INTRODUCCIÓN
Las fundiciones blancas con alto contenido de Cr son las más utilizadas en el recargue de piezas sometidas al desgaste por abrasión, ya que garantizan el despeño con un tiempo de vida razonable de numerosas piezas utilizadas en el procesamiento de minerales, en la industria del cemento, agricultura y la extracción de hidrocarburos (Venkatesha y Srikera, 2015), (Xin y col., 2020).
Cuando la abrasión es extrema, como en el caso de las barrenas de perforación y herramientas para el pulido de losas, se recomiendan otras aleaciones para el recargue, donde la microestructura de los depósitos se caracteriza por la presencia de carburos sinterizados, como por ejemplo: WC, W2C, TiC y VC, con durezas que pueden llegar hasta los 3000 HV0,1 (Durum Verschleiss-Schutz GMBH, 2016).
Las fundiciones blancas con alto contenido de Cr, pueden presentar una microestructura del tipo hipoeutéctica , eutéctica o hipereutéctica, dependiendo del contenido de C y de la presencia de otros elementos de aleación (Lin y col., 2009), (Chang y col., 2009). Las aleaciones hipoeutécticas, se caracterizan por una microestructura donde se manifiesta la austenita primaria de forma dendrítica y una red eutéctica con la presencia de carburos, que en dependencia de la relación Cr/C pueden ser del tipo M3C, M7C3 o M23C6 (Çetinkaya y col.,2006), (Chia-Ming y col., 2010). Las aleaciones hipereutécticas tienen una microestructura diferente, ya que exhiben carburos primarios de forma hexagonal, que ocupan generalmente más del 30 % de la microestructura y una matriz compuesta por carburos eutécticos y otras fases como; martensita, austenita o perlita, en dependencia de la velocidad de enfriamiento (Venkatesha y Srikera, 2015). Estos autores plantean que las aleaciones blancas hipereutécticas con alto contenido de Cr, pueden tener durezas en el orden de los 750 HV, la cual es proporcional a la fracción volumétrica de carburos, y por su fragilidad están recomendadas para utilizarse en el caso de que las piezas estén sujetas a la abrasión sin impacto.
Debido a la fragilidad de las fundiciones blancas con alto contenido de C (hipereutécticas), para los trabajos de recargue de piezas sometidas a la abrasión con impactos se utilizan las aleaciones del tipo hipoeutécticas, ya que presentan mayor tenacidad. En estos sistemas además del C y el Cr, se añaden otros elementos de aleación tales, como; Mo, Mn, V, y Nb, para mejorar la microestructura, fundamentalmente en la zona eutéctica, de forma tal que sean capaces de garantizar la resistencia a la abrasión y sobreponerse al efecto de los impactos (Liu y col., 2013).
Günther y y Bergmann, (2020) han demostrado que la adición de V en el sistema Fe-Cr-C, puede dar lugar a la presencia de VC, fenómeno que provoca una reducción del contenido de C en la zona interdendrítica y en consecuencia su templabilidad, manteniendo cierta ductilidad en la capa de recargue, sin afectar la resistencia a la abrasión.
El contenido de C en los depósitos de recargue de las fundiciones blancas hipoeutécticas al Cr, normalmente está en el rango de 2,3 - 4 %, y en dependencia de la presencia de otros elementos de aleación pueden tener diferente comportamiento ante el desgaste por abrasión (Sabet y col., 2011).
En el presente trabajo tiene como objetivo aumentar la resistencia al desgaste abrasivo de la aleación hipoeutéctica que se deposita con el electrodo AWS E FeCr- A8.
MATERIALES Y MÉTODOS
2.1. Metal base, electrodo y realización de los depósitos
Como material base se utilizaron chapas de acero S275JR de 100 x 50 x15 mm. Para la obtención de los depósitos se utilizó un electrodo comercial de recargue del tipo AWS E FeCr-A8, al cual se le adicionó un revestimiento periférico de 1 mm de espesor como se indica en la figura 1, compuesto por 100 % de grafito para incrementar el contenido de C.
Para la realización de los depósitos, se utilizó corriente directa con polaridad normal (CD -) y una intensidad de corriente entre 140 A y 150 A, manteniendo la velocidad de soldadura (Vs) en el rango de 4-5 m/h. Las muestras para el análisis de composición química y estructura metalográfica del depósito sin dilución fueron elaboradas cumpliendo lo establecido por la norma (AWS A5.13, 2021).
