pared de los tubos en la magnitud de las tensiones.
En las metodologías descritas en (ASME, 2011), (Fujio, 2012) y (Maile y Klenk, 2012) para la estimación de la vida útil por termofluencia y otros tipos de falla en tubos, no se toma en cuenta la influencia de la diferencia de la temperatura Δt entre la superficie exterior e interior de la pared en la magnitud de las tensiones (Rivero, 2012). Según Jusmatulin (1990), para el cálculo de la tensión en la pared (ya sea de recipientes o de tubos) tomando en cuenta la diferencia de temperatura Δt entre la superficie exterior e interior de la pared del componente en cuestión, para calentamiento exterior, se tiene que (Ecuación 1, Ecuación 2, Ecuación 3, Ecuación 4, Ecuación 5):
Donde: ti=temperatura interior en ºC y te=temperatura exterior en ºC.
Donde
p presión interior en el tubo en MPa, E Módulo de Elasticidad del material del tubo en MPa, α Coeficiente de dilatación térmica del material del tubo en ºK-1, µ coeficiente de Poisson del material del tubo, D diámetro medio del tubo en mm, h espesor de la pared del tubo en mm, ε Relación entre el diámetro y el espesor del tubo, m1 y a1 son simplificaciones matemáticas para reducir la ecuación de la tensión.
Estas expresiones para el cálculo de la tensión en la pared de los tubos de las calderas fueron incorporadas en la Metodología de Pronóstico de la vida por termofluencia elaborada en el los trabajos de Rivero (2012) y Goytisolo (2012). Se hace necesario destacar que el hecho de que incorporar la diferencia de temperatura Δt en las expresiones de cálculo de las tensiones, juega un papel importante en el valor de las tensiones calculadas en comparación con el valor cuando no se considera la misma. Por otra parte hay que agregar que es muy importante disponer de datos de las propiedades físicas y mecánicas, tales como: E, α y µ en función de la temperatura de trabajo para el material en cuestión (Birger, 1975).
2.3 Predicción de la vida útil por fractura, por creep considerando la diferencia de temperatura de la pared para el Acero SA-210 A1 y el Acero SA-213 T91 (9% Cr - 1% Mo), sin considerar el adelgazamiento de la pared.
2.3.1 Datos de los tubos de la Central Termoeléctrica de Cienfuegos (CMC).
Los siguientes valores fueron tomados de los parámetros de trabajo de la central termoeléctrica, los cuales son los parámetros nominales dados por el fabricante de la misma, donde p es la presión de trabajo, D es el diámetro nominal y h es el espesor de la pared de dos tubos y sus valores son los siguientes:
p = 14,32 MPa, D = 58,60 mm, h = 4,90 mm
2.3.2 Composición química del acero actualmente utilizado en los tubos SA-210 A1.
Según las especificaciones técnicas, el material de los tubos actuales de las calderas de la termoeléctrica, es un acero de resistencia media que se corresponde con el acero en la (ASME, 2011): SA-210 A1. En el trabajo de (Rivero, 2012) se utiliza la nomenclatura acero AISI (American Iron and Steel Institute) y SAE (Society of Automotive Engineers): 210 A1. La composición química del acero SA-210 A1 es (Tabla 1):
Tabla 1 Composición química del acero SA-210 A1 de los tubos de calderas (% en masa)
0,27 | 0,93 | 0,048 | 0,058 | 0,10 (Mínimo) |
Las propiedades físicas fundamentales fueron ajustadas por el método de los mínimos cuadrados. Las ecuaciones (Ecuación 6, Ecuación 7, Ecuación 8) obtenidas en los ajustes son:
Para 293≤T≤873ºK
2.3.3 Composición química del acero SA-213 T91 (9% Cr - 1% Mo).
En el Evento Científico “Creep 2012” celebrado en Mayo 2012 en Kyoto Japón, resultando muy significativo que una gran parte de los trabajos presentados se referían al empleo del acero con 9 % de cromo, (Fujio, 2012). (Maile y Klenk, 2012), (Mastaka, 2012), (Mayr, 2012), (Ukai, 2012), (Yamasaki, 2012), reflejan las diferentes propiedades de este material dando como resultado una mayor resistencia la termofluencia y por lo tanto una vida útil mucho mayor. Esto motivó que se incluyera este acero en el análisis realizado en el presente trabajo, lo que será presentado a continuación (Tabla 2).