Para determinar la resistencia al desgaste abrasivo se realizaron los depósitos con el mismo régimen de soldadura sobre placas de acero S275JR, con 7,62 x 2,54 x 1,27 cm, de acuerdo a las dimensiones que establece la norma (ASTM G65, 2017). En la figura 2 se puede observar la forma de realización de los depósitos con las dos variantes de electrodos (EO y EM), para el estudio de la resistencia al desgaste del metal del cordón.
2.2. Preparación de muestras para la determinación de la dureza y microestructura
Las probetas para el estudio metalográfico se obtuvieron mediante cortes transversales de los depósitos, utilizando una tronzadora y líquido refrigerante para evitar el sobrecalentamiento. Las muestras utilizadas para determinar la dureza y estudiar la microestructura fueron debidamente desbastadas y pulidas, teniendo en cuenta un conjunto de operaciones, según lo establecido en las normas (ASTM E3-11, 2017). El ataque fue realizado por inmersión con el reactivo Murakami, en correspondencia con la norma (ASTM E407, 2016). Las muestras fueron observadas mediante microscopía electrónica de barrido (SEM). La dureza se determinó en el centro de los depósitos con el empleo de una carga de 1000 g. Para obtener la composición química en la zona eutéctica se utilizó microscopía electrónica de barrido (SEM) con detector EDS.
2.3. Ensayo de desgaste
De acuerdo a los establecido por la norma (ASTM G65, 2017) se ha seleccionado el procedimiento B, considerando que las aleaciones aportadas por los consumibles a evaluar, no forman parte de los sistemas de aleación destinados a la abrasión extrema. Según lo establecido por el procedimiento B, se utilizó arena de sílice con una granulometría entre 210 - 300 µm, un flujo de 300 g/min y una carga de 30 N. En la figura 3 se muestra la máquina utilizada en los ensayos de desgaste abrasivo, fabricada en dependencia de los requerimientos que establece la norma ASTM G65.
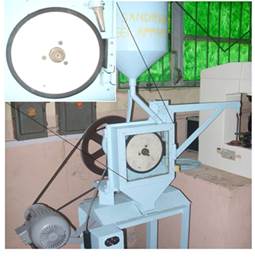
Figura 3 Máquina utilizada para el ensayo de la resistencia al desgaste abrasivo de acuerdo a ASTM G65 (Rodríguez y col., 2019)
RESULTADOS Y DISCUCIÓN
3.1.Comportamiento de la composición química de los depósitos de recargue con el electrodo original y modificado
La composición química de los depósitos, sin efecto de la dilución, obtenidos con el electrodo original y el modificado, se muestra en la tabla 1. La modificación del electrodo comercial trajo como resultado el incremento en la cantidad de carbono de 2,4% a 3,7%, manteniendo relativamente similar la cantidad del resto de los elementos de aleación. El electrodo utilizado se clasifica como E FeCr-A8 según la norma (AWS A5.13, 2021) de acuerdo con la composición química obtenida (tabla 1), para ambos depósitos.
Tabla 1 Composición química (% en peso) de los correspondientes depósitos sin efecto de la dilución
Electrodo | Identificación del depósito | C | Mn | Si | Cr | Mo | Fe |
---|---|---|---|---|---|---|---|
Original | EO | 2,7 | 1,2 | 1,1 | 32,0 | 1,8 | balance |
Modificado | EM | 3,7 | 1,3 | 1,0 | 31,5 | 2,0 | balance |
La composición química permite realizar una evaluación preliminar de las fases que se forman, en condiciones de equilibrio, durante la cristalización primaria y secundaria de cualquier aleación metálica; lo cual facilita el análisis y comprensión del tipo y el origen de la microestructura resultante en la aleación. En este sentido, para el caso de los depósitos obtenidos se recomienda trabajar con el diagrama de equilibrio del sistema Fe-Cr-C, analizando la proyección de la superficie del líquido a diferentes temperaturas (Atamert Bhadeshia, 1990).
Se ha demostrado que existen diferencias con relación a la proyección de la superficie del líquido del sistema Fe-Cr-C publicada por diferentes autores (Andersson y col., 1988), lo que puede conducir a diferencias en cuanto a la interpretación del resultado de la solidificación. Por esta razón, se recomienda utilizar el gráfico que aparece en la figura 4 (Bálsamo y col., 1995), sobre el cual se indica la región de composición química (Cr y C) correspondiente a los depósitos EO y EM, respectivamente.