Tabla 2 Composición química del acero AISI 213 T91 (% en masa)
|
||||||||||
---|---|---|---|---|---|---|---|---|---|---|
0,08 a 0,12 | 0,20 a 0,50 | 0,30 a 0,60 | 0,010 | 0,020 | 8 a 9 | 0,85 a 1,05 | 0,18 a 0,25 | 0,4 | 0,05 a 0,1 | 0,03 a 0,07 |
Las propiedades físicas fundamentales fueron también ajustadas por el método de los mínimos cuadrados. Las ecuaciones (Ecuación 9, Ecuación 10, Ecuación 11) obtenidas en los ajustes son:
Para 220≤T≤800ºC
2.3.4 Metodología de pronóstico de la vida útil por termofluencia de acuerdo con la Norma ISO/TR 7468 - 1981, sin considerar el adelgazamiento de la pared.
La vida útil por fractura bajo termofluencia se puede calcular partiendo del Parámetro Larson Miller según los datos dados por la Norma (ISO/TR 7468, 1981). Según esta Norma para el acero SA-210 A1 de los tubos de la central termoeléctrica de Cienfuegos (CMC) se tiene que (Ecuación 12 y Ecuación 13):
Según esta Norma para el acero SA-213 T91 (9% Cr - 1% Mo) se tiene que:
Tabla 3 Constantes de la correlación de Larson Miller para el acero SA-210 A1
-0,68628 | 1,459851 | -1,18513 | 0,424568 | -0,05725 |
Tabla 4 Constantes de la correlación de Larson Miller para el acero SA-213 T91 (9% Cr - 1% Mo)
-0,80630 | 1,75733 | -1,45750 | 0,53256 | -0,07342 |
Donde: a, b, c, d, e son constantes del ajuste de la curva. En esta expresión de cálculo, t es la vida útil en horas, T la temperatura de trabajo en grados Kelvin y P(σ) es la tensión equivalente en la pared del tubo en MPa. Esta tensión σ se calcula por la Ecuación 2 para el caso de calentamiento exterior. Conociendo el valor de la tensión σ se pude calcular el valor del Parámetro de Larson Miller partiendo del lado derecho de las ecuaciones (12) - (13) y teniendo entonces la temperatura de trabajo T (oK) del material, se puede despejar del lado izquierdo de la misma, el tiempo de rotura en el cual dicho material a esa tensión y a esa temperatura se deformará plásticamente por el fenómeno de termofluencia alcanzando la deformación de rotura y ésta será la vida útil por termofluencia para esas condiciones de trabajo.
2.4 Metodología de pronóstico de la vida útil por termofluencia en presencia del fenómeno de adelgazamiento de la pared.
La metodología existente para el pronóstico da la vida útil por fractura bajo termofluencia en presencia del fenómeno de adelgazamiento de la pared (Rogers y Sidey, 1982); (Zarrabi, 1993), parte de suponer una razón de adelgazamiento constante en el tiempo, o sea, el espesor del tubo en un instante cualquiera a partir del comienzo de su explotación se puede calcular por la expresión (Ecuación 14):
Donde: h = espesor de la pared del tubo después de transcurrir t horas de explotación en m.
= espesor original del tubo en m.
= razón de adelgazamiento en m/h.
En (Zarrabi, 1993) se da como rango de valores típicos de la razón de adelgazamiento para tubos característicos de calderas hechos de material 2,25% Cr; 1% Mo, el siguiente:
En este propio trabajo se propone establecer esta razón midiendo el espesor h después de un tiempo t de explotación y calculando la razón de adelgazamiento por la siguiente expresión (Ecuación 15):
En los tubos de las paredes de agua de la central termoeléctrica se asumió una razón constante. En este caso la predicción de la vida útil por fractura bajo termofluencia en presencia del adelgazamiento de la pared del tubo se realizará por la misma Metodología empleada cuando no existía adelgazamiento de la pared, simplemente al calcular la tensión por la ecuación de (Jusmatulin, 1990) el parámetro ε se modifica en función del adelgazamiento que se haya producido en el tubo, de acuerdo a las ecuaciones (2), donde: ℎ = razón de adelgazamiento en 𝑚 ℎ . (Ecuación 16)
En la Figura 3 se muestra algoritmo elaborado en el presente trabajo para el pronóstico de la vida útil por termofluencia sin y con adelgazamiento del tubo.
RESULTADOS Y DISCUSIÓN
3.1 Predicción de la vida útil por termofluencia considerando la diferencia de temperatura de la pared para los Aceros SA-210 A1 y SA-213 T91considerando el adelgazamiento de la pared.
3.1.1 Datos de los tubos para la comparación sin adelgazamiento.
Como presión de trabajo, diámetro nominal, espesor de la pared y razones de adelgazamiento en estos primeros cálculos de los tubos de la CTE tomaron los valores siguientes: p = 14,32 MPa, D = 58,60 mm, h = 4,90 mm para ver la influencia del adelgazamiento se evaluarán 2 razones de adelgazamiento: k = 2,5 nm/h y 15 nm/h.
3.1.2. Resultados obtenidos.
Los resultados obtenidos se muestran en los gráficos mostrados en la Figura 4 a) y b).

Figura 4 Vida por termofluencia en función de T oK y Δt oC para a) k=2,5*10-6 mm/h, b) k=15*10-6 mm/h para el acero SA-210 A1
Como se aprecia de las gráficas mostradas, la vida útil por fractura bajo termofluencia, realmente depende poco del adelgazamiento de la pared. Así por ejemplo, para el acero SA-210 A1, si la temperatura de la pared del tubo es de 500 K, la vida útil por fractura bajo termofluencia sin adelgazamiento de la pared es casi es 4,4 x 1010 horas. Sin embargo, para k = 2,5 x 10-6 mm/h la vida útil se reduce a 4,39 x 1010 horas. Esto para Δt con cualquier valor. Y para otras temperaturas y valores de Δt sucede algo similar. Se puede visualizar que cuando la razón de adelgazamiento (k) es mayor (en este trabajo se tomó k=15 x 10-6 mm/h) la vida útil a medida que aumenta la temperatura comienza a disminuir paulatinamente a 507 K va desde 9,379 x 109 horas (con k=0) hasta 8,022 x 109 horas (con k=15 x 10-6 mm/h) lo que equivale a 1,357 x 109 horas de vida.
La Figura 5 muestra los resultados obtenidos para el acero SA-213 T91. Como se puede apreciar de dichas gráficas, para la temperatura de T = 600 K la razón de adelgazamiento influye muy poco en la vida útil por termofluencia. Por ejemplo en el trabajo (Rivero, 2012) para T = 600 K sin adelgazamiento de la pared la vida por termofluencia da alrededor de 4,8 x 1011 horas y con una pequeña razón de adelgazamiento de k = 2,5 x 10-6 mm/h la vida da incluso ligeramente mayor, o sea, 4,85 x 1011 horas.
CONCLUSIONES
La metodología desarrollada y programada en MatLab mejora el pronóstico de vida útil por termofluencia al tomar en cuenta la forma de considerar el adelgazamiento de los tubos de calderas.
Aplicando la metodología así perfeccionada a los tubos de las calderas de la central termoeléctrica de Cienfuegos “Carlos Manuel de Céspedes”, para el acero SA-210 A1, a la temperatura de 500 K, se produce un punto de inflexión típico, donde el adelgazamiento de la pared puede llegar a representar 800 millones de horas, pero en porcentaje de reducción de la vida útil por termofluencia esto representa un 1,8 %.
Aplicando la metodología al acero SA-213 T91, muy empleado en la actualidad en los tubos de calderas, se aprecia que para T = 600 K, se produce un punto de inflexión típico, la vida es del orden de 10 veces superior a la del acero: SA-210 A1, sin embargo la influencia del adelgazamiento puede llegar a representar 1000 millones de horas, pero en porcentaje de reducción de la vida esto no supera el 0, 25 %, también casi 10 veces más pequeña que con el acero SA-210 A1.