Figura 4 Diagrama de equilibrio del sistema Fe-Cr-C con la proyección de la superficie del líquido (Bálsamo y col., 1995), y la región de composición química (Cr y C) correspondiente a los depósitos EO y EM, respectivamente
Se observa que, en el diagrama de la figura 4, ambos depósitos se sitúan en la región en la que solidifican carburos primarios (M7C3) y eutéctica (Fe( + M7C3), tal como ocurre en las aleaciones hipereutécticas. Sin embargo, las respectivas imágenes de la microestructura (figura 5) muestran que el comportamiento de los depósitos es característico de aleaciones hipoeutécticas, en las que durante la solidificación se forman dendritas primarias de austenita (Fe(() y eutéctica (Fe( + M7C3), indicadas como 1 (zonas claras) y 2 (zonas oscuras), respectivamente.
La discrepancia, entre los resultados experimentales y el análisis de la solidificación sobre la base de la proyección de la superficie del líquido, se ha reportado por otros autores, para el caso de fundiciones de pequeñas dimensiones, en las que la solidificación ocurre con velocidades de enfriamiento relativamente altas (Bálsamo y col., 1995). Estas condiciones de enfriamiento son características del proceso de recargue, por tanto, al igual que en las fundiciones, traen como resultado que la solidificación se aleje notablemente de lo que indica el diagrama de la proyección de la superficie del líquido.
Utilizando los valores de la composición química de la región eutéctica para ambos depósitos (figura 6), se determinó la fracción volumétrica de carburos eutécticos de acuerdo a la expresión 1, (Andersson, 1988).
Donde : %E.C. - fracción volumétrica de carburos; %C-por ciento de C en el depósito; % Cr - por ciento de Cr en el depósito.
Los resultados obtenidos de la fracción volumétrica de carburos (E.C.) para los depósitos realizados con el electrodo original (EO) y el modificado (EM) es de 63 % y de 74 %, respectivamente. Este resultado define el comportamiento de la dureza (tabla 2), de manera que con el aumento de la fracción volumétrica de los carburos eutécticos en la microestructura del depósito con el electrodo modificado se alcanza una dureza de 750 HV, considerablemente superior a la obtenida con el electrodo original (625 HV).
Tabla 2 Dureza de los depósitos obtenido con los electrodos EO y EM
Electrodo | Valores de dureza HV50 | Media (HV) | D.E.(s) | Dureza (HRC) |
---|---|---|---|---|
EO | 625 | 625 | 16,5 | 56 |
632 | ||||
603 | ||||
642 | ||||
EM | 744 | 750 | 14,9 | 62 |
735 | ||||
753 | ||||
770 |
Los resultados presentados en la figura 7 indican que hay diferencias estadísticamente significativas, al comparar la pérdida de volumen en las muestras ensayadas del metal depositado con las variantes de electrodos EO y EM.
Trascienden los menores volúmenes de pérdida de metal para el caso de los depósitos obtenidos con el electrodo modificado (EM), al cual se le adicionó un revestimiento periférico con 100 % de grafito. Lo anterior significa que el metal depositado con el electrodo modificado (EM) tiene mayor resistencia al desgaste abrasivo, lo que se puede explicar debido al incremento del volumen que ocupa la zona eutéctica en la microestructura para esta variante, cuya dureza supera los 700 HV. Por otra parte, para el depósito realizado con el electrodo modificado (EM) el volumen porcentual de carburos eutécticos es de 74 %, cuya dureza reducen el efecto de desbaste de las partículas abrasivas, ya que bloquean los microcortes y, por tanto, hace que aumente la resistencia al desgaste (Buchely y col., 2005), (Buchanan y col., 2008), (Kenchireddy y col., 2014).
CONCLUSIONES
El aporte de C adicional al metal depositado, proveniente del revestimiento periférico superpuesto al electrodo AWS E FeCr-A8, conduce a que en la microestructura, la austenita presente una forma irregular y aumente apreciablemente el volumen de la zona eutéctica (74%), provocando que la dureza alcance valores en el orden de 750 HV; mientras para el depósito con el electrodo convencional, con fracción volumétrica de eutéctica menor (63 %), la dureza fue también inferior (625 HV).
El incremento de la fracción volumétrica de los carburos eutécticos para los depósitos obtenidos con el electrodo AWS E FeCr-A8 modificado, permite obtener mayor resistencia al desgaste por abrasión, manteniendo el modo de solidificación propia de las aleaciones hipoeutécticas, aspecto fundamental para mantener cierta resistencia al desgaste por impacto.